Какой расход цемента и песка на 1 куб.м. цоколя из камня (бут)?
Цоколь – это
подножие здания, являющееся переходным элементом от фундамента к стенам.
Из бутового камня получается красивый дизайнерский цоколь. Бутовый камень бывает природный и искусственный. Природный камень добывается путем раскола породы из известняка, песчаника, доломита, ракушечника и т. п., искусственный из песка и стекла. Принято считать, что ширина среднего бутового камня варьируются в пределах от 20 до 30 см.
Общий обзор и картинки для того, чтобы понимать, что из себя представляет цоколь из бутового камня.
Для цокольной части сооружения бут должен иметь так называемую плиточную форму, т. е. иметь две ровные грани.
Камни плиточной формы желательно подбирать при укладке, скреплять раствором и периодически армировать.
Цементный раствор для кладки бута такой же как и для кладки кирпича. Консистенция «густой сметаны», раствор должен
не растекаться а «стоять» на мастерке в виде кома.
Для приготовления раствора используется цемент марок: М400 и М500.
Для цемента марки М400 раствор изготавливаем в пропорции 1:3, на одну часть цемента берем 3 части песка.
В зависимости от размеров, качества подбора бутового камня на 1 куб. метр кладки может уйти от 0,25 до 0,45 куб. м. раствора.
Вычисления будут такие: мы знаем, что в одном кубе кладочного раствора 1 куб. м. песка, возьмем 0,3 куба раствора — для изготовления данного количества на понадобится 0,3 куб. м. песка и по пропорции (0,3 : 3 = 0,1) 0,1 куб. м. (100 литров) цемента.
Если брать по весу, то один куб. м. песка весит в среднем 1 625 кг., а в одном литре цемента примерно 1,4 кг.
По весу получается — песка ( Х : 0,3 = 1625 : 1) надо 487,5 кг. и цемента ( Y : 100 = 1,4 : 1) надо 140 кг.
В литературе имеется информация, что
на 1 куб. кладки уходит 1 куб. бута, порядка 150 кг цемента и песка в пропорции от 1:3 до 1:5.
Когда будете готовиться к кладке цоколя из бута, при изготовлении раствора, можете воспользоваться гостовскими нормами по таблице, для получения нужной прочности, марки раствора.
Необходим тщательный подбор камней. При их укладке должны быть минимальные зазоры и пустоты. Каменные глыбы выкладывают горизонтально, а чтобы добиться абсолютной ровности по всей длине фундамента натягивают веревку. И главным аспектом является наличие приблизительно равных по величине бутовых камней.
Все расчеты очень и очень приблизительные, возможно понадобиться большее количество цемента и песка, приобретайте стройматериалы с запасом.
Успехов Вам! Да прибудет с Вами умение!
как рассчитать для пола —
Калькулятор стяжки пола, расчет стяжки
Сколько купить мешков цемента?
Пока дело не дошло до замеса, застройщику важно знать, сколько мешков с цементом придется закупить. Здесь также следует отталкиваться от стандартных норм расхода
Допустим, нам нужно подсчитать расход цемента на стяжку пола. Оптимальная пропорция для обеспечения высокой прочности — 1:4. Цемента для этой работы нам понадобится ¼ куба. Для перевода кубов в килограммы используют усредненный показатель насыпной плотности вяжущего: в 1 литре – 1,4 кг цемента.
1/4 часть куба это 250 литров. Умножив их на 1.4 кг, получим 350 кг цемента. Итак, нам всего придется закупить 350/50= 7 мешков цемента (по 50 кг) или 14 мешков по 25 кг.
Подсчитать расход вяжущего на 1 м2 стяжки можно «обратным ходом». При толщине в 10 см на заливку одного «квадрата» потребуется 0,1 м3 раствора. Цемента в нем содержится в 10 раз меньше, чем в 1 кубометре: 350 кг/10= 35 кг. Для стяжки толщиной в 5 см нам потребуется 35/2=17,5 кг цемента М500.
На норму расхода цемента сильно влияет такой его показатель, как активность. Она определяется экспериментальным путем при замесе контрольных образцов и испытании их на прочность. Для рядового застройщика такой метод не подходит. Практический метод, которым нужно пользоваться при покупке и перед использованием – срок хранения.
Потеря цементом своей активности может достигать 20 % за один месяц.
Бдительность следует проявлять и при покупке вяжущего, требуя от продавца сертификат на покупаемую партию, в котором указана заводская дата выпуска.
Заливка стяжки для пола
В последние годы для приготовления раствора используют пескобетон. Он представляет собой смесь из портландцемента, различных добавок (минеральных и натуральных) и песка.
После того, как рассчитано, сколько мешков пескобетона нужно для стяжки пола и приготовлен раствор, а также установлены маяки, нужно немедленно приступать к заливке.
Смесь выкладывают полосами, ориентируясь на направляющие. Плавными движениями проводят правилом по рейкам по направлению к себе, передвигаясь от стены противоположной входу.
После того, как раствор сх
Расход цемента на 1 м2 стяжки пола
Создавая бетонный опорный слой, крайне важно использовать оптимальный объем расходных материалов. В статье речь пойдет о том, как рассчитать потенциальный расход цемента на 1 м2 стяжки. Сложность задачи заключается в том, что помимо минимального задействования компонентов будущей смеси, следует получить качественное и долговечное покрытие. Помимо этого, далее рассматривается вопрос приготовления, в рамках которого цементная стяжка пола будет содержать оптимальный процент песка и прочих составляющих.
Потребность в вычислениях
Создание половой стяжки актуально при необходимости получения прочного основания или, когда производится выравнивание дефектной поверхности. Также коммуникационные узлы, могут быть размещены не в стенах, а в заливаемом основании. Понять, какая именно поверхность необходима, поможет предварительно определенная цель заливки:
- основное эксплуатируемое перекрытие, например, в гараже;
- промежуточная часть для укладки облицовочных стройматериалов;
- непрерывное заливание, способствующее исправлению высотных перепадов и устранению дефектов поверхности.
Особенностью напольного состава является повышенная текучесть, способствующая тому, что готовые поверхности выравниваются самостоятельно. Достаточно соблюсти герметичность чернового основания, по которому распределяется смесь.
Подготовительный этап
Процесс заливочных работ начинается с того, что помещение очищается. Затем выставляется нулевой уровень. Относительно него рассчитываем, какова будет максимальная высота поверхности. Механическая прочность значительно снизится, если толщина будет меньше 0,8 см. Оптимально, если она будет выдержана в диапазоне от 3 до 5 см.
Расчет потенциального расхода на 1 м
2Для определения расхода цементной стяжки на 1 м2 следует понимать, какой именно стройматериал будет задействован. Вяжущий порошок имеет сухую структуру, но она может отличаться по своему компонентному составу. Детальнее о выборе портландцемента и его модификациях можно узнать из других публикаций нашего сайта.
Рассмотрим, как покрыть комнату площадью в 20 квадратных метров, создав при этом 5-сантиметровую поверхность, если используется один из видов состава, подготовленного к эксплуатации.
- Необходимый раствор будет иметь объемное содержание: 20*0,05 = 1 кубометр.
- Качественное распределение потребует примерно 100 кг на 1 м2 такой поверхности. Соответственно масса состава, заливаемого на указанную площадь, равна: 20*100 = 2000 килограмм.
- При закупке стандартных 50-килограммовых мешков вам понадобиться партия в количестве 40 упаковок.
При использовании чистого вяжущего вещества в него придётся добавить песочную составляющую (вода вливается постепенно после замеса для достижения желаемой консистенции). В классическом рецепте сочетание вяжущего компонента и песочной россыпи — 3 к 1, т. е. 0,25 к 0,75 кубометра (при обработке площадки в доме из инструкции выше).
Внимание! Желательно увеличивать расходование строительных составов, чтобы исключить дефицит, возникающий по причине необходимости заполнения дефектных зон (трещины, поры).
При данном подходе проще взять показатель массы порошка из сводной таблицы, представленной далее. Обязательно нужно учитывать марку порошка и, особенно, состава, который мы получим в результате.
Необходимая масса вяжущего порошка (в килограммах) | ||||||
Марка порошка | Марка состава | |||||
150 | 100 | 75 | 50 | 25 | 10 | |
400 | 350 | 255 | 100 | 140 | — | — |
400 | 300 | 240 | 175 | — | — | |
300 | 470 | 340 | 270 | 185 | 105 | — |
510 | 385 | 310 | 225 | 135 | — | |
200 | — | — | 405 | 280 | 155 | 25 |
— | — | 445 | 325 | 190 | 95 | |
Примечание: верхняя строка указывает массу вяжущего вещества относительно песочной россыпи, а в нижней указывается масса с запасом (+25%).![]() |
Нюансы вычислений для заливочного состава
Помимо того, что полученную массу нужно увеличить на 25%, есть несколько сложностей. Мы решили составить небольшой чек-лист на этот случай:
- заливаемая поверхность над трубами не должна быть тоньше 5 см, если же она выше 15 см, то прогреть основание станет гораздо труднее;
- сохранить (оптимизировать) энергоэффективность поможет гранитная крошка, добавленная в состав;
- при заливании состава поверх действующего основания обязательно определяется предельно допустимая нагрузка на фундамент (опору) во избежание его механического разрушения;
- наконец, переустройство жилых площадок должно осуществляться в рамках законодательства.
Учтя всё это, вы гарантируете себе оптимальный результат с минимальными рисками. Также можно выполнить вычисления посредством специального калькулятора. Введя исходные параметры, вы узнаете результат гораздо быстрее, а все вышеперечисленные аспекты будут учтены.
Сотрудничество с «АльфаЦем»
Приобрести высококачественные стройматериалы вам помогут специалисты нашей компании. Оставьте заявку или позвоните напрямую для обсуждения деталей заказа. Менеджеры оперативно дадут ответ по поводу любой продукции. Вас ждут конкурентные расценки и выгодные условия сотрудничества (оплата, доставка, гарантийные обязательства). Ждём вас!
Расход цемента на 1 м2 стяжки: расчет пропорции песка и сухой смеси для пола, цементная стяжка
В процессе ремонта в квартире или частном доме важным этапом является подготовка основания пола – укладка стяжки. Наиболее популярна и давно известна цементная стяжка пола. Если вы решили делать ремонт сами, то наверняка задались вопросами, какую смесь приобрести, как рассчитать, сколько ее понадобится.
Особенности
Цементная стяжка не теряет своей востребованности благодаря тому, что подходит под любой чистовой пол. Изготавливается она из смеси цемента и песка и разбавляется водой. Затем полученный раствор заливают в помещение.
- Доступность. Ингредиенты или готовые смеси легко приобрести в любом строительном магазине.
- Прочность покрытия. Достаточно толстый слой (как правило, более 20 мм) обеспечивает надежность и долговечность пола.
- Способность изолировать звук. В современных многоквартирных домах это качество крайне важно.
- Подходит для устройства «теплого пола». В настоящее время в частных домах, в ванных квартир часто прибегают к использованию технологии обогрева пола.Это удобно и практично. Электрические или водяные нагревательные системы можно легко и безопасно «спрятать» в цементный слой. К тому же, он обладает хорошей теплопроводностью, и потери тепла будут минимальны.
- Трубы и иные коммуникации также можно скрыть с помощью цементной стяжки.
- После высыхания слой практически не деформируется, не дает усадки. Можно не беспокоиться за его целостность.
При всем этом имеется несколько отрицательных моментов:
- работа трудная и тяжелая. Новичкам будет непросто справиться с укладкой слоя;
- раствор не подходит для старых и деревянных перекрытий из-за большого веса;
- если вам требуются минимальные отклонения для декоративного пола, то на цементную стяжку придется укладывать выравнивающий слой другой смеси;
- обычный раствор долго сохнет, требует поддержания постоянной влажности.
Также необходимо обеспечить отсутствие сквозняков и перепадов температур в процессе сушки.
Разновидности растворов
Разнообразие видов стяжки на строительном рынке постоянно растет. Основой состава является песок. Лучше всего, когда он очищенный, белый, без примеси глины. Наличие глины в составе может привести к потере высоких прочностных характеристик будущей стяжки. Разрабатываются различные добавки и пластификаторы, с помощью которых достигаются определенные заданные свойства и характеристики смеси. Вторым основным компонентом в растворе становится цемент или гипс.
Раствор с добавлением цемента прочный, такую стяжку можно использовать в помещениях с высокими нагрузками. Смесь можно применять при повышенной влажности. Цемент бюджетный, поэтому он широко востребован, но его нужно укладывать слоем от 2 см, иначе нужный эффект достигнут не будет. В случае с гипсом работа несколько проще. Поверхность получается более ровной.
Смесь быстро сохнет, не дает усадки. Существенный недостаток – нетерпимость к влаге.
Существуют три вида цементной стяжки, которую можно укладывать в помещении.
Связанная
Само название говорит о том, что стяжка связана с основанием. Отсутствуют какие-либо прослойки между плитами перекрытия, стенами и черновым полом. Такой метод используется, если необходимо достичь толщины слоя не более 40 мм.
Смесь разводят до консистенции густой сметаны, затем сразу же выливают на поверхность пола. Через 20 минут стяжка начинает застывать. Процесс этот по-настоящему долгий, в этом кроется большой минус метода. Если обрабатывается большая поверхность, то справиться с работой в одиночку невозможно.
Несвязанная
Здесь слой может быть более 40 мм. Под стяжку обязательно укладывается гидроизоляция. Это защитит и основание от проникновения влаги во время заливки стяжки, и черновой слой от влажности, поступающей извне (например, если пол делают на первом этаже «многоэтажки» или в частном доме).
Плавающая стяжка
Ее укладывают на тепло- или звукоизолирующий слой. Толщина ее может быть различной, но при достижении высоты 3-4 см может возникнуть необходимость армирования.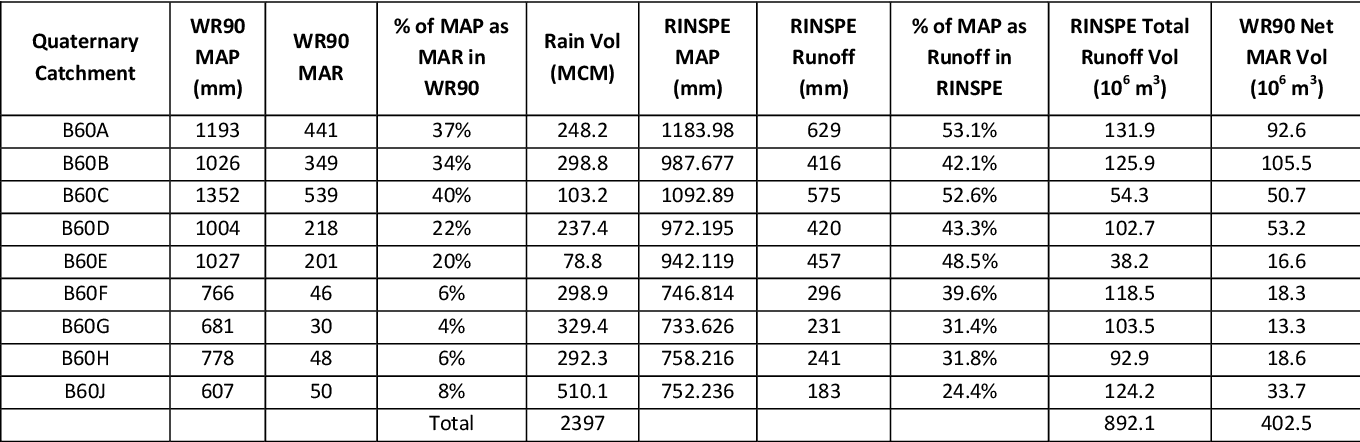
В зависимости от того, сколько добавляют воды, стяжка делится на мокрую и полусухую. Стяжка мокрым способом – это давно известный и широко распространенный метод. Так, покрытие нужно тщательно ровнять, и использовать гидроизоляцию, чтобы влага из смеси не впитывалась в основание и не ухудшала прочностные характеристики.
Полусухая стяжка получается за счет того, что норма воды снижена. Состав имеет пористую густую текстуру, похожую на пескосмесь. Его легче выровнять, и нет риска затопить соседей.
Цементную стяжку, в отличие от бетонной, применяют исключительно в помещениях, хотя стяжки из бетона также изготавливаются на основе цемента и пескосмеси с добавлением различных фракций дополнительных материалов. По стоимости они практически не различаются. Приготовить цементную стяжку можно двумя способами:
- Развести готовые смеси, которые в огромном количестве продаются в строительных магазинах. Вам нужно только изучить инструкцию, добавить нужное количество воды и размешать смесь строительным миксером.
Широко известны цементные смеси марок Knauf, Bergauf, Perel, «Геркулес», «Старатели». Фасуют смесь в мешки по 25 или по 50 кг. Такая фасовка более удобна при транспортировке, потому что цемент довольно тяжелый. Готовые стяжки имеют массу преимуществ перед самодельными. В них могут быть добавлены различные пластификаторы для улучшения прочностных характеристик и ускорения высыхания.
- Приготовить продукт самостоятельно из цемента, песка и воды. В данном случае, нужно внимательно подойти к выбору марки цемента, соблюсти пропорции воды и песка в растворе. Цифры в маркировке цемента (М200, М400 и так далее) показывают, какую максимальную нагрузку он выдерживает. Для квартир подойдут марки М150 и М200.
Важность пропорций
Если в сухие готовые смеси добавляют только воду, необходимое количество которой указывается на упаковке, то, когда готовят раствор самостоятельно, пропорции не всегда выдерживаются идеально. Крайне важна прочность на сжатие. Выше было упомянуто о максимальных нагрузках и маркировках цемента. Итак, цемент марки М150 выдерживает нагрузку 150 кг на квадратный сантиметр, его прочность на сжатие – 12,8 МПа. Чем выше показатель марки, тем больше прочность. В случаях, когда не уточняют конкретную марку, ориентируются именно на М150.
Для выполнения стяжки в квартире советуют использовать цементы марок М400 и выше.
Качество песка также влияет на общие характеристики смеси. Для высоких прочностных и качественных характеристик цементной стяжки лучше использовать песок с содержанием примесей менее 5%. В том случае, если вы воспользуетесь более загрязненным песком, итоговый результат станет совершенно непредсказуемым.После приобретения песка вы можете убедиться в его надежности, добавив некоторое его количество в бутылку с водой. Если после размешивания вода приобретает мутный коричневатый оттенок, то такой песок не стоит использовать.
Если по каким то причинам вы все-таки не уверены в ингредиентах, то советуют увеличить количество цемента на 20%, уменьшив объем воды. Важность соблюдения пропорций будет влиять на прочностные, влаго- и теплоизоляционные характеристики стяжки.Соотношение песка и цемента также зависит от предполагаемой максимальной нагрузки на стяжку. Для заливки пола в помещениях непромышленного характера, как правило, изготавливают ЦПС на основе М150 или М200. Цемент М400 и песок берут в пропорциях 1: 3 или 1: 2,8. Вода добавляется в соотношении 0,45-0,55 на 1 м2.
Нужно добиваться того, чтобы раствор был однородным, не растекался и не расслаивался, не имел сгустков. Это важно для сохранения прочности стяжки. При использовании большего количества воды стяжка будет слишком жидкой, будет долго застывать и потеряет нужные технические параметры.
Что влияет на расход
Расчет необходимого количества раствора обычно делают на основе расхода на квадратный метр. На этот расход влияет множество условий, поэтому единого механизма расчета нет. Можно выделить несколько факторов, влияющих на количество ингредиентов в смеси:
- строители знают, что на качественные характеристики стяжки влияет срок годности цемента, поэтому рекомендуется использовать порошок, выпущенный не более 6 месяцев назад, иначе прочность покрытия будет снижена как минимум на 10-15%.
Если цемент более старый, то для подстраховки его долю увеличивают.
- Неровность основания – это основной фактор, влияющий на увеличение расхода смеси. Мало только знать площадь заливаемой поверхности. Нужно учесть, что при наличии глубоких трещин и сильных перепадов поверхности расход увеличивается на 50%, поэтому замеры стоит проводить в нескольких местах.
- Чтобы сэкономить цемент, в смесь могут добавлять различные крупные фракции вроде керамзита или щебня. Это превращает раствор в пескобетон и может значительно изменить свойства покрытия.
- Количество смеси прямым образом зависит от вида стяжки. В тех случаях, если она несвязанная или плавающая, высота покрытия – более 4 см, поэтому расход материалов увеличивается.
- Марка цемента и назначение получаемой смеси влияют на соотношение сухого порошка и песка.
- Укладка коммуникаций – еще одно условие, которое может сильно повлиять на расход смеси. Диаметр труб служит основным фактором для увеличения объема смеси.
Слой стяжки над коммуникациями может достигать 5 см в высоту.
- Если задан технологический уклон (что актуально для ванной комнаты), то перепады также нужно включить в расчет готовой смеси.
- Если вы хотите добиться не только экономии ЦПС, но и повышения теплоизоляционных характеристик, то поможет не только добавление крупных частиц, но и увеличение высоты смеси. Мокрая стяжка с керамзитом для сохранения тепла должна укладываться слоем не менее 10 см.
Нюансы подсчета
При выполнении расчетов следует обратить внимание на следующие моменты:
- Назначение помещения должно влиять на выбор марок компонентов и состав добавок. Для складов, промышленных помещений с большой нагрузкой нужно выбирать цемент с более высокими показателями для повышения прочности пола.
- Если черновое покрытие нужно укладывать слоем от 80 мм, то будет эффективно использование пескобетона.
Если высоких нагрузок на покрытие не планируется, то можно монтировать ЦПС с закладкой армирующей сетки.
- При монтаже чистового покрытия толщина стяжки обычно варьируется в пределах 5-30 мм. Для такого вида стяжки лучше выбирать самовыравнивающиеся составы.
- При выполнении полусухой стяжки нужно учесть, что объем воды будет снижен в целях получения цементно-песчаной смеси необходимой консистенции.
- При устройстве «теплого пола» слой стяжки над трубами или сетью электропроводов не должен превышать 80-150 мм. Более толстый слой значительно снизит теплопроводность стяжки и эффективность действия всей системы.
- В старых многоэтажных зданиях при укладке новой стяжки поверх старой нужно учитывать, какую максимальную нагрузку выдерживает перекрытие.
Калькулятор расхода
Ввиду того, что на пропорции, количество и вид ингредиентов для стяжки влияет множество факторов, единой формулы для расчета нет. Так, для жилого помещения принято замешивать цемент с песком в пропорции 1: 3. Поскольку в некоторых комнатах предусмотрены повышенные нагрузки (например, в кухне, прихожей, ванной), то для итоговой смеси для пола предпочтительна марка М200. Для ее получения необходим цемент М500. Берется примерно 0,5 л воды. Лучше всего определять ее оптимальный объем в процессе перемешивания, так как слишком жидкий раствор может снизить качество стяжки. Объем смеси для слоя в 1 см рассчитывается на основе:
- длины помещения;
- его ширины.
Полученный результат нужно увеличить на 20% из-за усадки цементно-песчаной смеси. Для растворов собственного приготовления обычно необходимо от 14 до 21 кг смеси на 1 кв. м помещения. Для более толстого слоя расчеты нужно проводить на основе показателя его толщины. Для примера возьмем помещение 10х10 м и желаемую высоту стяжки в 5 см. Берем для заливки марку цемента М400 для получения итоговой смеси М100. Соотношение цемента и песка в данном случае – 1: 4.
- Общий объем смеси: 10*10*0,05=5 куб. м.
- Количество воды будет примерно равно половине общего объема, так что потребуется 5-2,5=2,5 куб. м сухой смеси.
- Исходя из пропорции 1: 4, цемента потребуется 0,5 куб.
м, а песка – 2 куб. м.
- Куб. м цемента весит примерно 1300 кг, куб. м песка – 1600 кг. На 100 кв. м площади нужно 1300*0,5=650 кг цемента и 1600*2=3200 кг песка.
- Так, для 1 кв. м стяжки толщиной 5 см понадобится 6,5 кг цемента.
- В мешках обычно по 50 кг. Следовательно, на всю площадь нужно 13 упаковок.
Мастер-класс по заливке стяжки пола смотрите далее.
Расход цемента на 1 м2 стяжки: как рассчитать количество
Расход цемента на 1 м2 стяжки рассчитывается в зависимости от того, с какой целью готовится раствор. Конструктивные особенности каждой смеси имеют значительные отличия, основанные на том, в каких условия будет использоваться поверхность, предусматривается укладка поверх стяжки финишного напольного покрытия, каков состав смеси, сколько слоев и каков способ скрепления с перекрытием. Расход цемента на стяжку остается основным параметром для всех видов работ, выполняемых на плоской кровле или внутри помещения, на открытых террасах или остекленных балконах.
Подготовительный этап
Определяйте объем смеси, ориентируясь на высоту стяжки
Прежде чем приступить к приготовлению раствора, предназначенного для заливки стяжки, нужно выполнить определенные замеры и рассчитать количество не только непосредственно цемента, но и самого раствора.
В первую очередь необходимо точно и правильно измерить площадь помещения или площадки, на которой будет залита стяжка.
Расчистив поверхность, на которой будет залита стяжка, от строительного мусора и лишних предметов, приступают к определению нулевого уровня. Нужно выполнить разметку на всех стенах, используя лазерный уровень нивелир или водный уровень ватерпас.
Определив высоту и толщину будущей стяжки, можно будет точно посчитать, сколько понадобится раствора, чтобы получить ровную гладкую поверхность.
Расчет ведется на 1 м2 и это поможет определить необходимое количество цемента, которое потребуется для создания качественного раствора.
После установки нулевого уровня все найденные отметки необходимо соединить одной ровной линией, чтобы определить уровень перепада высот.
Перепад высот должен вмещаться с промежуток от 0,8 см до 5 см
Уровень перепада высот – это расстояние или высота между основной (первоначальной) поверхностью и линией, соединяющей точки, найденные с помощью строительного уровня. Полученное значение не должно превышать 5 см, но оно не должно быть меньше 0,8 см. В противном случае впоследствии поверхность будет подвержена растрескиванию и начнет крошиться.
Определяя расход цемента на 1 м2 стяжки, следует учесть и его особенности. Так, например, используя для приготовления раствора Портландцемент, придется потратить немного больше песка, значит, сократится количество самого цемента.
Учитывать особенность той или иной марки материала необходимо потому, что при неправильном расчете созданная стяжка не сможет выдержать определенную нагрузку и не будет долговечной.
Выполняя расчеты, важно уделить внимание именно марке цемента. Для приготовления состава с использованием порошка марки М500 потребуется 5 частей песка и только одна часть цемента, а если используется марка М300, то песка понадобится уже всего три части.
Расчет
Чтобы приготовить качественную смесь, избежать перерасхода строительных материалов и, соответственно, денежных средств, необходимо выполнить точный расчет. Потребуется уточнить не только марку цемента, но и такие особенности, как:
- наличие в нем пластификаторов;
- сульфатостойкость;
- процентное содержание добавок;
- уровень нагрузки, которую способно выдержать созданное из данного порошка покрытие.
Умножьте площадь помещения на высоту стяжки
Для выполнения точного расчета расхода материала на 1 кв.м. можно воспользоваться простой формулой. Значение общей площади помещения нужно умножить на установленное значение высоты стяжки. Так, если в помещении, общая площадь которого составляет 80 м2, будет залита стяжка толщиной 5 см, потребуется 80 м2 х 0,05 м = 4 м3 раствора.
Учитывая, что для выполнения работ будет использован цемент марки М500, можно продолжить расчет:
По нормативу на один кубометр смеси потребуется 410 кг цемента. Для создания стяжки в данном помещении потребуется:
4 м3 х 410 кг = 1640 кг порошка марки М500.
1640 : 50 = 32,8 мешка (на 80 м2), где 50 – масса одного мешка цемента.
Это значит, что на 1 м2 стяжки в данном помещении придется потратить почти 0,5 мешка цемента, 1,5 мешка песка или 25 кг цемента марки М 500 и 75 кг мелкого песка. Подробнее о том, как правильно рассчитать расход материалов для стяжки, смотрите в этом видео:
При выполнении расчетов необходимо учитывать и особенности приготовления раствора из цемента различных марок.
Несоблюдение правил и нарушение технологического процесса ведет к созданию некачественного и недолговечного покрытия, расслоению, растрескиванию стяжки, которая очень быстро раскрошится и станет непригодной для использования.
Самые лучшие посты
Расход цемента на 1 м2 стяжки: как рассчитать количество
Расход цемента на 1 м2 стяжки рассчитывается в зависимости от того, с какой целью готовится раствор. Конструктивные особенности каждой смеси имеют значительные отличия, основанные на том, в каких условия будет использоваться поверхность, предусматривается укладка поверх стяжки финишного напольного покрытия, каков состав смеси, сколько слоев и каков способ скрепления с перекрытием. Расход цемента на стяжку остается основным параметром для всех видов работ, выполняемых на плоской кровле или внутри помещения, на открытых террасах или остекленных балконах.
Подготовительный этап
Определяйте объем смеси, ориентируясь на высоту стяжкиПрежде чем приступить к приготовлению раствора, предназначенного для заливки стяжки, нужно выполнить определенные замеры и рассчитать количество не только непосредственно цемента, но и самого раствора.
В первую очередь необходимо точно и правильно измерить площадь помещения или площадки, на которой будет залита стяжка.
Расчистив поверхность, на которой будет залита стяжка, от строительного мусора и лишних предметов, приступают к определению нулевого уровня. Нужно выполнить разметку на всех стенах, используя лазерный уровень нивелир или водный уровень ватерпас.
Определив высоту и толщину будущей стяжки, можно будет точно посчитать, сколько понадобится раствора, чтобы получить ровную гладкую поверхность.
Расчет ведется на 1 м2 и это поможет определить необходимое количество цемента, которое потребуется для создания качественного раствора.
Перепад высот должен вмещаться с промежуток от 0,8 см до 5 смПосле установки нулевого уровня все найденные отметки необходимо соединить одной ровной линией, чтобы определить уровень перепада высот.
Уровень перепада высот – это расстояние или высота между основной (первоначальной) поверхностью и линией, соединяющей точки, найденные с помощью строительного уровня. Полученное значение не должно превышать 5 см, но оно не должно быть меньше 0,8 см. В противном случае впоследствии поверхность будет подвержена растрескиванию и начнет крошиться.
Определяя расход цемента на 1 м2 стяжки, следует учесть и его особенности. Так, например, используя для приготовления раствора Портландцемент, придется потратить немного больше песка, значит, сократится количество самого цемента.
Учитывать особенность той или иной марки материала необходимо потому, что при неправильном расчете созданная стяжка не сможет выдержать определенную нагрузку и не будет долговечной.
Выполняя расчеты, важно уделить внимание именно марке цемента. Для приготовления состава с использованием порошка марки М500 потребуется 5 частей песка и только одна часть цемента, а если используется марка М300, то песка понадобится уже всего три части.
Расчет
Чтобы приготовить качественную смесь, избежать перерасхода строительных материалов и, соответственно, денежных средств, необходимо выполнить точный расчет. Потребуется уточнить не только марку цемента, но и такие особенности, как:
- наличие в нем пластификаторов;
- сульфатостойкость;
- процентное содержание добавок;
- уровень нагрузки, которую способно выдержать созданное из данного порошка покрытие.
Для выполнения точного расчета расхода материала на 1 кв.м. можно воспользоваться простой формулой. Значение общей площади помещения нужно умножить на установленное значение высоты стяжки. Так, если в помещении, общая площадь которого составляет 80 м2, будет залита стяжка толщиной 5 см, потребуется 80 м2 х 0,05 м = 4 м3 раствора.
Учитывая, что для выполнения работ будет использован цемент марки М500, можно продолжить расчет:
По нормативу на один кубометр смеси потребуется 410 кг цемента. Для создания стяжки в данном помещении потребуется:
4 м3 х 410 кг = 1640 кг порошка марки М500.
1640 : 50 = 32,8 мешка (на 80 м2), где 50 – масса одного мешка цемента.
Это значит, что на 1 м2 стяжки в данном помещении придется потратить почти 0,5 мешка цемента, 1,5 мешка песка или 25 кг цемента марки М 500 и 75 кг мелкого песка. Подробнее о том, как правильно рассчитать расход материалов для стяжки, смотрите в этом видео: youtube.com/embed/ScDM9vrfYaw?rel=0;controls=2;iv_load_policy=3;modestbranding=1;showinfo=1″ frameborder=»0″ allowfullscreen=»allowfullscreen»/>
При выполнении расчетов необходимо учитывать и особенности приготовления раствора из цемента различных марок.
Несоблюдение правил и нарушение технологического процесса ведет к созданию некачественного и недолговечного покрытия, расслоению, растрескиванию стяжки, которая очень быстро раскрошится и станет непригодной для использования.
Стяжка пола расход материала — расчет стяжки пола
Разновидности растворов
Многие пользователи ошибаются в процессе создания стяжки не только в технологии процедуры
Также очень важно не ошибиться, выбирая раствор для заливки пола, поскольку существует разнообразные виды смесей со своими преимуществами и недостатками. Не стоит пренебрегать качеством стяжки, поскольку этот слой хоть и не видно на фото, но функцию он выполняет важнейшую
Обычно связующий эффект в таких смесях создает цемент или гипс. Наполняются они песком, как мелким, так и крупнозернистым, либо полимерам или минералами, значительно улучшающими характеристики стяжки. В готовность раствор приводится при разведении определенным количеством воды.
У каждого вида раствора свои индивидуальные характеристики:
- смеси на основе цемента универсальны, поскольку обладают повышенной устойчивостью к самым разным видам негативного воздействия. Недостаток заключается в том, что происходит усадка созданного основания через некоторое время после заливки. Избежать образования трещин можно лишь при идеальном замесе раствора и закладки в него укрепляющей сетки из арматуры;
- растворы на гипсе (ангидридные смеси) очень легко применять и приходят в окончательное свое состояние они уже через 1-2 суток. Такая стяжка не подвергается усадке и их можно заливать очень тонким слоем. Гипс не переносит высокой влажности воздуха.
Составы, как из гипса, так и из цемента продаются уже в виде готовой смеси, дополненной различными модифицированными материалами, которые облегчают процесс замешивания, повышают текучесть раствора и делают его укладку проще. За счет таких смесей черновая поверхность выравнивается очень просто, и усадка создаваемой стяжки бывает минимальной. Но стоит готовая смесь в несколько раз больше, чем та, что приготавливается своими силами.
Заливка цементно-песчаной стяжки
После установки маяков, процесс заливки цементно-песчаной стяжки можно проводить уже через сутки. Но предварительно комнату на уровне пола, по периметру, оклеивают демпферной лентой.
Демпферная лента, это вспененный полимер, с нанесённым клеевым слоем. Она обеспечивает гораздо более качественную теплоизоляцию, а также предохраняет стяжку от появления трещин, в следствии сезонных перепадов температуры. Кроме того, все новые дома, в течении первых полутора лет, проходят этап усадки. А при наложении температурой деформации, этот процесс может быть очень разрушительным в отношении цементной стяжки.
Приготовленный раствор начинают заливать от дальнего угла комнаты. Залитую порцию выравнивают с помощью прави́ла. При этом, проводя прави́лом вдоль маяков, делают колебательные движения с амплитудой 5-10 см из с
Расход цемента M300-500 на стяжку пола + таблица – Блог Stroyremontiruy
Устройство стяжки – это необходимый этап капитального ремонта, поэтому надо к нему правильно подготовиться и рассчитать расход цемента M300-500 и песка. Это поможет обойтись без покупки лишнего материала и сэкономить, а также можно будет быть уверенным, что стяжка выдержит нагрузку и не потрескается от механического воздействия.
Виды и функции стяжки
Стяжка выполняет следующие функции:
- — Выравнивает поверхность, подготавливая основание пола под укладку ламината, паркета или иного покрытия,
- — Способствует правильному распределению тепловой энергии при эксплуатации тёплого пола,
- — Поглощает внешний шум и дополнительно утепляет пол,
- — Помогает создать нужный угол уклона.
Стяжки могут быть одно- и многослойными по конструкции, связанные и плавающие по способу крепления с основанием. Также разделим стяжки на:
- — Песчано-цементные (цемент, песок),
- — Наливные,
- — Бетонные (цемент, песок, гравий),
- — Гипсовые и мозаичные (цемент, мраморная крошка, песок) растворы.
Расчет расхода цемента для стяжки приведён в таблице ниже, из неё можно узнать, сколько надо цементного состава марок M300, 400, 500 на 1 м3 песка. Важно чтобы влажность песка не превышала 4-7%. Узнать уровень влажности (примерно) можно и без лаборатории – сожмите песок в ладони, если он не сохраняет форму сжатия, то влажность в норме и не превышает 6%.
Расход цемента для раствора М200: | ||||
Марка цемента ПЦ (М) | Расход цемента в кг | |||
на 1 м3 раствора | на 1 м3 песка | |||
М500 | 410 | 360 | ||
М400 | 490 | 450 | ||
Расход цемента для раствора М150: | ||||
М500 | 330 | 280 | ||
М400 | 400 | 350 | ||
М300 | 510 | 470 |
Замешивание раствора
Вода добавляется порциями в заранее перемешанные части сухого цемента и песка, раствор замешивается либо специальной мешалкой для бетона и штукатурного раствора, либо вручную лопатой или кельмой.
Консистенция готового раствора должна быть густой, проверить готовность можно на глаз – возьмите кельму смеси и положите её на ровное основание. Правильная консистенция не позволит раствору растекаться, он будет сохранять форму и иметь вымешанную однородную структуру, в которой не заметно отдельных фрагментов песка.
Расход раствора в м3
Норма расхода цемента на стяжку нами выяснена, теперь посмотрим, сколько песка и цемента надо для определённой площади.
Предположим, вам надо залить стяжку на площади 16 м2, а толщина слоя будет 3 см. В этом случае надо готовить 0,48 куба раствора (16х0,03) или 4 мешка цемента M500 (умножаем 0,48 на 410). Песка для раствора M200 понадобится в три раза больше или 600 кг, воды 100 литров.
Раствор M200
1 часть цемента M500 – 3 части песка (влажность до 6%) – 0,5 части воды.
Не забывайте, что на первом этаже или в подвале перед устройством стяжки надо делать гидроизоляцию (рулонную или мастикой), а также помните, что при дополнительном утеплении стяжки керамзитом надо раствор армировать. Для этого на подсыпку перед заливкой раствора укладывается металлическая сетка с ячейкой от 20.20 до 40/40 мм. Если армирование игнорировать, то трещины на стяжке появятся быстро.
Ответы и вопросы
В какой очерёдности добавлять материалы в раствор при замесе?
Тут есть два варианта: либо вы сначала перемешиваете в сухом виде цемент и песок, потом добавляете воду, либо в воду добавляете цемент, хорошо перемешиваете сей жидкий состав и в него добавляете песок.
Если цемента добавить в раствор больше нормы – состав будет только крепче?
Нет, нужно соблюдать указанные пропорции, излишек цемента сделает раствор не более крепким, а более слабым, отсутствие нужной пропорции связующего (песка) ухудшает характеристики смеси.
• Видимое потребление цемента США 2019
• Видимое потребление цемента США 2019 | StatistaДругая статистика по теме
Цемент Пожалуйста, создайте учетную запись сотрудника, чтобы иметь возможность отмечать статистику как избранную. Затем вы можете получить доступ к своей любимой статистике, нажав звездочку в заголовке.
Пожалуйста, авторизуйтесь, перейдя в «Моя учетная запись» → «Администрирование».После этого вы сможете отмечать статистику как избранную и использовать персональные статистические оповещения.
АутентифицироватьБазовый аккаунт
Познакомьтесь с платформой
У вас есть доступ только к базовой статистике.
Единая учетная запись
Идеальная учетная запись начального уровня для индивидуальных пользователей
- Мгновенный доступ к статистике 1 м
- Скачать в формате XLS, PDF и PNG
- Подробные ссылки
$ 59 39 $ / месяц *
в первые 12 месяцев
Корпоративный аккаунт
Полный доступ
Корпоративное решение, включающее все функции.
* Все продукты требуют годового контракта; Цены не включают налог с продаж.
Самая важная статистика
Самая важная статистика
Самая важная статистика
Самая важная статистика
Дополнительная статистика
Узнайте больше о том, как Statista может поддержать ваш бизнес .
Геологическая служба США. (7 февраля 2020 г.). Видимое потребление цемента в США с 2004 по 2019 год (в 1000 метрических тонн) [График]. В Statista. Получено 20 сентября 2020 г. с сайта https://www.statista.com/statistics/273367/consuming-of-cement-in-the-us/
US Geological Survey. «Видимое потребление цемента в США с 2004 по 2019 год (в 1000 метрических тонн)». Диаграмма. 7 февраля 2020 года. Statista. По состоянию на 20 сентября 2020 г. https://www.statista.com/statistics/273367/consuming-of-cement-in-the-us/
Геологическая служба США.(2020). Видимое потребление цемента в США с 2004 по 2019 год (в 1000 метрических тонн). Statista. Statista Inc .. Доступ: 20 сентября 2020 г. https://www.statista.com/statistics/273367/consuming-of-cement-in-the-us/
Геологическая служба США. «Видимое потребление цемента в США с 2004 по 2019 год (в 1000 метрических тонн)». Statista, Statista Inc., 7 февраля 2020 г., https://www.statista.com/statistics/273367/consuming-of-cement-in-the-us/
Геологическая служба США, Видимое потребление цемента в США.S. с 2004 по 2019 год (в 1000 метрических тонн) Statista, https://www.statista.com/statistics/273367/consuming-of-cement-in-the-us/ (последнее посещение — 20 сентября 2020 г.)
.Отверждение цементного бетона — время и продолжительность
Отверждение цементного бетона определяется как процесс поддержания нормальных условий влажности и температуры бетона для реакции гидратации, в результате чего бетон со временем приобретает затвердевшие свойства. Основные компоненты, о которых необходимо позаботиться, — это влажность, тепло и время в процессе отверждения.
Почему требуется выдержка цементобетона?
Выдержка цементобетона необходима по следующим причинам:
- Для предотвращения преждевременного высыхания бетона из-за солнечного излучения и ветра.Это предотвращает пластическую усадку бетона.
- Помогает поддерживать температуру бетона за счет процесса гидратации. Процесс гидратации требует, чтобы вода продолжалась и выделяла тепло.
- Отверждение способствует затвердеванию бетона и сцеплению с внутренними материалами и арматурой. Это помогает предотвратить повреждение соединения между бетоном и арматурой из-за вибрации и ударов.
- Это помогает создавать непроницаемый, прочный бетон без трещин.
Когда наступает время схватывания бетона?
Время начала отверждения бетона зависит от скорости испарения влаги из бетона. На скорость испарения влияют ветер, лучистая энергия солнечного света, температура бетона, климатические условия, относительная влажность.
Испарение влаги происходит за счет разницы в давлении пара на бетонной поверхности и в окружающем воздухе.Когда разница высока, скорость испарения высока.
Рис.2: Трехфазное отверждение бетонаACI 308 — Руководство по отверждению бетона предлагает три фазы отверждения бетона. Эти фазы показаны на рисунке 1.6 ACI 308.
Правильное время схватывания бетона зависит от:
1. Первоначальное отверждениеКогда бетон укладывается и уплотняется, происходит утечка воды, которая поднимается через поверхность бетона из-за оседания бетона.Скорость и продолжительность кровотечения зависят от многих факторов, включая свойства бетонной смеси, глубину или толщину бетона, метод уплотнения бетона и т. Д.
Эти сливные воды начинают испаряться с поверхности. Когда вся стекающая вода исчезнет с поверхности, начинается высыхание бетона, затем требуется первоначальное отверждение бетона, чтобы минимизировать потерю влаги и предотвратить пластические усадочные трещины в бетоне до и во время отделочных операций.
Первоначальное отверждение бетона может быть выполнено с помощью таких методов, как запотевание или использование средств уменьшения испарения, или путем установки солнцезащитных козырьков и ветровых стекол.
2. Промежуточное отверждениеПромежуточное отверждение проводится, когда операции по отделке бетонной поверхности были выполнены до окончательного схватывания бетона. Это происходит, когда необходимая текстура поверхности бетонных элементов достигается быстро или когда схватывание бетона задерживается.
3. Окончательное отверждениеКогда бетон закончен после окончательного схватывания бетона, должно быть выполнено окончательное отверждение бетона. Это помогает предотвратить высыхание поверхности бетона, поскольку потеря влаги с поверхности бетона происходит немедленно.
Какова продолжительность выдержки цементобетона?
Продолжительное отверждение бетона увеличивает прочность и долговечность бетонных конструктивных элементов. На следующем рисунке показано, как прочность бетона на сжатие увеличивается со временем, когда он затвердевает в течение более длительного времени.
Рис. 3: Влияние продолжительности отверждения в воде на прочность бетонаПродолжительность отверждения бетона зависит от
- Причина отверждения, т.е. предотвращение пластической усадки, контроль температуры, прочности и долговечности бетона.
- Размер бетонного конструктивного элемента
- Марка бетона и скорость твердения бетона
- Температурно-влажностный режим окружающей среды
- Условия воздействия на поверхность бетона во время и после твердения
- Требование отверждения продолжительность в соответствии со спецификацией бетона
Комитет 301 Американского института бетона (ACI) рекомендует минимальный период твердения, соответствующий бетону, достигающему 70 процентов указанной прочности на сжатие.Часто указываемое семидневное отверждение соответствует примерно 70 процентам указанной прочности на сжатие.
Индийский стандарт IS 456–2000 рекомендует, чтобы продолжительность отверждения бетона составляла не менее семи дней в случае обычного портландцемента и не менее десяти дней для бетона с минеральными добавками или цемента с добавками. Также рекомендуется, чтобы продолжительность отверждения была не менее десяти дней для бетона, подвергающегося воздействию сухой и жаркой погоды, и 14 дней для бетона с минеральными добавками или цементной смеси в жаркую и сухую погоду.
Ссылки- ACI 308, Американский институт бетона — Руководство по отверждению бетона
- BS 8110 — Британский стандарт для проектирования и строительства железобетонных и предварительно напряженных конструкций
- IS 456-2000: Индийский стандартный свод правил для простого и железобетона
Отверждение цементного бетона определяется как процесс поддержания нормальных условий влажности и температуры бетона для реакции гидратации, при которой бетон со временем приобретает затвердевшие свойства.
2. Почему требуется выдержка цементобетона? Отверждение цементного бетона необходимо по следующим причинам:
1. Для предотвращения преждевременного высыхания бетона из-за солнечного излучения и ветра.
2. Поддерживать температуру бетона за счет процесса гидратации.
3. Для упрочнения и сцепления с внутренними материалами и арматурой. Это помогает предотвратить повреждение соединения между бетоном и арматурой из-за вибрации и ударов.
4. Разработать непроницаемый, без трещин и прочный бетон.
Время начала отверждения бетона зависит от скорости испарения влаги из бетона. На скорость испарения влияют ветер, лучистая энергия солнечного света, температура бетона, климатические условия, относительная влажность.
4. Какова продолжительность выдержки цементобетона?Продолжительное отверждение бетона увеличивает прочность и долговечность бетонных конструктивных элементов.Однако через 28 дней после заливки бетона процесс гидратации бетона завершается на 99%. Далее продолжение лечения бесполезно.
5. Какие стандартные коды для твердения бетона? 1. ACI 308, Американский институт бетона — Руководство по отверждению бетона.
2. BS 8110 — Британский стандарт проектирования и строительства железобетонных и предварительно напряженных бетонных конструкций.
3. IS 456 — 2000: Индийский стандартный свод правил работы с обычным и железобетонным покрытием.
Подробнее:
1. Методы отверждения бетона для различных типов конструкций / конструкций
2. Методы отверждения бетонных конструкций и их сравнение
3. Отверждение высокоэффективного бетона — методы и продолжительность отверждения
4. Метод ускоренного отверждения для Испытание бетона на прочность при сжатии
5. Методы отверждения бетона для различных типов строительства / конструкций
Подготовка прочной цементной стяжки пола
СВЯЗАННЫЕ МАТЕРИАЛЫ
ADIPLAST Полимерный латекс для многократных улучшений строительных растворов
I. ХАРАКТЕР ПРОБЛЕМЫ — ТРЕБОВАНИЯ
Полы складов, гаражей и т.п. подвержены чрезмерному механическому износу, особенно трению.
Следовательно, полы в этих местах требуют как прочного сцепления с подстилающей поверхностью, чтобы они не отклеивались, так и значительного абразивного сопротивления (трения), чтобы не образовывать пыль.
II. РЕШЕНИЕ
Формирование поверхности пола со значительной прочностью и абразивной стойкостью может быть достигнуто формованием цементного раствора с добавлением полимерного латекса ADIPLAST.
Цементная стяжка, полученная в результате добавления ADIPLAST, демонстрирует повышенное сцепление, эластичность, сопротивление трению и т. Д., Обеспечивая поверхность, которая не образует пыли.
Эффективность сцепления этого раствора с основанием обеспечивается нанесением связующего слоя, в который добавлен ADIPLAST (цемент + песок + ADIPLAST).
III. ЗАЯВКА
Подготовка основания
Поверхность необходимо тщательно очистить от незакрепленных частиц, жира, масла и остатков штукатурки.
Затем его следует тщательно смочить, не оставляя луж.
Приложение
Адгезия цементной стяжки к основанию усиливается нанесением связующего слоя , а именно:
Растворная смесь из цемента: песка толщиной 2 мм: ADIPLAST: вода = 1: 1: 0,5: 0 5 (части по объему ) наносится щеткой на очищенный пол.
Это необходимо сделать перед нанесением цементного раствора на пол, чтобы связующий слой был еще свежим. Если площадь обширная, связующий слой наносится по частям, а также стяжка наносится, чтобы избежать высыхания связующего слоя в результате задержки нанесения цементного раствора. При необходимости просохшие участки и образовавшиеся швы покрывают заново.
ADIPLAST расход: прибл. 0,25 кг / м 2 / мм.Подготовка цементной стяжки с добавлением ADIPLAST в пропорции (по объему):
Сухой раствор: цемент к песку = от 1: 2 до 1: 4
Жидкость для смешивания: ADIPLAST с водой = от 1: 2 до 1: 4
Смешивание жидкости с сухим раствором = от 1: 4 до 1: 4,5
.Чем толще цементная стяжка, тем меньше пропорции цемента и ADIPLAST в смеси.
ADIPLAST следует добавить в воду для замеса в бетономешалке.
Приготовленную смесь разложить на полу еще свежим клеевым слоем с помощью направляющих толщиной 1–3 см, затем разровнять и разровнять.
Расход ADIPLAST: 0,5-1,0 кг / м 2 / см.
Гидроизоляция полов туалетов на цементной основе
Гидроизоляция полов туалетов на цементной основе помогает предотвратить попадание смывной воды. Это один из самых простых и традиционных способов гидроизоляции, который набирает популярность благодаря простоте конструкции. Гидроизоляционные материалы на цементной основе легко смешивать и наносить. Гидроизоляция на цементной основе — это легко доступные продукты, которые легко смешиваются с цементным раствором или бетоном.
Рис.1. Современный туалет с цементным полом
Гидроизоляция полов туалетов цементным раствором и бетономНиже приводится процедура гидроизоляции полов туалетов с помощью цементного раствора.
- Вначале поверхность плит пола туалета необходимо очистить от пыли, рыхлого материала и т. Д. Поверхность необходимо тщательно вымыть.
- На эту чистую и влажную поверхность укладывается стяжка из цементного раствора в соотношении 1: 3. Смесь сочетается с гидроизоляционным средством. Уложенная толщина может составлять 20 мм.
- Непрерывности швов можно избежать, укладывая слой кирпичной кладки со средней толщиной 115 мм. Подстилка для этого должна быть 10 мм. Шов должен производиться водостойким цементным раствором в соотношении 1: 3.
- Слой выполнен с уклоном для отвода воды в канализацию. Подготовленному слою дают высохнуть в течение 3 дней перед укладкой следующего слоя.
- Завершающий слой может быть выполнен из бетонного слоя толщиной 40 мм в соотношении смеси 1: 2: 4. Общий размер этой смеси составляет от 3 до 6 мм.
- Поверх цементной плитки укладывают раствор в соотношении 1: 2.
- Слой отверждается в течение 21 дня путем заливки водой на глубине 25 мм.
Фиг.2: Слой кирпичной летучей мыши с соответствующим градиентом
Примечание: Водоотталкивающие средства и гидроизоляционные добавки можно комбинировать с цементом, используемым для плит перекрытия. Добавки могут быть либо в жидкой, либо в порошковой форме. Доля добавок указана производителем.
Подробнее: Гидроизоляция полов в туалете
Преимущества гидроизоляции на цементной основеОсновными преимуществами применения гидроизоляции на цементной основе являются:
- Материалы легко доступны на рынке
- Дешевый способ гидроизоляции
- Правильно затвердевший пол станет водонепроницаемым бетонным или цементным полом.
- Этот способ гидроизоляции не требует высококвалифицированного труда
Гидроизоляция плит должна быть испытана путем заливки поверхности водой на глубину 50 мм в течение 48 часов или дольше. Таким образом проверяется водонепроницаемость пола. Испытание считается удовлетворительным, если нет утечки и не наблюдается влажных пятен на поверхности пола. Гидроизоляция считается удовлетворительной, если на потолке не видны протечки или влажные пятна.
Рис.3: Отверждение готового пола путем заливки воды
Гидроизоляционный материал, используемый для этого, должен быть либо модифицированным полимером цементным покрытием, либо любым утвержденным жидким покрытием. Согласно EN 12390 материал должен соответствовать испытаниям на проницаемость. Согласно испытаниям, утечки не должно наблюдаться через 24 часа. Этому заявлению следуют при проведении гидроизоляции туалетов и ванных комнат, в основном влажных помещений.
Подробнее на Технические характеристики
.количество песка на куб бетона, норма материала М100 и 200
Заливка стяжки пола в квартире или помещении производственного назначения является обязательной процедурой. По выровненному основанию укладывают финишное покрытие или его используют без отделки в качестве рабочей поверхности для промышленного производства. Прежде чем определиться с тем, как рассчитать количество цемента для стяжки пола, необходимо выяснить назначение помещения и предполагаемую нагрузку на бетонное основание.
Одним из главных критериев в подготовке раствора для заливки основания является его толщина. Следует помнить, что армирование металлической сеткой производят при минимальной толщине основания в 20 мм, максимальная высота заливки — 40 мм, именно такая толщина чаще всего применяется для устройства полов в гражданском домостроении.
Следующим важным пунктом для проведения вычислений является марка цемента. Для организации основания применяют цемент марок М300, М400, М500. В результате смешивания с песком и водой получают цементный раствор со значением М150 или М200.
Марка смеси определяется исходя из планируемой нагрузки на основание. Так М200 можно применять для организации оснований в зданиях промышленного назначения, например, в гаражах, а прочность марки М150 достаточна для заливки стяжки в квартире.
Для проведения расчетов необходимо знать норму расхода цемента для получения раствора определенной марки. Так, для получения одного кубометра раствора марки М150 потребуется 330 кг цемента М500 или 400 кг цемента М400. Чтобы получить такой же объем раствора марки, М200 нужно приобрести 410 кг цемента М500 или 490 кг цемента М400.
Выполним расчет организации основания толщиной 40 мм для помещения площадью 30 кв.м. в двух вариантах: для раствора марки М150 и для марки М200 с применением цемента марки М400. Порядок выполнения расчета:
- Сначала необходимо вычислить объем заливки в кубических метрах. Для этого необходимо площадь умножить на толщину (30х0,04). Получается объем раствора в 1,2 М3.
- Учитывая норму расхода цемента на 1 м3 для раствора М150 и цемента М400, получаем: 1,2 м3х400кг=480 кг. Вес одного мешка цемента – 50 кг, а значит, потребуется 10 мешков.
- Учитывая норму расхода цемента на 1 м3 для раствора М200 и цемента М400, получаем: 1,2 м3х490кг=588 кг, что соответствует 12 мешкам.
- Количество песка рассчитывается из пропорции 1:3, что означает для раствора марки М150, надо будет приобрести: 480х3=1 440 кг песка, а для раствора М200: 588х3=1 764 кг.
- Объем воды добавляют постепенно до получения требуемой пластичности раствора.
Для производства работ по организации стяжки в квартире используют речной песок, для производственных помещений выбирают песок из карьеров.
Данная модель расчета расхода цемента на стяжку пола применима для любых площадей и толщины слоя укладки смеси. Для получения площади помещения перемножают длину и ширину комнаты.
Если конфигурация помещения сложная, лучше всего использовать план этажа и посчитать площадь, сверяясь с бумажным носителем. Таким образом, учитывая соотношение 1:3, можно будет определить, сколько надо цемента и песка на куб раствора для стяжки.
От чего зависит расход
Приготовление раствора для конкретной задачи требует соблюдения пропорций и «правильной» технологии замеса. Пропорции отличаются даже для тяжелых бетонов разных марок, не говоря о штукатурке или кладочном растворе.
При этом знать справочные пропорции недостаточно – нужно понимать принципы смешивания, их зависимость от характеристик отдельных компонентов.
Хочу увидеть все голосования!
Хочу увидеть все голосования!
Здесь имеет смысл уточнить термины. Бетон – твердый камнеподобный материал на основе цемента, песка, щебня, воды. Бетонная смесь – сухой полуфабрикат для разведения водой. Цементно-песчаная смесь (ЦПС) – разновидность бетонной смеси, где отсутствует крупный заполнитель (щебень). ЦПС, разведенная водой, называется цементно-песчаным раствором.
Основные факторы, влияющие на расход
В первую очередь расход зависит от прочности (марки) бетона или раствора. Марку выбирают, исходя из вида планируемых работ.
Зная марку бетона и имеющегося сырья, можно определить нужные пропорции по справочным таблицам.
Из таблицы видно, что пропорции смеси для бетона М100 для портландцемента М500 – 1:5,8:8,1, а для бетона М300 – 1:2,4:4,3. Соответственно, чем прочнее бетонная смесь, тем выше норма расхода цемента.
Марочная прочность достигается только при условии соблюдения соотношений прочих компонентов смеси, изолированно увеличивать долю связующего бессмысленно. Кроме того, более прочный бетон часто требует введения добавок.
Кроме марки бетона на расход цемента влияет:
- марка цемента – из таблицы выше видно, что М500 на куб раствора уходит меньше, чем М400. При этом, чем прочнее связующее, тем выше марка бетона. Однако на деле на «выходную» прочность влияет также качество и тип заполнителя;
Знать плотность связующего для определения пропорций не обязательно – эта величина автоматически учитывается при выборе марки сырья. Плотность пригодится лишь тем, кому нужно вручную перевести объемный расход в массовый и наоборот.
- фактическая прочность – за 3 месяца хранения связующее может потерять до пятой части марочной прочности;
- количество заполнителя – цементное «тесто» должно полностью обволакивать частицы песка и щебня. Если «теста» будет слишком мало, смесь будет неоднородной. Поэтому на практике замешивать бетон М100–М200 из связующего М500 не вполне целесообразно;
- качество заполнителя – наличие пыли, органической грязи, глины (для песка) или лещадных зерен (для щебня) приведет к увеличению расхода связующего для компенсации потерь прочности смеси.
А вы знаете: Сколько цемента надо на 1 куб бетона
Вывод: расход прежде всего, зависит от проектной прочности бетона (раствора). Не стоит также игнорировать фактическую прочность связующего и качество заполнителей.
Приобретение раствора М150
Для покупки существует несколько удобных способов:
- заполнить форму онлайн заказа на сайте
- связаться с нами по электронной почте
- заказать по телефону
- заказать обратный звонок
Если остались вопросы, позвоните по телефонам / 8-967-593-17-23 (Анна) или воспользуйтесь формой обратной связи. Наши специалисты помогут Вам! Мы ждем ваших заявок!
Другие марки бетона
Раствор М50Раствор М75Раствор М100Раствор М125Раствор М200Раствор М250
Разновидности и марки цемента
Присвоение цементу марок позволило упростить расчет расхода. Для разных марок есть готовые таблицы с пропорциями смесей. Стандартами предусмотрен выпуск связующего М100–М900. Но на практике сфера применения низких марок (100 и 200) ограничена штукатурными и кладочными растворами с невысокой прочностью и морозостойкостью.
Разновидности портландцемента:
- обычный;
- быстротвердеющий;
- особо быстротвердеющий;
- с минеральными добавками;
- шлакопортландцемент;
- сульфатостойкий;
- пуццолановый;
- гидрофобный.
В частном строительстве обычно применяют обычный портландцемент, реже – с минеральными добавками.
Основные сферы использования марок:
- М300 – монтажные и отделочные работы, стяжка пола, растворы для кирпичной кладки. Для бетона марку почти не применяют;
- М400 – аналогично М300 плюс растворы для фундаментной кладки и (при наличии добавок) – бетона и железобетонных изделий. Не подходит для штукатурных работ;
- М500 – дорожное строительство (тротуары), лестницы, сооружения, устойчивые к влаге, массивные опалубочные плиты и фундаменты. Одна из самых покупаемых марок;
- М600 – высокопрочные бетоны для военных сооружений и восстановительных работ, где необходима высокая скорость отвердевания и прочность. Для обычных монолитов и ЖБИ используют при планируемых высоких нагрузках;
- М700 – возведение сооружений, работающих в условиях значительных нагрузок (высотные здания, мосты) и влажности. Марку применяют для реставрационных и декоративных работ.
Основных «частных» сфер применения бетонных (цементных) смесей четыре:
- фундаменты и перекрытия;
- кирпичная или блочная кладка;
- стяжка пола;
- штукатурные (отделочные) работы.
Исходя из вида работ, к раствору предъявляют разные требования. Максимальный расход связующего приходится на растворы для стяжек и прочные (М300 и выше) бетоны для оснований зданий – несмотря на использование крупного щебня или гравия. Минимальных затрат связующего требуют кладочные растворы и бетоны ниже М250.
В СНиПах есть рекомендации по расходу для приготовления 1 куба раствора смесей в зависимости от «выходной» марки. Общепринятые единицы расхода – кг на кубометр бетонной смеси (кг/м3).
Теоретически из цемента М500 можно (но нежелательно) замешивать и более низкие марки бетона.
Методики создания легкого бетона для стяжки пола
Иногда необходимо сделать легкий пол, чтобы уменьшить нагрузку на перекрытия. Для этого есть несколько способов. Благодаря им стяжка станет более легкой и воздушной.
Способы, которые помогут уменьшить вес раствора:
- Покупка готовых смесей;
- Создание легкой заливки своими руками.
Покупные варианты имеют в своем составе цемент, несколько наполнителей и добавок. Такие легкие смеси необходимы при деревянной основе. При этом их нельзя устанавливать на открытых площадках и в холодных комнатах. Влажность пола должна составлять 85%.
Для того чтобы существенно облегчить бетонную стяжку, можно использовать перлит или керамзит
Предлагаем ознакомиться Какие процедуры делать в бане для красоты и здоровья, косметические и омолаживающие процедуры
Легкие стяжки имеют значительные преимуществ. Они быстро застывают и уже спустя день можно начинать устанавливать основное покрытие. Также он утепляет пол и обеспечивает звукоизоляцию. Работы по заливке такой стяжки можно легко выполнить самостоятельно. Порадует и маленькая усадка – 0,5 мм на 1 м.
Можно самостоятельно приготовить облегченный раствор. При этом не будет потеряна прочность материала. А бетона для такой заливки потребуется меньше, что поможет сэкономить.
Облегчить стяжку можно при помощи следующих материалов:
- Керамзит;
- Вермикулит;
- Перлит.
Керамзит – это глиняные гранулы овальной формы. При этом они имеют множество пор и разных размеров. Ели его добавить в раствор, то получится керамзитобетон. Бетонная стяжка на керамзитовой подушке помогает поднять уровень пола.
Вермикулит – слоистый натуральный материал. Он достаточно прочный благодаря серебряным нитям в своей структуре. Обычно используют вспученный материал.
Вермикулит имеет высокие впитывающие качества. 100 г вещества может поглотить в 4 раза больше воды. Благодаря этому раствор получается максимально однородным.
При использовании перлита его нужно нагреть до температуры 1000 градусов. На вид перлит напоминает щебень. Он обеспечивает хорошую звукоизоляцию и хорошо утепляет пол.
Расход цемента для фундамента
Связующее – самый дорогой компонент смеси для заливки бетонного основания. Именно расход цемента прямо определяет смету для фундамента – затраты на заполнители невелики.
А вы знаете: Пропорции бетона: как правильно замесить
Расчет можно выполнить разными способами:
- при помощи различных калькуляторов – относительно точный способ узнать, сколько необходимо цемента: при разработке калькуляторов могут приниматься некоторые допущения;
- вручную при помощи справочных таблиц пропорций смеси – расчет сложнее, но точность выше.
Из таблиц можно взять и готовый расход – наполнители здесь почти не учитываются, зато примерные затраты можно узнать буквально в 2 шага:
Шаг 1. Выбрать марку раствора «на выходе». Для заливки основания обычно используют бетон М200–М300. М100 подойдет для одноэтажных легких зданий, а хозпостройка с деревянными стенами выдержит основание из М50.
Шаг 2. Выбрать марку цемента. Для бетона универсальных вариантов два – М400 и М500.
Теперь, когда марки выбраны, несложно ответить на главный вопрос.
Сколько кг цемента в 1 м3 раствора
Справочные данные позволяют узнать расход сразу – из таблицы выше видно, что на 1 м3 бетонного раствора М150 нужно 235 кг связующего марки 400. Соответственно, в 1 м3 бетона около 5 мешков цемента.
Если закуплен «пятисотый» цемент, можно взять норму расхода для М400 и вычесть 30–40 кг. Это «допущение» подтверждает следующая таблица:
Несколько правил для расчета каждого материала, необходимого для замеса бетона
- Масса цементного песка в бетоне влияет на подвижность будущей постройки. Следовательно, допустимая погрешность, при замере пропорций цементного пека, равна не больше 1 килограмма. Что касается гравийного материала, здесь погрешность допускается до пяти килограмм.
- Если положить, слишком мало цементного песка, он плохо свяжет другие компоненты бетонного раствора. А после высыхания конструкция, из-за влияния морозов и осадков простоит лишь сезон. Вывод, лучше пересыпать цемента, чем потом из-за нехватки связующего материала все перестраивать.
- При расчетах необходимых пропорций нужно учитывать марку используемого цемента. Для любой маркировки бетона нужно использовать цемент, чьи показатели в два раза выше необходимых. Тогда готовый бетонный раствор будет необходимого вам качества.
- Разумеется, прочность бетона учитывается при планировке постройки конструкций. Будет ли бетонной только основа здания или стены тоже. В первом случае можно использовать цемент марки М300, во втором лучше применять М400.
- Также бетонный раствор разделяется на области применения смеси. И для каждой используются свои пропорции, поэтому и маркировок бетона много, и при строительстве применяется определенная. Например:
- заливка фундаментного основания;
- для постройки бетонных стен здания;
- укладка дорожек;
- постройка мостов;
- заливка монолитных стен;
- половая и потолочная стяжка;
- отливка блоков, балок или колонн.
Всего составных частей в бетонном растворе девять, они меряются в смеси, определенными порциями, 135. Одна часть это цементный песок, три мерные части обычного песка, и пять – гравия.
Опытные застройщики советуют исключить ошибки за счет индивидуальной мерки каждой части в бетонную смесь, благодаря этому вы избежите некачественного конечного продукта. Расход цемента на 1 куб раствора для стяжки измеряется чуть иначе, без добавления гравия. Стоит учесть будущее использование помещения.
Средняя мера на 1 м3 бетона – 350 кг цемента, то есть 7 мешков. Только высчитывайте пропорции, ориентируясь на будущее использование конструкции.
В раствор бетона также могут добавляться и дополнительные пластификаторы, основная функция которых усилить прочность итоговой конструкции. Еще одним важным правилом являются характеристики используемых материалов.
У цемента учитываются:
- время схватывания;
- вес;
- объем;
- активность состава;
- плотность;
- удельный вес.
У бетонного раствора учитываются:
- прочность;
- подвижность;
- объем;
- водонепроницаемость;
- водоотделение.
К песку предъявляются следующие требования:
- влажность;
- объем;
- вес;
- насыпная плотность;
- количество посторонних примесей;
- размер песчинок;
- удельный вес.
К гравию:
- влажность;
- прочность;
- вес;
- форма;
- плотность.
Придерживаясь данных правил, вы с легкостью проведете все работы самостоятельно, хотя помощь никогда не помешает.
Расход цемента для кладки
Ходовые марки кладочных растворов – 25–100. «Универсальный» вариант – марка 75 с пропорцией Ц:П равной примерно 1:4.
Этих данных достаточно, чтобы узнать, сколько цемента потребуется для кладки – в одном кубе раствора 1/5 (0,2) м3 связующего. Песка нужно 4/5 (0,8) м3. Для расчета нужно принять усредненные плотности:
- цемента – 1400 кг/м3;
- песка – 1600 кг/м3.
Зная плотность и объем, рассчитывают массу в кг:
- 0,2*1400 = 280;
- 0,8*1600 = 1280.
Пример: рассчитать расход на стену толщиной в полтора кирпича. Размер здания – 10 на 14 м, высота стен – 3 м. Алгоритм расчета следующий:
- Определить расход по таблице – 0,234 м3 раствора на 1 куб. м кладки.
- Рассчитать массу цемента на м3 кладки 0,221*280 = 65,5 кг.
- Посчитать объем кладки – периметр стен*высоту*толщину. Объем равен (10+10+14+14)*3*0,38 = 55 м3.
- Узнать общий расход на стены: 55*65,5 = 3603 кг (72 мешков по 50 кг).
В кладочные смеси часто вводят известь, органические и неорганические добавки. Приготовление такого раствора потребует меньшего количества цемента на 1 куб.
Необходимые условия: как сделать стяжку пола
Перед заливкой нужно позаботиться о подготовительных работах самой основы. Нужно избавиться от глубоких ям, щелей и неровностях. Само помещение не должно иметь сквозняков. Также нужно гидроизолировать пол, выполнить армирование и утепление.
Перед тем как делать стяжку пола, следует тщательно обработать поверхность, вымыть ее от пыли и грязи
Порядок подготовки:
- Нужно сделать разводку, установить коммуникации;
- Очистить основу от грязи и пыли;
- Сделать разметку нулевого уровня;
- Основание следует обработать грунтовкой и дать время просохнуть.
Для частного дома потребуется утрамбовать почву и выровнять ее. Для этого нужен щебень и песок, который должен быть мокрым. И только после этого нужно с
разметку, гидроизоляцию и каркас.
Когда черновой пол в хорошем состоянии, то нужно понадобиться только тонкая стяжка. Выход коммуникаций необходимо обработать герметиком. Вдоль стен придется наклеить специальную ленту. Утеплитель используется только при желании хозяев.
Расход цемента для стяжки
Принцип расчета аналогичен предыдущим. В первую очередь нужно выбрать смесь, исходя из требований к покрытию, временных рамок и метода укладки (мокрая, полусухая, сухая).
А вы знаете: Цемент марки М500: как выбрать и характеристики
Выбрав тип смеси, подсчитывают, сколько нужно песка и цемента, действуя по плану:
Узнать объем работ. Пример: комната площадью 15 м2, толщина стяжки – 35 мм. Объем составит 12*0,03 = 0,53 м3.
Выбрать из табличных нормативов, сколько «пятисотого» цемента надо на 1 куб смеси М200 – это 410 кг.
Посчитать, сколько цемента надо для всей стяжки пола. Зная затраты на куб, получают общую массу 410*0,53= 217 кг – потребуется 5 мешков.
Рассчитать затраты песка на стяжку нужного объема. Согласно таблице пропорции Ц:П равны 1:3, объем песка равен 0,53*0,75 = 0,4 м3. Зная плотность заполнителя (1600 кг/м3), легко узнать массу: 0,4*1600 = 640 кг.
Для сухой смеси
При использовании сухих и полусухих смесей для организации стяжки, необходимо принимать во внимание характеристики для каждой конкретной смеси, которые можно найти на упаковке. Обычно указывают объем смеси для закрытия одного квадратного метра основания слоем в 1 мм. Например, для получения раствора марки М100, достаточного для использования внутри жилых помещений, производитель полусухой стяжки для пола рекомендует такой расход:
- расход смеси 2 кг на квадратный метр при толщине стяжки 1 мм;
- расход воды 0,22 л на один 1 кг смеси.
Учитывая перечисленные данные, можно выполнить расчет необходимого материала для 30 квадратных метров с толщиной стяжки в 40 мм.
Необходимо площадь умножить на расход смеси на 1 м2 и на 4 (так как планируемая толщина стяжки 4 мм, а расчет приведен для толщины в 1 мм). Получаем: 30х2х4=120 кг, при этом объем воды потребуется: 120 кг х 0,22 л= 26,4 литра.
Строительный раствор М-150 (B12)
Завод бетонной продукции «Брестон» рад предложить раствор кладочный М150 собственного производства, изготовленный на базе экологически чистых материалов согласно санитарно-эпидемиологическим нормам и стандартам ГОСТ. Мы осуществляем круглосуточную доставку нашей бетонной продукции по Москве и области без выходных дней.
Цементный раствор М150 – это строительная растворная смесь, которую используют в кладочной и штукатурной работе. Раствор кладочный М150 относят к простым растворам с классом прочности В12. М150 включает в себя воду, наполнитель и вяжущее вещество — портландцемент. В качестве наполнителя используется строительный песок.
При необходимости повышение морозостойкости, подвижности, водонепроницаемости и удобоукладываемости растворной смеси М150 производится за счет ввода в раствор добавок, присадок и пластификаторов.Для понижения таких параметров, как схватываемость смеси при транспортировке и отвердение в раствор кладочный М150 добавляют замедлители. В продаже раствор готовый кладочный представлен техническими характеристиками – М-150 Пк4 F50.
Стоимость строительного раствора М150 можно посмотреть на странице каталога. Помните, что на цементный раствор М150 цена в каталоге указана без учета доставки смеси на строительную площадку.
Ищите, где купить цементный раствор с круглосуточной доставкой?!
Подайте заявку менеджерам «Брестон» на сайте через форму заказ
Особенности проведения вычислений
При приготовлении смеси, предназначенной для заливки стяжки, такой как на фото, специалисты рекомендуют соблюдать определенное соотношение цемента и наполнителя — 1:3. Но при проведении ремонта в жилых домах используют состав, в котором эти компоненты смешивают в пропорции 1:4, причем подразумевается не вес материалов, а их объем.
Как правило, невозможно достаточно точно рассчитать высоту стяжки, поскольку в разных местах поверхности чернового пола она будет отличаться (подробнее: «Как рассчитать стяжку пола – сколько материалов нужно»). По этой причине, чтобы упростить расчет раствора для стяжки учитывают параметры максимального бетонного слоя.
Даже, если известны точная площадь поверхности пола и компоненты раствора, определить объем связующей жидкости всегда проблематично. Дело в том, что цемент продается в торговой сети в мешках, а отсев и песок реализуют в килограммах.
Принято считать, что конкретная марка цемента, используемого при обустройстве стяжки пола, имеет определенный вес. Например, куб цемента условно весит 1300 килограммов. Этот показатель при проведении расчетов для определения, сколько цемента нужно на куб стяжки, применяют в качестве постоянной величины.
Расход цементаПрофессионалы рекомендуют: если даже известно точное количество стройматериалов, их следует покупать с 10-процентным запасом, чтобы в процессе заливки не допустить нехватки компонентов.
в ПКЦ 1:5:10 и М5
расход цемента в ПКК 1:5:10 и М5, Как рассчитать количество цемента в ПКК, в этой теме мы знаем как рассчитать количество цемента в ПКК и расход цемента в ПКК 1:5:10 .Мы знаем, что у нас есть несколько марок бетона , таких как M5, M7.5, M10, M15, M20 и M25 и т. д., и обсуждаем водоцементное отношение для марки бетона m5
.Обычно PCC обозначает простой цементный бетон, который состоит из смеси цементного песка и заполнителя в фиксированной пропорции.PCC обычно изготавливается из тощего бетона и обычного бетона.
Как правило, тощий бетон и обычный бетон используются для выравнивания слоев основания и устройства бетонных дорог и тротуаров.
Какие типы бетона для ПКК?Существует два типа бетона для тощего бетона PCC и обычного бетона
что такое тощий бетон?Марка бетона, в которой количество цемента ниже, чем количество жидкости, присутствующей в пластах, называется тощим бетоном.
Обычно в качестве тощего бетона используется бетон марки М5 и М7,5. Его основное применение заключается в обеспечении однородной поверхности фундамента, что предотвращает прямой контакт фундамента с грунтом.
что такое обычный бетон?PCC, который изготовлен из бетона марок M10 и M15, известного как обычный бетон, в смеси которого присутствует среднее количество цемента. Его основная функция заключается в создании подстилки для фундамента и устройства бетонной дороги и тротуара.
расход цемента в ПКЦ 1:5:10 и М5 Марка бетона М5в м5 марка бетона М обозначает смесь, а числовая цифра 5 обозначает прочность на сжатие куба размером 150 мм после 28 дней твердения.2, а соотношение смеси в бетоне марки m5 составляет около 1:5:10, в котором одна часть составляет цемент, 5 часть — песок, а 10 часть — заполнитель.
Расход цемента в ПКК 1:5:10Соотношение бетона M5: — M обозначает смесь, а числовая цифра 5 — прочность бетона на сжатие составляет 5 Н/мм2 для времени отверждения 28 дней, а соотношение бетона M5 составляет 1 : 5 : 10, смесь цемента, песка и заполнителя, в которой часть цемента, 5 частей песка и 10 частей заполнителя или каменной смеси с водой.
Предположим, у нас есть проект устройства бетонного покрытия площадью 100 м2 и толщиной плиты ПКК 150 мм.
Площадь = 100 кв.м
Толщина = 150 мм = 0,15 м
Влажный объем бетона = 100 м2×0,15 м
Wv = влажный объем = 15 м2
Теперь нам нужно рассчитать сухой объем. Рассчитывая сухой объем, мы должны умножить коэффициент 1,54 на влажный объем.
Сухой объем бетона = 15м2×1,54
Сухой объем = 23,1 м2
Соотношение смеси для марки М5 = 1:5:10 1 часть цемента, 5 частей песка и 10 частей заполнителя.
Общая пропорция = 1+5+10=16
Часть комментария =1/16
Часть песка = 5/16
Часть агрегата = 10/16
расчет количества расхода цемента в процентах 1:5:10Вес = объем × плотность
Плотность цемента = 1440 кг/м3
Сухой объем = 23,1 м3
Вес одного мешка цемента = 50 кг
Часть цемента в смеси =1/16
Вес = (1/16) 23,1 м3×1440 кг/м3
Вес цемента = 2079 кг
мешка цемента = 2079/50= 41.6 пакетов
41,6 мешка (2079 кг) расход цемента в процентах 1:5:10 на 100 м2 и толщину бетонной плиты 150 мм.
расход песка в РСС 1:5:10Часть песка в смеси = 5/16
1 м3 = 35,32 куб.фута
Сухой объем = 23,1 м3
Объем песка = (5/16)×23,1×35,32 куб.фута
Объем песка = 255 куб. футов
если одна тележка трактора имеет = прибл. =80 куб. футов
Чем нет. тракторной тележки песка
= 255/80 = 3.19 =3,19 тракторная тележка для песка
Расход песка 255 куб. футов (3,19 тракторной тележки) в пропорции 1:5:10 на 100 м2 и толщину бетонной плиты 150 мм.
Суммарный расход в процентах 1:5:10Часть заполнителя в смеси = 10/16
1 м3 = 35,32 куб.фута
Сухой объем = 23,1 м3
Объем заполнителя = (10/16)×23,1×35,32 куб.фута
Объем песка = 510 куб. футов
если одна тележка трактора имеет = прибл. =80 куб. футов
Чем нет.тракторной тележки агрегата
= 510/80 =6,38 =6,38 тракторная тележка агрегат
510 кубических футов (6,38 тележки трактора) расход заполнителя в ПКК 1:5:10 для 100 м2 и гладкой бетонной плиты толщиной 150 мм.
41,6 мешка (2079 кг) цемента, 255 кубических футов (3,19 тракторной тележки) песка и 510 кубических футов (6,38 тракторной тележки) расход заполнителей в ПКК 1:5:10 для 100 м2 и толщиной 150 мм гладкой бетонной плиты.
◆Вы можете подписаться на меня в Facebook и подписаться на наш канал Youtube
Вам также следует посетить:-
1) рассчитать собственную нагрузку колонны
2) расчет собственной нагрузки балки на метр
3) расчет нагрузки плиты на квадратный метр
4) расчет статической нагрузки кирпичной стены на метр
5) предельная несущая способность колонны
водоцементное отношение для бетона марки m5Соотношение воды и цемента известно как водоцементное отношение, которое составляет около 60 литров на мешок цемента для бетона марки m5
Требуется 1 мешок цемента = 60 литров воды
41.6 пакетов = 41,6×60= 2496 литров воды
Таким образом, требуемый расход воды в пропорции 1:5:10 составляет примерно 2496 литров воды на 100 м2 при толщине плиты 150 мм.
Расход цементав ПКЦ 1:3:6 и М10
расход цемента в КПЦ 1:3:6, Как рассчитать количество цемента в КПЦ, в этой теме мы знаем как рассчитать количество цемента в КПЦ и расход цемента в КПЦ 1:3:6.we Знайте, что у нас есть несколько марок бетона , таких как М5, М7.5, М10, М15, М20 и М25 и так далее- и водоцементного отношения для бетона марки М10.
Обычно PCC обозначает простой цементный бетон, который состоит из смеси цементного песка и заполнителя в фиксированной пропорции. PCC обычно изготавливается из тощего бетона и обычного бетона. Как правило, тощий бетон и обычный бетон используются для выравнивания подстилающего слоя для основания и устройства бетонных дорог и тротуаров.
Типы простого цементного бетона (PCC)?Существует два типа простого цементного бетона: тощий бетон и обычный простой цементный бетон
что такое тощий бетон?Марка бетона, в которой количество цемента ниже, чем количество жидкости, присутствующей в пластах, называется тощим бетоном.Обычно в качестве тощего бетона используют бетон марок М5 и М7,5. Его основное применение заключается в обеспечении однородной поверхности фундамента, что предотвращает прямой контакт фундамента с грунтом.
обычный бетонPCC, который изготовлен из бетона марок M10 и M15, известного как обычный бетон, в смеси которого присутствует среднее количество цемента. Его основная функция заключается в создании подстилки для фундамента и устройства бетонной дороги и тротуара.
расход цемента в ПКК 1:3:6 Марка бетона М10в м10 марка бетона М обозначает смесь, а числовая цифра 10 обозначает прочность на сжатие куба размером 150 мм после 28 дней твердения.2, а соотношение смеси в бетоне марки m10 составляет около 1:3:6, в котором одна часть составляет цемент, 3 части — песок и 6 частей — заполнитель.
Расход цемента в ПКК 1:3:6Предположим, у нас есть проект устройства бетонного покрытия площадью 100 м2 и толщиной плиты ПКК 150 мм.
Площадь = 100 кв.м
Толщина = 150 мм = 0,15 м
Влажный объем бетона = 100 м2×0,15 м
Wv = влажный объем = 15 м2
Теперь нам нужно рассчитать сухой объем. Рассчитывая сухой объем, мы должны умножить коэффициент на 1.54 во влажном объеме.
Сухой объем бетона = 15м2×1,54
Сухой объем = 23,1 м2
Соотношение смеси для марки М10 = 1:3:6 1 часть цемента, 3 части песка и 6 частей заполнителя.
Общая пропорция = 1+3+6=10
Часть комментария =1/10
Часть песка = 3/10
Часть агрегата = 6/10
расчет количества расхода цемента в пкм 1:3:6Вес = объем × плотность
Плотность цемента = 1440 кг/м3
Сухой объем = 23.1м3
Вес одного мешка цемента = 50 кг
Часть цемента в смеси = 1/10
Вес = (1/10) 23,1 м3×1440 кг/м3
Вес цемента = 3326,4 кг
Мешки цемента = 3326,4/50= 66,5 мешка
66,5 мешков (3326,4 кг) расход цемента в ПКК 1:3:6 на 100 м2 и толщину 150 мм плиты ПКК.
расход песка в РСС 1:3:6Часть песка в смеси = 3/10
1 м3 = 35,32 куб.фута
Сухой объем =23.1 м3
Объем песка = (3/10)×23,1×35,32 куб.фута
Объем песка = 244,8 куб.фута
если одна тележка трактора имеет = прибл. =80 куб. футов
Чем нет. тракторной тележки песка
= 244,8/80 =2,91 =3 тракторная тележка для песка
244,8 кубических фута (3 тележки трактора) Расход песка в pcc 1:3:6 для 100 м2 и плиты pcc толщиной 150 мм.
Суммарный расход в процентах 1:3:6Часть заполнителя в смеси = 6/10
1м3 = 35.32 куб. фута
Сухой объем = 23,1 м3
Объем заполнителя = (6/10)×23,1×35,32 куб.фута
Объем заполнителей = 489,5 куб. футов
если одна тележка трактора имеет = прибл. =80 куб. футов
Чем нет. тракторной тележки агрегата
= 489,5/80 =5,83 =6,1 тракторная тележка агрегат
489,5 кубических футов (6 тракторных тележек) расход заполнителя в pcc 1:3:6 для 100 м2 и плиты pcc толщиной 150 мм.
66,5 мешков (3326,4 кг) цемента, 244,8 кубических футов (3 тракторные тележки) песка и 489.Расход заполнителя 5 куб. футов (6 тракторных тележек) в pcc 1:3:6 для 100 м2 и толщины 150 мм плиты pcc.
◆Вы можете подписаться на меня в Facebook и подписаться на наш канал Youtube
Вам также следует посетить:-
1) рассчитать собственную нагрузку колонны
2) расчет собственной нагрузки балки на метр
3) расчет нагрузки плиты на квадратный метр
4) расчет статической нагрузки кирпичной стены на метр
5) предельная несущая способность колонны
Водоцементное отношение для бетона марки М10Соотношение воды и цемента известно как водоцементное отношение, которое составляет около 34 литров на мешок цемента для бетона марки М10
.Требуется 1 мешок цемента = 34 литра воды
66.5 мешков = 66,5×34= 2261 литр воды
Таким образом, требуемый расход воды в пропорции 1:3:6 составляет примерно 2261 л воды на 100 м2 при толщине плиты 150 мм.
Связь между потреблением цемента и ВВП на душу населения. Источник:…
Контекст 1
… 2005 г. до 3,5 Гт к 2020 г. [2], затем 3,7-4,4 Гт к 2050 г. [3]. Мировой спрос на цемент в 2005 г. составлял около 2,3 Гт, при этом на Китай приходилось более 1 Гт (47% от общего объема). Ожидаемый спрос на 2020 и 2050 годы в целом увеличится, но может снизиться в некоторых странах мира.Спрос на цемент на душу населения имеет форму колоколообразной кривой, как показано на рис. 1. Некоторые развивающиеся и развивающиеся страны в фазе быстрого роста потребляют большое количество цемента из-за своих потребностей в инфраструктуре, в то время как транзитные и развитые страны определенно будут следовать тенденция снижения цемента …
Контекст 2
… к концу 2012 года мы закончили отбор проб 289 линий по производству цемента в 18 провинциях Китая (рис. 10). Известняк, глину, сланец, летучую золу, уголь, сырьевую муку, клинкер и цемент собирали в разных точках шпателем из нержавеющей стали.В 16 провинциях было собрано 685 образцов 144 производственных линий NSP. 314 образцов 67 производственных линий шахтных печей в 13 провинциях и 378 образцов 78 специальных цементных и/или помольных станций …
Контекст 3
… производство клинкера, коэффициент выбросов, связанных с процессом, составляет 62 % (или 522,84 кг CO 2 /т клинкера) от общих выбросов в случае A и 56 % (или 472,11 кг CO 2 /т) в случае C по сравнению с самым низким уровнем 25 % (или 252,95 кг CO 2 /т) в случае Б (рис.11). Это связано с тем, что известняк является основным сырьем, используемым в сырьевой муке в случаях A и C, но в случае B используется небольшое количество извести (45%, как показано в таблице 7). В целом можно утверждать, что как в процессе NSP, так и в шахтной печи преобладают выбросы, связанные с процессом, на уровне более 50% в целом. Мы также нашли …
Контекст 4
… только Всего выборок Группа Группа Группа Группа Выборки Группа Ляонин 7 41 5 31 12 72 Сычуань 10 54 3 18 4 20 17 92 Синьцзян 6 35 2 10 6 20 14 исследований указывают на то, что доля коэффициентов выбросов, связанных с процессом, составляет 58% для P.Цемент O.42.5 в случае A и 52% для P.O. 32,5 цемента в случае C, в то время как только 24% для алюминатного цемента в случае B (рис. 12). Это означает, что цемент с более высокой маркировкой имеет относительно более высокие коэффициенты выбросов, чем цемент с более низкой маркировкой. Мы также обнаружили, что определенные виды цемента выделяют больше CO 2 , чем обычные, потому что в их сырой муке преобладает известь. Точно так же и в процессе NSP, и в процессе шахтной печи доминируют связанные с процессом …
Контекст 5
… сравните наши коэффициенты выбросов CO 2 со значениями по умолчанию IPCC и CSI, мы выбрали два примера в Китае с суточной производительностью 2500 т и 5000 т для производства клинкера и цемента (рис. 13). Можно обнаружить, что различия коэффициентов выбросов клинкера между нашими результатами и значениями по умолчанию МГЭИК попадают в диапазон 10,90-13,19%, а более высокий диапазон неопределенности составляет 20,13-20,85% для цемента …
Мировое потребление цемента растет на 2,8% в 2019 году
Мировое потребление цемента выросло на 2.й Версия . Рост спроса во многом объясняется расширением китайского рынок цемента в 2019 году, который, по оценкам, достиг 2,28 млрд тонн, что на 4,9% больше, чем в годом ранее и составляет 56 процентов мирового потребления. За исключением Китая, мировое потребление цемента, по оценкам, осталось на прежнем уровне. до 1,81 млрд, увеличившись всего на 0,3% в годовом исчислении. Рост на втором по величине рынке в мире, Индии, оказался слабее, чем ожидалось. на три процента в 2019 году, но это отражало прочную основу для сравнения с годом ранее, когда годовой прирост превысил 15 процентов.В США спрос, по оценкам, увеличился на 2,1% в 2019 году. подтолкнув общее потребление к отметке в 100 млн тонн впервые с 2007 г., который стал отправной точкой обвала рынка во время Великая рецессия. По регионам самые высокие темпы роста были зарегистрированы в странах Африки к югу от Сахары на уровне 5-6 процентов, хотя совокупный регион производит всего 101 млн тонн цемента. потребление – равно всему США. В расчете на душу населения страны к югу от Сахары Африканские страны имеют одни из самых низких уровней потребления в мире.TM , 13-е издание уже доступно для покупки. Обзор и содержание отчета Этот 372-страничный отчет, полностью переработанный с учетом новых данных за период 2008-20F гг. предоставляет данные о потреблении и производстве цемента, импорте и экспорте статистика, а также свежая информация о ценах и новых заводских проектах – все в известном формате по странам. Обзор мира Комментарий с ключевыми диаграммами и таблицами: 1. Мировое потребление цемента, производство, загрузка мощностей и торговля уровни (2010-2020F) 2.Доли регионов в мировом потреблении цемента, 2018 г. 3. Основные страны-потребители цемента (2016-20F) 4. Производственные мощности основных производителей цемента, 2018 г. 5. Ведущие страны-экспортеры цемента и клинкера, 2016–2018 гг. 6. Ведущие страны-импортеры цемента и клинкера, 2016–2018 гг. Профили компаний 1. Лафарж Холсим 2. ХайдельбергЦемент 3. Цемекс 4. Аньхойская раковина 5. Ультратехнический цемент 6. Воторантим Чиментос 7. Цемент Данготе Профили стран * Комментарий о потреблении цемента и строительной деятельности, производстве и новые мощности, торговля цементом и клинкером, цены и перспективы отрасли * Статистические данные (2008-20F): потребление (млн тонн), производство (млн тонн), экспорт (млн тонн), импорт (млн т), мощность (млн т), потребление цемента на душу населения (кг) Страны, охваченные отчетом: Афганистан, Албания, Алжир, Ангола, Аргентина, Армения, Австралия, Австрия, Азербайджан, Бахрейн, Бангладеш, Беларусь, Бельгия, Белиз, Бенин, Бутан, Боливия, Босния и Герцеговина, Ботсвана, Бразилия, Бруней-Даруссалам, Болгария, Буркина-Фасо, Бурунди, Кабо-Верде, Камбоджа, Камерун, Канада, Карибский бассейн, Чад, Чили, Китай, Колумбия, Коморские Острова, Конго – Демократическая Республика, Конго – Республика, Коста-Рика, Кот-д'Ивуар, Хорватия, Куба, Кипр, Чехия, Дания, Джибути, Эквадор, Египет, Сальвадор, Экваториальная Гвинея, Эритрея, Эстония, Эсватини, Эфиопия, Фиджи, Финляндия, Франция, Габон, Гамбия, Грузия, Германия, Гана, Греция, Гватемала, Гвинея, Гвинея-Бисау, Гондурас, Гонконг, Венгрия, Исландия, Индия, Индонезия, Иран, Ирак, Ирландия, Израиль, Италия, Япония, Иордания, Казахстан, Кения, Косово, Кувейт, Кыргызская Республика, Лаос, Латвия, Ливан, Лесото, Либерия, Ливия, Литва, Люксембург, Макао, Мадагаскар, Малави, Малайзия, Мали, Мальта, Мавритания, Маврикий, Мексика, Молдова, Монголия, Черногория, Марокко, Мозамбик, Мьянма, Намибия, Непал, Нидерланды, Новая Зеландия, Никарагуа, Нигер, Нигерия, Северная Корея, Северная Македония, Норвегия, Оман, Пакистан, Палестина, Панама, Папуа-Новая Гвинея, Парагвай, Перу, Филиппины, Польша, Португалия, Пуэрто-Рико, Катар, Реюньон, Румыния, Россия, Руанда, Саудовская Аравия, Сенегал, Сербия, Сейшельские острова, Сьерра Леоне, Сингапур, Словакия, Словения, Сомали, Южная Африка, Южная Корея, Южный Судан, Испания, Шри-Ланка, Судан, Суринам, Швеция, Швейцария, Сирия, Тайвань, Таджикистан, Танзания, Таиланд, Тимор-Лешти, Того, Тунис, Турция, Туркменистан, Уганда, Украина, Объединенные Арабские Эмираты, Великобритания, Объединенные Штаты Америки, Уругвай, Узбекистан, Венесуэла, Вьетнам, Йемен, Замбия, Зимбабве.торговое судно th Edition Publications Ltd, Великобритания Электронная почта: [email protected] Ссылки по теме: http://www.CemNet.com/GCR13 Контакт: Контакт для СМИ: Тел: +44-(0)-1306-740-363
До того, как он появится здесь, он находится на терминале Блумберг.
ВЫУЧИТЬ БОЛЬШЕСколько мешков цемента на квадратный метр для штукатурки | Цементная штукатурка | Соотношение цементного раствора | Штукатурные работы
Штукатурные работы-
Штукатурка представляет собой тонкий слой раствора, наносимый на поверхность кирпичной кладки и выполняющий роль влагонепроницаемого слоя поверх кирпичной кладки.Штукатурка также обеспечивает готовую поверхность над каменной кладкой, которая является прочной и гладкой, что улучшает внешний вид здания.
Цементная штукатурка-
Цементная штукатурка представляет собой смесь воды, мелких заполнителей и портландцемента . Цемент и песок смешивают в разных количествах для получения цементной штукатурки . Для внутренних стен обычно достаточно одного слоя штукатурки , чтобы получить красивую поверхность.
Толщина штукатурки —
Рекомендуемая толщина штукатурки для кирпичных стен: 12 мм , 15 мм или 20 мм . 12 MM толстая цементная штукатурка выполняется там, где оштукатурена ровная поверхность кирпичной кладки. Цементная штукатурка 15 MM требуется на шероховатой стороне стены толщиной 9 дюймов и 4,5 дюйма.
Читайте также: Что такое гипс | Методы оштукатуривания
Соотношение цементного раствора-
Соотношение цементной смеси и раствора | Рекомендуется для общего применения |
1:3 | Очень богатая растворная смесь.Не рекомендуется для общего использования на сайтах. Может действовать как ремонтный раствор с гидроизоляционным/связующим веществом |
1:4 | Для наружной штукатурки и потолочной штукатурки |
1:5 | Раствор для кирпичной кладки и внутренней штукатурки (если песок не мелкий, модуль крупности > 3) |
1:6 | Для внутренней штукатурки (при наличии мелкого песка) |
Штукатурный расчет-
Шаг 1. Плотность цемента = 1440 кг/м 3 .
Этап 2. Плотность песка = 1450-1500 кг/м 3 .
Этап 3. Плотность заполнителя = 1450-1550 кг/м 3 .
Шаг 4. Сколько кг в 1 мешке цемента = 50 кг.
Этап 5. Количество цемента в литрах в 1 мешке цемента = 34,7 литра.
Шаг 6. 1 мешок цемента в кубических метрах = 0,0347 кубических метра .
Шаг 7. Сколько CFT (кубических футов) = 1,226 Cu.Ft.
Этап 8. Количество мешков в 1 куб. метр цемент = 28,8 мешков
Соотношение штукатурки потолка-
Соотношение цементной смеси и раствора | Рекомендуется для общего применения |
1:3 | Очень богатая растворная смесь. Не рекомендуется для общего использования на сайтах. Может действовать как ремонтный раствор с гидроизоляционным/связующим веществом |
1:4 | Для наружной штукатурки и потолочной штукатурки |
1:5 | Раствор для кирпичной кладки и внутренней штукатурки (если песок не мелкий, модуль крупности > 3) |
1:6 | Для внутренней штукатурки (при наличии мелкого песка) |
Читайте также: Что такое гипс | Виды штукатурки по материалу | Дефекты штукатурки
Расход цемента в штукатурке —
Расход цемента толщиной 12 мм штукатурка 1:4 на 1 м 2 штукатурка кирпичной стены 0.092 мешка (4,6 кг) цемент . Ответ: 4,6 кг (0,092 мешка), 46 кг (0,92 мешка) и 460 кг (9,2 мешка) составляют расход цемента и потребность в толщине 12 мм штукатурка 1:4 на 1 м 2 , 10 м 2 и 100 м 2 площадь кирпичной стены соответственно.
Соотношение цементного раствора для кирпичной кладки-
1:6 Соотношение цементного раствора обычно используется для кирпичной кладки. Чтобы рассчитать необходимое количество цемента, песка или раствора или кирпичной кладки, сначала узнайте количество раствора, необходимого для кирпичной кладки.После добавления воды в растворную смесь она набухает и уменьшается в объеме на 33% во влажном состоянии
Формула расчета цемента для штукатурки-
Этап 1. Плотность цемента = 1440 кг/м 3 .
Этап 2. Плотность песка = 1450-1500 кг/м 3 .
Этап 3. Плотность заполнителя = 1450-1550 кг/м 3 .
Шаг 4. Сколько кг в 1 мешке цемента = 50 кг.
Шаг 5. Количество цемента в литрах в 1 мешке цемента = 34,7 литра.
Шаг 6. 1 мешок цемента в кубических метрах = 0,0347 кубических метра .
Шаг 7. Сколько CFT (кубических футов) = 1,226 Cu.Ft.
Этап 8. Количество мешков в 1 куб. метр цемент = 28,8 мешков
Также прочтите: Что такое гипс | Гипсовое соотношение | История штукатурки | Требования Good Plaster
Как рассчитать количество штукатурки?
Шаг 1. Плотность цемента = 1440 кг/м 3 .
Этап 2. Плотность песка = 1450-1500 кг/м 3 .
Этап 3. Плотность заполнителя = 1450-1550 кг/м 3 .
Шаг 4. Сколько кг в 1 мешке цемента = 50 кг.
Этап 5. Количество цемента в литрах в 1 мешке цемента = 34,7 литра.
Шаг 6. 1 мешок цемента в кубических метрах = 0,0347 кубических метра .
Шаг 7. Сколько CFT (кубических футов) = 1,226 Cu.Ft.
Этап 8. Количество мешков в 1 куб. метр цемент = 28,8 мешков
Сколько песка и цемента для кирпичной кладки?
Соотношение 1:6 раствора для кирпичной кладки , что означает цемент : песок = 1 часть цемента и 6 частей песка .
Сколько цемента в 1 кубометре кирпичной кладки?
500 кирпичей, 1,26 мешка (63 кг) цемента , и 9.Для 1 кубометра кирпичной кладки требуется 28 куб. футов песка.
Как рассчитать расход цемента в кирпичной кладке?
Стандартный размер кирпича = 190 х 90 х 90 (мм) Проверка качества кирпича.
Толщина раствора = 10 мм.
Количество раствора – 0,2305 (влажное состояние), мы рассчитываем значение в сухом состоянии.
Объем = 0,306565x (1/7) = 0,0438.
Объем = 0,306565x (6/7) = 0,2627.
Также читайте: анализ скорости гипса
Сколько мешков цемента на квадратный метр для штукатурки?
0.Для оштукатуривания требуется 154 мешка цемента на квадратный метр при соотношении 20 гипса и цемента и песка 1:4.
Как рассчитать количество цементного песка для штукатурки?
- Плотность цемента = 1440 кг/м 3 .
- Плотность песка = 1450-1500 кг/м 3 .
- Плотность заполнителя = 1450-1550 кг/м 3
- Сколько кг в 1 мешке цемента = 50кг.
- Количество цемента в литрах в 1 мешке цемента = 34.7 литров.
- 1 мешок цемента в кубических метрах = 0,0347 кубических метра.
- Сколько CFT (кубических футов) = 1,226 Cu.Ft.
- Количество мешков в 1 кубометре цемента = 28,8 мешков
Как рассчитать количество цементного песка для кирпичной кладки?
- Стандартный размер кирпича = 190 x 90 x 90 (мм) Проверка качества кирпича.
- Раствор Толщина = 10 мм.
- Количество раствора составляет 0,2305 (влажное состояние), мы рассчитываем значение в сухом состоянии.
- Объем = 0,306565x (1/7) = 0,0438.
- Объем = 0,306565x (6/7) = 0,2627.
Как рассчитать количество цементного раствора в кирпичной кладке и штукатурке?
- Стандартный размер кирпича = 190 x 90 x 90 (мм) Проверка качества кирпича.
- Раствор Толщина = 10 мм.
- Количество раствора составляет 0,2305 (влажное состояние), мы рассчитываем значение в сухом состоянии.
- Объем = 0.306565x (1/7) = 0,0438.
- Объем = 0,306565x (6/7) = 0,2627.
Также прочтите: Что такое раствор | Как сделать миномет » вики полезно Как смешать миномет » вики полезно Использование раствора | Цементный раствор в строительстве
Как рассчитать количество цемента и песка, необходимое для штукатурки?
Шаг 1. Стандартный размер кирпича = 190 x 90 x 90 (мм) Проверка качества кирпича.
Шаг 2. Раствор Толщина = 10 мм.
Шаг 3. Количество раствора составляет 0,2305 (влажное состояние), мы вычисляем значение в сухом состоянии.
Шаг 4. Объем = 0,306565x (1/7) = 0,0438.
Шаг 5. Объем = 0,306565x (6/7) = 0,2627.
2 Департамент экономики и Санкт-Петербурга.Екатерининский колледж, Оксфордский университет, Оксфорд OX2 6, Великобритания |
Расход материала для M10 (1:3:6)
(Часть-3)
М 10 (1:3:6) расход материала
Сухой бетон 52% экстра
цементобетон объем 1 м3
сухой объем = 1,52 м3
общий объем = 1+3+6 = 10
для цемента = (1/10)*1,52= 0,152 м3
для веса = 0.152 х 1440 (плотность) = 218,88 кг.
песок = (3/10)*1,52 = 0,456 м3
для веса = 0,456 x 1600 (плотность) = 729,6 кг.
Заполнитель = (6/10)*1,52 = 0,912 м3
для веса = 0,912 x 1600 (плотность) = 1459,2 кг
Плотность PCC = 2400
Теперь мы выполнили расчет всех материалов и сверили с плотностью PCC = 218,88 + 729.6 + 1459,2 = 2407,68 (хорошо)
Вы должны увидеть для анализа скорости часть-4
Количество и трудозатраты согласно спецификации.
Если вы хотите ВСЕ ТЫСЯЧИ АНАЛИЗ СТАВОК И ПОТРЕБЛЕНИЕ МАТЕРИАЛОВ в IS CODE, ПОЖАЛУЙСТА, ОТПРАВЬТЕ ВАШ ПОЧТОВЫЙ ID НА ДОМАШНЕЙ СТРАНИЦЕ и прокомментируйте свой почтовый идентификатор, чтобы я выслал вам копию.
как
1. Базовая норма материала,
2. Основная задача труда,
3.перевозка материалов,
4. земляные работы, раствор,
5. бетонные работы,
6. железобетонные работы,
7. кирпичные, каменные, мраморные и гранитные работы 8,404 ,
9.
9. Работа из дерева и ПВХ,
10. Стальные работы, настил,
11. Кровля, отделка,
12. Ремонт до зданий,
13. Разборка и снесение,
14.Дорожная работа,
15. Санитарные установки,
16. Водоснабжение,
17. Дренаж, ворс работы,
18. Алюминиевая работа,
19. Вода, дренаж,
20. Куча работа,
21. Алюминиевая работа,
22. Водозаконирование,
23. Уборка дождевых вод и трубы,
24. Сохранение здания наследия,
25.