Страница не найдена
05 Сентября 2012 | Просмотров: 239893
Вы можете перейти на главную страницу сайта или воспользоваться простым или визуальным поиском.Возможно Вас заинтересует
Пред След Страница:
Лучшие шаровые опоры ВАЗ 2110-12
Просмотров:28110
Шаровые опоры — еще один важный элемент подвески автомобиля за состоянием которого нужно следить. Качественная шаровая опора –…
Ремонт бардачка ВАЗ 2110
Просмотров:36291
Замечали, как со временем становится все тяжелее открыть бардачок ВАЗ 2110, особенно зимой. Иногда в…
Лада Калина рестайлинг
Просмотров:9268
В августе на Московском международном автосалоне АвтоВАЗ представил новую Лада Калина.
Перетяжка панели автомобиля
Просмотров:58272
Самый сложный этап перетяжки салона авто. Его следует оставить на последний момент, чтобы сначала «набить»…
Подробно о турбине на ВАЗ
Просмотров:68568
Один из способ добавить лошадиных сил мотору — установить турбонаддув. Почему именно турбина ? Чтобы ответить…
Что такое винтовая подвеска и какие о ней отзывы
Один из популярных способов тюнинга автомобиля считается его занижение. Для этого подвеску дорабатывают разными методами, например, спиливают пружины (чего делать нерекомендуется), ставят комплект заниженной подвески, устанавливают пневмоподвеску или используют подвески с…
Инвертор из бесперебойника своими руками
Автомобильный инвертор (преобразователь 12v в 220v) является незаменимым аксессуаром не только в походе или на даче, но и в дальней дороге.
Мало кто знает, что можно не покупать готовое устройство,…
Популярные ключевые слова (ТОП 50)
Интересный сайт? Поделись с друзьями
Как делают карбоновые детали — Как это сделано, как это работает, как это устроено — LiveJournal
Оригинал можно посмотреть здесь.Был у одного нашего заказчика такой проект: сделать линейку техники с корпусами из углеродного волокна. Лёгкие, прочные, красивые — сплошные плюсы. Только цена кусается. Вот и командировали меня на разведку: узнать как бы сделать то же самое, но подешевле.
Честно говоря, я ни разу до этого не видел, как производятся подобные вещи, и даже не представлял себе всю технологию. Поэтому сразу и с удовольствием взялся за задачу.
Но оказалось, что попасть на завод не так просто. Два производителя под разными предлогами отказались встречаться на производстве и настойчиво звали к себе в офис. У третьего офис и производство были в одном здании, и я недолго думая поехал к нему.
Завод выглядит вполне прилично, меня проводят в переговорную-шоурум.
От разнообразия образцов разбегаются глаза: карбоновый велосипед, детали для авто и мототюнинга, всякие штуковины непонятного назначения.
Целиковый капот для BMW — мечта пацанов с раёна.
Иногда в карбоновую ткань вплетают цветные нити: красные или синие, выглядит очень необычно.
Детали, покрашенные целиком, сразу и не отличишь от обычных. Обычно спортсмены так делают: им нужен низкий вес, а не понты 🙂
Мотошлем.
И нечто, неизвестно для чего нужное.
Но главной целью моего визита, было вот это:
Чехол для iPad. Меня интересовал не сам чехол, конечно, а похожие на него штуки: детали для корпусов телефонов, ноутбуков, планшетов. Было важно разобраться в технологии произодства, понимать, как правильно их проектировать, чтобы это было максимально дешево и технологично. Поэтому после долгих переговоров и уговоров я всё-таки напросился на экскурсию по цеху.
Производство занимает один этаж здания, тут чисто, но довольно пустынно.
Карбоновое полотно с нанесенным клеящим слоем поступает в рулонах. Оно бывает разной толщины, с разным рисунком плетения. Хранится в специальных холодильниках.
Ткань нарезается на куски по выкройке, и наклеиваются в несколько слоёв на матрицу. Матрицы бывают лёгкими, из чего-то типа пластика и с увеличенным ресурсом, из алюминия.
Матрицы, идущие в работу раскладываются прямо на полу, каждая в своём секторе.
Сам процесс наклейки карбона был расположен за стеклянными дверьми, но мне наотрез отказались его показывать, мол страшная коммерческая тайна. Но я не думаю, что там есть что-то секретное, просто вырезают ножницами, и укладывают лоскутки в форму.
После этого каждую деталь упаковывают в вакуумные пакеты.
Откачивают из пакетов воздух и загружают в одну из двух печей, побольше или поменьше.
Готовые детали извлекают из матриц. Если деталь сложной формы, то и матрица для неё будет сложносоставной, из нескольких частей.
Контроль качества перед сдачей на склад.
Как вы догадываетесь, это не весь процесс. Теперь у деталей нужно обрезать края и покрасить их лаком. Но это делается на другой площадке, у субподрядчика. Предлагали поехать посмотреть, но я отказался — вот там уж точно ничего нового.
Ой, вом же наверное интересно узнать про цены? Так вот, карбоновый чехольчик на iPad стоит с завода 25 долларов. А велосипед — несколько тысяч. Улыбаться перестанешь, как говорит один мой знакомый. И вариантов снижения особо не видать, слишком мелкосерийное производство, слишком много ручного труда.
Карбоновые мелочи. Делаем салон спортивнее
24.07.2016,
Любая даже самая мелкая и незначительная деталь может придать общей композиции определенное направление. Вроде бы мелочь, а внешний вид изменит и композиции повернет из классики в спорт.
Например, некоторые детали интерьера отделанные деревом придадут салону классический строгий вид с теплыми оттенками. Сидя в таком салоне не возникает желания срываться со светофора или выгонять машину на загородный трек, чтоб обкатать авто на пределе возможностей. А вот алюминиевая ручка кпп или рычаг ручного тормоза, алюминиевые элементы в панели приборов, тут же подвигают вас вести себя более агрессивно на дороге, резко разгоняться, мгновенно останавливаться, перемещаться в рядах на грани штрафа или притирки с другим авто. С чем это связано? Все просто — с восприятием спортивной атмосферы, созданной собственными руками, даже если все остальное стоит стандартное.
Многие не раз видели обычную машину без какого-либо тюнинга, агрессивно ведущую себя на дороге, и переделки на ней только некоторые надписи брендов производителей тюнинг-аксессуаров или маркировкой GT или GTI и прочее. Подумать только, какие-то надписи, а как меняют поведение. Что уж говорить, если в салоне будут стоять вместо «родных» сидений — спортивные ковши, алюминиевая или карбоновая отделка элементов, пусть даже и пленка, дополнительные выводы приборов на панель и тд. Но почему отделка карбоном увязывает со спортом? Психологи бы ответили, что карбон современный материал, а мир автоспорта любит высокотехнологичные «фишки», поэтому то, что новое в этой области, то автоматически становится в тренде и влечет за собой определенные прослойки общества, особенно определенную возрастную категорию.
Карбон — не только спорт
Однако, карбоновые детали в салоне — это не только спортивно, это прежде всего практично. Ибо материал очень легок, прочен, долговечен и достаточно красив. Им вполне возможно отделать салон классического седана или внедорожника, дабы подчеркнуть статус владельца, обновить потертые детали или освежить интерьер. Можно подобрать различную фактуру плетения нити различные цвета, комбинировать их в рамках общей концепции. В зависимости от структуры рисунка, салон можно сделать более классическим или более спортивным.
Надо сказать, что сама ткань представляет собой материал из углеродных нитей, покрытых эпоксидной смолой. При изготовлении определенной детали, слои ткани накладываются друг на друга, делая изделие максимально прочны и при этом незнаничетельно увеличивая его вес. В мире большого автоспорта, карбон повсеместно применяют для увеличения прочности конструкции и облегчения веса автомобиля. Например, кузов Lamborghini Aventador представляет собой карбоновый монокок с навешанным на него оборудованием. Внешние детали кузова тоже из карбона.
Что отделывают карбоном?
Естественно таким материалом сидения и потолок отделывать не будешь. Но вот элементы этих деталей вполне подходят. Например, панель управления подсветкой салона или люка на потолке, вполне пригодная для отделки карбоном, тем более что это места постоянно прикосновения не только водителе, но и пассажиром, ногти которого зачастую царапают стандартную обшивку и приводят через некоторое время в неприглядный вид. Или же ставки на панели приборов, молдинги, ручку кпп и ручного тормоза, руль, подлокотник, крышки различных ниш, ручки открывания дверей и консоль стеклоподъемников, а также панели сидений и кнопки управления положением сидений.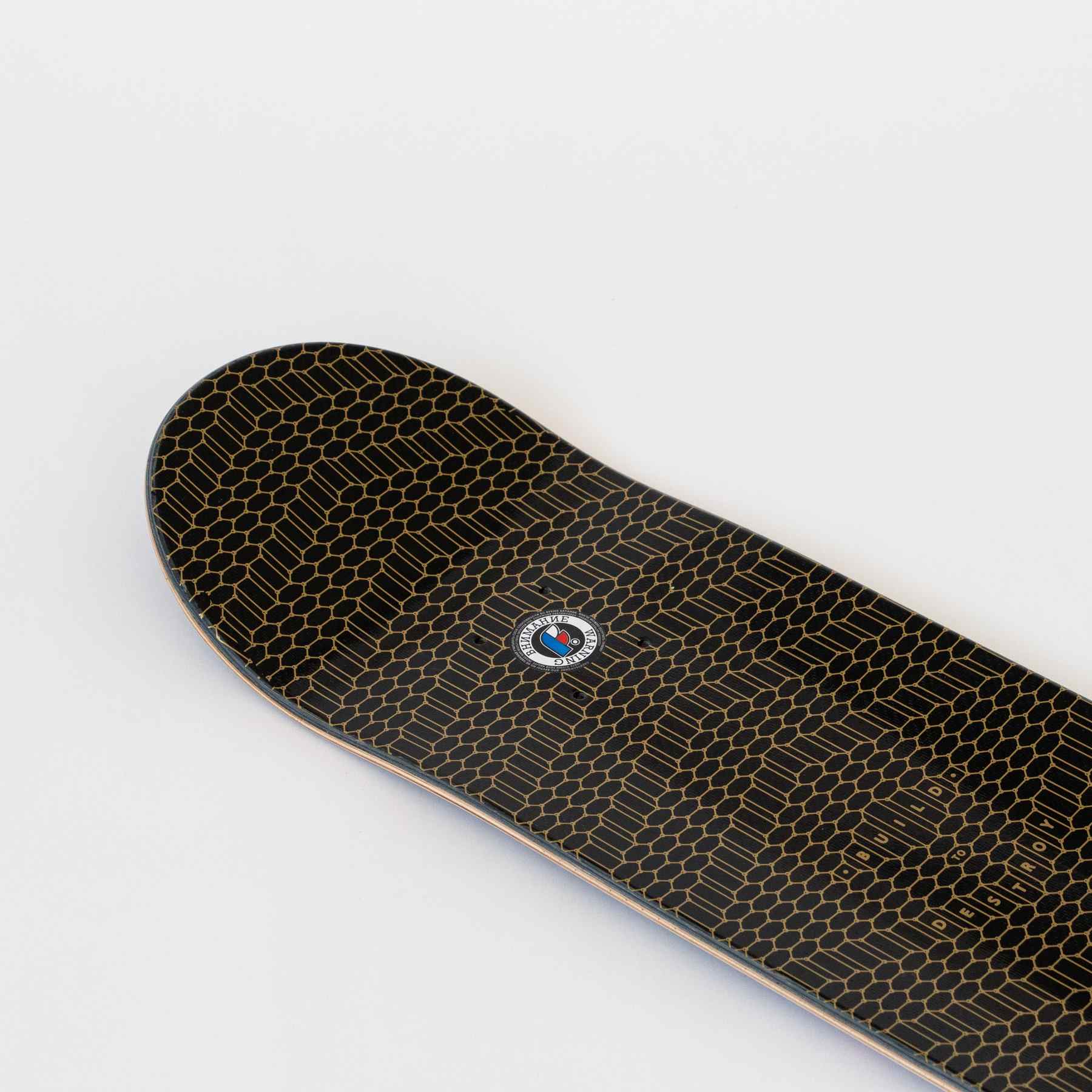
Где достать вожделенные аксессуары?
Авторынок предлагает множество вариаций карбоновых деталей для различных авто, однако моделей много, вкус у автомобилиста различный и на всех не угодить. Тем более, что производители предлагают готовые решения, только для самых популярных моделей, а если ваш автомобиль в их число не входит, то придется основательно поискать.Как вариант, выступают компании, производящие элементы на заказ, но и у них ограниченное число матриц и возможно под вашу модель, придется делать новый шаблон, а это существенно удорожает стоимость изделия (в разы). Обиднее всего, что изготовление матрицы оплачиваете вы, а ей потом пользуется компания изготовившая вам деталь, совершенно бесплатно.
Выход — изготовить все самому. Этот путь не менее тернист, чем предыдущие, однако она вам даст определенные умения и навыки, если конечны вы ими еще не владеете. При чем, данные навыки в будущем помогут вам зарабатывать приличные деньги.
Карбоновые детали своими руками
Самый простой и распространенный способ привнести карбоновые нотки в собственный салон — это нанести на готовые детали карбоновую ткань.
После высыхания наносим финишный слой.Важно! Если пузыри все таки образовались, то выгнать их можно паяльной лампой, но выгнать их необходимо обязательно, ибо он в последствии разрушит деталь. После окончательно высыхания, необходимо очистить наждачной бумагой место прогревания паяльной лампой (на случай если пришлось применять) и все тщательно отполировать.
Для получения качественной детали необходимо наносить минимум 4 слоя смолы. Если вы нb разу этим не занимались, то необходимо сперва начать максимально прямых и не сложных деталей, дабы набить руку и испортить материала.
P.S. Если получилось, что деталь получилась не очень удачная или вы ее испортили, не стоит отчаиваться. Достаточно положить ее в морозилку на несколько часов, потом легка скрутить ее и слой отвалится, а далее повторяем действие, только уже более осторожно.
Арт, станки и мебель из карбона. Как устроена первая «ТехТочка Кипения»
19.04.2019
В конце марта на «Ивановской композитной мануфактуре» открылась первая в России технологическая «Точка кипения». В отличие от 20 других «Точек», в «ТехТочке» развернется полный цикл производства изделий из композитных материалов, а также образовательная программа по обучению новым специальностям для детей и взрослых.
Кирилл Игнатьев
В 2017 году в Иванове открылась первая «Точка кипения», она стала третьей по счету в сети после московской и питерской «Точек». Спустя два года вы открываете вторую – технологическую «Точку кипения». Зачем она нужна городу и как взаимодействуют «ТехТочка» и «Ивановская композитная мануфактура», на площадке которой она расположена?
Кирилл Игнатьев: Мы решили открыть технологическую «Точку», потому что в какой-то момент осознали, что в сообществе растет запрос на практическую повестку. В первой «Точке кипения» проводятся в основном образовательные мероприятия, люди приходят туда общаться, работать в зоне коворкинга. И со временем площадки и возможностей «Точки» стало не хватать, многие активные участники сообщества, в том числе стартаперы, технологические предприниматели, стали уходить оттуда и запускать свои проекты на других площадках. Тогда мы подумали, почему бы нам не открыть новое пространство, где люди смогут делать что-то руками, заниматься практической деятельностью, реализовывать свои проекты. Так родилась идея создания «ТехТочки» – места, где воплощаются замыслы.
Что касается взаимодействия с мануфактурой, то в первую очередь это единое пространство, объединяющее повестку «Точки кипения» и задачи технологического бизнеса. Мы создали атмосферу производственного коворкинга, абсолютно новый подход к производственной среде. Люди, которые здесь работают, которые заказывают продукцию, которые приходят на мероприятия, видят как работает современный технологический бизнес и как устроена новая технологическая среда.
Сергей Лебедев (первый справа)
Сергей Лебедев: Добавлю, что мы все начинали делать одновременно и с нуля – и работу над мануфактурой, и проектирование «Точки кипения». Еще прошлым летом на площадке не было практически ничего, сегодня же на мануфактуре есть все условия и возможности для полного цикла производства, начиная с инжиниринга и заканчивая финальной сборкой.
В чем особенность производства на мануфактуре?
К.И.: Главная особенность и преимущество производства – в его гибкости. В течение дня и даже считанных часов, практически в онлайн-режиме мы можем поменять производственный процесс и вместо, например, лонгбордов начать делать кресла. Эта гибкая рыночная модель, на мой взгляд, станет в определенном смысле вечной, поскольку мы производим тот продукт, на который есть спрос здесь и сейчас. Чем лучше мы выстроим IT-систему и управление, тем быстрее мы сможем менять формат производства и тем выгоднее это производство будет. Эту модель можно в дальнейшем распространить на любую технологию. Мы не работаем в парадигме прошлого, когда для каждой группы продуктов были отдельные фабрики – обувные, мебельные, текстильные – отдельное оборудование, станки и т.
Именно гибкость организации бизнеса – главный смысл, который мы будем транслировать в «ТехТочке».
Как устроен процесс производства? Какие продукты вы уже производите на ИКМ и планируете в будущем?
К.И.: Производство полностью цифровизовано, все наши сотрудники работают на планшетах, фактически у наших рабочих нет начальников, вместо них – программа дня, технологическая карта на планшете, в соответствии с которой рабочие выполняют задания. Цифровизация доведена даже до ручного труда. У нас нет мастеров и менеджеров среднего звена. Есть директор ИКМ и рабочие.
Так мы создали первое в России цифровизованное предприятие по производству изделий из композитных материалов. Эта модель может масштабироваться на другие рынки, поэтому делать «ТехТочку» именно в Иванове очень правильно, поскольку мы можем показывать возможности производства.
Мы осуществляем кастомизированное производство в штучном режиме. Среди наших продуктов композитные карбоновые лонгборды и скейтборды. Другой проект выстроенный в аналогичной логике с точки зрения кастомизации, – люксовый карбоновый чемодан. Сейчас мы отрабатываем палитру финишей и окрашивание металлов, корпусов, отделку кожей. Палитра будет широкой и можно будет собрать практически любой чемодан.
Другое направление – мебель. Мы запускаем линейку офисной мебели в нескольких вариантах дизайна – столы, кресла, стулья, стойки на ресепшн.
Еще одно направление – прочные и легкие транспортные кейсы из композитных материалов. Они пользуются высоким спросом, поскольку заявленные характеристики позволяют экономить на перелетах и не переживать за безопасность перевозимого груза.
Мы производим корпуса для роботизированных комплексов – кронштейны для камер, которые используют для съемок на стадионах, в экстремальных условиях, где важна прочность и надежность конструкции.
И еще один важный проект – городской складной велосипед, который в будущем мы планируем сделать электрическим.
Сколько человек будет работать на мануфактуре и в «Точке»?
К. И.: Сейчас на мануфактуре работают 15 специалистов, в какой-то момент мы планируем ввести ночную смену и тогда количество рабочих удвоится. В «ТехТочке» будут работать трое – два администратора и программный директор.
Какие цели и задачи стоят перед технологической «Точкой кипения»?
С.Л.: Первая задача – привлечь молодежь и показать на наглядных примерах, как устроено технологическое производство. На примере открытой в 2017 году первой «Точки кипения – Иваново» мы видим, что и школьникам, и студентам очень интересен подобный формат. Мы решили спроектировать пространство таким образом, чтобы наши посетители могли сразу осваивать теорию и практику. Например, основная производственная площадка и цех финальной сборки расположены между лекционным залом и офисным пространством, поэтому на лекции о производственном цикле того же лонгборда мы можем в буквальном смысле развернуть аудиторию на 180 градусов и показать процесс сборки, проиллюстрировав таким образом теорию. Это и есть слияние практики и знаний.
То есть школьники и студенты смогут участвовать в производственном процессе?
С.Л.: Да, под руководством наставников они смогут что-то сделать своими руками и таким образом понять, нравится им та или иная профессия, хотят ли они этим заниматься в будущем или нет.
Какие профессии они могут освоить?
С.Л.: Мы даем им возможность попробовать себя во всех профессиях, представленных на мануфактуре. Самые востребованные – это оператор станка с ЧПУ (числовое программное управление) и формовщик. Анализ рынка труда показал, что в Иванове практически отсутствуют молодые специалисты по этим направлениям, квалифицированным специалистам было в основном за 50 лет. Тогда мы решили зайти с другой стороны и выяснить, где готовят нужные нам кадры. Выяснилось, что операторов станка с ЧПУ готовят в Вичугском многопрофильном колледже. Наша команда познакомилась с директором и попросила порекомендовать наиболее толковых ребят, которых мы могли бы взять к себе на мануфактуру. А дальше, после колледжа, к нам пришли работать двое выпускников, одного из них сразу же отправили на стажировку в Москву в инжиниринговое бюро «КБ Архипов».
Также у нас есть кожевенник, работающий над проектом, который уже упомянул Кирилл, над умным чемоданом с элементами интернета вещей. Среди них геолокация, функция определения веса, зарядка для телефона. Внутренняя часть чемодана отделана хорошей кожей или алькантарой – отделочным материалом, известным как искусственная кожа. Наш кожевенник делает лекала, выклеивает внутреннюю часть. Этот род деятельности ребята также могут попробовать.
Другая востребованная профессия – формовщик. На мануфактуре мы производим изделия из карбона, и совсем недавно в Ивановской области с этим материалом практически никто не работал. И мы опять же вынуждены были самостоятельно набирать ребят, учить их, отправлять на стажировки. Изначально мы думали о том, чтобы пригласить уже работающих специалистов из Москвы, Санкт-Петербурга или Екатеринбурга, но в итоге решили воспитать своих. И сейчас на нашей мануфактуре работают только специалисты из Иванова.
Почему вы решили работать именно с карбоном?
С.Л.: Это легкий и прочный материал, применяется практически везде, начиная с медицины и заканчивая космосом. Конечно, это достаточно затратное производство, поэтому мы говорим, что у нас современное производство, рассчитанное на кастомизированную продукцию. В основном это небольшие заказы, даже если мы договариваемся с каким-то предприятиями.
Несмотря на гибкость производства, вы сейчас ограничены в выборе материала?
К.И.: Сейчас мы работаем с углепластиками, но это не значит, что завтра мы не начнем работать с кевларом или графеном. Потенциально мы можем использовать любой материал. Спрос на технологию композитного производства достаточно долгосрочен. Но по нашим прогнозам на горизонте 7-8 лет вряд ли появятся более дешевые технологии. Более того технология уже стала значительно дешевле, 15 лет назад, когда были запущены первые композитные производства для авиапрома и космической отрасли, это было очень затратная история. Сегодня производство из композитов стало гораздо более экономичным. В этом смысле мы как страна, конечно, отстаем от стран-лидеров в области композитного производства, например, Германии и Италии, поскольку позже начали, но мы зато выигрываем у этих стран по себестоимости производства.
Вы говорите, что основная задача – привлечь школьников и студентов. Планируете ли вы работать со взрослыми?
К.И.: В образовательных мероприятиях могут участвовать все: и школьники, и студенты, и взрослые. К тому же наша площадка полностью открыта: чтобы попасть на мероприятие, достаточно зарегистрироваться на портале Leader-ID.
Почему вы решили создать новое пространство, а не, скажем, снять складское помещение, ведь это было бы дешевле?
С.Л.: Я считаю, что надо приобщать людей к прекрасному, показывать им, как должно быть. Если есть возможность сделать хорошую и красивую мануфактуру с интеграцией передовых производственных технологий, ее нужно делать, а не загонять людей на склад.
К.И.: У нас очень креативное производство, на площадке мануфактуры мы проводим выставки современных художников, это комиксы, картины, карикатуры. Арт-среда по задумке должна вдохновлять людей. Выставки будут регулярно меняться. Мы привозим картины, арт-объекты из других стран и городов, которые жители Иванова никогда бы здесь не увидели. На креатив людей вдохновляет что-то новое и это новое должно проявляться и в том, что они видят вокруг.
#Точка кипения, #Ивановская область
виды, плюсы и минусы материала
Рано или поздно облик новой, горячо любимой вещи все-таки поднадоедает, или изменяется не в лучшую сторону. Поэтому «голову хозяев» в один прекрасный момент посещает идея изменить его, причем лучше почти до неузнаваемости, кардинально. И в этом случае на помощь приходят удобные, практичные материалы — разнообразные пленки, работа с которыми относительно легка и не отнимает много времени. Если говорить только об автолюбителях, то у них уже довольно давно появился свой фаворит — изделие под карбон. Чтобы понять, почему оно быстро завоевало «бешеную» популярность, секрет его привлекательности надо раскрыть. И попутно узнать, что такое карбоновая пленка, оценить ее плюсы и минусы, а также целесообразность оригинальной отделки железного друга данным материалом.
Что такое карбон?
Прежде чем переходить непосредственно к пленочному материалу, в большей мере используемому в тюнинге автомобилей, нужно рассмотреть оригинал — настоящий углепластик, или карбонопластик. Это композит — материал, изготовленный из нескольких видов сырья.
Карбон — это инновационный материал: он представляет собой полотно из углеродных нитей с добавлением эпоксидных смол и каучуковых волокон. Особенность материала — его оригинальная, узнаваемая текстура, причина — уникальное переплетение нитей. Самым популярным вариантом до сих пор остается «елочка».
Сферы применения углепластика
Сейчас карбон используется в тех отраслях, где необходимы материалы эластичные, суперпрочные, но максимально легкие. Например, углепластик стал незаменимым в авиационной и космической промышленности, при производстве протезов. Автомобилестроение — еще одна «сфера деятельности» углепластика. Поскольку материал этот дорогой, используют его только для моделей премиум-класса: из карбона изготавливают ручки АКП, вставки для руля, панелей и другие декоративные элементы.
Спорт — еще одна область применения углепластика. Карбон активно используют для отделки салонов и корпуса гоночных болидов, из него изготавливают основные детали мотоциклов, катеров, снегоходов и т. д. В этом случае основным достоинством материала является сочетание «минимальный вес и легкость». Карбон легче алюминия и стали: на 20% и 40% соответственно. Однако в прочности он не уступает ни одному сплаву.
Недостатки карбона
Его высокая цена — самый существенный минус почти безупречного материала, если говорить о автовладельцах, страстно желающих изменить вид своего «коня». По этой причине тюнинговать автомобиль дорогим карбоном позволить себе могут далеко не все, причем смысла в таких тратах многие владельцы в России попросту не видят. Основание для этих сомнений одно: это другой недостаток натурального материала.
Оригинальный карбон имеет «ахиллесову пяту»: это невозможность противостоять точечному сильному воздействию. Даже небольшой камень, вылетевший из-под колеса едущего автомобиля, способен стать причиной замены карбонопластикового элемента, который при наших «чудесных» (в большинстве регионов) дорогах превратится в очень дорогое удовольствие. Восстановлению поврежденные детали не подлежат.
Еще один огромный минус оригинального карбонопластика — его нелюбовь к солнечным лучам. Если владельцы привыкли оставлять средство передвижения на улице, то вскоре карбоновые детали потеряют первоначальный цвет.
Знакомство с карбоновой пленкой
Желание иметь прекрасное оформление, не нежелание отдавать за относительно хрупкую красоту большую сумму вполне резонно. Поэтому вскоре после углепластика на рынке появилась карбоновая пленка — альтернатива, которая, наоборот, доступна всем. Внешне она практически неотличима от дорогого оригинала, но может быть прозрачной, с характерным рисунком, или цветной. Эта имитация состоит из 3 слоев.
- Клеевая основа. Это основа для материала, ее задача — обеспечивать максимально качественное сцепление с оклеиваемыми поверхностями.
- Декоративный слой. Это практически полная имитация настоящего карбона. У бюджетных образцов разницу в материалах не понять визуально. Дорогие пленки под карбон способны «обмануть» даже при тактильном контакте.
- Защитное покрытие. Оно предохраняет изделие практически от всех механических повреждений, от грязи, осадков.
Поскольку спрос на этот чудо-материал неуклонно растет, на рынке регулярно появляются новые производители. Не вся «новоприбывшая» продукция имеет высокое качество, однако есть фирмы, успевшие создать себе безупречную репутацию. К ним можно с полным правом отнести Hexis, Suntek, 3M, Eclat, Graphjet.
Основы изделий под карбон
Изучение карбоновой пленки на этом не заканчивается, так как в роли ее основы может выступать или винил, или полиуретан. Выбор полимера важен: тип основы влияет на качества (толщину, надежность) материала и на его стоимость.
- Поливинилхлорид. Средняя толщина покрытия — 100 микрон. Этот полимер отличается невысокой ценой, но обратная сторона «медали» — его недолговечность. Виниловое покрытие может относительно быстро выгореть на солнце. К тому же не исключено его пожелтение из-за частого контакта с противогололедными реагентами. Этот материал прочен, но если все же поверхность была повреждена, переклеивать придется весь элемент. Плюс — быстрое схватывание, не требующее времени на просушку. Средний срок службы «винило-карбона» составляет 3 года.
- Полиуретан. Эти карбоновые изделия новинки, так как «классика» — обычная прозрачная антигравийная защита из ПУ. Толщина таких пленок — от 150 до 300 микрон. Многие уже знакомы с этим материалом, широко применяемым в строительстве. Пленка на полиуретановой основе прочна, в том числе из-за большей толщины. Такие изделия максимально стойки к ультрафиолету, а также к различным механическим повреждениям (даже острыми предметами), поэтому прослужат как минимум 5 лет, максимум — 10.
Недостаток у ПУ есть: это высокая цена продукции из-за сложности технологии изготовления. Если сравнивать эти изделия с винилом, то полиуретановая карбоновая пленка обойдется в 4-5 раз дороже.
Еще один минус полиуретана — необходимость оклеивать автомобиль целиком. Этот материал способен пропускать ультрафиолетовое излучение, поэтому изменение цвета лакокрасочного покрытия будет очень заметно, особенно после снятия пленки.
Для чего используется карбоновая пленка?
Из настоящего карбона изготавливается только определенный набор элементов. Для спортивных, гоночных болидов производят большое количество кузовных деталей, для машин в массовом сегменте карбон используют для создания спойлеров, обвесов и декоративных элементов салонов.
Карбоновая пленка в этом случае более универсальна. Ее можно наклеивать на любую часть автомобиля — на кузов, на пластиковые элементы, в том числе и в салоне. Чаще всего автолюбители используют пленку для защиты:
- дверных ручек и пластика зеркал заднего вида;
- дверей, капота, крыши;
- крышки багажника.
Большинство автомобилистов не забывают оклеить самый «тяжело эксплуатируемый» элемент в салоне — «многострадальную» торпеду.
Карбоновая пленка: плюсы и минусы
Прежде чем принять окончательное решение насчет целесообразности покупки, всегда знакомятся с преимуществами и недостатками материала, причем любого. Карбоновая пленка, которую приобретают для преображения средств передвижения, ноутбуков, смартфонов и мебели, не исключение.
Начинать принято с плюсов, и здесь именно главное достоинство многими воспринимается как недостаток. Речь идет о кардинальном изменении внешнего вида автомобиля. Некоторым владельцам он безумно нравится. Другие автолюбители, наоборот, не в восторге: они считают такое оформление проявлением «дурновкусия».
Преимущества «недокарбона»
Теперь о том, что действительно можно считать плюсами карбоновых пленок. К этой категории относится:
- Защита лакокрасочного покрытия от ультрафиолета.
- Шанс скрыть незначительные дефекты поверхности кузова.
- Простой уход за покрытием. Материал не боится ни «душа», ни автомобильных шампуней.
- Способность защитить автомобиль от различных видов угрозы — от механических повреждений, от мелких камней, песка, осколков стекла и т. д.
- Предохранение кузова от контакта с «агрессивно настроенными» веществами: например, с химикатами, предназначенными для борьбы с гололедом.
- Достаточно долгий срок эксплуатации: высококачественная карбоновая пленка способна служить до 5-7 лет, и не требовать замены или регулярного «латания дыр». Некоторые изделия умеют самовосстанавливаться.
- Практичность, удобство пленки под карбон. Сюда относится скорость преображения автомобиля (мебели, техники), сравнительная простота работы, а также быстрое снятие материала, который удаляется, не оставляя ни малейшего следа.
Главное же преимущество этих альтернативных изделий — вполне «удобоваримая» цена. Для достижения лучшего результата при оклеивании все-таки рекомендуют использовать профессиональный инструмент. И это можно считать первым минусом данной продукции.
Недостатки пленки под карбон
Второй минус — требование к объекту. Лучше оклеивать новую машину, так как невозможно предсказать, как поведет себя пленочная замена карбона. Она может дать два противоположных результата: либо успешно скрыть имеющиеся недостатки, либо сделать их более заметными.
Другие претензии в большей мере относятся к низкокачественной продукции. Главный из них — недолговечность. Такая карбоновая пленка прослужит недолго: покрытие может преподнести неприятный сюрприз уже через несколько месяцев. Чтобы не столкнуться с подобными изделиями под карбон, лучше отдавать предпочтение пленкам средней либо высокой ценовой категории.
Виды композитной пленки
Теперь надо рассмотреть карбоновый материал, принимая во внимание именно качество продукции. Разновидностей карбоновой пленки существует несколько. Отличаются они качеством, а значит, и ценой. Самый недорогой вариант — однотонная матовая или глянцевая продукция.
- Изделия, имеющие индекс 2D. Это тоже простая продукция, так как имитацию легко обнаружить при первом же прикосновении к поверхности. Причина — декоративный слой-рисунок, представляющий собой плоскую, двухмерную картинку. Его наносят на стандартную основу — глянцевую или матовую.
- Пленки класса 3D. Они имитируют не только «выразительную внешность» карбона, но и его оригинальную текстуру. Чтобы обеспечить такой эффект, в декоративный слой добавляют рельефные элементы. Результат их «работы» — видимое изменение поверхности при взгляде на материал с разных углов.
- Продукция 4D. Ее без преувеличения можно назвать профессиональной. Если в пленках 3D за объемность отвечают узкие рельефные полоски, то в этих изделиях их заменяют полусферические элементы, позволяющие передать текстуру оригинального карбона максимально точно. Карбон 4D практически невозможно найти в розничной продаже.
Его заказывают в специализированных магазинах либо в фирмах, занимающихся тюнингом автомобилей.
Существуют еще 3 разновидности карбоновых пленок — 5D, 6D и 7D. Это самые качественные изделия, покрытые несколькими слоями лака. С одной стороны, такие пленки гарантируют полную защиту поверхностей. Однако из-за стоимости их логичнее приобретать для отделки салонов.
Ни для кого не секрет, что высокому качеству всегда соответствует такая же цена. Сохранить часть денег позволяет практичный способ. Например, детали, которые находятся на виду, декорируют дорогим видом материала — 4-7D. Другие поверхности, менее бросающиеся в глаза, закрывают более дешевыми пленками.
Отдельно надо сказать об отличиях изделий разных производителей. Для 3D-пленок, которые выпускает компания Eclat, характерна более низкая зернистость, даже в сравнении с аналогичной продукцией Graphjet и 3M. Поэтому при выборе рекомендуют всегда знакомиться с демонстрационными образцами. Только так можно объективно оценить вид и текстуру материала.
Как наклеивают карбоновую пленку?
Способов существует два — сухое и влажное оклеивание. Перед операцией обязательно проводят подготовку. Поверхности, на которые будет приклеиваться карбоновая пленка, моют, а затем обезжиривают. В помещении для работы обеспечивают оптимальный температурный режим (от 15 до 20°).
Чтобы минимизировать риск попадания под покрытие пыли или грязи, процедуру рекомендуют проводить в малярной камере. После завершения преображения автомобиля ему необходимо сделать перерыв в работе. На улицу машину лучше «выпустить» только через 24 часа, независимо от вида основы пленки.
Главное, на что необходимо обратить внимание при наклеивании пленки, — корректный раскрой материала. Поэтому перед началом операции определяют общее направление рисунка, так как куски, которые будут «смотреть» в разные стороны, машину не украсят, а, наоборот, «изуродуют».
Сухой метод
В этом случае пленку во время операции нагревают строительным феном. Цель процедуры — придание ей эластичности. Эта работа достаточно сложна, поэтому ее лучше доверить профессионалам. Противопоказания — сильная коррозия и крупные дефекты кузова.
После тщательной очистки и обезжиривания выбранных участков автомобиля ждут, пока поверхности высохнут. Вырезанные элементы с припуском на загиб (5 мм) примеряют вместе с подложкой, затем избавляются от нее и прикладывают пленку к автомобилю.
Материал аккуратно разглаживают от центра к краям с помощью резинового ракеля (либо широкого, но не металлического шпателя). Пузыри ни в коем случае не прокалывают. После завершения этого этапа нагревают поверхность строительным феном. Подгибы тщательно проклеивают герметиком.
Влажный способ
При наклеивании используют либо мыльный раствор, либо парогенератор. Оба варианта дают шанс избавить поверхности от пыли и грязи, которая помешает сцеплению (адгезии) материалов. Однако мыльный раствор используют чаще.
После подготовки и примерки деталей переходят к обработке поверхности. Ее опрыскивают мыльным раствором из пульверизатора, потом с заготовки снимают подложку и прикладывают к поверхности, потом, немного натягивая, фиксируют на «законном месте».
Вооружаются ракелем, разглаживают пленку. Если образовались пузыри, то проблемный участок отклеивают, затем этап повторяют. После того как от дефектов удалось избавиться, поверхность прогревают феном, а подгибы аналогично фиксируют герметиком. Сутки — время, которое необходимо дать на высыхание пленочного покрытия.
Существуют еще два способа, позволяющих получить эффект, который называют «под карбон». Аквапечать — процесс, при котором пленка соединяется с поверхностью с помощью давления струи воды. Этот вариант невозможно повторить самостоятельно, зато он дает шанс покрыть пленкой детали любых сложных форм и размеров. Аэрография — второй способ имитации текстуры карбона, но здесь не участвует пленка. Используется большое количество слоев краски, но результат не всегда и не совсем оправдывает ожидания.
Что надо учесть?
Такие операции кажутся совершенно простыми, однако свои особенности есть у любой работы. Перед оклейкой кузова нужно узнать некоторые детали.
- Оптимальное расстояние от фена до поверхности составляет 20 см. Главное — гарантировать равномерный прогрев. Перегрева надо, наоборот, избегать.
- После завершения работы приклеенную пленку еще раз прогревают. Цель — активизация клеевого состава. Поверхность протирают только сухой салфеткой.
- Сушка в среднем занимает сутки, на этот период и лучше ориентироваться. Если возникнет необходимость в мытье автомобиля, то с этой процедурой лучше повременить. «Принять душ» машина сможет лишь спустя неделю после операции.
Нередко для защиты и преображения автомобиля выбирают именно карбоновую пленку, так как она кажется самым подходящим вариантом. Однако если нет уверенности в том, что мастер сможет выполнить оклейку безупречно, то лучше обратиться к профессионалам. В этом случае автовладельца, скорее всего, не разочарует качество работы.
Простая ли процедура изменение облика машины с помощью карбоновой пленки? Чтобы ответить на этот вопрос, можно самим потренироваться на подходящих (но не автомобильных) поверхностях. Однако для этого необходимо будет купить рулон пленки, длина-минимум у компаний отличается. «По чуть-чуть» этот материал, как правило, не продают.
С ценами на карбоновые пленки можно познакомиться здесь:
Те мастера, что уже сталкивались с такой работой, утверждают, что лучше переложить ее на «плечи» автоателье. Однако тем, кто загорелся этой идеей, не помешает увидеть, как другие «расправляются» с автомобилем. Например, представление о грядущей работе даст этот оцененный ролик:
Видео загружается…
Покрытие карбоновым волокном.
Тщательная подготовка оклеиваемой поверхности: зашкуривание, обезжиривание, скругление углов.
Нанесение адгезива.
Склеивание углеволокна с пропитыванием эпоксидной смолой с отвердителем.
Сушка.
Покрытие краской.
Наполнители для смолы используют как для придания декоративности, так и для предотвращения стекания смолы с вертикальных поверхностей.
Необходимые материалы
Адгезив для фиксации углеткани на поверхности.
Ткань из углеволокна, которую укладывают на смолу послойно, с прикатыванием твердым валиком.
Эпоксидная смола средней вязкости с отвердителем (иногда она используется в качестве адгезива).
Защитный лак. Лучше всего для защиты от царапин подходит полиуретановый. Нужно выбирать водостойкий и светостойкий.
Он не помутнеет. Для высокого блеска в качестве финишного покрытия можно использовать акриловый лак.
Смолу наносят 2-3 раза с промежуточной сушкой и шлифовкой.
Этот метод отличается от традиционного изготовления карбоновых изделий по моделям нанесением адгезива, а не разделителя для легкого съема получившегося полуфабриката.
Компания 3М предлагает даже самоклеющееся углеполотно, но работа с ним требует хороших навыков.
И карбон остается на оклеиваемой детали, упрочняя ее. Этот метод чаще всего используется для оклеивания бампера, приборной панели и пр.
Метод формования в форме с вакуумом
Нанесение разделительного состава на поверхность модели. Для матовых и полуглянцевых поверхностей обычно применяется разделительный воск, а для глянцевых поверхностей(пластик и металл) — разделитель типа WOLO и растворы для грунтования, которые используются при мелкосерийном призводстве.
Выкладывание углеткани в матрицу, без морщин и пузырей.
Пропитка углеткани смолой.
Слоев может быть несколько. В некоторых случаях углеткань можно чередовать со стеклотканью.
Наложение перфорированной пленки для отжима излишков смолы и выхода воздуха. Желательно укладывать внахлест.
Прокладка впитывающего слоя.
Установка вакуумной трубки и порта для подключения вакуумного насоса.
Помещение всей конструкции в прочную вакуумную пленку, приклеивание герметизирующим жгутом к оснастке.
Вся процедура напоминает помещение какого-либо предмета в вакуумный пакет, которые продаются в магазинах для хранения вещей, с последующей откачкой из него воздуха. Можно, кстати, поэкспериментировать с такими вакуумными пакетамий. Они очень прочные и продаются разных размеров. А вакуумный насос для домашнего использования обойдется в среднем в 200$.
Метод формования с помощью давления
Применяется для самостоятельного изготовления деталей из карбона и аналогичен методу формования вакуумом, но без использования дорогостоящей оснастки. Наборы включают кисти для нанесения смолы и валики для выдавливания воздуха и прикатки слоев.
Для простого тюнинга автомобиля понадобятся:
углеполотно плотностью 200-300 г/м,
эпоксидная смола,
отвердитель,
жесткий валик и кисть.
На поверхность формы наносится разделительный воск для формирования защитно-декоративного слоя на поверхности готового изделия. После его высыхания кистью наноситсяэпоксидная смесь для углепластика и начинается выкладка углеткани.
Каждый слой прокатывается валиком для удаления пузырьков воздуха и получения максимального сцепления. После полного высыхания на воздухе или в термошкафу деталь извлекается из матрицы, шлифуется, покрывается защитным лаком.
При таком методе получается высокий расход смолы (в три раза выше плотности углеполотна), но зато именно таким способом можно изготовить любую деталь из карбона своими руками.
Изготовление кивка для зимней рыбалки своими руками
Изготовление кивка (сторожка) для зимней рыбалки – это важная часть подготовки к ловле рыбы, ведь этот элемент снасти сигнализирует о поклевке, и от него зависит игра мормышки. Если правильно выбрать материал, то изготовление самодельных зимних кивков не составит сложностей даже для новичков.
Из чего можно делать кивки для зимней рыбалки
При самостоятельном изготовлении кивка для зимней рыбалки можно использовать пластик, металл, жесткую леску, карбон, шерсть кабана и т.д. При выборе материала стоит учитывать его жесткость: мягкий подойдет для ловли рыбы в стоячей воде, а для участков с интенсивным течением потребуется жесткий кивок. Ориентироваться следует и на вес приманки: чем он выше, тем жестче должен быть сторожок.
Самодельный кивок из пластика
Пластиковые кивки — самые простые в исполнении, но подходящий материал подобрать непросто. Лучшей считается лавсановая пленка, которая держит форму даже в морозы. Для изготовления зимних кивков подойдут и обычные пластиковые бутылки, но такие изделия быстро приходят в негодность.
Металлические сторожки делают из тонких стальных пластин или пружинок и применяют для мормышечных удочек. Такие кивки отлично подходят для мелкоамплитудной и высокочастотной ловли, главное – не «переборщить» с длиной, иначе хорошей игры не добиться.
Кивки из карбона своими руками изготовить непросто, ведь, придавая изделию нужный вид, его легко повредить или сломать. Но итоговый результат стоит всех усилий: сторожок хорошо держит заданную форму, не деформируется и обеспечивает стабильную игру.
Кивки из лески и кабаньей щетины сделать проще, но они весьма специфичны и подходят только для насадочной мормышки.
Самостоятельное изготовление кивка для зимней рыбалки
Подобрав подходящий материал для кивка, необходимо вырезать из него длинную пластину, которая сужается к одному краю. Широкую заднюю часть можно оставить без изменений, а узкую следует сточить, чтобы ее толщина составляла 1-2 мм. На тонком кончике нужно проделать небольшое отверстие раскаленной иглой (для пластика) или припаять к нему тонкое маленькое колечко (для металла).
Изготавливая кивок из лески или щетины кабана, главное – надежно присоединить один конец щетинки к держателю, а из второго сформировать петлю и закрепить ее кембриком.
На рыбалке самодельные боковые кивки ни в чем не уступают покупным и даже превосходят их по чувствительности.
Разобравшись, как сделать удочку с боковым кивком, и вооружившись подходящей палаткой для зимней рыбалки, например, палаткой Нельма-2, можно смело отправляться на водоем и рассчитывать на хороший результат.
Как производить детали из углеродного волокна
Композитные материалы, такие как пластмассы, армированные углеродным волокном, являются универсальными и эффективными материалами, стимулирующими инновации на различных рынках от аэрокосмической до здравоохранения. Они превосходят традиционные материалы, такие как сталь, алюминий, дерево или пластик, и позволяют изготавливать высокопроизводительные легкие изделия.
В этом руководстве вы узнаете основы производства деталей из углеродного волокна, включая различные методы и способы использования 3D-печати для снижения затрат и экономии времени.
Информационный документЗагрузите этот информационный документ с рекомендациями по проектированию композитных форм и пошаговыми инструкциями по методам препрега и ручного ламинирования для создания деталей из углеродного волокна.
Загрузить информационный документКомпозитный материал — это комбинация двух или более компонентов, характеристики которых отличаются от этих отдельных компонентов сами по себе. Инженерные свойства обычно улучшаются, такие как добавленная прочность, эффективность или долговечность. Композиты состоят из армирования — волокна или частицы — удерживаемого вместе матрицей (полимером, металлом или керамикой).
Армированные волокном полимеры (FRP) доминируют на рынке и способствуют росту новых применений в различных отраслях промышленности. Среди них углеродное волокно — широко используемый композит, в частности, для самолетов, гоночных автомобилей и велосипедов, поскольку он более чем в три раза прочнее и жестче, чем алюминий, но на 40% легче. Он состоит из армированного углеродного волокна, соединенного с эпоксидной смолой.
Волокна могут быть сплетены однонаправленно и стратегически выровнены для создания прочности по отношению к вектору.Перекрестно переплетенные волокна можно использовать для создания прочности в нескольких векторах, и они также отвечают за фирменный стеганый вид композитных деталей. Обычно детали производятся с их комбинацией. Доступно несколько типов волокон, в том числе:
Стекловолокно | Углеродное волокно | Арамидное волокно (кевлар) |
---|---|---|
Самое популярное волокно Легкое, умеренное растяжение и прочность на сжатие Низкая стоимость и простота для работы с | Самое высокое соотношение прочности и жесткости к весу в отрасли (предел прочности на растяжение, сжатие и изгиб) Дороже, чем другие волокна | Более высокая стойкость к ударам и истиранию, чем углеродное волокно Низкая прочность на сжатие Трудно резать или обрабатывать |
Смола используется для удержания этих волокон вместе и создания жесткого композита.Хотя можно использовать сотни типов смол, вот самые популярные из них:
Смола | Плюсы | Минусы | Отверждение |
---|---|---|---|
Эпоксидная смола | Максимальная прочность Самый легкий вес Самая длинная полка срок службы | Самая дорогая Чувствительность к соотношению компонентов смеси и колебаниям температуры | Использует специальный отвердитель (двухкомпонентная система) Некоторые эпоксидные смолы требуют тепла |
Полиэстер | Простота использования (наиболее популярна) Устойчивость к ультрафиолетовому излучению Самая низкая стоимость | Низкая прочность и коррозионная стойкость | Отверждается с катализатором (MEKP) |
Сложный виниловый эфир | Сочетает в себе характеристики эпоксидной смолы и стоимость полиэфира Лучшая устойчивость к коррозии, температуре и удлинению | Более низкая прочность, чем у эпоксидной смолы и стоимость выше, чем у полиэстера Ограниченный срок хранения | Отверждается с катализатором (МЕКП) 9 0030 |
Производство армированных волокном полимеров, таких как детали из углеродного волокна, представляет собой искусный и трудоемкий процесс, используемый как в единичном, так и в серийном производстве.Время цикла составляет от одного часа до 150 часов в зависимости от размера и сложности детали. Обычно при производстве стеклопластика непрерывные прямые волокна соединяются в матрице с образованием отдельных слоев, которые накладываются слой за слоем на конечную деталь.
Свойства композита определяются как материалами, так и процессом ламинирования: способ включения волокон сильно влияет на характеристики детали. Термореактивным смолам придают форму вместе с арматурой в инструменте или форме и отверждают, чтобы получить прочный продукт.Доступны различные методы ламинирования, которые можно разделить на три основных типа:
При мокрой укладке волокно разрезают и укладывают в форму, затем наносят смолу с помощью кисти, валика или пистолета-распылителя. Этот метод требует большого количества навыков для создания высококачественных деталей, но это также наименее затратный рабочий процесс с минимальными требованиями для начала изготовления деталей из углеродного волокна своими руками. Если вы новичок в производстве деталей из углеродного волокна и еще не оборудовали его, мы рекомендуем начать с ручного ламинирования мокрым слоем.
Посмотрите видео, чтобы увидеть, как работает процесс мокрой укладки при ламинировании деталей из углеродного волокна.
При ламинировании препрега смола вводится в волокно впереди. Предварительно пропитанные листы хранят в холоде, чтобы предотвратить отверждение. Затем слои затвердевают в форме под действием тепла и давления в автоклаве. Это более точный и повторяемый процесс, поскольку количество смолы регулируется, но это также самый дорогой метод, который обычно используется в высокопроизводительных приложениях.
При формовании RTM сухое волокно вставляется в форму, состоящую из двух частей. Форма закрывается зажимом перед тем, как под высоким давлением нагнетать смолу в полость. Обычно он автоматизирован и используется для крупносерийного производства.
Поскольку качество пресс-формы напрямую влияет на качество готовой детали, изготовление инструмента является критическим аспектом производства FRP. Большинство форм изготавливаются из воска, пены, дерева, пластика или металла с помощью обработки с ЧПУ или вручную. Хотя ручные методы очень трудозатратны, обработка с ЧПУ по-прежнему является сложным и трудоемким рабочим процессом — особенно для сложных геометрических форм — а аутсорсинг, как правило, требует больших затрат и требует длительного времени на выполнение заказа.Оба варианта требуют квалифицированных рабочих и предлагают небольшую гибкость при изменении дизайна и корректировки пресс-формы.
Аддитивное производство предлагает решение для быстрого изготовления форм и моделей с низкими затратами. Использование полимерной оснастки в производственных процессах постоянно растет. Замена металлических инструментов пластиковыми деталями, напечатанными собственными силами, — это мощное и экономичное средство сокращения времени производства при одновременном расширении гибкости дизайна. Инженеры уже работают с деталями из полимерной смолы, напечатанными на 3D-принтере, для изготовления приспособлений и приспособлений для поддержки таких методов, как намотка нити или автоматическая укладка волокна.Аналогичным образом, мелкосерийные печатные формы и матрицы используются при литье под давлением, термоформовании или формовании листового металла для доставки небольших партий продукции.
Для 3D-печати с настольных компьютеров требуется ограниченное количество оборудования, что упрощает рабочий процесс. Профессиональные настольные принтеры, такие как Form 3, доступны по цене, просты в установке и могут быстро масштабироваться в соответствии со спросом. Производство больших инструментов и форм также возможно с помощью широкоформатных 3D-принтеров, таких как Form 3L.
Стереолитография (SLA) Технология 3D-печати позволяет создавать детали с очень гладкой поверхностью, что очень важно для пресс-формы.Он позволяет создавать сложные геометрические формы с высокой точностью. Кроме того, библиотека смол Formlabs содержит технические материалы с механическими и термическими свойствами, которые хорошо сочетаются с производством форм и моделей.
3D-печатные формы для производства деталей из углеродного волокна могут снизить затраты и сократить время выполнения заказа.
Для мелкосерийного производства инженеры могут напрямую распечатать пресс-форму с небольшими затратами и в течение нескольких часов без необходимости вырезать ее вручную или иметь дело с оборудованием с ЧПУ; Программное обеспечение CAM, наладка станка, оснастка, инструмент и удаление стружки.Значительно сокращаются трудозатраты и сроки изготовления пресс-форм, что позволяет быстро изменять дизайн и настраивать детали. Они могут создавать сложные формы с мелкими деталями, которые было бы трудно изготовить традиционными методами.
Студенческая команда Формулы Берлинского технического университета (FaSTTUBe) изготовила десяток деталей из углеродного волокна для гоночных автомобилей. Инженеры в команде вручную наносят ламинат на форму, непосредственно напечатанную с помощью смолы Formlabs Tough 1500. Эта смола характеризуется модулем упругости при растяжении, равным 1.5 ГПа и удлинение при разрыве 51%. Он не только прочный и поддерживающий во время укладки, но и достаточно гибкий, чтобы отделить деталь от формы после отверждения.
Испытательный стенд FaSTTUBe с установкой производства деталей из углеродного волокна.
Хотя этот метод не связан с интенсивными условиями отверждения, другие процессы ламинирования часто связаны с более высокими давлениями и температурами. Компания DeltaWing Manufacturing использует высокотемпературную смолу для создания компонентов воздушного потока посредством процесса препрега.Смола High Temp Resin имеет температуру теплового отклонения (HDT) 238 ° C при 0,45 МПа и способна выдерживать тепло и давление автоклава. Компания DeltaWing Manufacturing напрямую печатает пресс-формы для производства серии из 10 деталей по индивидуальному заказу.
Воздуховод крыла из углеродного волокна рядом с двухкомпонентной формой, напечатанной с использованием высокотемпературной смолы, произведенной DeltaWing Manufacturing.
Полимерные формы, напечатанные на 3D-принтере, являются отличным инструментом для оптимизации мелкосерийного производства. Однако их срок службы сокращен по сравнению с традиционными формами, что делает их непригодными для массовых серий.
Для увеличения производства DeltaWing Manufacturing печатает модели пресс-форм с помощью высокотемпературной смолы, а затем заливает их в смолу. Печать рисунка также является мощной альтернативой для процессов ламинирования, требующих интенсивных условий отверждения, которые не подходят для форм, напечатанных на 3D-принтере. Производители могут печатать индивидуальные выкройки по запросу и при этом исключить один шаг из своей техники изготовления форм — изготовление выкройки.
Производство армированных волокном полимеров — увлекательный, но сложный и трудоемкий процесс.Использование 3D-печатных форм и шаблонов позволяет предприятиям упростить рабочий процесс, расширить гибкость и возможности проектирования, а также сократить расходы и время выполнения заказа.
На основе тематических исследований с TU Berlin и DeltaWing Manufacturing в нашем техническом документе представлены три рабочих процесса для использования 3D-печати в производстве композитов с быстрым изготовлением пресс-форм и шаблонов.
5 фактов о производстве углеродного волокна своими руками
5 Что нужно знать о DIY Carbon Волокно Изготовление . В Интернете можно найти всевозможные видеоролики, в которых объясняется, как самому сделать DIY детали из углеродного волокна в домашних условиях.Мы бы никогда никого не отговорили от этого. Фактически, многие наши покупатели до изготавливают сделай сам для . Но мы бы предостерегли людей, которые не знакомы с миром композитных материалов, не торопитесь. В эпоху современных видеотехнологий любой может сделать любой процесс простым. Но для каждого из тех видеороликов « чтобы o легко быть правдой», которые вы найдете на YouTube, было много часов работы, которые не вошли в финальную версию.В конце концов, продюсеры видео не хотят, чтобы вы видели их неудачи. Ниже приведены пять вещей, которые вам следует знать о изготовлении углеродного волокна своими руками , если вы планируете изготавливать детали самостоятельно в домашних условиях. Знайте , что вы всегда можете обратиться к Rock West Composites за сырьем. У нас есть углеродные волокна, панели, трубы и т. Д. У нас также есть на выбор .1. Это не так просто, как кажется. Первое, что нужно понять, это то, что изготовление углеродного волокна не так просто, как кажется. Если бы это было так, все бы это делали. В таких компаниях, как наша, не было бы необходимости, потому что наши клиенты могли изготавливать свои собственные детали. Правда в том, что процесс изготовления сложен. Это также точный процесс, который не оставляет места для ошибок. Вы действительно должны знать, что делаете. 2. Углерод Волокно — неправильное употребление Термин «углеродное волокно» на самом деле неправильное.То, что мы называем углеродным волокном, на самом деле является пластиком, армированным углеродным волокном (CFRP). Это готовый продукт, в котором ткань из углеродного волокна сочетается с эпоксидной смолой, которая при нагревании соединяется с вместе , образуя единый материал. Таким образом, теннисная ракетка из углеродного волокна технически является пластиковой теннисной ракеткой. Пластиковый материал усилен тканью из углеродного волокна. 3. У вас должен быть инструмент. В нашей отрасли пресс-формы называются to ols.Мы упоминаем об этом, потому что вам понадобится какой-то to ol для изготовления ваших деталей дома. Допустим, вы хотите сделать замену крыла для того классического автомобиля, который вы пытаетесь заменить. Вам понадобится какой-то to ol на to p, из которого вы можете уложить несколько слоев углеродного волокна.
Как производится углеродное волокно?
Сырье, используемое для производства углеродного волокна, называется прекурсором.Около 90% производимых углеродных волокон производится из полиакрилонитрила (ПАН). Остальные 10% сделаны из искусственного шелка или нефтяного пека. Все эти материалы представляют собой органические полимеры, характеризующиеся длинными цепочками молекул, связанных вместе атомами углерода. Точный состав каждого прекурсора варьируется от одной компании к другой и обычно считается коммерческой тайной.
В процессе производства используются различные газы и жидкости. Некоторые из этих материалов предназначены для взаимодействия с волокном для достижения определенного эффекта.Другие материалы предназначены для того, чтобы не вступать в реакцию или предотвращать определенные реакции с волокном. Как и в случае с прекурсорами, точные составы многих из этих технологических материалов являются патентованными.
Процесс изготовления углеродных волокон частично химический, а частично механический. Прекурсор вытягивается в длинные пряди или волокна, а затем нагревается до очень высокой температуры, не позволяя ему вступать в контакт с кислородом. Без кислорода волокно не может гореть. Вместо этого высокая температура заставляет атомы в волокне сильно вибрировать до тех пор, пока большинство неуглеродных атомов не будет вытеснено.Этот процесс называется карбонизацией, и в результате остается волокно, состоящее из длинных, тесно связанных цепочек атомов углерода, и остается лишь несколько неуглеродных атомов.
Хотя у ZOLTEK есть свои коммерческие секреты, мы также стремимся способствовать более широкому пониманию углеродного волокна как идеального материала для коммерческого использования.
Стабилизатор
Перед карбонизацией волокон их необходимо химически изменить, чтобы преобразовать их линейную атомную связь в более термически стабильную лестничную связь.Это достигается путем нагревания волокон на воздухе примерно до 390-590 ° F (200-300 ° C) в течение 30-120 минут. Это заставляет волокна улавливать молекулы кислорода из воздуха и изменять структуру их атомных связей. Стабилизирующие химические реакции сложны и включают несколько этапов, некоторые из которых происходят одновременно. Они также генерируют собственное тепло, которое необходимо контролировать, чтобы избежать перегрева волокон. В коммерческих целях для процесса стабилизации используется различное оборудование и методы. В некоторых процессах волокна протягиваются через ряд камер с подогревом.В других случаях волокна проходят через горячие валки и через слои сыпучих материалов, удерживаемых во взвешенном состоянии потоком горячего воздуха. В некоторых процессах используется нагретый воздух, смешанный с определенными газами, которые химически ускоряют стабилизацию.
Карбонизация
После того, как волокна стабилизируются, их нагревают до температуры примерно 1,830-5,500 ° F (1,000-3,000 ° C) в течение нескольких минут в печи, заполненной газовой смесью, не содержащей кислорода. Недостаток кислорода предотвращает сгорание волокон при очень высоких температурах.Давление газа внутри печи поддерживается выше, чем давление наружного воздуха, а точки входа и выхода волокон из печи герметизированы, чтобы не допустить попадания кислорода. Когда волокна нагреваются, они начинают терять свои неуглеродные атомы, а также несколько атомов углерода в виде различных газов, включая водяной пар, аммиак, монооксид углерода, диоксид углерода, водород, азот и другие. Когда неуглеродные атомы вытесняются, оставшиеся атомы углерода образуют прочно связанные углеродные кристаллы, которые ориентированы более или менее параллельно длинной оси волокна.В некоторых процессах используются две печи, работающие при двух разных температурах, чтобы лучше контролировать скорость нагрева во время карбонизации.
Обработка поверхности
После карбонизации волокна имеют поверхность, которая плохо сцепляется с эпоксидными смолами и другими материалами, используемыми в композитных материалах. Чтобы волокна лучше склеивали, их поверхность слегка окисляется. Добавление атомов кислорода к поверхности обеспечивает лучшие свойства химического связывания, а также травит и делает поверхность шероховатой для улучшения механических свойств связывания.Окисление может быть достигнуто путем погружения волокон в различные газы, такие как воздух, диоксид углерода или озон; или в различных жидкостях, таких как гипохлорит натрия или азотная кислота. На волокна также можно нанести электролитическое покрытие, сделав волокна положительным выводом в ванне, заполненной различными электропроводящими материалами. Процесс обработки поверхности необходимо тщательно контролировать, чтобы избежать образования крошечных дефектов поверхности, таких как ямки, которые могут вызвать повреждение волокна.
Калибр
После обработки поверхности волокна покрываются покрытием для защиты от повреждений при намотке или плетении.Этот процесс называется калибровкой. Материалы покрытия выбираются таким образом, чтобы они были совместимы с клеем, используемым для формирования композитных материалов. Типичные материалы покрытия включают эпоксидную смолу, полиэстер, нейлон, уретан и другие.
Волокна с покрытием наматываются на цилиндры, называемые бобинами. Бобины загружаются в прядильную машину, и волокна скручиваются в пряжу различных размеров.
Ben’s Car Blog
Углеродное волокно всегда привлекало меня. С эстетической точки зрения, в хорошо сделанном изделии есть что-то особенное; как солнце ловит ткань, подчеркивая странно приятный, бесконечно повторяющийся узор.С функциональной точки зрения детали, изготовленные из композитных материалов, настолько же прочны, насколько красивы. Если вы когда-нибудь брали в руки готовую карбоновую деталь, вы понимаете, что я имею в виду, когда говорю, что трудно представить что-то настолько прочное, но при этом такое легкое!
Хотя углеродное волокно как материал существует в той или иной форме десятилетиями, только недавно материалы стали достаточно доступными и доступными для любителей выходного дня. Когда в начале 2000-х годов у меня появилась моя первая машина, углеродное волокно было материалом, предназначенным для более дорогих автомобилей класса люкс и спортивных автомобилей, а также для автоспорта.Сегодня каждый, у кого есть небольшой интерес и свободное время, может производить свои запчасти в своем гараже!
Строго говоря, существует огромное количество разнообразных «композитных» материалов, которые можно использовать — кевлар, стекловолокно и т. Д., А также их разновидности «pre-preg» (в которых эпоксидная смола предварительно пропитана материал), но для целей этого руководства я собираюсь сосредоточиться исключительно на необработанном углеродном волокне и использовать его для снятия шкур (обертывания) существующих деталей.
Карбоновая пленка / пленка
Skinning — это именно то, на что это похоже — использование углеродной композитной ткани и создание «оболочки» для существующей детали.Хотя этот процесс теоретически очень похож на обертывание виниловой пленкой, он намного сложнее. Кроме того, конечный результат — это деталь, обладающая всеми эстетическими качествами углеродного волокна, но без дополнительной сложности или головной боли, связанной с необходимостью изготовления собственных форм.
При традиционном обертывании винилом вы кладете самоклеящийся материал на деталь, используя немного тепла и поощряя создание обертки вокруг изгибов / краев. Однако обертывание настоящего углеродного волокна — гораздо более трудоемкий процесс.Поскольку большая часть необработанного углеродного переплетения представляет собой просто свободные нити, удерживаемые вместе с натяжением, попытка натянуть или сформировать их вокруг острых углов не только исказит само переплетение, но и у вас останутся неприятно выглядящие края. Кроме того, в то время как большинство виниловых пластинок являются самоклеящимися, необработанный углерод требует отдельного адгезионного компонента, чтобы он соответствовал и сохранял форму деталей, вокруг которых он наматывается.
Шаг 1: Инструменты / Материалы
В своем исследовании я наткнулся на Composite Envisions — местную компанию из Ваузау, штат Висконсин, которая продает все виды композитных материалов и эпоксидных смол, идеально подходящих для проектов из углеродного волокна.После просмотра их веб-сайта я решил использовать следующий комплект:
- Комплект для обертывания деталей из углеродного волокна (S) — я выбрал небольшой размер этого комплекта, потому что он дал мне много материала для экспериментов и включал почти все, что мне нужно для начала! Это было огромной помощью, так как мне не приходилось беспокоиться о том, какой отвердитель купить или сколько каждого продукта мне понадобится. Кроме того, он поставляется с мерными стаканами, кистями, палочками для смешивания и т. Д.
Кроме того, вам нужно забрать еще несколько предметов:
- Тепловая пушка. Тепловая пушка может спасти жизнь, когда дело доходит до удаления пузырьков воздуха с эпоксидной смолы или помогает «растекать» эпоксидную смолу после того, как она застыла.Его также можно использовать для (осторожного) ускорения процесса отверждения основы и лака.
- Цифровые кухонные весы — подойдут любые кухонные весы, но вам понадобится что-то, что поможет измерить ваши эпоксидные смолы / отвердители.
- Разная влажная / сухая наждачная бумага — вам захочется взять много каждого зерна, но я предпочитаю использовать 400, 800, 1000 и 2000.
- Клей 3M Super 77 — он будет использоваться, чтобы помочь прикрепить уголь к деталям перед укладкой.
- Duplicolor Gloss Black Enamel — Используя различные Krylon, Rustoleum и Duplicolor, я могу с уверенностью сказать, что линия эмалей Duplicolor, вероятно, лучшая из всех возможных. В качестве бонуса, эмаль означает, что она будет намного более долговечной, чем у альтернативных конкурентов на основе лака.
- SprayMax 2K Clear Coat — это лучший прозрачный лак, который вы можете купить. Устойчивый к ультрафиолетовому излучению, чрезвычайно глянцевый и невероятно прочный / пригодный для мокрой шлифовки. Это дорого, но если вы хотите, чтобы отделка была бескомпромиссной, это то, что вам нужно.Только будьте осторожны, всегда надевайте маску при распылении!
- Респиратор 3M — потому что 30 долларов — это дешевая страховка, позволяющая не покрывать ваши легкие неприятными растворителями / химическими веществами, которые выбрасываются эпоксидными смолами и красками. Серьезно — не возитесь с этим.
- Бумажные полотенца — Очистка чашек для смешивания, вытирание пролитых веществ и т. Д. Вы будете использовать их много, так что запустите Costco!
- Изопропиловый спирт — IPA, разбавленный в пропорции 50/50 водой из пульверизатора, является идеальным очищающим раствором.Я использую его для очистки чашек для смешивания после удаления излишков смолы, а также для очистки кистей. В качестве бонуса его удобно иметь при себе, если вы полируете / смешиваете свой автомобиль, поскольку он удалит весь воск или грязь!
Шаг 2: Подготовка
Первый шаг — выбрать деталь для упаковки! После бесконечных исследований по этой теме и почти единодушного чтения, что ваши первые несколько попыток будут дерьмовыми, я бросил осторожность и решил попробовать обернуть лицевую панель переключателя на моем WRX.Я остановился на отделке рычага переключения передач по нескольким причинам: во-первых, гораздо легче научиться оборачивать детали с плоскими поверхностями, а во-вторых, я действительно хотел добавить углеродное волокно в область центральной консоли, чтобы разбить все детали. черный и серый пластик.
Демонтировать обшивку рычага переключения передач было так же просто, как отвинтить ручку переключения передач и потянуть вверх весь пыльник / обшивку в сборе, чтобы отсоединить ее от центральной консоли. Отделить кожаный чехол от самой рамки оказалось немного сложнее, так как есть несколько удерживающих зажимов, которые необходимо ослабить.В конце концов, я смог все разобрать и был готов к следующему шагу: подготовке поверхности детали для нанесения угля и эпоксидной смолы!
Если деталь, которую вы оборачиваете, имеет любой цвет, кроме черного или темно-серого (как и накладка переключателя), я настоятельно рекомендую на этом этапе нанести слой черной краски. В зависимости от сорта / качества угля, который вы используете, во время укладки может быть некоторое разделение переплетения, что позволит просвечивать исходный цвет детали.Я столкнулся с этой проблемой, когда завернул свою кнопку опасности — я поленился и забыл покрасить, поэтому, к сожалению, если вы внимательно посмотрите, есть красный пластик OEM. Если сомневаетесь, избавьте себя от головной боли и просто отключите все.
ПРИМЕЧАНИЕ: Обязательно дайте вашему базовому слою достаточно времени для высыхания — у меня были проблемы, когда я закончил детали полностью (прозрачное покрытие и все такое) только для того, чтобы они покрылись волдырями после дня, проведенного на жарком солнце. Это не только крайне неприятно, но и избежать этого, не дав краске должного времени для высыхания, очень сложно.Обратитесь к этикетке с инструкциями на вашей краске, чтобы узнать конкретный период времени, но если сомневаетесь, подождите несколько дней.
Если вы не красите поверхность детали, то сейчас самое время обработать ее наждачной бумагой. Я обнаружил, что зернистость 800 создает красивую грубую поверхность, с которой эпоксидная смола связывается.
Последний этап подготовки — отрезать лист углерода до нужного размера перед укладкой. ПРИМЕЧАНИЕ. Перед тем, как работать с необработанным углем, обязательно защитите руки перчатками. Углеродные нити очень тонкие и могут раздражать кожу.
Как я уже упоминал ранее, необработанный углерод легко деформируется, поэтому использование тонкой полоски малярной ленты по краям разрезов, чтобы ткань не распускалась, в дальнейшем избавит от головной боли. Сама резка угля также может оказаться трудной — обязательно используйте очень острые и прочные ножницы.
Подготовив деталь и обрезав уголь до нужного размера, вы готовы приступить к процессу простоя!
Шаг 3: Отложение углерода
Поскольку углеродное волокно относительно гибкое, процесс прикрепления его к деталям на самом деле довольно прост.К сожалению, из-за его хрупкости в необработанном состоянии у вас есть практически один шанс настроить переплетение для простоя. Попытка отрегулировать его постфактум приведет только к испорченному углеродному волокну и общей грусти.
После долгих проб и ошибок я обнаружил, что легкий туман спрея клея 3M Super 77 на обратной стороне углеродного листа обеспечивает идеальную липкость для прикрепления углеродного листа к детали. В зависимости от температуры / климата окружающей среды вы можете подождать несколько минут, пока клей не схватится достаточно, чтобы уголь сохранил контур детали.Однако после того, как он застынет, вы сможете слегка прижать углеродное волокно к поверхности. Будьте осторожны, не тяните и не перекручивайте ткань после того, как она закрепится на месте.
Когда вы будете уверены в правильности размещения, аккуратно потрите уголь, чтобы закрепить клей, и начните согласовывать любые края или изгибы. В некоторых случаях вам может потребоваться добавить несколько рельефных разрезов, чтобы уголь мог более резко согнуться — только будьте осторожны, чтобы не разрезать слишком близко к лицевой стороне вашей детали, так как ткань может начать распускаться. Вам нужно подождать несколько часов, пока клей схватится, но когда все станет надежным и сухим, вы можете нанести первый слой эпоксидной смолы.
Я не буду вдаваться в подробности о смолах, но достаточно сказать, что их обычно бывает два типа: эпоксидная и полиэфирная. Большинство комплектов из стекловолокна поставляются с последним, так как он намного дешевле и более щадящий. К сожалению, полиэфирная смола также ужасно пахнет и не обладает большой структурной жесткостью (что не идеально для карбоновых деталей). Большинство комплектов углеродного волокна будет включать смолы на основе эпоксидной смолы из-за их превосходной прочности и прозрачности. Для всех смол требуются две части — сама смола и катализатор / отвердитель.Эпоксидные смолы можно использовать с различными отвердителями, каждый со своими требованиями к смешиванию и временем подготовки, поэтому подробные инструкции см. На этикетках вашего набора.
В моем случае набор Composite Envisions включал медленно отверждаемый отвердитель и эпоксидную смолу. Медленно отверждаемая смола обеспечивает максимальное рабочее время (до того, как эпоксидная смола начнет затвердевать), что идеально подходит для начинающих. В моем случае соотношение смеси эпоксидной смолы и отвердителя составляло 2: 1, поэтому я использовал кухонные весы и предоставленную чашку для смешивания, чтобы взбить небольшую порцию (всего около 30 унций) для первого слоя.Тщательно перемешайте эпоксидную смолу и отвердитель примерно в течение минуты.
СОВЕТ: После смешивания ударьте по чашке с эпоксидной смолой с помощью теплового пистолета, чтобы выпустить все пузырьки воздуха, прежде чем наносить ее кистью на свою часть — это поможет предотвратить появление точечной коррозии позже в процессе, когда придет время шлифовать эпоксидную смолу.
После того, как эпоксидная смола будет тщательно перемешана, возьмите кисть с чистой щетиной и начните легкими движениями нанести эпоксидную смолу на углеродное волокно. Будьте очень осторожны, чтобы не тянуть углеродные нити, а легкими промокательными движениями пропитайте ткань.На этом этапе вам не нужно топить уголь, просто нанесите достаточно, чтобы намочить поверхность.
ПРИМЕЧАНИЕ: Любую неиспользованную эпоксидную смолу необходимо утилизировать надлежащим образом. НЕ СЛИВАЙТЕ ЕГО В СЛИВКУ. Я использую несколько бумажных полотенец, чтобы впитать остатки эпоксидной смолы, и быстрый спринт разбавленного раствора IPA, чтобы очистить чашку для смешивания. Также не забудьте тщательно очистить кисть уайт-спиритом / IPA, если вы планируете использовать ее повторно.
В зависимости от типа используемого катализатора время отверждения может сильно различаться — опять же, обратитесь к этикетке вашей бутылки, чтобы узнать о времени установки и отверждения.В моем случае через несколько часов эпоксидная смола застыла достаточно, чтобы нанести второй слой.
Шаг 4: Шлифование
После нанесения и полного отверждения нескольких слоев эпоксидной смолы можно безопасно удалить излишки застывшей смолы острыми ножницами и / или отрезным кругом dremel.
Подготовленную деталь пора отшлифовать поверхность до гладкости! Начиная с зернистости 400 (может помочь влажный песок), аккуратно выровняйте поверхность детали. Будьте осторожны, не будьте слишком агрессивны и не прожигайте уголь.Если вы это сделаете, это не имеет большого значения — до конца будет нанесено еще несколько слоев эпоксидной смолы! Сосредоточьтесь на удалении выступов и подготовке поверхности для нанесения готового слоя лака.
В зависимости от того, сколько слоев эпоксидной смолы вы нанесли изначально, вы можете нанести еще несколько слоев после шлифовки. Повторяйте процесс до тех пор, пока не получите идеально ровную поверхность — без ямок и / или пустот. Затем постепенно переходите к более мелкой и мелкой зернистости наждачной бумаги (я обычно использую 400, 800 и 1000, если необходимо).После того, как вы удалите все глубокие царапины, у вас останется почти идеальное матовое покрытие, готовое к нанесению прозрачного покрытия!
Шаг 5: Прозрачное покрытие
Хотя лаки на основе эпоксидной смолы чрезвычайно эластичны при отверждении, они не устойчивы к ультрафиолетовому излучению. Это может быть проблематично для деталей, используемых в автомобилях, поскольку со временем они постепенно желтеют и тускнеют. К счастью, нанесение качественного прозрачного покрытия поверх эпоксидной смолы — простое решение!
Если у вас есть доступ к окрасочной кабине / системе распылителя профессионального качества, я завидую, и вы должны позволить мне ее использовать.А если серьезно, то хотя система сжатого воздуха — идеальное решение, большинство домашних мастеров, таких как я, просто не имеют места или нужды в чем-то столь сложном. Некоторые быстрые поисковые запросы могут предположить, что погремушка может привести к тому, что шерсть не порежется из-за ее низкого качества и непоследовательной отделки. Тем не менее, за немного больше денег, чем у обычного аэрозольного лака, вы действительно можете получить профессиональное покрытие в банке!
Двухэтапные прозрачные покрытия (часто называемые «2k») отличаются от имеющихся в продаже альтернатив от Krylon, Duplicolor и т. Д.SprayMax создает отличное двухкомпонентное прозрачное покрытие, которое по-прежнему поставляется в одной банке, но использует вручную активированную смесь второй стадии для создания гораздо более прочного покрытия. Их банки поставляются со второй крышкой, которая помещается на дно банки и удаляется, чтобы высвободить катализатор / отвердитель.
К сожалению, природа двухступенчатых лаков такова, что жизнеспособность смеси составляет всего около двух дней. При цене ~ 20 долларов за банку они все еще намного дешевле, чем полная установка.
Нанесениеничем не отличается от традиционного прозрачного лака — обязательно протрите детали разбавленным раствором IPA перед нанесением чего-либо.Вы должны быть уверены, что поверхность прозрачного лака максимально чистая! Выложите прозрачную пленку на свету ровными слоями, оставив 5-10 минут между нанесениями. SprayMax должен быть очень глянцевым, но будьте осторожны, чтобы не допустить растекания слишком толстого слоя — проявите терпение! После нанесения последнего слоя он высохнет на ощупь через несколько часов, но вам нужно подождать около 24 часов, прежде чем можно будет приступить к отделке / шлифовке.
Когда вы будете довольны результатом, поздравляем — вы готовы переустановить детали!
Заключение
Как видите, обернуть детали карбоном не так уж и сложно.Хотя это требует много времени и шлифовки, полировки и доводки, конечный результат того стоит. Не говоря уже о том, что вы можете с гордостью демонстрировать свои детали с карбоновым покрытием в собственном автомобиле, зная, что вы сделали всю тяжелую работу!
Следите за обновлениями — в следующем посте я расскажу, как создавать собственные детали из углеродного волокна из нестандартных форм!
Обновление— сентябрь 2020 г.
Я создал здесь сообщение с «извлеченными уроками» в качестве обновления к исходному сообщению.Если вам нужна дополнительная информация о работе с углеродным волокном, обязательно ознакомьтесь с ней!
Изготовление из углеродного волокна
Конец линии: Волокна в этом тщательно контролируемом лабиринте волокон (слева) выходят со станций отделки поверхности Grafil (Сакраменто, Калифорния, США) на намоточные устройства (справа) перед отгрузкой, их путь определяется определенным модулем упругости . ИСТОЧНИК | Grafil Inc.
Хотя многие читатели HPC используют углеродное волокно, немногие знают толк в том, как это делается.Это никого не должно удивлять. Производители углеродного волокна умалчивают о том, как производится их продукция. Волокно каждого производителя отличается от волокна его конкурентов, и детали обработки, которые придают каждой торговой марке характерные характеристики, считаются интеллектуальной собственностью. Известно, что процесс производства углеродного волокна сложен и дорог. Оснащение единственной производственной линии мирового класса требует больших капиталовложений — минимум 25 миллионов долларов на одно только оборудование — и может занять до двух лет.На самом деле стоимость может быть намного больше.
ИСТОЧНИК | Предконференционный семинар по углеродному волокну 2020 (Ноксвилл, штат Теннеси, США), проведенный Тони Робертсом, AJR Consultancy.
Расчетная годовая мощность производства углеродного волокна в мире в 2010 году.
Токийское производственное предприятие Mitsubishi Rayon Co. Ltd. (MRC) площадью 9,4 миллиона футов² / 874000 м² в Otake, например, планируется расширить на 100 миллионов долларов на три года — производственная линия, которая могла бы ежегодно производить как почти 20 миллионов фунтов / 9 072 метрических тонны углеродного волокна.Это во многом объясняет, почему исторически было трудно избежать дисбаланса между спросом и предложением, который приводит к резкому падению цен и их пику. Неудивительно, что нынешний штат производителей углеродного волокна по всему миру насчитывает менее десятка.
HPC , с помощью нескольких поставщиков процесса обработки углеродного волокна, недавно заглянул за завесу секретности, чтобы найти эту более всеобъемлющую, хотя и неполную, картину процесса.
Окончательная разницаВ отличие от металлов, которые являются однородными и по своей конструкции обладают свойствами, соответствующими установленным стандартам, что делает сталь P20 каждого производителя, например, взаимозаменяемой с другой, композиты неоднородны.Состоящие из комбинаций разнородных материалов (волокна и смолы), их вариативность и, следовательно, адаптируемость являются ключевыми для их привлекательности. Соответственно, производители углеродного волокна производят похожие, но не идентичные продукты. Углеродное волокно различается по модулю упругости (или жесткости, определяемой как деформация под действием деформации), а также по прочности на растяжение, сжатие и усталость. Углеродное волокно на основе PAN доступно сегодня с низким модулем упругости (менее 32 миллионов фунтов / кв. Дюйм или <32 Msi), стандартным модулем (33–36 Msi), промежуточным модулем (40–50 Msi), высоким модулем (50–70 Msi). ) и сверхвысоким модулем (от 70 до 140 Msi).Волокно, которое доступно в пучках, называемых жгутом, бывает разных размеров, от 1K до 350K (1K соответствует 1000 нитей диаметром от 5 до 10 микрон). Продукты также различаются по степени содержания углерода и типу обработки поверхности / покрытия.
«Сложность, присущая композитам из углеродного волокна, — это как раз то, что увеличивает ценность конструкций из углеродного волокна», — говорит Стивен Кармайкл, директор по продажам и маркетингу дочерней компании MRC Grafil Inc. (Сакраменто, Калифорния).«Как и при изготовлении хорошего вина, правильное количество терпения, тонкости и опыта обработки позволяет выявить тонкости углеродного волокна, которые увеличивают ценность». Эта ценность, конечно, очень высока: композиты из углеродного волокна в качестве замены металла обладают в 10 раз большей прочностью, чем сталь при половинном весе.
Проще говоря, углеродное волокно получают пиролизом органического волокна-предшественника в инертной атмосфере при температурах выше 982 ° C / 1800 ° F. Однако производство углеродного волокна — сложное дело.Завод Grafil площадью 60 000 футов² / 5 574 м² в Сакраменто, Калифорния — небольшой по сравнению с заводом MRC в Отаке, даже после увеличения мощности на 2 миллиона фунтов / 544 тонны в 2005 году с параллельными производственными линиями — стал основой для Прохождение HPC по этапам первичного производства. Это полимеризация и прядение, окисление (также называемое стабилизацией), карбонизация (иногда неточно именуемая графитизацией), обработка поверхности и нанесение аппрета. На протяжении всего процесса жесткие допуски определяют максимальную полезность волокна.«Целевой коэффициент вариации урожайности составляет 1%», — говорит Гордон Ширер, операционный директор Grafil, отмечая, что реальная вариация составляет около 3% для небольшой буксировки (от 1 до 24 тысяч), которая используется в сложных приложениях, например в самолетах. (отсюда и обозначение как аэрокосмический сорт), а крупный жгут (промышленный или коммерческий) может варьироваться до 15%.
Основные этапы двухэтапного процесса, используемого для производства углеродного волокна на основе ПАН, включают этапы процесса, используемого для производства основной цепи полиакрилонитрила (ПАН).ИСТОЧНИК | Grafil Inc.
ПолимеризацияПроцесс начинается с полимерного сырья, известного как прекурсор («то, что было раньше»), которое обеспечивает молекулярную основу волокна. Сегодня около 10% производимого углеродного волокна производится из прекурсора на основе вискозы или пека, но большая часть производится из полиакрилонитрила (ПАН), полученного из акрилонитрила, который получают из пропилена и аммиака, производимых товарными химическими веществами.
По этой причине в данной статье описывается производство углеродного волокна на основе ПАН.
Упрощенное изображение линии карбонизации.
Иллюстрация | Карл Реке; Исходный материал | Grafil Inc.
Преобразование PAN в углеродное волокно является проблемой для производителей более 30 лет. Кармайкл добавляет, что большая часть инвестиций производителя углеродного волокна тратится на прекурсор, а качество готового волокна напрямую зависит от качества прекурсора. В частности, отмечает Ширер, внимание к качеству прекурсора сводит к минимуму колебания выхода или длины на единицу веса волокна.
Обычно рецептура предшественника начинается с мономера акрилонитрила, который объединяют в реакторе с пластифицированными сомономерами акрила и катализатором, таким как итаконовая кислота, диоксид серы, серная кислота или метилакриловая кислота. Непрерывное перемешивание смешивает ингредиенты, обеспечивает консистенцию и чистоту и инициирует образование свободных радикалов в молекулярной структуре акрилонитрила. Это изменение приводит к полимеризации — химическому процессу, в результате которого образуются длинноцепочечные полимеры, из которых можно превратить акриловые волокна.
Детали полимеризации, такие как температура, атмосфера, конкретные сомономеры и катализатор, являются собственностью. По словам Питера Моргана, автора книги «Углеродные волокна и их композиты» (CRC Press, 2005), «полимеризация должна достичь по крайней мере 85% содержания акрилонитрила и относительной молекулярной массы 100 000 г / моль с равномерным распределением, чтобы наполнить белое волокно PAN хорошим механические свойства.» Прекурсор MRC, используемый Grafil, например, обеспечивает содержание акрилонитрила от 94 до 98%.
После промывки и сушки акрилонитрил, теперь в форме порошка, растворяется либо в органических растворителях, таких как диметилсульфоксид (ДМСО), диметилацетамид (DMAC) или диметилформамид (ДМФ), либо в водных растворителях, таких как хлорид цинка и родановая соль. Органические растворители помогают избежать загрязнения ионами металлов в следовых количествах, которые могут нарушить термоокислительную стабильность во время обработки и снизить высокотемпературные характеристики готового волокна. На этом этапе суспензия порошка и растворителя или предшественник «прядильный раствор» представляет собой консистенцию кленового сиропа.Выбор растворителя и степень, до которой можно контролировать вязкость пасты (посредством интенсивной фильтрации), имеют решающее значение для успеха следующей фазы, формирования волокна.
Прядильная ВолокнаPAN формируются методом мокрого прядения. Смазка погружается в жидкую коагуляционную ванну и экструдируется через отверстия фильеры из драгоценных металлов. Отверстия фильеры соответствуют желаемому количеству нитей в ПАН-волокне (например,г., 12000 отверстий под углепластик 12К). Это волокно, полученное мокрым формованием, относительно гелеобразное и хрупкое, протягивается роликами через промывку для удаления избытка коагулянта, затем сушится и растягивается для продолжения ориентации полимера PAN. Здесь внешняя форма и внутреннее поперечное сечение нити определяется степенью проникновения выбранного растворителя и коагулянта в волокно-предшественник, величиной приложенного натяжения и процентом удлинения нити. Последний является собственностью каждого производителя, но Морган утверждает, что степень растяжения может в 12 раз превышать первоначальную гибкость исходного волокна.
Альтернативой мокрому прядению является гибридный процесс, называемый сухим струйным / мокрым прядением, при котором используется вертикальный воздушный зазор между волокном и ванной коагулята. В результате получается гладкое круглое волокно из полиамида PAN, которое может улучшить границу раздела между волокном и матричной смолой в композитных материалах.
Последним этапом формирования волокон-предшественников ПАН является нанесение финишного масла для предотвращения комкования липких волокон. Затем белое волокно PAN снова сушат и наматывают на бобины.
ОкислениеЭти бобины загружаются в шпулярник, через который волокно PAN подается через ряд специализированных печей на наиболее трудоемкой стадии производства — окислении.Перед тем, как попасть в первую печь, волокна PAN раскладываются в жгутовую ленту или лист, называемый основой. Температура в печи окисления находится в диапазоне от 392 ° F до 572 ° F (от 200 ° C до 300 ° C). Этот процесс объединяет молекулы кислорода из воздуха с волокнами PAN в основе и вызывает сшивание полимерных цепей. Это увеличивает плотность волокна с ~ 1,18 г / см до 1,38 г / см.
Чтобы избежать неконтролируемого экзотерма (общая экзотермическая энергия, выделяемая при окислении, оцениваемая в 2000 кДж / кг, представляет реальную опасность возгорания), производители духовок используют различные конструкции воздушного потока, чтобы помочь отводить тепло и контролировать температуру (см. Врезку ниже).Мэтт Литцлер, президент C.A. Litzler Co. Inc. (Кливленд, Огайо) отмечает, что «каждый предшественник имеет свой собственный экзотермический образец. Поскольку химический состав отдельных прекурсоров фиксирован, контроль температуры и воздушного потока в печи окисления адаптирован для каждого прекурсора и обеспечивает стабилизацию экзотермической реакции ».
Время окисления варьируется в зависимости от химического состава прекурсора, но Литцлер считает, что жгут 24K можно окислить со скоростью около 43 футов / 13 м в минуту на большой производственной линии с несколькими печами для окисления.Рэнди Строп, генеральный менеджер производителя печей Despatch Industries (Лейквилл, Миннесота), говорит, что обычно требуется от 60 до 120 минут, как и от четырех до шести печей на производственную линию, при этом печи расположены друг над другом, чтобы обеспечить две зоны нагрева, которые предлагают 11 до 12 проходов волокна на печь. В конце концов, окисленное (стабилизированное) волокно PAN содержит от 50 до 65% молекул углерода, а остальное — смесь водорода, азота и кислорода.
Воздушный поток и скорость воздуха являются ключами к контролю экзотермической и температурной стабильности в процессе окисления.На этой схеме от Despatch Industries показана запатентованная компанией конструкция с параллельным потоком от центра до конца. ИСТОЧНИК | Отгрузка Индустрии
Духовые шкафы нового поколения, повышающие КПДПри производстве углеродного волокна многое зависит от конструкции печей и печей, в которых волокна подвергаются пиролизу.
В процессе окисления воздушный поток печи играет решающую роль в регулировании температуры процесса и предотвращении экзотермических реакций. Конструкции воздушного потока могут быть однопоточными (параллельными или перпендикулярными буксирной ленте) или многолучевыми.
По словам Рэнди Стропа, генерального менеджера компании Despatch Industries (Лейквилл, Миннесота), производящей углеродное волокно, производителя печей, производители углеродного волокна требуют от печей окисления три важных элемента: производительность, масштабируемость и энергоэффективность. Чтобы определить оптимальную уставку печи окисления для конкретных требований производителей углеродного волокна среди своих клиентов, Despatch протестировал свой запатентованный параллельный поток воздуха от центра к концу через температурные градиенты, измеряемые 40 различными калиброванными термопарами, расположенными с каждой стороны рабочей зоны печи.Строп отмечает, что эта конструкция позволяет использовать более высокие скорости воздуха — до 13,1 фута / сек (4 м / сек) на выходе из сопла — и больший объем воздуха, чем в других конфигурациях печи. Эта конфигурация также обеспечивает равномерную температурную однородность ± 1 ° C, в среднем по бокам, по всей ширине ленты жгута. По сообщениям клиентов, скорость окисления в промышленных печах на 25% выше.
Despatch предлагает печи шириной от 1 фута до 11,5 футов (от 0,3 м до 3,5 м), автоматические входные и выходные жалюзи, которые сводят к минимуму потери тепла и сокращают время настройки, а также рециркуляцию нагретого воздуха для снижения общего энергопотребления.Расчетная экономия энергии по сравнению с предыдущими конструкциями печей при использовании противостоящих автоматических жалюзи шириной 6,6 фута / 2 м с уменьшенным щелевым отверстием 0,35 дюйма / 9 мм составляет 10 кВт / ч.
C.A. Компания Litzler Co. Inc. (Кливленд, Огайо), производитель печи окисления в течение 30 лет, оснащает свою продукцию несколькими температурными зонами и регулируемым поперечным потоком воздуха, который доставляет воздух со скоростью 5-9 футов (1,5-2,7 м). в секунду для каждого жгута, что приводит к равномерной обработке волокна-предшественника. Запатентованные торцевые уплотнения решают то, что президент компании Мэтт Литцлер описывает как «простую физику эффекта дымохода, когда холодный воздух попадает в нижние прорези продукта, а горячий воздух выходит из верхних прорезей.Это может привести к появлению холодных пятен в духовке и быть опасным для операторов. Наши торцевые уплотнения делают каждую прорезь нейтральной, сокращают количество необходимого вытяжного воздуха и эффективно удлиняют полезную печь, устраняя проникновение холодного воздуха ».
Помимо экспериментальных и производственных печей шириной до 10 футов / 3 м, C.A. Litzler также разрабатывает и производит направляющие ролики, ведущие ролики и натяжные стойки для вытягивания волокон.
Поставщик печей для карбонизации с 1940-х годов, Harper International (Ланкастер, Н.Y.) начал предлагать комплексные конструкции и оборудование для производства углеродного волокна в 1990-х годах и установку под ключ линий на основе PAN в 2000 году. Роберт Блэкмон, вице-президент отдела технологических систем, отмечает, что новейшее поколение более широких печных систем больше эффективный, производя больший объем углеродного волокна с меньшим потреблением энергии на фунт волокна. Harper предлагает печи шириной до 13 футов / 4 м и длиной более 46 футов / 14 м с высокоэффективной изоляцией.
Особое внимание уделяется камерам продувки на входе и выходе.Блэкмон объясняет, что каждая молекула кислорода, попадающая в систему, разрушает не только волокно, но и графитовую огнеупорную поверхность печи. «Наша система продувки значительно снижает иммиграцию кислорода, что может увеличить выход продукта, качество и срок службы оборудования». Для повышения энергоэффективности и снижения производственных затрат компания Harper разработала рекуперативную систему рекуперации отработанного тепла термического окисления. Блэкмон признает, что такой оптимизированный контроль за окружающей средой связан с затратами, но он считает, что «рекуперированная энергия обычно вполне оправдывает затраты.”
«Печи Harper’s контролируются атмосферой с помощью инертных газов, таких как азот или аргон, и могут работать в диапазоне температур от 572 ° F до 5432 ° F [от 300 ° C до 3000 ° C] для углеродного волокна с низким и сверхвысоким модулем упругости, — заявляет Джон Имхофф, менеджер по маркетингу и развитию бизнеса. Harper также предлагает системы отделки поверхности и калибровки для соответствия различным химическим составам электролитических смол и матричных смол.
КарбонизацияКарбонизация происходит в инертной (бескислородной) атмосфере внутри ряда специально разработанных печей, которые постепенно повышают температуру обработки.На входе и выходе каждой печи продувочные камеры предотвращают проникновение кислорода, поскольку каждая молекула кислорода, которая проходит через печь, удаляет часть волокна, объясняет Роберт Блэкмон, вице-президент отдела технологических систем. у источника печи Harper International (Ланкастер, Нью-Йорк). Это предотвращает потерю углерода, образующегося при таких высоких температурах. В отсутствие кислорода только неуглеродные молекулы, включая элементы цианистого водорода и другие летучие органические соединения (образующиеся во время стабилизации на уровнях концентрации от 40 до 80 частей на миллион) и твердые частицы (например, локальные скопления остатков волокна), удаляются и выводятся из печи в течение последующая обработка в мусоросжигательной печи с контролируемым экологическим контролем.В Grafil карбонизация начинается в низкотемпературной печи, в которой волокно подвергается воздействию температуры 1292–1472 ° F (700–800 ° C), и заканчивается в высокотемпературной печи при температуре 2192–2732 ° F (1200–1500 ° C). Натяжение волокна должно продолжаться на протяжении всего производственного процесса. В конечном итоге кристаллизацию молекул углерода можно оптимизировать для производства готового волокна, содержащего более 90 процентов углерода. Хотя термины углерод и графит часто используются как синонимы, первые обозначают волокна, карбонизированные при температуре около 1315 ° C / 2400 ° F и содержащие от 93 до 95% углерода.Последние графитируются при 1900–2480 ° C (3450–4500 ° F) и содержат более 99 процентов элементарного углерода.
Количество печей определяется желаемым модулем упругости углеродного волокна; Отчасти относительно высокая стоимость высокомодульного и сверхвысокомодульного углеродного волокна объясняется продолжительностью времени выдержки и температурами, которые должны быть достигнуты в высокотемпературной печи. Хотя время выдержки является запатентованным и отличается для каждого сорта углеродного волокна, время выдержки при окислении измеряется в часах, но карбонизация на порядок короче, измеряется в минутах.Когда волокно карбонизируется, оно теряет вес и объем, сужается на 5-10% в длину и сужается в диаметре. Фактически, продемонстрированное соотношение химического состава прекурсора PAN к углеродному волокну PAN составляет примерно 2: 1 с изменчивостью менее 2%, то есть значительно меньше материала выходит из процесса, чем идет в него.
Обработка поверхности и калибровкаОбработка поверхности и проклейка увеличивают общую площадь поверхности и пористость волокна и изменяют его поверхностную энергию, чтобы улучшить адгезию между волокном и полимерной матрицей в композите.ИСТОЧНИК | Grafil Inc.
Следующий шаг имеет решающее значение для характеристик волокна, и, помимо прекурсора, он больше всего отличает продукт одного поставщика от продуктов его конкурентов. Адгезия между матричной смолой и углеродным волокном имеет решающее значение для армированного композита; Во время производства углеродного волокна проводится обработка поверхности для улучшения этой адгезии. Производители используют разные методы обработки, но общий метод включает протягивание волокна через электрохимическую или электролитическую ванну, содержащую такие растворы, как гипохлорит натрия или азотная кислота.Эти материалы травят или делают поверхность каждой нити шероховатой, что увеличивает площадь поверхности, доступную для межфазного соединения волокна / матрицы, и добавляет реактивные химические группы, такие как карбоновые кислоты.
Затем наносится фирменное покрытие, называемое проклейкой. При содержании от 0,5 до 5% веса углеродного волокна проклейка защищает углеродное волокно во время обработки и переработки (например, ткачества) в промежуточные формы, такие как сухая ткань и препрег. Проклейка также скрепляет волокна в отдельные жгуты, чтобы уменьшить пушистость, улучшить технологичность и увеличить прочность на сдвиг на границе раздела между волокном и матричной смолой.Производители углеродного волокна все чаще используют калибровку, соответствующую конечному использованию потребителя (см. Врезку ниже и «Достижения в калибровке и обработке поверхности углеродных волокон»). В Grafil, добавляет Кармайкл, «мы можем настроить обработку поверхности и размер в соответствии с характеристиками смолы конкретного клиента, а также с конкретными свойствами, желаемыми для композита».
По словам Энди Бринка, соучредителя компании Hydrosize Technologies (Роли, Северная Каролина), ныне входящей в Michelman (Цинциннати, штат Огайо), в которой он работает менеджером по развитию бизнеса, «полимерные пленкообразователи, изготовленные путем диспергирования частиц, взвешенных в воде, обеспечивают стабильный химический состав, который при высыхании создает хорошее покрытие.Скорость большинства линий из углеродного волокна позволяет наносить достаточно однородный размер, что сводит к минимуму комки заполнителя или голые пятна ».
Когда клей высохнет, долгий процесс завершен. Grafil (как и другие поставщики) отделяет отдельные жгуты от основы и наматывает их на бобины для отправки клиентам, в том числе предпреггерам и ткачам.
Если история отрасли служит предвестником ее будущего, то огромное количество оборудования и производственная проницательность, необходимые для успешного преобразования белого волокна PAN в черное углеродное волокно, предполагает, что производство этого передового материала — дело не для слабонервных или слабонервных. неопытный.Три десятилетия совершенствования технологии обработки данных привели к зрелости технологий и возможности трансформировать превосходные характеристики и универсальность применения с помощью волокон в передовые композиты. То, что произошло раньше, как с технологической, так и с экономической точки зрения, создает основу для потенциального роста спроса, знаменующего будущее.
Тенденции в производстве углеродного волокнаТехнологические изменения сделали углеродное волокно доступным и более практичным для использования производителями оригинального оборудования в широком диапазоне рынков и сфер применения.Поставщики размеров и те, кто строит печи и печи для пиролиза, недавно обрисовали в общих чертах некоторые из наиболее важных разработок для HPC.
Размеры для многих матрицПоскольку большая часть углеродного волокна исторически использовалась с эпоксидными матрицами, проклейка в основном производится на основе эпоксидной смолы и имеет низкий молекулярный вес, чтобы способствовать податливости и растекаемости волокна. Тем не менее, в настоящее время ведутся исследования по созданию размеров с химическим составом, которые подходят для разнообразных матричных смол, востребованных сейчас для конечного использования.
Hydrosize Technologies (Роли, Северная Каролина, который был приобретен Мишельманом из Цинциннати, штат Огайо в июне) предлагает на коммерческой основе 17 размеров углеродного волокна, хотя менеджер по развитию бизнеса Энди Бринк указывает, что компания может создавать размеры для нескольких комбинаций волокна / матрицы, а также для различных композитов. производственные процессы. Он говорит, что почти все размеры компании не содержат растворителей и опасных загрязнителей воздуха. Одним из примеров является Hydrosize U601, уретановая проклейка с высоким молекулярным весом, которая, как сообщается, улучшает как смачивание волокна уретановыми смолами, так и смазывающую способность (снижение трения во время работы) с помощью экологически чистого состава.
В научно-исследовательском центре Adherent Technologies в Альбукерке, штат Нью-Мексико, президент Рональд Оллред в течение 35 лет занимался научным анализом проблем интерфейса волокно / матрица. Сообщается, что он обнаружил реактивную химию, которая влияет на молекулы углерода в волокне, чтобы улучшить межфазное соединение между волокном и матрицей. «В настоящее время мы используем этот химический состав для улучшения межфазной адгезии углеродного волокна / винилового эфира и углеродного волокна / бисмалеимида для ВМС США, в том числе в композитных компонентах двигателя для F-35 Joint Strike Fighter.Он отмечает, что до использования аппрета Adherent на основе сложного винилового эфира «военно-морской флот наблюдал только 50 процентов желаемых теоретических свойств из-за плохой передачи сдвига на границе раздела. Точно так же высокотемпературные композиты могут страдать от плохой стойкости к окислению из-за того, что состав проклейки не соответствует требованиям свойств матричной смолы ».
любопытных вопросов по углеродному волокну от специалистов по композитам
Изображения с помощью ультрауглерода и APR Performance
Углеродное волокно — один из самых современных материалов, используемых в производстве гоночных автомобилей во всем мире; Технология, которая проявила себя в индустрии производительности за счет использования легких панелей, изначально была разработана для аэрокосмической промышленности.Его широкое распространение в профессиональных гоночных классах сделало производственные процессы более доступными, позволяя спортсмену-гонщику использовать его с целью снижения веса без потери прочности компонентов.
Чтобы узнать больше об этом удивительном материале, методах его изготовления и других важных деталях, связанных с его использованием в производственной индустрии, мы задали ряд вопросов двум экспертам по производству углеродного волокна: Грегу Шампину из Ultra-Carbon и KC Chou из Годовая производительность.Эти два магазина применяют совершенно разные методы производства; Ultra-Carbon специализируется на мелкосерийных легких панелях для дрэг-рейсинга, а APR Performace обслуживает индустрию спортивных компактных автомобилей, производя панели в стиле крупносерийного производства. Их ответы поучительны, информативны и их стоит прочитать. Остерегайтесь — это долго, но вы будете очарованы повсюду.
Без лишних слов, вот что вы хотите знать об углеродном волокне.
Front Street: В чем разница между пластиком, армированным углеродным волокном (CFRP), и пластиком, армированным стекловолокном (FRP)?
Greg Shampine / Ultra-Carbon: CFRP и FRP — это просто аббревиатуры для того, что мы с вами называем деталями из углеродного волокна и деталями из стекловолокна соответственно.Общность в двух последних словах — «армированный пластик». Итак, оба способа усилить пластик, который является смолой, создающей структуру. Стекловолокно — это просто мягкая белая ткань, пока вы не намочите ее смолой, а затем, когда смола застынет, она станет жесткой или полужесткой. Углеродное волокно работает примерно так же. Вы можете залатать треснувший бампер на старом Corvette углеродным волокном так же легко, как и стекловолокном, и фактически используя ту же смолу.
Итак, теперь, когда мы понимаем их сходство, давайте обсудим их различия.Стекловолокно обычно создается в матах для того вида работ, о котором мы будем говорить, хотя его можно найти во многих формах. Коврики создаются путем взятия миллионов крошечных рыхлых стеклянных волокон и их беспорядочного прессования в рыхлую структуру. Этим ковриком можно легко манипулировать и разбирать вручную. Он дешев, с ним легко работать, и он может дать относительно легкую деталь по сравнению со стальной деталью того же размера. Компромисс в том, что он может быть хрупким. Его можно заставить изгибаться, не ломаясь (например, доска для серфинга), но со временем он становится слабее, чем больше движения к нему прилагается.Вот почему стекловолокно, хотя и широко используется из-за его дешевизны, на самом деле является плохим выбором материала для автомобильных запчастей. И как только он треснет или сломается, поломка обычно быстро распространяется.
И наоборот, углеродное волокно — это материал, состоящий из тысяч крошечных волокон толщиной примерно 1/50 толщины человеческого волоса, настолько тонких, что на самом деле очень трудно увидеть отдельное волокно невооруженным глазом. Эти волокна скручены вместе с тысячами других волокон в «жгут». Буксировка — это то, что делает ткань, которую вы обычно называете углеродным волокном.Жгут обычно состоит из 3000-24000 волокон, сгруппированных вместе, что обычно определяет толщину всего материала.
Это все на буксире. Форма, размер, толщина и направление жгута определяют прочность углеродного волокна как рыхлой ткани. То, как он сочетается со смолой, и свойства этих смол — вот что определяет свойства отвержденного материала. И как эта комбинация материала, смолы, количества слоев, направления материалов и многих других значений определяет прочность всей детали.В общем, углеродное волокно может быть значительно легче и прочнее, чем такая же деталь из стекловолокна, но при этом иметь большую гибкость и одновременно выдерживать большее напряжение. Все дело в том, как вы его сконструируете. Как и дом, он состоит из множества частей, работающих вместе, и нет двух одинаковых частей, даже если они кажутся одинаковыми.
KC Chou / APR Performance: У пластика, армированного углеродным волокном, и пластика, армированного стекловолокном, много разных характеристик.Во-первых, внешний вид обоих материалов очень разный: углеродное волокно имеет черный графитовый цвет, а стекловолокно — прозрачный белый цвет. Во-вторых, углеродное волокно имеет гораздо большую прочность на разрыв и меньший вес, чем стекловолокно. В-третьих, цена на углеродное волокно значительно выше, чем на стекловолокно. В-четвертых, из-за гибкости материала углеродное волокно сложнее придать форму, чем стекловолокно. Наконец, углеродное волокно является проводящим материалом, а стекловолокно — непроводящим материалом.Углеродное волокно также может быть огнестойким, а стекловолокно легко воспламеняется.
Front Street: С точки зрения потребителя, является ли один материал лучшим выбором, чем другой?
Грег Шампин / Ультра-углерод: С точки зрения потребителя, есть что учесть. В первую очередь это обычно цена. У вас есть три типичных типа частей тела, которые производятся для потребителей на рынке дрэг-рейсинга.
Первым, наиболее распространенным и наименее дорогим является стекловолокно.Это дешево, просто в изготовлении и практически любой может себе это позволить. Это и польза, и противник. Существует очень широкий круг компаний, производящих детали из стекловолокна. Некоторые очень хорошие, некоторые очень плохие. Здесь очень важна репутация компании. Один капюшон из стекловолокна за 600 долларов может быть самым качественным капюшоном, который вы когда-либо видели, а капюшон из стекловолокна другой компании за 600 долларов может быть самым ужасным мусором из когда-либо созданных. Все сводится к качеству формы, из которой создаются детали, и мастерству мастера, создающего детали.То же самое верно и для двух других типов частей, которые мы обсудим далее.
Вторая и самая дорогая — это детали из настоящего углеродного волокна. Я говорю «настоящие», потому что есть много деталей, которые на самом деле не являются углеродным волокном, но мы вернемся к этому через минуту. Настоящие детали из углеродного волокна, как правило, самая легкая вещь, которую вы можете купить для части тела. Конечно, их вес может варьироваться от производителя к производителю в зависимости от строительной философии производителя. Обычно я делаю детали немного тяжелее, чем другие производители карбона, потому что мои клиенты больше заботятся о качестве и долговечности.Это не значит, что более легкая деталь не может быть долговечной, мы просто ошибаемся, когда дело касается этого.
Обычно вы будете платить в три-пять раз больше за настоящую деталь из углеродного волокна, чем за аналогичную деталь из стекловолокна, при этом обычно экономите 30-50 процентов веса стекловолокна. Для некоторых, если платить значительно больше, не стоит экономить несколько фунтов. Для других это так. Еще одна вещь, которую следует учитывать между углеродом и стекловолокном, — это ваша краска. Мы все видели детали из стекловолокна, которые растрескиваются и растрескиваются и в конечном итоге выглядят как полный мусор сразу после новой покраски.Этого не происходит с углеродным волокном. Однако углеродное волокно оставит призрачный отпечаток вплетения краски. Это особенно заметно на черной машине или на любом глянцевом покрытии. Чем он глянцевее, тем больше вы его видите.
Третий тип композитного материала, который используется для изготовления частей тела, — это гибрид, или то, что я называю «поддельным углеродным волокном». Они стоят примерно в 1,5-2 раза больше, чем качественная деталь из стекловолокна, весят примерно столько же, как деталь из стекловолокна, и обычно изготавливаются дешевле, чем качественная деталь из стекловолокна.Все дело во внешнем виде, это то, что мы видим на большинстве последних моделей импортных автомобилей с прозрачным карбоновым капотом с жалюзи и сеткой. Это детали, которые представляют собой верхний слой из углеродного волокна со структурой из стекловолокна. Обычно их называют углеродным волокном, но это обман. Видите ли, углеродное волокно получает свою силу от плотности. Для этого требуется несколько слоев углеродного волокна, чтобы придать детали достаточную прочность. Когда деталь представляет собой всего лишь один слой углеродного покрытия, наложенного поверх стекловолокна, углерод также может вообще отсутствовать.Однослойное углеродное волокно толщиной 3k имеет такую же структуру, как лист бумаги. Более того, когда вы покупаете эти поддельные карбоновые детали, вы обычно получаете что-то, сделанное в Китае или сделанное американским производителем, который пытается обманом заставить потребителя платить больше за то, что по сути является частью из стекловолокна. Вы доплачиваете за внешний вид, вот и все. И что самое худшее? Эти детали, за внешний вид которых вы платите дополнительно, не долговечны. Обычно они не защищают эти части от ультрафиолета, поэтому в течение двух-трех лет, даже без длительного пребывания на солнце, ваша часть начнет желтеть или тускнеть.Дело не только в цвете. Изменение цвета означает, что вы видите начало разрушения смолы. Когда смола начнет разрушаться, прозрачный верхний слой начнет отслаиваться, и деталь станет более хрупкой. По мере дальнейшего разрушения смолы она вызывает цепную реакцию, которая проникает глубже в деталь. В конце концов, вы настолько теряете структурную целостность детали, что она трескается и ломается от нормального повседневного использования. Такие детали даже не стоит ремонтировать. Как только начинается пожелтение и процесс уже запущен, лекарства от него нет.Эти детали — электрические тостеры автомобильного мира. Когда он начнет портиться, выбросьте его и купите другой. Каждые три-пять лет.
KC Chou / APR Характеристики: Это зависит от конструктивного назначения детали, а также от того, используется ли деталь с нагрузочным давлением, высокой силой или зоной нагрева, поскольку углеродное волокно имеет более высокий предел прочности на разрыв, чем стекловолокно. Заднее крыло — хороший пример детали, в которой мы настоятельно рекомендуем использовать углеродное волокно вместо стекловолокна для обеспечения прочности и жесткости.Опорная пластина тормозного ротора также является одним из компонентов, в которых должно использоваться углеродное волокно вместо стекловолокна из-за высокой температуры, создаваемой теплом ротора.
Front Street: Какие преимущества использования углеродного волокна перед пластиком или алюминием?
Грег Шампин / Ультра-углерод: Углеродное волокно, по сути, пластично. На самом деле, сравнивая это с пластиком, вы действительно сравниваете что-то из неармированного пластика, например, АБС, с чем-то из армированного пластика, например, углеродным волокном.Вес у них будет почти одинаковым.
Конструктивная целостность и возможность изготовления больших объемов — вот где мы видим разницу. АБС может быть хрупким, когда он очень тонкий. Это не лучший материал для чего-то вроде части тела, потому что он может треснуть и сломаться, если просто установить его на машину и отправиться в магазин на углу. Преимущество АБС заключается в том, что его можно быстро, легко и дешево налить жидкостью в форму и заполнить ее, чтобы создавать повторяемые детали тысячи раз.Инструменты в таком объеме обходятся довольно дорого, но, разбитые на весь срок службы, они позволяют получать действительно дешевые детали.
Углеродное волокно, как правило, необходимо вручную укладывать в форму. Да, существуют роботизированные процессы и другая автоматизация, если вы начнете производство углеродных деталей в среде, требующей огромных объемов. Но это по-прежнему нисколько не снижает стоимость до того, для чего может быть изготовлена АБС.
Что касается сравнения алюминия с углеродным волокном, то они совершенно противоположны.По сути, углеродная заготовка весит вдвое меньше алюминия. Алюминий существенно расширяется и сжимается в результате тепловых изменений, тогда как углеродное волокно практически не изменяется.
Представьте, что вы делаете двигатель с блоком из углеродного волокна, головками, поршнями, шатунами, коромыслами и т. Д. Если бы каждое звено цепи было из углеродного волокна, зазор клапана был бы таким же на холодном двигателе, как и на горячем. двигатель, и поршневые кольца потребуют нулевого зазора. Представьте себе дополнительную мощность, которую вы могли бы получить, решив только эти две «отстойные» проблемы типичного двигателя внутреннего сгорания.Что касается обрабатываемости, то углеродная заготовка может обрабатываться как алюминий, просто для этого требуется другой инструмент.
Практически все, что может быть сделано из алюминия, также может быть сделано из углеродного волокна. Дело не в том, можно это сделать или нет, а в том, практично это делать или нет. Некоторые вещи просто требуют так много инженерных усилий или стоят так дорого для создания каждого отдельного элемента, что это больше не становится практичным.
KC Chou / APR Performance: Основным преимуществом является снижение прочности и веса по сравнению с пластиком и алюминием.Углеродное волокно намного жестче и жестче, чем пластиковые детали. Углеродное волокно на 50 процентов легче алюминия.
Фронт-стрит: Существует довольно много различных рисунков плетения. Можете ли вы объяснить разницу между вариантами? Какие из них наиболее популярны в автомобильной промышленности и почему?
Greg Shampine / Ultra-Carbon: Узоры плетения основаны на двух вещах: внешнем виде и характеристиках. Некоторые плетения созданы, чтобы выглядеть круто, а некоторые созданы для определенных целей.Такие вещи, как саржа 2 × 2, являются хорошей универсальной тканью, которая больше предназначена для красивого внешнего вида, чем что-либо еще. Это силовой компромисс по всем направлениям. У него нет особых свойств, которые делали бы его лучше, чем что-либо еще. Это материал, который вы обычно видите и который у большинства людей ассоциируется с углеродным волокном. 1 × 1, или полотняное переплетение, похоже, но используется реже просто потому, что саржа легче соответствует форме и обычно считается более приятной на вид.
После этих двух у вас есть специализированные направленные и однонаправленные структуры. Они не так сильны в одном конкретном направлении, но значительно сильнее в другом. Давайте возьмем карданный вал как отличный пример этой силы. Карданный вал из углеродного волокна изготовлен из однонаправленного углеродного волокна, которое образует круг. Это волокно совсем не прочно по отношению к силам, приложенным к нему сбоку, но оно очень прочно, когда к нему прилагаются силы против скручивания.Другими словами, все буксиры, о которых мы говорили в первом вопросе, сопротивляются скручивающим силам, потому что все они уложены в одном направлении, чтобы противостоять скручиванию. Эти приводные валы обычно противостоят силам, которые многократно прилагаются к крутящему моменту, превышающему 2000 фунт-фут. Однако, если вы ударите по этому же валу сбоку металлическим каркасным молотком с силой, вероятно, менее 100 фунтов на квадратный дюйм всего один раз, вы, вероятно, повредите его без возможности ремонта.
KC Chou / APR Performance: Саржа 2 × 2 — это тип текстильного переплетения с рисунком диагональных параллельных ребер под углом 45 градусов, который сегодня очень часто используется в автомобильных деталях. Он показывает большую глубину формованной детали, что часто требуется потребителю. Углерод с полотняным переплетением 1 × 1 имеет квадратный рисунок с меньшей глубиной. Он обычно используется для изготовления внутренних панелей для экзотики, производимой на ранних этапах производства, и менее востребован сегодняшним потребителем.
Front Street: В случае производства автомобильных панелей изготавливаются формы, чтобы каждая деталь соответствовала панели OEM.Можете ли вы описать материалы / общий процесс, использованный при создании этих форм?
Грег Шампин / Ультра-углерод: Это длинный и скучный ответ, и я, вероятно, мог бы провести целый семестр только по нашей технике изготовления пресс-форм, и каждый магазин делает свою работу по-своему. Но я опущу детали и коснусь основ, чтобы ответ был кратким и понятным.
Пресс-форма — самая важная часть процесса создания качественных частей тела. Все начинается с плесени.Если у вас нет хорошей формы, у вас не может быть хорошей роли. Во-первых, вы должны начать с качественной части. Предпочтительнее использовать оригинальные запчасти, но в случае с более старыми автомобилями это не всегда возможно или практично. Итак, найдите самую красивую деталь, которую вы можете достать, независимо от цены, и сделайте ее лучше.
Я получил двери бесплатно и заплатил более 1000 долларов за одну дверь. В любом случае, вы потратите время или деньги, чтобы сделать часть настолько красивой, насколько это возможно. Затем вы устанавливаете на деталь фланцы и заполняете все отверстия.Затем вы наносите инструментальный гелькоут, а затем несколько слоев стекловолокна в течение недели. Нельзя наносить слишком много стекловолокна за один раз, иначе вы исказите деталь или сделаете волдыри на гелевом покрытии. Итак, мы не торопимся с работой со стеклом. Нет смысла портить всю эту другую работу только ради того, чтобы сэкономить день или два.
Когда форма готова, мы сушим песок, влажный песок и затем полируем форму. Это чрезвычайно трудоемкий процесс, который начинается с бумаги с зернистостью 80 и проходит на каждом этапе наждачной бумаги от 80 до 3000.Когда мы достигаем зернистости 3000, мы выполняем трехэтапный процесс полировки детали, а затем мы можем воском ее восемь раз перед укладкой первой части. В итоге мы тратим где-то 160-200 часов рабочего времени на создание одного набора дверных форм от начала до конца, если у нас нет работы над самими деталями. Как вы можете видеть, изготовление деталей очень высокого качества требует больших затрат на изготовление пресс-форм. Да, мы могли бы изготовить тот же набор дверных форм за 40–50 часов и иметь в четыре раза больше деталей, предлагаемых в нашем каталоге, но тогда формы не будут давать такие же высококачественные детали, которые мы предлагаем.Это причина того, что сроки изготовления пресс-форм от шести месяцев до года являются обычным явлением. На то, чтобы сделать это правильно, уходит очень много времени, а у нас всегда есть невыполненная работа.
KC Chou / APR Характеристики: Для производства панелей OEM из углеродного волокна, которые подходят как пластиковые детали OEM, мы используем пресс-форму для заготовок с предварительно пропитанным углеродом. Это единственный способ обеспечить заводскую установку и качество панели из углеродного волокна. Форма для заготовок имеет меньше шансов на коробление и усадку при отверждении детали при высокой температуре.Также, используя препрег из углеродного волокна, мы можем контролировать толщину материала панели для плотно прилегающих участков. Формы для заготовок создаются путем цифрового сканирования прототипа в файл САПР, а затем обработки алюминиевых заготовок с ЧПУ до модулированной многокомпонентной пресс-формы, что приводит к чрезвычайно высокой стоимости оснастки из углеродного волокна с использованием этого процесса.
Front Street: Нужно ли заменять пресс-форму для обеспечения точности по мере износа?
Грег Шампин / Ультрауглерод: Да и нет.Мы создаем наши пресс-формы, чтобы выдержать нагрузку до 50 циклов. Это означает, что мы сможем вытащить 50 деталей из формы, прежде чем ее нужно будет заменить. Некоторые детали более жесткие для форм и уменьшают это число, некоторые детали мы можем получить 100 или более вытягиваний. И другие формы для таких вещей, как сиденья, которые мы производим, можно ремонтировать или перекрашивать снова и снова, потому что для них нет оригинальной формы, которой они могли бы придерживаться.
KC Chou / APR Performance: Да и нет. В зависимости от материала пресс-форм и количества единиц детали, которые вы планируете воспроизвести.Большая часть кристаллизатора для одной заготовки прослужит от 4 000 до 5 000 единиц, прежде чем вам понадобится новая оснастка. Срок службы одной пресс-формы для композитной оснастки составляет около 400 единиц. Если вы планируете использовать 2000 единиц и используете форму для заготовок, вам, вероятно, вообще не потребуется ее заменять. Но если вы используете композитную форму, вам понадобится как минимум пять форм для завершения этого производства.
Front Street: Какие дополнительные шаги предпринимаются в процессе создания панели, чтобы гарантировать точность вашего продукта?
Greg Shampine / Ultra-Carbon: Как было сказано выше, все дело в медленном укладывании стекла — чем медленнее, тем лучше.Кроме того, делая форму толстой и жесткой, она не сгибается или перекручивается во время хранения. Наши формы обычно изготавливаются из твердого стекловолокна толщиной от до ½ дюйма.
Форма для вытяжки обычно весит около 150 фунтов или более. Кроме того, мы сохраняем оригинальную деталь, из которой была изготовлена форма, поэтому мы можем периодически проверять форму, чтобы убедиться, что она не деформировалась во время хранения. Это особенно характерно для вытяжек и дверных обшивок, поэтому мы часто сверяем их с оригинальной деталью.
И, наконец, мы поощряем отзывы наших клиентов, ОСОБЕННО, если они отрицательные.Некоторые производители хотят снять с себя ответственность или зарыться в песок, когда что-то не подходит. Это редкое явление, но я хочу знать об этом, чтобы исправить это до того, как следующий клиент получит деталь из этой формы, и поработать над решением проблемы, связанной с этой деталью. Иногда это что-то, что они могут легко исправить с небольшим руководством, иногда нам нужно отправить запасную часть. Большинство клиентов, которых мы обслуживаем, строят маслкары возрастом от 35 до 45 лет, поэтому каждая проклятая машина будет немного уникальной.Всегда будут небольшие проблемы с установкой, но если они начинают с качественной детали, она обычно подходит для 99% автомобилей. Форма не должна быть изменяемой, старые автомобили уже достаточно изменчивы…
KC Chou / APR Performance: Мы предпринимаем дополнительные меры по замене всех OEM-компонентов, таких как вентиляционные отверстия капота, вентиляционные отверстия крыльев, воздушные заслонки, диффузоры , зеркала, внутренние консоли и световые лицевые панели. Измерение и документирование заводской толщины панели, изготовление конечного продукта той же толщины и технических характеристик, что и заводская деталь.Расположение зажимов и выступов такое же, как и у оригинального заводского компонента, и мы повторно используем все заводское оборудование с элементом из углеродного волокна. Все эти шаги предназначены для обеспечения и гарантии того, что все наши компоненты из углеродного волокна подходят для изготовителей оборудования.
Front Street: Существуют ли какие-либо конкретные продукты, которые требуют более утомительных производственных процессов, чем другие?
Greg Shampine / Ultra-Carbon: Каждая деталь индивидуальна. Даже две разные дверные обшивки разные.Внутренние дверные панели для наших стандартных дверей довольно утомительны. На изготовление каждой внутренней панели и около 35 отдельных частей из углеродного волокна уходит день. Крышки клапанов и бамперы тоже довольно утомительны, но в большей степени это заноза в заднице, потому что их так легко испортить. Мне не нравится делать ни то, ни другое, но я люблю делать двери.
KC Chou / APR Performance: В нашей линейке продуктов много компонентов, которые требуют утомительных производственных процессов. Например, капот C7 / Z06 Corvette и вентиляционные отверстия крыльев и вентиляционные отверстия крыльев Viper ACR — эти части состоят из множества маленьких прорезей и отверстий, и все они должны быть идеально обрезаны и равномерно подогнаны к одному и тому же заводскому размеру.Отдельные вкладки и зажимы необходимо разместить и приклеить к карбоновому элементу, соответствующему месту расположения оригинального производителя, что является чрезвычайно трудоемким процессом.
Front Street: Какую роль играет конструкция в усилении / прочности готового продукта?
Greg Shampine / Ultra-Carbon: Как и следовало ожидать, конструкция детали — это все. У вас может быть три парня, которые делают один и тот же капюшон из одной и той же формы, с одинаковым количеством слоев углеродного волокна, и один получается тяжелым и хрупким, другой — мягким спагетти, а третий — идеальным.Смола играет в этом большую роль. Существует столько же различных смол, сколько кодов краски для новых автомобилей. Выбор безграничен, а цены могут варьироваться от 10 до 800 долларов за галлон, и даже больше за действительно редкие вещи.
Затем основной материал. Некоторым частям это нужно, некоторым нет. Это целая наука сама по себе. Существуют также десятки различных материалов для сердцевины. Однако при работе с углеродным волокном вы действительно хотите работать с материалом сердцевины, предназначенным для использования с углеродным волокном в среде, в которой будет использоваться деталь.Материал сердечника, который мы обычно используем, на самом деле дороже, чем сам углерод. С углеродом ядро не обязательно означает экономию средств, это просто еще один фрагмент головоломки.
KC Chou / APR Производительность: Конструкция арматуры играет огромную роль в нашем конечном продукте. Например, крылья полностью усилены дополнительными слоями углеродного волокна в местах крепления к нему. Крылья с высокой прижимной силой усилены внутренней поперечной балкой. Некоторые из применений аэродрома поставляются с дополнительными распорками для усиления заводских обшивок бампера.Задние диффузоры часто поставляются с дополнительными опорами и оборудованием для установки на шасси автомобиля.
Front Street: Как некоторые общие дефекты углеродного волокна возникают в процессе создания?
Грег Шампин / Ультра-углерод: Это довольно сложный вопрос, но сначала я дам вам комичный ответ, который я люблю давать людям:
Углеродное волокно вас ненавидит. Это не твой друг, он не хочет быть твоим другом. Он хочет, чтобы вы облажались, чтобы посмеяться над вами.Он хочет надрать вам по яйцам, когда вы не смотрите, а затем сказать всем своим друзьям, насколько вы глупы. Есть дюжина способов правильно сделать углеродное волокно и сотни способов испортить его. Если вы занимаетесь чистым углеродом, есть всего пара способов сделать это правильно и тысячи способов испортить дело. Отстойно работать и отстойно обращаться, но награды в виде почти идеальной роли достаточно, чтобы любой стал наркоманом.
Обратите внимание, я не сказал «идеальная деталь», я сказал «почти идеально». Не существует идеальной детали из углеродного волокна.Я всегда могу найти недостаток. Я никогда не делал идеальных ролей, это просто невозможно. Иногда он такой крохотный, как нить переплетения, неуместного на незаметном месте, иногда крошечный пузырь воздуха, застрявший между двумя рядами жгута.
Наиболее распространенные дефекты связаны с воздухом или смолой. Воздух попадает в деталь из-за неравномерного распределения вакуума или из-за того, что смола не может проходить через деталь достаточно эффективно, чтобы вытеснить воздух. Иногда эти проблемы могут быть настолько незначительными, что деталь все еще идеально подходит для использования, иногда они могут привести к тому, что хорошая деталь станет непригодной для использования.Это действительно зависит от степени тяжести.
Вот почему влажная укладка углеродного волокна без мешков — действительно плохой выбор для качественных деталей. Конечно, в крайнем случае это работает. Я отремонтировал у рельсов дрэг-кары со скоростью 250 миль в час, которые нужно было промокнуть и вылечить за ночь, чтобы парень мог снова выехать на трассу на скорости 250 миль в час на следующее утро. Но это не идеально, и клиенты не должны платить за такую работу над новой деталью.
Если бы вы могли разделить рядом мокрую уложенную часть без мешка и часть с мешком бок о бок и исследовать их, вы бы ясно увидели, что вакуум из-за мешка детали создает гораздо более однородную дисперсию смолы с меньшим количеством воздушных пустот и меньшим общим насыщением смолой. части.Итак, вакуумная упаковка в целом — лучший способ.
Чтобы сделать еще один шаг вперед, мы используем метод, называемый вакуумной инфузией, также известный как инфузия смолы и маркетинговый термин «сухой уголь». Здесь материал укладывается в форму полностью сухим, помещается под полный вакуум, а затем смола впрыскивается в форму с использованием отрицательного давления, создаваемого вакуумом. Когда все идет хорошо, этот процесс создает почти безупречную, однородную деталь, где вы полностью контролируете распределение смолы, плотность, время отверждения, проникновение смолы и множество других факторов.
Это метод, который такие компании, как SpaceX, используют для создания форм для своих чувствительных частей космических кораблей. Из-за соответствия требованиям FAA они фактически не могут изготавливать детали для чего-либо летного из чего-либо, кроме препрега, но формы, из которых сделаны эти детали, сделаны так же, как мы.
KC Chou / APR Характеристики: В процессе изготовления угольного препрега требуется автомобильное прозрачное покрытие, которое впоследствии наносится на верхнюю поверхность углеродного волокна.Между слоями прозрачных слоев немного влаги может остаться между ними, и это приведет к образованию пятнистых пятен. Искажение рисунка плетения и пузырьки воздуха не являются обычным явлением в нашем процессе формования препрега, но они обычны в процессе мокрой укладки.
Front Street: Сколько слоев материала используется для создания прочности, необходимой для внешней панели кузова?
Greg Shampine / Ultra-Carbon: Это действительно зависит от панели корпуса, но обычно требуется от двух до четырех слоев, плюс иногда сердцевина.Мы почти всегда начинаем со слоя саржи толщиной 6k на наших деталях, потому что все они сделаны из чистого угля; Я просто считаю, что 6к выглядит лучше 3к.
Имейте в виду, что единственная разница между саржевой 3k и 6k — это количество отдельных прядей в каждом ряду жгута. Итак, жгут 6k выглядит немного шире 3k, а ткань почти вдвое тяжелее слоя 3k, но она заменяет два слоя 3k. Если хотите, назовите 6k «двухслойным».
Некоторые вещи, которые мы делаем, например, задние фонари и лицевые панели фар, представляют собой просто два слоя 6k, и все, без сердечника.Другие вещи, такие как капюшоны, широкие и плоские, поэтому им нужно больше прочности. В итоге получается слой 6k, два-три слоя 3k и сердцевина.
KC Chou / APR Performance: Мы используем три слоя материала для неструктурных деталей и пять или более слоев для конструктивных деталей.
Front Street: Чем это отличается от чего-то вроде внутренней панели?
Greg Shampine / Ultra-Carbon: Внутренняя панель обычно состоит из двух-трех слоев.Также важно сделать внутренние панели из жаропрочной или огнестойкой смолы. Если ваши внутренние панели сделаны из обычной смолы, которая начинает плавиться при температуре 120–150 градусов, то даже небольшое количество огня мгновенно превратит их в слизь и почти сразу же подвергнет вас возгоранию. Высокотемпературная смола тоже подойдет, но она может дать вам несколько дополнительных секунд защиты в то время, когда каждая секунда имеет решающее значение для вашего выживания.
KC Chou / APR Характеристики: Поскольку это неструктурная внутренняя панель, мы используем от двух до трех слоев материала.
Front Street: Каким вы видите использование композитных материалов в других областях производства автомобильных запчастей?
Грег Шампин / Ультра-углерод: Я думаю, было бы проще спросить, как его нельзя использовать для автомобильных деталей — на самом деле, нет предела. Я думаю, что мы далеки от того, чтобы это было практично, но даже такие вещи, как каркасы безопасности, могут быть построены из углеродных труб или как полностью цельная конструкция.
Проблема с этим и трудность в том, что нужно будет установить стандарт. Углерод по-прежнему остается таким черным искусством, что подобные инновации невозможны до тех пор, пока стандарты не станут универсальными. Прямо сейчас у каждого свой образ действий. Нет двух одинаковых магазинов. Таким образом, это делает практически невозможным регулирование конструкции или стандартизацию метода строительства.
Вы можете регулировать расположение рулей в типичном гоночном автомобиле, их толщину и внешний вид сварных швов.Все это легко контролировать санкционирующим органом. Постройте драгстер с лучшим топливом с монококовым шасси из углеродного волокна, сформованным с внешней обшивкой, и вы сможете создать что-то намного, намного более прочное, чем типичный корпус драгстера… ..но кто позволит вам запустить его? Как они это удостоверят? Какой стандарт? Даже если вы перестроили его на 300 процентов, а первый прототип оказался вдвое тяжелее драгстера для трубной эстакады, они все равно надорвут вам задницу с любого пути, даже если вы попытаетесь запустить его.
KC Chou / APR Характеристики: Углеродное волокно широко использовалось в аэрокосмической программе еще в 1970 году, затем оно стало материалом для спортивных товаров, строительным материалом и материалом для гоночной промышленности, а теперь мы видим, что оно часто используется в ветроэнергетической программе и медицине. поле за последнее десятилетие.На данный момент мы видели несколько компаний, использующих его для производства мебели и одежды. Я думаю, если у вас есть идея, из углеродного волокна можно сделать все, что вы пожелаете.
Front Street: Грег, мы понимаем, что вы экспериментировали с многослойными компонентами двигателя из углеродного волокна (в частности, коромыслами). Считаете ли вы, что использование компонентов двигателя из углеродного волокна когда-нибудь станет широко распространенным? Есть ли другие части, с которыми вы экспериментируете?
Грег Шампин / Ультрауглерод: Да, они будут широко распространены.Коромысла и шатуны, вероятно, являются единственным наиболее выгодным местом для таких деталей, но их долгосрочное использование в среде дрэг-рейсинга еще не доказано. Могу я заставить их работать на выходные? Конечно. Но кто потратит 4000 долларов на комплект изнашиваемого предмета, чтобы заменять его каждые выходные? Итак, долговечность — вот что сделает их практичными и широко распространенными. Мы недалеко от этого.
Честно говоря, я не касался этого проекта несколько месяцев, потому что мы просто завалены производством частей тела.Хотел бы я, однако, моя страсть заключается в деталях заготовок и конструктивных элементах. Если бы я мог уйти от изготовления частей тела и сосредоточиться только на конструкционном / заготовочном углероде и разработке новых дизайнов и идей, я бы не задумывался. Если бы счета оплачивались только экспериментами, не так ли? Честно говоря, я думаю, что не так давно наступит время, когда мы вообще перестанем делать части тела, холодная индейка. Может быть, кто-то, читая это, захочет бросить в меня миллион долларов и сказать: «Давай, малыш».А пока мне нужно держать двери открытыми и светить. Счета нужно оплачивать, и для этого нужно продавать части тела.
У нас в разработке есть и другие идеи. Мы можем начать эксперименты с угольными головками цилиндров и блоками двигателей. Блоки двигателя должны быть легко продаваемыми, кроме реальной цены. В два-три раза дороже алюминиевого блока из заготовок, это не было бы покупкой для кого-то с ограниченным бюджетом. Однако имейте в виду, что преимущества ошеломляют. Половина веса сопоставимого алюминиевого блока из заготовок.Отсутствие расширения и сжатия при изменении температуры приводит к более жестким допускам. Он не поглощает тепло так быстро, как алюминий, в нем меньше гармоник, и его легко исправить в случае поломки или трещины. И, что самое важное, он прочнее алюминия, поэтому вероятность того, что вы закроете блок, значительно снизится, если вы бросите удочку.
На данный момент это все чисто теоретически, но у меня есть инвестор, который хочет начать экспериментировать. Я очень рад этому.За блоками и головками из углеродного волокна, безусловно, будущее автоспорта. Я чувствую, что нахожусь в уникальном положении благодаря своим уникальным навыкам и экспериментам, которые мы уже провели, чтобы это произошло. Я обязан сделать это, чего бы это ни стоило.
Углеродное волокно в автомобильной промышленности
Углеродное волокно — популярный материал для изготовления высококачественных и долговечных потребительских товаров, от рюкзаков до велосипедов. Но именно автомобильная промышленность вторгается в приложения из углеродного волокна, которые принципиально меняют автомобили для повышения скорости и повышения энергоэффективности.
Что такое углеродное волокно?
Углеродное волокно относится к материалу, состоящему из атомов углерода, расположенных в виде длинных тонких кристаллов, которые сплетены или сплетены вместе в ткань. Затем ткань можно комбинировать с эпоксидной смолой, чтобы придать ей практически любую форму.
Благодаря расположению кристаллов в углеродном волокне, он невероятно прочен по сравнению с его размером. По этой причине материалы из углеродного волокна также легче по сравнению с другими материалами с такой же прочностью, а углеродное волокно находит применение в различных отраслях промышленности в качестве замены стальных и алюминиевых деталей.
Углеродное волокно в автомобильной промышленности
Аэрокосмическая промышленность и обрабатывающая промышленность уже воспользовались преимуществами деталей из углеродного волокна, но автомобильная промышленность активно внедряет некоторые из последних достижений из углеродного волокна. Углеродному волокну можно придать практически любую форму, включая формы, которые невозможно создать из традиционных материалов. В автомобильной промышленности углеродное волокно используется для изготовления прочных и легких деталей, которые увеличивают скорость и улучшают аэродинамику и топливную экономичность.
В настоящее время большинство автомобильных запчастей из углеродного волокна используется в спортивных автомобилях высокого класса и европейских суперкарах; хотя некоторые детали из углеродного волокна доступны на вторичном рынке. В таких деталях автомобиля, как детали кузова, колеса и обода, а также внутренняя отделка, используется углеродное волокно, благодаря его уникальным свойствам и элегантному внешнему виду.
Корпус из углеродного волокна
Поскольку спортивные автомобили должны быть скоростными, углеродное волокно является идеальным материалом для уменьшения общего веса автомобиля без ущерба для безопасности.BMW, Chevrolet Corvette и Alfa Romeo включили элементы из углеродного волокна в кузова своих высококлассных автомобилей для повышения скорости и энергоэффективности.
BMW использует компоненты из углеродного волокна в верхних частях своего седана 7-й серии, такие как элементы крыши и опорные стойки, чтобы снизить центр тяжести автомобиля. Alfa Romeo 4C, с другой стороны, имеет полностью карбоновое шасси, что снижает вес автомобиля до 2500 фунтов.Другие автомобили аналогичного стиля и размера обычно весят 3000 фунтов или более, что делает 4C легкой роскошью в своем классе.
Компоненты кузова из углеродного волокна — это больше, чем просто ускорители. Легкие шасси также идеально подходят для электромобилей. При меньшем общем весе автомобиля можно использовать меньшую батарею для достижения того же или даже более высокого уровня производительности, поскольку для движения автомобиля требуется меньше энергии.
Колеса и диски из углеродного волокна
При цене в 65 000 долларов Alfa Romeo 4C — мечта большинства потребителей.Колеса и ободья на основе углеродного волокна стали одним из самых популярных применений материала в автомобильной промышленности, доступном в качестве дополнительных компонентов или запчастей.
Конструкция и конструкция колес из углеродного волокна снижают шум и вибрацию, обеспечивая при этом такие же легкие, но сильные преимущества использования углеродного волокна в шасси автомобиля. Углеродное волокно лучше, чем сталь и алюминий, поглощает высокочастотный шум, вибрацию и резкость дороги, что делает кабину автомобиля более тихой.
При отливке из надлежащей эпоксидной смолы углеродное волокно также может выдерживать нагрев и давление с течением времени и не деформируется, что делает его отличным материалом для колес и ободов. Они также уменьшают вес и повышают топливную экономичность транспортных средств, а поскольку они доступны на вторичном рынке, они могут принести пользу практически любому транспортному средству.
Обода из углеродного волокнавыглядят более эстетично, придавая колесам гладкий, обтекаемый вид, который мгновенно добавит стоимости любому автомобилю.Однако внешний вид — это еще не все для обода из углеродного волокна, и они обладают теми же преимуществами, что и колеса, за счет уменьшения веса и сохранения формы под давлением.
Интерьер из углеродного волокна
Обода— это сочетание формы и функции, но иногда вам просто нужен гладкий, высококачественный вид. Углеродное волокно по-прежнему остается вашим предпочтением. Элементы интерьера, обычно сделанные из полимеров или алюминия, заменяются элементами из углеродного волокна для большей детализации. Из-за своей прочности углеродное волокно также является отличным материалом для интерьера.
Транспортные прицепы из углеродного волокна
Подобно кузовам из углеродного волокна в спортивных автомобилях, появляются различные концепции применения углеродного волокна в транспортных средствах, а именно в полуприцепах для грузовиков. Walmart в сотрудничестве с Peterbilt, Great Dane Trailers и Capstone Turbine создали концептуальный полуприцеп с прицепом из углеродного волокна. 53-футовый прицеп, наряду с улучшенной конструкцией кабины, по оценкам, на 20% более аэродинамичен, чем средний полуприцеп.Более легкие прицепы помогают отгрузочным центрам соответствовать требованиям по весу и позволяют грузовикам сократить время в пути.