Подробные данные об ошибке IIS 8.5 — 404.0
Ошибка HTTP 404.0 — Not Found
Разыскиваемый вами ресурс был удален, было изменено его имя или он временно недоступен.
Наиболее вероятные причины:
- Указанный каталог или файл не существует на данном веб-сервере.
- URL-адрес содержит орфографическую ошибку.
- Специальный фильтр или модуль, такой как URLScan, ограничивает доступ к файлу.
Возможные решения:
- Создайте содержимое на веб-сервере.
- Проверьте URL-адрес веб-браузера.
- Создайте правило трассировки с целью отслеживания невыполненных запросов для данного кода состояния HTTP и определите, какой модуль вызывает SetStatus. Чтобы получить дополнительные сведения о создании правила трассировки для невыполненных запросов, щелкните здесь.
Подробные сведения об ошибке:
Модуль | IIS Web Core |
---|---|
Уведомление | MapRequestHandler |
Обработчик | StaticFile |
Код ошибки | 0x80070002 |
Запрошенный URL-адрес | http://library.![]() |
---|---|
Физический путь | F:\WWW\Library\librarticlessectionseditionsfilesdownload.asp?lngsection=21&lngedition=4354&lngfile=4331&strparent=librarticlessectionseditionsfiles |
Метод входа | Анонимная |
Пользователь, выполнивший вход | Анонимная |
Дополнительные сведения:
Эта ошибка означает, что данный файл или каталог не существует на этом сервере. Создайте нужный файл или каталог и вновь направьте запрос.Технологические режимы литья под давлением
К важнейшим параметрам технологического процесса при литье под давлением относятся: продолжительность заполнения пресс-формы расплавом; скорость поступления расплава в пресс-форму; размеры и расположение вентиляционных каналов; количество и свойства смазочного материала пресс-формы; температура расплава и пресс-формы.
Продолжительность заполнения пресс-формы. Рекомендуемая зависимость продолжительности заполнения пресс-формы металлом (t
Рисунок 4.4 – Зависимость времени заполнения пресс-формы от толщины отливки: 1 – магний; 2 – магниевый сплав; 3 – алюминиевый сплав; 4 – цинковый сплав
Скорость поступления расплава в пресс-форму, определяя характер его движения (сплошной спокойный или с высокой турбулентностью, дисперсный), оказывает влияние не только на качество отливки, но и на долговечность пресс-формы. Так, слишком высокая скорость расплава повышает вероятность смыва смазочного материала с рабочих поверхностей пресс-формы, эрозионного воздействия на ее стенки и, как следствие этого, приваривания отливки к пресс-форме. При извлечении отливки это может приводить к поломке пресс-формы, короблению, образованию трещин на отливке или ее разрушению. Работа при низких скоростях расплава, как правило, не обеспечивает высокого качества поверхности отливок.
Для всех типов сплавов, используемых при литье под давлением, опти-мальная скорость поступления расплава в пресс-форму чаще всего составляет 10 – 50 м/с (меньшие значения – скорости, используемые при изготовлении отливок из сталей и медных сплавов, большие – из цинковых и свинцово-оловянистых сплавов).
Температура пресс-формы перед заливкой назначается с учетом состава заливаемого сплава, конфигурации отливки, толщины ее стенки, а также других факторов. При литье цинковых сплавов температура пресс-формы должна составлять 120 – 160 Для уменьшенной толщины стенки отливки и усложненной ее конфигурации температуру пресс-формы назначают ближе к верхнему пределу указанных интервалов, а для более массивных отливок – ближе к нижнему. Соблюдение этого принципа позволяет при изготовлении тонкостенных отливок улучшить заполнение формы расплавом, а для более массивных – повысить скорость затвердевания и уменьшить количество усадочных дефектов. Для регулирования температурного режима работы пресс-формы, управления процессом затвердевания и охлаждения отливки в конструкциях пресс-форм служат системы охлаждения или тепловой изоляции отдельных элементов пресс-формы.
Температура заливки расплава зависит от химического состава сплава, конфигурации отливки, ее размеров и выбранного режима заполнения пресс-формы. При заполнении пресс-форм значительно перегретым расплавом последний может проникнуть в вентиляционные каналы пресс-формы и закупорить их, что приведет к увеличению газовой пористости в отливках, а в некоторых случаях к браку по незаполнению формы. Высокая температура расплава способствует увеличению объема усадочных пор в отливке. Длительность затвердевания и охлаждения отливки возрастает. При этом снижается темп работы машин, возрастает тепловая нагрузка на пресс-форму, вследствие чего снижается ее стойкость, увеличивается опасность «приваривания» отливки к пресс-форме, возникает опасность поломки отливки или пресс-формы при выталкивании отливки.
Этим объясняется стремление литейщиков заливать расплав при возможно более низкой температуре: для цветных сплавов температура заливки расплава в камеру прессования обычно на 10 – 30оС выше температуры ликвидуса. С увеличением размеров отливки и уменьшением толщины ее стенки температуру заливки принимают ближе к верхнему пределу, а для массивных отливок простой конфигурации – ближе к нижнему. Для массивных отливок, а также отливок с повышенными требованиями по плотности температуру расплава часто принимают а интервале ликвидус – солидус, т.е. проводят заливку расплава в твердожидком состояния.
При литье сплавов в твердожидком состоянии уменьшается пористость отливок, вследствие чего возрастает их герметичность, несколько повышаются их механические свойства. Температуру заливки в этом случае назначают в соответствии с необходимым содержанием твердой фазы в расплаве и определяют по диаграмме состояния сплава. Содержание твердой фазы обусловливает реологические свойства сплава, эффективную вязкость, модуль упругости, предельные напряжения сдвига, т.е. характеристики его свойств, от которых зависит способность сплава заполнять полость пресс-формы. Для алюминиевых сплавов типа АЛ9 содержание твердой фазы, при котором обеспечиваются хорошая заполняемость форм и удовлетворительные свойства отливок, должно находиться в пределах 40 – 60 %.
Давление прессования зависит от толщины стенки отливки, ее размеров и конфигурации, химического состава сплава.
Анализ требований, предъявляемых к отливке, позволяет оценить минимально необходимое давление прессования Pnpmin. При этом чем больше толщина стенки отливки, тем более высокое давление прессования требуется для обеспечения ее качественных характеристик. Для примера, приведенного в таблице 4.1, меньшие значения рекомендуемого давления прессования соответствуют толщине стенки отливки около 3 мм, а большие – 5 – 7 мм.
Таблица 4.1 – Рекомендуемое давление прессования для отливок разного назначения
Смазочные материалы, которые используются при литье под давлением, делятся на две основные группы: первая для смазывания рабочих поверхностей пресс-формы, вторая для смазывания пресс-поршня и камеры прессования.
Смазочные материалы для пресс-форм защищают их рабочие поверхности от химического, механического, теплового воздействия струи расплава, предотвращают приваривание отливки к пресс-форме, а также снижают усилие извлечения стержней и отливок из пресс-формы, т.е. предотвращают поломку оснастки и деформацию отливок при извлечении их из пресс-форм.
Смазочные материалы для пресс-форм должны обладать высокими смазывающими и противозадирными свойствами при температурах взаимодействия отливки и пресс-формы, иметь минимальную газотворность при разложении под действием высоких температур, не оказывать вредного влияния на свойства отливок (герметичность, газосодержание, коррозионную стойкость), не повреждать поверхность пресс-формы и отливки, быть нетоксичными, не содержать дефицитных материалов. Кроме этого, смазочный материал должен сохранять свои свойства при хранении, быть пожаро- и взрывобезопасным, обладать такими свойствами, чтобы его можно было наносить на поверхность пресс-формы автоматическими устройствами.
Чаще всего для автоматизированного выполнения операции смазывания в производстве используют смазочные материалы на основе минеральных масел в виде эмульсии масла в воде с добавками твердых наполнителей со сложной молекулярной структурой и различных химически активных присадок.
Способ управления процессом кристаллизации алюминиевых сплавов при литье под давлением
Изобретение относится к литейному производству и может быть использовано для управления структуры алюминиевых сплавов с целью повышения механических свойств изделий.
Известен способ литья под давлением, который заключается в заливке дозированного объема расплавленного металла в цилиндр прессования, заполнение полости формы расплавом, последующее наложение давления на него и выдержку. Расплав перед заливкой перегревают на 40-70К выше его температуры ликвидуса. При этом расплав заливают в промежуточную емкость, а в это время производят вакуумирование полости формы, после чего полость формы и связанные с ней камеры прессования заполняют расплавом из промежуточной емкости. Одновременно с заполнением камер прессования, сообщающихся с полостью формы, продолжается вакуумирование полости формы. Скорость заполнения регулируют изменением скорости откачки воздуха и газов из полости формы и камер прессования до окончания их заполнения. При этом регулирование скорости откачки воздуха и газов осуществляют изменением площади отверстия, связывающего полость формы через контркамеру прессования с системой вакуумирования, за счет перемещения контрплунжера. Затем осуществляется двухстороннее наложение давления на расплав по оси заготовки, при этом величина давления составляет 200-500 МПа. Выдержку металла под давлением производят до момента окончания кристаллизации. Для реализации этого способа используется машина для литья под давлением, которая оснащена гидравлической системой и блоком управления, содержит механизм прессования с плунжером и камерой, размещенными в корпусе, и связанную с ними разъемную пресс-форму с литейной полостью, сообщающейся с отверстиями для заливки расплава и удаления воздуха и газов.
При этом механизм прессования оснащен дополнительной камерой прессования и контрплунжером, размещенными в неподвижной части корпуса соосно пресс-форме ответно камере и плунжеру, выполненными в подвижной части корпуса. Отверстие для заливки расплава выполнено с возможностью его перекрытия плунжером и сообщено с промежуточной емкостью, жестко закрепленной на подвижной части корпуса, а отверстие для удаления воздуха (газов) выполнено с возможностью его перекрытия контрплунжером и сообщено с системой вакуумирования (Патент RU №2193945, С2, МПК B22D 18/02, заявлено 30.05.2000. Опубликовано 10.12.2002 г.).
Недостатком вышеуказанного способа является то, что он не обеспечивает повышения механических свойств отливок путем формирования фрагментов наноструктур из отдельных атомов и их ассоциаций, так как температура перегрева жидкого металла на 40-70К недостаточна, чтобы обеспечить степень переохлаждения, которая определяется разностью равновесной температуры кристаллизации и фактической температуры образования твердой фазы. Снижение степени переохлаждения связано еще и с тем, что заливка металла производится из невакуумированной промежуточной емкости, что требует дегазации жидкого металла. На первом этапе наложения давления на металл, который свободной заливкой заполняет полость формы, увеличивается скорость удаления газов и сжатия межплоскостных поверхностей с образованием пустот. Температура расплава при этом понижается до температуры образования твердых кристаллических фаз. В этот момент наступает второй этап наложения давления, заключающийся в наложении давления изнутри из-под корки закристаллизовавшегося металла. При этом структура формируется в результате запрессовывания дополнительных объемов металла на компенсацию усадки, а также на пластическую опрессовку литых кристаллов, сформировавшихся до наложения давления. Такой способ не обеспечивает формирование в металле фрагментов наноструктуры из отдельных атомов и их ассоциаций, так как уже образовались твердые фазы кристаллов, для получения в которых наноструктур необходима их пластическая деформация твердого металла за счет приложения более высокого давления.
Полученная по этому способу структура не имеет усадочных дефектов, характеризуется высокой герметичностью, но она состоит из отдельных зон-фрагментов, отличающихся по виду и характеру строения. Таким образом, способ решает проблему уплотнения кристаллизующегося металла за счет наложения давления, т.е. влияние давления на качество и свойства отливок проявляется лишь в устранении обычных дефектов усадочного происхождения.
Наиболее близким к заявляемому является способ управления процессом кристаллизации и устройство для его осуществления (патент №RU 2516210), при котором жидкий металл, находящийся при температуре выше ликвидуса на 150-200 К, заливают в контейнер — кристаллизатор из вакуумной камеры. Величина вакуума в контейнере-кристаллизаторе составляет 0,2-0,3⋅10-5 мм рт.ст. На кристаллизующийся металл накладывают давление пресс-плунжерами и повышают его со скоростью более чем 40 МПа/с до величины 300-400 МПа. После сжатия металла на 10% повышают давление с той же скоростью до 500 МПа и дополнительно уплотняют металл на 2,4-2,8%. Изостатическое сжатие металла осуществляют до тех пор, пока металл не охладится до 100-150°С.
Недостатком вышеуказанного способа является то, что наложение давления осуществляется в 2 этапа, процесс опрессовки металла растягивается на значительный период времени: 1 фаза — 5 с, 2 фаза — 60 с и более. За указанные отрезки времени диффузионные процессы приводят к тому, что достигаемое за счет наложения давления неравновесное состояние сплава стремится к равновесному. Из фиг. 1 видно, что структура, сформированная при наложении давления в два этапа, не существенно отличается от равновесной структуры; процесс опрессовки осуществляется без использования частотно-импульсной модуляции, что не обеспечивает влияния давления на формирование фрагментов наноструктуры и требуемого повышения механических свойств.
Таким образом, экспериментально было установлено, что способ наложения давления, для получения требований заданного результата необходимо осуществлять опрессовку за один этап и с использованием частотно-импульсной модуляции. График изменения коэффициента сжимаемости жидкого (до т.R) металла от времени приведен на фиг. 2, который подтверждает, что процесс осуществляется в один этап.
Задачей заявленного изобретения является получение более высокого уровня механических свойств изделий путем формирования неравновесной структуры сплава. При этом управление формированием структуры алюминиевых сплавов нацелено на то, чтобы всестороннее давление, накладываемое на жидкий металл, было направлено на формирование заданной неравновесной структуры, определяющей свойства, не уступающие или превосходящие свойства проката, кованных и штампованных заготовок.
Поставленная задача решается за счет того, что способ управления процессом кристаллизации алюминиевых сплавов при литье под давлением включает (см. фиг. 3) заливку жидкого металла 5, находящегося при температуре выше ликвидуса на 150-200 К, в вакуумируемую полость формы 3 через заливочную чашу 7, путем подрыва стопора 6. Величина вакуума составляет 0,2-0,3⋅10-2 мм рт. ст. Полость формы связана с вакуумным насосом с помощью штуцера 2. На кристаллизующийся металл накладывают давление левым пресс-плунжером 1 и правым пресс-плунжером 4, которые движутся навстречу, в однофазном режиме и повышают его со скоростью 120-125 МПа/с, с интервалами 0,5-0,1 с, в течение 4 с до величины 500 МПа, тем самым уплотняя металл на 12,8% (см. фиг. 2). Подпрессовка металла осуществляется под давлением p=3σт(t), где σт(t) — предел текучести опрессовываемого сплава с учетом температуры, до тех пор, пока металл не охладится до 100-150°С.
Предлагаемый способ управления процессом кристаллизации алюминиевых сплавов при литье под давлением основан на установленной авторами закономерности влияния скорости, интервалов и величины накладываемого давления на жидкий металл, которые приводят к увеличению коэффициента сжимаемости и, как следствие, повышению качества получаемых отливок. Наложение давления в однофазном режиме с использованием частотно-импульсной модуляции и уменьшение объема металла связано с улучшением процесса кристаллизации тем, что сохраняющиеся в жидкой фазе кластеры к моменту начала кристаллизации и в процессе кристаллизации занимают в пространстве положение и ориентацию, способствующие процессу кристаллизации. При этом сопровождаемое выделением скрытой теплоты кристаллизации сближение атомов направлено на формирование дополнительных межатомных связей, приводящих к образованию сильно неравновесной структуры.
Величина накладываемого давления 500 МПа течение 4 с, по 120-125 МПа/с, с интервалами 0,5-0,1 с, экспериментально определена для сплавов различного состава.
Таким образом, экспериментально было установлено, что способ наложения давления, для получения требований заданного результата необходимо осуществлять за 1 этап, а именно сжатие жидкого металла на 12,8% давлением 500 МПа в течение 4 с, по 120-125 МПа/с, с интервалами 0,5-0,1 с, который определяет сближение атомов и получение неравновесного состояния жидкого металла.
Предлагаемый способ дает возможность накладывать давление с фиксированной скоростью до уровня 500 МПа в однофазном режиме, исключающем развитие диффузионных процессов. С этой целью в системе управления устанавливается пропорциональный регулятор, параметры настройки которого выбираются из условия, что скорость наложения давления превышает требуемую по технологии скорость на 20-25%. При включении гидросистема поднимает давление, которое начинает превышать требуемую скорость, это фиксируется датчиком давления. По программе, когда давление достигает 100-125 МПа, подается команда на отключение гидропривода, давление в системе начинает падать, при этом осуществляется сравнение фактического давления с давлением, которое должно быть в данной момент времени по программе. В момент, когда значения выравниваются, происходит включение гидропривода, и так через каждые 120-125 МПа, пока давление не достигнет 500 МПа.
Установленное на 20-25% увеличение скорости наложения давления выбрано с учетом чувствительности датчика и времени срабатывания клапана, которое составляет 0,5-0,1 с.
В предлагаемом способе давление используется как термодинамический фактор, который, как и температура, определяет состав фаз в неравновесных условиях и влияет на фазовые превращения и структуру в твердом состоянии при изменении скорости наложения давления. То есть наложение изостатического давления является фактором воздействия, определяющего множество вариантов технологических параметров, приводящих к формированию неравновесной структуры сплавов.
Формирование фрагментов неравновесного состояния может быть достигнуто, в соответствии с данной заявкой, в условиях сверхбыстрого сжатия при температуре выше температуры начала кристаллизации, когда атомы утрачивают характерную для них диффузионную подвижность и способность формировать равновесные фазы, отличающиеся по составу и строению кристаллической решетки. Такое состояние может быть достигнуто, если такие параметры процесса, как перегрев жидкого металла над температурой ликвидуса, скорость нарастания давления, временные интервалы между импульсами, величина давления, накладываемого на жидкий металл, степень изостатического сжатия жидкого металла до начала кристаллизации, подобраны предварительно опытным путем и обеспечивают необходимое сближение атомов до начала кристаллизации; при этом необходимо не снимать усилие с прессующих плунжеров, пока температура отливки не понизится до 100-150°С. Фрагмент микроструктуры, полученный с помощью заявляемой технологи, представлен на фиг. 4.
Для обеспечения вакуума в полости формы 0,2-0,3⋅10-2 мм рт.ст. в процессе заливки жидкого металла в комплексе предусмотрена автономная вакуумная система, представляющая собой вакуумный насос, вакуумный ресивер, штуцер и пр., обеспечивающая заданное значение разрежения в течение времени всего технологического процесса. Разница разрежения в полости формы, равное 0,2-0,3⋅10-2 мм рт.ст. против 1⋅10-1 мм рт.ст. в корпусе вакуумного насоса, позволяет не только увеличить скорость заполнения полости формы жидким металлом, но и создает условия, при которых полости формы заполняются жидким металлом с заданной скоростью плавно, сплошным фронтом, без разбрызгивания. Применение такого способа заливки жидкого металла в полость формы позволяет получать необходимые заданные свойства не только в слитках, но и в изделиях сложной формы, в том числе и пустотелых заготовок типа втулок, колец и т.п., без использования стержней, установка которых требует дополнительной оснастки. Заливка жидкого металла в полость формы сплошным фронтом обеспечивает поверхность слитков/изделий, на которой не наблюдалась волнистость, заусенцы и другие дефекты поверхности.
В этих условиях, когда полость формы заполняется жидким металлом, то (при такой схеме и параметрах процесса) распределение температуры по всему объему изделия происходит равномерно. Таким образом, создаются благоприятные условия для наложения давления на жидкий, а не на кристаллизующийся, и тем более, не на уже закристаллизовавшийся (твердый) металл. Закристаллизовавшийся металл оказывает на порядок более высокое сопротивление деформации и исключает распространение давления на еще не имеющийся в полости формы жидкий металл.
Управление работой гидросистемы осуществляется системой управления в автоматическом режиме. С помощью прикладной программы фиксируется режим управления формированием однородной квазикристаллической структуры, а значения и изменения параметров от времени процесса отражаются на осциллограмме. Для наложения на расплавленный металл давления по некоторому закону в управляющей программе предусмотрена возможность управления параметрами широкоимпульсной модуляцией электрического сигнала на дискретный электромагнитный клапан пресса. Данный принцип управления обеспечивает широкие пределы регулирования, как по давлению, так и по времени его поддержания, позволяет эффективно использовать возможности программирования без включения в гидросистему обычно применяемых дополнительных элементов: объемных или дискретных регуляторов.
Автоматическое управление величиной накладываемого давления и соответственно перемещением исполнительного органа гидропривода — плунжера, происходит таким образом, чтобы его ход отвечал задачам, которые решает процесс, обеспечивающий получение более высокого уровня механических свойств изделий, путем формирования неравновесной структуры металла.
В результате использована структура управления, принадлежащая к классу самонастраивающихся систем с математической моделью, имеющей обратную связь: основанную на внутренней корректирующей связи по положению. С помощью функции управления определяется требуемое управляющее воздействие усилия гидропривода, которое преобразуется в необходимую величину перемещения плунжеров. В связи с этим гидропривод, используемый для наложения давления на жидкий металл, помимо статических (развиваемое усилие, жесткость) и динамических (устойчивость, точность, качество переходного процесса) характеристик должен отвечать требованиям управления законом развиваемого усилия и скорости перемещения. К числу параметров, определяющих усилие и скорость перемещения плунжеров, относится давление в рабочей полости цилиндров и полости слива, масса движущихся частей, силы трения, площади поршня в напорной и сливной плоскостях.
Изобретение иллюстрируется фиг. 3. Для управления процессом кристаллизации алюминиевых сплавов при литье под давлением слитки (размером ∅80×70 мм) из алюминиевого сплава марки В95 (система Al-Zn-Mg-Cu) изготавливали в полости формы с применением предлагаемого способа по схеме, приведенной на фиг. 3. Выплавку сплава осуществляли в тигле, в индукционной печи мощностью 30 кВт. Так как принципиальное значение имеет температура заливаемого металла и температуры формы перед заливкой, то их измерение имело значение. По ходу плавки температуру металла и температуру формы контролировали тепловизором ThermaCAM Е25 с точностью ±5К. Сплав перегревали до 850°С, проводили термовременную обработку расплава в течение 15 мин, после чего металл заливали в полость формы, подрывая стопор заливочной чаши, полость формы вакуумировали до разрежения 0,2 0,3⋅10-5 мм рт.ст., предварительно нагретую до 300°С. Указанной величины перегрев необходим для того, чтобы расплавленный металл перед наложением давления представлял собой однофазную систему — раствор гомогенной концентрации с явно выраженными свойствами жидкости, которая, как известно, передает давление равномерно во всех направлениях.
Скорость наложения давления, интервалы наложения давления и максимальную величину давления выбирали по результатам предварительных исследований исходя из зависимости коэффициента давления от времени.
Для ряда алюминиевых сплавов необходимо наложить давление р = 500 МПа, при котором относительное уменьшение объема жидкого металла составляет 12,8%. В т.R фиксируется качественно новое состояние металла, когда, с одной стороны, перегрев над линией ликвидуса составляет ~200 К, а, с другой стороны, межатомные расстояния в твердом состоянии атомы теряют подвижность, по мере приближения к т. R происходит резкое повышение вязкости расплава.
Это состояние можно назвать квазитвердым состоянием. В квазитвердом состоянии атомы зафиксированы в тех положениях, в которых они находились до наложения давления, их диффузия затруднена, так как междоузлия, вакансии, дислокации и др. дефекты упаковки атомов при достигнутой степени сжимаемости не обладают требуемой пропускной способностью.
Для того чтобы квазитвердое состояние создать гарантировано, давление р = 500 МПа накладывали в течение 4 с, т.е. со скоростью v = 120-125 МПа/с, с интервалами 0,5-0,1 с.
Когда температура в тепловом центре слитка достигла значения ниже температуры 150-200°С, давление сняли, плунжеры отвели в исходное положение. Форму раскрыли, слиток извлекли из формы и охладили до цеховой температуры.
По результатам анализа структуры слитка (В95), выполненного с помощью растровой электронной микроскопии, установлено, что структура сплава, полученного по предлагаемому способу (фиг. 4), представляет собой твердый раствор с неравновесной структурой (A16Mn, A181Mn19) с размером зерен менее 50 нм. При этом сплав имеет более высокую плотность и более высокий уровень механических свойств, чем у проката, полученного по промышленной технологии.
Как видно из приведенных примеров и подтверждено результатами производственных испытаний, предлагаемый способ по сравнению с известными, включая прототип, позволяет управлять процессом кристаллизации алюминиевых сплавов при литье под давлением с целью получения более высокого уровня механических свойств слитков / изделий путем формирования неравновесной структуры сплава. Для его осуществления используется наложение изостатического давления 500 МПа с применением частотно-импульсной модуляции на весь объем кристаллизующегося металла вплоть до температуры 150-200°С.
Новый способ является универсальным, так как пригоден для управления процессом кристаллизации алюминиевых сплавов при литье под давлением. Видами положительного эффекта, производными от достигнутого технического решения, являются:
— улучшение качества целевого продукта в отношении однородности структуры сплавов, повышение уровня механических свойств сплавов;
— формирование неравновесной структуры сплавов;
— технологический процесс, в котором давление эффективно используется для управления формированием однородной квазикристалической структуры металла в процессе кристаллизации под давлением.
Способ управления процессом кристаллизации алюминиевых сплавов при литье под давлением, включающий нагрев металла до температуры выше ликвидуса, заливку жидкого металла в вакуумируемую полость формы из заливочной чаши после подрыва стопора, наложение давления на жидкий кристаллизующийся металл, уплотнение металла и выдержку под давлением, отличающийся тем, что давление накладывают с повышением его до 500 МПа со скоростью 120-125 МПа/с и интервалами 0,5-0,1 с, а выдержку металла под давлением осуществляют до момента охлаждения сплава до 100-150°С.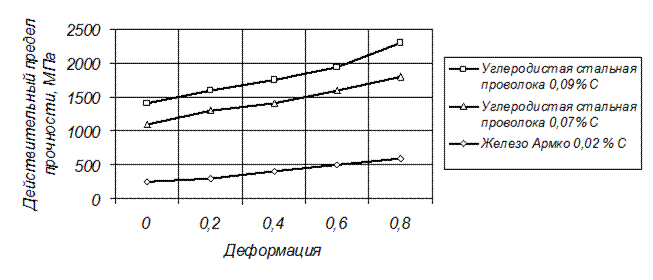
Литье в кокиль (кокильное литье) | Специальные методы литья
Литье в кокиль (кокильное литье), или литье в металлическую форму многоразового использования, является одним из прогрессивных методов производства. Оно предназначено для получения отливок из чугуна, стали, алюминиевых, магниевых, цинковых, медных и других сплавов. Наиболее широко применяется литье в кокиль при применении цветных металлов. Кокильное литье повышает формовочную площадь (в 2—6 раз), производительность труда (в 1,5—6 раз), точность исполнения отливки, выход годного литья благодаря уменьшению припусков. При этом методе литейного производства снижаются количество брака (особенно, если отливки подвергаются гидропробе) и себестоимость продукции.
Отливки, затвердевшие в металлической форме, имеют более плотную мелкозернистую структуру и более высокие механические свойства. Значительно улучшаются санитарно-гигиенические условия работы. Недостатками кокильного литья являются невысокая стойкость форм, высокая стоимость их изготовления при отливке чугунных и стальных деталей, отбел и неоднородность структуры металла по сечению отливки. Для ликвидации отбела применяют защитные покрытия в виде обмазок, красок, припыленного ферросилиция, наносимых перед заливкой на рабочую поверхность кокиля, а также выбивку горячих деталей при температуре более 700 °С и перенос их в условия медленного охлаждения (печь, колодец, песок), отжиг в печи.
Стойкость кокиля является наиболее важным фактором, определяющим рентабельность и области применения данного способа. Стойкость форм при литье цинка, алюминия и магния измеряется сотнями тысяч отливок, количество отливок из чугуна составляет 1500—2000 шт., из стали — 600—700 шт. Если для цветных сплавов выгодно изготовлять металлические формы сложной конфигурации, то для отливок из чугуна и стали следует ограничиваться выбором несложных деталей, так как в противном случае значительные затраты и высокая стоимость кокилей приводят к нерентабельности литья. Наиболее выгодным является кокильное литье алюминиевых сплавов, так как оно, улучшая структуру отливок, является эффективным методом борьбы с газовой и усадочной пористостью этих сплавов.
Большое влияние на свойства чугуна и других металлов оказывает температура заливки кокиля. С повышением температуры заливки увеличивается жидкотекучесть металла, лучше заполняются тонкостенные формы, но снижается стойкость кокиля, усиливаются его коробление и разгар. Изменение температуры заливки влияет на скорость кристаллизации и охлаждения отливок. Чем ниже температура заливки, тем больше скорость охлаждения и более мелкозернистой получается структура металла. Но наряду с положительным влиянием увеличение скорости охлаждения повышает отбел чугуна вследствие образования цементита. Для чугуна желательная высокая температура заливки. Это способствует разогреву кокиля, замедлению процесса кристаллизации, уменьшению отбела и удалению растворимых газов. Рекомендуемая температура заливки серого чугуна в кокиль составляет 1350—1260 °С в зависимости от толщины стенок отливки.
Литьё цветных металлов под давлением
Развитие методов литья в металлические формы под давлением вызвано большим спросом на изделия из легких и цинковых сплавов. Этим способом отливают примерно 50% всего фасонного литья из алюминиевых и до 95% из цинковых сплавов. Отливают также магниевые сплавы и латуни, но в меньших количествах. Машины литья под давлением, применяемые в настоящее время для изготовления изделий из цветных сплавов, подразделяют на машины с горячей камерой прессования и с холодной.
Рис. 1 Схема машины литья под давлением (ЛПД) с горячей камерой для прессования
1 — обогрев пламенем от форсунки; 2 — котёл с расплавленным металлом; 3 — отверстие; 4 — поршень; 5 — мундштук; 6 — разъёмная пресс-форма; 7 — подвижная часть пресс-формы; 8 — неподвижная часть пресс-формы
Принципиальная схема устройства машины с горячей камерой прессования (поршневого действия) приведена на рис. 1. Она состоит из обогреваемого чугунного котла, составляющего конструктивно одно целое с камерой прессования (камеры можно также выполнять отдельно от котла). Когда поршень 4 находится в верхнем положении, металл через отверстие поступает в цилиндр а и металлопровод б. При перемещении поршня вниз металл, находящийся в цилиндре и в изогнутой трубе (металлопроводе), поступает через мундштук 5 в пресс-форму. Такие машины в основном применяют для сплавов, имеющих низкую температуру плавления (300—400° С), например, для сплавов на оловянной, свинцовой и цинковой основах.
Алюминиевые сплавы не отливают на этих машинах, так как они имеют относительно высокую температуру плавления, а также вследствие того, что железо растворяется в алюминии, в результате может происходить заедание поршня в цилиндре и имеет место загрязнение сплава.
Рис. 2 Схема машины литья под давлением с холодной камерой прессования
1 — пресс-форма; 2 — цилиндр камеры прессования; 3 — прессующий поршень; 4 — отверстие для заливки порции металла в цилиндр
Более удобны в работе машины с холодной камерой прессования, принципиальная схема которой приведена на рис. 2. В цилиндр машины вручную специальной мерной ложкой или с помощью автоматического дозатора заливают порцию расплавленного металла, достаточную для заполнения полости пресс-формы, после чего поршень под действием гидравлического давления перемещается влево и запрессовывает металл в пресс-форму.
Имеются машины с горизонтальной и вертикальной камерой прессования. Усилие прессования на этих машинах от 120 до 140 Мн/м2 (1400 кГ/см2).
Машины с холодной камерой прессования применяют для литья цинковых, алюминиевых, магниевых и медных сплавов. Средняя производительность машин с горячей камерой прессования 100—200 ударов в час, а машин с холодной камерой — 50—180 ударов в час.
Пресс-формы изготовляют из сталей (углеродистых и жаропрочных типа ЗХ2В8, ЭИ121 и др.). Сложные формы состоят из корпуса и нескольких съемных вставок, что облегчает изготовление, ремонт пресс-форм и улучшает их смену после износа по частям. Вставки могут быть литыми, что удешевляет их стоимость и повышает стойкость. Средняя стойкость форм при работе на цинковых сплавах 150—250 тыс. ударов, на алюминиевых 50 тыс. ударов, магниевых 60—80 тыс. ударов и медных 2—10 тыс. ударов.
Температура заливки различных сплавов следующая: для цинковых сплавов 400—450° С, алюминиевых 660—750° С, магниевых 700—780° С, латуней 950—1020° С. Чтобы получить высококачественную плотную отливку и увеличить стойкость пресс-форм стремятся к минимально возможным температурам заливки. Чем отливка сложнее и стенки ее тоньше, тем температуру расплава следует держать более высокой.
Наиболее хорошие результаты получают при изготовлении этим методом деталей с небольшой и равномерной по всем сечениям толщиной стенок. Особенности этого метода (принудительная подача расплава в форму) позволяют получать изделия с толщиной стенок до 0,5—1 мм.
Наличие в деталях местных скоплений металла затрудняет получение качественных отливок вследствие появления в этих местах усадочных пороков, так как устроить питание от прибылей трудно, а давления не хватает, чтобы запрессовывать образующиеся при затвердевании отливки усадочные пороки.
Температура нагрева пресс-форм зависит от сложности и толщины тела отливки. Если отливка имеет тонкие стенки (2—2,5 мм), то температура формы должна быть выше. Однако чрезмерный нагрев формы приводит к привару и снижению прочности литого изделия. Заниженная температура вызывает массовый брак по недоливам и воздушным включениям (пузырям). При литье цинковых сплавов температуру формы поддерживают в пределах 180—250° С, при литье алюминиевых сплавов 120—280° С, а при литье медных 300—400° С.
Перед началом, а также и во время работы рабочую поверхность пресс-формы покрывают смазкой. Смазка частично предохраняет форму от термического удара и, следовательно, увеличивает сроки службы формы, она способствует более легкому извлечению отливки из формы, предохраняя форму от приваривания. Смазка помогает получить также более качественную поверхность отливки.
При литье под давлением применяют в основном жирные смазки на основе минеральных масел, которые при сгорании не дают минеральных осадков. При литье алюминиевых сплавов применяют смесь масла с графитом или смесь графита с воском и вазелином и др. Смазку наносят тонким, ровным слоем через 1—2 заливки. Для получения качественного изделия необходимо соблюдать определенные значения удельного давления прессования. Повышение давления вызывает уплотнение отливки. Практически при литье цинковых сплавов удельное давление в настоящее время применяют до 35 Мн/м2 (350 кГ/см2), для алюминиевых сплавов до 60 Мн/м2 (600 кГ/см2), для латуней 100 Мн/м2 (1000 кГ/см2). Увеличение удельных давлений до 150—250 Мн/м2 (1500—2500 кГ/см2) считается полезным, так как происходит дополнительное уплотнение металла, повышается прочность и плотность изделия, особенно если заливаемый сплав имеет широкий интервал кристаллизации и склонен к рассеянной пористости.
Важнейшие достоинства литья под давлением следующие: возможность получения тонкостенных отливок сложной конфигурации, высокая точность размеров и высокая чистота поверхности, позволяющая исключить или свести к минимуму механическую обработку, самая высокая производительность из всех известных методов литья, что делает этот способ незаменимым при массовом производстве отливок.
Однако более широкое применение литья под давлением ограничивается тем, что металл при заполнении полостей пресс-форм захватывает воздух, и отливки имеют значительно рассеянную газовую пористость. Однако в последнее время эти трудности начинают преодолевать, для чего помещают пресс-формы в герметические камеры, из которых удаляется воздух.
Поэтому, как правило, отливки, полученные методом литья под давлением, применяют без последующей механической обработки. Если же механическая обработка необходима, то припуск не должен превышать 0,3—0,5 мм, так как механической обработкой снимается наиболее прочная наружная литейная корка, под которой могут вскрываться мелкие пузыри.
Рис. 3 Схема штамповки металла из жидкого состояния
а — заливка дозированной порции металла; б — прессование; в — извлечение готовой; 1 — пресс-форма; 2 — металл; 3 — ложка; 4 — пуансон; 5 — деталь
Этого серьезного недостатка можно избежать при получении изделий методом штамповки из жидкого металла на гидравлических специализированных прессах. Сущность метода заключается в следующем (рис. 3): в металлическую форму, состоящую из неподвижной части пресс-формы и подвижного пуансона, укрепленных на гидравлическом или фрикционном прессах, заливают мерную порцию жидкого металла.
Затем приводят в движение пуансон, который медленно входит в жидкий металл и производит выдавливание жидкого металла в полость формы, образуемой неподвижной пресс-формой и пуансоном, т. е. происходит формообразование отливки. Вслед за этим, когда металл уже почти полностью затвердеет и находится в пластическом состоянии, происходит его пластическая деформация под давлением. В результате этого отливка получается плотной, с чистой поверхностью и с высокими механическими свойствами. Захвата воздуха, наблюдаемого при прессовании на машинах литья под давлением при штамповке из жидкого металла, не наблюдается из-за сравнительно медленного движения пуансона.
Преимущества этого способа заключаются также в том, что выход годных отливок достигает 90—98%; так как нет необходимости в литниковой системе и прибылях.
Производство отливок из сплавов цветных металлов
ВВЕДЕНИЕЛитейное производство — одно из древнейших ремёсел, освоенных человечеством. Первым литейным материалом была бронза. В древности бронзы представляли собой сложные сплавы на основе меди с добавками олова (5-7 %), цинка (3-5 %), сурьмы и свинца(1-3%) с примесями мышьяка, серы, серебра (десятые доли процента). Зарождение выплавки бронзы и получения из нее литых изделий (оружия, украшения, посуды и др.) в разных регионах относится к ,3—7 тысячелетию до и, э. По-видимому, почти одновременно была освоена плавка самородных серебра, золота и их сплавов. На территории, где жили восточные славяне, развитое литейное ремесло появилось в первых веках н. э.
Основными способами получения отливок из бронзы и сплавов серебра и золота были литье ij каменные формы и литье по воску. Каменные формы делали из мягких пород известняка, в которых вырезали рабочую полость. Обычно каменные формы заливали в открытую, так что одна сторона изделия, образуемая открытой поверхностью расплава, оказывалась плоской. При литье по воску сначала изготовляли восковые модели как точные копии будущих изделий. Эти модели погружали в жидкий глиняный раствор, который затем высушивали н обжигали. Воск выгорал, в образовавшуюся полость заливали расплав.
Большой шаг вперед в развитии бронзового литья был сделан, когда началось литье колоколов и пушек (XV—XVI вв.). Широко известно мастерство и искусство русских умельцев, изготовивших уникальные бронзовые отливки — «Царь-пушку» массой 40 т (Андрей Чохов, 1586 г.), и «Царь-колокол» массой 200 т (Иван и Михаил Моторины, 1736 г.).
Бронзы и позже латуни на протяжении многих веков были главным материалом для изготовления художественных отливок, памятников и скульптур. До наших дней сохранилась бронзовая скульптура римского императора Марка Аврелия (II век н, э.). Всемирную известность получили отлитые из бронзы памятники Петру 1 в Ленинграде (1775 г.) и памятник «Тысячелетие России» в Новгороде (1862 г.). В наше время был изготовлен литой бронзовый памятник Юрию Долгорукому — основателю Москвы (1954 г. ).
В XVIII в. на первое место по массовости и универсальности выходит новый литейный материал — чугун, послуживший основой развития машинной индустрии в первой половине XIX в, К началу XX в. литейное производство цветных металлов и сплавов заключалось в получении фасонных отливок из оловянных бронз и латуней и слитков из меди, бронзы и латуней. Фасонные отливки изготовляли только литьем в песчаные формы (тогда говорили и писали «земляные формы», «литье в землю»). Слитки получали массой не более 200 кг литьем в чугунные изложницы.
Следующий этап развития литейного производства цветных металлов и сплавов начался примерно с 1910—1920 гг., когда были разработаны новые сплавы, прежде всего на основе алюминия и несколько позже на основе магния. Одновременно началось освоение фасонного и заготовительного литья из специальных бронз и латуней — алюминиевых, кремниевых, марганцевых, никелевых, а также освоение производства слитков из никеля и его сплавов. В 1920—1930 гг. создаются цинковые сплавы для литья под давлением. В 1930—1940 гг. получает развитие фасонное литье из никелевых сплавов. Период 1950—1970 гг. был ознаменован разработкой технологии плавки и литья титана и его сплавов, урана и других радиоактивных металлов, циркония и сплавов на его основе, молибдена, вольфрама, хрома, ниобия, бериллия и редкоземельных металлов.
Освоение новых сплавов потребовало коренной перестройки технологии плавки и плавильного оборудования, применения новых формовочных материалов и новых способов изготовления форм. Массовый характер производства способствовал разработке новых принципов организации производства, основанных на широкой механизации и автоматизации процессов изготовления форм и стержней, плавки, заливки форм, обработки отливок.
Необходимость обеспечения высокого качества литых заготовок привела к глубоким научным исследованиям свойств жидких металлов, процессов взаимодействия расплавов с газами, огнеупорными материалами, шлаками и флюсами, процессов рафинирования от включений и газов, процессов кристаллизации металлических сплавов при очень малых и очень больших скоростях охлаждения, процессов заполнения
литейных форм расплавом, затвердевания отливок с сопутствующими явлениями — объемной и линейной усадкой, возникновением различной структуры, ликвацией, напряжениями. Начало этим исследованиям было положено в 1930—1940 гг. акад. А. А. Бочваром, заложившим основы теории литейных свойств сплавов.
Начиная с 1920—1930 гг. для плавки цветных [металлов и сплавов широко применяют электрические печи — сопротивления, индукционные канальные и тигельные. Плавка тугоплавких металлов практически оказалась возможной только при использовании дугового разряда в вакууме и электронно-лучевого нагрева. В настоящее время идет освоение плазменной плавки, на очереди — плавка лазерным лучом.
В 1940—1950 гг. произошел массовый переход от литья в песчаные формы к литью в металлические формы — кокили (алюминиевые сплавы, магниевые и медные) к литью под давлением (цинковые, алюминиевые, магниевые сплавы, латуни). В эти же годы в связи с производством литых турбинных лопаток из жаропрочных никелевых сплавов возродился на новой основе древний способ литья по воску, названный точным литьем и называемый теперь литьем по выплавляемым моделям. Этот способ обеспечил получение отливок с очень небольшими припусками на механическую обработку вследствие очень точных размеров и высокой чистоты поверхности, что было необходимо в связи с крайне трудной обрабатываемостью всех жаропрочных сплавов на никелевой и кобальтовой основах.
В заготовительном литье (получение слитков для последующего деформирования с целью изготовления полуфабрикатов) в 1920—1930 гг. вместо чугунных начали широко использовать водоохлаждаемые изложницы, В 1940—1950 гг. происходит внедрение полунепрерывного и непрерывного литья слитков из алюминиевых, магниевых, медных и никелевых сплавов.
В 1930—1940 гг. произошли коренные изменения в принципах построения технологии заливки литейных форм и затвердевания отливок. Эти изменения были обусловлены как резким отличием свойств новых литейных сплавов от свойств традиционного серого чугуна и оловянной бронзы (образование прочных оксидных плен, большая объемная усадка, меняющийся от сплава к сплаву интервал кристаллизации), так и возросшим уровнем требований к отливкам по прочности, плотности и однородности.
Были разработаны конструкции новых расширяющихся литниковых систем в отличие от старых сужающихся. В расширяющихся системах площади поперечного сечения каналов увеличиваются от стояка к литникам-питателям, так что самым узким местом является сечение стояка на переходе к шлаковику-коллектору. В этом случае первые порции металла, вытекающие из стояка в шлаковик, не могущего заполнить, Истечение расплава из шлаковика в литники происходит под действием очень небольшого напора в незаполненном шлаковике. Этот небольшой напор создает соответственно небольшую линейную скорость поступления расплава в полость литейной формы. Струи расплава в форме не разбиваются на капли, не, захватывают воздух; но разрушается оксидная плена на поверхности расплава в форме, расплав не загрязняется пленами. Благодаря таким достоинствам расширяющихся литниковых систем их применяют в настоящее время для получения ответственных отливок из всех сплавов,
Другим важным достижением в технологии получения качественных отливок развитым и реализованным в период освоения фасонного литья из новых сплавов цветных металлов, является принцип направленного затвердевания отливок. Опыт, накопленный при получении отливок из традиционных, «старых» литейных сплавов — серого чугуна и оловянной бронзы, свидетельствовал о том, что не обходимо рассредоточить подвод расплава в литейную форму, обеспечивая в первую очередь надежное заполнение полости формы и не допуская местного ее разогрева. Объем серого чугуна почти не меняется при кристаллизации, и поэтому отливкам из этого сплава практически не поражаются усадочной пористостью или раковина `i`e и не нуждаются в прибылях.
«Старые» оловянные бронзы с 8—10 % олова имели очень большой интервал) кристаллизации, поэтому при литье в песчаные формы вся объемная усадка в отливках проявлялась в виде мелкой рассеянной пористости, неразличимой простым глазом. Создавалось впечатление, что металл в отливке плотный и что использовании опыта получения чугунных отливок, с подводом металла к тонким частям ее, оправдывает себя и в случае литья изделий из бронзы. Прибыли как технологические приливы на отливках просто не существовали. В форме предусматривался лишь выпор — вертикальный канал из полости формы, появление расплава в котором служило признаком заполнения литейной формы.
Для получения отливок высокого качества из новых сплавов оказалось необходимым осуществить направленное затвердевание от тонких частей, которые, естественно, затвердевают первыми, к более массивным и далее к прибылям. При этом убыль объема при кристаллизации каждого ранее затвердевающего участка восполняется расплавом из участка, еще не начавшего затвердевать, и, наконец, из прибылей, которые затвердевают последними. Такое направленное затвердевание требует очень грамотного выбора места подвода расплава в форму. Нельзя подводить расплав в самый тонкий по сечению участок, рациональнее осуществить подвод жидкого металла около прибыли с тем, чтобы в ходе заполнения эта часть формы разогрелась. Для создания направленного затвердевания необходимо намеренно замораживать те части формы, где затвердевание должно произойти быстрее. Это достигается с помощью холодильников в песчаных формах или специальным охлаждением в металлических формах. Там, где затвердевание должно совершаться в последнюю очередь, форму намеренно утепляют или разогревают.
Принцип направленного затвердевания, осознанный и сформулированный при освоении производства отливок из алюминиевых и магниевых сплавов, сейчас совершенно обязателен для получения качественных отливок из любых сплавов.
Разработка научных основ плавки сплавов цветных металлов, их кристаллизации, освоение технологии получения фасонных отливок и слитков является заслугой большой группы ученых, многие из которых были тесно связаны с высшей школой. К ним в первую очередь следует отнести А. А. Бочвара, С. М. Воронова, И. Е. Горшкова, И. Ф. Колобнева, Н. В. Окромешко, А. Г. Спасского, М. В. Шарова.
Научные разработки и производственные процессы в области литейного производства цветных металлов в нашей стране соответствуют передовым достижениям научно-технического прогресса. Их результатом, в частности, явилось создание современных цехов кокильного литья и литья под давлением на Волжском автомобильном заводе и ряде других предприятий. На Заволжском моторном заводе успешно работают крупные машины литья под давлением и усилием запирания пресс-формы 35 МН, на которых получают блоки цилиндров из алюминиевых сплавов для автомашины «Волга». На Алтайском моторном заводе освоена автоматизированная линия по получению отливок литьем под давлением. В Советском Союзе впервые в мире разработан и освоен процесс непрерывного литья слитков из алюминиевых сплавов в электромагнитный кристаллизатор. Этот способ существенно повышает качество слитков и позволяет снизить количество отходов в виде стружки при их обточке.
Основная задача, стоящая перед литейным производством в нашей стране, заключается в существенном общем повышении качества отливок, которое должно найти выражение в уменьшении толщины стенок, снижении припусков на механическую обработку и на литниково-питающие системы при сохранении должных эксплуатационных свойств изделий. Конечным итогом этой работ))» должно быть обеспечение возросших потребностей машиностроения необходимым количеством литых заготовок без существенного роста общего выпуска отливок но массе.
Проблема повышения качества отливок тесно связана с проблемой экономного расходования металла. Применительно к цветным металлам обе эти проблемы приобретают особую остроту. В связи с истощением богатых месторождений цветных металлов стоимость их производства непрерывно и существенно возрастает. Сейчас цветные металлы в пять—десять и более раз дороже чугуна и углеродистой стали. Поэтому экономное расходование цветных металлов, сокращение потерь, разумное использование отходов является непременным условием развития литейного производства.
В промышленности постоянно увеличивается доля сплавов цветных металлов, получаемых путем переработки отходов — обрези, стружки, различного лома и шлаков. Эти сплавы содержат повышенное количество разнообразных примесей, способных снизить их технологические свойства и эксплуатационные характеристики изделий. Поэтому в настоящее время ведутся широких исследования для выработки способов рафинирования подобных расплавов и отработки технологии получения качественных литых заготовок.
ТРЕБОВАНИЯ К ОТЛИВКАМ
Отливки из сплавов цветных’ металлов должны иметь определенный химический со став, заданный уровень механических свойств, необходимые размерную точность и чистоту поверхности без внешних и внутренних дефектов. В отливках не допускаются трещины, неслитины, сквозные раковины и рыхлоты. Поверхности, являющиеся базами для механической обработки, не должны иметь наплывов и повреждений. Допустимые дефекты, их количество, способы обнаружения и методы исправления регламентируются отраслевыми стандартами (ОСТами) и техническими условиями.
Отливки поставляют с обрубленными литниками и обрезанными прибылями. Места обрезки и обрубки на необрабатываемых поверхностях зачищают заподлицо. Допускается исправление дефектов заваркой и пропиткой. Необходимость термической обработки определяется техническими условиями.
Точность размеров отливок должна отвечать требованиям ОСТ 1.41154—72. Допуски, включающие в себя сумму всех отклонений от размеров чертежа, имеющих место на различных стадиях изготовления отливки, кроме отклонений, обусловленных наличием литейных уклонов, должны соответствовать одному из семи классов точности (табл. 20). В каждом классе точности все допуски на любой размер одного вида (Д,Т или М) являются для данной отливки равными и устанавливаются по наибольшему габаритному размеру.
Обрабатываемые поверхности отливок должны иметь припуск на механическую обработку. Минимальный припуск должен быть больше допуска. Величина припуска определяется габаритными размерами и классом точности отливок.
Чистота поверхности отливок должна соответствовать заданному классу шероховатости. Она зависит от способа изготовления отливок, применяемых материалов для изготовления форм, качества подготовки поверхности моделей, кокилей и пресс-форм. Для получения отливок, отвечающих перечисленным выше требованиям, применяют различные способы литья в разовые формы и формы многократного использования.
КЛАССИФИКАЦИЯ ОТЛИВОК
По условиям службы независимо от способа изготовления отливки делят на три группы: общего, ответственного и особо ответственного назначения.
К группе общего назначения относят отливки для деталей, не рассчитываемых на прочность. Конфигурация и размеры их определяются только конструктивными и технологическими соображениями. Такие отливки не подвергают контролю рентгенопросвечиванием.
Отливки ответственного назначения используют для изготовления деталей, рассчитываемых на прочность и работающих при статических нагрузках. Они проходят выборочный контроль рентгенопросвечиванием.
К группе особо ответственного назначения относят отливки для деталей, рассчитываемых на прочность и работающих при циклических и динамических нагрузках. Их подвергают индивидуальному контролю рентгенопросвечиванием, флуоресцентному контролю и контролю вихревыми токами.
В зависимости от объема приемно-сдаточных испытаний отраслевыми стандартами ОСТ11.90021— 71, ОСТ 1.90016— 72, ОСТ1.90248— 77 предусмотрено деление отливок из сплавов цветных металлов на три группы.
К 1 группе относят отливки, контроль механических свойств которых осуществляют выборочно на образцах, вырезанных из тела контрольных отливок, с одновременным испытанием механических свойств на отдельно отлитых образцах от каждой плавки или поштучное испытание на образцах, вырезанных из прилитых к каждой отливке заготовок, а также поштучный контроль на плотность (рентгенопросвечивание).
Ко II группе относят отливки, механические свойства которых определяют на отдельно отлитых образцах или на образцах, вырезанных из прилитых к отливке заготовок, и по требованию завода-потребителя на образцах, вырезанных из отливок (выборочно), а также поштучный или выборочный контроль на плотность отливок методом рентгенопросвечивания. (Для отливок IIа группы контроль на плотность не производят).
III группу составляют отливки, у которых контролируют только твердость. По требованию завода-потребителя производят контроль механических свойств на отдельно отлитых образцах.
Отнесение отливок к соответствующей группе производится конструктором и оговаривается в чертеже.
В зависимости от способа изготовления, конфигурации поверхностей, масс максимального геометрического размера, толщины стенок, характеристики в ступов, ребер, утолщений, отверстий, количества стержней, характера механической обработки и шероховатости обработанных поверхностей, назначения и особых технических требований предусмотрено деление отливок на 5—6 групп сложное (литье в песчаные формы и под давлением — 6 групп; литье в кокиль, по выплавляемым моделям и в оболочковые формы — 5 групп). При этом число совпадающих признаков должно быть не мен пяти или четырех для шести или пяти групп сложности соответственно. При меньшем числе совпадающих признаков применяют способ группировки их путем последовательного отнесения начиная с более высоких групп сложности в сторону более низких и останавливаются на группе сложности, при которой достигается необходимое число условно совпадающих признаков. При равенстве числа признаков по двум группам сложно отливку относят к той группе, при определении которой использован признак «конфигурация поверхностей».
ОСНОВЫ ТЕХНОЛОГИИ ПЛАВКИ
Располагая сведениями о свойствах материалов и их взаимодействий с газами и огнеупорными материалами, можно создавать научно обоснованную технологию плавки. Разработка технологии плавки для конкретной обстановки включает в себя выбор плавильного агрегата, вида энергии, выбор материала футеровки печи, определение необходимого состава атмосферы в печи при плавке. Создавая технологию, решают вопрос о способах предотвращения возможного загрязнения расплава и способах его рафинирования. Рассматривают также необходимость раскисления и модифицирования сплава.
Очень важным вопросом является правильный выбор шихтовых материалов, т. е. тех материалов, которые подлежат сплавлению. При создании технологии предусматривают также уменьшение расхода металлов, вспомогательных материалов, энергии, труда. Эти вопросы могут быть решены лишь в совершенно конкретной обстановке.
Следует иметь в виду, что приведенные выше сведения о свойствах металлов и протекающих процессах относились к условиям «чистого» эксперимента, когда влияние прочих процессов намеренно сводилось к минимуму. В реальной обстановке это влияние может существенно изменить отдельные свойства. Кроме того, в реальной обстановке расплав как система никогда не находится в равновесии с окружающей средой, он оказывается либо пересыщенным, либо недосыщенным. В связи с этим приобретает большое значение кинетическая сторона процесса. Количественная оценка кинетику весьма затруднительна ввиду неопределенности уравнений, описывающих во времени процессы газонасыщения, дегазации, взаимодействия с футеровкой и т. п. Поэтому в итоге оказывается, что для правильного суждения о протекающих при плавке явлениях важны не только количественные расчеты отдельных процессов, но и возможны более полный учет и оценка наибольшего числа этих процессов.
РАЗРАБОТКА ТЕХНОЛОГИИ ПЛАВКИ
Отправными точками при создании технологии плавки металла или сплава являются его состав, который включает в себя основу, легирующие компоненты и примеси, и заданный уровень механических и других свойств сплава в отливке. Кроме того, учитывается количественная потребность в расплаве в единицу времени. Вид плавильной печи подбирают, исходя из температуры плавления основного компонента сплава и химической активности как его, так и всех легирующих компонентов и наиболее вредных примесей, 0дно-временно решается вопрос о материале футеровки печи.
В большинстве случаев плавку ведут на воздухе. Если взаимодействие с воздухом ограничивается образованием на поверхности нерастворимых в расплаве соединений и возникающая пленка этих соединений существенно замедляет дальнейшее взаимодействие, то обычно не принимают каких-либо мер для подавления такого взаимодействия. Плавку в этом случае ведут при прямом контакте расплава с атмосферой. Так поступают при приготовлении большинства алюминиевых, цинковых, оловянносвинцовых сплавов. Если же образующаяся пленка нерастворимых соединений непрочна и неспособна защитить расплав от дальнейшего взаимодействия (магний
и его сплавы), то принимают специальные меры, используя флюсы или защитную атмосферу.
Защита расплава от взаимодействия с газами совершенно необходима, если газ растворяется в жидком металле. Главным образом стремятся предотвратить взаимодействие расплава с кислородом. Это относится к плавке сплавов на основе никеля и медных сплавов, способных растворять кислород, где расплавы обязательно защищают от взаимодействия с .атмосферой печи. Защита расплава достигается прежде всего применением шлаков, флюсов и других защитных покровов. Если подобные меры оказываются недостаточными или невозможными, прибегают к плавке в атмосфере защитных или инертных газов. Наконец, используют плавку в вакууме, т. е. при пониженном до определенного уровня давлений газов. В некоторых случаях для уменьшения интенсивности взаимодействия расплава кислородом в него вводят добавки бериллия (сотые доли процента в аллюминиевомагниевые и магниевые сплавы), кремния и алюминия (десятые доли процента в латуни).
Несмотря на защиту, металлические расплавы все же загрязняются различными примесями выше допустимого предела. Нередко в шихтовых материалах имеется слишком много примесей. Поэтому часто при плавке проводят рафинирование расплавов — очистку от растворимых и нерастворимых примесей, а также раскисление — удаление растворенного кислорода. Многие сплавы находят применение, в модифицированною состоянии, когда они приобретают мелкокристаллическое строение и более высокие механические или технологические свойства. Операция модифицирования проводится как одна из последних ступеней процесса плавки непосредственно перед разливкой. При разработке технологии плавки учитывают, что масса полученного жидкого металла всегда будет несколько меньше массы металлической шихты из-за потерь металла в шлаке и потерь на угар. Эти потери составляют в сумме 2-5 %, при этом чем больше масса единичной плавки, тем меньше потери.
Шлак, всегда появляющийся на поверхности расплава, представляет собою сложную систему из сплавов-растворов и смесей оксидов основного компонента сплава, легирующих компонентов и примесей. Кроме того, в шлаке обязательно присутствуют оксиды футеровки плавильной печи. Такой естественно возникающий на расплаве первичный шлак может быть полностью жидким, частично жидким (творожистым) и твердым. Кроме оксидов, шлаки всегда содержат некоторое количество свободного металла. В жидких и творожистых шлаках свободный металл находится в виде отдельных капель — корольков. Если же оксиды, составляющие шлак, находятся ниже своей точки плавления, то они являются твердыми. При перемешивании расплава и попытках удаления с него шлака происходит замешивание этих оксидов, часто и имеющих вид плен, в расплав. Таким образом, несмотря на тугоплавкость оксидов, образующийся и удаляемый шлак имеет жидкую консистенцию, которая обусловлена большим количеством захваченного расплава. В таком шлаке количество свободного металла составляет около 50% от всей массы удаляемого шлака, тогда как в действительно жидких шлаках его содержание не превышает 10—30%.
Потери металлов при плавке на угар определяются их испарением и взаимодействием с футеровкой, выражающемся в ее металлизации.
Металл, находящийся в шлаке, может быть возвращен в производство. Наиболее просто это достигается по отношению к свободному металлу, не связанному в какие-либо соединения. Дробление и просев шлака позволяют возвратить 70—80 % свободного металла. Оставшийся шлак представляет собой доброкачественное металлургическое сырье, и его направляют на металлургические предприятия для выделения наиболее ценных компонентов.
При определении потерь металла при плавке на угар и со шлаком нельзя забывать о загрязненности шихтовых материалов инородными неметаллическими примесями и включениями в виде остатков масла, эмульсии, воды, шлака, формовочной и стержневой смесей. Масса этих примесей при невнимательной работе автоматически засчитывается как масса подвергаемого плавке металла, и в итоге получается необоснованно завышенная величина потерь при плавке.
Важной стороной технологии является температурный режим плавки, порядок загрузки шихтовых материалов и введения отдельных компонентов сплава, последовательность технологических операций металлургической обработки расплава. Плавку всегда проводят в предварительно разогретой печи, температура в которой должна быть на 100—200 °С выше температуры плавления основного компонента сплава. Желательно, чтобы все загружаемые в печь материалы были нагреты до 150—200°С с тем, чтобы в них не оставалась влага. Первым в плавильную печь загружают тот шихтовой материал, который составляет наибольшую долю в навеске. В случае приготовления сплава из чистых металлов первым всегда загружают основной компонент сплава. Если плавку ведут с применением шлаков и флюсов, то их обычно засыпают сверху загружаемой металлической шихты. Если условия производства позволяют, новую плавку начинают, оставляя в печи некоторое количество расплава от предыдущей плавки. Загрузка шихты в жидкую ванну существенно ускоряет процесс плавки и снижает потери металла. Сначала в жидкую ванну загружают более тугоплавкую шихту. Периодически добавляют свежий шлак или флюс и, если необходимо, удаляют старый. Если по технологии необходимо раскисление расплава (удаление растворенного кислорода), то его проводят таким образом, чтобы избежать образования в расплаве трудно удаляемых и вредных неметаллических включений и обеспечить надежное удаление продуктов раскисления (см. ниже). В последнюю очередь в расплав вводят летучие и химически активные компоненты сплава, чтобы уменьшить их потери. Затем проводят рафинирование расплава. Непосредственно перед разливкой расплав модифицируют.
Условия введения отдельных видов шихты или компонентов сплава в жидкую ванну целесообразно определять, сопоставляя температуру плавления загружаемого материала и его плотность с температурой плавления и плотностью сплава. Необходимо также знать хотя бы двойные диаграммы состояния основного компонента сплава с легирующими компонентами, примесями и модифицирурующими и добавками.
В подавляющем большинстве случаев все легирующие компоненты и примеси растворяются в жидкой основе сплава, так что расплав можно считать раствором. Однако получение и образование такого раствора осуществляют различными путями. Если очередная твердая добавка будет иметь температуру начала плавления более высокую, чем расплав, то возможно лишь обычное растворение твердого тела в жидком. Для этого необходимо активное принудительное перемешивание. Указанная тугоплавкая добавка может иметь плотность, меньшую плотности расплава, и в этом случае она будет плавать на поверхности, где возможно ее окисление, запутывание в шлак. Отсюда возникает опасность непопадания в заданный состав сплава. Если такая «легкая» добавка имеет меньшую температуру плавления, чем расплав, она переходит в жидкое состояние и поэтому ее даль-дальнейшее растворение в расплаве существенно облегчается. В некоторых случаях, чтобы избежать окисления и потерь, подобные добавки вводят в расплав с помощью так называемого колокольчика— дырчатого стакана, в который закладывают вводимую добавку, и затем погружают в расплав. Если добавка тяжелее расплава, она погружается на дно жидкой ванны, поэтому ее окисление маловероятно. Однако трудно проследить за растворением таких добавок, особенно если они более тугоплавки, чем расплав. Необходимо достаточно длительное и тщательное перемешивание всей массы расплава, чтобы обеспечить полное растворение.
Для приготовления сплавов нередко пользуются лигатурами. Так называют промежуточные сплавы, состоящие обычно из основного компонента рабочего сплава с одним или несколькими легирующими компонентами, но в значительно больших содержаниях, чем в рабочем сплаве. К использованию лигатур приходится прибегать в тех случаях, когда введение компонента-добавки в чистом виде затруднено по различным причинам. Такими причинами могут быть длительность процесса растворения, потери от окисления, испарения, шлакообразования.
Лигатуры используют также при введении химически активных добавок, которые на воздухе в свободном виде могут взаимодействовать с кислородом и азотом. Лигатуры широко используют и в тех случаях, когда чистый элемент-добавка слишком дорог или его вообще не получают, производство же сплавов-лигатур уже освоено, они доступны и достаточно дешевы.
Наконец, лигатуры целесообразно применять при необходимости введения в сплав очень малых добавок. Навеска чистой добавки может составлять всего несколько сот граммов на несколько сот килограммов расплава. Надежно ввести такое малое количество легирующего компонента практически невозможно из-за различного рода потерь и неравномерности распределения. Использование лигатуры, которую вводят в значительно большем количестве, устраняет эти трудности.
Следует отметить, что общим правилом технологии плавки сплавов является как можно меньшее время процесса. Это способствует уменьшению затрат энергии, потерь металла, загрязнения расплава газами и примесями. Вместе с тем необходимо иметь в виду, что для полного растворения всех компонентов и усреднения состава сплава обязательно следует «проварить» расплав — выдержать его при наибольшей допустимой температуре в течение 10—15 мин.
КЛАССИФИКАЦИЯ ПЛАВИЛЬНЫХ ПЕЧЕЙ
В зависимости от масштабов производства, требований, предъявляемых к качеству выплавляемого металла и целого ряда других факторов, в цехах заготовительного и фасонного литья цветных металлов применяют различные типы плавильных печей.
По виду используемой для плавки сплавов энергии все плавильные печи делят на топливные и электрические. Топливные печи подразделяют на тигельные, отражательные и шахтно-ванные. Электрические печи классифицируют в зависимости от способа преобразования электрической энергии в тепловую. В литейных цехах применяют печи сопротивления, индукционные, электродуговые, электронно-лучевые и плазменные.
В электрических печах сопротивления нагрев и расплавление шихты осуществляются за счет тепловой энергии, поступающей от электронагревательных элементов, установленных в своде или в стенках плавильной печи. Эти печи применяют для плавки алюминиевых, магниевых, цинковых, оловянных и свинцовых сплавов. 6 пер/с] и промышленной частоты (50 пер/с).
Независимо от частоты питающего тока принцип работы всех индукционных тигельных печей основан на индуктировании электромагнитной энергии в нагреваемом металле (токи Фуко) и превращении ее в тепловую. При плавке в металлических или других тиглях, изготовленных из электропроводных материалов, тепловая энергия передается к нагреваемому металлу также стенками тигля. Индукционные тигельные печи применяют для плавки алюминиевых, магниевых, медных, никелевых сплавов, а также сталей и чугунов.
Индукционные канальные печи используют для плавки алюминиевых, медных, никелевых и цинковых сплавов. Помимо плавильных печей, применяют также индукционные канальные миксеры, служащие для рафинирования и поддержания температуры жидкого металла на заданном уровне. Плавильно-литейные комплексы, состоящие из плавильной печи — миксера — литейной машины, используют при литье слитков из алюминиевых, магниевых и медных сплавов непрерывным методом. Принцип тепловой работы канальных индукционных печей аналогичен принципу работы силового электрического трансформатора тока, состоящего, как известно, из первичной катушки, магнитопровода и вторичной катушки. Роль вторичной катушки в печи играет короткозамкнутый канал, заполненный жидким металлом. При пропускании тока через индуктор печи (первичная катушка) в заполненном жидким металлом канале индуцируется электрический ток большой величины, который разогревает находящийся в нем жидкий металл. Тепловая энергия, выделяемая в канале, нагревает и расплавляет металл, находящийся над каналом в ванне печи.
Электродуговые печи по принципу передачи тепла от электрической дуги к нагреваемому металлу подразделяются на печи прямого и косвенного нагрева.
В печах косвенного нагрева большая часть тепловой энергии от горячей дуги передается к нагреваемому металлу излучением, а в печах прямого действия — излучением и теплопроводностью. Печи косвенного действия применяют в настоящее время ограниченно. Печи прямого действия (электродуговые вакуумные с расходуемым электродом) используют для плавки тугоплавких, химически активных металлов и сплавов, а также легированных сталей, никелевых и других сплавов. -3 Па. Электронно-лучевую плавку используют для получения слитков, и фасонных отливок. При электроннолучевой плавке можно значительно перегревать жидкий металл и длительное время выдерживать его в жидком состоянии. Это преимущество позволяет эффективно рафинировать расплав и очищать его от ряда примесей. С помощью электронно-лучевой
Плавки из металла могут быть удалены все примеси, давление пара которых существенно превышает давление пара основного металла. Высокая температура и глубокий вакуум способствуют также очистке металла от примесей за счет термической диссоциации оксидов нитридов и других соединений, находящихся в металле. Печь электрошлакового переплава ЭШП по принципу работы Представляет собой печь сопротивления косвенного нагрева, в которой источником тепла является ванна расплавленного шлака заданного химического состава. Переплавляемый металл в виде расходуемого электрода погружают в слой (ванну) жидкого электропроводного шлака. Через расходуемый электрод и шлак пропускают электрический ток. Шлак разогревается, торец расходуемого электрода оплавляется и капли жидкого металла, проходя через слой химически активного шлака, очищаются в результате контакта с ним и формируются в изложнице в виде слитка. Шлак защищает жидкий металл- от взаимодействия с атмосферой воздуха. Печи ЭШП в основном применяют для получения слитков из высококачественных сталей, жаропрочных, нержавеющих и других сплавов. Метод ЭШП используют также для производства крупных фасонных отливок: коленчатых валов, корпусов, арматуры и других изделий.
В плазменных плавильных печах источником тепловой энергии является поток нагретого до высокой температуры ионизированного газа (плазменная дуга), который при соприкосновении с металлом нагревает и расплавляет его. Для получения потока плазмы плавильные печи оборудуют специальными устройствами — плазмотронами. Плазменный способ нагрева и плавления сплавов применяют в печах ванного типа, в плавильных установках для получения слитков в кристаллизаторе и для плавки металлов в гарнисажном тигле.
Плазменные печи ванного типа в основном применяют для плавки сталей, а также сплавов на основе никеля. Плазменные печи для плавки в кристаллизаторе могут использоваться для получения слитков из сталей, бериллия, молибдена, ниобия, титана и других металлов. Плазменные печи для плавки в гарнисажном тигле предназначены для фасонного литья сталей, тугоплавких и химически активных металлов.
ПРОИЗВОДСТВО ОТЛИВОК ИЗ АЛЛЮМИНИЕВЫХ СПЛАВОВ
Литье в песчаные формы
Из перечисленных выше способов литья в разовые формы наиболее широкое применение при изготовлении отливок из алюминиевых сплавов получило литье в сырые песчаные формы. Это обусловлено невысокой плотностью сплавов, небольшим силовым воздействием металла на форму и низкими температурами литья (680—800С).
Для изготовления песчаных форм используют формовочные и стержневые смеси, приготовленные из кварцевых и глинистых песков (ГОСТ 2138—74), формовочных глин (ГОСТ 3226—76), связующих и вспомогательных материалов. Выполнение полостей в отливках осуществляют с помощью стержней, изготавливаемых в основном по горячим (220—300 °С) стержневым ящикам. Для этой цели используют плакированный кварцевый песок или смесь песка с термореактивной смолой и катализатором. Для изготовления стержней широко используют однопозиционные пескострельные автоматы и установки, а также карусельные многопозиционные установки. Стержни, подвергающиеся сушке, изготавливают на встряхивающих, пескодувных и пескострельных машинах или вручную из смесей масляными (4ГУ, С) или водорастворимыми связующими. Продолжительность сушки (от 3 до 12 ч) зависит от массы и размеров стержня и определяется обычно опытным путем. Температуру сушки назначают в зависимости от природы связующего: для масляных связующих 250—280 °С, а для водорастворимых 160—200 °С. Для изготовления крупных массивных стержней все большее применение получают смеси холодного твердения (ХТС) или жидкодвижные самотвердеющие смеси (ЖСС). Смеси холодного твердения в качестве связующего содержат синтетические смолы, а катализатором холодного твердения обычно служит ортофосфорная кислота.
Смеси ЖСС содержат поверхностно-активное вещество, способствующее образованию пены.
Соединение стержней в узлы производят склейкой или путем заливки алюминиевых расплавов в специальные отверстия в знаковых частях. Усадка сплава при охлаждении обеспечивает необходимую прочность соединения.
Плавное без ударов и завихрений заполнение литейных форм обеспечивается применением расширяющихся литниковых систем с соотношением площадей сечений основных элементов Fст : Fшп : Fпит 1:2:3; 1:2:4; 1:3:6 соответственно для нижнего, щелевого или многоярусного подвода металла к полости литейной формы. Скорость подъема металла в полости литейной формы не должна превышать 4,5/6, где 6 — преобладающая толщина стенок отливки, см. Минимальную скорость подъема металла в форме (см/с) определяют по формуле А. А. Лебедева Vmin = 3/§.
Тип литниковой системы выбирают с учетом габаритов отливки, сложности ее конфигурации и расположения в форме. Заливку форм для отливок сложной конфигурации небольшой высоты осуществляют, как правило, с помощью нижних литниковых систем. При большой высоте отливок и тонких стенках предпочтительно применение вертикально-щелевых или комбинированных литниковых систем. Формы для отливок малых размеров допустимо заливать через верхние литниковые системы. При этом высота падения струп металла в полость формы не должна превышать 80 мм.
Для уменьшения скорости движения расплава при входе в полость литейной формы и лучшего отделения взвешенных в нем оксидных плен и шлаковых включений в литниковые системы вводят дополнительные гидравлические сопротивления — устанавливают сетки (металлические или из стеклоткани) или ведут заливку через зернистые фильтры.
Литники (питатели), как правило, подводят к тонким сечениям (стенкам) отливок рассредоточенно по периметру с учетом удобств:» их последующего отделения при обработке. Подвод металла в массивные узлы недопустим, так как вызывает образование в них усадочных раковин, макрорыхлот и усадочных «провалов» на поверхности отливок. В сечении литниковые каналы чаще всего имеют прямоугольную форму с размером широкой стороны 15—20 мм, а узкой 5—7 мм.
Сплавы с узким интервалом кристаллизации (АЛ2, АЛ4, АЛ), АЛ34, АК9, АЛ25, АЛЗО) предрасположены к образованию концентрированных усадочных раковин в тепловых узлах отливок. Для выведения этих раковин за пределы отливок широко используют установку массивных прибылей. Для тонкостенных (4—5 мм) и мелких отливок масса прибыли в 2—3 раза превышает массу отливок, для толстостенных—до 1,5 раз. Высоту прибыли выбирают в зависимости от высоты отливки. При высоте менее 150 мм высоту прибыли Нприб принимают равной высоте отливки Нотл. Для более высоких отливок отношение Нприб/Нотл принимают равным 0,3 0,5. Соотношение между высотой прибыли и ее толщиной составляет в среднем 2—3. Наибольшее применение при литье алюминиевых сплавов находят верхние открытые прибыли круглого или овального сечения; боковые прибыли в большинстве случаев делают закрытыми. Для повышения эффективности работы прибылей их утепляют, заполняют горячим металлом, доливают. Утепление обычно осуществляют наклейкой на поверхность формы листового асбеста с последующей подсушкой газовым пламенем. Сплавы с широким интервалом кристаллизации (АЛ1, АЛ7, АЛ8, АЛ19, АЛЗЗ) склонны к образованию рассеянной усадочной пористости. Пропитка усадочных пор при помощи прибылей малоэффективна. Поэтому при изготовлении отливок из перечисленных сплавов не рекомендуется применять установку массивных прибылей. Для получения высококачественных отливок осуществляют направленную кристаллизацию, широко используя для этой цели установку холодильников из чугуна и алюминиевых сплавов. Оптимальные условия для направленной кристаллизации создает вертикально-щелевая литниковая система. Для предотвращения газовыделения при кристаллизации и предупреждения образования газо-усадочной пористости в толстостенных отливках широко используют кристаллизацию под давлением 0,4—0,5 МПа. Для этого литейные формы перед заливкой помещают в автоклавы, заливают их металлом и кристаллизуют отливки под давлением воздуха. Для изготовления крупногабаритных (высотой до 2—3 м) тонкостенных отливок используют метод литья с последовательно направленным затвердеванием.
Сущность метода состоит в последовательной кристаллизации отливки снизу вверх. Для этого литейную форму устанавливают на стол гидравлического подъемника и внутрь ее опускают нагретые до 500—700 °С металлические трубки диаметром 12—20 мм, выполняющие функцию стояков. Трубки неподвижно закрепляют в литниковой чаше и закрывают отверстия в них стопорами. После заполнения литниковой чаши расплавом стопоры поднимают и сплав по трубкам поступает в литниковые колодцы, соединенные с полостью литейной формы щелевыми литниками (питателями). После того как уровень расплава в колодцах поднимается на 20—30 мм выше нижнего конца трубок, включают механизм опускания гидравлического стола. Скорость опускания принимают такой, чтобы заполнение формы осуществлялось под затопленный уровень и горячий металл непрерывно поступал в верхние части формы. Это обеспечивает направленное затвердевание и позволяет получать сложные отливки без усадочных дефектов.
Заливку песчаных форм металлом ведут из ковшей, футерованных огнеупорным материалом. Перед заполнением металлом ковши со свежей футеровкой сушат и прокаливают при 780—800 °С для удаления влаги. Температуру расплава перед заливкой поддерживаю на уровне 720—780 °С. Формы для тонкостенных отливок заполняют расплавами, нагретыми до 730—750 °С, а для толстостенных до 700—720 °С.
Литье в гипсовые формы
Литье в гипсовые формы применяют в тех случаях, когда к отливкам предъявляются повышенные требования по точности, чистоте поверхности и воспроизведению мельчайших деталей рельефа. сравнению с песчаными гипсовые формы обладают более высокой прочностью, точностью размеров, лучше противостоят воздействию высоких температур, позволяют получать отливки сложной конфигурации с толщиной стенок 1,5 мм по 5—6-му классу точности. Формы изготавливают по восковым или металлическим (латунь, сталь) хромированным моделям с конусностью по наружным размерам не более 30′ и по внутренним размерам от 30′ до 3°. Модельные плиты выполняют из алюминиевых сплавов. Для облегчения удаления моделей из форм поверхность их покрывают тонким слоем керосиново-стеариновой смазки.
Мелкие и средние формы для сложных тонкостенных отливок изготавливают из смеси, состоящей из 80′ % гипса, 20 % кварцевого песка или асбеста и 60—70 % воды (от массы сухой смеси). Состав смеси для средних и крупных форм: 30 % гипса, 60 % песка, 10% асбеста, 40—50 % воды. Смесь для изготовления стержней содержит 50 % гипса, 40 % песка, 10 % асбеста, 40—50 % воды. замедления схватывания в смесь вводят 1—2 % гашеной извести. Необходимая прочность форм достигается за счет гидратации безводного или полуводного гипса. Для снижения прочности и увеличения газопроницаемости сырые гипсовые формы подвергают гидротермической обработке — выдерживают в автоклаве в течение 6—10 ч под давлением водяного пара 0,13—0,14 МПа, а затем в течение суток на воздухе. После этого формы подвергают ступенчатой сушке при 350-500 °С.
Особенностью гипсовых форм является их низкая теплопроводность. Это обстоятельство затрудняет получение плотных отливок из алюминиевых сплавов с широким интервалом кристаллизации. Поэтому основной задачей при разработке литниково-прибыльной системы для гипсовых форм является предотвращение образования усадочных раковин, рыхлот, оксидных плен, горячих трещин и недоливов тонких стенок. Это достигается применением расширяющихся литниковых систем (Fст : Fшл : EFпит == 1 : 2 : 4), обеспечивающих низкую скорость движения расплавов в полости формы, направленным затвердеванием тепловых узлов в сторону прибылей с помощью холодильников, увеличением податливости форм за счет повышения содержания кварцевого песка в смеси. Заливку тонкостенных отливок ведут в нагретые до 100—-200 °С формы методом вакуумного всасывания, что позволяет заполнять полости толщиной до 0,2 мм. Толстостенные (более 10 мм) отливки получают заливкой форм в автоклавах. Кристаллизация металла в этом случае ведется под давлением 0,4—0,5 МПа.
Литье в оболочковые формы
Литье в оболочковые формы целесообразно применять при серийном и крупносерийном производстве отливок ограниченных размеров с повышенной чистотой поверхности, большей размерной точностью и меньшим объемом механической обработки, чем при литье в песчаные формы.
Оболочковые формы изготавливают по горячей (250—300 °С) металлической (сталь, чугун) оснастке бункерным способом. Модельную оснастку выполняют по 4—5-му классам точности с формовочными уклонами от 0,5 до 1,5 %. Оболочки делают двухслойными: первый слой из смеси с 6—10 % термореактивной смолы, второй из смеси с 2 % смолы. Для лучшего съема оболочки модельную плиту перед засыпкой формовочной смеси покрывают тонким слоем разделительной эмульсии (5 % силиконовой жидкости № 5; 3 % хозяйственного мыла; 92 % воды).
Для изготовления оболочковых форм применяют мелкозернистые кварцевые пески, содержащие не менее 96 % кремнезема. Соединение полуформ осуществляют склеиванием на специальных штыревых прессах. Состав клея: 40 % смолы МФ17; 60 % маршалита и 1,5 % хлористого алюминия (катализатор твердения). Заливку со бранных форм производят в контейнерах. При литье в оболочковые формы применяют такие же литниковые системы и температурные режимы, как и при литье в песчаные формы.
Малая скорость кристаллизации металла в оболочковых формах и меньшие возможности для создания направленной кристаллизации обусловливают получение отливок с более низкими свойствами, чем при литье в сырые песчаные формы.
Литье по выплавляемым моделям
Литье по выплавляемым моделям применяют для изготовления отливок повышенных/точности (3—5-ый класс) и чистоты поверхности (4—6-й класс шероховатости), для которых этот способ является единственно возможным или оптимальным.
Модели в большинстве случаев изготавливают из пастообразных парафино-стеариновых (1 : 1) составов запрессовкой в металлические пресс-формы (литые и сборные) на стационарных или карусельных установках. При изготовлении сложных отливок размерами более 200 мм во избежание деформации моделей в состав модельной массы вводят вещества, повышающие температуру их размягчения (оплавления).
В качестве огнеупорного покрытия при изготовлении керамических форм используют суспензию из гидролизованного этилсиликата (30—-40 %) и пылевидного кварца (70—60 %). Обсыпку модельных блоков ведут прокаленным песком 1КО16А или 1К025А. Каждый слой покрытия сушат на воздухе в течение 10—12 ч или в атмосфере, содержащей пары аммиака, 0,5 1 ч. Необходимая прочность керамической формы достигается при толщине оболочки 4—6 мм (4—6 слоев огнеупорного покрытия). Для обеспечения спокойного заполнения формы применяют расширяющиеся литниковые системы с подводом металла к толстым сечениям и массивным узлам. Питание отливок осуществляют обычно от массивного стояка через утолщенные литники (питатели). Для сложных отливок допускается применение массивных прибылей для питания верхних массивных узлов с обязательным заполнением их из стояка.
Выплавление моделей из форм Осуществляют в горячей (85-90 С) воде, подкисленной соляной кислотой (0,5—1 см3 на литр воды) для предотвращения омыления стеарина. После выплавления моделей керамические формы просушивают при 150—170 °С в течение 1—2 ч, устанавливают в контейнеры, засыпают сухим наполнителем и прокаливают при 600—700 °С в течение 5—8 ч. Заливку ведут в холодные и нагретые формы. Температура нагрева (50-300 °С) форм определяется толщиной стенок отливки. Заполнение форм металлом осуществляют обычным способом, а также с использованием вакуума или центробежной силы. Большинство алюминиевых сплавов перед заливкой нагревают до 720—750 °С.
Литье в кокиль
Литье в кокиль — основной способ серийного и массового производства отливок из алюминиевых сплавов, позволяющий получать отливки 4—6-го классов точности с шероховатостью поверхности Rz = 50-20 и минимальной толщиной стенок 3—4 мм. При литье в кокиль наряду с дефектами, обусловленными высокими скоростями движения расплава в полости литейной формы и несоблюдением требований направленного затвердевания (газовая пористость, оксидные плены, усадочная рыхлота), основными видами брака отливок являются недоливы и трещины. Появление трещин вызывается затрудненной усадкой. Особенно часто трещины возникают в отливках из сплавов с широким интервалом кристаллизации, имеющих большую линейную усадку (1,25—1,35 %). Предотвращение образования указанных дефектов достигается различными технологическими приемами.
Для того чтобы обеспечить плавное, спокойное поступление металла в полость литейной формы, надежное отделение шлака и оксидных плен, образовавшихся в металле в процессе плавки и движения по литниковым каналам, и предотвращение их образования в литей-ной форме, при литье в кокиль применяют расширяющиеся литниковые системы с нижним, щелевым и многоярусным подводом металла к тонким сечениям отливок. В случае подвода ме-талла к толстым сечениям должна быть предусмотрена подпитка места подвода установкой питающей бобышки (прибыли). Все элементы литниковых систем располагают по разъему кокиля. Рекомендуются следующие соотношения площадей сечения литниковых каналов: для мелких отливок EFст : EFшл : EFпит = 1 : 2 : 3; для крупных отливок EFст : EFшл : EFпит = 1 : 3 : 6.
Для снижения скорости поступления расплава в полость формы применяют изогнутые стояки, сетки из стеклоткани или металла, зернистые фильтры. Качество отливок из алюминиевых сплавов зависит от скорости подъема расплава в полости литейной формы. Эта скорость должна быть, достаточной для гарантированного заполнения тонких сечений отливок в условиях повышенного теплоотвода и в то же время не вызвать недоливов, обусловленных неполным выходом воздуха и газов через вентиляционные каналы и прибыли, завихрений и фонтанирования расплава при переходе из узких сечений в широкие. Скорость подъема металла в полости формы при литье в кокиль принимают несколько большей, чем при литье в песчаные формы. Минимально допустимую скорость подъема рассчитывают по формулам А. А. Лебедева и Н. М. Галдина (см. раздел «Литье в песчаные формы»).
Для получения плотных отливок создают, так же как и при литье в песчаные формы, направленное затвердевание путем надлежащего расположения отливки в форме и регулирования теплоотвода. Как правило, массивные (толстые) узлы отливок располагают в верхней части кокиля. Это дает возможность компенсировать сокращение их объема при затвердевании непосредственно из прибылей, установленных над ними. Регулирование интенсивности теплоотвода с целью создания направленного затвердевания осуществляют охлаждением или утеплением различных участков литейной формы. Для местного увеличения теплоотвода широко используют вставки из теплопроводной меди, предусматривают увеличение поверхности охлаждения кокиля за, счет оребрения, осуществляют локальное охлаждение кокилей сжатым воздухом или водой. Для снижения интенсивности теплоотвода на рабочую поверхность кокиля наносят слой краски толщиной 0,1—0,5 мм. На поверхность литниковых каналов и прибылей для этой цели наносят слой краски толщиной 1-1,5 мм. Замедление охлаждения металла в прибылях может быть достигнуто также за счет местного утолщения стенок кокиля, применения различных малотеплопроводных обмазок и утепления прибылей наклейкой асбеста. Окраска рабочей поверхности кокиля улучшает внешний вид отливок, способствует устранению газовых раковин и неслитин на их поверхности и повышает стойкость кокилей. Перед окраской кокили подогревают до 100—120 °С. Излишне высокая температура нагрева нежелательна, так как при этом снижаются скорость затвердевания отливок и длительность срока службы кокиля. Нагрев уменьшает перепад температур между отливкой и формой и расширение формы за счет прогрева ее металлом отливки. В результате этого в отливке уменьшаются растягивающие напряжения, вызывающие появление трещин. Однако одного только подогрева формы недостаточно, чтобы устранить возможность возникновения трещин. Необходимо своевременное извлечение отливки из формы.
Удалять отливку из кокиля следует раньше того момента, когда температура ее сравняется с температурой кокиля, а усадочные напряжения достигнут наибольшей величины. Обычно отливку извлекают в тот момент, когда она окрепнет настолько, что ее можно перемещать без разрушения (450—500 °С). К этому моменту литниковая система еще не приобретает достаточной прочности и разрушается при легких ударах. Длительность выдержки отливки в форме определяется скоростью затвердевания и зависит от температуры ме-талла, температуры формы и скорости заливки. Алюминиевые сплавы в зависимости от состава и сложности конфигурации отливок заливают в кокили при 680—750 °С. Весовая скорость заливки составляет 0,15—3 кг/с. Отливки с, тонкими стенками заливают с большими скоростями, чем с толстыми.
Для устранения прилипания металла, повышения срока службы и облегчения извлечения металлические стержни в процессе работы смазывают. Наиболее распространенной смазкой является водно-графитовая суспензия (3—5 % графита).
Части кокилей, выполняющих наружные очертания отливок, изготавливают из серого чугуна. Толщину стенок кокилей назначают в зависимости от толщины стенок отливок в соответствии с рекомендациями ГОСТ 16237—70. Внутренние полости в отливках выполняют с помощью металлических (стальных) и песчаных стержней. Песчаные стержни используют для оформления сложных полостей, которые невозможно выполнить металлическими стержнями. Для облегчения извлечения отливок из кокилей наружные поверхности отливок должны иметь литейный уклон от 30′ до 3° в сторону разъема. Внутренние поверхности отливок, выполняемых металлическими стержнями, должны иметь уклон не менее 6°. В отливках не допускаются резкие переходы от толстых сечений к тонким. Радиусы закруглений должны быть не менее 3 мм. Отверстия диаметром более 8 мм для мелких отливок, 10 мм для средних и 12 мм для крупных выполняют стержнями. Оптимальное отношение глубины отверстия к его диаметру равно 0,7—1. Величина припуска на обработку при литье в кокиль назначается в два раза меньшей, чем при литье в песчаные формы.
Воздух и газы выводятся из полости кокиля с помощью вентиляционных каналов, размещаемых в плоскости разъема, и пробок, размещаемых в стенках вблизи глубоких полостей.
В современных литейных цехах кокили устанавливают на однопозиционные или многопозиционные полуавтоматические литейные машины, в которых автоматизированы закрытие и раскрытие кокиля, установка и извлечение стержней, выталкивание и удаление отливки из формы. Предусмотрено также автоматическое регулирование температуры нагрева кокиля. Заливку кокилей на машинах осуществляют с помощью дозаторов.
Для улучшения заполнения тонких полостей кокилей и удаления воздуха и газов, выделяющихся при деструкции связующих, осуществляют вакуумирование форм, заливку их под низким давлением или с использованием центробежной силы.
Литье выжиманием
Литье выжиманием является разновидностью литья в кокиль, Оно предназначено для изготовления крупногабаритных отливок (2500х1400 мм) панельного типа с толщиной стенок 2—3 мм (рис. Допустимая скорость подъема расплава на рабочем участке полости формы при литье панелей из алюминиевых сплавов должна быть в пределах 0,5—0,7 м/с. Меньшая скорость может привести к незаполнению тонких сечений отливок, излишне высокая — к дефектам гидродинамического характера: волнистости, неровностям поверхности отливок, захвату воздушных пузырьков, размыву песчаных стержней и образованию трещин из-за разрыва потока. Заливку металла производят в подогретые до 250—-350 °С металлоприемники. Регулирование скорости охлаждения расплава осуществляют нанесением на рабочую поверхность полости форм
теплоизоляционного покрытия различной толщины (0,05—1 мм). Перегрев сплавов перед заливкой не должен превышать 15—20° над температурой ликвидуса. Длительность сближения полуформ 5-3 с.
Литье под низким давлением
Литье под низким давлением является другой разновидностью литья в кокиль. Оно получило применение при изготовлении крупногабаритных тонкостенных отливок из алюминиевых сплавов с узким интервалом кристаллизации (АЛ2, АЛ4, АЛ9, АЛ34). Так же как и при литье в кокиль, наружные поверхности отливок выполняются металлической формой, а внутренние полости — металлическими или песчаными стержнями.
Для изготовления стержней используют смесь, состоящую из 55% кварцевого песка 1К016А; 13,5 % полужирного песка П01; 27% пылевидного кварца; 0,8 % пектинового клея; 3,2 % смолы М и 0,5 % керосина. Такая смесь не образует механического пригара. Заполнение форм металлом осуществляют давлением сжатого осушенного воздуха (18—80 кПа), подаваемого на поверхность расплава в тигле, нагретого до 720—750 °С. Под действием этого давления расплав вытесняется из тигля в металлопровод, а из него в коллектор литниковой системы и далее — в полость литейной формы. Преимуществом литья под низким давлением является возможность автоматического регулирования скорости подъема металла в полости формы, что позволяет получать тонкостенные отливки более качественными, чем при литье под действием силы тяжести.
Кристаллизацию сплавов в форме проводят под давлением 10— 30 кПа до образования твердой корки металла и 50—80 кПа после образования корки.
Более плотные отливки из алюминиевых сплавов получают литьем под низким давлением с противодавлением. Заполнение полости формы при литье с противодавлением осуществляют за счет разницы давлений в тигле и в форме (10—60 кПа). Кристаллизация металла в форме ведется под давлением 0,4—0,5 МПа. При этом предотвращается выделение растворенного в металле водорода и образование газовых пор. Повышенное давление способствует лучшему питанию массивных узлов отливок. В остальном технология литья с противодавлением не отличается от технологии литья под низким давлением.
При литье с противодавлением успешно совмещены достоинства литья под низким давлением и кристаллизации под давлением.
Литье под давлением
Литьем под давлением из алюминиевых сплавов АЛ2, АЛЗ, АЛ1, АЛО, АЛ11, АЛ13, АЛ22, АЛ28, АЛ32, АЛ34 изготавливают сложные по конфигурации отливки 1—3-го классов точности с толщиной стенок от 1 мм и выше, литыми отверстиями диаметром до 1,2 мм,
литой наружной и внутренней резьбой с минимальным шагом 1 мм и диаметром 6 мм. Чистота поверхности таких отливок соответствует 5— 8-му классам шероховатости. Изготовление таких отливок осуществляют на машинах с холодной горизонтальной или вертикальной камерами прессования, с удельным давлением прессования 30— 70 МПа. Предпочтение отдается машинам с горизонтальной камерой прессования.
Размеры и масса отливок ограничиваются возможностями Машин литья под давлением: объемом камеры прессования, удельным давлением прессования (р) и усилием запирания (0). Площадь проекции (F) отливки, литниковых каналов и камеры прессования на подвижную плиту пресс-формы не должна превышать значений, определяемых по формуле F = 0,85 0/р.
Во избежание незаполнения форм и неслитин толщину стенок оливок из алюминиевых сплавов назначают с учетом площади их поверхности:
Площадь поверхности
отливки, см2 До 25 25—150 150—250 250—500 Св. 500
Толщина стенки, мм. 1—2 1,5—3 2—4 2,5—6 3—8
Оптимальные значения уклонов для наружных поверхностей составляют 45′; для внутренних 1°. Минимальный радиус закруглений 0,5—1′ мм. Отверстия более 2,5 мм в диаметре выполняются литьем. Отливки из алюминиевых сплавов, как правило, подвергают механической обработке только по посадочным поверхностям. Припуск на обработку назначается с учетом габаритов отливки и составляет от 0,3 до 1 мм.
Для изготовления пресс-форм применяют различные материалы. Части пресс-форм, соприкасающиеся с жидким металлом, изготавливают из сталей ЗХ2В8, 4Х8В2, 4ХВ2С, плиты крепления и обоймы матриц — из сталей 35, 45, 50, штыри, втулки и направляющие колонки — из стали У8А.
Подвод металла к полости пресс-форм осуществляют с помощью внешних и внутренних литниковых систем. Питатели подводят к участка отливки, подвергающимся механической обработке. Толщину их назначают в зависимости от толщины стенки отливки в месте подвода и заданного характера заполнения пресс-формы. Эта зависимость определяется отношением толщины Питателя к толщине стенки отливки . Плавное, без завихрений и захвата воздуха, заполнение пресс-форм имеет место, если отношение близко к единице. Для отливок с толщиной стенок до 2 мм питатели имеют толщину 0,8 мм; при толщине стенок 3 мм толщина питателей равна 1,2мм; при толщине стенок 4—6 мм—2 мм.
Для приема первой порции расплава, обогащенного воздушными включениями, вблизи полости пресс-формы располагают специальные резервуары-промывники, объем которых может достигать 20 -40 % от объема отливки. Промывники соединяют с полостью литейной формы каналами, толщина которых равна толщине питателей. Удаление воздуха и газа из полости пресс-форм осуществляют через специальные вентиляционные каналы и зазоры между стержнями (выталкивателями) и матрицей пресс-формы. Вентиляционные каналы выполняют в плоскости разъема на неподвижной части пресс-формы, а также вдоль подвижных стержней и выталкивателей. Глубина вентиляционных каналов при литье «алюминиевых сплавов принимается равной 0,05—0,15 мм, а ширина 10—З0 мм в целях улучшения вентиляции пресс-форм полости промывников тонкими каналами (0,2—0,5 мм) соединяют с атмосферой.
Основными дефектами отливок, полученных литьем под давлением, являются воздушная (газовая) подкорковая пористость, обусловленная захватом воздуха при больших скоростях впуска металла в полость формы, и усадочная пористость (или раковины) в тепловых узлах. На образование этих дефектов большое влияние оказывают параметры технологии литья—скорость прессования, давление прессования, тепловой режим пресс-формы.
Скорость прессования определяет режим заполнения пресс-формы. Чем выше скорость прессования, тем с большей скоростью перемещается расплав по литниковым каналам, тем больше скорость впуска расплава в полость пресс-формы. Высокие скорости прессования способствуют лучшему заполнению тонких и удлиненных полостей. Вместе с тем они являются причиной захвата металлом воздуха и образования подкорковой пористости. При литье алюминиевых сплавов высокие скорости прессования применяют лишь при изготовлении сложных тонкостенных отливок. Большое влияние на качество отливок оказывает давление прессования. По мере повышения его увеличивается плотность отливок.
Величина давления прессования ограничивается обычно величиной усилия запирания машины, которое должно превышать давление, оказываемое металлом на подвижную матрицу (рF). Поэтому большой интерес приобретает локальная подпрессовка толстостенных отливок, известная под названием «Асигай-процесс». Малая скорость впуска металла в полость пресс-форм через питатели большого сечения и эффективная подпрессовка кристаллизующегося расплава с помощью двойного плунжера позволяют получать плотные отливки.
На качество отливок существенною влияние оказывают также температуры сплава и формы. При изготовлении толстостенных отливок несложной конфигурации заливку расплава ведут при температуре на 20—30 °С ниже температуры ликвидуса. Тонкостенные отливки требуют применения расплава, перегретого выше температуры ликвидуса на 10—15 °С. Для снижения величины усадочных напряжений и предотвращения образования трещин в отливках пресс-формы перед заливкой нагревают. Рекомендуются следующие температуры нагрева:
Толщина стенки отливки, мм 1—2 2—3 3—5 5—8
Температура нагрева
пресс-форм, °С 250—280 200—250 160—200 120—160
Стабильность теплового режима обеспечивают подогревом (электрическим) или охлаждением (водяным) пресс-форм.
Для предохранения рабочей поверхности пресс-форм от налипания и эрозионного воздействия расплава, уменьшения трения при извлечении стержней и облегчения извлечения отливок пресс-формы подвергают смазке. Для этой цели используют жирные (масло с графитом или алюминиевой пудрой) или водные (растворы солей, водные препараты на основе коллоидального графита) смазки.
Существенно повышается плотность отливок из алюминиевых сплавов при литье с вакуумированием пресс-форм. Для этого пресс формы помещают в герметичный кожух, в котором создают необходимое разрежение. Хорошие результаты могут быть получены при использовании «кислородного процесса». Для этого воздух в полости пресс-формы заменяют кислородом. При больших скоростях впуска металла в полость формы, вызывающих захват расплавом кислорода, подкорковая пористость в отливках не образуется, так как весь захваченный кислород расходуется на образование мелкодисперсных оксидов алюминия, не влияющих заметно на механические свойства отливок. Такие отливки можно подвергать термической обработке.
Контроль качества отливок и исправление их дефектов
В зависимости от требований технических условий отливки из алюминиевых сплавов могут подвергаться различным видам контроля: рентгеновскому, гаммадефектоскопии или ультразвуковому для обнаружения внутренних дефектов; разметке для определения размерных отклонений; люминесцентному для обнаружения поверхностных трещин; гидро- или пневмоконтролю для оценки герметичности. Периодичность перечисленных видов контроля оговаривается техническими условиями или определяется отделом главного металлурга завода. Выявленные дефекты, если это допускается техническими условиями, устраняют заваркой или пропиткой. Аргонно-дуговую сварку используют для заварки недоливов, раковин, рыхлости трещин. Перед заваркой дефектное место разделывают таким образом, чтобы стенки углублений имели наклон 30— 42. Отливки подвергают местному или общему нагреву до 300— 350С. Местный нагрев ведут ацетиленокислородным пламенем, общий нагрев — в камерных печах. Заварку ведут теми же сплавами, из которых изготовлены отливки, с помощью неплавящегося вольфрамового электрода диаметром 2—6 мм при расходе аргона 5— 12 л/мин.-Сила сварочного тока составляет обычно 25—40 А на 1 мм диаметра электрода.
Пористость в отливках устраняют пропиткой бакелитовым лаком, асфальтовым лаком, олифой или жидким стеклом. Пропитку ведут специальных котлах под давлением 490—590 кПа с предварительной выдержкой отливок в разреженной атмосфере (1,3— 6,5 кПа). Температуру пропитывающей жидкости поддерживают на уровне 100°С. После пропитки отливки подвергают сушке при 65-200°С, в процессе которой происходит твердение пропитывающей жидкости, и повторному контролю.
Список литературы
- Литейные сплавы и технологии их плавки в машиностроении. М.: Машиностроение. 1984.
- Теория литейных процессов. Л.: Машиностроение. 1976.
- Отливки из алюминиевых сплавов. М.: Машиностроение. 1970.
- Производство отливок из сплавов цветных металлов. М.: Металлургия. 1986.
- Производство литых алюминиевых деталей. М.: Металлургия. 1979.
- Алюминиевые сплавы. Справочник. М.: Металлургия. 1983.
В этом декламации мы покажем, как использовать методы, подобные тем, которые преподавались в классе на этой неделе, для создания слепков с использованием более высокотемпературного материала: алюминия.
Зачем беспокоиться?
- Удельная жесткость : Алюминий имеет удельную жесткость на 1-2 порядка выше, чем у большинства полимеров! Это означает, что вы часто можете сделать более легкую, прочную и простую деталь.
- Возможность вторичной переработки : Алюминий имеет долю пригодности для вторичной переработки между .8 и .9. Наиболее пригодные для повторного использования полимеры (HDPE) имеют долю от 0,5 до 0,6.
- Стоимость/Наличие : Алюминиевый лом повсюду! (посмотрите возле водомета) Высокотемпературные формы можно сделать из песка, глины и масла (очень дешевые материалы). Колбы для форм для песка можно сделать из древесных отходов. В целом, это очень недорогая процедура.
По сравнению с низкотемпературными сплавами алюминий превосходит по своим характеристикам. Рассмотрим эту тестовую установку Brinnell:
. тестирование по Бриннелю.Они дают твердость по Бринеллю 27 и 102 для баббита и алюминия соответственно (близко к их спецификациям материалов). Посетите мою страницу NMM для более подробной информации.
тестирование по Бриннелю.Мы также можем сами измерить эластичность материала, и разница очевидна:
тестирование по Бриннелю.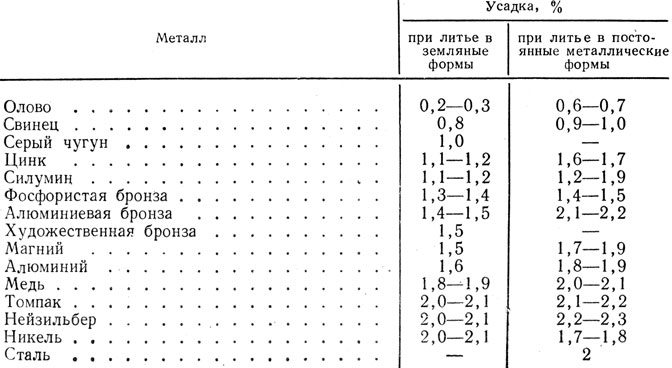
Безопасность
Работа с расплавленными металлами опасна по своей природе. Участвуйте на свой страх и риск!
Вот несколько советов по безопасности от alluminium.org:- Алюминий обычно обрабатывается при температуре 1300-1450 градусов по Фаренгейту.
- Смесь с загрязняющими веществами может вызвать взрыв. Плавятся только чистые, известные алюминиевые сплавы.
- Контакт с расплавленным алюминием может вызвать серьезные ожоги и создать опасность возгорания. Всегда знайте местонахождение ближайшего огнетушителя и создавайте план безопасности.
- При работе с расплавленным алюминием необходимо использовать средства защиты глаз и защитную одежду. Также желательно защиту лица.
Создание шаблона
Как и в случае с обрабатываемым воском и рабочим процессом oomoo из еженедельного задания, первым шагом в этом процессе является создание положительной версии нашего дизайна.Мы можем использовать многие цифровые процессы изготовления для создания шаблона желаемой формы, включая фрезерование воска или дерева или 3D-печать.
При проектировании песчаных форм необходимо учитывать несколько моментов. Во-первых, не забудьте приложить тягу к части, чтобы помочь ей отделиться от песка. Песок может легко крошиться, и правильный угол уклона во многом предотвращает это. Во-вторых, с помощью песчаной формы трудно создать маленькие отверстия. Отверстия 1/2 дюйма в моей модели примерно такие же маленькие, как и следовало бы.Если вам нужны меньшие отверстия в окончательной алюминиевой детали, вы можете сделать небольшие конические «выемки» на поверхности детали и просверлить их позже. Эти канавки помогают сверлу начать отверстие в нужном месте и удивительно точны.
Инструмент черновика Onshape.Я использовал Onshape для моделирования нужной детали. Он имеет удобный инструмент «Черновик» для выполнения конической экструзии. Я использовал 5 градусов со своей стороны.
Изготовление колб
Наши формы для песка формируются внутри деревянного ящика, называемого флягой.Это забавный проект, чтобы сделать их на шопботе. Я спроектировал свой так, чтобы он имел заданную длину с регулируемой шириной, устанавливаемой путем обрезки отрезков 2×4.
В большинстве конструкций фляг используется какая-то функция кинематического выравнивания, как в моей конструкции, выполненной под углом. Это позволяет нам упаковать половинки пресс-формы, разделить их, чтобы удалить шаблон, и точно выровнять их.
Упаковка фляги
Выкройку кладем внутрь одной половинки колбы лицевой стороной вниз на твердую поверхность.Теперь немного утрамбовываем песок вокруг узора. Это может занять много времени, но давление трамбовки имеет решающее значение для формирования хорошей детали.
А) После упаковки первой половины колбы и ее переворачивания. Б) После нанесения талька на интерфейс.Утрамбовав первую половину, мы переворачиваем ее и наносим тальк, чтобы песок для второй половины не склеивался с первой половиной.
А) После удаления выкройки из первой половины колбы.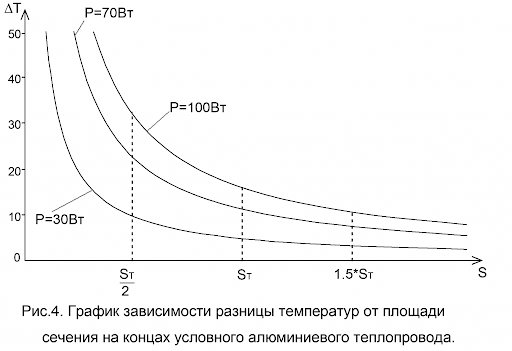
После упаковки фляги разделяем половинки фляги, и аккуратно снимаем выкройку. Можно слегка постучать по нему небольшим молотком, чтобы отделить его от песка. После удаления шаблона мы можем использовать тонкую трубку, чтобы вырезать литник и подступенок.
Заливка детали
Теперь мы готовы залить деталь. Алюминию требуется некоторое время, чтобы нагреться до температуры, поэтому запланируйте достаточно времени. В зависимости от размера детали правильная температура заливки алюминия составляет от 1300 до 1400 градусов по Фаренгейту.
В защитной маске, перчатках, куртке и кожаных ботинках (или гетрах) осторожно вытащите тигель из печи и залейте в литник.
А) После заливки алюминий заполнил и литник, и стояк. Б) Распаковка фляги для извлечения нашей детали.Очистка детали
А) Наш узор из песка. B) Две копии нашего шаблона, объединенные в одну форму. С помощью нашей литой детали мы можем легко добавить прецизионные поверхности с помощью сверлильного станка и/или фрезерного станка.
Разработка шаблонов для литья в песчаные формы — это своего рода искусство, но с помощью надлежащих методов мы можем создавать точные детали с минимальной механической обработкой и чрезвычайно низкими затратами.
Насколько важна температура при литье под давлением?
Контроль температуры литья под давлением является серьезной проблемой. Когда дело доходит до литья под давлением, по мере повышения температуры предел прочности при растяжении и текучести сплава снижается. Пластичность также увеличивается с повышением температуры, но различается в зависимости от типа отливаемого сплава.Правильная температура имеет решающее значение как для штампа, так и для отливаемого металла. Отливаемый металл необходимо правильно нагреть, чтобы обеспечить надлежащее течение и заполнение формы. Если температура расплавленного металла слишком высока для формы, это может повредить форму. Если температура формы слишком низкая, металл будет остывать слишком быстро, затекая в форму, что приведет к возникновению дефектов.
Затекание металла в матрицу
Какие температуры необходимо тщательно контролировать?
• Температура самой формы
• Температура машины для литья под давлением или литейной камеры
• Температура сплава, используемого для литья
Все три из этих температур должны поддерживаться в индивидуальном оптимальном диапазоне для производства литых деталей высочайшего качества.
Какова правильная температура штампа?
Температура формы будет зависеть от того, какой сплав вы собираетесь отливать. Вы хотите избежать чрезмерной нагрузки на матрицу, поскольку нагрузка на матрицу снизит ожидаемый срок службы самой матрицы. Лучше всего заливать сплав в форму, когда он примерно на 50–70° выше температуры кристаллизации сплава. Температура штампа должна поддерживаться примерно на одной трети температуры сплава.
Какова правильная температура камеры/машины для литья под давлением?
Температура, необходимая для машины для литья под давлением, представляет собой сложный расчет, включающий такие параметры, как тип сплава, тип штампа, размер отливаемой детали и многое другое.Температуру в камере должен определять опытный литейщик.
Какова правильная температура сплава?
Температура сплава сильно различается в зависимости от материала. Вот два примера наиболее распространенных сплавов для литья под давлением — алюминий и цинк.
Алюминий
Алюминий 360, 380 и 413 на сегодняшний день являются наиболее популярными металлами для литья под давлением. Алюминий устойчив к коррозии, легкий и чрезвычайно прочный. Например, при литье алюминия марки 380 вы получите предел прочности на растяжение 48 при 75° с пределом текучести 24 тысячи фунтов на квадратный дюйм (Kips per Square Inch). Если вы повысите температуру до 212°, вы получите предел прочности на разрыв 45 KSI, в то время как предел текучести останется постоянным на уровне 24.
Цинк
Цинк 3, 5 и 7 также являются невероятно популярными сплавами для литья под давлением. Для этих цинковых сплавов температура 75° дает в среднем 40 KSI. Если вы повысите температуру до 275°, вы получите среднее значение KSI около 10,
Оптимальные диапазоны температур для обработки поверхности:
Что произойдет, если температура будет неправильной?
Если температура отливаемого металла слишком высока для формы, это может привести к повреждению формы, что резко сократит эффективный срок службы формы.Если температура слишком низкая, металл будет остывать слишком быстро, поскольку он затекает в форму, что может вызвать дефекты (такие как проблемы с пористостью или пропуски).
Чем может помочь литье под давлением A&B?
Компания A&B Die Casting очень серьезно относится к вопросу контроля температуры. У нас большой опыт в поддержании оптимальной температуры наших материалов и литейного оборудования. Мы используем программное обеспечение для трехмерного анализа потока, чтобы обеспечить оптимальное заполнение матрицы для превосходного качества литья.Программное обеспечение позволяет нам смоделировать, как указанный материал будет течь в форму, чтобы мы могли более точно оценить общую эффективность формы, а также выявить любые потенциальные проблемы с колебаниями температуры материала, когда он течет в форму.
Уже более 70 лет компания A&B Die Casting обслуживает мировых производителей литьем под давлением алюминия и цинка в малых и средних объемах. Наша опытная команда создает решения для ваших производственных потребностей, начиная с начальных этапов проектирования и прототипирования и заканчивая механической обработкой, отделкой, сборкой, упаковкой и доставкой с соблюдением ваших точных спецификаций.
Нужна помощь или хотите приступить к следующему проекту литья под давлением? Свяжитесь с A&B Die Casting сегодня!
(PDF) Поведение отливок из алюминиевых сплавов при различных температурах и скоростях заливки
Поведение отливок из алюминиевых сплавов при различных температурах и скоростях заливки
Мохаммад Б. НДАЛИМАН и Акпан П. П.И.
Диапазон скоростей заливки, который дал наилучшие отделка поверхности, составляет от 2,0 см/с до
2,8 см/с.В этом интервале температур
были получены оптимальные значения твердости, предела прочности и деформации.
Дальнейшие исследования по металлургическим исследованиям отливок, произведенных в различных
диапазонах этих параметров {температуры и скорости}, в настоящее время продолжаются. Это необходимо для проверки
размеров зерен, неметаллических включений и субмикроскопических отверстий.
Ссылки
1. Пиус А. П., Влияние некоторых параметров литья на механические свойства сплава алюминия
и среднеуглеродистой стали, неопубликовано B.Eng Проект представлен на кафедру
Машиностроение, Федеральный технологический университет, Минна, 2000.
2. Уоррендейл Дж. Л., Скорость заливки некоторых черных и цветных металлов, Бумага
Представлено на Четвертой — Пятой Питтсбургской конференции Ежегодное собрание Американского общества инженеров-металлургов
, 20 апреля 1981 г. , с. 37-45.
3. Джайн П. Л. Принципы технологии литейного производства. М.: Изд-во МИР, 1986, с. 22-64.
4. Линдберг Р.А., Процессы и материалы для производства, 2-е издание, Allyn and Bacon
Inc. Бостон, Лондон, Сидней и Торонто, 1997, с. 90-96.
5. ASME, Диапазоны температур заливки металлов и сплавов, Публикация Американского общества машиностроения
, Vol. III, Чикаго, США, 1996.
6. Лансер Н.С. Руководство по организации литейного производства. М.: Изд-во МИР, 1981, с.
72-75.
7. Гриль П. Л., Принцип литья металлов, McGraw-Hill Book Company, Нью-Йорк, 1982, с.
160-166.
8. Аделеке О.П., Влияние температуры заливки на растворимость газов, B. Eng Project
Представлено в Отдел машиностроения, Ф.У.Т. Минна, 1992, с. 17-18.
9. Кемстер М. Х. А., Материалы для инженеров, Ходдер и Стоутон, Лондон, Сидней,
Окленд и Торонто, 1976, с. 161-170.
10. Споттс М. Ф., Дизайн элементов машин, 6-е издание, Prentice — Hall of India Private
Limited, Нью-Дели — 110001, 1988, с. 705 — 709.
80
Алюминий и алюминиевые отливки | Ресурсы по металлическому литью
Добыча, переработка и литье в литейных цехах
Растущая популярность алюминия
Алюминий — третий по распространенности элемент в мире и самый распространенный металл в земной коре. Алюминий составляет более 8% массы ядра Земли. Однако его трудно очистить по сравнению с другими металлами, такими как железо. По этой причине использование алюминия отстает от других металлических изделий, в то время как для преодоления этих сложностей были разработаны эффективные и экономичные методы.
Существует много общего между алюминиевой и сталелитейной промышленностью. Оба основаны на извлечении металлов из минеральных руд, залегающих на поверхности земли. Производственные процессы обоих энергоемки и включают заливку жидкого металла в отливки или использование машин непрерывного литья заготовок. Алюминий и сталь также конкурируют на аналогичных рынках автомобильной и аэрокосмической промышленности. Однако существуют существенные различия в обработке и свойствах этих металлов.
Обработка алюминия
Бокситы — осадочные породы с высоким содержанием алюминия; обычно около 46–60%. Бокситы часто покрыты несколькими метрами камня и глины, которые необходимо сначала удалить, прежде чем боксит можно будет извлечь. Затем боксит проходит дробление или промывку перед транспортировкой на переработку.
В середине 1880-х годов были изобретены и последовательно использовались два различных метода производства алюминия.Метод Байера использует химический процесс для извлечения алюминия из бокситов. В процессе Холла-Эру используется электролиз для извлечения алюминия из оксида алюминия или оксида алюминия, полученного в процессе Байера.
Кава-ди-Боксит в городе Отранто до 1976 года был бокситовым рудником и до сих пор содержит большое количество бокситов в этом районе.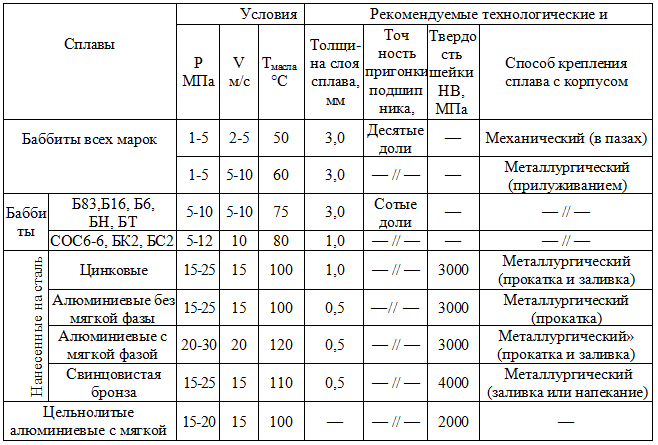
Процесс Байера
Бокситовая руда измельчается и смешивается с едким натром для получения суспензии, содержащей мелкие частицы руды. Суспензия выдерживается при температуре от 140°C до 280°C, в зависимости от конкретной перерабатываемой руды.За это время алюминий растворяется в растворе едкого натра. Все примеси оседают из раствора в остаток, называемый красным шламом.
Завершающим этапом процесса является добавление затравочных кристаллов в раствор едкого натра. Растворенный оксид алюминия присоединяется к этим затравочным кристаллам. Конечным продуктом процесса Байера является оксид алюминия или оксид алюминия, который имеет вид белого порошка.
Процесс Холла-Эру
Редукционная установка алюминиевого завода состоит из редукционных ванн или ячеек, соединенных последовательно.Каждый горшок изготовлен из стальной оболочки, облицованной углеродом. В каждый котел заливают расплавленный криолит (фторидный минерал), содержащий оксид алюминия, и сверху в раствор вставляют угольные электроды. Когда ток проходит через раствор криолита, алюминий отделяется от кислорода, образуя углекислый газ. Жидкий алюминий скапливается на дне кастрюли.
Затем жидкий глинозем через равные промежутки времени всасывается из восстановительных ванн в вакуумные баки. Его переносят в печь и разливают в слитки в изложницах или на машине непрерывного литья заготовок.Алюминий, полученный с помощью этого процесса, имеет чистоту примерно 99,8%. Электролитический процесс производства алюминия является очень энергоемким, требуя 15 МВтч на тонну продукции. Поэтому большинство плавильных заводов расположены рядом с генераторами электроэнергии, такими как гидроэлектростанции.
Алюминиевое литье
После того, как алюминий извлечен и обработан, следующим шагом является его отливка в форму продукта. Алюминиевые отливки формируются путем заливки расплавленного металла в формы, которым придана форма желаемого конечного продукта.Для производства отливок используются три распространенных метода формования: литье под давлением, литье в постоянные формы и литье в песчаные формы.
Литье под давлением
Литье под давлением использует давление для подачи расплавленного алюминия в стальную форму. Этот вид литья часто используют для серийного производства деталей, требующих минимального объема доводки и механической обработки. Литье под давлением имеет короткое время цикла, но высокие затраты на оснастку. Система литья под давлением создает высокопрочную оболочку, но более прочную внутреннюю часть, чем литье в постоянные формы.Существует два типа литья под давлением: литье под низким давлением и литье под высоким давлением.
ЛИТЬЕ
Простая технология изготовления штампов и машин
Сложные и дорогие штампы
Снижение капиталовложений и эксплуатационных расходов
Высокие инвестиционные и эксплуатационные расходы
Минимальная толщина стенки около 3 мм
Подходит для тонкостенных компонентов
Литье в постоянную форму
Для литья в постоянные формы используются стальные или другие металлические формы и стержни. Прочные отливки получают путем заливки алюминия в форму. Постоянные формы используются для создания деталей с высокой повторяемостью и постоянством. Их высокие скорости охлаждения создают более однородную микроструктуру, которая может значительно улучшить механические свойства.
Постоянное литье в формы используется для создания легкосплавных дисков. Алюминиевые колеса также легче стальных и требуют меньше энергии для вращения. Они обеспечивают большую топливную экономичность, а также лучшую управляемость, ускорение и торможение.Однако для тяжелых промышленных гусениц чаще используются стальные колеса. Благодаря своей прочности их практически невозможно согнуть или расколоть. При использовании на треке стальные колеса более терпимы к неровностям пути, что повышает безопасность.
Алюминиевые колеса легче стальных и требуют меньшей мощности двигателя. Тем не менее, для промышленных гусениц стальные колеса по-прежнему предпочтительнее из-за их долговечности и стабильности.Литье в песчаные формы
Отливки в песчаные формы создаются путем набивки мелкозернистой песчаной смеси вокруг образца желаемого изделия. Шаблон немного больше, чем конечный продукт, чтобы учесть усадку алюминия при охлаждении. Литье в песчаные формы экономично, потому что песок можно использовать многократно. Он также эффективен для создания больших молдингов или деталей с подробным дизайном. Первоначальные затраты на инструменты низкие, но цены за деталь выше, что делает литье в песчаные формы подходящим для специализированных отливок, а не для массового производства.
Контроль расплавленного алюминия напрямую влияет на качество отливки.Легирующие элементы добавляются к расплавленному алюминию для достижения требуемой марки алюминия и свойств. Контролируемое добавление и распределение сплава по всему алюминию гарантирует, что продукт будет прочным и с ожидаемыми механическими свойствами.
Алюминий затвердевает со столбчатой структурой зерна. Эти столбики растут до точки соприкосновения с другим зерном — чем больше зерен, тем тоньше молекулярная структура. При рафинировании зерна титан и бор используются для создания зародышей зерен для достижения этой тонкой структуры.
Газообразный водород является примесью, которая может вызывать дефекты в алюминиевом литье, создавая поры при затвердевании продукта. Во время литья требуются дегазация и продувочные газы, чтобы защитить окружающую среду от любых примесей, которые могут негативно повлиять на конечный продукт.
Литейные сплавы
Доступен широкий спектр литейных сплавов, подходящих для конечного применения. Каждый из этих литейных сплавов имеет свои характеристики, такие как свариваемость, обрабатываемость, коррозионная стойкость и свойства термообработки.
Расплавленный алюминий имеет несколько характеристик, которыми можно управлять, чтобы максимизировать литейные свойства. Расплавленный алюминий склонен поглощать газообразный водород и оксиды в расплавленном состоянии и может быть чувствителен к второстепенным микроэлементам. Хотя некоторые декоративные или коммерческие отливки могут не требовать дополнительной обработки, дальнейшая отделка часто бывает полезной. Жесткий контроль расплава и специальные методы обработки расплавленного металла могут обеспечить улучшенные механические свойства.
Алюминиевые отделки и покрытия
Одним из эстетических достоинств алюминия является его высокая отражательная способность.Эта характеристика была использована для производства высококачественных потребительских товаров с чистой поверхностью. Это дополнительно усиливается за счет естественного образования тонкого оксидного слоя на поверхности. Этот слой можно сделать толще за счет анодирования изделия. Наличие оксидного слоя эффективно защищает алюминий от дальнейшего окисления, делая его очень устойчивым к коррозии. Различные отделки и покрытия могут помочь алюминию достичь этого блестящего, но прочного качества.
Отделка
Некоторые алюминиевые сплавы подвергаются термообработке для улучшения их свойств для конкретных применений.Цельный литой алюминий нагревается до заданной температуры, что приводит к равномерному распределению молекулярной микроструктуры по всему материалу. Затем быстрое охлаждение приводит к тому, что рисунок микроструктуры остается на месте, и достигаются идеальные свойства.
Сплавы, не поддающиеся термической обработке, отделывают холодной обработкой, преимущественно прокаткой. Прочность металла значительно повышается, поскольку дефекты микроструктуры сводятся к минимуму за счет плотного уплотнения молекул.
Покрытия
Алюминийимеет высококачественную поверхность, которая уже эстетически приятна. Тем не менее, различные покрытия могут предложить дополнительные преимущества для отделки.
Покрытия PVDF
ПокрытияPVDF представляют собой краски на основе растворителей с очень высокой устойчивостью к атмосферным воздействиям. Однако их можно поцарапать. ПВДФ не выгорает под воздействием солнечных лучей и может иметь металлический вид.
Жидкие краски
Жидкие краски более экономичны, чем покрытия PVDF, но их свойства также менее желательны.У них более низкое качество отделки и стойкость к атмосферным воздействиям не такая сильная.
Порошковые покрытия
Порошковые покрытия соответствуют самым строгим требованиям к долговечности на том же уровне, что и покрытия PVDF. Они имеют превосходный внешний вид и популярны в строительстве оконных и дверных рам, а также для строительной мебели, такой как столбы и стойки для велосипедов. Они выдерживают больший износ и часто используются в местах с интенсивным движением, таких как отели и магазины.
Анодирование
Анодирование используется для утолщения оксидированного поверхностного слоя и повышения коррозионной стойкости продукта.Покрытие твердое, прочное и самовосстанавливающееся, что делает его популярным выбором для архитекторов. Процесс анодирования осуществляется с использованием погружных ванн.
Анодирование повышает коррозионную стойкость алюминия за счет утолщения окисленного поверхностного слоя.Свойства алюминия
Алюминий известен своей легкостью. На самом деле он почти в три раза легче железа и имеет плотность 2700 кг/м 3 . Примечательно, что низкая плотность алюминия не влияет на его прочность.Алюминиевые сплавы имеют широкий диапазон прочностных характеристик с пределом прочности при растяжении от 70 до 700 МПа. При низких температурах прочность алюминия увеличивается, а при высоких – снижается.
также легко поддается механической обработке, а требуемая мощность невелика из-за меньшей плотности. Высокий уровень пластичности алюминия позволяет легко экструдировать его. Это позволяет изгибать и скручивать продукт, что является ключевой характеристикой при производстве алюминиевой фольги.
https://www.reliance-foundry.com/wp-content/uploads/aluminum-rolling.mov
Качество алюминия и стандарты
Алюминиевые изделия сертифицированы в соответствии с легирующим материалом, используемым в изделии. К наиболее распространенным легирующим элементам относятся следующие:
- Кремний
- Железо
- Медь
- Магний
- Цинк
АЛЮМИНИЙ, ОТНОСЯЩИЙСЯ К СЕРИЯМ ПО СВОЙСТВАМ И СОСТАВАМ
- Отличная коррозионная стойкость и обрабатываемость
- Высокая тепло- и электропроводность
- Передачи
- Линии электропередач
- Высокая прочность и ударная вязкость
- Более низкая коррозионная стойкость
- Умеренная крепость
- Хорошая обрабатываемость
- Теплообменники
- Кухонная утварь
- Банки для напитков
- более низкая температура плавления без хрупкости
- Проволока сварочная
- Прутки для пайки
- От умеренной до высокой прочности
- Стойкость к коррозии в морской среде
- Хорошая свариваемость
- Строительство и строительство
- Резервуары для хранения
- Сосуды под давлением
- Морское применение
- Средневысокая прочность
- Отличная коррозионная стойкость
- Высокая свариваемость
- Архитектурный
- Структурный
- Грузовики
- Морские рамы
- Отличная коррозионная стойкость и обрабатываемость
- Высокая тепло- и электропроводность
- Высокая прочность и ударная вязкость
- Более низкая коррозионная стойкость
- Умеренная крепость
- Хорошая обрабатываемость
- более низкая температура плавления без хрупкости
- От умеренной до высокой прочности
- Стойкость к коррозии в морской среде
- Хорошая свариваемость
- Средневысокая прочность
- Отличная коррозионная стойкость
- Высокая свариваемость
- Передачи
- Линии электропередач
- Теплообменники
- Кухонная утварь
- Банки для напитков
- Проволока сварочная
- Прутки для пайки
- Строительство и строительство
- Резервуары для хранения
- Сосуды под давлением
- Морское применение
- Архитектурный
- Структурный
- Грузовики
- Морские рамы
Здоровье и безопасность
Во время процесса Холла-Эру выделяется большое количество газов. Эти газы улавливаются и перерабатываются, поскольку токсичные соединения фтора должны быть удалены до того, как они будут выпущены в атмосферу. В процессе производства алюминия выделяется CO 2 , что приводит к более высокому углеродному следу алюминиевых изделий. Многие производители размещают алюминиевые заводы рядом с возобновляемыми источниками энергии, такими как гидроэлектростанции, вместо того, чтобы производить электроэнергию из ископаемого топлива.
В растворимой форме Al 3+ алюминий токсичен для растений.Кислые почвы, как правило, ускоряют высвобождение Al 3+ из его минералов и снижают выход продукта с этих полей. Поскольку почти половина пахотных земель во всем мире является кислой, негативное воздействие алюминия на урожайность может быть серьезным.
Алюминий также может воздействовать на человеческий организм. Последствия накопления алюминия для здоровья включают повышенный риск болезни Альцгеймера и некоторых видов рака, хотя это и не доказано окончательно. В высоких концентрациях алюминий является нейротоксином, который действует на мозг и костную структуру.Алюминий содержится в закваске, эмульгаторах и красителях, а также в некоторых антацидных продуктах.
Применение алюминия
Алюминий — это хорошо закругленный металл со светящейся отделкой, который подходит для широкого рынка, включая различные коммерческие и бытовые товары.
Аэрокосмическая отрасль
Достижения в аэрокосмической промышленности в значительной степени зависят от разработки алюминиевых изделий. Сочетание их свойств, особенно малого веса и прочности, позволило человечеству разработать достаточно прочные и легкие транспортные средства, чтобы покинуть атмосферу Земли.Братья Райт использовали алюминий для картера двигателя своего первого биплана с деревянным каркасом. Современные коммерческие транспортные самолеты на 80% состоят из алюминия, который в основном содержится в их планерах, особенно в фюзеляжах и крыльях. Алюминий широко используется в космической промышленности для изготовления шаттлов и конструкций на международной космической станции.
Строительство и архитектура
Электросети и линии электропередачи переведены на алюминиевую основу, а не на медную.Это связано с отличной проводимостью и малым весом для больших длин кабелей. Алюминиевые сплавы также используются в строительстве для изготовления прочных рам, способных выдержать значительный вес больших оконных стекол. Архитекторы широко используют эти характеристики в аэропортах и высотных зданиях.
Мебель для сайта
Несмотря на то, что большая часть мебели на участке (скамейки, урны для мусора, стойки для велосипедов и т. п.) закреплена на месте, съемные болларды представляют собой устройство, направляющее движение, которое можно установить на месте, чтобы предотвратить доступ транспортных средств, или снять, чтобы открыть его.Алюминий часто используется для съемных столбов из-за легкости металла; персоналу мероприятия гораздо проще перемещаться или покидать место.
Продукты питания и напитки
Консервы и напитки — еще один рынок, на котором доминирует алюминий. Алюминиевые банки быстро охлаждаются и обеспечивают поверхность, пригодную для печати. Высокий уровень пригодности к вторичной переработке также делает алюминий привлекательным продуктом для этой отрасли. Они также защищают вкус и целостность содержимого, запечатанного внутри, благодаря защите от кислорода, света и других загрязняющих веществ.
Приборы и технологии
Бытовая техника также выиграла от свойств алюминия. Благодаря своим тепловым свойствам он идеально подходит для холодильных установок, а легкий вес позволяет легко перемещать и транспортировать приборы. С развитием отделки «матовый алюминий» можно создавать высокоэстетичные продукты для рынка высокого класса. Технологическая компания Apple лидирует в создании алюминиевых ноутбуков, которые изготавливаются из цельного блока алюминия.Телевизоры с плоским экраном также выигрывают от легкости алюминия; эквивалентное стальное изделие было бы слишком тяжелым, чтобы его можно было повесить на стену.
Автомобилестроение
Автопроизводители испытывают все большее давление, чтобы уменьшить углеродный след своих автомобилей. Легкие алюминиевые рамы, панели кузова и двигатели помогают в этом, улучшая экономию топлива. Есть и другие экологические преимущества, поскольку почти 90% автомобильного алюминиевого лома собирается для переработки.
Переработка алюминия
Большая часть алюминия может быть переработана.Банки из-под напитков и автомобильные детали — это отрасли промышленности с высоким водосбором, где материалы собираются и эффективно перерабатываются. После того, как использованный алюминий собран, он доставляется на перерабатывающее предприятие, где сортируется по сортам и очищается. Затем металл расплавляют, чтобы удалить покрытия, чернила и другие примеси. На этом этапе при необходимости могут быть добавлены сплавы, после чего он отливается в слитки. Эти слитки могут быть поставлены на литейные заводы, где они используются для литья, или переданы другим производителям для дальнейшей обработки. Переработанный алюминий можно вернуть на рынок в качестве новых продуктов всего за шесть недель.
Очистка и уход за алюминием
Большинство алюминиевых изделий можно содержать в чистоте с помощью простой воды, мягкого мыла или моющего средства. Если пятна более стойкие, можно использовать скипидар или химический очиститель, не вызывающий травления. Для большей очищающей способности можно использовать полироли на основе воска, абразивные воски или абразивные чистящие средства.Важно высушить алюминиевые изделия после очистки, чтобы избежать образования полос, а остатки очистки необходимо удалить с краев и стыков.
Для получения дополнительной информации об алюминии или запроса коммерческого предложения по индивидуальному проекту, пожалуйста, свяжитесь с нами.
Выбор подходящего сплава для ваших литых изделий
В современном литье металлов сталь и алюминий являются двумя претендентами на звание лучшего материала. Тысячи производителей по всему миру используют оба металла для производства прочных, легких и устойчивых к коррозии металлических деталей и изделий.
Вы найдете сотни различных марок и сплавов как для стали, так и для алюминия, и каждый из них имеет свои преимущества и недостатки. Для этого сравнения мы сосредоточимся на различиях между алюминиевыми и стальными сплавами в целом, а не на различиях между конкретными сплавами.
Алюминий против. Сталь: Прочность
Стальобычно прочнее алюминия, но некоторые алюминиевые сплавы прочнее некоторых видов стали. Для несущих конструктивных элементов или приложений, требующих значительной прочности для работы, сталь часто является предпочтительным выбором.Алюминий может дать преимущества в весе, но он должен быть тщательно спроектирован, чтобы соответствовать требованиям прочности.
Это видео иллюстрирует разницу в характеристиках при столкновении двух почти одинаковых кузовов грузовиков, стального и алюминиевого.
Алюминий против. Сталь: Вес
Алюминий намного менее плотный, чем сталь, как и большинство алюминиевых сплавов. На самом деле алюминий часто в 2,5-3 раза менее плотный, чем сталь. Эта более низкая плотность приводит к заметному преимуществу в весе.Алюминиевые изделия могут повысить прочность и жесткость за счет увеличения количества материала в жизненно важных областях, сохраняя при этом общий меньший вес.
Алюминий против. Сталь: коррозионная стойкость
В зависимости от конкретных рассматриваемых сплавов это совпадение может быть любым. Алюминий по своей природе обладает высокой коррозионной стойкостью и способен выдерживать длительное время на открытом воздухе и во влажной среде. Углеродистая сталь легко подвергается коррозии, и для правильной работы ее часто необходимо красить или герметизировать.Нержавеющая сталь, напротив, обладает превосходной коррозионной стойкостью не только по сравнению с углеродистой сталью, но и по сравнению с алюминием.
На самом деле распространен миф о том, что алюминий не подвержен коррозии. Это правда, что алюминий не ржавеет — красный цвет ржавчины исходит от железа в сплаве — но в кислой или щелочной среде алюминий подвергается коррозии быстрее, чем некоторые другие сплавы.
Чтобы узнать больше о коррозионной стойкости 8 популярных литейных сплавов, ознакомьтесь с нашей предыдущей публикацией в блоге о литье металлов.
Алюминий против. Сталь: Стоимость
Стоимость различных сплавов сильно различается, и мировой рынок постоянно колеблется. Сталь производится на основе железной руды, а алюминий добывается из бокситовой руды. Оба относительно распространены, но железо, как правило, дешевле в добыче. Оба металла также могут быть переработаны, часто с меньшими затратами, чем переработка нового сырья. Как правило, алюминий дешевле нержавеющей стали и дороже углеродистой стали.
Стоимость конкретного сплава во многом зависит от его состава и, как мы видим в последних новостях, политики, связанной с импортом и добычей материалов.
Алюминий против. Сталь: Термостойкость
Алюминий имеет гораздо более низкую температуру плавления, чем сталь, поэтому изделия из алюминия не такие термостойкие. В то время как сталь не плавится, пока не достигнет температуры около 2500 градусов по Фаренгейту, алюминий начинает значительно размягчаться при температуре 900 градусов по Фаренгейту. В результате сталь можно использовать в высокотемпературных приложениях, чего нельзя делать с алюминием.
Алюминий против. Сталь: Обрабатываемость
После того, как отливка извлечена из формы, она часто подвергается нескольким дополнительным процессам, чтобы подготовить ее к использованию.Машинисты просверливают отверстия, нарезают резьбу, заделывают критические участки и обычно удаляют материал, пока изделие не приобретет правильную форму.
Сталь, как правило, намного тверже алюминия. Хотя это дает преимущества в прочности и долговечности, это недостаток для механической обработки. Для обработки стали может потребоваться больше времени, и часто требуются более дорогие инструменты для резки материала.
Алюминий против. Сталь: Castability
Если вы производите литые изделия и задаетесь вопросом, что лучше — сталь или алюминий, ответ может зависеть от процесса литья, который вы хотите использовать.Алюминий имеет гораздо более низкую температуру плавления, чем сталь. Как мы уже упоминали, это свойство приводит к меньшей термостойкости. Обратной стороной является то, что алюминий гораздо лучше поддается литью, чем сталь.
Мало того, что алюминий требует меньше энергии для плавления и поддержания температуры литья, он также может быть отлит с использованием различных методов, недоступных для стали. Литье под давлением, один из самых распространенных способов литья, использует преимущественно цветные металлы: цинк, магний и алюминий.Точно так же формы для универсального процесса литья в постоянные формы часто изготавливаются из стали. Алюминий — отличный выбор для постоянного литья в формы, в то время как сплавы железа, такие как сталь, слишком горячие в расплавленном состоянии.
Заключение: алюминий против. Стальное литье
Как видите, существует множество факторов, которые необходимо учитывать, прежде чем решить, какой материал, алюминий или сталь, подходит для вашего продукта. Если вы не знаете, как поступить, лучше всего проконсультироваться со специалистом, который разбирается в кастинге и может ответить на ваши вопросы на месте.
Для получения дополнительной информации о методах литья металлов для различных сплавов и типов изделий ознакомьтесь с нашим Руководством по литью металлов и обработке на станках с ЧПУ :
Влияние температур перегрева расплава и заливки на качество литья по газифицируемым моделям из алюминиевых сплавов
Нестеров Н.В., Ермилов А.Г. Низкочастотные пульсации расплава в процессе литья по газифицируемым моделям: Часть 2, Рус. . J. Цветные металлы., 2012, том. 53, нет. 2, стр. 150–154.
Артикул Google Scholar
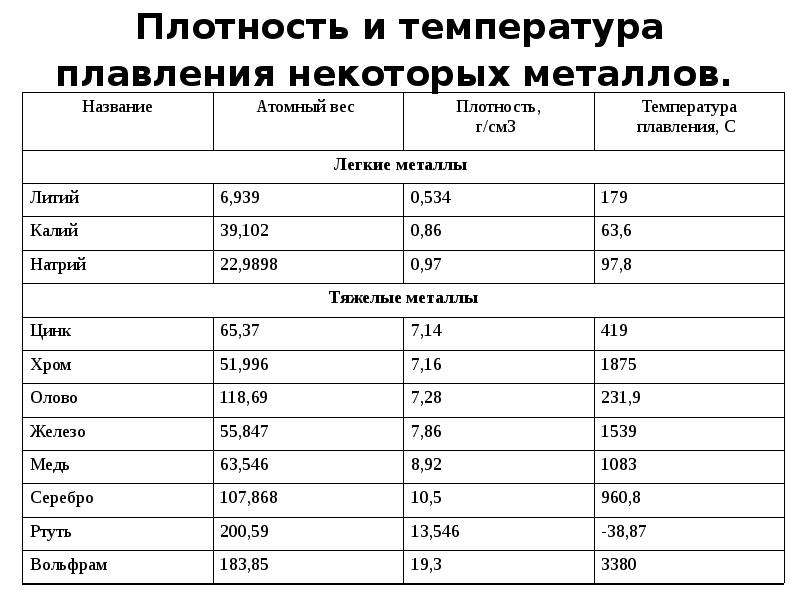
Чжан Л., Тан В. и Ху Х., Определение коэффициента теплопередачи на границе раздела металл-песчаная форма в процессе литья по газифицируемым моделям, Тепломассообмен , 2016, том . 52, нет. 6, стр. 1131–1138.
Артикул Google Scholar
Тихомирова М.И. и Клименок Е.В., Разработка технологии изготовления отливок методом литья по газифицируемым моделям, Литье Металл. , 2013, вып. 3S (72), стр. 132–137.
Google Scholar
Исагулов А.З., Куликов В.Ю., Лоран С., Твердохлебов Н.И., Щербакова Е.П. Совершенствование литья по моделям литья по газифицируемым моделям // Литейное производство. , 2014, вып. 4, стр. 16–18.
Google Scholar
Гулер К.А., Кисасоз А., Карааслан А. Исследование применения шаблона вспененного полиэтилена (ЭПЭ) при литье алюминиевых пенопластов // Рус. J. Цветные металлы. , 2015, том. 56, нет. 2, стр. 171–176.
Артикул Google Scholar
Griffiths, W.D. and Ainsworth, M.J., Поглощение водорода во время заполнения формы при литье по выплавляемым моделям алюминиевых сплавов, J. Mater. науч. , 2012, том. 47, нет. 1, стр. 145–150.
Артикул Google Scholar
Jiang, W., Li, G., Fan, Z., Wang, L., and Liu, F., Исследование характеристик интерфейса биметаллических отливок Al/Mg, обработанных методом литья по выплавляемым моделям . Металл. Матер. Транс. А , 2016, т. 1, с. 47, нет. Исс. 5, стр. 2462–2470.
Артикул Google Scholar
Гриффитс В.Д. и Эйнсворт М.J., Нестабильность поверхности раздела жидкий металл-модель в литье по газифицируемым моделям алюминиевых сплавов, Metall. Матер. Транс. А , 2016, т. 1, с. 47, нет. 6, стр. 3137–3149.
Артикул Google Scholar
Бароне, М. и Колк, Д., Анализ заполнения формы при литье алюминия по газифицируемым моделям: метод, Int. Ж. Металлолитье , 2008, т. 1, с. 2, нет. 3, стр. 29–45.
Артикул Google Scholar
Вали, К.Ф., Бхавнани, С.Х., Оверфельт, Р.А., Шелдон, Д.С., и Уильямс, К., Исследование производительности инжектора из вспенивающегося полистирола для использования в процессе литья по газифицируемым моделям, Metall. Матер. Транс. В , 2003, том. 34, нет. 6, стр. 843–851.
Артикул Google Scholar
Каримян М., Урджини А., Идрис М.Х. и Джафари Х. Влияние параметров литья на воспроизведение формы и шероховатость поверхности алюминиевого сплава LM6, отлитого с использованием технологии потерянной пены, Trans.Индийский инст. Встретились. , 2015, том. 68, нет. 2, стр. 211–217.
Артикул Google Scholar
Гулер К.А., Кисасоз А., Карааслан А. Влияние модельного покрытия и вакуумной поддержки на пористость алюминиевых отливок по выплавляемым моделям // Рос. J. Цветные металлы. , 2014, том. 55, нет. 5, стр. 424–428.
Артикул Google Scholar
Деев В.Б., Пономарева К.В., Юдин А.С. Исследование плотности моделей пенополистирола при реализации ресурсосберегающей технологии изготовления // Рос. J. Цветные металлы. , 2015, том. 56, нет. 3, стр. 283–286.
Артикул Google Scholar
Pacyniak, T. Влияние огнеупорного покрытия на процесс потери пены, Arch. Литейный инж. , 2009, вып. 9 (3), стр. 255–260.
Google Scholar
Шарифи, А. , Мансури Хасан Абади, М., и Ашири Р., Непосредственное наблюдение за влиянием плотности пены, конструкции литника и температуры заливки на процесс заполнения формы при литье по газифицируемым моделям сплава A356, в: Conf.: Proc. . Материалы TMS Ближнего Востока и Средиземноморья. Конгресс по энергетическим и инфраструктурным системам , MEMA, 2015 г., стр. 109–118.
Google Scholar
Диспинар, Д. и Кэмпбелл, Дж., Пористость, содержание водорода и бипленки в отливках из алюминиевых сплавов, Mater.науч. англ. , 2011, том. 528, нет. 10, стр. 3860–3865.
Артикул Google Scholar
Сэндс, М. и Шивкумар, С., Влияние сплавления валиков пенополистирола на образование складчатых дефектов при литье по газифицируемым моделям алюминиевых сплавов, J. Mater. науч. , 2006, том. 41, нет. 8, стр. 2373–2379.
Артикул Google Scholar
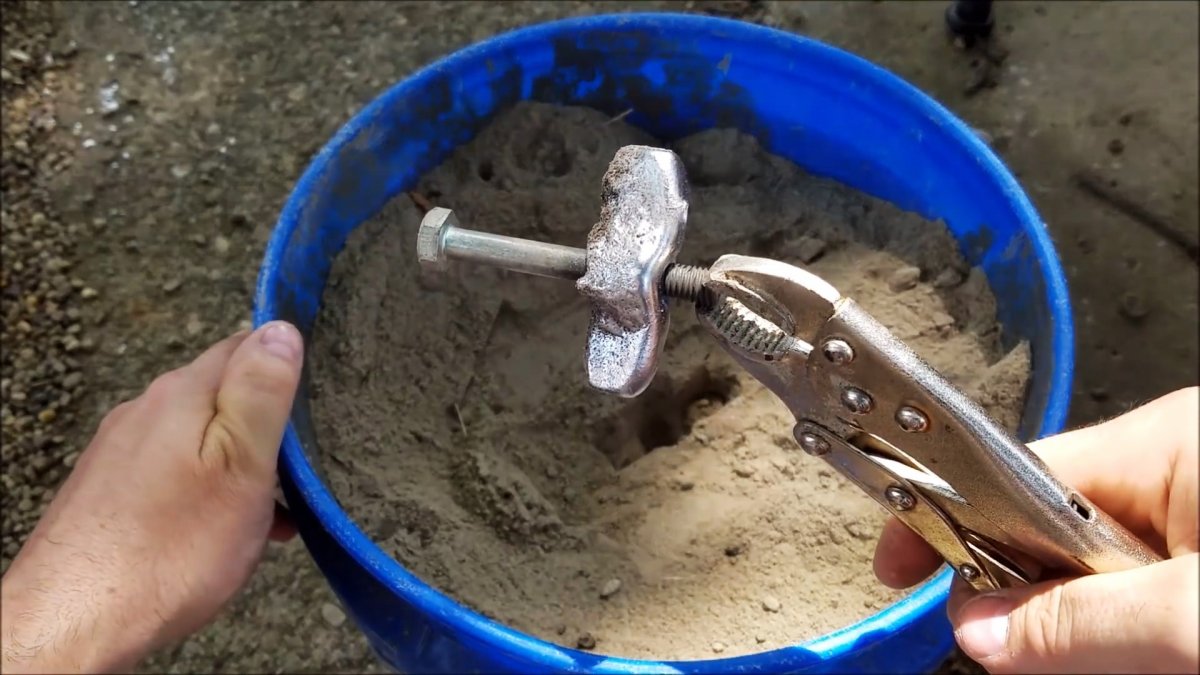
Табибиан С., Чаркалук Э., Константинеску А.и Шмытка Ф., Оценка поведения, повреждения и усталостной долговечности алюминиевых сплавов для литья по газифицируемым моделям в условиях термомеханической усталости, Procedia Eng. , 2010, том. 2, нет. 1, стр. 1145–1154.
Артикул Google Scholar
Пациняк, Т., Влияние проницаемости огнеупорного покрытия на процесс потери пены, Arch. Литейный инж. , 2008, том. 8, нет. 3, стр. 199–204.
Google Scholar
Гриффитс, В. Д. и Дэвис, П. Дж., Проницаемость покрытий с рисунком Lost Foam для отливок из алюминиевых сплавов, J. Mater. науч. , 2008, том. 43, нет. 16, стр. 5441–5447.
Артикул Google Scholar
Деев В.Б., Селянин И.Ф., Куценко А.И., Белов Н.А., Пономарева К.В. Перспективная ресурсосберегающая технология обработки расплавов при производстве литых алюминиевых сплавов. 58, вып. 11–12, стр. 1123–1127.
Артикул Google Scholar
Колонаков А.А., Кухаренко А.В., Деев В.Б., Абатурова А.А. Структура и химический состав поршневого сплава АК12ММгН, изготовленного на основе различных зарядов // Рос. J. Цветные металлы. , 2015, том. 56, нет. 4, стр. 428–433.
Артикул Google Scholar
Деев В.Б., Селянин И.Ф., Пономарева К.В., Юдин А.С., Цецорина С.А. Быстрое охлаждение алюминиевых сплавов при литье с газифицирующим стержнем // Steel Transl. , 2014, том. 44, нет. 4, стр. 253–254.
Артикул Google Scholar
Никитин В.И. Наследственность в литых сплавах , Никитин К.В. М.: Машиностроение-1, 2005.
. Google Scholar
Селянин И.Ф., Деев В.Б., Кухаренко А.В. Ресурсосберегающие и экологические технологии производства вторичных алюминиевых сплавов // Рос. J. Цветные металлы. , 2015, том. 56, нет. 3, стр. 272–276.
Артикул Google Scholar
Бранчуков Д.Н., Панфилов А.В. Новые комбинированные флюсы для рафинирования алюминиевых сплавов // Литейное производство. , 2009, вып. 1, стр. 2–5.
Google Scholar
Тен Э.Б., Рахуба Е.М., Киманов Б.М., Жолдубаева Ж.Д. Ресурсы повышения очищающей способности фильтров по жидким металлам // Литейщик России . 11, стр. 38–42.
Google Scholar
Румянцева Г.А., Немененок Б.М., Задруцкий С.П., Муравицкий А.М. Повышение экологической безопасности силуминов за счет применения малотоксичных продуктов и флюсов // Литье Металл. , 2010, вып.4 (58), стр. 77–82.
Google Scholar
Садоха М.А., Волочко А.Т. Рафинирование алюминиевых сплавов инертными газами // Литье металл. , 2012, вып. 3 (69), стр. 69–71.
Google Scholar
Грачев А.Н., Леушин И.О., Маслов К.А., Леушина Л.И. Применение шламов солевых закалочных ванн для рафинирования алюминиевых сплавов // Цветн.Встретились. , 2015, вып. 11 (875), стр. 76–79.
Артикул Google Scholar
Никитин К.В., Никитин В.И., Тимошкин И.Ю., Глущенков В.А., Черников Д.Г. Обработка расплава импульсными магнитными полями с целью управления структурой и свойствами промышленных силуминов. J. Цветные металлы. , 2016, том. 57, нет. 3, стр. 202–210.
Артикул Google Scholar
Никитин К.В., Амосов Е.А., Никитин В.И., Глущенков В.А., Черников Д.Г. Теоретическое и экспериментальное обоснование обработки расплавов на основе алюминия импульсными магнитными полями. J. Цветные металлы. , 2015, том. 56, нет. 6, стр. 599–605.
Артикул Google Scholar
Прусов Е.С. Свойства литейных композиционных сплавов на основе алюминия, армированных эндогенными и экзогенными фазами, Рос.Металл. , 2011, вып. 7, стр. 670–674.
Артикул Google Scholar
Прусов Е.С. Влияние повторных переплавов на формирование структуры отливок из алюминиевых матричных композиционных сплавов // Металл. 2013. Тр. 22-я межд. конф. по металлургии и материалам , 2013, вып. 1, стр. 1152–1156.
Google Scholar
Иванов Ю.Ф., Алсараева К.В., Громов В.Е., Попова Н.А., Коновалов С.В. Усталостная долговечность силумина, обработанного высокоинтенсивным импульсным электронным пучком // J. Surf. Вкладывать деньги. Рентгеновские, синхротронные и нейтронные методы , 2015, т. 1, с. 9, нет. 5, стр. 1056–1059.
Артикул Google Scholar

Иванов Ю.Ф., Алсараева К.В., Громов В.Е., Коновалов С.В., Семина О.А. Эволюция структуры поверхности сплава Al–19.4Si после электронно-лучевой обработки и многоцикловой усталости.науч. Технол. (Великобритания) , 2015, том. 31, нет. 13а, стр. 1523–1529.
Артикул Google Scholar
Селянин И.Ф., Деев В.Б., Белов Н.А., Приходько О.Г., Пономарева К.В. Физические модифицирующие эффекты и их влияние на кристаллизацию литейных сплавов // Рос. J. Цветные металлы. , 2015, том. 56, нет. 4, стр. 434–436.
Артикул Google Scholar
Литье под высоким давлением | Базовый процесс литья алюминия под давлением
Basic Aluminium использует процесс литья под высоким давлением с использованием машин с холодной камерой.Определение литья под высоким давлением эффективно охватывает фазу сжатия или интенсификации процесса впрыска металла, когда давление алюминия превышает 10 000 фунтов на квадратный дюйм. Машины для литья под давлением с холодной камерой — это машины, в которых дробовая гильза, в которую заливается металл перед впрыском, не нагревается.
Процесс плавки алюминия
Литье под давлением требует, чтобы алюминий был хорошо нагрет до жидкой фазы для впрыска. Температура плавления алюминия конкретно зависит от его сплава, но обычно полная жидкая фаза достигается при температуре выше 1100 градусов по Фаренгейту.Температура алюминия обычно должна быть на несколько сотен градусов выше, чтобы гарантировать сохранение химического состава сплава.
Basic плавит алюминий в центральных отражательных печах, работающих на природном газе. Компания Basic использует слиток, приобретенный у сертифицированных плавильщиков алюминия, а также повторно расплавляет лишний материал в процессе литья. Химический состав сплава регулярно проверяется, чтобы убедиться, что химический состав металла соответствует спецификациям сплава.
После расплавления и нагрева до нужной температуры алюминий подается на каждую машину для литья под давлением. Basic использует запатентованный метод фильтрации для удаления примесей и оксидов из жидкого алюминия, когда алюминий выкачивается из отражательной печи.
Каждая машина для литья под давлением имеет собственную печь для выдержки, которая поддерживает температуру расплавленного алюминия в ожидании использования в машине для литья под давлением.
Процесс литья под давлением
Когда машина для литья под давлением готова к следующему циклу (матрица закрыта, готовая к выстрелу), автоматический ковш отбирает заданный объем расплавленного алюминия из раздаточной печи и заливает его в рукав дроби.После завершения заливки начинается фаза впрыска.
Первая фаза впрыска — это фаза медленного впрыска, когда плунжер впрыска движется вперед с низкой скоростью, чтобы начать выталкивать воздух из рукава и двигаться мимо заливного отверстия в рукаве. После заданного расстояния, в зависимости от настройки процесса, плунжер переходит в фазу промежуточной скорости, где скорость увеличивается, чтобы заполнить литниковую систему алюминием. Как только это завершено, машина переходит в фазу быстрого выстрела, когда скорость значительно увеличивается, чтобы заполнить полость детали алюминием.
После заполнения полости детали и прекращения движения плунжера гидравлический цилиндр, толкающий плунжер, подвергается более высокому давлению. Эта фаза интенсификации или сжатия требует давления алюминия более 10 000 фунтов на квадратный дюйм, чтобы обеспечить надлежащее заполнение и свести к минимуму проблемы с усадкой алюминия.
Фаза затвердевания
Машина для литья под давлением продолжает удерживать половинки штампа вместе с номинальным весом во время фазы затвердевания. Литые штампы охлаждаются водой или маслом для отвода тепла от расплавленного алюминия во время затвердевания.Машина также поддерживает давление интенсификации, чтобы свести к минимуму усадочную пористость по мере затвердевания алюминия. По истечении заданного времени (когда отливка достаточно затвердела и остыла), пресс-форма открывает эжектор или подвижную половину пресс-формы.
Удаление деталей
Когда машина полностью открыта, срабатывает выброс литья под давлением. Литые штампы имеют выталкивающие штифты, проходящие через полость детали. Эти штифты установлены в пластине выталкивателя на задней части инструмента для литья под давлением. Эта пластина приводится в действие гидравликой машины для литья под давлением.
После полного выталкивания отливки удаляются с помощью автоматизированной машины или 6-осевого робота. Затем это устройство переносит литье под давлением в охлаждающее оборудование, где деталь доводится до температуры, подходящей для последующих операций.
Это охлаждение может быть достигнуто с помощью воздушного охлаждения с приводом от вентилятора или закалки деталей водой. Закалка снижает температуру литья быстрее, но процесс необходимо контролировать, чтобы предотвратить деформацию детали.
Смазка штампа
После того, как отливка вынута из инструмента для литья под давлением, другая часть оборудования автоматически смазывает матрицу. Эти смазки предназначены для литья под давлением и обычно представляют собой смесь специальных силиконов, эмульгаторов и воды. Эта смазка служит как для охлаждения поверхности штампа до надлежащей температуры для следующего цикла, так и для создания пленки на поверхности штампа, которая позволяет снять деталь.
После завершения машина для литья под давлением закрывается и готова к следующему циклу.
The Basic Aluminium Castings Company * Cleveland OH * 216-481-5606
.
