Пропорции раствора для производства шлакоблоков
Дата: 15.09.2014
Для возведения малоэтажных зданий часто используются шлакоблоки – стеновые камни, получаемые путем прессования бетонного раствора в форме. Они обладают рядом преимуществ, среди которых звуконепроницаемость, хорошая теплоизоляция и невысокая стоимость. Ранее их производили только на заводе, с использованием специального оборудования и пропарочной камеры, теперь же изготовлением можно заняться самостоятельно, для этого достаточно знать пропорции раствора для шлакоблока и иметь виброустановку.
Оглавление:
- Подготовительные работы
- Изготовление
Шлакоблоки подходят для возведения производственных зданий, сараев, гаражей, подвалов, мастерских, СТО, также их используют для закладки фундамента, строительства межкомнатных перегородок, прокладки вентиляционных каналов, утепления стен.
Пропорции раствора для шлакоблоков
Для изготовления используются 3 составляющие: вяжущий агент, песок и наполнитель — шлак. В роли связующего вещества могут выступать глина, гипс, известь или цемент. Большое внимание уделяется чистоте наполнителя – в нем должны отсутствовать посторонние примеси, такие как уголь, зола или земля. Состав раствора для шлакоблоков: цемент-песок-шлак в пропорции 1:3:5. При приготовлении смеси в нее необходимо добавить небольшое количество воды, примерно 0,5% от общего объема цемента. Сделать шлакоблоки можно и без использования песка, тогда пропорции будут составлять 1:9, расход воды останется тем же.
Подготовительные работы
Первым делом следует приготовить формы, делают их из дерева разборными и без дна, чтобы легко было доставать готовые изделия. Для создания пустот используются обычные бутылки, вдавленные в бетонную смесь.
Процесс получения шлакоблоков
Этапы:
- Подготовка цементно-песчаного раствора. Для перемешивания удобно использовать бетоносмеситель, но если его нет, то можно использовать лопату.
- Помещение готового раствора в форму, его уплотнение с помощью виброустановок, что позволит сохранять форму во время высыхания.
Обработка смеси при изготовлении шлакоблока своими руками длится 20-30 сек.
- Просушка. Затвердевание происходит в течение 3-4 недель при температуре 20 °C и высокой влажности воздуха.
Для ускорения схватывания бетона специалисты рекомендуют использовать пластификаторы.
- Хранение. К складированию блоков приступают через 96 часов. В зимний период времени их следует укладывать пустотами вниз, что позволит снизить вероятность разрушения или частичного повреждения.
Технология изготовления шлакоблоков отличается своей простотой, что позволяет без труда организовать их производство в домашних условиях.
Как сделать раствор для кладки шлакоблока: способы его замеса
Как правильно сделать раствор для кладкиКак сделать состав раствора для кладки шлакоблока беспокоит всех начинающих строителей, которые решились самостоятельно выложить собственный дом.
Виды составов для кладки
Можно использовать несколько вариантов расвора:
- Приготовленный своими руками.
- Приобретенный сухой порошок, для изготовления которого понадобится определенное количество воды.
Какими свойствами должен обладать раствор для кладки шлакоблока
Пропорции раствора встречаются разные, все зависит от разных случаев. По этой причине большую роль играет:
- Вязкость состава.
- Прочность после высыхания.
- Растекаемость при нанесении на поверхность.
Также стоит учесть:
- Состав раствора должен быть без комков.
- Это даст возможность ровно выполнять кладку материала.
- Большой популярностью в приготовлении раствора пользуются специальные добавки.
- Они позволяют увеличить прочность и надежность состава.
Типы кладки шлакоблока и характеристики материала
Методы кладки шлакоблокаМатериал пользуется огромной популярностью и для этого есть свои причины:
- Обусловлено это большими размерами материала.
- Они составляют 390х188х190 мм.
- Материал обладает отличными характеристиками и свойствами.
- Звуко- и теплоизоляционные свойства находятся на высоких показателях.
- Прочность материала обусловлена его структурой.
- Благодаря всем доступным ингредиентам сделать шлакоблок можно самостоятельно.
- Только для такого процесса есть специальная инструкция.
Количество сырья нужно уточнить у профессионалов в этой области.
Расход раствора на кубический метр кладки шлакоблока зависит от типа кладки. Самой экономичной является кладка в 0,5-1 блока.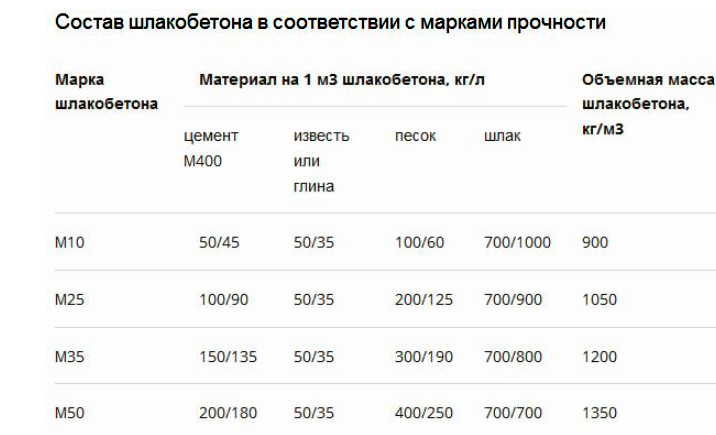
Рекомендации:
- Изначально просчитывается количество необходимого материала для кладки.
- Затем на основе полученных данных получают расход раствора на кладку шлакоблока.
- Она зависит еще от толщины накладываемого средства.
- Не рекомендуется для большей экономичности раствор выполнять его наложение более чем в 10 мм.
Самодельные растворы для кладки шлакоблока
Есть стандартные замесы раствора для кладки шлакоблока, которые чаще всего используются в строительстве.
Подробнее:
- Они характеризуются приготовлением обычного бетонного раствора.
- Он состоит из бетона, песка и воды.
- Песчано-цементная смесь составляется из 3-4 ведер песка на 1 ведро цемента.
Как делать раствор для кладки шлакоблока? Ниже приведен пример еще одного довольно простого и стандартного раствора для кладки материала:
- Песок (очищенный или нет, речной или карьерный).
- Портландцемент (марка не ниже М 400 или М 500).
- Вода.
- Красная глина.
- Пластификаторы, которые регулируют плотность раствора.
Рекомендации:
- Отношение песка и цемента составляет при этом 3 к 1.
- Емкость для определения пропорций песка и цемента должна быть одной и той же. Например, ведро или таз.
- Также стоит учитывать и размеры бетономешалки, в которой выполняется замес средства.
- Добавить в нее или убрать уже смешанные ингредиенты будет невозможно.
- Раствор для кладки шлакоблока пропорции такого типа подразумевают использование на 3 ведра песка и 1 ведро цемента 1/3 ведра красной глины.
Этапы работ:
- В подготовленную емкость высыпается песок, цемент и глина.
- Все они перемешиваются при помощи специальной деревянной лопаты или простой палки.
- После того, как бетономешалка начинает вращаться, постепенно, ведром такого же объема выполняется добавление воды.
- Ее количество зависит от того, какой тип кладки выбран.
- Также учитывается и полный вес будущего строения. Раствор должен выдержать все нагрузки и надежно закрепить материал.
- М25.
- М75.
- М100.
- М150.
- М300.
Все эти растворы можно сделать самостоятельно:
- Как приготовить раствор для кладки шлакоблока М 25? Для этого используется готовый раствор цемента марки 300, в который добавляется одна часть песка.
- Приготовление раствора М 75 также довольно простой процесс. Для этого необходимо марка готового раствора М 400. Одна часть цемента должна смешиваться в 0,5 частью известкового порошка и 4 частями песка.
- Марка раствора М 100 приготавливается из цемента марки 400, с которым смешивается 4 части песка и 0/3 извести.
- Раствор марки М 150 приготавливается с применением цемента М 400. Смешивается песок в пропорции 2,5/0,1 песка / извести и 1 часть цемента.
- Такой расход актуален только при кладке, которая выполняется при температуре от +5 и до +25 градусов.
- Также толщина стен при этом составляет от 40 и до 50 см.
Готовые растворы для кладки шлакоблока
Как работать с готовым растворомПрежде, чем приступить к изготовлению раствора для кладки шлакоблоков, стоит оценить преимущества готовых растворов.
Подробнее.
- При покупке готовой смеси не нужно искать подходящие ингредиенты. Все они уже идут в порошке в нужных пропорциях.
- Есть смеси с пластификаторами или со специальными добавками, которые придадут прочность кладке.
- Стоимость готовых смесей не слишком отличается от приготовленной самостоятельно.
Рекомендации:
- Использовать их в довольно большом количестве не рекомендуется, так как прочность стены или любого другого сооружения будет под вопросом.
- Толщина раствора с применением готовых смесей не отличается от толщины из приготовленного раствора.
- Также не рекомендуется добавлять в них известь, которая нарушить прочность раствора после высыхания.
Примеры готовых клеящих растворов для кладки шлакоблока:
- Ivsil Block.
- Weberbat Block.
- Юнис-Униблок.
- Основит Т-112.
- Knauf LM-21.
Стоит учесть:
- Эти растворы универсальные.
- Они могут использоваться как для более плотной кладки, так и для кладки с тонким слоем раствора.
- Минимальная толщина раствора при этом составляет не менее 3 мм.
- Можно использовать их не только для кладки, но и отделки сколов и других деформаций.
- Несмотря на тонкий слой, раствор не промерзнет и не утратит свои свойства и качества.
Перед выбором средства для кладки шлакоблока необходимо позаботится об удобстве и простоте приготовления. Некоторым непрофессионалам лучше отдать предпочтение уже готовым порошкам, которые просто разводятся с добавлением воды, смотрите видео по теме.
Изготовление бетонных блоков своими руками
Для изготовления бетонных блоков в качестве наполнителя подойдет: шлак, зола, отходы горения угля, отсев щебня (камня, гранита), отходы кирпича, гравий, песок, опилки (после обработки), керамзит, перлит, песчано-гравийная смесь, граншлак, зала, щебень, опилки, гипс, кирпичный бой и т.
Раствор для изготовления шлакоблоков
Раствор для шлакоблоков: шлак угольный:песок крупный (керамзитовый):гравий 5-15 мм, цемент М500, вода (7:2:2:1,5:1,5-3). Важно ледить за количеством воды, чтобы блоки не растеклись при снятии. Раствор должен при падении на землю рассыпаться, но в кулаке должен соединяться.
Для пластичности блоков можно добавить пластификатор (5 грамм на блок — прочность, водонепроницаемость и морозостойкость, меньше трещин) при вибролитье, можно и при вибропрессовании, но нужно добавлять слишком много для эффекта, а это дорого.
Чтобы шлакоблоки были прочными, нужно учитывать:
Качество песка – нужен крупный.
Шлак идеален доменный.
Цемент – качественный М400.
Оборудование – чтобы лучше прессовало, нужно добиться вибропрессования.
Время приготовления и хранение бетонных блоков
мать с ленты можно через сутки. Полное высыхание через пару месяцев. Через день блоки уже можно носить — не ломаются, класть через неделю.
При использовании пластификатора готовые блоки можно убирать с площадки и складировать уже через 6-8 часов. Без УПД – через двое суток. Хранить готовые шлакобетонные блоки нужно в пирамидальных штабелях по 100 штук с небольшим (2-3 см) промежутком между блоками – чтобы досыхали «боковушки».
На первых порах бетон можно готовить вручную. В последствии эффективнее и легче – на электрической бетономешалке объемом 0,2-0,5 куб. м.
Производственная площадка – помещение с ровным полом, хорошей вентиляцией/отоплением или ровная площадка на улице под навесом.
Преимущества шлакоблоков
- низкая себестоимость
- высокая скорость постройки из шлакоблоков;
- хорошая звукоизоляция
- хорошая теплоизоляция
- можно изготавливать и для себя, и на продажу
Отрицательные мнения по изготовления блоков из бетона своими руками
Станок выгоден лишь при наличии дешевого или «халявного» сырья или же при огромных объемах работ.
Пустотный блок, изготовленный где угодно, дороже, участка стены такого же размера, сделанного методом съемной или несъемной опалубки, тем более вы тратите свое время и силы. Поэтому, в основном, продажа этих станков – это всего лишь возможность заработать на других.
Пример расходов и стоимости изготовления самодельных блоков
На производство одного шлакоблока уходит 0,011 куб.м раствора, в пропорции 1:7 (цемент:граншлак), т.е. 1 мешок цемента = 36 блоков.
Законодательство
Постановлениями Правительства РФ от 13.08.97 № 1013, Госстандарта РФ № 86 от 08.10.2001 г. и Госстроя РФ № 128 от 24.12.2001 г. в перечень продукции, требующей обязательной сертификации не входят строительные бетонные блоки с различными наполнителями (шлак, керамзит, опил и т. п.), а так же виброформовочное оборудование для их производства.
Изготовление формы своими руками для литья бетонных блоков
Форма для самостоятельного изготовления шлакобетонных блоков представляет собой ящик из 3-мм металла без дна с ручками. Чтобы лицевая часть блоков была более ровной, их нужно сушить на резиновой ленте, смоченной раствором какого-нибудь моющего средства.
Начинаем процесс изготовления
Что для этого надо? Прежде всего нужно определиться с размерами. Я предлагаю остановиться на следующих размерах: 200х200х400 мм и 200х200х200 мм (это «половинки» и они обязательно потребуются при проведении работ).
Теперь подготовим формы-опалубки. Для этого необходимо распилить старые мебельные щиты из ДСП соответствующих размеров и соединить шурупами через поперечные и продольные перегородки, выпиленные из доски 40 мм(смотрите рисунок).
Такая форма удобна тем, что в нее можно одновременно закладывать 4 блока. Далее форма без дна выставляем на ровное основание под навесом, застеленное полиэтиленовой пленкой. Их внутренние поверхности промазываются отработ анным машинным маслом. Это сделано для того, что бы легче было винимать блоки после того как они затвердеют.
Теперь подготовим материал из которого будем делать блоки. В бетономешалку, а при ее отсутствии в любую емкость насыпаете гравий песок и немного извести. После того как это перемешается добавляете цемент.
Соотношение при закладке должно соответствовать пропорции — 1 часть цемента на 4 части заполнителя. Все это тщательно перемешивается и разбавляется водой до нужной консистенции. Раствор должен получится таким, что бы его удобно закладывать в форму.
Далее в форму укладывается по две лопаты раствора, армирующую проволку. На всем это еще следует расположить «вальтом» две стеклянные бутылки, заткнутые пробками. Бутылки будут играть роль герметичных стеклоблоков и благодаря им внутри блока создаются две воздушные камеры, создающие теплозвукоизоляцию.
После укладки бутылок снова заливается слой раствора с армирующей проволкой. Сверху все покрывается дополнительным слоем раствора, который заглаживается мастерком. При заливке раствора нужно хорошо утрамбовывать его, что бы внутри формы не образовывались пустоты. Когда бетон затвердеет снимается боковая стенка формы и вынимаются блоки.
Изготовлять блоки лучше в пасмурную погоду, поскольку время испарения воды из раствора увеличивается, что уменьшает вероятность появления трещин на готовых блоках. Если все же вы производите работы в жаркое время, то фомы необходимо размещать в тени и желательно накрывать их, чтобы уменьшить скорость испарения воды. Используя данный метод вы экономите до 60 процентов средств.
Вот пожалуй и все, что я хотел рассказать о народном способе изготовления бетонных блоков своими руками в домашних условиях.
Видео изготовления бетонных блоков своими руками
Читаем дальше — узнаём больше!
Оценка: 2.7 из 5
Голосов: 139
Соотношение растворной смеси для каменной кладки
🕑 Время чтения: 1 минута
Соотношение растворной смеси, т.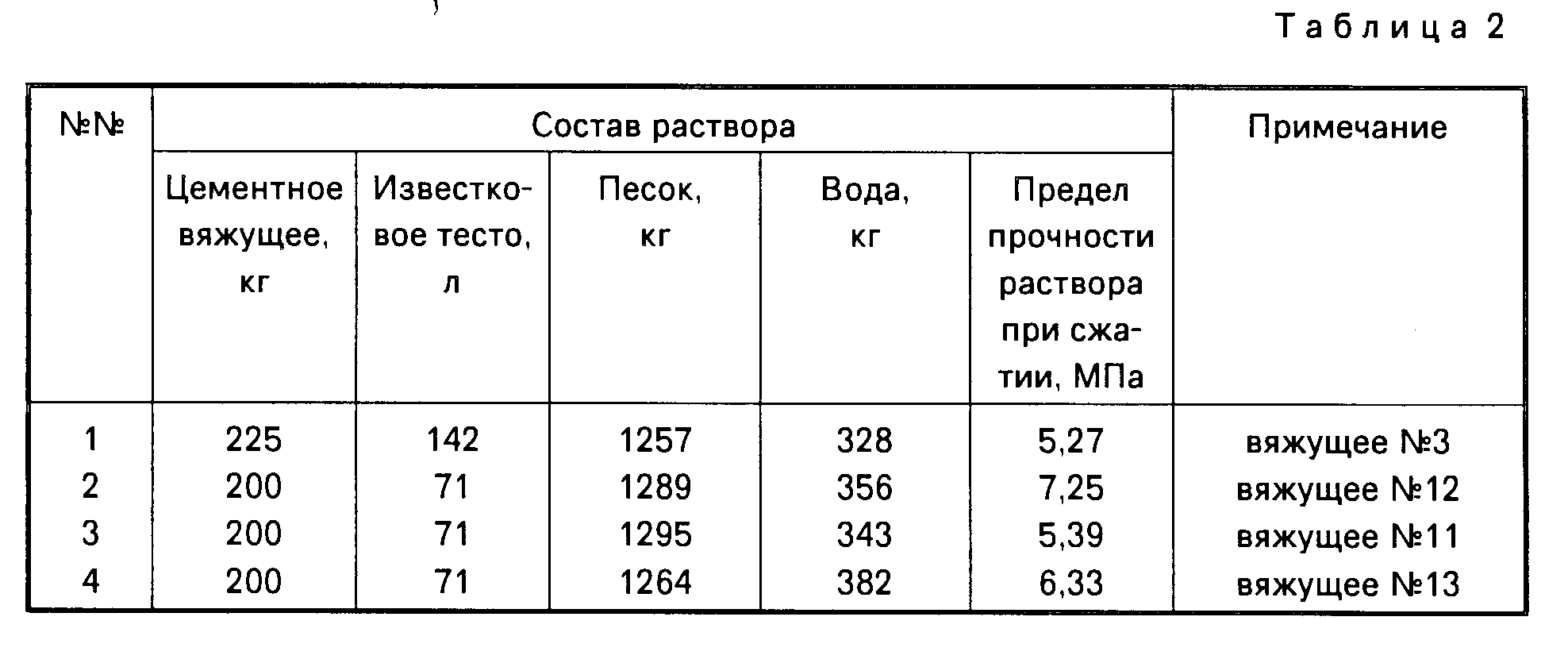
- Однородность прочности
- Равномерная обрабатываемость
- Однородный цвет
- Однородность пропорций и выхода
Минометный тип | Пропорции по объему | ||
Портландцемент | Лайм | Песок | |
М | 1 | = | 3 ½ |
С | 1 | ½ | 4 ½ |
Н | 1 | 1 | 6 |
О | 1 | 2 | 9 |
К | 1 | 3 | 12 |
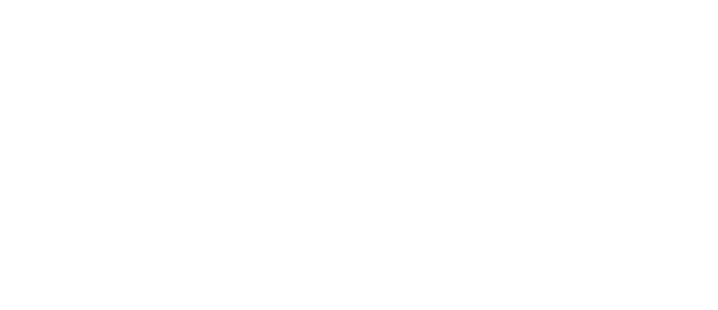
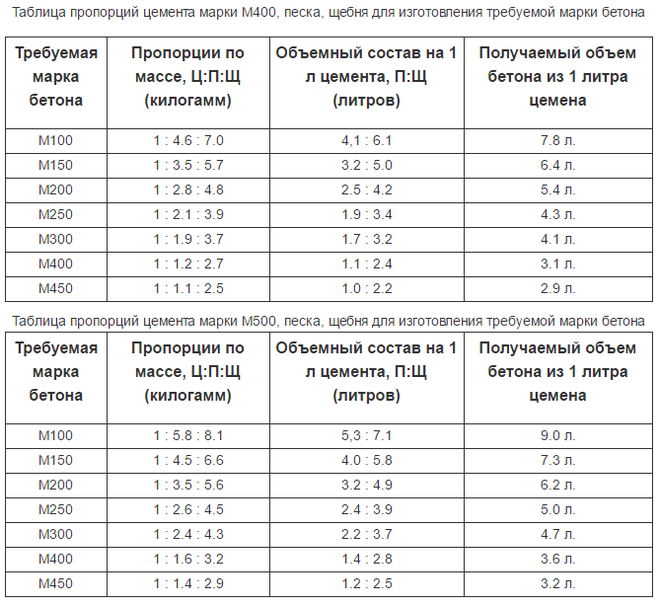
- Должен обладать хорошей обрабатываемостью
- Раствор должен легко распределяться
- Раствор должен легко проникать в швы
- Он должен легко прилипать к вертикальным поверхностям
- Обеспечивает простое позиционирование устройства на линии, отвесе и уровне
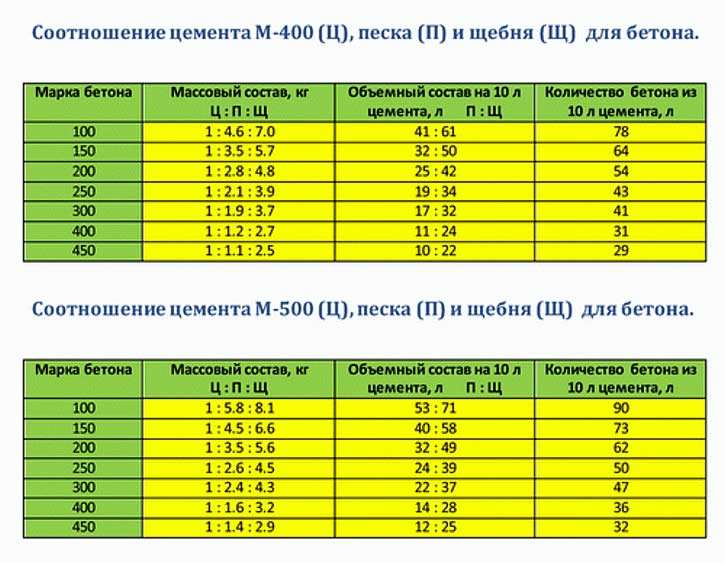
- Цементно-известковая растворная смесь
- Растворная смесь Masonry Cements
- Смесь цементных растворов
- Для большей прочности и увеличения времени схватывания используется портландцемент
- Для повышения удобоукладываемости используются пластификаторы
- Для большей долговечности и технологичности используются воздухововлекающие добавки

Каково соотношение для бетонных блоков? — Ответы на все
Какой коэффициент для бетонного блока?
Бетонные блоки часто изготавливают из бетона 1:3:6 с максимальным размером заполнителя 10 мм или из цементно-песчаной смеси в соотношении 1:7, 1:8 или 1:9.Эти смеси при правильном отверждении придают бетонным блокам прочность на сжатие, значительно превышающую требуемую для одноэтажного здания.
Что такое соотношение блоков?
Измерение коэффициента ошибок по блокам Описание 1 определяет коэффициент ошибок по блокам (BLER) следующим образом: «Коэффициент ошибок по блокам определяется как отношение количества принятых ошибочных блоков к общему количеству отправленных блоков. Ошибочный блок определяется как транспортный блок, проверка циклическим избыточным кодом (CRC) которого неверна».
Какая пропорция цемента и песка используется в блоке покрытия?
Соотношение блоков покрытия должно быть 1:2 (1 цемент и 2 песок).Размер блока крышки должен быть 2,5 см x 2,5 см (1 дюйм x 1 дюйм).
Сколько блоков мне нужно для подпорной стены?
Чтобы найти общее количество блоков, необходимых для стены, умножьте количество столбцов на количество рядов; не забудьте вычесть строку, если используете заглавные буквы.
Как рассчитать пропорцию смеси бетона?
Предписанная номинальная пропорция бетонной смеси для бетона марки М20 составляет 1:1,5:3.
- Цемент = 1 часть.
- Песок = 1.5 Часть.
- Совокупность = 3 части.
- Общий сухой объем требуемых ингредиентов = 1,57 куб.м.
Каково наилучшее соотношение смеси для бетона?
Самая безопасная ставка для любой бетонной смеси – четыре-два-один: четыре части щебня; две части песка; и одна часть цемента. Микс четыре-два-один, очевидно, состоит из семи частей. Удобно, что при смешивании бетона соотношение можно смешивать в любом диапазоне масштабов.
Какова стандартная процедура дозирования бетонной смеси?
АКИ 211.1, «Стандартная практика выбора пропорций для обычного, тяжелого и массивного бетона» была принята бетонной промышленностью в качестве стандартной процедуры для дозирования смеси. Если вы занимаетесь проектированием бетонных смесей, обязательно прочтите.
Каково соотношение цемента и бетона 20 МПа?
Бетон 20 МПа эквивалентен бетонной смеси 3000 фунтов на квадратный дюйм, поэтому соотношение такое же, как указано выше: 1. Цемент = 301,2 кг 2. Камень = 978,1 кг 3. Песок = 882,3 кг
Каково соотношение бетонной смеси для бетона с давлением 3500 фунтов на квадратный дюйм?
Это означает, что бетон с вязкостью 3500 фунтов на квадратный дюйм называется смесью из 6 мешков или смесью из 6 мешков бетона.(# округляются). Каково соотношение бетонной смеси для бетона 25 МПа? Бетон 25 МПа эквивалентен бетонной смеси 3500 фунтов на квадратный дюйм. Таким образом, соотношение смешивания такое же, как указано выше:
Сколько бетона нужно смешать на 10,5 ярдов?
Приведенный ниже талон бетона показывает бетонную смесь с давлением 3500 фунтов на квадратный дюйм для 10,5 ярдов бетона. В билете указано количество цемента, камня и песка, использованных для изготовления бетона с давлением 3500 фунтов на квадратный дюйм.
РАСТВОРЫ ДЛЯ БЕТОННОЙ КЛАДКИ — NCMA
ВВЕДЕНИЕ
Несмотря на то, что раствор составляет лишь небольшую долю от общей площади стены в строительстве из бетонной кладки (примерно 7 процентов), его влияние на эксплуатационные характеристики стены является значительным. Раствор выполняет множество важных функций: он соединяет блоки вместе в цельный структурный узел, герметизирует швы от проникновения воздуха и влаги, компенсирует небольшие смещения в стене, компенсирует небольшие различия между размерами блоков и связывает арматуру швов, связи и анкеры, чтобы все элементы работают как сборка.
РАСТВОРНЫЕ МАТЕРИАЛЫ
ASTM International поддерживает следующие национальные стандарты строительных растворов и материалов, обычно используемых в строительных растворах:
Портландцемент (ASTM C150, исх.4г) представляет собой гидравлический цемент (схватывается и твердеет в результате химической реакции с водой) и является одним из основных компонентов раствора. Типы I (нормальный), II (умеренная сульфатостойкость) и III (высокая ранняя прочность) разрешены в соответствии с ASTM C270 (ссылка 4f). Портландцементы с воздухововлекающими добавками (IA, IIA и IIIA) могут использоваться в качестве альтернативы каждому из этих типов.
Кладочный цемент (ASTM C91, ссылка 4b) представляет собой гидравлический цемент, состоящий из смеси портландцемента или смешанного гидравлического цемента и пластифицирующих материалов (таких как известняк, гашеная или гидравлическая известь) вместе с другими материалами, вводимыми для воздействия на такие свойства как время схватывания, удобоукладываемость, водоудержание и долговечность.Кладочные цементы классифицируются как тип M, тип S или тип N в соответствии с ASTM C270. Кроме того, кладочный цемент типа N можно комбинировать с портландцементом или смешанным гидравлическим цементом для получения строительных растворов типа S или M.
Растворный цемент (ASTM C1329, ссылка 4j) представляет собой гидравлический цемент, аналогичный кладочному цементу, с дополнительным требованием минимальной прочности сцепления.
Смешанные гидравлические цементы (ASTM C595, ссылка 4g) состоят из стандартного портландцемента или портландцемента с воздухововлекающими добавками (обозначается -A), объединенных путем смешивания с такими материалами, как доменный шлак (S) или пуццолан (P & PM), который обычно представляет собой летучую золу. Смешанные цементы типов IS, IS-A, IP, IP-A, I(PM) или I(PM)-A могут использоваться в качестве альтернативы портландцементу для производства строительных растворов, соответствующих стандарту ASTM C270. Типы S или SA (шлакоцемент) также могут использоваться в строительных растворах, отвечающих требованиям спецификации свойств ASTM C270 (таблица 2 настоящего ТЭК).
Негашеная известь (ASTM C5, ссылка 4a) представляет собой кальцинированный (обожженный-декарбонизированный) известняк, основными компонентами которого являются оксид кальция (CaO) и оксид магния (MgO). Перед использованием негашеная известь должна быть гашена (химически смешана с водой).Полученную известковую замазку необходимо хранить и давать гидратироваться не менее 24 часов перед использованием. Следовательно, негашеная известь редко используется в строительных растворах.
Гашеная известь (ASTM C207, ссылка 4e) представляет собой сухой порошок, полученный путем обработки негашеной извести достаточным количеством воды, чтобы удовлетворить ее химическое сродство к воде. ASTM C207 обозначает тип N (обычный), тип S (особый) и воздухововлекающие гашеную известь типа NA и типа SA. Гашение гашеной извести не требуется, поэтому гашеная известь сразу пригодна к употреблению и намного удобнее, чем негашеная.ASTM C207 ограничивает количество негидратированных оксидов в гашеной извести типа S или типа SA, обеспечивая прочность раствора, приготовленного с использованием этой извести. Известь типов N или NA обычно не используется в строительных растворах; тем не менее, они разрешены, если в ходе испытаний или протоколов испытаний показано, что они не наносят ущерба прочности строительного раствора. Использование извести с воздухововлекающими добавками разрешено только в растворах, содержащих цемент без воздухововлекающих добавок.
Заполнители (ASTM C144, ссылка 4c) для строительного раствора состоят из природного или промышленного песка.Искусственный песок – это продукт, полученный путем дробления камня, гравия или доменного шлака с воздушным охлаждением. Для него характерны острые частицы угловатой формы. Пределы градации установлены в ASTM C144 как для природных, так и для искусственных песков. Можно использовать заполнители, которые не соответствуют этим пределам градации, при условии, что полученный раствор соответствует требованиям спецификации свойств ASTM C270, как показано в таблице 2.
Вода для кладочного раствора (ASTM C270, ссылка 4f) должна быть чистой и не содержать вредных количеств кислот, щелочей или органических материалов.Питьевая вода сама по себе не рассматривается, но вода, полученная из источников питьевого водоснабжения, считается пригодной для использования.
Добавки (также иногда называемые модификаторами или добавками) для кладочных растворов (ASTM C1384, ссылка 4k) доступны для различных целей. Добавки функционально классифицируются как усилители сцепления, усилители удобоукладываемости, ускорители схватывания, замедлители схватывания и гидрофобизаторы. Поскольку хлориды ускоряют коррозию стальной арматуры и аксессуаров, ASTM C1384 предусматривает добавление примесей не более чем на 65 частей на миллион (0. 0,065%) водорастворимого хлорида или 90 ppm (0,0090%) кислоторастворимого хлорида от массы портландцемента. Точно так же Спецификации для каменных конструкций (ссылка 3) ограничивают примеси не более чем 0,2% ионов хлорида. Документ также ограничивает количество пигментов для окрашивания не более чем от 1 до 10% от массы цемента в зависимости от типа пигмента.
Влияние материалов на раствор
Благодаря разнообразию доступных материалов, кладочные растворы могут быть составлены таким образом, чтобы обеспечить желаемые свойства для большинства конкретных рабочих задач.Каждый из отдельных ингредиентов (цемент, известь, песок, вода и любые присутствующие модификаторы) влияет на характеристики раствора. Портландцемент обеспечивает прочность и долговечность. Известь придает удобоукладываемость, водоудержание, а также некоторые ограниченные вяжущие и аутогенные целебные свойства. Песок действует как наполнитель и придает раствору плотность, помогая уменьшить усадку и предотвратить растрескивание. Вода действует как смешивающий агент, смазка, а также необходима для гидратации портландцемента.
Различные варианты материалов изменяют характеристики раствора предсказуемым образом. Изменения в типе цемента вызывают небольшие изменения в характеристиках схватывания, удобоукладываемости, цвете и наборе прочности. Использование воздухововлекающего цемента или извести обычно приводит к снижению водопотребления, улучшению удобоукладываемости, повышению морозостойкости и снижению прочности сцепления. Кладочные цементы, используемые отдельно или в сочетании с портландцементом, обеспечивают строительные растворы с превосходной удобоукладываемостью и морозостойкостью; однако сила связи может быть снижена.Следовательно, расчетные допустимые значения напряжения при изгибе варьируются в зависимости от типа раствора и цементных материалов или извести, используемых для неармированной кладки (ссылка 1).
Изменения типа и градации песка влияют на свойства раствора. Природный песок обеспечивает улучшенную удобоукладываемость при более низкой потребности в воде из-за сферической формы частиц, в то время как искусственный песок требует дополнительного количества воды из-за своей угловатой формы. Как правило, хорошо отсортированные заполнители уменьшают сегрегацию в пластиковом растворе, что, в свою очередь, препятствует вытеканию и улучшает удобоукладываемость.Песок с недостаточным содержанием мелких частиц обычно дает жесткие растворы, в то время как пески с чрезмерным содержанием мелких частиц обычно приводят к получению строительных растворов с более низкой прочностью на сжатие.
ВИДЫ РАСТВОРА
Строительные нормы обычно определяют типы строительных растворов, как указано в ASTM C270, Стандартные технические условия на строительные растворы для модульной кладки (ссылка 4f). В настоящий стандарт включены четыре типа строительных растворов: M, S, N и O. Однако строительные нормы и правила обычно требуют типов M, S и N.Строительные нормы и правила также могут ограничивать использование некоторых растворов для конкретных целей. Например, для эмпирического проектирования фундаментных стен требуется раствор типа M или S, а для кладки стеклопакетов требуется раствор типа N или S (ссылка 1). Для категорий сейсмостойкости D, E и F требуется портландцемент/известь или цементный раствор типа S или M (ссылка 1).
РАСТВОР ДЛЯ ПРОПОРЦИОНИРОВАНИЯ
Все типы строительных растворов регулируются одной из двух спецификаций, содержащихся в ASTM C270: спецификацией пропорции или спецификацией свойств.В проектных документах следует указывать только одну из спецификаций, а не обе. Спецификация пропорции (Таблица 1) предписывает объемные части каждого ингредиента, необходимые для получения определенного типа строительного раствора. Комбинация портландцемента и извести может использоваться в качестве вяжущего вещества в каждом типе раствора. Кроме того, доступны кладочные цементы (ссылка 4b) или растворные цементы (сноска 4j), которые соответствуют требованиям растворов M, S и N с дополнительным добавлением цемента или без него.
В качестве альтернативы разрешенные материалы можно смешивать в контролируемых пропорциях при условии, что полученный раствор соответствует физическим требованиям, установленным в ASTM C270, как показано в таблице 2. Соотношение агрегатов, указанное в таблице 2, должно соблюдаться. Соответствие свойствам спецификации ASTM C270 устанавливается путем испытания раствора, приготовленного в лаборатории, во время предварительной оценки раствора, предложенного для проекта. Затем лаборатория устанавливает пропорции раствора на основе успешных испытаний. Эти пропорции затем соблюдаются при приготовлении полевого раствора.
СВОЙСТВА РАСТВОРА ДЛЯ КЛАДКИ
Многие свойства строительного раствора не поддаются точному количественному определению из-за отсутствия четких стандартов для их измерения. Например, строительные растворы могут быть оценены на основе получения визуально удовлетворительных растворных швов.
В зависимости от конкретных обстоятельств для данного проекта критерии выбора раствора основаны на соображениях конструкции, свойствах раствора в пластичном состоянии или свойствах раствора в отвержденном состоянии. Учет каждого необходим для достижения желаемого результата.
Свойства пластикового раствора
Удобоукладываемость – это свойство раствора, характеризующееся однородной пластичной консистенцией, что облегчает его нанесение. Это свойство наиболее важно для каменщика.Рабочий раствор легко растекается под кельмой; прилипает к вертикальным поверхностям во время обработки, размещения и укладки устройства; поддерживает выравнивание по мере позиционирования других юнитов; и обеспечивает водонепроницаемое закрытое соединение при обработке.
После того, как пропорции смеси установлены, добавление воды должно соответствовать количеству, необходимому для улучшения укладки раствора без ущерба для способности поддерживать элемент кладки. Адекватное содержание воды способствует тесному контакту между единицей и раствором, что необходимо для удовлетворительного сцепления.В то время как содержание воды оказывает наибольшее влияние на удобоукладываемость строительного раствора, вяжущие материалы, градация заполнителя и воздухововлечение также вносят меньший вклад.
Водоудержание раствора — это мера способности раствора сохранять свою пластичность при воздействии атмосферы или поглощающих сил бетонной кладки. Растворы с низкой водоудерживающей способностью быстрее затвердевают, что затрудняет каменщику укладку и регулировку блока кладки во время укладки.Растворы с желаемыми водоудерживающими характеристиками позволяют каменщику укладывать слой раствора на две или три единицы вперед, прежде чем размещать последующие единицы. Водоудерживающая способность зависит от свойств вяжущих материалов, градации песка и пропорций раствора.
Промежуток времени между нанесением слоя раствора и укладкой блока должен быть сведен к минимуму, поскольку удобоукладываемость уменьшится, так как вода впитается в блок. Если пройдет слишком много времени, прежде чем блок будет помещен на свежую подушку из раствора, блоки будут менее легко позиционироваться, и связь будет уменьшена.
Испарение воды затворения из строительного раствора может потребовать повторного отпуска (подмешивание дополнительной воды). Как правило, это не вредно, если это делается до гидратации раствора. Во избежание затвердевания при гидратации, раствор должен быть помещен в окончательное положение в течение 2,5 часов после первоначального смешивания (ссылка 3), если только не используются специальные добавки, замедляющие схватывание.
Свойства затвердевшего раствора
Свойства затвердевшего раствора, влияющие на характеристики готовой бетонной кладки, включают сцепление, прочность на сжатие и долговечность.Эти свойства трудно измерить, кроме как в лабораторных или полевых образцах, приготовленных в контролируемых условиях. Тем не менее, ASTM C1324, Стандартный метод испытаний для исследования и анализа затвердевшего кладочного раствора (ссылка 4i), содержит процедуры петрографического исследования и химического анализа компонентов кладочного раствора в затвердевшем состоянии. 0,35 унции. Образца (10 г) обычно достаточно как для петрографического, так и для химического анализа. Однако при получении образца важно убедиться, что образец является репрезентативным для рассматриваемого строительного раствора, т. е.е. оригинальный миномет, в отличие от точечного миномета или других минометов, используемых в проекте.
Бонд — это термин, используемый для описания как степени контакта между раствором и единицей, так и прочности сцепления. Сцепление зависит от нескольких факторов, включая свойства строительного раствора, характеристики поверхности изделия, качество изготовления и отверждение. При прочих равных условиях прочность сцепления будет увеличиваться по мере увеличения прочности раствора на сжатие, хотя и не прямо пропорционально. Адгезия также может быть эффективно увеличена за счет использования правильно разработанных строительных растворов с содержанием воды, обеспечивающим хорошую удобоукладываемость.
Прочность на сжатие, возможно, является наиболее часто измеряемой характеристикой строительного раствора, но, возможно, наиболее неправильно понимается. Всякий раз, когда предполагается использовать результаты прочности на сжатие для определения соответствия строительного раствора спецификациям свойств ASTM C270, испытания на прочность на сжатие должны проводиться в соответствии с лабораторными процедурами, требуемыми ASTM C270. Тем не менее, испытания раствора на сжатие в полевых условиях должны проводиться в соответствии со стандартом ASTM C780, Стандартным методом испытаний растворов для предварительной и строительной оценки строительных растворов для простой и армированной кирпичной кладки (см.4h) и предназначен только для проверки совместимости материалов и процедур, а не для определения прочности раствора (ссылка 3). ASTM C780 не содержит требований к минимальной прочности на сжатие полевого раствора. Прочность раствора в стене будет намного выше, чем при полевых испытаниях, из-за пониженного водоцементного отношения из-за поглощения воды смесью в элементах кладки и значительно уменьшенного коэффициента формы в растворном шве по сравнению с испытательным кубиком раствора. ASTM C 780 признает это и указывает, что прочность не должна толковаться как показатель фактической прочности строительного раствора.
Долговечность раствора также является важным фактором для парапетов или других стен, подвергающихся экстремальному воздействию погодных условий. Перешлифовка или чрезмерный отпуск могут снизить долговечность. Высокопрочные растворы и растворы с вовлечением воздуха обеспечивают повышенную долговечность. Для более подробного обсуждения полевых испытаний строительного раствора см. TEK 18-5B, Испытание кладочного раствора (ссылка 2).
Ссылки
- Строительные нормы и правила для каменных конструкций, ACI 530-02/ASCE 5-02/TMS 402-02.Отчет Объединенного комитета по стандартам каменной кладки, 2002 г.
- Испытание кладочного раствора, ТЭК 18-5Б. НЦМА, 2014.
- Спецификации для каменных конструкций, ACI 530.1-02/ASCE 6-02/TMS 602-02. Отчет Объединенного комитета по стандартам каменной кладки, 2002 г.
- Ежегодный сборник стандартов ASTM за 2004 г., Американское общество по испытаниям и материалам:
4a. C5-03, Стандартные технические условия на негашеную известь для строительных целей.
4б. C91-03a, Стандартные технические условия на кладочный цемент.
4с.C144-03, Стандартные технические условия на заполнитель для кладочного раствора.
4д. C150-04, Стандартные технические условия на портландцемент.
4д. C207-04, Стандартные технические условия на гашеную известь для каменной кладки.
4ф. C270-03b, Стандартные технические условия на раствор для модульной кладки.
4г. C595-03, Стандартные технические условия на смешанные гидравлические цементы.
4ч. C780-02, Стандартный метод испытаний для предварительной и строительной оценки строительных растворов для простой и армированной кирпичной кладки.
4и.C1324-03, Стандартный метод испытаний для исследования и анализа затвердевшего кладочного раствора.
4к. C1329-04, Стандартные технические условия на цементный раствор.
4к. C1384-03, Стандартные технические условия на добавки для кладочных растворов.
NCMA TEK 9-1A, редакция 2004 г.
NCMA и компании, распространяющие эту техническую информацию, отказываются от какой-либо ответственности за точность и применение информации, содержащейся в этой публикации.
— Соотношение цемента и грунтового раствора, применяемого в качестве покрытия стен, и его прочность на растяжение…
Контекст 1
… с другой стороны, соотношение извести в дозировках отражает меньший коэффициент корреляции (R² = 0,85) между доля грунта в дозировке и испытание на сжатие. При сравнении цементно-известково-грунтовых растворов с той же пропорцией грунта уменьшение дозировки извести приводит к более высокой механической прочности из-за большей удельной поверхности извести, которая потребляла большую норму воды для достижения той же консистенции (таблица 1). и, следовательно, привело к большей пористости и меньшей механической прочности (СИЛЬВА; КАМПИТЕЛИ, 2006)….
Контекст 2
… применяя статистическую обработку и классификацию по минимальным критериям, указанным в этом исследовании, дозировки, используемые в качестве стеновых покрытий на кладочных блоках, представлены в таблице 1. …
Контекст 3
… стандарт NBR 13528 (ABNT, 2005b) устанавливает, что 66,67% результатов испытаний на прочность сцепления при растяжении должны быть больше или равны 0,3 МПа, поэтому раствор идеально подходит для использования в качестве раствора для наружных покрытий, и больше или равно 0.2 МПа для использования в качестве внутреннего раствора. Таким образом, растворы с добавками песчано-глинистого грунта или гашеной извести (максимальное соотношение 0,6 к массе грунта) допустимо использовать для внутреннего покрытия земляных сооружений (табл. 1). Хотя песчано-глинистый грунтовый средний раствор с добавкой добавки не достигает минимального значения прочности сцепления, он представляет потенциал для использования благодаря своему низкому коэффициенту вариации. …
Контекст 4
… с грунтом, песком, цементом и известью имеют самые низкие значения прочности сцепления при растяжении, за ними следуют растворы с более высоким содержанием извести (Таблица 1). Согласно Azeredo, Morel and Barbosa (2007), гашеная известь химически реагирует с иллитом и монтморинолитом, которые существуют в частицах глины, что приводит к стабилизации цементно-почвенно-известкового композита. …
Контекст 5
… также видно из Таблицы 1, что прочность сцепления в цементных и песчано-глинистых покрытиях, за исключением дозировок с более высоким содержанием извести, не меняется при добавлении известь или смесь. Однако класс дозировки важен для повышения адгезии, другими словами, чем выше доля почвы в дозировке раствора, тем ниже прочность сцепления растворов при растяжении….
Контекст 6
… растворы с известью обладают высокой склонностью к растрескиванию вследствие высыхания, тогда как растворы с добавками стабилизируются как в процессе усадки, так и при отсутствии трещин (табл. 2). Добавка позволяет снизить расход воды без снижения ее водоудерживающей способности (табл. 1). Следовательно, в испаряемой смеси меньше свободной воды, что снижает объемную изменчивость строительных растворов и, следовательно, приводит к снижению напряжений в покрытии. …
Контекст 7
… цементно-грунтовые растворы, не подверженные растрескиванию, показали минимальную прочность на сжатие 4 МПа и водоудержание более 96% (рисунки 4 и 5 и таблицы 1 и 2) . Тем не менее, следует отметить, что прочность сцепления при растяжении является еще одним важным фактором, который необходимо оценивать при оценке характеристик раствора для покрытия, поскольку он указывает на поведение с учетом деформации и растяжения, а также возможность возникновения патологических проявлений….
Пропорции бетонных и растворных смесей (по объему) verificando o comportamento mecânico dos prismas eo modo de ruptura de cada tipologia quando submetidos à сжатие осевого. Os dois blocos ceramicos utilizados são de parede maciça e parede vazada.В качестве сопротивления сред сжатию блоков до 9,85 МПа для керамического блока из пареде-вазада и 22,50 МПа для керамического блока из пареде-масиса. Os prismas foram moldados com argamassa produzida em Laboratorio, de cimento, cal e areia, Visando obter argamassas com relação de Resistance em relação ao bloco (fa/fbm,líquida) igual a 0,30 e 0,70.


Соотношение цемента – обзор
7.5.1 Влияние содержания летучей золы на механические свойства
Прочность на сжатие композита с различным соотношением летучей золы и цемента, испытанная в возрасте 7, 14 и 28 дней (Tian и Zhang, 2013) показано в таблице 7.3.
Таблица 7.3. Сила компрессовой составляющей с различной летучей золой / соотношением цемента

можно увидеть, что прочность на сжатие композита сопоставима с традиционным бетоном с значение в возрасте 28 дней, достигающее 42,37, 36,67 и 33,82 МПа для композита с соотношением золы-унос/цемент 1,2, 1,6 и 2,0 соответственно. По мере увеличения отношения летучей золы к цементу с 1,2 до 1,6 и 2,0 прочность композита на сжатие через 28 дней снижается.Это можно объяснить следующим образом. После смешивания между различными ингредиентами композита произойдет химическая реакция. В процессе химической реакции лишь небольшая часть состава золы-уноса вступает в пуццолановую реакцию с вяжущим веществом, в то время как большая часть состава золы-уноса играет роль лишь для заполнения пространства между соединениями. матрицы. Из-за большого количества летучей золы в новом композите и значительно меньшего количества цемента по сравнению с обычным бетоном снижается адгезионное напряжение между частицами, поскольку для соединения частиц, содержащихся в матрице, доступно меньше пасты. Кроме того, добавление летучей золы может увеличить содержание воздуха в матрице; это также может вызвать снижение прочности композита на сжатие. Для композита с постоянным соотношением золы-унос/цемент прочность на сжатие композита увеличивается с 7 до 14 дней с увеличением на 13,93% при соотношении зола-уноса/цемент 1,2, на 14,16% при соотношении зола-уноса/цемент 1,2. 1,6 и 14,27% при соотношении золы-унос/цемент 2,0 соответственно. Но прирост прочности на сжатие на 28 сутки по сравнению с 7 сутками более значителен при увеличении на 35.4 %, 51,2 % и 55,7 % при соотношении летучей золы/цемента 1,2, 1,6 и 2,0 соответственно. Это явление отражает более интенсивную пуццолановую реакцию между материалами в период между 14 и 28 днями, чем на более ранней стадии.
Испытанный модуль Юнга композита с различным соотношением золы-унос/цемент в возрасте 7, 14 и 28 дней показан на рис. 7.6.
Рисунок 7.6. Модуль Юнга композита с различным соотношением золы-унос/цемент.
Как видно из рисунка 7. 6, с 7 по 28 день модуль Юнга композита увеличивается на 92,05% при отношении зола-уноса/цемент 1,2, на 60,52% при соотношении зола-унос/цемент 1,6 и на 68,52% при соотношении зола-унос/цемент. 2.0. Более того, тестируемый модуль Юнга в том же возрасте отверждения уменьшается с увеличением отношения золы-уноса/цемента. В возрасте 28 дней модуль Юнга составляет 18,59 ГПа для отношения золы-унос/цемент 1,2, 15,25 ГПа для отношения золы-унос/цемент 1,6 (при уменьшении 17,97%) и 14.24 ГПа при соотношении золы-унос/цемент 2,0 (при снижении на 6,62%). Применение большого количества летучей золы вместо цемента приводит к меньшему напряжению сцепления между частицами и большему содержанию воздуха в матрице; следовательно, модуль Юнга композита соответственно уменьшается.
В таблице 7.4 показана прочность на изгиб композита с различным соотношением летучей золы/цемента 1,2, 1,6 и 2,0, испытанная в возрасте 7, 14 и 28 дней. Видно, что прочность композита на изгиб снижается с увеличением отношения золы-унос/цемент. В возрасте 28 дней испытанная прочность композита на изгиб составляет 5,74 МПа для соотношения золы-унос/цемент 1,2, 5,22 МПа (снижение на 9,06%) и 4,67 МПа (снижение на 18,64%) для золы-уноса/цемент. цементный коэффициент 1,6 и 2,0 соответственно. Прочность композита на изгиб в возрасте 7 дней для всех трех соотношений золы-унос/цемент составляет более 3 МПа. Из-за реакции гидратации вяжущего материала образцы становятся более твердыми, а их прочность на изгиб постепенно увеличивается со временем отверждения, с увеличением на 24.51% для отношения летучая зола/цемент 1,2, 61,61% для отношения летучая зола/цемент 1,6 и 55,15% для отношения летучая зола/цемент 2,0, соответственно, в возрасте от 7 дней до возраста 28 дней .
Таблица 7.4. Сила изгиба к составным составным соотношением со составным соотношением на разных летушке / цемента
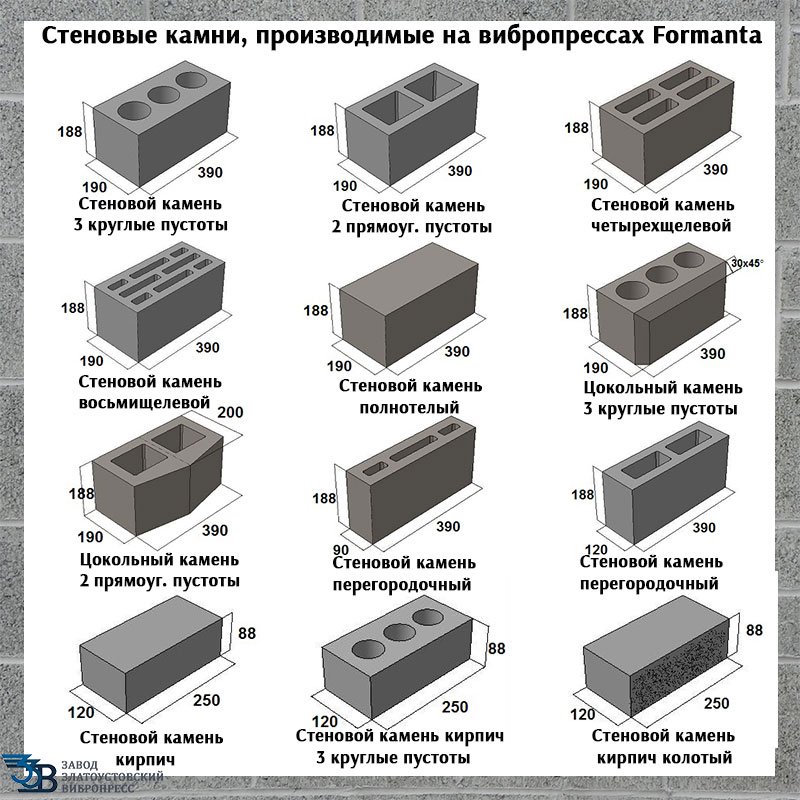
Проведенные испытания зависимости прочности на растяжение от деформации композита с различным соотношением золы-уноса и цемента показаны на рис. 7.7.
Рисунок 7.7. Прямые кривые растяжения новых композитов при различном содержании летучей золы.
На рис. 7.7 показано незначительное изменение прочности композита на растяжение при изменении отношения золы-уноса к цементу от 1,2 до 2,0. Чтобы лучше интерпретировать механическое поведение разработанного композита, представлено другое механическое свойство, а именно пластичность при растяжении. Пластичность при растяжении означает способность определенного материала поглощать энергию и может быть рассчитана как площадь под кривыми до определенного значения деформации. Это видно из рисунка 7.7 видно, что до того, как деформация достигает 2%, площадь под кривыми сильно увеличивается с увеличением содержания летучей золы. Это означает, что пластичность композита при растяжении резко возрастает, и с увеличением содержания летучей золы поглощается больше энергии. Для нового композита с отношением золы-уноса к цементу, равным 1,2, предел прочности при растяжении внезапно упал до уровня не более 1 МПа, когда возникли трещины, и предел прочности при растяжении продолжал постепенно снижаться до тех пор, пока образец не был окончательно поврежден.Хотя предел прочности при растяжении также внезапно снижался, когда в образцах для растяжения с отношением золы-уноса к цементу 1,6 возникали трещины, остаточная прочность на растяжение составляла около 2 МПа, что почти в два раза больше, чем у его аналога с отношением золы-унос/цемент. 1.2. Повышенная ударная вязкость была более очевидной для цементного композита с соотношением летучей золы/цемента 2,0. Для этого композита предел прочности при растяжении также резко снижался, когда образец растрескивался, но остаточное растягивающее напряжение снова увеличивалось с увеличением деформации, причем пик остаточного предела прочности при растяжении достигал 2.
41 МПа. Это означает, что композит проявляет способность к деформационному упрочнению, что обычно связано с превосходной ударной вязкостью материалов. Как показано на рис. 7.7, такое упрочнение продолжается до тех пор, пока деформация образца при растяжении не достигнет 0,4 %, а затем остаточная прочность на растяжение постепенно снижается до тех пор, пока образец не будет окончательно поврежден.
Деформационное упрочнение можно объяснить микромеханизмами композита. В самом начале при приложении растягивающего усилия к концам образца такая же деформация происходила с волокнами и матрицей образца при приложении растягивающего усилия.С увеличением растягивающей нагрузки в матрице возникали и развивались микротрещины, и волокна перекрывали микротрещины. По мере продвижения и распространения микротрещин поперек волокон сначала происходило отслоение между частью волокон и матрицей в области трещины, а затем дальнейшее развитие вдоль поверхности между волокнами и матрицей. Во время этого процесса растягивающее напряжение в растрескавшейся матрице снималось и передавалось на мостиковые волокна, а растягивающее напряжение обычно удерживалось за счет напряжения химической связи и механического взаимодействия между матрицей и мостиковыми волокнами в несвязанной области. Прочность на растяжение, внезапно придаваемая соединительным волокнам, увеличивала деформацию соединительных волокон и способствовала процессу отсоединения волокон от матрицы. Несмотря на микротрещины в матрице, растягивающее напряжение образца увеличивалось с деформацией из-за эффекта перемычки волокон. По мере развития микротрещин микротрещины постепенно срастались между собой и образовывали видимую трещину в самом слабом сечении образца. Формулировка этой крупной трещины привела к внезапному падению кривой растяжения-деформации от пикового значения из-за быстрого снятия растягивающего напряжения из хрупкого цементного материала (Jun and Mechtcherine, 2010).Затем, с увеличением деформации, ширина основной трещины увеличивалась, а напряжение усиливалось за счет упрочняющей роли мостиковых волокон. В результате остаточное растягивающее напряжение снова увеличивалось и демонстрировало деформационное упрочнение до тех пор, пока растягивающее напряжение не достигло второго пикового значения (Zhang et al.
, 2000; Roth et al., 2010). После этого, когда к образцу прикладывалась большая растягивающая нагрузка, быстро происходило разрушение связи между мостиковыми волокнами и матрицей, и мостиковые волокна начинали вытягиваться из матрицы.Когда волокна были полностью отсоединены от окружающей матрицы, адгезионное напряжение между волокном и матрицей из-за эффекта химического связывания исчезало, и, таким образом, между соединяющими волокнами и матрицей проявлялось только напряжение трения. Для волокон багассы, когда волокна вытягивались, поверхность натуральных волокон повреждалась, и волокна становились более грубыми, что приводило к увеличению напряжения трения. Следовательно, после того, как растягивающее напряжение достигло второго пикового значения, оно постепенно снижалось с увеличением деформации из-за возникшего частичного напряжения.Наконец, когда волокна были полностью вытянуты из матрицы, перекрывающее действие волокон через большую трещину было утрачено; в результате образец разрушился и полностью потерял несущую способность.
Летучая зола играет роль заполнения пространства между продуктами гидратации, делая композит более компактным и, следовательно, повышая способность связывания волокон. Однако с уменьшением содержания летучей золы поведение композита при деформационном упрочнении становилось неочевидным.Из результатов испытаний можно сделать вывод, что увеличение содержания летучей золы в композите может повысить ударную вязкость цементного композита, армированного нитевидными кристаллами, но за счет снижения прочности на сжатие и модуля Юнга. Увеличение содержания летучей золы могло нарушить процесс гидратации цемента, что привело к снижению прочности на сжатие и модуля Юнга композита. Частица золы-уноса могла заполнить пространство между продуктами гидратации, т.е., между матрицей и волокнами для композита. В результате использование летучей золы может уплотнить матрицу и улучшить сцепление композита, что играет важную роль в механизме ударной вязкости композита.
Как смешивать раствор для бетонных блоков? – Richardvigilantebooks.

Как замешивать раствор для бетонных блоков?
Стандартное соотношение смешивания раствора: одна часть портландцемента на три части песка. Это зависит от типа раствора, который вам нужен для вашей работы.Добавьте песок в бетон и используйте мастерок для раствора или мотыгу, чтобы сложить их вместе. Убедитесь, что бетон и песок полностью перемешаны.
Какое соотношение компонентов бетонного блока?
Соотношение цементного заполнителя: Доля цементного заполнителя должна быть найдена с различными соотношениями, такими как 1: 6, 1: 8, 1: 10 до 1: 16 по весу, в зависимости от применения, т. е. несущая или не несущая. Соотношение вода-цемент: Должна использоваться питьевая вода.
Как смешивать цемент и песок для блоков?
Рекомендуемая смесь для раствора для кладки блоков 1:3, 1 часть цемента на 3 части песка.
Какой раствор используется для блоков?
Основное применение кладочного цемента Кладочный цемент типа N, кладочный цемент типа S и кладочный цемент типа M компании CEMEX специально разработаны и изготовлены для производства кладочного раствора. Кладочный раствор часто используется в строительстве из кирпича, бетонных блоков и каменной кладки; он также используется для производства каменной штукатурки.
Какая смесь лучше для бетонных блоков?
Стандартная смесь для бетонных блоков составляет 1:3:5, 1 часть цемента на 3 части песка и 5 частей каменного заполнителя по объему.1 часть цемента на 8 частей смешанного заполнителя — это почти то же самое. Обратите внимание, что соотношение отличается по весу, так как ингредиенты не имеют одинаковой плотности.
Можно ли сделать бетон только из песка и цемента?
Могу ли я сделать бетон только из песка и цемента? Нет, вы не можете сделать бетон только из песка и цемента. Бетон не считается бетоном без заполнителей, таких как гравий и камень. Именно заполнители способствуют получению бетоном высокой прочности.
Каково соотношение песка и цемента для раствора?
Для стандартной растворной смеси это обычно на основе соотношения (обычно около 3 или 4 частей строительного песка на 1 часть цемента) рекомендации различаются, но вы не хотите, чтобы смесь была слишком влажной или слишком сухой.
Какой раствор использовать для шлакоблоков?
Кладочный цемент типа N, кладочный цемент типа S и кладочный цемент типа M компании CEMEX специально разработаны и изготовлены для производства кладочного раствора. Кладочный раствор часто используется в строительстве из кирпича, бетонных блоков и каменной кладки; он также используется для производства каменной штукатурки.
Какой раствор лучше для шлакоблока?
Цементный порошок обычно изготавливается из известняка и глины и является ключевым компонентом бетона.Цемент типа 1, также известный как раствор, обычно используется для склеивания шлакоблоков или кирпичей в строительстве.
Каково соотношение песка и раствора?
Растворсмешивают в различных пропорциях, в зависимости от требований к прочности материала раствора. Наиболее распространенное соотношение растворной смеси для штукатурки стен составляет 1:6, здесь 1 часть цемента и 6 частей песка в рабочем количестве воды.
Какой раствор для кирпича лучше?
тип М является самым прочным типом кирпичного раствора и используется в несущих конструкциях.