Как обрабатывают кромку стекла | Статьи компании Технопарк
Главная » Новости » Шлифовка и полировка кромки стекла: особенности процессаОбработка стекла – один из важных этапов изготовления готовой продукции из этого материала. Когда завершается резка стекла, торец имеет неаккуратный внешний вид, а острые углы могут стать причиной травм в процессе эксплуатации изделия. Шлифовка и полировка позволяют сделать материал безопасным для дальнейшего использования. Исключение – вырезка стекол для окон и дверей, когда обработка лишь отнимает лишнее время и деньги.
Процесс полировки торца стекла – важный
этап обработки материала, в ходе которого с поверхности удаляются все сколы и
неровности. При полировке используется высокоточное оборудование, которое
способствует удалению тонкого слоя стекла на режущей кромке. При этом размеры
заготовки не изменяются. Это заключительный этап производства, когда края заготовки
становятся прозрачными и идеально гладкими. Форма прозрачных торцов изделий
может быть полукруглой или трапециевидной.
Обработанное стекло с декоративной матовой кромкой используется при изготовлении элементов декора для мебели или полок с подсветкой, витрин, а также в области дизайна интерьеров.
Как шлифуют кромку стекла?
Процесс шлифования является начальным при создании привлекательного торца изделия. Выполнить такую процедуру можно и дома, для этого потребуется дрель, тарельчатая насадка, а так же шлифбумага. Такой метод подойдет только для домашней обработки, а в условиях масштабного производства задействуются шлифовальные станки, при помощи которых можно обрабатывать как фигурную, так и прямолинейную кромку. В ходе шлифования используют абразивные диски или ленты с различной степенью зернистости. Если стекло шлифуется на шайбочном станке, то в ходе грубой обработки материал накладывается на вращающийся круг. При помощи таких станков производится ультразвуковая полировка или обработка щетками.
Как происходит полировка?
Технология шлифовки кромки стекла позволяет придать поверхности эффект матовости, с легкой шершавостью с зеленоватым оттенком. При этом после обработки шлифовальной машиной допустимы небольшие трещины или царапины. Для их устранения используется второй этап обработки – полировка при помощи мягких волокон. В результате воздействия полировальной машиной, кромки приобретают прозрачность и гладкость, а изделие становится эстетически привлекательным. В отличие от шлифовки, при полировке выполняется более тонкая обработка характеристики которой зависят от толщины заготовки.
Цельностеклянные изделия обладают полировочным торцом, придающим им яркий дизайн. Также обязательно проводится полировка перед закаливанием стеклянных изделий. Полировальные работы начинаются только после завершения шлифования с использованием абразива с самой мелкой зернистостью, так как из-за низкой абразивности при полировке крупные дефекты с кромки не будут удалены.
Полирование или шлифование кромки стекла
Обработка торца стекла является обязательною процедурой в случае использования стекольного покрытия в качестве открытых поверхностей, которые могут представлять собой полочки, дверцы, столешницы и другие изделия подобного рода.
Осуществление выравнивания торца включает в себя процедуру шлифовки или процедуру полировки.
Процесс шлифовки или полирование кромки стекла необходим для придания ему более гладкой поверхности и получения различных форм (еврокромка, каскад, карандаш, трапеция).
Вашему вниманию представлено профессиональное выполнение обработки стеклянных поверхностей с применением различных методов:
Шлифовка
Резка стекла является начальным периодом рабочего процесса, в результате которой мы получаем достаточно острые и опасные для здоровья человека края. Вначале этой процедуры устраняются все присутствующие на стекольном торце зазубрины и неровности, а после чего осуществляется выделывание кромки определенной формы.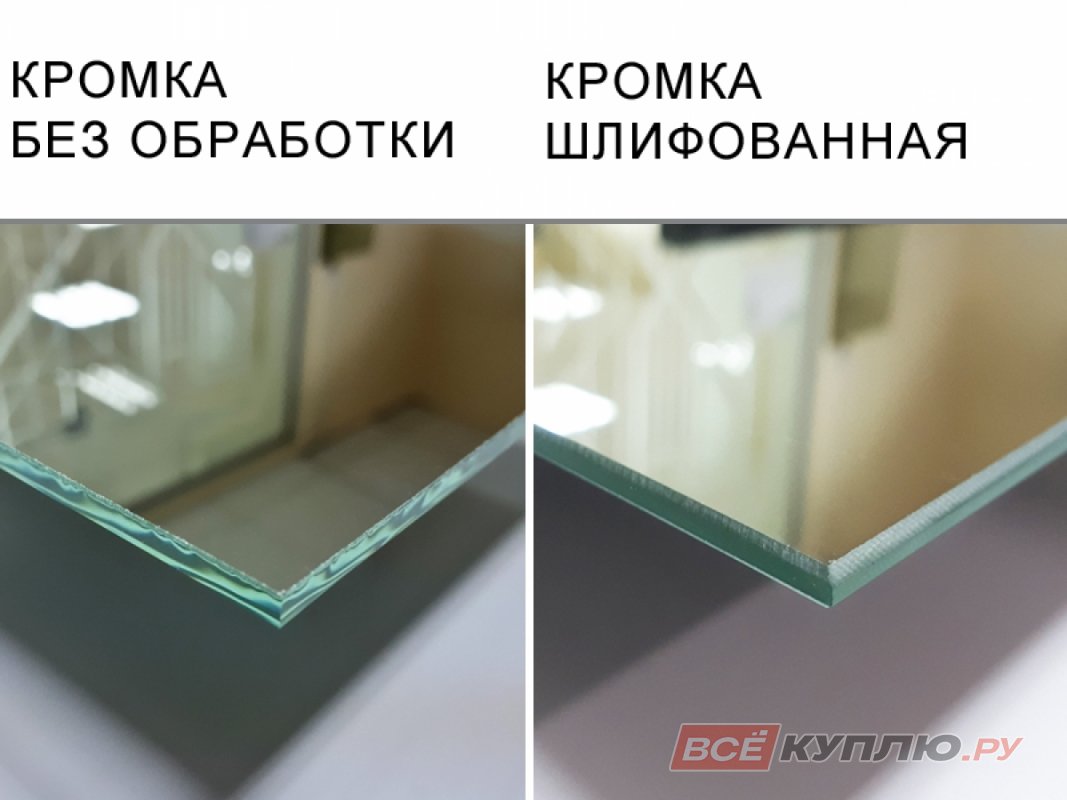
Процесс шлифования позволяет удалять все возможные острые или же опасные грани и придает кромке небольшую матовую шероховатость.
Полировка
Процедура полировки торца стекла, производится с целью придания стекольной поверхности гладкости и прозрачности. Обработка кромки особенно важна, поскольку несет в себе не только безопасность при использовании, но и важную эстетическую составляющую. Применение стеклянных конструкций в интерьере частного дома или же квартиры должно отвечать всем требованиям и нормам безопасности, и, конечно, радовать глаз хозяина. Помните о том, что плохо обработанный край стекла может поранить и даже отколоться.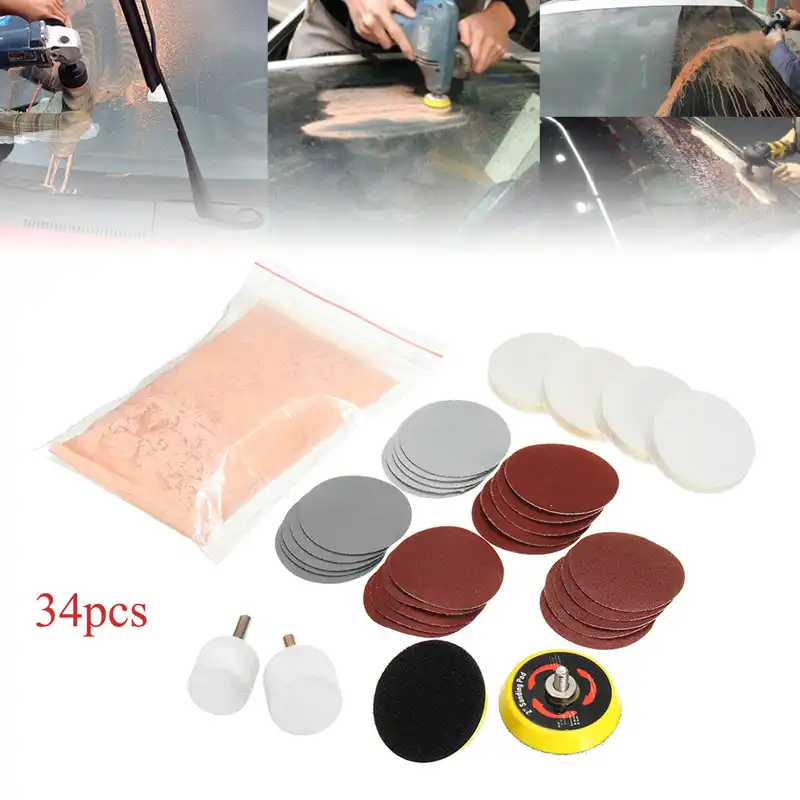
Шлифовка кромки стекла – простой процесс сделать стекло безопасным — Инфокам
Всем
известно, что обыкновенное стекло при разрезании или разбитии имеет
острые кромки, которые могут причинить серьезные раны. Чтобы избежать
порезов и сделать края стекла безопасными, их подвергают процедуре под
названием шлифовка кромки стекла. Благодаря несложному процессу край
стекла не только больше не опасен, но и выглядит очень эстетично.
- на производстве;
- в домашних условиях.
В
первом случае процесс происходит автоматически на специальных машинах.
Существуют целые шлифовальные линии, способные обрабатывать большие
объемы стекол. Такие аппараты стоят на крупных производствах, например,
на заводах по изготовлению стекла или на мебельных фабриках. Суть
процесса очень простая – после порезки большого листа стекла на
необходимые фрагменты, они плашмя укладываются на специальные валики, по
которым передвигаются к шлифовальной головке. Использование алмаза в
обработку стеклянной поверхности. Сама процедура может занимать от
нескольких секунд – все зависит от размера обрабатываемой кромки.
В
домашних условиях произвести шлифовку кромки стекла можно довольно
легко. Для проведения процедуры не понадобится дорогостоящий инструмент
или расходные материалы и сам процесс не займет много времени.
Обрабатываем стекло своими руками
Существует три основных формы шлифованной поверхности:
- полукруглая или «карандаш»;
- правильная трапеция;
- произвольная
Любую
из этих разновидностей можно произвести в домашних условиях.
простым вариантом считается полукруглая форма. Для ее достижения не
требуется прилагать особых усилий, поэтому она чаще всего и встречается
на кромках стекол, зашлифованных вручную.
Шлифовка кромки стекла в домашних условиях проводится вручную или при помощи бытовой дрели.
В
первом случае нам понадобится наждачная шкурка различной зернистости.
Как правило, используется крупная, средняя и мелкая. Рекомендуется
приобретать именно шкурку, а не бумагу по причине того, что бумага очень
быстро придет в негодность за счет острых кромок стекла. Также нам
примерно таким образом – наматываем крупнозернистую шкурку на брусок и
поступательными движениями обрабатываем острый край стекла. После
обработки всего участка поверхности меняем шкурку на среднезернистую и
повторяем процесс. Аналогично поступаем и с применением мелкозернистой
шкурки. Главным индикатором завершения процедуры является матовый край
стекла.

порезаться.
При
работе с дрелью процедура аналогичная с той лишь разницей, что
креплении-липучке для дрели. Некоторые люди рекомендуют воспользоваться
«болгаркой», аргументируя выбор отсутствием надобности приобретать
специальную насадку и быстротой процесса. На самом деле, пользоваться
этим инструментом для шлифовки стекла нельзя из-за большого количества
оборотов шлифовальной машинки. Стекло является довольно хрупким
материалом и при перегреве быстро трескается. Для шлифовки необходимы
низкооборотные инструменты (1200-1700 об/мин). Этим характеристикам
соответствует бытовая дрель, которая есть практически в каждом доме. Для
избегания перегрева стекла при использовании брели, кромку во время
Важным моментом является соблюдение элементарных правил безопасности при работе со стеклом:
- шлифовку необходимо проводить в хорошо проветриваемых помещениях или на открытом месте;
- при работе использовать респиратор, чтобы не вдыхать мелкую стеклянную пыль;
- пользоваться защитными перчатками.
На выставке «Мир стекла»
будет представлен широкий выбор современного оборудования для полировки
и шлифовки стекол и зеркал в условиях производства или дома. Кроме
оборудования на выставочных стендах будут располагаться различные
расходные материалы и вспомогательные приспособления. Само мероприятие
пройдет в период с 6 по 9 июня на территории ЦВК «Экспоцентр» в
павильоне №2.
Cпособы и виды обработки стеклоизделий
Cпособы и виды обработки стеклоизделий
Категория:
Шлифование и полирование стекла
Cпособы и виды обработки стеклоизделий
Существуют следующие способы обработки стекла и стеклоизделий: механическая (холодная) обработка поверхности и края стеклянных изделий, химическая, тепловая и нанесение поверхностных покрытий. При декоративной обработке изделий эти способы используют в разных сочетаниях.
Механическая (холодная) обработка — это обработка стекла резанием. К механической обработке поверхности изделий относится шлифование, полирование, гранение и гравировка. Такие способы, как матирование, притирка (пришлифовывание), сверление и градуирование, являются частными видами перечисленных способов.
Шлифованием называется процесс снятия слоя стекла абразивным инструментом (шлифовальным кругом). Шлифованию подвергают поверхности плоские и другой формы. Цель шлифования — во-первых, обеспечить правильную геометрическую форму изделия и придать ему точные размеры, во-вторых, подготовить поверхность обрабатываемого изделия к последующей механической обработке — полированию.
Шлифование включает в себя две стадии. Первая стадия — обдирка или грубое шлифование; на этой стадии применяют крупнозернистые абразивы. Вторая стадия — дистировка или тонкое шлифование, когда поверхность обрабатывают последовательно все более мелкими абразивными порошками.
Сущность процесса шлифования заключается в следующем. Вращающийся в горизонтальной или вертикальной плоскости круг (шлифовальник) опирается своей тяжестью на зерна абразива, находящиеся на поверхности обрабатываемого изделия. Стекло, в свою очередь, перемещается либо в горизонтальной, либо в вертикальной плоскости вращательным или прерывисто-поступательным движением. При этом зерна абразива перекатываются и проникают в пространство между стеклом и шлифующей деталью.
В процессе шлифования шлифующая деталь опирается приблизительно на 15—20% зерен, находящихся под ней. Эти зерна передают стеклу усилия от находящейся в движении шлифующей детали. Размеры зерен абразивного материала неодинаковы в различных направлениях, поэтому и воздействие этих зерен на стекло неодинаково. Оно носит вибрационно-ударный характер. В результате в точках соприкосновения зерен со стеклом возникают трещины, максимальная глубина которых зависит от природы и размера зерен выбранного абразивного материала. Крупные зерна абразивного материала более прочны, поэтому при обработке стекла такими зернами образуются более глубокие трещины, чем при обработке мелкими.
После многократного действия зерен поверхностный слой стекла покрывается сетью трещинок. При последующем прокатывании зерен удаляются осколки, отделяющиеся в результате растрескивания поверхностного слоя от основной массы стекла. Это приводит к образованию «выколок» или «каверн». Бесчисленное количество расположенных рядом выколок способствует рассеянию света и образует матовую поверхность, характерную для шлифованного стекла. Глубина выколок от 3 до 30 мкм. Глубже этого поверхностного, изрытого выколками слоя расположен другой, с более слабыми признаками разрушения. Этот второй слой образован трещинами, идущими в глубь стекла. Толщина его в 1,2… 1,3 раза больше толщины верхнего рельефного слоя. Отдельные трещины проникают еще глубже.
Таким образом, при шлифовании стекла происходят два параллельных, совпадающих по времени, но не по месту процесса: при первом, который является подготовительным, происходит разрушение на некоторую глубину поверхности с образованием развитой сети трещинок; при втором, являющемся производительным, из верхней части слоя, покрытого трещинами, извлекаются осколки, отделенные от основной массы стекла. При шлифовании все более мелкими абразивными порошками структура обрабатываемой поверхности стекла подготовляется к следующей стадии процесса — полированию. В некоторых случаях поверхности, подвергнутые шлифованию, оставляют неполированными, матовыми.
В механическом разрушении стекла при шлифовании активно участвует и вода, которую подают на обрабатываемую поверхность. Проникая в образующиеся трещины стекла, она оказывает в силу своей упругости расклинивающее действие, что значительно снижает поверхностную прочность стекла, способствуя тем самым повышению производительности сошлифовыва-ния.
Полированием достигаются высокая чистота и зеркальный блеск поверхности стекла. Полирование обычно выполняют вслед за шлифованием. Эти процессы взаимосвязаны. Однако назначение и природа их различны.
Механизм процесса полирования можно представить следующим образом. Мягкий полировальник (круг, изготовленный из мягких материалов: войлока, фетра, сукна) с закрепленными на его поверхности зернами полировального порошка снимает во время вращения с вершин, образовавшихся при шлифовании выколок, защитную пленку. Мгновенно на обнажившихся участках выколок от соприкосновения с влагой, содержащейся в полировальной суспензии, образуется пленка, которая при очередном повороте полировальника снимается полировочным порошком. Под действием влаги на поверхности стекла происходит процесс гидролиза, т. е. химическое взаимодействие поверхности стекла с водой. Продукты гидролиза образуют .тончайшую поверхностную пленку, защищающую стекло от дальнейшего разрушения. По химическому составу эта пленка представляет собой гель кремниевой кислоты. На свежей поверхности стекла пленка появляется чрезвычайно быстро, прочно сцепляется с основным стеклом и имеет высокую механическию прочность. Толщина пленки колеблется в зависимости от химического состава стекла от 0,001 до 0,1 мкм.
Скорость полирования зависит от ряда технологических параметров. Так, повышение давления полировальника на изделие всегда увеличивает скорость полирования. В практике полирования это давление колеблется от 3000 до 13 000 Па. Дальнейшее повышение давления может привести к увеличению температуры стекла и разрушению изделия. На повышение производительности полирования положительно влияет увеличение скорости полировальника, на практике она составляет 4…7 м/с. Дальнейшее увеличение скорости нежелательно, так как это может привести к сбрасыванию полирующего материала с полировальника и к нарушению его контакта со стеклом.
Большое значение имеет температура поверхности стекла. Обычно полирование ведут при повышенных температурах (60… 70 °С). Дальнейшее увеличение температуры вызывает бой стекла от перегрева. Понижение температуры ниже 60°С значительно замедляет процесс полирования.
Гранение — способ обработки, при котором на поверхности изделия режущей кромкой абразивных инструментов создают узоры в виде разнообразных надрезов или прорезов, а также придают поверхности изделия правильные геометрические грани. Как прием механической обработки стекла гранение было заимствовано из приемов обработки природных камней.
По своей природе процесс гранения не отличается от процесса шлифования стекла, основан на возвратно-ударном действии зерен абразивного порошка на поверхность стеклянного изделия и отличается только большим съемом стекла в процессе обработки. Наибольшее распространение гранение получило при декоративной обработке хрустального стекла.
Разновидностью гранения является алмазная резьба, некоторые элементы рисунков которой напоминают граненые драгоценные камни и вызывают игру света.
Гравирование — вид обработки, при которой на поверхности изделия вырезают различные изображения, орнаменты, надписи. Гравированные рисунки бывают выпуклые и углубленные.
Сверление — обработка, при которой в результате резания сверлом в стекле образуются сквозные отверстия. Чаще всего отверстия высверливают в технических стеклах. В исключительных случаях сверлению подвергают декоративные изделия.
Сверление — длительная операция, в процессе сверления изделие может расколоться, прочность изделия после сверления значительно понижается, поэтому отверстия в стеклянных изделиях целесообразней делать в процессе их изготовления прожиганием или прокалыванием при формовании.
При сверлении используют охлаждающие жидкости: воду, керосин или скипидар. Назначение этих жидкостей состоит не только в охлаждении стекла, но и в удалении мелких обломков и крошек стекла. Под просверливаемое изделие подкладывают мягкую тонкую подложку. Чтобы на выходе сверла из изделия не образовывались большие раковины и выколки, при достижении сверлом определенной глубины, изделие переворачивают и сверлят с другой стороны.
Градуированием на поверхность изделий наносят основные (опорные) точки, необходимые для дальнейшего построения отсчетных или измерительных шкал. Градуирование широко используется при изготовлении химико-лабораторного стекла и специальных стекол, используемых в точном приборостроении.
Химическая обработка — декоративная обработка стекла, при которой художественный эффект достигается путем взаимодействия компонентов состава стекла с химическими реагентами (газообразным фторидом водорода HF, его водными растворами, плавиковой кислотой и ее солями), находящимися в контакте с поверхностью изделия.
При химической обработке протекают химические процессы, в результате которых фтористый водород или плавиковая кислота начинают реагировать не только с такими составляющими стекла, как оксиды лития, натрия, калия, магния, кальция, бария, свинца, цинка, но и с диоксидом кремния, который является основным компонентом большинства неорганических стекол. В процессе химической обработки образуются фториды, растворимые в воде, чем и завершается процесс разрушения поверхностного слоя стекла, т. е. происходит как бы травление поверхности. Кроме того, в зоне химического взаимодействия выделяется и кремнефтористоводородная кислота, которая вступает в реакцию с ранее образовавшимися фторидами, что приводит к появлению среди продуктов реакции солей кремнефтористоводо-родной кислоты.
Если при химической обработке образуются нерастворимые соли, прочно связанные с основным стеклом, протравленная поверхность стекла из прозрачной становится матовой. Если растворимые соли могут быть легко удалены с обработанной поверхности, то стекло остается прозрачным.
Существуют следующие виды химической обработки изделий из стекла: полирование рисунков алмазной резьбы на поверхности изделий; матирование поверхности стекла; декоративное травление.
Полирование — это процесс, при котором с поверхности изделия стекла удаляют микронеровности, образовавшиеся при механической обработке стекла. В результате полирования поверхность приобретает прозрачность и блеск. Полирование применяют главным образом для отделки элементов алмазной резьбы на изделиях из свинцового хрусталя. Изделия полируют смесью водных растворов плавиковой и серной кислот. Для каждого состава стекла устанавливают свои режимы полирования, которые корректируют в процессе работы.
Стекло, подвергнутое химическому полированию, приобретает серебристый блеск. Если вращать такое изделие, то блеск его сначала увеличивается, а затем уменьшается. Угол рассеяния может достигать 20° и более, что и объясняет появление серебристого блеска. Химически полированные стекла отражают и рассеивают лучи света, а стекла, полированные механическим способом, характеризуются полным отражением лучей.
Матирование поверхности — способ обработки стекла, при котором на поверхности изделия создается разветвленная сеть микронеровностей и выколок, что приводит к сильному рассеянию света такой поверхностью. Обработанная таким образом поверхность становится матовой. Матирование используют для придания элементам рисунка матовости или создания на поверхности изделия светорассеивающего фона.
Состав травильных растворов для матирования поверхности зависит от химического состава стекла, вида изделий и желательной фактуры поверхности: тонко- или грубозернистой. Во многих случаях изделия матируют не растворами, а пастами.
Применяют пасты жидкие и густые. При использовании жидких паст участки поверхности стекла, которые должны остаться прозрачными, покрывают защитными составами. Рисунок густыми пастами наносят на поверхность изделия без защитного покрытия.
Декоративное травление — способ обработки, при котором на поверхности изделия путем травления стекла создают рельефный рисунок. Этот способ обработки сходен с механическим гравированием стекла.
Тепловой обработкой называют совокупность операций, связанных с нагреванием изделий, выдерживанием их при высоких температурах и последующим охлаждением, направленных на изменение либо свойств стекла (отжиг, закалка), либо формы и поверхности изготовляемых изделий (моллирование, отопка, оплавление края, термическое полирование). Шлифовщик и полировщик стеклоизделий имеет дело с отопкой, оплавлением края и термическим полированием. Отопку и оплавление края изделий используют только для подготовки изделия к декоративному оформлению.
Отжиг — способ обработки изделий из стекла, который ставит целью удалить или уменьшить внутренние остаточные напряжения в стеклоизделиях.
При формовании изделий и их последующем охлаждении из-за плохой теплопроводности стекла в разных частях изделия возникает разность температур. В результате поверхностные и внутренние слои остывают неравномерно и в них появляются напряжения сжатия и растяжения. Когда изделие полностью остывает, т. е. температуры по всему объему изделия выравниваются, напряжения, возникшие в момент охлаждения, либо исчезают, либо остаются. Исчезающие напряжения называют временными, а те, которые остаются — остаточными. Наличие в изделии из стекла временных или остаточных напряжений, особенно неравномерно распределенных по объему, отрицательно сказывается на его механической прочности. Поэтому для снятия напряжений применяют дополнительную тепловую обработку — отжиг, который является необходимой стадией технологического процесса изготовления стеклоизделий.
Условия изготовления художественных изделий из стекла особенно способствуют возникновению напряжений. Такие изделия часто изготовляют толстостенными и чем толще стенка, тем значительнее в ней напряжения. Многие художественные изделия имеют сложную конфигурацию при неравномерно распределенной стекломассе по объему изделия, с резким переходом от тонких частей к утолщениям. Как правило, художественные изделия в процессе изготовления подвергают либо механическому воздействию, либо частичному повторному нагреванию, в связи с чем по высоте изделия возникают зоны перепадов температур. На тонких стенках изделий часто устанавливают массивные элементы (например, ручки), имеющие в момент соединения более высокую температуру. Поэтому в местах крепления приставных деталей возникают местные напряжения. Разрушение таких изделий, как правило, начинается с появления трещин в местах концентрации этих напряжений. Образованию местных напряжений стекла способствует также применение непрогретых металлических инструментов. Иногда напряжения возникают в изделиях из многослойных (накладных) стекол в .связи с разницей термических коэффициентов линейного расширения соединяемых стекол, а также неравномерностью остывания слоев.
Режим отжига зависит от химического состава стекла, назначения, размеров и формы изделия, условий формования, допустимости остаточных напряжений. Для большинства стекол, из которых производят художественные изделия из стекла, максимальная температура отжига 500…520 °С.
Успех механической обработки стекла зависит от того, насколько качественно отожжено изделие. Наличие остаточных внутренних напряжений в стекле может привести к его растрескиванию в процессе обработки.
Закалка — способ обработки изделий, в результате которой в поверхностных слоях стеклянных изделий с целью повышения механической и термической прочности создают равномерно распределенные напряжения. В результате прочность закаленного стекла повышается в 4…6 раз по сравнению с прочностью отожженого стекла. Закаленное стекло нельзя подвергать механической обработке. Закалка является конечной стадией технологического процесса.
Термическое полирование — способ тепловой обработки, при котором нагретое изделие из стекла подвергается действию острого высокотемпературного пламени. При этом очень тонкий поверхностный слой стекла расплавляется и все микронеровности, мельчайшие трещинки, образующиеся при формовании, под действием поверхностного натяжения, сглаживаются. Термическое полирование способствует также повышению механической прочности и химической стойкости изделий. Для расплавления стекла в поверхностных слоях при термическом полировании применяют высокотемпературное пламя, плазменные источники, источники инфракрасного и лазерного излучения.
Нанесение поверхностных покрытий — способ декоративной обработки, при котором на поверхности изделий создают тонкие слои металлов или их оксидов разнообразного химического состава, внешнего вида и свойств. Например, при обработке изделий непосредственно после формования растворами солей различных металлов на стекле получают цветные оксидометалличе-ские покрытия. При соприкосновении с горячей поверхностью раствор соли разлагается под действием высоких температур и образуются тонкие пленки металлов, оксидов металлов или смеси металлов с оксидами. За счет этого поверхность изделия окрашивается в разные цвета.
К разновидностям этого способа обработки относятся лризация и украшение изделий пленками драгоценных металлиризация (от греческого ирис — радуга) — это способ обработки подогретого стекла парами солей некоторых металлов, которые образуют на поверхности стекла тонкую радужную пленку. При ирризации чаще всего применяют легковозгоняющие-ся соли металлов. Эти соли обладают способностью превращаться в пар без плавления и, наоборот, переходить из газообразного состояния сразу в твердое. Эффект ирризации обусловлен тем, что лучи света с волнами различной длины, отраженные от обеих поверхностей пленки, складываются. При этом одни цветовые волны усиливаются, а другие ослабляются. В зависимости от этого в суммарном отраженном луче преобладает некоторый цветовой оттенок.
Украшение пленками драгоценных металлов выполняют, нанося на стекло пасты и краски, которые разлагаются при повышенных температурах. Таким способом наносят слои золота, серебра, платины.
Для декорирования художественных изделий используют силикатные и люстровые краски.
Силикатные краски представляют собой тонкомолотые легкоплавкие цветные стекла. Во время обжига (при температурах 500…550 °С) изделия, расписанного силикатными красками, краски приплавляются к поверхности стекла, образуя прозрачные или непрозрачные цветные покрытия. Поэтому различают прозрачные и непрозрачные силикатные краски (эмали). Полупрозрачные краски занимают промежуточное положение.
Люстровые краски (люстры) представляют собой растворы смолянокислых солей тяжелых металлов в органических растворителях. После нанесения таких красок на стекло и последующего обжига на поверхности изделий образуется тончайшая окрашенная пленка оксидов металлов. Эта пленка отливает в отраженном свете металлическим блеском. Цвет пленки и оттенок металлического блеска зависят от металла, на основе которого приготовлен люстр.
Метод поверхностного окрашивания листового стекла путем электрохимического осаждения металлов основан на регулируемом ионном обмене, который состоит в следующем. Если к находящимся в соприкосновении листовому стеклу и расплаву металла приложить разность электрических потенциалов от источника постоянного тока, то ионы металла-красителя диффундируют (проникают) в поверхностные слои стекла, вызывая окраску. Таким способом можно окрашивать стекло в серовато-бронзовые и медно-бронзовые тона разной интенсивности.
Устройство для окрашивания стекла этим методом состоит из медного электрода, под которым находится расплав окрашивающей лигатуры (приготовляется путем взаимного плавления олова или свинца с металлом-красителем — медью, кобальтом, никелем — в соответствующих пропорциях). Металл-краситель диффундирует направленно в поверхностные слои ленты стекла, которая находится в пластичном состоянии на поверхности расплава олова, имеющего температуру 600…800 °С. Для того чтобы концентрация меди в лигатуре не снижалась, медь непрерывно подводят в расплав и растворяют в нем. Сплав меди со свинцом окрашивает стекло в бронзовый цвет, меди и олова — в розоватый, серебра и олова — в желтый, кобальта и олова — в серовато-синий.
Реклама:
Читать далее:
Абразивные материалы в обработке стекла
Статьи по теме:
Как отполировать стекло на часах и что делать, если треснуло стекло на часах: народные приметы
Любая вещь со временем изнашивается и приходит в негодность. Такая же ситуация обстоит и с наручными часами. Даже если их носить аккуратно, то всё равно не получится избежать мелких царапин на стекле и потертостей на корпусе. Причем такие дефекты не только портят эстетику, но и затрудняют видимость циферблата. Если царапины неглубокие и нет сколов, то отполировать стекло на часах можно даже самому, не обращаясь при этом к часовщику. Если же, допустим, ребенок серьезно поцарапал стекло часов по причине своей невнимательности, то такой дефект сможет исправить только мастер, возможно, с полной заменой испорченной детали.
Как убрать царапины на стекле на часах
Чтобы понять, какой способ полировки подойдет, нужно выяснить, из какого материала выполнено стекло. Существует несколько стекол, используемых для часов:
- органическое;
- сапфировое;
- минеральное;
- пластиковое.
При органическом типе шлифовка стекла часов может быть выполнена несколькими способами. Самый простой и действенный — с помощью белой негранулированной зубной пасты без отбеливающих свойств:
- протрите стекло от остатков пыли и загрязнений;
- выдавите мелкую горошину зубной пасты на ватный диск;
- поместите часы на ровную поверхность, и, почти не надавливая, круговыми движениями втирайте пасту в стекло;
- буквально через минуту работы возьмите чистый тампон, смочите водой и смойте остатки пасты.
Следите, чтобы вода не проникла в корпус часов. Если сомневаетесь в водонепроницаемости устройства, то имеет смысл разобрать часы и проделать процедуру полировки стекла отдельно. Можно повторить её около четырех раз — до полного удаления мелких царапин.
Паста ГОИ для полировки часовЕсли же имеются более основательные дефекты, то подойдет второй способ, при котором используется паста ГОИ (существует четыре типа зернистости):
- нанесите пасту под номером четыре (крупнозернистая) на влажный ватный диск;
- полируйте круговыми движениями около двух минут;
- смойте влажным диском остатки пасты и протрите насухо;
- если царапины стали менее заметны, то стоит повторить процедуру, но с пастой ГОИ номер три;
- для удаления мелких дефектов подойдет мелкозернистая паста под номером два или один, либо зубная паста, описанная в первом способе шлифования.
Главное условие — не торопитесь и будьте аккуратны.
Если сомневаетесь в своем успехе, то имеет смысл обратиться за помощью к профессионалу.
Полировка сапфирового стекла часов от царапин
Такой вид стекла требует большей осторожности, ведь оно очень твердое и одновременно хрупкое, то есть не терпит точечных ударов и падений. Поэтому самостоятельная полировка сапфирового стекла часов от царапин в домашних условиях не рекомендуется. Если же вы все-таки решили выполнить данную процедуру, то замените пасту ГОИ на алмазную. В остальном принцип шлифовки такой же, что и при органическом стекле.
Шлифовка наручных часовУчтите, что сапфировое стекло самое дорогое среди других типов, поэтому придется раскошелиться, если самостоятельный ремонт не удастся.
Как отшлифовать минеральное стекло на часах своими руками
Удаление царапин со стекла часов потребует наличия шлифовального круга, пасты ГОИ, спирта и ватных дисков. Минеральное стекло очень твердое и не боится механических нагрузок, поэтому обрабатываться должно хоть и аккуратно, но более жестко по сравнению с другими типами:
- нанесите пасту на рабочую поверхность шлифовального круга;
- отполировать минеральное стекло нужно до полной его прозрачности, при шлифовке перемещайте часы от края к центру и назад, распределяйте нагрузку равномерно;
- смочите ватный диск в спирте и зачистите стекло до появления блеска.
Можно ли избавиться от царапин на пластиковом стекле
Это довольно прочный и износостойкий материал. Царапины с такого стекла не так сложно удалить. Достаточно использовать при этом зубную пасту или пасту ГОИ мелкой зернистости. Сначала нужно нанести абразив на ватный диск, а затем заполировать царапину до полного ее исчезновения.
Что делать, если запотевает стекло в часах
В свойствах воздуха в любом случае присутствует влажность, а часы собираются не в вакууме, поэтому запотевшее стекло не такое уж и редкое явление, особенно при резком перепаде температур. Браком это назвать нельзя, но если потеет стекло на часах, значит дефект в каком-то роде присутствует.
Есть шанс обратиться в сервисный центр, если гарантия на изделие еще не истекла, в обратном же случае — можно проделать кое-какие действия для устранения неполадки самостоятельно:
- снимите заднюю крышку часов;
- поместите часы вблизи источника тепла на некоторое время (до двух дней), если нет возможности ждать — воспользуйтесь феном;
- накройте салфеткой на время просушки во избежание попадания пыли внутрь изделия;
- не открывайте окна, не используйте увлажнители — нужно постараться минимизировать влажность в помещении;
- поставьте аккуратно крышку на место, не нарушая конструкции изделия (если имеются какие-либо резиночки или прокладки — их нужно установить туда, где они были).
Следует понимать, что наличие влаги под корпусом часов чревато порчей деталей и механизма часов. Если запотевание происходит редко, например, только при выходе на улицу в мороз, то не стоит переживать и устраивать разборку изделия. Причиной для беспокойства можно расценивать испарину, которая появляется при комнатной температуре.
Учтите, что можно только ухудшить ситуацию: занести пыль под корпус устройства, порвать прокладку или усилить запотевание. Поэтому, если сомневаетесь в своем успехе, то лучше довериться профессионалам.
Разбилось или треснуло стекло на часах: народные приметы
Приметы издавна были объяснением непонятных событий в жизни каждого народа. Человек видел в них свою судьбу, предназначение, искал скрытый смысл. В наши дни вера в приметы не теряет своей актуальности. Люди продолжают ими руководствоваться в планировании дел, оценивая влияние примет на будущее.
Треснутое стеклоЧасы непосредственно связаны со временем, течением жизни. Многие эзотерики считают, что ходики способны впитывать энергию своего носителя, из-за этого не рекомендуется дарить часы малознакомым людям или поднимать их на улице, поэтому примета о разбитом стекле на часах обладает такой важностью для большинства.
Треснутое стекло в разные времена предвещало разные невзгоды:
- скорое возможное недомогание владельца, причем, чем больше трещина, тем более продолжительной и сильной будет болезнь;
- крах и неудача в бизнесе или личной жизни — намек о пустой трате времени;
- разбить стекло на часах во время снятия с руки — предупреждение об опасности для родных, возможной утрате близкого человека.
Носить часы с разбитым стеклом категорически не рекомендуется — это не сулит ничего хорошего.
С поломанными ходиками следует поступить следующим образом:
- если есть возможность их починить, то не стоит затягивать с ремонтом — отнесите мастеру;
- если ремонт невозможен, то важно как можно быстрее избавиться от испорченного изделия — оберните в фиолетовую ткань (считается, что такой цвет поглощает всю негативную энергию) и вынесите часы туда, где их никто не найдет;
- если вещь очень дорога, то, обернув их в ткань, можно спрятать в коробочку или шкатулку дома.
Нередко человек связывает свои неудачи с приметами, поэтому старайтесь настраивать себя на те суеверия, которые предрекают удачу или счастливые события.
Приметы о разбитом стекле на часах не сулят ничего хорошего…Помните, что каждый сам выбирает, во что ему верить!
Автор статьи: Александр Москалец
Полировка стекол в Челябинске | RDS detailing
ПРИМЕРЫ НАШИХ РАБОТ
За время эксплуатации автомобиль, как человек, «теряет зрение». Стекла, особенно лобовое, испытывают постоянные ударные нагрузки от камней, частиц пыли. Помутнение, царапины ухудшают прозрачность, видимость, особенно ночью, при дожде, снегопаде. Появляется необходимость замены или полировки автостекол.
Работа щеток стеклоочистителей приводит к появлению потертостей на стеклянной поверхности. Процесс усугубляется при попадании под резинки дворников частиц пыли, дорожных реагентов, других химических, активных веществ. Летящие из-под колес движущихся транспортных средств предметы наносят повреждения автостеклу.
Движение на автомобиле становится затруднительным. Причина – потеря прозрачности, ухудшение обзора ситуации на дороге. Возможно ухудшение зрения у автовладельца. Водитель должен сделать выбор: произвести замену или отполировать лобовое автостекло.
Зачем нужна шлифовка и полировка стекла автомобиля
При интенсивной эксплуатации автомобиля лобовое стекло теряет за год 5% – 7% прозрачности. Микротрещины, сколы, помутнение если вовремя не устранить, приводят к потере обзора на дороге, возможному ДТП. Автостекло требует восстановления. Появляющиеся сколы устраняются шлифованием. Царапины удаляются полированием.
Отполировать автостёкла или заменить – цена
При повреждении лобового стекла вопрос о замене или восстановлении чаще решается в пользу последнего. Новое стоит дорого. На брендовых, престижных автомобилях стоимость автостекла сопоставима с ценой двигателя или коробки передач. Отполировать поверхность стоит в разы меньше. Затраты времени не велики. Операция занимает от 2 до 5 часов. При этом стекла после восстановления выглядят как новые.
Где в Челябинске сделают полировку стекла – защиту стекла от царапин
В студии RDS detailing проведут анализ состояния стекла вашего автомобиля. По результатам проверки предложат комплекс мер по шлифованию, полировке и дальнейшей защите стеклянной поверхности. Мы сделаем все, чтобы поездка на машине для вас была безопасной и комфортной.
Как мы отполируем автостекла
Проведение анализа дефектов стекла позволяет разделить их по размерам:
1. До 150 – 200 мкм. Незначительные повреждения, помутнение, поверхности. Устраняются полировочными войлочными или легкими абразивными кругами с применением абразивной пасты.
2. 200 – 350 мкм. Потертости, мелке сколы. Устраняется полированием абразивными кругами, или войлочными с применением пасты со средней зернистостью.
3. Свыше 350 мкм. Глубокие царапины, сколы, микротрещины. Устраняются шлифовкой абразивными кругами с дальнейшей обработкой мелкозернистыми полировочными пастами.
Преимущества полировки стеклянных поверхностей
Удается вернуть автостеклу прозрачность, восстановить оптические свойства. При сравнении с операцией замены автовладелец получает ряд бонусов:
• Восстановление полированием дешевле замены автостекла;
• Качество восстановленного максимально приближено к новому;
• Операция занимает малый период времени.
Покупайте у нас услугу «полировка автостекла» это выгодно
Потому, что вы становитесь нашими партнерами. Вы становитесь нашими друзьями. Мы рады друзьям!
Отполировав стекло автомобиля в нашем салоне, вам захочется вернуться. Мы окажем любую услугу по обслуживанию вашего любимого авто. Ознакомиться с перечнем и ценами можно на сайте.
Салон RDS Detailing ценит своих друзей, их фантазии. И дарит скидки, бонусы, подарки.
Мы ждем вас!
RDS Detailing предоставляет широкий спектр услуг:
Примеры работ можете посмотреть в портфолио.
Мы готовы ответить на все ваши вопросы. Звоните!
Полировка стекол авто своими руками
Нет ничего вечного, поэтому и кузов автомобиля постепенно царапается, на нем образуются потертости и другие визуальные дефекты. Особенно трудно избавиться от повреждений на поверхности лобового стекла, но существует специальная полировка стекол авто, при помощи которой можно придать машине первозданный вид.
Для чего полируют стекла?
Процесс полировки
Полировка стекла автомобиля от царапин помогает избавиться от потертостей и царапин, которые могут возникать под воздействием щеток стеклоочистителей. Дворники повреждают его из-за изношенности, а также в случае загрязнения льдом и песком. Абразивные частицы, попадающие между резинками и стеклом, царапают гладкую поверхность. Нередко микроцарапины образуются по вине самих автомобилистов, когда они трут поверхность грязной сухой тряпкой или пытаются отодрать ледяную корку скребками.
Поцарапанное стекло делает небезопасным эксплуатацию машины в темное время суток, так как на царапинах свет от встречных фар преломляется и вызывает блики с засветами. При этом пятна потертостей существенно ухудшают обзор, из-за чего встречные транспортные средства сильно слепят своими фарами, а глаза автомобилиста сильно устают, и он утомляется. Именно в таких случаях автовладельцы задаются вопросом – как производится полировка стекла от царапин своими руками?
Разумеется, всегда можно купить новое стекло и заменить его, но это не очень дешево, поэтому лучше начать с полировки. При качественном выполнении работ стеклу вернется первозданный блеск и прозрачность. Кроме того, при замене могут образоваться протечки из-за плохо проложенных уплотнителей. Кроме того, качество продаваемых автомагазинами стекол не всегда высокое.
к содержанию ↑Полировка и шлифовка
Существует не только полировка лобового стекла, но и его шлифовка. Полировку применяют для устранения мелких повреждений с помощью специальных паст и несильной обработки. Шлифование применяют в случае более глубоких повреждений, а для обработки используются особые абразивные материалы с алмазной пылью и наждачная бумага. Этот вариант возможен для обработки не каждого стекла, так как он снимает толстый верхний слой. Шлифование обычно применяют для обработки стекол фар, так как они более толстые.
С полировкой каждый автомобилист может самостоятельно справиться, так как снимается лишь поверхностный слой. На первый взгляд, задача непростая, но если приложить определенные усилия и потратить немного времени, все получится.
к содержанию ↑Что потребуется?
полировальный круг из фетра
Полировка стекла автомобиля от царапин требует применения специальных принадлежностей и инструментов, среди которых:
- шлифмашинка или дрель со специальной войлочной насадкой;
- полировальный круг из фетра;
- полировальный порошок для стекол;
- салфетки;
- малярный скотч;
- цветной маркер;
- жидкость для чистки стекол;
- полиэтиленовая пленка для защиты окружающих деталей;
- пульверизатор для жидкости.
Выбирая электрический инструмент для полировки стекол фар, необходимо учитывать, что полировать стекла нужно с оборотами не более 1700-1800 в минуту. В противном случае, стекло может перегреться, треснуть или деформироваться.
к содержанию ↑Поиск и выявление повреждений
Поцарапанное стекло
Полировка лобового стекла своими руками позволяет убрать лишь мелкие повреждения, среди которых неглубокие бороздки от дворников. Проверить это нетрудно: если ноготь ни за что не цепляется, когда вы проводите им по стеклу, дефект можно исправить самостоятельно.
Вообще при определенных усилиях можно убрать и более глубокие дефекты, но увеличится риск образования эффекта волны или линзы, что для лобовых стекол очень небезопасно. Вообще сразу при обнаружении того, что дворники начали оставлять следы на поверхности стекла, щетки нужно поскорее заменить, чтобы избежать ремонта.
Сколы от камней заполировать невозможно – их можно лишь отремонтировать в сервисном центре или самостоятельно, изучив нашу подробную инструкцию. Существенные температурные перепады вызывают образование трещин, которые расходятся от мелких сколов.
к содержанию ↑Подготовительные работы
Начинается полировка стекол от царапин с подготовительных работ. Прежде всего, важно тщательно вымыть машину и уделить отдельное внимание чистоте рабочего места. Инструменты, в особенности салфетки и фетровый круг должны быть идеально чистыми, так как даже незначительная пыль или немного песка могут оставить новые царапины.
Все выявленные на стекле повреждения необходимо обвести маркером с внутренней стороны, так как при начале работ полироль скроет дефектные места и вы их уже не увидите. Далее необходимо укрыть детали машины пленкой во избежание из загрязнения летящими брызгами полироли.
Далее в полиэтилене необходимо вырезать окошки в местах, которые нужно обработать, а края отреза зафиксировать малярным скотчем. Подлежащие полировке области хорошенько моем жидкостью для стекол – это очень важно.
разведите полировальный порошок, купленный заранее в магазине, обычной водой по инструкции. Вы должна получить смесь кремообразной консистенции. Налейте чистую воду в пульверизатор и вставьте фетровый круг в патрон дрели или шлифовальной машинки.
Полировальные работы
Набор для полировки
Все готово к началу полировки лобового стекла, поэтому можете приступать. Сначала нанесите немного пасты на круг и разотрите ее по поврежденному участку. Не следует за раз обрабатывать область более 30х30 см. Далее включите шлифмашинку и легкими движениями начните водить по обрабатываемой поверхности.
На долгое время не задерживайтесь на определенном участке, чтобы не образовались выемки, меняющие оптические свойства стекла. Дрель или шлифовальную машинку держите так, чтобы круг из фетра отстоял приблизительно на пять градусов от поверхности. Не давите слишком сильно – процесс должен идти мягко и аккуратно. Постоянно контролируйте, чтобы поверхность обрабатываемого участка не пересыхала, а для этого нужно пульверизатором опрыскивать ее водой.
После полировки выбранной области приступайте к обработки другого участка, повторяя все процедуры. Во избежание пропуска мест новую область обрабатывайте с небольшим нахлестом в 5-7 см. после завершения работ протрите стекло бумажной салфеткой и посмотрите на него изнутри – не должно остаться ни царапин, ни матовых пятен. При их обнаружении повторите обработку.
Если стекло слишком старое, можете полностью его отполировать. Со сравнительно новым стеклом можете обработать лишь области, по которым ездят дворники.
Полировка всего стекла
После полировки лобового стекла своими руками нужно удалить укрывную пленку и отмыть стекло. Процесс полировки занимает минимум несколько часов, то есть занятие не очень быстро и требует определенного терпения.
Полировка стекла автомобиля от царапин и потертостей – это очень ответственная работа, так как требования к оптическим свойствами прозрачности особенно высоки. Задние и боковые стекла обрабатывают так же, как лобовое, но здесь можно прилагать больше усилий, так как оптические свойства не столь важны.
Тщательно отполированное стекло автомобиля по характеристикам лишь слегка уступает новому. При качественном проведении работ оно по оптическим и светопропускающим свойствам будет на 80% соответствовать новому. Сильные и средние дефекты удалить таким образом вы не сможете или они будут устранены частично. В любом случае полировка является единственным экономичным способом продления срока службы авто.
Видео:
Видео:
Видео:
Видео:
Шлифовка, полировка и резка изделий из стекла
Шлифовка, полировка и резка изделий из стекла, как правило, выполняются в коммерческих целях в качестве конечных процессов на заводах по производству стекла. После плавления стекла в специальных печах выполняются необходимые операции формовки для получения стеклянной посуды необходимой формы. После этого выполняются операции термообработки для получения требуемых механических свойств.
Последними процессами, применяемыми к стеклянным изделиям, являются операции шлифовки, полировки и резки.Здесь мы объясняем эти процессы, которые применяются к изделиям из стекла.
Шлифование стекла.Отделочные операции, применяемые к изделиям из стекла
Часть стеклянной посуды производится с помощью операций выдувания и прессования, при которых образуются следы швов за счет использования штампов разъемного типа. Эти следы швов можно компенсировать полировкой после термообработки.
Чистка произведенных стеклянных изделий.Волочение и прокатка расплавленных стеклянных изделий также являются очень важными приложениями для получения стеклянной тары.Из-за инструментов и оборудования для прокатки и волочения поверхности стекол могут иметь царапины и другие дефекты, которые нежелательны с коммерческой точки зрения. Таким образом, некоторые операции полировки и шлифования могут быть применены для устранения этих дефектов после процессов термообработки.
Выпускается декоративная и нарядная стеклянная посуда. На этапе производства этих типов стекол могут применяться некоторые операции полировки, шлифования, травления и нанесения покрытия.
Полировка посуды.Операции по резке изделий из стекла обычно связаны с производством длинных трубок и других изделий из плоского стекла. Эти виды продукции производятся непрерывно. Таким образом, резка такой производимой посуды должна производиться на стандартные размеры в заводских условиях. Как и другие операции отделки изделий из стекла, операции резки выполняются после операций термообработки.
Заключение по отделке стеклянной посуды
Как вы понимаете, отделочные операции, применяемые к изделиям из стекла, аналогичны операциям обработки металлов.
Если у вас есть дополнительная информация об операциях отделки стеклянной посуды, она может быть очень полезной для людей, которые ищут информацию об этом.
Не забывайте оставлять ниже свои комментарии и вопросы по поводу операций по отделке изделий из стекла.
Ваши ценные отзывы очень важны для нас.
Шлифовка стекла | Машины | Магазин
С начала 1990-х годов Bohle занимается разработкой и производством оборудования для обработки стекла — сначала в своем филиале в Торгау, а с 2009 года в штаб-квартире Haan.Обширный портфель оборудования постоянно расширяется — как за счет других станков собственного производства Bohle, так и за счет продуктов от избранных поставщиков, которые были разработаны и / или модифицированы в соответствии с нашими требованиями. В настоящее время из-за небольшого вертикального диапазона производства больше не актуально, производится ли каждая отдельная часть продукта собственными силами: все сводится к качеству, обслуживанию клиентов, техническим советам и соотношению цены и качества — все эти факторы являются приоритетами компании Bohle.Независимо от того, какой станок для обработки стекла вы выберете, вы всегда можете рассчитывать на его отличную производительность, потому что машины Bohle разрабатываются и производятся профессионалами в области стекла для профессионалов в области стекла.
С начала 1990-х годов Bohle занимается разработкой и производством оборудования для обработки стекла — сначала в своем филиале в Торгау, а с 2009 года в штаб-квартире Haan. Комплексный … Подробнее » Закрыть окноШлифовка стекла
С начала 1990-х годов Bohle занимается разработкой и производством оборудования для обработки стекла — сначала в своем филиале в Торгау, а с 2009 года в штаб-квартире Haan.Обширный портфель оборудования постоянно расширяется — как за счет других станков собственного производства Bohle, так и за счет продуктов от избранных поставщиков, которые были разработаны и / или модифицированы в соответствии с нашими требованиями. В настоящее время из-за небольшого вертикального диапазона производства больше не актуально, производится ли каждая отдельная часть продукта собственными силами: все сводится к качеству, обслуживанию клиентов, техническим советам и соотношению цены и качества — все эти факторы являются приоритетами компании Bohle.Независимо от того, какой станок для обработки стекла вы выберете, вы всегда можете рассчитывать на его отличную производительность, потому что машины Bohle разрабатываются и производятся профессионалами в области стекла для профессионалов в области стекла.
Эффективное и точное шлифование сапфирового стекла на основе шлифовального круга грубого алмазного шлифования, подвергнутого сухому электрическому разряду.
Аннотация
Импульсный электрический разряд был предложен для эффективной и точной шлифовальной обработки сапфирового стекла.Технология правки с помощью сухого электрического разряда использовалась для получения большого выступа зерна и острых режущих кромок с микрозернистостью. Было исследовано влияние параметров процесса шлифования, таких как скорость круга, глубина резания и скорость подачи, на качество шлифованной поверхности, усилие шлифования и соотношение сил шлифования на сапфировом стекле, а также выявлена взаимосвязь между усилием шлифования и качеством шлифованной поверхности. Результаты экспериментов показывают, что высота выступа зерна на поверхности грубого алмазного шлифовального круга, обработанного сухим электрическим разрядом, может достигать 168.5 мкм. Минимальная шероховатость линии R a и шероховатость поверхности S a шлифованной поверхности сапфирового стекла составляла 0,194 мкм и 0,736 мкм, соответственно. Для достижения высокого качества шлифовки сапфирового стекла глубина резания контролировалась в пределах 7 мкм, а скорость вращения круга и скорость подачи составляли 3000–5000 об / мин и 10–20 мм / мин соответственно. Влияние скорости подачи и скорости круга на коэффициент шлифовального усилия было более значительным, но влияние глубины резания было незначительным.
Ключевые слова: шлифование , сапфировое стекло, крупнозернистый алмазный шлифовальный круг, сила шлифования, шероховатость поверхности
1. Введение
Сапфировое стекло обладает превосходными физическими, химическими и механическими свойствами, такими как термостойкость, износостойкость, коррозионная стойкость, высокая твердость, хорошее светопропускание и стабильные свойства. Поэтому он широко используется в оптической электронике, авиакосмической промышленности, освещении дисплеев и других областях [1,2,3]. Сапфировое стекло — типичный твердый и хрупкий материал.Хотя гладкую поверхность можно получить с помощью методов шлифовки и полировки [4,5,6], очень трудно обеспечить общий размер и точность формы заготовки из-за длительного времени полировки.
Шлифование мелкозернистыми алмазными кругами позволяет получить высокое качество поверхности и точность формы [7,8,9]. Например, качество шлифованной поверхности сапфирового стекла сравнивалось с использованием алмазных шлифовальных кругов на керамической связке с различными размерами алмазных зерен 35 и 64 мкм при одинаковом давлении шлифования 20.5 кПа и частота вращения ± 120 об / мин [7]. Эллиптическое ультразвуковое шлифование на основе алмазного шлифовального круга № 800 на связке из смолы было разработано для шлифования сапфирового стекла с целью получения лучшего качества шлифованной поверхности [8]. Результаты экспериментов показали, что область стабильного шлифования может быть увеличена примерно на 20% по сравнению с традиционным шлифованием. Алмазный шлифовальный стержень №500 с гальваническим покрытием использовался для проведения экспериментов по шлифованию микроканавок на поверхности сапфирового стекла с целью исследования механизмов образования микротрещин в различных кристаллических плоскостях [9].
Однако мелкозернистый алмазный шлифовальный круг требовал частой правки и правки [10,11] из-за его быстрого износа, что приводило к низкой эффективности шлифования. Пассивированные зерна вызовут больше дефектов на шлифованной поверхности, а быстрый износ шлифовального круга также легко повлияет на общую точность формы заготовки [12]. Таким образом, алмазный шлифовальный круг на металлической связке с хорошей износостойкостью был предложен для реализации высокой эффективности и точности шлифования сапфирового стекла благодаря его большой высоте выступа зерна и острым режущим кромкам с микрозернистыми зернами в этой бумаге.
Правка алмазного шлифовального круга с использованием традиционного метода механической правки и правки является очень сложной задачей [13]. Кроме того, эффективность правки и правки была крайне низкой. Хотя метод лазерной правки может заставить алмазные зерна быстро выступать из металлической связующей поверхности шлифовального круга [14], высокоэнергетический луч также будет удалять алмазные зерна, что не способствует шлифованию. Предыдущие исследования показали, что высокоэффективная правка мелкозернистого алмазного шлифовального круга может быть достигнута с помощью импульсного электрического разряда и оперативных методов электролитической правки [15,16].Тем не менее, было мало исследований по правке разгрузки грубого алмазного шлифовального круга. Поэтому в этой статье метод правки с импульсным разрядом с простым процессом и защитой окружающей среды был разработан для быстрой правки крупных алмазных зерен на поверхности шлифовального круга для обеспечения эффективного и точного шлифования сапфирового стекла.
В данной работе сапфировое стекло шлифовалось грубым алмазным шлифовальным кругом, обработанным методом сухого электрического разряда.Выявлена связь между усилием шлифования и шероховатостью шлифованной поверхности сапфирового стекла. Влияние параметров процесса шлифования, включая скорость круга, глубину резания и скорость подачи, на качество шлифованной поверхности, усилие шлифования и соотношение шлифовальных усилий сапфирового стекла было исследовано для оптимизации условий процесса шлифования.
2. Эксперименты и методы
2.1. Правка грубого алмазного шлифовального круга с помощью электрического разряда
Целью правки алмазного шлифовального круга является обеспечение того, чтобы алмазное зерно с поверхности круга выступало за пределы связки, образуя новую острую режущую кромку с микрозернистостью.Предварительно разработанная технология правки и правки с помощью сухого электроконтактного разряда [17], мощный высокочастотный импульсный источник питания ELID (Electrolytic In-Process Dressing) для зеркального шлифования (HDMD, Харбин, Китай), разработанный Харбинским институтом Технология и правочный электрод, смешанный с чугуном и медным порошком (Fe + C + Cu), были использованы для правки алмазного круга № 46 диаметром 150 мм и толщиной 2,5 мм, чтобы получить большую высоту выступа зерна на поверхности. алмазного круга.Эксперименты по разгрузке алмазного шлифовального круга проводились на прецизионном трехосевом шлифовальном станке с ЧПУ (компьютерное числовое программное управление) (SMART-B818III, CHEVALIER, Тайвань). Принципиальная схема электроразрядной перевязки показана на а, а фотография разрядной перевязки — на б. Положительный полюс импульсного источника питания был подключен к алмазному шлифовальному кругу через графитовую щетку, а отрицательный полюс — к смешанному электроду. После того, как шлифовальный круг разрезал смешанный электрод, между образовавшейся стружкой и металлической связкой поверхности круга возник электрический искровой разряд.На поверхности металлической связки образовывались многочисленные разрядные кратеры для правки колеса. Принцип разгрузочной повязки показан на c. Напряжение холостого хода импульсного разряда составляло 60–120 В, а ток составлял 6,7–20,1 А. После правки алмазного шлифовального круга многие алмазные зерна выступали за пределы поверхности металлической связки, образуя острые режущие кромки с микрозернистыми зернами. Из-за большого размера зерна алмазные зерна не могли легко затупиться и отвалиться. Кроме того, алмазный шлифовальный круг для грубого шлифования не нуждался в частой правке и правке, что обеспечивает непрерывную обработку в течение длительного времени.Следовательно, он обладал высокой эффективностью шлифования и длительным сроком службы и, следовательно, был более экономичным по сравнению с мелкозернистым алмазным шлифовальным кругом. После правки поверхности колеса можно было получить выступы зерна с большой высотой, что было полезно для улучшения качества шлифованной поверхности. Таким образом, алмазный шлифовальный круг для грубого шлифования может использоваться для эффективного шлифования заготовок.
Устройство и принцип сухой электроразрядной правки алмазного шлифовального круга: ( а ) принципиальная схема; ( b ) фото повязки и ( c ) принцип повязки.
2.2. Эксперименты по осевому шлифованию сапфирового стекла
После правки алмазного шлифовального круга были проведены эксперименты по шлифованию сапфирового стекла с осевой подачей на трехкоординатном шлифовальном станке (SMART-B818III, CHEVALIER, Тайвань). В экспериментах по шлифованию в качестве заготовки было выбрано синтетическое сапфировое стекло, и в его состав в основном входил оксид алюминия (Al 2 O 3 ). Сапфировое стекло сначала было прикреплено к пластине из полиметилметакрилата (ПММА), а затем пластина была закреплена на динамометре с помощью приспособления.Правильный алмазный шлифовальный круг совершал поступательное осевое возвратно-поступательное движение по поверхности сапфирового стекла. Принципиальная схема шлифования осей показана на a, а фотография шлифования показана на b. Размер заготовки составлял 30 мм × 15 мм × 0,5 мм. Физические свойства показаны в. Площадь шлифования составляла 20 мм × 6 мм.
Принципиальная схема и фото осевого шлифования сапфирового стекла: ( a ) принципиальная схема и ( b ) фотография шлифования.
Таблица 1
Физические свойства сапфирового стекла [18,19].
Физические характеристики | Сапфировое стекло |
---|---|
Плотность, ρ (г / см 3 ) | 3,98 |
Шкала твердости по шкале Мооса 43 | 2|
Коэффициент Пуассона, μ | 0,25–0,3 |
Модуль упругости, G (ГПа) | 145 |
Модуль упругости, E (ГПа) 43101 9011 901 901 | |
2.5 |
Чтобы изучить влияние различных параметров процесса шлифования на силу шлифования поверхности сапфирового стекла, в процессе шлифования было испытано трехстороннее усилие шлифования сапфирового стекла, а именно нормальное усилие шлифования F. Y перпендикулярно шлифовальной поверхности и заготовке, тангенциальное усилие шлифования F X вдоль тангенциального направления скорости круга и осевое усилие шлифования F Z параллельно направлению подачи заготовки (см. а).Принципиальная схема и фото шлифовки сапфирового стекла с осевой подачей представлены на рис. Динамометр и датчик Кистлера использовались для хранения сигнала силы шлифования в компьютере через систему сбора данных TNS-DES07. Время сбора данных составляло 60–90 с, включая весь процесс измельчения. Среднее значение сигнала шлифовального усилия во время процесса шлифования рассматривалось как значение шлифовального усилия F для каждого условия процесса шлифования.
Чтобы изучить влияние параметров процесса шлифования, таких как глубина резания a , скорость подачи v f и скорость круга N на качество шлифованной поверхности, были выбраны три различных параметра процесса шлифования и четыре переменные были установлены для каждого параметра процесса в этой статье.Основываясь на предыдущих экспериментальных результатах, при глубине пропила a = 1 мкм, скорости подачи v f = 10 мм / мин и скорости вращения колеса N = 3000 об / мин, качество шлифованной поверхности сапфирового стекла был самым высоким. Таким образом, всего было экспериментально разработано 10 групп различных условий процесса шлифования, а суммарная глубина резания при каждом наборе параметров шлифования составляла 30 мкм. Списки экспериментальных параметров показаны в.
Таблица 2
Параметры процесса прецизионного шлифования сапфирового стекла.
Клемма № | Глубина резания a (мкм) | Скорость подачи v f (мм / мин) | Скорость вращения колеса N (об / мин) |
---|---|---|---|
1 | 1 | 10 | 3000 |
2 | 3 | 10 | 3000 |
3 | 5 | 10 | 3000 |
5 | 1 | 15 | 3000 |
6 | 1 | 20 | 3000 |
7 | 9011 9011 901 901 9011 901 901 901 901 9011 901 901 901 81 | 10 | 2000 |
9 | 1 | 10 | 4000 |
10 | 1 | 10 | 5000 90 115 |
Из-за небольшой глубины резания и количества подачи требовался динамометр с высокой точностью измерения и хорошими динамическими характеристиками сбора данных.После того, как аналоговый сигнал фактического усилия шлифования был получен во время процесса шлифования, он был преобразован в электрический сигнал с помощью прибора для измерения деформации динамического сопротивления. Сигнал усиливался усилителем заряда и преобразовывался в трехканальный цифровой сигнал трехканального шлифовального усилия, собираемый картой сбора данных. Цифровой сигнал записывался и сохранялся с помощью компьютерного программного обеспечения, а трехстороннее шлифовальное усилие отображалось на компьютерном терминале.
2.3. Измерение
Как и в нашем предыдущем опыте [10], результаты измерения шероховатости с помощью бесконтактного оптического трехмерного лазерного сканирующего микроскопа в основном совпадали с результатами, измеренными ручным механическим контактным измерителем шероховатости. После завершения экспериментов по осевому шлифованию и измерению силы сапфирового стекла с помощью трехмерного лазерного сканирующего микроскопа (VK-250, Кейенс, Осака, Япония) были протестированы трехмерные топографии поверхности шлифованного сапфирового стекла и поверхности шлифовального круга. шероховатость поверхности S a и шероховатость линии R a шлифованной поверхности и высота выступа зерна на поверхности колеса.Шероховатость шлифованного сапфирового стекла измеряли в осевом направлении шлифования трижды для каждого набора параметров процесса шлифования, и средние значения измеренных данных принимали за значения шероховатости S a и R a . Сканирующий электронный микроскоп высокого разрешения (SEM, Apreo S, FEI Company, Hillsboro, OR, USA) использовался для обнаружения микроскопических морфологий выступов алмазных зерен на поверхности круга и поверхности шлифованного сапфирового стекла.Динамометр (Kistler, 9119AA1, Винтертур, Швейцария) использовался для проверки силы шлифования при осевом шлифовании сапфирового стекла с использованием шлифовального круга с алмазным шлифованием с крупными шлифовальными кругами. Использовался динамометр Kistler с высоким разрешением и точностью, и его точность измерения достигла 0,01 Н. Этот фиксированный динамометр с горизонтальным предварительным натягом имел компактную конструкцию, а диапазон измерения по трем направлениям мог достигать 30 кН.
3. Результаты и обсуждение
3.1. Выступ зерна на поверхности крупного алмазного шлифовального круга
Характеристики выступа зерна на поверхности алмазного круга напрямую влияют на качество шлифования и эффективность обработки поверхности сапфирового стекла.После правки шлифовального круга сухим электрическим разрядом топография выступов зерна на поверхности шлифовального круга показана на рис. Можно видеть, что большая часть алмазных зерен выступила из поверхности металлической связки, образуя острые режущие кромки с микрозернами. Между тем, можно увидеть, что возникла кратер разряда из-за выпадения алмазного зерна, что в основном было вызвано чрезмерной обработкой электрическим разрядом, что указывает на то, что электрический искровой разряд произошел на поверхности шлифовального круга.Кроме того, на поверхности шлифовального круга были обнаружены царапины. Возможная причина заключалась в том, что между поверхностью алмазного шлифовального круга и абразивными зернами, полученными из смешанного электрода, происходил процесс экструзии. Он также подтвердил принцип перевязки электрического контакта, показанный на c.
Фотография с помощью сканирующего электронного микроскопа (СЭМ) обработанной поверхности грубого алмазного шлифовального круга.
Как видно из рисунка, распределение зерен алмаза было случайным.Хотя некоторые зерна выпали, общая режущая способность шлифовального круга не изменилась с макроскопической точки зрения. После правки алмазного круга необходимо было определить высоту выступа зерна на поверхности шлифовального круга. показывает трехмерную топографию и профиль высоты выступа одиночного алмазного зерна после правки алмазного шлифовального круга с крупными частицами. а показывает трехмерную топографию одиночного выступа алмазного зерна. Показано, что высота выступа алмазного зерна составляла около 168.5 мкм через измеренную профильную кривую выступа зерна (см. B). Поскольку средний размер алмазного зерна № 46 составлял около 350 мкм, высота выступа зерна может достигать 48% от теоретического размера зерна после правки электрическим разрядом. Согласно литературным данным [20], после традиционной механической правки высота выступа зерна составляла всего около 1/3 от теоретического размера зерна. Таким образом, по сравнению с традиционной механической правкой, метод правки сухим электрическим разрядом не только имел более высокую эффективность правки, но также позволял достичь более высокого выступа зерна, что способствовало непрерывному и эффективному измельчению.Большая высота выступа зерна может привести к образованию большого пространства для стружки, что может уменьшить накопление стружки в зоне шлифования, что приведет к снижению трения и силы шлифования и улучшению качества шлифованной поверхности.
3D-топография и определение высоты выступа алмазного зерна: ( a ) 3D-топография выступа алмазного зерна и ( b ) определение высоты выступа.
3.2. Шероховатость шлифованного сапфирового стекла
Бесконтактный оптический трехмерный лазерный сканирующий микроскоп использовался для измерения шероховатости шлифованной поверхности сапфирового стекла.Кривую профиля шероховатости можно извлечь из трехмерной топографии с помощью программного обеспечения для анализа. Шероховатость поверхности S a и шероховатость линии R a шлифованной поверхности могут быть получены с помощью измеренной трехмерной топографии и кривой профиля сапфирового стекла. показана трехмерная топография и кривая шероховатости шлифованной поверхности сапфирового стекла. При параметрах процесса шлифования глубина резания a = 1 мкм, скорость подачи v f = 15 мм / мин и скорость круга N = 3000 об / мин, шероховатость поверхности S a и шероховатость линии R и шлифованного сапфирового стекла равнялись 0.736 мкм (а) и 0,194 мкм (б) соответственно. Можно сделать вывод, что эффективное и точное шлифование сапфирового стекла на основе грубого алмазного шлифовального круга, обработанного сухим электрическим разрядом, было возможным.
3D топография и кривая шероховатости поверхности шлифованного сапфирового стекла: ( a ) 3D топография и ( b ) кривая шероховатости.
показывает влияние параметров процесса шлифования, таких как глубина резания a , скорость подачи v f и скорость круга N на шероховатость поверхности S a и шероховатость линии R a шлифованной поверхности сапфирового стекла.Можно видеть, что шероховатость поверхности S , a и шероховатость линии R a лишь незначительно увеличивались с увеличением глубины резания и (см. А). Когда глубина резания a = 1 мкм, шероховатость поверхности шлифованного сапфирового стекла S, , , и R , и составляла 0,899 мкм и 0,260 мкм соответственно. Когда глубина резания a постепенно увеличивалась до 7 мкм, шероховатость поверхности шлифованного сапфирового стекла S, , , и R, , и составляла 0.964 мкм и 0,277 мкм соответственно. Хотя глубина резания увеличилась на 6 мкм, шероховатость поверхности и шероховатость линий увеличились только на 0,065 мкм и 0,017 мкм соответственно. Это связано с тем, что алмазный шлифовальный круг для грубого шлифования имел большую высоту выступа зерна и пространство для стружки и мог поддерживать режущую кромку с острым зерном, которая не могла легко повредить поверхность заготовки. Это отразило отличные характеристики шлифования алмазного шлифовального круга для грубого шлифования. Следовательно, при прецизионном шлифовании сапфирового стекла с использованием шлифовального круга с алмазным шлифованием с крупной шлифовкой глубина резания может быть соответствующим образом увеличена для эффективного повышения эффективности шлифования.
Влияние различных параметров процесса шлифования на шероховатость поверхности сапфирового стекла: ( a ) глубина резания a ; ( b ) скорость подачи v f и ( c ) скорость вращения колеса N .
Как показано на b, шероховатость поверхности шлифованного сапфирового стекла сначала существенно уменьшилась, а затем увеличилась с увеличением скорости подачи v f . Когда скорость подачи составляла 10 мм / мин, количество алмазных зерен, требующих шлифования в единицу времени, становилось меньше, так что шлифовальная сила одного зерна становилась большой, что приводило к большой шероховатости поверхности на поверхности сапфирового стекла.Если скорость подачи была слишком высокой, это привело бы к недостаточному удалению алмазных зерен с поверхности сапфирового стекла, что привело бы к столкновению с поверхностью заготовки и возникновению множества микропитаний и трещин. Когда скорость подачи v f составляла 15 мм / мин, значения шероховатости S a и R a шлифованной поверхности достигли минимальных значений 0,736 мкм и 0,194 мкм соответственно. R a 0,194 мкм было намного меньше, чем 0.Значение 392 мкм получено при использовании мелкозернистых алмазных шлифовальных кругов [5]. Следовательно, при шлифовании сапфирового стекла с использованием шлифовального круга с алмазным шлифованием с крупной шлифовкой подходящая скорость подачи должна быть установлена на уровне 15 мм / мин.
Как видно из в, шероховатость поверхности шлифованного сапфирового стекла немного уменьшилась с увеличением скорости вращения колеса N . Когда скорость вращения колеса достигла 5000 об / мин, значения шероховатости S a и R a шлифованного сапфирового стекла были равны 0.810 мкм и 0,226 мкм соответственно, которые были самыми низкими зарегистрированными значениями. Это связано с тем, что чем выше была скорость вращения круга, тем больше алмазных зерен участвовало в шлифовании в единицу времени, что приводило к уменьшению глубины резания отдельного зерна и уменьшению шероховатости шлифованной поверхности. Результаты соответствовали основному принципу шлифования твердых и хрупких материалов. Следовательно, чтобы гарантировать, что круг и станок не вибрируют, необходимо было выбрать как можно более высокую скорость вращения круга в процессе шлифования сапфирового стекла.
Основываясь на приведенных выше экспериментальных результатах, в процессе шлифования сапфирового стекла с использованием грубого алмазного шлифовального круга, обработанного сухим электрическим разрядом, было более выгодно выбрать большую глубину резания, чем большую скорость подачи при условии обеспечения качество шлифованной поверхности. Большая глубина резания увеличила глубину резания отдельного зерна для повышения эффективности шлифования. Следовательно, можно реализовать эффективное шлифование сапфирового стекла и получить высокое качество шлифованной поверхности за счет выбора большой глубины резания и соответствующих скоростей подачи и круга.
3.3. Топографии поверхности шлифованного сапфирового стекла
Для изучения влияния различных параметров процесса шлифования на качество поверхности шлифованного сапфирового стекла были изучены и проанализированы микроскопические топографии осевой шлифованной поверхности. приведены СЭМ-фотографии поверхности шлифованного сапфирового стекла при различных параметрах процесса шлифования. Сравнивая a, b, при увеличении глубины резания и уменьшении скорости подачи шероховатость поверхности S a и шероховатость линии R a шлифованного сапфирового стекла увеличивалась, что приводило к ухудшению общего качества шлифованной поверхности. .Кроме того, слишком большое удаление обрезков может привести к поломкам на поверхности земли. Сравнивая a, c, можно видеть, что значения шероховатости S a и R a шлифованного сапфирового стекла значительно увеличивались с увеличением скорости подачи, указывая на то, что скорость подачи имела большее влияние на качество шлифованной поверхности, чем глубина резания. В соответствии с основным принципом шлифования твердых и хрупких материалов [21], увеличение скорости круга увеличивает количество алмазных зерен, участвующих в шлифовании в единицу времени, так что режущее количество отдельного зерна будет уменьшаться, что приведет к уменьшению как шлифования. сила и шероховатость поверхности.Сравнивая a, d, обнаруживается, что при увеличении скорости вращения колеса и уменьшении скорости подачи качество поверхности шлифованного сапфирового стекла ухудшалось, демонстрируя, что скорость подачи имела большее влияние на качество поверхности земли, чем скорость вращения колеса. Поэтому при прецизионном шлифовании сапфирового стекла необходимо выбирать соответствующую скорость подачи.
СЭМ-фотографии поверхности шлифованного сапфирового стекла при различных параметрах процесса шлифования: ( a ) Опыт № 5; ( b ) Эксперимент No.4; ( c ) Эксперимент № 7 и ( d ) Эксперимент № 10.
В результате умеренная скорость подачи и скорость вращения колеса могут поддерживать качество поверхности земли, а глубина резания может быть увеличена для достижения эффективного шлифовка сапфирового стекла. Следовательно, выбор правильных параметров процесса шлифования может улучшить скорость съема материала.
3.4. Сила шлифования поверхности сапфирового стекла
Для исследования влияния различных параметров процесса шлифования на силу шлифования поверхности сапфирового стекла для сбора сигнала усилия шлифования использовался динамометр Kistler.Связь между усилием шлифования и периодом времени может быть получена путем фильтрации. Фильтрация среднего арифметического использовалась для устранения точек шума, полученных из собранных исходных данных перед вычислением усилия шлифования. Поскольку сигнал формы измеренного усилия шлифования имел среднее значение за период, сигнал колебался вверх и вниз в определенном диапазоне значений. В эксперименте среднее значение абсолютного значения пика (впадины) шлифовального усилия рассматривалось как среднее шлифовальное усилие при каждом наборе параметров процесса шлифования.показаны кривые испытания силы шлифования по трем направлениям при условии шлифования: глубина резания a = 1 мкм, скорость подачи v f = 25 мм / мин и скорость вращения круга N = 3000 об / мин. Также были получены кривые изменения тангенциального усилия шлифования F X , осевого усилия шлифования F Z и нормального усилия шлифования F Y в зависимости от периода времени. Таким образом, значения усилия шлифования для каждой группы параметров процесса шлифования могут быть получены, как показано на.
График испытания усилия шлифования F на поверхности сапфирового стекла: ( a ) тангенциальное усилие шлифования F X ; ( b ) осевое усилие шлифования F Z и ( c ) нормальное усилие шлифования F Y .
Зависимость усилия шлифования F поверхности сапфирового стекла от параметров процесса шлифования: ( a ) глубина резания a ; ( b ) скорость подачи v f и ( c ) скорость вращения колеса N .
показывает влияние различных параметров процесса шлифования на шлифовальное усилие поверхности сапфирового стекла. Как показано на a, нормальное усилие шлифования F Y , осевое усилие шлифования F Z и тангенциальное усилие шлифования F X все увеличивались с увеличением глубины резания a . Можно также видеть, что при одинаковых условиях процесса шлифования нормальное шлифовальное усилие было наибольшим, за ним следовало тангенциальное шлифовальное усилие, а осевое шлифовальное усилие было наименьшим.Это происходит главным образом потому, что глубина резания алмазных зерен играет важную роль в усилии шлифования. Режущее удаление материала заготовки происходило в основном в тангенциальном направлении шлифовального круга, что соответствует основному принципу шлифования твердых и хрупких материалов. Когда глубина резания a увеличилась с 1 мкм до 7 мкм, нормальное усилие шлифования F Y , тангенциальное усилие шлифования F X и осевое усилие шлифования F Z увеличилось с 0.От 45 до 1,4 Н, от 0,31 до 1,0 Н и от 0,22 до 0,66 Н соответственно. Хотя глубина резания алмазного зерна увеличилась, сила шлифования не претерпела явных изменений. Следовательно, качество поверхности земли было в основном таким же. Это можно использовать для объяснения результатов a. Подтверждено, что надлежащее увеличение глубины резания мало повлияло на силу шлифования и качество шлифованной поверхности сапфирового стекла, что может эффективно повысить эффективность шлифования.
Как показано на b, нормальное усилие шлифования F Y сначала уменьшалось, а затем увеличивалось с увеличением скорости подачи.По мере увеличения скорости подачи увеличивались как осевое усилие шлифования F Z , так и тангенциальное усилие шлифования F X . Это связано с тем, что слишком высокая скорость подачи увеличивает объем резки одного алмазного зерна, что приводит к увеличению усилия шлифования. Однако меньшая скорость подачи имела тенденцию вызывать недостаточное удаление резания и удаление стружки с поверхности сапфирового стекла, что приводило к увеличению силы шлифования и шероховатости поверхности. Следовательно, подходящая скорость подачи v f должна контролироваться в пределах от 10 до 20 мм / мин.В это время шлифовальное усилие было существенно меньше 0,5 Н.
Как показано на c, нормальное шлифовальное усилие, осевое шлифовальное усилие и тангенциальное шлифовальное усилие постепенно уменьшались с увеличением скорости вращения круга. Причина может заключаться в том, что увеличение скорости вращения круга привело к увеличению количества алмазных зерен, участвующих в резке в единицу времени, чтобы уменьшить количество разрезаемого одиночного зерна, что может обеспечить удаление пластика сапфирового стекла и улучшить качество шлифованной поверхности заготовки.Однако слишком высокая скорость вращения круга может вызвать вибрацию системы станка, что приведет к увеличению погрешности шлифования. Следовательно, подходящая скорость вращения колеса N составляла от 3000 до 5000 об / мин. Это в основном соответствует результатам шероховатости, показанным на.
3.5. Коэффициент шлифовального усилия поверхности сапфирового стекла
Сила шлифования отражает взаимодействие между шлифовальным кругом и заготовкой в зоне шлифования, которое напрямую связано с механизмом удаления материала во время процесса шлифования, качеством шлифования детали и износом шлифовального круга.Коэффициент шлифовального усилия может напрямую отражать состояние резания алмазных зерен, врезающихся в поверхность заготовки, а именно степень трения между алмазными зернами и поверхностью заготовки. Путем изменения параметров процесса шлифования для управления соотношением усилий шлифования для уменьшения износа от трения между алмазными зернами шлифовального круга и сапфировым стеклом можно улучшить качество шлифованной поверхности. Коэффициент шлифовального усилия λ можно определить как отношение нормального шлифовального усилия F Y к тангенциальному шлифовальному усилию F X [22]:
показывает взаимосвязь между различными параметрами процесса шлифования и шлифования. коэффициент сил λ.Как видно из a, когда скорость подачи v f составляла 10 мм / мин, а скорость круга N составляла 3000 об / мин, коэффициент шлифовального усилия λ находился в диапазоне от 1,40 до 1,71. Соотношение усилий шлифования практически не изменилось с увеличением глубины резания — . Можно видеть, что коэффициент шлифовального усилия λ изменялся с изменением скорости подачи в пределах от 0,97 до 1,64 (см. B). Когда скорость подачи v f составляла 15 мм / мин, коэффициент шлифовального усилия λ достиг максимального значения 1.64. По мере того, как скорость подачи продолжала увеличиваться, коэффициент шлифовального усилия уменьшался, так что объем резания в единицу времени и толщина резки отдельного зерна увеличивались, что приводило к увеличению шероховатости шлифованной поверхности и усилия шлифования, что соответствовало результатам. показано в b и b. Как показано на c, когда скорость круга увеличивалась, коэффициент λ шлифовального усилия также изменялся от 0,86 до 1,64. Исходя из приведенных выше результатов, влияние скорости подачи и скорости круга на коэффициент шлифовального усилия было значительным, но глубина резания не имела большого влияния.
Соотношение усилий шлифования λ в зависимости от параметров процесса шлифования: ( a ) глубина резания a ; ( b ) скорость подачи v f и ( c ) скорость вращения колеса N .
Вклад авторов
Концептуализация, Y.L .; Data curation, W.L .; Формальный анализ, C.Z. и H.Z .; Финансирование, Ю.Л. и X.W .; Исследование, W.L .; Методология, H.Z .; Администрация проекта, B.X. и L.L .; Надзор, X.W., B.X. и L.L .; Validation, W.L .; Письмо — оригинальный черновик, Ю.Л .; Написание — просмотр и редактирование, C.Z.
Сверхточная шлифовка и полировка прецизионного электронного стекла
Сверхточное шлифование и полировка цилиндрического стекла и кварца — особенность прецизионного электронного стекла. Аналогичным образом, наши возможности включают концентрическое шлифование: ступенчатое / уступчатое и контурное / профильное шлифование с соблюдением строгих требований к концентричности / параллельности и строгим допускам на внешний диаметр (OD).
Сверхточное измельчение широкого спектра компонентов
PEG обеспечивает сверхточное измельчение цилиндров шприцев, шлифованных и полированных трубок и заостренных наконечников / ( призм ). Это все примеры типовых компонентов, которые производит наша команда.Однако теперь большинство новых технологий требует большей сложности. В результате необходимы высококачественные и сверхточные операции шлифования и полировки. Поэтому мы производим новое поколение прецизионных требований к внешнему диаметру.В PEG мы шлифуем и полируем очень точные цилиндрические наружные диаметры (OD) до 8 дюймов и сохраняем допуски на концентричность стенок до 0,0005 дюймов или выше, если этого требуют технические условия. Кроме того, мы обрабатываем изделия длиной до 170 дюймов.
Широкий диапазон возможностей
Разрешить уникальные индивидуальные инженерные опции
Например, наши возможности включают снятие фаски, корончатое сверление до 0,03 дюйма, полировку стеклянных трубок с внешним диаметром / стержни и бесцентровое шлифование. Кроме того, мы также занимаемся финишной обработкой концов, а также шлифовкой до 27 дюймов и механической полировкой.Наконец, мы выполняем концентрическое измельчение до 40 дюймов, управляем несколькими диаметрами, прецизионными пестами и ступенчатым измельчением.
Неважно технические характеристики проекта,
PEG преобразует большинство типов стекла в соответствии со всеми потребностями
Кроме того, мы преобразовываем различные типы стекла, подходящие для большинства промышленных, медицинских и научных нужд. Во-первых, мы улучшаем кварц, стекло Pyrex, натриево-известковое стекло, боросиликат 8330, 8245 и 8447.