Пропитка для дерева от влаги, описание пропитки для дерева от влаги и гниения
Древесина относится к лидерам среди материалов для строительства частных домов. Однако при всех своих преимуществах она имеет один недостаток – способность повреждаться и приходить в негодность под воздействием повышенной влажности. Предотвратить ее разрушение можно при помощи пропитки для дерева от влаги и гниения, которая позволяет сохранить первоначальные характеристики деревянных конструкций и значительно продлить срок их эксплуатации.
Для чего нужна пропитка для дерева от влаги?
Будучи натуральным материалом, дерево обладает природной гигроскопичностью и имеет свойство вбирать в себя влагу при контакте с талыми водами и атмосферными осадками. При повышении влажности древесины более чем на 15 % она начинает набухать, расслаиваться, терять свою форму. С течением времени на ней появляются плесень, грибки, развиваются процессы гниения, которые снижают долговечность и эстетику деревянных конструкций.
Современная пропитка для дерева от влаги наделяет изделия водоотталкивающими свойствами и помогает избежать их высокого увлажнения. Ее использование сводит к минимуму риски появления гнили, которая не просто портит внешний вид дерева, но и негативно сказывается на здоровье людей. Споры гнилостных образований способны попадать в лёгкие человека и провоцировать хронические болезни, поэтому защита древесины от чрезмерной влажности является важным этапом в создании благоприятного микроклимата в доме.
Причины ускоренного разрушения дерева
Деревья, произрастающие в природе, обладают надежной защитой в виде собственной древесной коры. При строительстве зданий или изготовлении различных изделий из дерева кора удаляется, что влечет за собой нарушение древесной структуры под негативным влиянием внешней среды. Если на конструкциях нет пропитки для дерева от влаги и гниения, то они разрушаются вследствие следующих факторов:
- Грибки и плесень – часто поражают древесину в условиях влажности и ограниченного доступа воздуха.
Дерево служит отличной питательной средой для вредных микроорганизмов, особенно если оно напитано влагой.
- Насекомые – наиболее распространенными врагами дерева являются жук-долгоносик, короед, древоточец, которые способны не только навредить древесине, но и полностью ее разрушить. Характерными признаками появления насекомых служат небольшие дырочки и канавки, видимые на деревянной поверхности.
- Влага – дожди, туманы, тающий снег, да и просто повышенная влажность внутри помещения приводят к разбуханию древесины и образованию трещин, а также благоприятствуют появлению гнили. Пропитка для дерева от воздействия влаги снижает водопоглощение материала, не влияя при этом на его способность «дышать».
В качестве дополнительных факторов, отрицательно воздействующих на дерево, стоит упомянуть ультрафиолетовые лучи, которые разрушают природное вещество лигнин, отвечающее за твердость и жесткость древесины. Под влиянием солнца деревянные изделия становятся более мягкими, теряют природный цвет и покрываются трещинами.
Виды средств для защиты дерева
Современный рынок предлагает потребителю качественные растворы, которые предотвращают процессы гниения и становятся надежной биологической защитой деревянных конструкций. Все пропитки для дерева от влаги и гниения могут различаться между собой в зависимости от состава и способов их применения:
- по месту обработки;
- по природе используемых растворителей;
- по характеру активного компонента.
По месту нанесения
Исходя их локализации обработки, пропитки бывают внутренними и внешними. Первые используются для проведения внутренних работ и отличаются экологической чистотой. Они мягко воздействуют на микроорганизмы и не наносят вреда здоровью человека. Внешние средства применяются для наружных работ и обеспечивают лучшую защиту для дерева, но отличаются более высокой токсичностью.
По активному компоненту
Главным действующим компонентом в пропитках для дерева от влияния влаги могут быть вещества органического и неорганического происхождения. Чаще всего составы изготавливаются на масляной основе, акрилате или алкидных смолах, а также на летучих химических компонентах, которые не могут проникнуть глубоко в дерево, но формируют прочную защитную пленку на его поверхности.
По растворителю
В зависимости от растворителя для пропиток смеси бывают водными и неводными. В первом случае активный компонент смешивается с водой, которая обеспечивает древесине хорошую смачиваемость пор. Что касается неводных смесей, то их разводят при помощи спирта или химических растворителей, которые при нанесении на поверхность быстро улетучиваются в атмосферу.
Если вам нужна надежная пропитка для дерева от влаги и гниения, подобрать необходимый материал можно в магазине «ТБМ-Маркет». В нашем каталоге представлены средства как для наружных, так и для внутренних работ, позволяющие обеспечить хорошую защиту для дерева на долгие годы.
Как подобрать эффективную пропитку для дерева от влаги?
Чтобы пропитка дала максимальный эффект, рекомендуется ознакомиться с характеристиками предлагаемых средств и подобрать именно тот материал, который лучше всего подходит конкретному типу деревянных конструкций и условиям их эксплуатации. К главным аспектам, на которые следует обратить внимание, относятся:
- глубина проникновения средства в древесину;
- экологическая безопасность пропитки для дерева от негативного воздействия влаги, наличие/отсутствие резкого запаха;
- место применения – для внешних или внутренних работ;
- степень действия состава на разные виды грибка, плесени и насекомых;
- расход материала – в среднем он должен составлять до 200–250 г/м²;
- срок действия смеси.
При покупке следует учитывать климатические условия местности. Если дом находится в областях с частыми атмосферными осадками, лучше всего выбирать пропитки, которые эффективно защищают дерево при резких перепадах температур. Для мест с повышенной влажностью желательно брать водоотталкивающий состав, основной функцией которого является защита дерева от влаги.
Правила обработки пропиткой для дерева от влаги
- Перед обработкой необходимо очистить древесину от пыли, жира или ранее нанесенных красок и лаков.
- Если на дереве уже заметны следы грибка, его нужно обработать щеткой с металлическими щетинками.
- Неотъемлемым этапом является тщательная сушка дерева, поскольку сухая древесина не так интенсивно впитывает влагу.
- Если пропитку для дерева от влаги нужно нанести в несколько слоев, то следует подождать высыхания каждого предыдущего слоя.
Когда использование пропиток особенно необходимо?
Поскольку древесина подвергается наибольшему повреждению в условиях повышенной влажности, применение антисептиков особенно важно в местах, где влага оказывает максимальное разрушительное воздействие. К таковым относятся подвальные помещения, бани и сауны, уличные беседки, садовая мебель, а также те части деревянных сооружений, которые имеют тесный контакт с землей.
Обработка такой поверхности может производиться как на этапе строительства, так и на готовых конструкциях. При помощи пропитки для дерева для защиты от влаги и гниения можно свести к минимуму появление грибка и плесневых пятен, избежать появления гнили и защитить деревянные материалы от разрушительной силы воды.
Как защитить дерево подручными средствами?
Существует немало подручных средств, которые вполне могут заменить магазинные растворы. Чаще всего для защиты дерева используют:
- силикатный (столярный) клей;
- раствор соды с уксусом;
- смолу;
медный купорос;- отработанное машинное масло;
- серную кислоту в сочетании с бихроматом калия;
- составы из борной кислоты, воды и соли.
Указанные варианты не так эффективны, как пропитка для дерева от влаги и гниения, поскольку препятствуют воздействию влаги только на короткое время. Если вы хотите получить длительный и действительно качественный эффект, оптимальным решением станет обращение в интернет-магазин «ТБМ-Маркет» и покупка надежных пропиток для древесины от европейских производителей.
Идеальная водоотталкивающая пропитка для дерева — знакомимся!
28.08.2018
Водоотталкивающая пропитка для дерева — Гидроэффект — защитит дерево от любой влаги!
Предлагаем клиентам отличное решение для защиты древесины в экстерьере и интерьере. Водоотталкивающая пропитка для дерева (гидрофобизатор) Гидроэффект — способна решить даже самые сложные задачи. Мало кто знает о гидрофобизаторе, но многие сталкиваются с задачей защитить дерево от влаги. У нас на сайте представлен самый качественный вариант гидрофобизатора за небольшие деньги.
Водоотталкивающая пропитка для дерева расходуется очень экономично, поэтому можно сказать, что даже при больших площадях затраты будут минимальные, а эффект долговечный.
При обработке поверхности пропитка законсервирует поверхность и защитит от капиллярного подъема влаги.
Водоотталкивающая пропитка для дерева проникает глубоко в структуру дерева создает защитную пленку. Разрушить ее можно только сильными механическими воздействиями на поверхность, поэтому продержится она на поверхности до момента разрушения самого дерева.
Характеристики водоотталкивающей пропитки для дерева:
- ✔ Экологически чистый — применяется внутри и снаружи помещения без ограничений!
- ✔ Стойкий к солнечному свету.
- ✔ Применят при температуре от — 60 до +200 градусов.
После нанесения на поверхность дерева можно наносить краску так как пропитка имеет высокую степень адгезии. Производитель гарантирует, что слой краски будет даже более долговечный. Почему так? Дело в том, что отшелушивание краски происходит от поверхности из-за воды, которая поступает из глубины материала. А гидрофобизатор надежно защищает поверхность от прохода влаги в обе стороны. После обработки дерева, если вы решили поменять экстерьер или интерьер, то любые манипуляции с обработанной поверхность можно производить и не бояться за результат.
Купить водоотталкивающую поверхность для дерева можно через сайт. Звоните по телефонам, уточняйте наличие: +37529-611-73-00
+375 29 611-73-00
+375 29 870-55-52
+375 17 508-74-87
+375 29 186-57-70 (б/н)
+375 29 168-73-67 (б/н)
+375 33 376-07-97
(отдел светильников)
E-mail: [email protected]
Магазин-склад
с 8:00 до 17:00,
Выходные дни — сб., вс.
Прием заказов через сайт — круглосуточно. Наличие товаров и цену уточняйте в отделе продаж!
Технология пропитки фанеры – ФронтСтрой
Для повышения устойчивости фанерного полотна к влаге, воздействию грибков, вредных микроорганизмов и плесени используются водоотталкивающие пропитки.
Дополнительная обработка потребуется в случае производства мебели для кухни или помещений с высокой влажностью. С помощью составов и лакокрасочных покрытий можно повысить стойкость полотна к воде и механическим повреждениям, придать поверхности требуемый цвет и дизайн.
Чем пропитать фанеру для повышения влагостойкости?
Для защиты фанеры используются разные покрытия, в зависимости от уровня исходной влагостойкости материала. Полностью устойчивые к воде полотна очень дорогие, поэтому многие производители мебели и домашние мастера решаются обработать дешевые сорта фанеры для снижения стоимости готовой продукции и повышения срока службы мебели. Для пропитки фанерного полотна можно выбрать следующие типы покрытий:
- Олифу – наиболее популярный и недорогой вариант, который подходит для обработки стандартной кухонной мебели;
- Стеклоткань – подходит для подготовки материала к окрашиванию эмалью;
- Нитрокраску – обычно используют для обработки покрытий, которые постоянно контактируют с водой;
- Краски и лаки, красящее масло для создания требуемого оттенка или же глянцевого блеска.
Как наносить влагозащитную пропитку на поверхность фанеры?
Обрабатывать специальными составами или лаками желательно уже готовые элементы конструкции – вырезанные по размерам и модификации детали. Лаки, краски и масла наносят кисточкой с тонким и мягким ворсом или же валиком. Для использования составов с жидкой текстурой допускается использование распылителя.
Любые виды пропиток наносятся на поверхность фанеры исключительно в направлении вдоль волокон. В момент обработки полотна желательно размещать в горизонтальном направлении. После обработки необходимо дать каждому слою высохнуть в течение минимум 10-12 часов.
Если же в процессе обработки на плитах появились следы лишнего лака или краски, их можно удалить мягкой ветошью. Грунтовать, красить и лакировать листы желательно с обеих сторон.
Четкое соблюдение технологии обработки фанеры позволяет получить изделие, которое гарантированно прослужит десятки лет без повреждений, появления плесени и грибков.
Чем обработать фанеру. Все способы защиты фанеры
Фанера – один из самых востребованных материалов в строительстве и при отделочных работах. Изготавливают его из древесины методом склеивания между собой слоев шпона таким образом, чтобы каждый последующий слой накладывался перпендикулярно направлению волокон предыдущего. Профессионалы ценят фанеру за универсальность в применении и доступность в цене. Главный недостаток – этот материал боится влаги. При неправильной обработке фанеры, отсыревшие слои распадаются, коробятся и, впоследствии, материал превращается в труху. Чем обработать фанеру, чтобы уберечь ее от быстрого износа — очень уместный вопрос, если вы решили сами выполнить все строительные работы. Существует несколько способов и средств для продления срока службы этого материала, о которых вы и узнаете из этой статьи.
Способы обработки
Чтобы защитить фанеру от быстрой порчи, ее необходимо оградить от пагубного воздействия внешней агрессивной среды. Для этого случая были задействованы материалы, которые способны обеспечить гидроизоляцию и уберечь от износа при перепадах температур.
Чем обработать фанеру:
- Стеклотканями.
- Лаком.
- Олифой.
- Краской.
Отдельный нюанс — больше всего подвержены пагубному воздействию влаги торцы фанерного листа. Они требуют особо тщательной обработки и дополнительной изоляции. Чтобы обеспечить таким местам защиту, выполняют такие работы:
- Шпаклевка.
- Оклеивания краев металлическим или пластиковым кантом.
- Обработка глубоко проникающими грунтовками.
- Применение густотертых красок.
Важно! Прежде, чем выбрать подходящий вам вариант защитной обработки фанеры, ознакомьтесь с плюсами и минусами каждого материала, его стоимостью и выясните, насколько проста технология нанесения. Только после этого примите окончательное решение.
Оклеивание стеклотканью
Такая гидроизоляция фанеры существенно увеличивает срок службы материала. Производится посредством нанесения на поверхность специальной стеклоткани. Если такой материал вам недоступен, вы можете использовать обыкновенную марлю. Приклеивается любой из этих материалов с помощью лака. Главное условие при выборе такого раствора — в нем не должно быть полиэфирных и эпоксидных компонентов.
Проводите работы со стеклотканью или марлей в такой последовательности:
- Покройте фанерный лист лаком.
- Дайте лаку впитаться в течение 3 часов.
- Нанесите на поверхность марлю или стеклоткань.
- Обработайте лаком торцы листа.
- Оставьте просушиваться на несколько дней.
- Когда вы убедитесь, что лак высох – повторно нанесите лак на всю поверхность фанеры.
- Просушите еще несколько дней.
Пропитка олифой
Самый популярный способ гидроизоляции фанеры – это обработка ее олифой. Она доступна по цене, продается в любом строительном магазине и в значительной мере увеличивает влагостойкость материала. Чтобы работа была более продуктивной, фанеру нужно пропитывать горячей олифой.
Работа состоит из таких этапов:
- Нагрейте олифу до 60 градусов на водяной бане.
- С помощью кисточки нанесите раствор на фанерный лист, уделяя особое внимание краям и торцу.
- Возьмите строительный фен и выполните принудительное просушивание поверхности. Если у вас нет фена — прогладьте фанеру утюгом, нагретым до 200 градусов.
- Убедитесь, что олифа полностью высохла, и нанесите еще один слой вещества.
- Наносите каждый слой до тех пор, пока олифа не перестанет впитываться.
Важно! После всех проведенных манипуляций фанерный лист готов к покраске и установке. Для удобства и качества нанесения обрабатывайте фанеру, которая находится в горизонтальном положении.
Окрашивание фанеры
Когда возникает вопрос, чем обработать фанеру от влаги, специалисты советуют покрывать ее лаком или краской. Эти материалы однозначно на порядок продлевают жизнь фанерному листу. Для проведения качественной работы, с использованием краски, вам понадобятся:
- наждачная бумага;
- шпаклевка;
- грунтовка для фанеры;
- кисточка, валик или пульверизатор;
- шпатель;
- краска для фанеры.
Выбор краски
Чтобы максимально продлить срок службы покрытия из этого материала, при выборе раствора для обработки учитывайте следующие рекомендации:
- Краска прекрасно справляется с водоотталкивающей функцией и облагораживает внешний вид фанеры.
- Если вы намерены устанавливать фанерные листы в жилом помещении, краску для них выбирайте на водной основе. Она не имеет ярко выраженного неприятного запаха, быстро сохнет и легко наносится.
- Если вы будете работать на открытом пространстве, лучше подойдут для этой цели эмалированные краски для дерева. Любые из них вы можете приобрести как в готовом виде, так и в концентрированном, которые предназначены для самостоятельной колеровки.
Технология окрашивания — способ 1
Полноценная технология покраски заключается в нескольких этапах:
- С помощью наждачной бумаги отшлифуйте фанеру до гладкости.
- Нанесите акриловую грунтовку валиком или кисточкой.
- Дайте просохнуть в течение нескольких часов.
- Прошпаклюйте поверхность, устраняя все микротрещины.
- Оставьте лист до полного высыхания шпаклевки.
- Отшлифуйте, устраняя все неровности, вызванные шпаклевкой, до ровного основания.
- Снова проведите грунтовочные работы.
- Сделайте техническую паузу до полного высыхания раствора.
- Приготовьте краску, если вы ее самостоятельно колеруете.
- Покрасьте фанерный лист.
Важно! Шлифование проводят крупнозернистой наждачной бумагой — это позволяет устранить все неровности на поверхности. Для придания идеальной гладкости шлифование производится мелкозернистой наждачной бумагой вдоль структуры волокон фанеры.
Грунтовка и шпаклевка выполняют следующие функции:
- устранение микротрещин;
- качественное выравнивание основания;
- защита структуры древесины от механических повреждений.
![]()
Технология окрашивания — способ 2
Еще один способ защиты фанеры от влаги подразумевает использование нитрокраску вместе с тканью. Обычно применяют бязевую или миткалевую ткань. Обработка фанеры этими материалами проводится так:
- Нанесите на фанерный лист слой олифы.
- Просушите в течение нескольких часов.
- Обработайте жидкой краской, которая будет нести функцию грунтовочного слоя.
- Опять просушите.
- Щедро покройте фанеру слоем густой краски или нитрошпаклевки, предварительно разведя ее растворителем.
- Приготовьте ткань и расстелите ее по всей поверхности плиты. Слегка прижмите.
- Пропитайте растворителем для нитрокрасок. Удобно делать это кисточкой.
- Дождитесь, пока высохнет, и покройте всю поверхность жидкой нитрокраской.
Важно! Специалисты советуют не злоупотреблять финишным слоем, так как большое количество краски в завершении отделочных работ делают покрытие менее прочным.
Такая технология применяется чаще всего при самостоятельной постройке лодок.
Дополнительные рекомендации
Еще несколько особенностей, которые нужно учитывать при окрашивании фанеры:
- Фанерные листы, которые находились в сыром влажном помещении, перед обработкой необходимо качественно высушить.
- Если вы планируете устанавливать фанеру на открытом пространстве или в местах с повышенной сыростью, то окрашивайте лист с обеих сторон и в несколько слоев. Особенно тщательно обрабатывайте края.
- Окрашивание не подходит для фанеры, которая монтируется на пол. От постоянного хождения по окрашенной поверхности такого покрытия краска будет шелушиться и отпадать. Для того чтобы определиться, чем обработать фанеру на полу, проконсультируйтесь со специалистами в строительных магазинах.
- Если вы будете наносить краску с помощью распылителя, добьетесь более равномерного распределения цвета. В труднодоступных местах используйте кисточку.
- Если вы решили покрасить фанеру в разные цвета, ограничьте рабочую зону малярным скотчем.
Видео
Если вы задаетесь вопросом, как быстро покрасить фанеру, приложенное ниже видео точно для вас.
Лакирование фанеры
Лак для фанеры тоже является отличным защитником от влаги и сырости. Для работы с такими плитами предназначены такие виды лаков:
- нитроцеллюлозные;
- спиртовые;
- масляные;
- полиэфирные;
- мочевиноформальдегидные;
- полиуретановые.
Выбор лака для фанеры
Учитывая такое разнообразие видов и к тому же производителей, чтобы не растеряться и быстро определиться с нужным вам вариантом, примите во внимание такие факторы:
- Самые востребованные из всех при обработке фанеры – это нитролаки. Они быстро высыхают, обладают необходимыми качествами твердости, влагостойкости и эластичности.
- Самые непопулярные – спиртовые составы.
- С каждым годом все чаще используются полиуретановые лаки. Это связано с устойчивостью к воздействию атмосферных явлений, износостойкостью и долговечностью.
Инструкция по лакировке фанеры
- Тщательно отшлифуйте поверхность мелкозернистой наждачной бумагой.
- Очистите от отходов переработки.
- Обработайте фанеру грунтовкой и просушите.
- Нанесите первый слой лака длинными мазками, распределяя его по всей поверхности. Делайте это с помощью кисти, валика или специального шпателя для лака.
- Дождитесь полного высыхания вещества.
- Повторно нанесите лак.
Важно! Специалисты утверждают, что чем большее слоев лака вы нанесете, тем долговечнее и красивее будет покрытие. Перед каждой следующей обработкой лаком слои тщательно просушите. В конце обработки нанесите на поверхность фанеры олифу или растительное масло – это придаст дереву более насыщенный и глубокий оттенок.
![]()
Дополнительные способы обработки фанеры и их особенности
Чтобы все работы по раскройке и подготовке фанеры к отделочным работам дались вам намного проще, ознакомьтесь с рекомендациями профессиональных строителей:
- Выравнивание краев фанерного листа. Если вы хотите избежать расщепления материала, обрабатывайте древесину от углов к центру листа.
- Шлифование. Используйте для этого вида работы грубую наждачную бумагу от №80 и выше. Работу проводите перпендикулярно структуре волокон фанеры. Для шлифовки под покраску или лакировку применяйте мелкозернистую бумагу, работая ею в продольном направлении.
- Сверление. Для работы с фанерным листом отдавайте предпочтение острому сверлу с передним резаком. Сверлите с лицевой стороны материала, используя подкладку для предотвращения образования сколов.
- Распиловка. Для лицевой стороны листа используйте ленточную пилу. Для изнаночной – дисковую.
- Грунтовка. Этот вид обработки должен проводиться в обязательном порядке.
Она обеспечит фанере дополнительную защиту от воздействия неблагоприятных внешних факторов. Для лучшего результата грунтуйте фанеру с обеих сторон.
Продление срока службы фанерных конструкций
Еще несколько советов для увеличения срока эксплуатации фанеры помогут вам сэкономить в дальнейшем на непредвиденном ремонте:
- Если фанерный лист будет устанавливаться снаружи строения, старайтесь расположить его под навесом.
- Покрывайте изготовленные из фанеры конструкции другими отделочными материалами, тем более, если она расположена на улице.
- На вертикальные поверхности листы устанавливайте тоже вертикально.
- Самыми уязвимыми местами на фанере являются зоны крепления. Поэтому все участки рядом с саморезами и гвоздями должны быть особенно тщательно обработаны.
- Если вы обнаружили на поверхности фанерного покрытия множество мелких трещин, это значит, что оно требует принятия срочных мер. Закрашивать трещины без предварительной обработки не стоит.
Вначале с помощью наждачной бумаги удалите все отслаивающиеся элементы, а потом восстановите защитное покрытие лаком или краской.
Заключение
Фанера – это древесный материал, который подвержен воздействию температур, влажности и давления. При правильном уходе и при обеспечении адекватной гидроизоляции этот материал способен прослужить вам долго и качественно. Правильно примененные технологии по защите фанеры позволят вам добиться нужной прочности плит и не беспокоиться о необходимости ее замены в ближайшем будущем.
15 лучших пропиток для дерева
Обновлено: 12.03.2021 15:14:28*Обзор лучших по мнению редакции expertology.ru. О критериях отбора. Данный материал носит субъективный характер, не является рекламой и не служит руководством к покупке. Перед покупкой необходима консультация со специалистом.
Дерево является популярным строительным материалом, который широко используется в России. Чтобы увеличить срок жизни древесине, за ней нужно бережно ухаживать. Оградить деревянные сооружения от негативных атмосферных воздействий, гниения, появления грибка, плесени и насекомых помогают специальные пропитки. Кроме того, некоторые составы снижают горючесть материала, делая его пожаробезопасным. На отечественном рынке представлена продукция разных производителей, каждый из них хвалит свой антисептик. Советы наших экспертов позволят не ошибиться при выборе состава.
Как выбрать пропитку для дерева
- Основа. Сегодня в магазинах встречается несколько типов пропиток. Самыми универсальными специалисты считают антисептики на водной основе. Они наносятся разными способами (кисть, краскопульт, валик), обеспечивая защиту от огня, влаги, солнца и биопоражения. Акриловые составы отличаются невысокой ценой, хорошими водоотталкивающими свойствами, экологичностью. Но работать с такой пропиткой при отрицательной температуре нельзя. Антисептики на основе органических растворителей хорошо защищают древесину от разрушающих факторов, но таят опасность для человека во время нанесения.
- Назначение. Использование пропитки может быть вызвано несколькими причинами. Антисептические свойства предотвращают развитие микроорганизмов. Такие пропитки нужны при отделке бань и саун. Введение в препарат антипиренов препятствует процессам горения. Это качество востребовано при обработке котельных. Водоотталкивающими и морозостойкими качествами обладают наружные пропитки. Кроме того, важным элементом рецептуры является УФ-фильтры, которые защищают дерево от выгорания. Набор атмосферостойких качеств понадобится при оформлении наружных оснований. Чтобы подчеркнуть природную красоту древесины, требуется декоративная пропитка. Она сделает внутреннее пространство особенно красивым.
- Расход. При выборе пропитки многие пользователи обращают внимание на цену, забывая о расходе. Чаще всего он указывается производителем, исходя из идеальных условий. Только на практике удается определить реальный расход. Если хорошая защита появляется после нанесения 1-2 слоев, то затраты на отделку будут ниже, чем при многослойной пропитке дерева дешевым составом.
- Экологичность. Когда выбирается антисептик для внутренних работ, определяющим фактором при покупке станет экологичность продукта. Это особенно актуально при отделке спальных и детских комнат. В этом случае самыми безопасными будут препараты на водной основе.
Мы включили в наш обзор 15 лучших пропиток для дерева. Все они продаются в российских магазинах и имеют положительные отзывы от экспертов и потребителей.
Рейтинг лучших пропиток для дерева
Лучшая пропитка для дерева для внутренних работ
Заботясь о защите дерева, важно помнить и о собственной безопасности. Поэтому пропитки для внутренних работ выбираются с учетом экологичности. Эксперты обратили внимание на несколько составов.
Pinotex Interior
Рейтинг: 4.9
Эффективную защитную пленку на древесине образует пропитка Pinotex Interior. Лакокрасочная продукция эстонского производителя хорошо зарекомендовала себя в суровом российском климате. Состав сделан на водной основе, у него отсутствует резкий запах. Эксперты отмечают легкость нанесения антисептика, во время работы не образуются потеки. Быстрое высыхание обработанной поверхности сочетается с равномерным впитыванием, что делает структуру дерева выразительной и красивой. На образуемом матовом слое не видны следы от пальцев рук, а также небольшие дефекты древесины.
Пользователи довольны внешним видом матового покрытия, надежной защитой дерева от влаги и грязи. Из минусов следует отметить появление подделок на отечественном рынке.
Достоинства
- безопасность и экологичность;
- широкая гамма оттенков;
- быстрое высыхание;
- отсутствие запаха.
Недостатки
- встречается контрафактная продукция.
Читайте также: 10 лучших производителей массивной доски
Tikkurila Supi
Рейтинг: 4. 8
На втором месте нашего рейтинга расположилась финская пропитка Tikkurila Supi. Защитный состав образует полуматовое акрилатное покрытие, которое допускается колеровать. Антисептик предназначен для обработки деревянных поверхностей в помещениях с разной влажностью, включая парные, душевые и другие комнаты бань и саун. С помощью обработки удается сохранить первоначальный цвет древесины, поддерживать отделку в чистоте. Эксперты отмечают надежную защиту от грязи и влаги, которую обеспечивает состав.
Пользователи хвалят финскую пропитку за долговечную защиту дерева от плесени и синевы, небольшой расход, быстроту высыхания. Любое помещение сразу приобретает индивидуальность и уникальность.
Достоинства
- надежная защита от плесени и грибка;
- экономный расход;
- влаго- и грязестойкость;
-
возможность колеровки.
Акватекс Рогнеда Экстра
Рейтинг: 4.8
Российский состав для древесины Акватекс Рогнеда Экстра отличается комплексной защитой. При этом стоимость обработки получается ниже, чем после применения нескольких лакокрасочных продуктов. Пропитка предотвращает биопоражение дерева (грибок, плесень, синева), потемнение от УФ лучей и атмосферных воздействий. Антисептик отличается высокой декоративностью, позволяя делать отделку под элитные сорта дерева. Наносить состав можно не только на новые материалы (брус, фанера, ДВП, ДСП), но и старые основания.
К преимуществам состава пользователи относят хорошую комплексную защиту, высокие декоративные качества, простое нанесение, богатую палитру. Из недостатков можно упомянуть о неприятном запахе и большом времени высыхания. Пропитка попадает в призовую тройку рейтинга.
Достоинства
- красивый внешний вид;
- комплексная защита;
- сохраняет рисунок дерева;
-
простота в нанесении.
Недостатки
- неприятный запах;
- долго сохнет.
NEOMID 430 ЕСО
Рейтинг: 4.7
Прочную химическую связь образует с древесиной водный раствор антисептика NEOMID 430 ЕСО. Этот консервирующий состав не вымывается водой, он может сохранять все качества дерева в самых тяжелых условиях. Эксперты рекомендуют использовать продукт для обработки досок и брусков, которые длительное время контактируют с водой или почвой (баня, парник, оформление грядок). Пропитанная антисептиком древесина не подвержена воздействию грибков, мха, водорослей, насекомых-древоточцев. Длительность защиты достигает 35 лет.
Пользователи довольны такими свойствами NEOMID 430 ЕСО, как длительный срок защиты, экологичность, широкая сфера применения. К минусам следует отнести окрашивание дерева в зеленовато-серый цвет, наличие специфического запаха. Поэтому 4 позиция рейтинга.
Достоинства
- приемлемая цена;
- длительная защита от биопоражения;
- экологичность;
- не вымывается.
Недостатки
- окрашивание древесины;
- неприятный запах.
Читайте также: 11 лучших яхтных лаков
Текс Биотекс Классик Универсал
Рейтинг: 4.7
Универсальными качествами может похвастаться отечественная пропитка Текс Биотекс Классик Универсал. Рецептура разработана российскими учеными, а выпуск антисептика происходит в цехах с современным импортным оборудованием. В составе пропитки имеется биоцид, который препятствует появлению гнили, грибка, плесени и т. д. Производитель рекомендует наносить антисептик на грунтованную поверхность. Для защиты дерева в помещениях с высокой влажностью и температурой (бани, сауны) состав не подходит.
Пользователи лестно отзываются о доступности препарата, красивых оттенках на дереве, простотой в применении. Эксперты поставили пропитку на пятое место рейтинга из-за въедливого запаха, недолговечность защитного покрытия.
Достоинства
- доступная цена;
- хорошая укрывистость;
- простота в применении;
- подчеркивает структуру дерева.
Недостатки
- въедливый запах;
- слабая влагостойкость.
Экстра Акватекс с воском
Рейтинг: 4.6
Красивый полуглянцевый вид придает древесине пропитка Экстра Акватекс с воском. Этот несмываемый состав обладает противогрибковым действием, он препятствует появлению плесени и синевы на деревянных изделиях. Наличие в препарате УФ фильтров и наночастиц надежно защищает поверхность от выгорания при попадании прямых солнечных лучей. В рецептуру введены такие натуральные компоненты, как воск и растительные масла. Они не только подчеркивают текстуру, но и делают древесину эластичной, защищая ее от растрескивания. Экспертам понравилась эффективность борьбы с насекомыми и несильный запах.
Пропитка не смогла подняться выше в нашем рейтинге из-за недолговечности. Пользователи обновляют покрытие каждые 3-4 года, к тому же состав долго сохнет.
Достоинства
- защита от микроорганизмов и насекомых;
- доступная цена;
- не смывается водой;
- хорошая палитра.
Недостатки
- недолговечность;
- долго сохнет.
Экодом
Рейтинг: 4.5
По самой привлекательной цене реализуется на российском рынке пропитка Экодом. Но не только за низкую стоимость она попадает в наш рейтинг. Эксперты высоко оценили экологичность состава, отсутствие в нем органических растворителей. Препарат не только препятствует появлению микроорганизмов, но и эффективно борется с уже поселившимися грибками и плесенью. После обработки древесина не меняет свой привлекательный вид, покрытие не затрудняет дыхание материала, не ухудшает адгезию к лакокрасочным и клеящим составам.
Отечественным потребителям нравится цена, эффективная борьба с биопоражением, сохранение структуры дерева. К минусам стоит отнести длительное высыхание, плохую укрывистость, неприятный запах.
Достоинства
- низкая цена;
- эффективная борьба с биопоражением;
- сохранение текстуры дерева;
- низкая коррозионная активность.
Недостатки
- долго сохнет;
- плохая укрывистость;
-
неприятный запах.
Лучшая пропитка для дерева для наружных работ
На деревянные конструкции, находящиеся на улице, негативно влияют дождь, солнце, мороз. Поэтому от пропитки требуется максимальная устойчивость к атмосферным воздействиям. Специалистам понравились следующие препараты.
Tikkurila Eko Wood
Рейтинг: 4.9
Сохранить природную красоту дерева удается с помощью лессирующего состава Tikkurila Eko Wood. Эксперты отдали пропитке первую строчку рейтинга за надежную защиту от атмосферных воздействий. Она нивелирует влияние на древесину воды, ультрафиолета и микроорганизмов. Антисептик хорошо проявил себя при обработке наружных стен домов, дверей, окон, заборов, террас и т. д. В каталоге производителя имеется 40 цветов, что позволяет подобрать наиболее подходящую колеровку.
Производится продукт в Санкт-Петербурге, что делает его доступным по цене для многих российских потребителей. Пользователям нравится хорошая проникающая способность антисептика, долговечная защита наружных поверхностей.
Достоинства
- сохраняет природную красоту дерева;
- хорошо защищает от биопоражения;
- предотвращает выгорание древесины на солнце;
- приемлемая цена.
Недостатки
- не обнаружены.
Luxens
Рейтинг: 4.8
Известная компания Леруа Мерлен организовала на территории России производство пропитки Luxens. С конвейера предприятия выходят как бесцветные, так и окрашенные антисептики. Состав завоевал второе место в рейтинге за экономный расход, устойчивость к атмосферным воздействиям, простоту в нанесении. Долговечность защитного покрытия составляет 3-4 года, при этом сохраняется естественный вид деревянных оснований. Благодаря алкидной основе пропитка имеет умеренный запах, который не доставляет проблем при выполнении наружных работ. Кстати, сразу после высыхания слоя запах полностью исчезает.
Пользователи отмечают маленький расход пропитки, даже одного слоя хватает для защиты деревянных конструкций. Не все довольны запахом состава, не совсем удобно наносить препарат кистью.
Достоинства
- подчеркивает красоту дерева;
- длительная защита от биопоражения;
- доступная цена;
- экономный расход.
Недостатки
- неприятный запах.
Pinotex Ultra
Рейтинг: 4.8
Атмосфероустойчивость и декоративность стали главными факторами для попадания пропитки Pinotex Ultra на третью строчку рейтинга. Производитель предлагает как бесцветные, так и окрашенные составы. Покрытие защищает древесину не только от воды и УФ лучей, но и предотвращает горение. В рецептуре имеется специальный фильтр, который препятствует проникновению солнечных лучей в структуру дерева. Благодаря ему сохраняется натуральная текстура древесины долгие годы. Для улучшения впитывания в основание производитель разработал особую технологию AWB.
Пользователям понравилась простота нанесения, отсутствие разбрызгивания и потеков, влагостойкость и грязеотталкивающие способности. К минусам можно отнести высокую цену и длительное высыхание.
Достоинства
- хорошая защита от выгорания;
- водо- и грязеотталкивающая способность;
- красивый вид;
- высокое качество.
Недостатки
- высокая цена;
- долго сохнет.
EXTREME CLIMATE
Рейтинг: 4.7
Любые породы дерева защитит от внешних воздействий пропитка EXTREME CLIMATE. Состав сделан на водной основе и предназначен для внутренних и наружных работ. Обработанная антисептиком древесина не боится дождя, снега, солнечного света. Глубокое проникновение в структуру предотвращает появление и размножение насекомых. Микропленка отличается способностью пропускать воздух, поэтому натуральный материал сможет «дышать».
В отзывах пользователи лестно высказываются по поводу быстрого высыхания пропитки, отсутствие запаха и хорошую укрывистость. Из недостатков отмечается высокая цена, а также дефицит продукта в торговой сети. Поэтому пропитка останавливается в шаге от призовой тройки рейтинга.
Достоинства
- универсальность применения;
- надежная защита от атмосферных воздействий;
- отсутствие неприятного запаха;
- дышащая структура пленки.
Недостатки
- высокая цена;
- дефицит в торговой сети.
Dufa Wood Protect
Рейтинг: 4. 7
Широкую сферу применения находит пропитка Dufa Wood Protect. С помощью этого состава осуществляется долговечная защита наружных деревянных поверхностей. Обработке рекомендуется подвергать стены и фасады домов, беседки и заборы. Матовое покрытие полностью сохраняет привлекательность текстуры. Благодаря акрил-алкидной основе образуется надежный заслон для погодных воздействий. Наносить пропитку на деревянные конструкции можно любыми способами, время высыхания слоя при 20°С составляет всего 1 ч. Состав занимает пятую позицию в рейтинге.
Отечественным потребителям понравилась гладкая поверхность после нанесения, простоту нанесения, отсутствие запаха. Применять антисептик для большого объема работ мешает высокая цена.
Достоинства
- нет запаха;
- долговечная защита от погодных явлений;
- легко смывается с рук;
-
гладкое покрытие.
Недостатки
- высокая цена;
- требуется наносить несколько слоев.
Нортекс-Дезинфектор
Рейтинг: 4.6
Антисептик Нортекс-Дезинфектор применяется для защиты не только деревянных оснований, но кирпичных, бетонных сооружений от плесени и грибка. Эксперты высоко оценили способность пропитки лечить «заболевший» материал. Действие препарата основано на глубоком проникновении в структуру и антисептическом воздействии на грибок и плесень. Производитель рекомендует использовать продукт в экстремальных условиях (повышенная сырость, контакт с почвой). После высыхания слой не осветляет и не тонирует дерево, сохраняя его природную красоту.
Состав попал в наш рейтинг благодаря соотношению цены и качества. Пользователи заметили несколько минусов, к которым можно отнести длительный срок высыхания (10-15 дней), неудобную фасовку и скромный ассортимент.
Достоинства
- лечит болезни;
- глубоко проникает в структуру;
- сохраняет красоту природного материала;
- приемлемая цена.
Недостатки
- долго сохнет;
- неудобная фасовка;
- скромный ассортимент.
Лучшие огнезащитные пропитки для дерева
Если деревянная отделка находится вблизи от источника открытого огня, то ее необходимо обработать огнезащитной пропиткой. Она делает древесину трудно горючим материалом, расширяя его сферу применения. Вот лучшие составы с защитой от огня.
NEOMID 450
Рейтинг: 4.9
Высокоэффективным средством для огнезащиты деревянных конструкций является пропитка NEOMID 450. Состав может использоваться как внутри, так и снаружи зданий. При взаимодействии препарата с древесиной образуется плохо воспламеняемый и трудно горючий материал. Одновременно деревянная поверхность защищается от гниения и появления плесени. Отечественный производитель обещает до 7 лет огнезащиты и 10 летний срок защиты от биопоражения. Продукт предлагается потребителю в бесцветном и тонированном варианте. Эксперты отдали составу первое место в нашем рейтинге.
Пользователям нравится одновременная защита дерева от биопоражения и огня и простота применения. К недостаткам стоит отнести длительное время высыхания (12-14 дней) перед нанесением лакокрасочных материалов.
Достоинства
- комплексная защита дерева;
- универсальность применения;
- длительный срок службы покрытия;
- разные способы нанесения.
Сенеж Огнебио Проф
Рейтинг: 4.8
Комплексную защиту для дерева можно создать с помощью пропитки Сенеж Огнебио Проф. После обработки основание становится трудно горючим, оно не подвергается гниению, биопоражению, поселению жучков. Древесина приобретает стойкость к влаге и перепадам температуры. Только с грунтом не рекомендуется контактировать обработанным элементам. Пользователям следует учитывать, что после высыхания поверхность изменяет свой цвет, хотя природная структура древесины сохраняется. Препарат может применяться и при биопоражении дерева.
Взвесив все плюсы и минусы состава, эксперты отдали ему второе место в рейтинге. Пользователи отмечают отсутствие запаха, пожаробезопасность и простоту применения. Из недостатков часто упоминается про высокий расход антисептика.
Достоинства
- комплексная защита дерева;
- лечит зараженные микроорганизмами основания;
- доступная цена.
Недостатки
- не допускается контакт с почвой;
-
высокий расход.
Оцените статью | |
Всего голосов: 4, рейтинг: 5 |
Патентная заявка США на водный гидрофобизатор для обработки подложек, метод изготовления, подготовка модифицированной фанеры или модифицированного ламинированного шпона и подготовка древесноволокнистой плиты.
ПЕРЕКРЕСТНАЯ ССЫЛКА НА РОДСТВЕННЫЕ ПРИЛОЖЕНИЯ[0001] Настоящая заявка частично является продолжением международной заявки PCT № PCT/JPO2/01560, поданной 21 февраля 2002 г., по которой испрашивается приоритет в соответствии с 35 USC 120, полное содержание которой включено в настоящий документ посредством ссылки.
ТЕХНИЧЕСКАЯ ОБЛАСТЬ [0002] Настоящее изобретение относится к водному водоотталкивающему средству, используемому для обработки подложек, таких как бумага, волокна, кирпич и материалы, полученные из лигноцеллюлозы, такие как древесина, с целью предотвращения изменения размеров бумаги под действием воды или чернил и улучшения свойств печати или придания воды. отталкивание волокон и материалов, происходящих из лигноцеллюлозы, таких как древесина, и способ их получения. Оно также относится к способу изготовления фанеры или клееного бруса и способу изготовления древесноволокнистой плиты.
[0003] В предшествующем уровне техники известно множество способов придания размерной стабильности и водоотталкивающих свойств подложкам, например бумажным изделиям, волокнистым изделиям и строительным материалам, таким как дерево и кирпич. Обычно материалы покрывают или пропитывают растворами силиконовых, акриловых, уретановых, сложноэфирных, жирных и маслянистых смол или мономеров с последующей сушкой. Из этих репеллентов широкое распространение получили силиконовые репелленты. В частности, основным потоком становятся силиконовые гидрофобизаторы типа растворителя.
[0004] Однако гидрофобизаторы типа разбавления растворителем обычно оказывают более негативное влияние растворителя на окружающую среду, чем средства типа разбавления водой. Также с точки зрения защиты окружающей среды и сохранения ресурсов существует сильное желание иметь гидрофобизаторы, в которых не используются растворители, особенно гидрофобизаторы на водной основе с высокими эксплуатационными характеристиками.
[0005] Хотя недавно были разработаны многие водоотталкивающие средства на водной основе, JP-A 1-292089, JP-A 5-156164 и JP-A 5-221748 раскрывают долговременно стабильные эмульсии, содержащие алкилтриалкоксисиланы, эмульгированные в воде.Однако эти эмульсии имеют ряд недостатков, поскольку в них используются алкоксисиланы, характеризующиеся очень медленной гидролитической реакцией. Когда эмульсию наносят на материал, материал эффективно пропитывается ею, но силан улетучивается с поверхности материала. В результате поверхность материала теряет водоотталкивающие свойства, становится уязвимой к смачиванию водой, окрашиванию и вздутию из-за инея и, таким образом, становится нежелательно менее прочной и внешне выглядит молочно-белой.
[0006] Помимо упомянутого выше типа эмульсии, JP-A 61-162553, JP-A 4-249588 и JP-A 10-81752 раскрывают гидрофобизаторы типа гомогенного водного раствора.
[0007] Однако композиции JP-A 61-162553 не хватает стабильности при хранении, поскольку при разбавлении водой происходит быстрая реакция полимеризации. Композиция должна быть использована в течение суток после разбавления и, таким образом, нецелесообразна. Быстрая реакция полимеризации приводит к увеличению молекулярной массы, что замедляет пропитку им материала, иногда оставляя мокрые следы на поверхности материала.
[0008] Композиция согласно JP-A 4-249588, включающая водорастворимый связующий агент, содержащий аминогруппу, и алкилтриалкоксисилан с короткой углеродной цепью, обладает хорошей стабильностью при хранении, но плохой водоотталкивающей способностью, вероятно, потому, что водоотталкивающей способности способствует только низшая алкильная группа.Поскольку компонент связывающего агента, содержащий аминогруппу, включается в избытке по отношению к алкилалкоксисилановому компоненту, о чем свидетельствует молярное соотношение алкилалкоксисиланового компонента/содержащего аминогруппу связующего агента в диапазоне от 0,5/10 до 3/1, возникают проблемы, связанные со смачиванием. на поверхности материала остаются цветные пятна, а бумага, волокнистые изделия и древесина существенно желтеют.
[0009] В JP-A 2000-95868 описан способ получения композиции путем сначала частичного гидролиза алкилтриалкоксисилана или алкилдиалкоксисилана, имеющего короткую углеродную цепь и алкоксисилан, содержащий аминогруппу, добавления гидролизной воды и кислоты для осуществления дальнейшего гидролиза и, наконец, добавления нейтрализующей агент.Этот метод сложный. На первой стадии осуществления гидролитической реакции на смеси алкилалкоксисилана и алкоксисилана, содержащего аминогруппу, алкоксисилан, содержащий аминогруппу, обычно имеет более высокую скорость гидролиза, чем алкилалкоксисилан, который становится препятствием для совместного гидролиза, не в состоянии эффективно образуют согидролитический продукт. Композиция, в конечном итоге полученная этим способом, является, таким образом, неудовлетворительной. Обработка нейтральных субстратов композицией нежелательно придает плохую водоотталкивающую способность.
[0010] JP-A 7-150131 описывает обработку древесины композицией, включающей соль органической или неорганической кислоты с основным азотсодержащим органополисилоксаном, водоотталкивающее вещество и воду. Эта композиция, однако, имеет проблемы недостаточной водоотталкивающей способности и нестабильности при хранении.
[0011] JP-A 55-133466 и JP-A 55-133467 раскрывают композицию, полученную гидролизом алкилалкоксисилана, алкоксисилана, содержащего аминогруппу, алкоксисилана, содержащего эпоксидную группу, и соли металла и металлоида с водой.Обработка подложек композицией сводит к минимуму пожелтение. Однако, поскольку аминогруппы блокируются реакцией аминогрупп с эпоксидными группами, композиция становится настолько труднорастворимой в воде, что ее нельзя использовать в качестве водного обрабатывающего агента. Блокирование аминогрупп также ограничивает адсорбцию композиции на субстратах, так что композицию нельзя использовать для обработки субстратов.
[0012] Для решения вышеупомянутых проблем мы предложили в JP-A 9-77780 композицию, включающую согидролизат алкилалкоксисилана, имеющего от 7 до 18 атомов углерода, силоксан, содержащий алкоксигруппу, и алкоксисилан, содержащий аминогруппу. Несмотря на использование длинноцепочечного алкилсилана, композиция обеспечивает основания со слабыми водоотталкивающими свойствами. При обработке композицией бумаги, волокнистых изделий и дерева происходит несколько заметное пожелтение.
[0013] В JP-A 10-81752 предложена связующая композиция, которая стабильна в щелочной области. Из-за того, что в ней используется значительное количество алкоксисилана, содержащего аминогруппу, эта композиция имеет много проблем, включая недостаточную водоотталкивающую способность в качестве средства для обработки нещелочных субстратов, мокрый цвет, остающийся на обработанном материале, и существенное пожелтение.
[0014] Соответственно, все гидрофобизаторы, описанные выше, редко считаются удовлетворительными для обработки поверхностей, особенно нейтральных (от слабокислых до слабощелочных) поверхностей.
[0015] С другой стороны, элементы корпуса, доступные в настоящее время, включают элементы из фанеры, которые часто используются в качестве элементов несущей стены, элементов структурной обшивки пола и элементов обшивки крыши, а также ламинированные пиломатериалы из шпона, которые часто используются в качестве элементов размером два на четыре и японских традиционных элементах. элементы деревянного каркаса.
[0016] До сих пор было возможно производить фанеру и ламинированные пиломатериалы из шпона из полезного древесного сырья с превосходными свойствами, которое выбирали для конкретной цели или применения из древесного сырья с относительно хорошими свойствами, например тропической древесины. Из-за истощения древесных ресурсов не всегда возможно в сложившихся в настоящее время условиях использовать только древесное сырье, обладающее отличными свойствами.Теперь, когда были введены в действие положения о страховании и продвижении качества домов и зданий, требования к качеству жилья для участников растут и будут расти. Прогнозируется, что в будущем потребуется производить фанеру или ламинированные пиломатериалы из шпона, которые являются менее дорогими, имеют хорошие физические свойства и создают меньшую нагрузку на окружающую среду при утилизации.
[0017] Эти факты говорят о том, что с прогрессом истощения древесных ресурсов изготовление деревянных панелей из древесного материала, обладающего превосходными свойствами в качестве сырья, не всегда возможно. В частности, фанера и изделия из клееного шпона из типичного лесного дерева, сосны лучистой (Pinus Radiata D. DON) в качестве сырья не получили широкого распространения из-за проблем, включая изменение размеров, коробление и плесневение из-за их высокой водо- и влагопоглощаемости. характеристики.
[0018] Одним из традиционных подходов к решению этих проблем является нанесение эмульсий акриловых гидрофобизаторов или парафиновых гидрофобизаторов. Однако проблема блокировки часто возникает, когда эти водоотталкивающие средства наносятся на слои и высушиваются, а слои складываются в кучу.Эта проблема препятствует широкому использованию в практических приложениях.
[0019] Для изготовления древесноволокнистых плит в технике известны мокрый и сухой способы. В любом способе изделия в форме листа из древесных волокон, полученные путем механической обработки бумаги или листового проката, обычно подвергают прессованию при тепловом прессовании с помощью горячего пресса или аналогичного оборудования. ДВП, формованные горячим прессованием, сразу после выхода из горячего пресса охлаждаются и складываются в холодильное оборудование элеваторного или калиточного типа.
[0020] В способе изготовления таких древесноволокнистых плит обычно используют клеи, содержащие формальдегидсодержащие смолы, такие как карбамидоформальдегидные смолы, меламиноформальдегидные смолы и фенолформальдегидные смолы, отдельно или в смеси. В то же время в клеях используются различные воски для придания водостойкости древесноволокнистым плитам, например, так называемые синтетические воски, такие как акриловые воски, полиэтиленовые воски, синтезированные из полиэтилена, имеющего низкую степень полимеризации, или модифицированные кислотой продукты из них, воски Фишера-Тропша, синтезированные из окиси углерода и водорода, и амидные воски, синтезированные из различных жирных кислот и аммиака или амина; воски на нефтяной основе, такие как парафиновый воск и микрокристаллический воск, и минеральные воски, такие как горный воск, озокерит и церезин.
[0021] Кроме того, поскольку древесноволокнистые плиты формуют под давлением, они претерпевают значительные изменения размеров из-за поглощения и выделения влаги или воды после формования. Когда они действительно использовались в домах, часто возникали проблемы. Затем были проведены исследования по повышению водостойкости древесноволокнистых плит с целью улучшения размерной стабильности древесноволокнистых плит. Помимо упомянутого выше примерного решения по добавлению парафина также было предложено использовать клеи на изоцианатной основе, обладающие высокой водостойкостью, для проведения термической или паровой обработки при высокой температуре (от 150 до 200°С.), и проводить химическую обработку, такую как формализация.
[0022] Однако использование вышеупомянутых восков в качестве средства для улучшения водостойкости древесноволокнистых плит обычно приводит к ухудшению прочностных характеристик древесноволокнистых плит, таких как прочность на изгиб и прочность внутреннего соединения. Использование клеев на изоцианатной основе находится в стадии изучения и фактического использования, как упоминалось выше, хотя эти клеи очень дороги по сравнению с смолами на мочевино-формальдегидной основе и меламино-формальдегидными смолами и настолько токсичны, что требуют тщательного обращения и строгого контроля. их использование, а также новое добавление или изменение меры безопасности.
[0023] Среди мер по улучшению водостойкости использование клеев на изоцианатной основе, обладающих высокой водостойкостью, связано с проблемами дороговизны и тщательного обращения и строгого контроля за их использованием, как описано выше; а термообработка при высокой температуре (от 150 до 200°С) имеет недостаток, заключающийся в увеличении стоимости, необходимой для обеспечения высокой температуры, и дополнительно поднимает проблему необходимости дополнительной стадии увеличения содержания воды в древесноволокнистых плитах, которая когда-то уменьшается почти до абсолютной сухости во время обработки, до содержания воды (от 5 до 13%), приемлемого для практического использования. Обработка паром имеет проблемы, связанные с тем, что технологическое оборудование является дорогостоящим, а эксплуатационные расходы очень высокими. Химическая обработка, такая как формализация, сама по себе является очень дорогостоящей, а в случае формализации проблемой является повышенное количество выделяемого формальдегида.
[0024] Кроме того, способ, предусматривающий нанесение модификатора поверхности на листовой элемент из древесных волокон, например, путем распыления с последующим формованием под давлением, как раскрыто в JP-A 2001-260104, имеет проблему, заключающуюся в том, что избыточные участки обрезаются при отделке. элемента в продукт, вода может проникнуть в элемент через торцы, так что элемент легко набухнет.
[0025] Как обсуждалось выше, способы повышения водостойкости предшествующего уровня техники имеют проблемы при практическом использовании, поскольку реагенты, такие как воски, являются экономически эффективными, но вызывают снижение прочностных характеристик древесноволокнистых плит, описанные выше клеи, термическая обработка, обработка паром. и химическая обработка эффективны для повышения водостойкости, но требуют увеличения затрат; то есть ни одна из этих мер не удовлетворяет обоим этим требованиям.
[0026] Цель изобретения, которая была сделана с учетом вышеупомянутых обстоятельств, состоит в том, чтобы предложить водоотталкивающее средство на водной основе для обработки подложек из материалов, происходящих из лигноцеллюлозы или подобных материалов, которое улучшено при пропитке подложек и придает им стабильность размеров и водоотталкивающие свойства обработанных субстратов, а также способ их получения.
[0027] Другой целью изобретения является создание способа изготовления модифицированной фанеры или модифицированного клееного бруса из шпона, который может сделать фанеру или клееный брус из шпона устойчивыми к термитам, гниению, плесени, водостойким, влагостойким и стабильным по размеру и Таким образом, достигается желаемая производительность без умаления его легкого преимущества.
[0028] Еще одной целью изобретения является создание способа изготовления древесноволокнистых плит, при котором древесноволокнистые плиты, обладающие водостойкостью, долговечностью и прочностными характеристиками, могут быть получены с высокой производительностью и низкими затратами.
[0029] Предприняв значительные усилия для достижения вышеуказанных целей, изобретатели обнаружили, что когда продукт получают путем проведения согидролитической конденсации в присутствии органической кислоты или неорганической кислоты
[0030] (A) 100 массовых частей кремнийорганического соединения, имеющего следующую общую формулу (1):
(R1)a(OR2)bSiO(4-a-b)/2 (1)
[0031] где R1 представляет собой алкильную группу, имеющую от 1 до 6 атомов углерода, R2 представляет собой алкильную группу, имеющую от 1 до 4 атомов углерода, буква а представляет собой положительное число 0.от 75 до 1,5, b — положительное число от 0,2 до 3, a+b — от более 0,9 до 4, и
[0032] (B) от 0,5 до 49 частей по весу алкоксисилана, содержащего аминогруппу, имеющего следующую общую формулу (2):
R3R4NR5-SiR6n(OR2)3-n (2)
[0033] где R2 имеет значение, определенное выше, каждый из R3 и R4 независимо представляет собой водород или алкильную или аминоалкильную группу, содержащую от 1 до 15 атомов углерода, R5 представляет собой двухвалентную углеводородную группу, содержащую от 1 до 18 атомов углерода, R6 представляет собой алкильную группу, содержащую от 1 до 4 атомов углерода. атомов, а n равно 0 или 1, или его неполный гидролизат, и в особенности кремнийорганическое соединение делают бесспиртовым путем удаления спирта из реакционной системы, неожиданно сам продукт согидролитической конденсации растворим в воде и остается однородным при растворении в воде может использоваться просто после разбавления водой и сохраняет хорошую стабильность при хранении даже после разбавления водой, хотя количество алкоксисиланового компонента, содержащего аминогруппу, невелико по сравнению с короткоцепочечным алкилтриалкоксисиланом или силоксаном, содержащим алкоксигруппу.Продукт совместной гидролитической конденсации эффективно проникает в подложки, тем самым придавая подложкам длительные водоотталкивающие свойства и стабильность размеров. Когда органические материалы, такие как бумага, волокнистые изделия и древесина, обрабатываются продуктом совместной гидролитической конденсации, пожелтение сводится к минимуму из-за пониженного содержания алкоксисиланового компонента, содержащего аминогруппу.
Поскольку длинноцепочечный алкилсилановый компонент, который был необходим в предшествующем уровне техники для придания водоотталкивающих свойств, устранен, стоимость силанового компонента снижается, что приводит к экономическому преимуществу.Таким образом, продукт совместной гидролитической конденсации улучшает пропитку им подложек, эффективен для придания подложкам размерной стабильности, водоотталкивающих и прочных водоотталкивающих свойств и доступен по низкой цене.
[0034] Кроме того, проводя обширные исследования по разработке способа получения улучшенной фанеры или пиломатериалов из клееного шпона из древесного сырья, не полностью удовлетворяющего требуемым свойствам, изобретатели также обнаружили способ изготовления модифицированной деревянной панели, обладающей улучшенной устойчивостью к термитам, гниению. стойкость к плесени, водостойкость, влагостойкость и стабильность размеров путем пропитки фанеры или клееного бруса вышеописанным водоотталкивающим средством на участках, простирающихся от его передней и задней поверхностей до первого клеевого слоя, то есть, как правило, от его передней и задней поверхностей на глубину 0. от 5 до 10 мм в направлении толщины лицевой и тыльной стороны шпона, и проведение гидролитической поликонденсации для создания и закрепления на внутренних поверхностях межклеточных и внутриклеточных пространств в древесине неоргано-органического композиционного вещества на основе оксида кремния (SiO2), дающего минимальную нагрузку на окружающей среды при выбросе. Изобретатели также открыли способ получения улучшенной модифицированной фанеры или модифицированного клееного бруса из шпона путем одновременного нанесения того же реагента на вырезанный или обработанный участок фанеры или клееного бруса из шпона.
[0035] Кроме того, изобретатели обнаружили, что при добавлении вышеописанного водного водоотталкивающего средства к древесным волокнам и формовании их горячим прессованием древесноволокнистая плита улучшается как в отношении водостойкости, так и в отношении прочности. Настоящее изобретение основано на этих открытиях.
[0036] Соответственно, в первом аспекте изобретение предлагает водный гидрофобизатор для обработки подложки, содержащий продукт согидролитической конденсации
[0037] (A) 100 массовых частей кремнийорганического соединения, имеющего следующую общую формулу (1):
(R1)a(OR2)bSiO(4-a-b)/2 (1)
[0038] где R1 представляет собой алкильную группу, имеющую от 1 до 6 атомов углерода, R2 представляет собой алкильную группу, имеющую от 1 до 4 атомов углерода, буква а представляет собой положительное число 0. от 75 до 1,5, b — положительное число от 0,2 до 3, a+b — от более 0,9 до 4, и
[0039] (B) от 0,5 до 49 частей по весу алкоксисилана, содержащего аминогруппу, имеющего следующую общую формулу (2):
R3R4NR5-SiR6n(OR2)3-n (2)
[0040] где R2 имеет значение, определенное выше, каждый из R3 и R4 независимо представляет собой водород или алкильную или аминоалкильную группу, содержащую от 1 до 15 атомов углерода, R5 представляет собой двухвалентную углеводородную группу, содержащую от 1 до 18 атомов углерода, R6 представляет собой алкильную группу, содержащую от 1 до 4 атомов углерода. атомов, n равно 0 или 1, или их неполный гидролизат, при этом согидролитическая конденсация осуществляется в присутствии органической кислоты или неорганической кислоты; и способ приготовления водного гидрофобизатора для обработки подложки, включающий осуществление совместной гидролитической конденсации указанных выше компонентов (А) и (В) в указанных выше количествах в присутствии органической кислоты или неорганической кислоты. кислота.В этом варианте осуществления к водоотталкивающему средству предпочтительно добавляют алифатическое соединение четвертичного аммония и/или борсодержащее соединение.
[0041] В другом аспекте изобретение обеспечивает способ получения модифицированной фанеры или модифицированного клееного бруса из шпона, включающий стадию пропитки фанеры или клееного бруса водным водоотталкивающим средством с его передней и задней поверхностей для придания водоотталкивающих свойств. избирательно проникать в меж- и внутриклеточные пространства древесины в областях фанеры или клееного бруса между лицевой и изнаночной поверхностями и первыми слоями клея, расположенными ближе всего к лицевой и изнаночной поверхностям.В этом варианте осуществления фанера или брус из клееного шпона имеет вырезанный или обработанный участок, и тот же самый водоотталкивающий материал, который используется здесь, предпочтительно наносят на вырезанный или обработанный участок фанеры или клееного бруса из шпона для пропитки.
[0042] В еще одном аспекте изобретение обеспечивает способ изготовления древесноволокнистой плиты, включающий стадию термокомпрессионного формования листового элемента из древесных волокон с добавленным в него водным водоотталкивающим средством с использованием клея; и способ изготовления древесноволокнистой плиты, включающий стадию термокомпрессионного формования листового элемента из древесных волокон с использованием клея, в который добавлен водный водоотталкивающий агент.
КРАТКОЕ ОПИСАНИЕ ЧЕРТЕЖЕЙ[0043] ИНЖИР. 1 представляет собой поперечное сечение фанеры или клееного бруса из шпона, пропитанных с лицевой и тыльной поверхностей водоотталкивающим средством согласно изобретению.
[0044] ИНЖИР. 2 представляет собой поперечное сечение фанеры или клееного бруса из шпона с нанесенным на его вырезанные или обработанные участки водоотталкивающим средством согласно изобретению. ИНЖИР. 2А, иллюстрирующий нанесение водоотталкивающего средства на торцевые поверхности; ИНЖИР. 2В, иллюстрирующий пропитку гидрофобизатором торцевых поверхностей; ИНЖИР. 2С, иллюстрирующий нанесение водоотталкивающего средства на обработанные поверхности; ИНЖИР. 2D, иллюстрирующий пропитку гидрофобизатором торцевых поверхностей.
[0045] ИНЖИР. 3 представляет собой график, показывающий изменения процентного водопоглощения примера 8 и сравнительного примера 6 во времени в испытании 1.
[0046] ИНЖИР. 4 представляет собой график, показывающий изменения во времени процентного набухания по толщине в примере 8 и сравнительном примере 6 в испытании 1.
[0047] ИНЖИР. 5 представляет собой график, показывающий изменения процентного набухания по ширине примера 8 и сравнительного примера 6 в испытании 1 во времени.
[0048] ИНЖИР. 6 представляет собой график, показывающий изменения процентного водопоглощения примера 8 и сравнительного примера 6 в испытании 2 во времени.
[0049] ИНЖИР. 7 представляет собой график, показывающий изменение процентного набухания по толщине в примере 8 и сравнительном примере 6 в испытании 2 во времени.
[0050] ИНЖИР.8 представляет собой график, показывающий изменения процентного набухания по ширине примера 8 и сравнительного примера 6 в испытании 2 во времени.
[0051] ИНЖИР. 9 представляет собой график, показывающий изменения процентного водопоглощения примера 9 и сравнительного примера 7 во времени.
ЛУЧШИЙ СПОСОБ ОСУЩЕСТВЛЕНИЯ ИЗОБРЕТЕНИЯ[0052] Теперь настоящее изобретение описано более подробно.
[0053] Компонент (А), используемый для получения водоотталкивающего средства для обработки субстратов согласно изобретению, представляет собой кремнийорганическое соединение, имеющее следующую общую формулу (1).
(R1)a(OR2)bSiO(4-a-b)/2 (1)
[0054] Здесь R1 представляет собой алкильную группу, имеющую от 1 до 6 атомов углерода, R2 представляет собой алкильную группу, имеющую от 1 до 4 атомов углерода, буква а представляет собой положительное число от 0,75 до 1,5, b представляет собой положительное число от 0,2 до 3, а а+b представляет собой от более 0,9 до 4,
[0055] Более конкретно, в формуле (1) R1 представляет собой алкильную группу, содержащую от 1 до 6 атомов углерода, предпочтительно от 1 до 3 атомов углерода. Примеры включают метил, этил, н-пропил, изопропил, н-бутил, изобутил, н-пентил и н-гексил, причем метил является предпочтительным.
[0056] R2 представляет собой алкильную группу, содержащую от 1 до 4 атомов углерода, например, метил, этил, н-пропил, изопропил, н-бутил и изобутил, причем метил и этил являются предпочтительными.
[0057] Иллюстративные примеры кремнийорганического соединения формулы (1) приведены ниже. 1 Ch4Si(OCh4)3, Ch4Si(OC2H5)3, Ch4Si(OCH(Ch4)2)3, Ch4Ch3Si(OCh4)3, Ch4Ch3Si(OC2H5)3, Ch4Ch3Si(OCH(Ch4)2)3, C3H6Si(OCh4)3 , C3H6Si(OC2H5)3, C3H6Si(OCH(Ch4)2)3, C4H9Si(OCh4)3, C4H9Si(OC2H5)3, C4H9Si(OCH(Ch4)2)3, C5h21Si(OCh4)3, C5h21Si(OC2H5)3 , C5h21Si(OCH(Ch4)2)3, C6h23Si(OCh4)3, C6h23Si(OC2H5)3, C6h23Si(OCH(Ch4)2)3
[0058] Эти силаны могут быть использованы отдельно или в смеси с любым из них.Также пригодны частичные гидролизаты смешанных силанов.
[0059] Здесь в качестве компонента (А) предпочтительно используют силоксаны, содержащие алкоксигруппы, полученные в результате частичной гидролитической конденсации вышеуказанных силанов. Частичные гидролизаты (силоксановые олигомеры) предпочтительно содержат от 2 до 10 атомов кремния, особенно от 2 до 4 атомов кремния. В качестве компонента (А) также могут быть использованы продукты реакции алкилтрихлорсиланов, содержащих от 1 до 6 атомов углерода, с метанолом или этанолом в воде.Силоксановые олигомеры и в этом случае предпочтительно содержат от 2 до 6 атомов кремния, особенно от 2 до 4 атомов кремния. Из этих силоксановых олигомеров особенно предпочтительны силоксановые димеры формулы (Ch4(OR2)2Si)2O. Они могут содержать силоксановые тримеры и силоксановые тетрамеры. Предпочтительными силоксановыми олигомерами являются те, которые имеют вязкость до 300 мм2/с при 25°С, особенно от 1 до 100 мм2/с при 25°С.
[0060] Компонент (В) представляет собой содержащий аминогруппу алкоксисилан, имеющий следующую общую формулу (2), или его частичный гидролизат.
R3R4NR5-SiR6n(OR2)3-n (2)
[0061] Здесь R2 имеет значение, определенное выше, R3 и R4, которые могут быть одинаковыми или разными, независимо представляют собой водород или алкильную или аминоалкильную группу, содержащую от 1 до 15 атомов углерода, предпочтительно от 1 до 8 атомов углерода, более предпочтительно от 1 до 4 атомов углерода, R5 представляет собой двухвалентную углеводородную группу, содержащую от 1 до 18 атомов углерода, предпочтительно, от 1 до 8 атомов углерода, более предпочтительно, 3 атома углерода, R6 представляет собой алкильную группу, содержащую от 1 до 4 атомов углерода, и n равно 0 или 1.
[0062] В формуле (2) примеры R3 и R4 включают метил, этил, пропил, бутил, аминометил, аминоэтил, аминопропил и аминобутил. Примеры R5 включают алкиленовые группы, такие как метилен, этилен, пропилен и бутилен. Примерами R6 являются метил, этил, пропил и бутил.
[0063] Иллюстративные примеры алкоксисилана, содержащего аминогруппу, формулы (2) приведены ниже. 2 h3N(Ch3)2Si(OCh4)3, h3N(Ch3)2Si(OCh3Ch4)3, h3N(Ch3)3Si(OCh4)3, h3N(Ch3)3Si(OCh3Ch4)3, Ch4NH(Ch3)3Si(OCh4)3 , Ch4NH(Ch3)3Si(OCh3Ch4)3, Ch4NH(Ch3)5Si(OCh4)3, Ch4NH(Ch3)5Si(OCh3Ch4)3, h3N(Ch3)2NH(Ch3)3Si(OCh4)3, h3N(Ch3)2NH (Ch3)3Si(OCh3Ch4)3, Ch4NH(Ch3)2NH(Ch3)3Si(OCh4)3, Ch4NH(Ch3)2NH(Ch3)3Si(OCh3Ch4)3, C4H9NH(Ch3)2NH(Ch3)3Si(OCh4)3 , C4H9NH(Ch3)2NH(Ch3)3Si(OCh3Ch4)3, h3N(Ch3)2SiCh4(OCh4)2, h3N(Ch3)2SiCh4(OCh3Ch4)2, h3N(Ch3)3SiCh4(OCh4)2, h3N(Ch3)3SiCh4 (OCh3Ch4)2, Ch4NH(Ch3)3SiCh4(OCh4)2, Ch4NH(Ch3)3SiCh4(OCh3Ch4)2, Ch4NH(Ch3)5SiCh4(OCh4)2, Ch4NH(Ch3)5SiCh4(OCh3Ch4)2, h3N(Ch3)2NH (Ч3)3SiCh4(OCh4)2, h3N(Ch3)2NH(Ch3)3SiCh4(OCh3Ch4)2, Ch4NH(Ch3)2NH(Ch3)3SiCh4(OCh4)2, Ch4NH(Ch3)2NH(Ch3)3SiCh4(OCh3Ch4)2 , C4H9NH(Ch3)2NH(Ch3)3SiCh4(OCh4)2, C4H9NH(Ch3)2NH(Ch3)3SiCh4(OCh3Ch4)2
[0064] Из них предпочтительными являются N-(2-аминоэтил)-3-аминопропилтриметоксисилан, N-(2-аминоэтил)-3-аминопропилметилдиметоксисилан, N-(2-аминоэтил)-3-аминопропилтриэтоксисилан, N-(2-аминоэтил)-3 -аминопропилметилдиэтоксисилан, 3-аминопропилтриметоксисилан, 3-аминопропилметилдиметоксисилан, 3-аминопропилтриэтоксисилан и 3-аминопропилметилдиэтоксисилан.
[0065] Что касается пропорции смешивания компонентов (А) и (В), то используют от 0,5 до 49 частей, предпочтительно от 5 до 30 частей по массе компонента (В) на 100 частей по массе компонента (А) (все части составляют по вес, далее). При содержании менее 0,5 части компонента (В) продукт становится менее растворимым в воде и нестабильным в форме водного раствора. Продукт, в котором используется более 49 частей компонента (В), может ухудшить водоотталкивающие свойства и долговременное ингибирование водопоглощения и вызвать значительное пожелтение при обработке им подложек.
[0066] В молярном отношении компоненты (А) и (В) используются так, что на моль атомов кремния в компоненте (А) приходится от 0,01 до 0,3 моль, особенно от 0,05 до 0,2 моль атомов Si в компоненте (В).
[0067] При приготовлении водного гидрофобизатора с использованием компонентов (А) и (В) проводят совместный гидролиз компонентов (А) и (В) в присутствии органической кислоты или неорганической кислоты.
[0068] В предпочтительном варианте продукт согидролитической конденсации получают сначала путем гидролиза компонента (А) в присутствии органической кислоты или неорганической кислоты, смешивания полученного гидролизата с компонентом (В) и осуществления дальнейшего гидролиза в присутствии органическая кислота или неорганическая кислота.
[0069] Органическая кислота или неорганическая кислота, используемая для первого гидролиза компонента (А), представляет собой по меньшей мере одну кислоту, выбранную из соляной кислоты, серной кислоты, метансульфоновой кислоты, муравьиной кислоты, уксусной кислоты, пропионовой кислоты, лимонной кислоты, щавелевой кислоты и малеиновой кислоты. . Из них предпочтительными являются уксусная кислота и пропионовая кислота. Кислоту предпочтительно используют в количестве от 2 до 40 частей, более предпочтительно от 3 до 15 частей на 100 частей компонента (А).
[0070] Гидролиз предпочтительно проводить в состоянии, умеренно разбавленном растворителем. Растворитель предпочтительно выбирают из спиртовых растворителей, особенно метанола, этанола, изопропилового спирта и трет-бутилового спирта. Подходящее количество используемого растворителя составляет от 50 до 300 частей, более предпочтительно от 70 до 200 частей на 100 частей компонента (А). При содержании менее 50 частей растворителя может иметь место чрезмерная конденсация. При содержании более 300 частей растворителя гидролиз может занять больше времени.
[0071] Количество воды, добавляемой к компоненту (А) для гидролиза, предпочтительно равно 0.от 5 до 4 моль, особенно от 1 до 3 моль на моль компонента (А). Если количество добавленной воды меньше 0,5 моль, может остаться больше алкоксигрупп. При количестве воды более 4 моль может иметь место чрезмерная конденсация. Предпочтительные условия реакции для гидролиза компонента (А) включают температуру реакции от 10 до 40°С, особенно от 20 до 30°С, и время реакции от 1 до 3 часов.
[0072] Полученный таким образом гидролизат компонента (А) затем подвергают взаимодействию с компонентом (В). Предпочтительные условия реакции на этой стадии включают температуру реакции от 60 до 100°С и время реакции от 1 до 3 часов. В конце реакции реакционную систему нагревают выше температуры кипения растворителя для отгонки спиртового растворителя. Предпочтительно спиртовой растворитель отгоняют до тех пор, пока содержание всех спиртов (включая спирт в качестве реакционной среды и спирт в качестве побочного продукта) в системе не станет 30% по весу или менее, особенно 10% по весу или менее. Если продукт содержит много спирта, он может стать белым мутным или превратиться в гель при разбавлении водой и потерять стабильность при хранении.Продукт реакции, полученный вышеописанным способом, предпочтительно должен иметь вязкость от 5 до 2000 мм2/с при 25°С, особенно от 50 до 500 мм2/с при 25°С. Слишком высокая вязкость может неблагоприятно сказаться на простоте работы. стабильность при хранении и снижение растворимости в воде. Продукт предпочтительно имеет среднемассовую молекулярную массу в диапазоне от 500 до 5000, особенно от 800 до 2000.
[0073] Водный гидрофобизатор по изобретению состоит из продукта реакции совместной гидролитической конденсации компонентов (А) и (В), полученного вышеописанным способом.Предположительно из-за того, что продукт находится в растворенном или мицеллярном состоянии в водном растворе из-за податливой ориентации гидрофильных фрагментов (амино- и силанольных групп) и гидрофобных фрагментов (алкилсилильные группы), продукт проявляет водорастворимость, несмотря на низкое содержание компонента (В) . Продукт проявляет хорошие водоотталкивающие свойства независимо от удаления длинноцепочечного алкилсиланового компонента, хорошую проницаемость и устойчивые водоотталкивающие свойства, предположительно из-за ориентации по отношению к подложке.Когда репеллент наносится на строительные материалы, такие как кирпич, минимальное улетучивание на поверхности предотвращает смачивание поверхности водой, появление пятен и вздутие из-за инея. Когда репеллент разбавляют водой, реакция полимеризации в воде сдерживается, а стабильность при хранении улучшается.
[0074] В предпочтительном варианте (С) алифатическое соединение четвертичного аммония и/или (D) борсодержащее соединение добавляют к водоотталкивающему средству согласно изобретению.
[0075] Предпочтительно алифатическое соединение четвертичного аммония (С) представляет собой алкоксисилан, содержащий четвертичную аминогруппу, имеющий следующую общую формулу (3), или его частичный гидролизат.
&lqb;(Ch4)2R7N(Ch3)3-SiR6n(OR2)3-n]+X- (3)
[0076] Здесь R2 и R6 имеют указанные выше значения, R7 представляет собой одновалентную углеводородную группу, содержащую от 11 до 22 атомов углерода, особенно алкильную или алкенильную, и n равно 0 или 1. Это компонент, который придает древесине антибактериальные и противогрибковые свойства при обработке древесины. с водным водоотталкивающим средством.
[0077] В формуле (3) примерами R7 являются группы -C11h33, -C12h35, -C16h41, -C16h43, -C18h47, -C20h51 и -C22h55.
[0078] Иллюстративные и предпочтительные примеры алкоксисилана, содержащего четвертичную аминогруппу, имеющего формулу (3), включают
[0079] [C12h35(Ch4)2N(Ch3)3Si(OCh4)3+Cl-,
[0080] [C14h39(Ch4)2N(Ch3)3Si(OCh3Ch4)3+Cl-,
[0081] [C16h43(Ch4)2N(Ch3)3Si(OCh4)3+Cl-,
[0082] [C16h43(Ch4)2N(Ch3)3Si(OCh3Ch4)3+Cl-,
[0083] [C16h43(Ch4)2N(Ch3)3SiCh4(OCh4)2+Cl-,
[0084] [C16h43(Ch4)2N(Ch3)3SiCh4(OCh3Ch4)3+Cl-,
[0085] [C18h47(Ch4)2N(Ch3)3Si(OCh4)3+Cl-,
[0086] [C18h47(Ch4)2N(Ch3)3Si(OCh3Ch4)3+Cl-,
[0087] [C18h47(Ch4)2N(Ch3)3SiCh4(OCh4)2+Cl- и
[0088] [C18h47(Ch4)2N(Ch3)3SiCh4(OCh3Ch4)3+Cl-.
[0089] Добавление компонента (С) может придавать антибактериальные и противогрибковые свойства. Количество смешанного компонента (С) предпочтительно составляет от 0,05 до 10 частей, особенно от 0,1 до 5 частей по массе на 100 частей по массе водных водоотталкивающих твердых веществ (согидролизный конденсат компонентов (А) и (В)). Слишком малые количества могут придать недостаточные антибактериальные и противогрибковые свойства, тогда как слишком большие количества могут неблагоприятно повлиять на стабильность при хранении водоотталкивающего средства на водной основе.
[0090] С другой стороны, борсодержащее соединение предпочтительно представляет собой соединение борной кислоты. Примеры включают ортобораты, такие как InBO3 и Mg3(BO3)2; дибораты, такие как Mg2B2O5 и CO2B2O5; метабораты, такие как NaBO2, KBO2, LiBO2 и Ca(BO2)2; тетрабораты, такие как Na2B4O7; и пентабораты, такие как KB5O8. Также пригодны борные кислоты, такие как ортоборная кислота (h4BO3), метаборная кислота (HBO2) и тетраборная кислота (h3B4O7), а также бура (Na2B4O7. 10h3O).
[0091] Добавление компонента (D) может придать свойства защиты от термитов.Количество смешанного компонента (D) предпочтительно составляет от 0,1 до 10 частей, особенно от 2 до 8 частей по массе на 100 частей по массе водных водоотталкивающих твердых веществ (согидролизный конденсат компонентов (А) и (В)). Слишком малые количества могут придать недостаточную защиту от термитов, тогда как слишком большие количества могут неблагоприятно повлиять на стабильность при хранении водоотталкивающего средства на водной основе.
[0092] Водный гидрофобизатор изобретения используется для обработки подложек, особенно бумаги, волокон, кирпича и веществ, происходящих из лигноцеллюлозы, таких как древесина, для придания водоотталкивающих свойств.Вещества, образующие лигноцеллюлозу, включают древесные материалы, такие как древесина, фанера, ламинированные пиломатериалы из шпона, прессованные изделия из древесных частиц и древесноволокнистые плиты, а также бумагу и волокна, происходящие из целлюлозы.
[0093] В частности, водоотталкивающее средство на водной основе по изобретению применимо к листам бумаги в качестве стабилизатора размеров. Репеллент не только предотвращает изменение размеров бумаги, например, из-за волнистости или сморщивания с водными чернилами (что часто используется в струйной печати), но также улучшает восприимчивость бумаги к краске, обеспечивая хорошее качество печатного изображения.Репеллент также применим к другим субстратам, включая различные волокнистые изделия и строительные материалы, такие как кирпич, дерево, фанера, ламинированные пиломатериалы из шпона и древесные волокна для древесноволокнистых плит. Репеллент также является полезной грунтовкой для различных красок и отделки.
[0094] Когда вышеупомянутые субстраты обрабатываются водным водоотталкивающим средством по изобретению, перед использованием репеллент может быть разбавлен водой до концентрации от 0,5 до 50%, предпочтительно от 1 до 10% по весу.При тонком разбавлении менее 0,5% по весу репеллент может не проявить свои свойства в полной мере и его необходимо наносить в большем количестве, что может потребовать более длительного времени для высыхания. Концентрация более 50 мас.% указывает на недостаточное разбавление и придает слишком высокую вязкость для пропитки им подложек, иногда оставляя следы покрытия и вызывая обесцвечивание.
[0095] Когда водный гидрофобизатор по изобретению разбавляют водой с образованием водного раствора, водный раствор предпочтительно должен иметь рН от 7 до 3, особенно рН от 6 до 4.Если водный раствор имеет рН выше 7 или является щелочным, раствор может повредить целлюлозные подложки, такие как бумага и дерево. Если водный раствор имеет рН ниже 3 или сильно кислый, возникают проблемы, связанные с повреждением субстратов и коррозией оборудования, используемого для обработки. Когда синтез проводят вышеописанным способом, получают продукт совместной гидролитической конденсации, попадающий в указанный выше диапазон рН. Водный раствор репеллентов на уровне от нейтрального до слабокислого лучше всего подходит для обработки им субстратов.
[0096] При разбавлении водоотталкивающего средства по изобретению водой могут быть добавлены различные второстепенные добавки. Такие добавки включают консерванты, противогрибковые агенты, агенты для борьбы с термитами, ароматизаторы, красители, карбоксиметилцеллюлозу, поливиниловый спирт (ПВС), водорастворимые акриловые смолы, латекс SBR и коллоидный диоксид кремния. Такой необязательный компонент может быть добавлен в обычном количестве до тех пор, пока это не ставит под угрозу преимущества изобретения.
[0097] Если желательно, чтобы водное водоотталкивающее средство проникало глубоко в подложку, к репелленту может быть добавлено поверхностно-активное вещество для повышения его проницаемости.
[0098] Используемое здесь поверхностно-активное вещество не является критическим, и можно использовать любое из хорошо известных неионогенных, катионогенных и анионных поверхностно-активных веществ. Примеры включают неионогенные поверхностно-активные вещества, такие как алкиловые эфиры полиоксиэтилена, алкилфениловые эфиры полиоксиэтилена, полиоксиэтиленкарбоксилат, сложные эфиры сорбитана и жирных кислот, сложные эфиры полиоксиэтиленсорбитана и жирных кислот и модифицированные полиэфиром силиконы; катионные поверхностно-активные вещества, такие как хлорид алкилтриметиламмония и хлорид алкилбензиламмония; анионные поверхностно-активные вещества, такие как алкил- или алкилаллилсульфаты, алкил- или алкилаллилсульфонаты и диалкилсульфосукцинаты; и амфолитные поверхностно-активные вещества, такие как поверхностно-активные вещества типа аминокислот и бетаина. Из них предпочтительны силиконовые поверхностно-активные вещества, модифицированные полиэфиром.
[0099] Соответствующее количество добавляемого поверхностно-активного вещества составляет от 0,01 до 5% по весу, более предпочтительно от 0,2 до 2,5% по весу в расчете на твердые вещества водного водоотталкивающего средства. При содержании поверхностно-активного вещества менее 0,01 мас.% результаты практически не изменились по сравнению с результатами обработки одним водным гидрофобизатором, то есть по существу не достигается эффект добавления. Поверхностно-активное вещество в количестве более 5% по весу может иногда неблагоприятно влиять на ингибирование водопоглощения и водоотталкивающие свойства.
[0100] Вместо предварительного добавления поверхностно-активного вещества к водному водоотталкивающему средству подложку можно предварительно обработать разбавлением поверхностно-активного вещества перед обработкой водным водоотталкивающим средством. В этом случае ПАВ разбавляют водой или органическим растворителем до концентрации от 0,01 до 5 %, особенно от 0,1 до 2 % по весу, предварительно обрабатывают этим разбавлением ПАВ валиком, кистью или распылением или даже окунанием, а затем поверхность обрабатывают водным гидрофобизатором. Эта процедура обеспечивает глубокое проникновение репеллентов в основание.
[0101] При нанесении водного раствора водоотталкивающего средства на подложку можно использовать валик, кисть, распылитель и т.п. В некоторых случаях можно использовать погружение. Применение может быть сделано при атмосферном давлении или пониженном давлении. Последующая стадия сушки может представлять собой выдержку при комнатной температуре, сушку на солнце или сушку при нагревании.
[0102] Водный гидрофобизатор, которым пропитана подложка вышеописанным способом, подвергается гидролитическим реакциям и реакциям конденсации с образованием прочного водоотталкивающего слоя.Следовательно, когда репеллент наносится на бумагу, стабильность размеров бумаги улучшается. Когда репеллент наносится на волокнистые изделия, волокнистые изделия становятся полностью водоотталкивающими. Когда репеллент наносится на строительные материалы, такие как кирпич и дерево, устраняются проблемы образования пузырей, коррозии и плесени, вызванные водой. Кроме того, репеллент служит базовой водостойкой грунтовкой для различных красок и отделок.
[0103] Водный водоотталкивающий агент по настоящему изобретению успешно используется при получении модифицированной фанеры и модифицированного клееного бруса из шпона.В частности, фанеру или клееный брус пропитывают и обрабатывают с лицевой и тыльной поверхностей водным гидрофобизатором, при этом участки фанеры или клееного бруса, простирающиеся от лицевой и изнаночной поверхностей до первых слоев клея (обычно 0,5 до 10 мм в направлении толщины) выборочно пропитываются за счет использования того факта, что плоские клеевые слои, характерные для фанеры и клееного бруса, препятствуют легкому проникновению раствора за пределы клеевых слоев при нанесении раствора на лицевую и тыльную поверхности.Таким образом, достигается желаемая производительность при уменьшении количества репеллентов, пропитанных на единицу объема изделия. При этом тот же раствор предпочтительно наносится на вырезанные и/или обработанные участки фанеры или клееного бруса для пропитки.
[0104] В частности, порода дерева древесного сырья, из которого изготовлена фанера или брус из клееного шпона, не имеет решающего значения, и тип клеевой смолы, используемой при получении фанеры и/или клееного бруса из шпона, не имеет решающего значения.
[0105] При нанесении водного водоотталкивающего средства на переднюю и заднюю поверхности и вырезанные секции или обработанные секции фанеры или клееного бруса для пропитки температура фанеры или клееного бруса может быть комнатной. Однако желательно, чтобы температура порядка 40-80°С поддерживалась не только на поверхностях, но также и внутри фанеры или ламинированного шпона для обеспечения проникновения. И наоборот, водный гидрофобизатор нагревают до температуры от 40 до 80°С.можно использовать, сохраняя фанеру или клееный брус при комнатной температуре. Поскольку содержание воды в фанере или клееном брусе должно находиться в диапазоне, обеспечивающем уровень очистки до 14%, как это предписано японскими сельскохозяйственными и лесохозяйственными стандартами, водоотталкивающий репеллент наносится в таких количествах, чтобы обеспечить содержание воды в пределах этого диапазона. диапазон.
[0106] Отмечается, что при нанесении водного гидрофобизатора как на переднюю, так и на заднюю поверхность фанеры и/или клееного бруса на производственной линии с учетом степени испарения под действием тепла предпочтительный процесс включает стадию предварительного смешивания. От 10 до 100 частей воды на 1 часть согидролизного конденсата компонентов (А) и (Б) в растворе покрытия или стадии нанесения воды как на лицевую, так и на изнаночную поверхности фанеры или клееного бруса непосредственно перед нанесением водного водоотталкивающего средства.В последнем случае количество применяемой воды может быть отрегулировано таким образом, чтобы на 1 часть согидролизного конденсата компонентов (А) и (В) приходилось от 10 до 100 частей воды.
[0107] Далее описываются масса покрытия и техника нанесения покрытия. В случае покрытия лицевой поверхности масса покрытия такова, что от 0,1 до 20 г, предпочтительно от 1 до 5 г согидролизного конденсата компонентов (А) и (В) покрывают и пропитывают на квадратный метр площади поверхности и на миллиметр расстояния от лицевой поверхности до первого клеевого слоя. То же самое относится и к покрытию задней поверхности. В случае покрытия на вырезанном или обработанном участке масса покрытия должна быть такой, чтобы от 0,1 до 20 г, предпочтительно от 1 до 5 г согидролизного конденсата компонентов (А) и (В) покрывали и пропитывали на квадратный метр. площади поперечного сечения и на миллиметр на расстоянии от 1 до 5 мм от поверхности сечения.
[0108] Что касается техники нанесения покрытия, то покрытие с помощью валика или губчатого валика является желательным с точки зрения управления весом покрытия, в то время как нанесение распылением и нанесение методом погружения в ванну также приемлемы.Для увеличения степени погружения стадию покрытия можно повторить два или более раз.
[0109] ИНЖИР. 1 показаны передняя и задняя пропитанные области фанеры или клееного бруса из шпона. Ламинированный пиломатериал из шпона, обозначенный цифрой 1, включает в себя множество слоев шпона 2, ламинированных с помощью клеевых слоев 3. Устройство для нанесения покрытия, такое как валковая установка для нанесения покрытий, обозначено цифрой 4. С помощью устройства для нанесения покрытия 4 водоотталкивающее средство на водной основе выборочно наносится на лицевую и изнаночную стороны шпона. 2а и 2б для пропитки с образованием пропитанных слоев 5.
[0110] ИНЖИР. 2 показаны участки, пропитанные водоотталкивающей пропиткой, на торцах или обработанных участках фанеры или клееного бруса из шпона. Водный водоотталкивающий агент наносится на торцевые поверхности 6 или обработанные участки 7 с помощью средства 8 для нанесения покрытия, такого как распылители, как показано на фиг. 2А и 2С, тем самым формируя пропитанные области 9, как показано на ФИГ. 2В и 2D.
[0111] Что касается старения для гелеобразования, водному гидрофобизатору по изобретению обычно требуется от 12 до 200 часов для старения для гелеобразования после покрытия.Старение желательно проводить при температуре воздуха от 10 до 35°С в условиях полной вентиляции.
[0112] Описанный выше метод подготовки гарантирует, что фанера или клееный брус из шпона будут стойкими к термитам, гниению, плесени, водостойким, влагостойким и стабильным по размеру, так что их можно будет использовать в качестве основных элементов конструкции или элементов интерьера здания. легко подготавливаться без нарушения текстуры, присущей древесине, и без слипания из-за отложений.
[0113] Кроме того, гидрофобизатор на водной основе по изобретению успешно используется при изготовлении древесноволокнистых плит. В одном варианте осуществления способ изготовления древесноволокнистой плиты включает добавление водоотталкивающего средства к деревянному волокну, затем добавление клея, а затем термокомпрессионное формование листового элемента. Количество гидрофобизатора, добавляемого в этом варианте осуществления, предпочтительно составляет от 0,04 до 10 г на 100 г веса высушенного в печи древесного волокна.В качестве альтернативы, древесноволокнистая плита может быть изготовлена путем термокомпрессионного формования листового элемента из древесных волокон с использованием клея, в который добавлен водоотталкивающий агент. Количество гидрофобизатора, добавляемого в альтернативном варианте осуществления, предпочтительно составляет от 0,04 до 30 г на 100 г веса высушенного в печи древесного волокна.
[0114] Более конкретно, способ изготовления древесноволокнистой плиты включает прессование под давлением листового элемента из древесных волокон.Листовой элемент из древесных волокон формируется путем фибриллирования древесины в волокна или нити и обработки их бумагой в лист или пластинчатый элемент с помощью мокрого или сухого процесса. Фибриллирование может быть осуществлено с помощью различных хорошо известных способов предшествующего уровня техники, таких как использование измельчителя, использование дискового рафинера или истирающей мельницы и взрыв. Последующая стадия нанесения водного гидрофобизатора на древесные волокна может быть проведена путем нанесения внутри каждой из фибриллирующих машин или после выхода из каждой из фибриллирующих машин.Техника нанесения может использовать распылитель или капельный аппарат, если это возможно для определенной фибриллирующей машины. В качестве альтернативы, необходимое количество водоотталкивающего средства на водной основе может быть добавлено к вводимому клею перед термопрессованием. Отмечается, что техника бумажной обработки может быть как техникой мокрого валяния, так и техникой воздушного валяния.
[0115] Стадия термического компрессионного формования представляет собой стадию нагрева и прессования листового элемента из древесных волокон, полученного обработкой бумаги, с образованием пластинчатого элемента.Используемые здесь методы термокомпрессионного формования включают в себя метод мокрого прессования горячего прессования мокрого листа (полученного в результате метода мокрого валяния) с помощью многоступенчатого горячего прессования, метод мокрого формования/сухого прессования сушки мокрого листа с последующим горячим прессованием. , метод сухого прессования горячего прессования сухого листа (результат техники воздушного валяния) с помощью многоступенчатого горячего прессования и метод полусухого прессования горячего прессования полусухого листа. В способе изготовления древесноволокнистой плиты в соответствии с изобретением этапы, выполняемые до термического компрессионного формования листового элемента из древесных волокон с образованием пластинчатого элемента из древесных волокон (далее именуемого древесноволокнистой плитой), могут быть аналогичны используемым в известном способе изготовления древесноволокнистой плиты, если не указано иное. Древесноволокнистые плиты представляют собой плиты любого типа, включая изоляционные плиты (IB) и твердые плиты (HB), хотя предпочтительно они представляют собой древесноволокнистые плиты средней плотности (MDF).
[0116] Затем в способе изготовления древесноволокнистой плиты согласно изобретению количество добавляемого водного гидрофобизатора обычно составляет от 0,04 до 10 г, предпочтительно от 0,2 до 7 г и более предпочтительно от 0,5 до 2 г на 100 г материала. древесные волокна, высушенные в печи. Если количество добавки составляет менее 0,04 г, древесноволокнистая плита, полученная прессованием под давлением, часто имеет недостаточно улучшенную водостойкость.Количество добавки, превышающее 10 г, имеет неудобную вероятность скручивания древесных волокон, что влияет на последующее равномерное нанесение клея на древесные волокна, невозможно получить листовой элемент, имеющий однородное распределение плотности, и упадок воды. возникает эффект улучшения сопротивления и даже снижение силовых показателей.
[0117] С другой стороны, количество гидрофобизатора, добавляемого в клей, обычно равно 0.от 04 до 30 г, предпочтительно от 5 до 25 г и более предпочтительно от 15 до 20 г на 100 г высушенных в печи древесных волокон. Если количество добавки составляет менее 0,04 г, древесноволокнистая плита, полученная прессованием под давлением, часто имеет недостаточно улучшенную водостойкость. Количество добавки, превышающее 30 г, указывает на слишком большую пропорцию веса водоотталкивающего средства (включая клей) по отношению к древесным волокнам, что приводит к неудобной вероятности того, что это станет фактором, препятствующим собственной адгезионной силе клея. , и, как упоминалось ранее, элемент в форме листа, имеющий однородное распределение плотности, получить с трудом, что приводит к снижению эффекта улучшения водостойкости и даже к снижению прочностных характеристик.Также увеличивается стоимость.
ПРИМЕР [0118] Примеры изобретения приведены ниже вместе со сравнительными примерами в качестве иллюстрации, а не в качестве ограничения. Все части указаны по весу.
[0119] В четырехгорлую колбу объемом 500 мл, снабженную холодильником, термометром и капельной воронкой, загружают 85 г (0,37 моль в пересчете на димер) метилтриметоксисиланового олигомера, 154 г метанола и 5.1 г уксусной кислоты. При перемешивании к шихте добавляли 6,8 г (0,37 моль) воды, которую перемешивали в течение 2 ч при 25°С. Затем по каплям добавляли 8,9 г (0,04 моль) N-(2-аминоэтил)-3-аминопропилтриметоксисилана. . Реакционный раствор нагревали до температуры кипения метанола и реакцию проводили в течение одного часа. С прикрепленным сложноэфирным адаптером метанол отгоняли до достижения внутренней температуры 110°С. Получали 81 г бледно-желтого прозрачного раствора с вязкостью 71 мм 2 /с (средневесовая молекулярная масса 1100).Содержание остаточного метанола в растворе составляло 5% по массе. Обозначается как Репеллент 1.
Пример 2 [0120] Реакцию проводили, как в примере 1, за исключением того, что количество N-(2-аминоэтил)-3-аминопропилтриметоксисилана было изменено на 17,8 г (0,08 моль). Получали 86 г бледно-желтого прозрачного раствора с вязкостью 116 мм 2 /с (средневесовая молекулярная масса 1200). Содержание остаточного метанола в растворе составляло 5% по массе.Обозначается Repellent 2.
[0121] В четырехгорлую колбу объемом 500 мл, снабженную холодильником, термометром и капельной воронкой, загружают 50,3 г (0,37 моль) метилтриметоксисилана, 124 г метанола и 5,1 г уксусной кислоты. При перемешивании к шихте добавляли 6,8 г (0,37 моль) воды, которую перемешивали в течение 2 ч при 25°С. Затем по каплям добавляли 8,9 г (0,04 моль) N-(2-аминоэтил)-3-аминопропилтриметоксисилана. . Реакционный раствор нагревали до температуры кипения метанола и реакцию проводили в течение одного часа.С прикрепленным сложноэфирным адаптером метанол отгоняли до достижения внутренней температуры 110°С. Получали 43 г бледно-желтого прозрачного раствора с вязкостью 65 мм 2 /с (средневесовая молекулярная масса 1000). Содержание остаточного метанола в растворе составляло 6% по массе. Обозначается Repellent 3.
[0122] В четырехгорлую колбу емкостью 500 мл, снабженную холодильником, термометром и капельной воронкой, помещают 60 мл.6 г (0,37 моль) пропилтриметоксисилана, 144 г метанола и 5,1 г уксусной кислоты. При перемешивании к шихте добавляли 6,8 г (0,37 моль) воды, которую перемешивали в течение 2 ч при 25°С. Затем по каплям добавляли 8,9 г (0,04 моль) N-(2-аминоэтил)-3-аминопропилтриметоксисилана. . Реакционный раствор нагревали до температуры кипения метанола и реакцию проводили в течение одного часа. С прикрепленным сложноэфирным адаптером метанол отгоняли до достижения внутренней температуры 110°С. Получали 51 г бледно-желтого прозрачного раствора с вязкостью 65 мм 2 /с (средневесовая молекулярная масса 800).Содержание остаточного метанола в растворе составляло 7% по массе. Обозначается Repellent 4.
Пример 5 [0123] Реакцию проводили, как в примере 1, за исключением того, что вместо N-(2-аминоэтил)-3-аминопропилтриметоксисилана использовали 17,7 г (0,08 моль) 3-аминопропилтриэтоксисилана. Получали 90 г бледно-желтого прозрачного раствора с вязкостью 220 мм2/с (средневесовая молекулярная масса 1300). Содержание остаточного метанола в растворе составляло 5% по массе.Обозначается Repellent 5.
[0124] В четырехгорлую колбу объемом 500 мл, снабженную аспиратором и термометром, загружали 136 г (1,0 моль) метилтриметоксисилана, 222,0 г (1,0 моль) N-(2-аминоэтил)-3-аминопропилтриметоксисилана и 43,2 г (2,4 моль ) воды. При нагревании и перемешивании отгонку проводили через аспиратор до достижения внутренней температуры 60°С. Получали бледно-желтый прозрачный раствор (средневесовая молекулярная масса 900).Содержание остаточного метанола в растворе составляло 1% по массе. Обозначается Repellent 6.
Сравнительный пример 2 [0125] Смесь 10,5 г (0,04 моль) децилтриметоксисилана, 8,8 г метанола, 0,8 г уксусной кислоты и 2,2 г (0,12 моль) воды перемешивали в течение одного часа при 25°С с получением прозрачного раствора.
[0126] В четырехгорлую колбу вместимостью 500 мл, снабженную холодильником, термометром и капельной воронкой, помещают 85 г (0.37 моль в пересчете на димер) метилтриметоксисиланового олигомера и 170 г метанола. При перемешивании к шихте по каплям добавляли полученный выше гидролизат децилтриметоксисилана, который перемешивали в течение часа при 25°С. Затем к раствору добавляли 5,1 г уксусной кислоты и 6,7 г (0,37 моль) воды, перемешивали в течение еще одного часа при 25°С. Затем по каплям добавляли 17,8 г (0,08 моль) N-(2-аминоэтил)-3-аминопропилтриметоксисилана. Реакционный раствор нагревали до температуры кипения метанола и реакцию проводили в течение одного часа.С прикрепленным сложноэфирным адаптером метанол отгоняли до тех пор, пока внутренняя температура не достигала 110°С. Получали бледно-желтый прозрачный раствор (средневесовая молекулярная масса 1300). Содержание остаточного метанола в растворе составляло 8% по массе. Обозначается Repellent 7.
Сравнительный пример 3 [0127] В четырехгорлую колбу объемом 500 мл, снабженную холодильником, термометром и капельной воронкой, загружают 85 г (0,37 моль в пересчете на димер) метилтриметоксисиланового олигомера и 8. 9 г (0,04 моль) N-(2-аминоэтил)-3-аминопропилтриметоксисилана. При перемешивании к шихте добавляли 5,1 г уксусной кислоты, которую перемешивали в течение часа при 25°С. Получали 98 г бледно-желтого прозрачного раствора. Была предпринята попытка разбавить 10 частей композиции 90 частями воды, но сразу после разбавления образовался гель.
[0128] В четырехгорлую колбу вместимостью 500 мл, снабженную холодильником, термометром и капельной воронкой, помещают 85 г (0.37 моль в пересчете на димер) олигомера метилтриметоксисилана и 8,9 г (0,04 моль) N-(2-аминоэтил)-3-аминопропилтриметоксисилана. При перемешивании к шихте добавляли 6,8 г (0,37 моль) воды. Хотя раствор пытались перемешивать в течение 3 часов при 60°С, реакционный раствор загущал после одного часа реакции.
Сравнительный пример 5 [0129] В четырехгорлую колбу емкостью 1 л, снабженную холодильником, термометром и капельной воронкой, помещают 150 г (1.1 моль) метилтриметоксисилана, 100 г (0,41 моль) 3,4-эпоксициклогексилэтилтриметоксисилана и 20 г (0,09 моль) N-(2-аминоэтил)-3-аминопропилтриметоксисилана. При перемешивании к шихте по каплям в течение 30 мин добавляли смесь 100 г (5,55 моль) воды и 200 г метанола. Раствор перемешивали еще в течение одного часа при 60°С для реакции. Получали 567 г бледно-желтого прозрачного раствора. Была предпринята попытка разбавить 10 частей композиции 90 частями воды, но сразу после разбавления образовался гель.
[0130] Композиция, полученная смешиванием 10 частей Репеллента 1, синтезированного в Примере 1, и 0,5 части 3-(триметоксисилил)пропилоктадецилдиметиламмония с 89,5 частями воды и растворением в ней, обозначена как Репеллент 8.
Пример 7[0131] Композиция, полученная смешиванием 10 частей Репеллента 1, синтезированного в Примере 1, и 2 частей борной кислоты с 88 частями воды и растворением в ней, обозначена как Репеллент 9.
[0132] Оценка стабильности при хранении
[0133] Пластиковые контейнеры загружали растворами по 10 частей каждого из репеллентов 1-7 (синтезированных в примерах 1-5 и сравнительных примерах 1-2), разбавленных 90 частями воды, и репеллентов 8 и 9 (полученных в примерах 6 и 7). Стабильность при хранении исследовали при комнатной температуре и 40°C. Результаты представлены в Таблице 1. 3 ТАБЛИЦА 1 Внешний вид репеллента в готовом виде Хранение при комнатной температуре Хранение при 40°C.1 слабомутный, прозрачный ≧180 дней ≧120 дней 2 слабомутный, прозрачный ≧180 дней ≧120 дней 3 слабомутный, прозрачный ≧180 дней ≧120 дней 4 слабомутный, прозрачный ≧180 дней ≧ 120 дней 8 слегка мутный, прозрачный ≧180 дней ≧120 дней 9 слегка мутный, прозрачный ≧180 дней ≧120 дней 5 желтый, прозрачный ≧180 дней ≧120 дней 6 слегка мутный, прозрачный гелеобразование на 120-м день 80-й день 7-й день белый мутный желированный на 14-й день 5-й день
[0134] Используйте Пример 1
[0135] Растворы 10 частей репеллентов 1-7 (полученных в примерах 1-5 или сравнительных примерах 1-2), разбавленных 90 частями воды, наносили распылением на листы простой бумаги весом 70 г/м2, которые пропускали между пара нагревательных валов для сушки. Выяснилось, что репелленты проникли внутрь листов обычной бумаги. Все листы обработанной бумаги (образцы №№ 1-6) были гладкими и содержали 4,0 г/м2 силоксана (в расчете на твердые вещества).
[0136] С помощью струйного принтера PM-750C (Seiko Epson Co., Ltd.) на листах обработанной бумаги печатали цветные изображения. После высыхания краски отпечатанные листы визуально наблюдали, были ли они деформированы или насколько четкими были отпечатанные изображения. Критерии оценки деформации и остроты приведены ниже.Результаты представлены в таблице 2.
[0137] (1) Обесцвечивание обработанной бумаги
[0138] ◯: без обесцвечивания
[0139] &Dgr;: несколько обесцвеченный
[0140] X: обесцвеченный
[0141] (2) Деформация обработанной бумаги
[0142] ◯: без деформации или куколки
[0143] &Dgr;: немного моллюсков
[0144] X: отмеченные моллюски
[0145] (3) Резкость напечатанного изображения
[0146] ◯: очень острый без кровотечения
[0147] &Dgr;: небольшое кровотечение
[0148] X: заметное кровотечение 4 ТАБЛИЦА 2 Репеллент Изменение цвета Деформация Резкость Примеры 1 ◯ ◯ ◯ 2 ◯ ◯ ◯ 3 ◯ ◯ ◯ 4 ◯ ◯ ◯ 5 ◯ ◯ ◯ Сравнительный анализ 6 &Dgr; &Dgr; &Dgr; Примеры 7 X ◯ Х
[0149] Используйте Пример 2
[0150] Кусочки кирпича погружали в растворы из 5 частей репеллентов 1-7 (полученных в примерах 1-5 и сравнительных примерах 1-2), разбавленных 95 частями воды (обозначенных ингибиторами водопоглощения 1-7) и выдерживали в них, вынимали и сушат на воздухе в течение одной недели при комнатной температуре, получая опытные образцы. Были проведены испытания образцов описанными ниже методами для изучения состояния поверхности, ингибирования водопоглощения, глубины проникновения и водоотталкивающих свойств. Результаты представлены в таблице 3.
[0151] В другом опыте куски кирпича погружали в растворы из 5 частей репеллентов 1-7 (полученных в примерах 1-5 и сравнительных примерах 1-2) и 0,5 части силиконового поверхностно-активного вещества, модифицированного полиэфиром (KF640 производства Shin-Etsu Chemical Co.). ., Ltd.), разбавленных 95 частями воды (обозначенных как ингибиторы водопоглощения от 1′ до 7′) и выдержанных в ней, вынутых и высушенных на воздухе в течение одной недели при комнатной температуре, с получением испытуемых образцов.Были проведены испытания образцов описанными ниже методами для изучения состояния поверхности, ингибирования водопоглощения, глубины проникновения и водоотталкивающих свойств. Результаты представлены в таблице 4.
[0152] В следующем цикле кирпичи погружали в водный раствор 0,5 части модифицированного полиэфиром силиконового поверхностно-активного вещества (KF640 от Shin-Etsu Chemical Co. , Ltd.) в 99,5 части воды на 5 минут в качестве предварительной обработки, затем погружали в ингибиторах водопоглощения 1-7 и выдерживали в них, вынимали и сушили на воздухе в течение одной недели при комнатной температуре, получая тестовые образцы.Были проведены испытания образцов описанными ниже методами для изучения состояния поверхности, ингибирования водопоглощения, глубины проникновения и водоотталкивающих свойств. Результаты представлены в таблице 5.
[0153] (a) Состояние поверхности, ингибирование водопоглощения
[0154] Образец кирпича размером 50×50×25 мм погружали в водный раствор репеллента на 30 секунд так, чтобы обеспечить покрытие 100 г/м2 репеллента по всей поверхности образца.Образец выдерживался в течение 7 дней в атмосфере с относительной влажностью 50%. Состояние поверхности образца наблюдали визуально и оценивали в соответствии со следующим критерием. Затем образец погружали в городскую воду на 28 дней, после чего рассчитывали процент водопоглощения.
[0155] Рейтинг состояния поверхности
[0156] ◯: нет смоченного цвета
[0157] X: смоченный цвет 1 Water ⁢ &Это; поглощение ⁢ &Это; ( % ) = ⁢ [(вес ⁢ ⁢ из ⁢ ⁢ кирпич ⁢ ⁢ после ⁢ ⁢ вода ⁢ ⁢ впитывание) — ⁢ (вес ⁢ ⁢ из ⁢ ⁢ кирпич⁢ ⁢ до ⁢ ⁢ вода ⁢ ⁢ впитывание) ] / ⁢ (вес ⁢ ⁢ из ⁢ ⁢ кирпича ⁢ ⁢ до ⁢ ⁢ водопоглощения ) × 100
[0158] (b) Глубина проникновения
[0159] Образец кирпича, который был погружен и состарен, как в испытании (а), разрезали на две половины.На разрез наносили воду так, чтобы затвердевший слой был хорошо виден. Измерялась глубина проникновения от поверхности.
[0160] (c) Водоотталкивающие свойства
[0161] Каплю воды объемом 0,5 см3 капали на поверхность образца кирпича, который был погружен в воду и состарен, как в испытании (а), после чего состояние капли наблюдали и оценивали в соответствии со следующим критерием. 5 ТАБЛИЦА 3. Водопроницаемость. Водопоглощение. 0.5 10,0 ◯ 2 ◯ 0,8 9,0 ◯ 3 ◯ 1,0 8,0 ◯ 4 ◯ 1,2 7,0 ◯ 5 ◯ 0,5 11,0 ◯ Сравнительный 6 X 12,0 0,2 X Пример 7 ◯ 4,0 2,0 &Dgr; ◯: большой контактный угол (хорошая водоотталкивающая способность) &Dgr;: умеренный контактный угол X: водопоглощение
[0162] 6 ТАБЛИЦА 4. Водопроницаемость. Водопоглощение. 0.4 25,0 ◯ 2′ ◯ 0,5 17,0 ◯ 3′ ◯ 0,8 18,0 ◯ 4′ ◯ 0,9 15,0 ◯ 5′ ◯ 0,4 30,0 ◯ Сравнительный 6′ X 10,0 3,0 X Пример 7′ ◯ 3,5 2,0 &Dgr;
[0163] 7 ТАБЛИЦА 5. Водопроницаемость. Водопоглощение. 0,4 26,0 ◯ 2 ◯ 0,6 17,0 ◯ 3 ◯ 0,7 17,0 ◯ 4 ◯ 0.9 14,0 ◯ 5 ◯ 0,4 29,0 ◯ Сравнительный 6 X 10,0 2,0 X Пример 7 ◯ 4,0 2,0 &Dgr;
[0164] Используйте пример 3
[0165] Куски дерева погружали в растворы 2,5 частей репеллентов 1-7 (полученных в примерах 1-5 и сравнительных примерах 1-2), разбавленных 97,5 частями воды (обозначенных ингибиторами абсорбции 8-14) и растворами 25 частей репеллентов 8. и 9 (полученные в примерах 6 и 7), разбавленные 75 частями воды (обозначенные как ингибиторы абсорбции 15 и 16) и выдержанные в ней, вынутые и высушенные на воздухе в течение одной недели при комнатной температуре, с получением испытуемых образцов.Были проведены испытания образцов описанными ниже способами для изучения обесцвечивания поверхности и ингибирования водопоглощения. Результаты представлены в таблице 6.
[0166] В другом опыте деревянные детали погружали в растворы, содержащие 2,5 части репеллентов 1-7 (полученных в примерах 1-5 и сравнительных примерах 1-2) и 0,5 части силиконового поверхностно-активного вещества, модифицированного полиэфиром (KF640 производства Shin-Etsu Chemical Co.). ., Ltd.), разбавленных 97,5 частями воды (обозначенных как ингибиторы водопоглощения от 8′ до 14′) и выдержанных в ней, вынутых и высушенных на воздухе в течение одной недели при комнатной температуре, с получением испытуемых образцов.Были проведены испытания образцов описанными ниже способами для изучения обесцвечивания поверхности и ингибирования водопоглощения. Результаты представлены в таблице 7.
[0167] В следующем цикле деревянные детали погружали в водный раствор 0,5 части модифицированного полиэфиром силиконового поверхностно-активного вещества (KF640 от Shin-Etsu Chemical Co., Ltd.) в 99,5 части воды на 5 минут в качестве предварительной обработки, затем погружали в ингибиторах водопоглощения 8-14 и выдерживали в ней, вынимали и сушили на воздухе в течение одной недели при комнатной температуре, получая тестовые образцы.Были проведены испытания образцов описанными ниже способами для изучения обесцвечивания поверхности и ингибирования водопоглощения. Результаты представлены в таблице 8.
[0168] (a) Изменение цвета поверхности, ингибирование водопоглощения
[0169] Образец кедра 50×50×21 мм и образец лауана 50×50×21 мм целиком погружали в водный раствор репеллента на 24 часа при комнатной температуре и атмосферном давлении. Образцы выдерживались в течение 7 дней при комнатной температуре.Поверхность образцов визуально наблюдали на предмет обесцвечивания или пожелтения и оценивали в соответствии со следующим критерием. Затем образцы целиком погружали в городскую воду на 24 часа, после чего рассчитывали процент водопоглощения.
[0170] Обесцвечивание поверхности
[0171] ◯: без обесцвечивания
[0172] &Dgr;: слегка обесцвеченный
[0173] X: обесцвеченный
[0174] Ингибирование водопоглощения 2 Вода ⁢ &Это; поглощение ⁢ &Это; ( % ) = ⁢ [(вес ⁢ ⁢ из ⁢ ⁢ дерева ⁢ ⁢ после ⁢ ⁢ воды ⁢ ⁢ поглощения) — ⁢ (вес ⁢ ⁢ из ⁢ ⁢ дерева ⁢ ⁢ до⁢ ⁢ вода ⁢ ⁢ впитывание) ] / ⁢ (вес ⁢ ⁢ из ⁢ ⁢ древесины ⁢ ⁢ до ⁢ ⁢ водопоглощения ) × 100 8 8 ◯ ◯ 10 8 9 ◯ ◯ 15 12 10 ◯ ◯ 11 9 11 ◯ ◯ 13 10 12 ◯ ◯ 10 9 15 ◯ ◯ 11 9 16 ◯ ◯ 11 10 Com- 13 X X 47 45 паранативный 14 &Dgr; &Dgr; 33 26 Пример — ◯ ◯ 67 55 (городская вода)
[0175] 9 ТАБЛИЦА 7 Водопоглощение Водопоглощение Поглощение Изменение цвета поверхности (мас. %) Ингибитор образца Кедр Лауан Кедр Лауан Пример 8′ ◯ ◯ 8 6 9′ ◯ ◯ 10 8 10′ ◯ ◯ 7 7 11′ ◯ ◯ 11 9 12′ ◯ ◯ 8 5 Сравнительный 13′ X X 37 33 Пример 14′ &Dgr; &Dgr; 23 19
[0176] 10 ТАБЛИЦА 8 Водопоглощение Водопоглощение Абсорбция Изменение цвета поверхности (мас. %) Образец ингибитора Кедр Лауан Кедр Лауан Пример 8 ◯ ◯ 8 6 9 ◯ ◯ 9 7 10 ◯ ◯ 8 8 11 ◯ ◯ 10 9 12 ◯ ◯ 7 5 Сравнительный 13 X X 35 31 Пример 14 &Dgr; &Dgr; 24 20
[0177] Используйте пример 4
[0178] Кусочки древесины погружали в растворы 25 частей репеллентов 8 и 9 (полученных в примерах 6 и 7), разбавленных 75 частями воды, выдерживали в них, сушили на воздухе при комнатной температуре в течение одной недели, получая тестовые образцы.Они были подвергнуты тесту на гниение древесины и тесту на гибель термитов, как описано ниже. Результаты представлены в таблице 9.
[0179] (a) Тест на гниение древесины с использованием грибов белой и бурой гнили
[0180] Для изучения антибактериальной/противогрибковой активности было проведено испытание на гниение древесины, состоящей из неорганических веществ, в соответствии со стандартом Японской ассоциации по консервации древесины (JWPA), № 3 (1992), «Метод испытания на долговечность деревянного материала». После этого образцы для испытаний сушили и стерилизовали при 60°С.на 48 часов их помещали на полностью обработанные газоны с грибком белой гнили Coriolus versicolor (L. ex Fr.) Quel (IFO 30340) и грибом бурой гнили Tyromyces palustris (Berk. et Curk. Murr.) (IFO 303390). выращивают в культуральной посуде в стеклянной посуде. После культивирования в инкубаторе при комнатной температуре (26°С) и относительной влажности от 55 до 65% в течение 8 недель образцы извлекали и стирали с поверхности грибковые клетки. Определяли абсолютную сухую массу испытуемых образцов.По абсолютной сухой массе испытуемых образцов перед испытанием рассчитывали процентную потерю массы из-за древесной гнили.
[0181] (b) Тест на подземное гниение
[0182] Необработанные образцы древесины и образцы древесины, обработанные водоотталкивающим средством, подвергали экстракции по Сокслету ацетоном и водой каждый в течение 24 часов. Подземный опыт закапывания образцов в нестерилизованный грунт на глубину 17 см от поверхности земли проводился в течение 9 месяцев. Потеря веса в процентах рассчитывалась по абсолютному сухому весу каждого образца до и после испытания на закапывание, исходя из которого предполагалось развитие разложения.
[0183] (c) Тест на гибель термитов.
[0184] По двести (200) особей домашних термитов помещали в каждый из контейнеров с необработанной древесиной и обработанной водоотталкивающим составом древесиной и оставляли там на 20 дней, после чего определяли смертность термитов. 11 ТАБЛИЦА 9 Древесная гниль с грибами (%) Древесная гниль по Кедр Лауан подземный Термит Белый Коричневый Белый Коричневый тест смертность гниль гниль гниль гниль (%) (%) Образец гриб гриб гриб гриб гриб Кедр Лауан Кедр Лауан Изобретение Репеллент 8 0.7 0,4 0,8 0,3 2,1 2,8 35 33 Репеллент 9 2,2 1,5 3,1 2,0 8,9 7,5 100 100 Сравнение — 3,0 3,1 4,1 4,3 25,0 29,3 23 25 (городская вода)
Пример 8 [0185] Используемый образец для испытаний представлял собой ламинированный пиломатериал из шпона, изготовленный с использованием сосны лучистой из Новой Зеландии в качестве исходного материала. Образец для испытаний был покрыт и пропитан водоотталкивающим средством перед измерением для предотвращения водопоглощения и стабильности размеров.
[0186] Подготовку клееного бруса, покрытие и пропитку, а также измерение предотвращения водопоглощения и размерной стабильности проводили следующим образом.
[0187] Используя шпон сосны Radiata толщиной 3 мм, обычным способом был изготовлен клееный брус из 9 слоев шпона, имеющий толщину 27 мм, ширину 300 мм и направление волокон 300 мм. Выдерживался 7 дней. Затем одну клееную фанеру разрезали на три части шириной 100 мм и направлением волокон 300 мм. Испытываемые образцы сушили обдувом горячим воздухом при 105°С в течение 2 часов, а затем наносили кистью на все поверхности (6 сторон) водным раствором, содержащим 2% Репеллента 1, для пропитки.Пропитанная масса составляла 200 г/м2. Затем испытуемые образцы выдерживались еще 10 дней, после чего они подвергались испытаниям, описанным ниже как испытания 1 и 2.
Сравнительный пример 6 [0188] Используя шпон сосны Radiata толщиной 3 мм, обычным способом был изготовлен клееный брус из 9 слоев шпона, имеющий толщину 27 мм, ширину 300 мм и направление волокон 300 мм. Выдерживался 7 дней. Затем одну клееную фанеру разрезали на три части шириной 100 мм и направлением волокон 300 мм.Образцы для испытаний сушили обдувом горячим воздухом при 105°С в течение 2 часов и выдерживали еще 10 дней, после чего подвергали испытаниям, описанным ниже как Испытания 1 и 2.
[0189] Тест 1
[0190] Ламинированный брус из шпона, полученный в Примере 8 и Сравнительном примере 6, погружали в воду при комнатной температуре на 32 часа, вынимали и сушили обдувом горячим воздухом при 40°С в течение 16 часов. Далее их погружали в воду комнатной температуры на 24 часа.Во время процесса через соответствующие интервалы времени измеряли вес, толщину и ширину образцов для испытаний, исходя из которых рассчитывали процент водопоглощения и набухание по толщине и ширине, получая результаты, показанные на фиг. 3-5. Следует отметить, что процент водопоглощения и набухание по толщине и ширине рассчитывали в соответствии со следующими уравнениями.
Водопоглощение(%)=[(Wt-Wo)/Wo×100
[0191] Вес: вес (г) испытуемого образца после истечения времени t
[0192] Wo: вес (г) испытательного образца перед началом испытания
Толщина набухания (%)=[(Tt-To)/To×100
[0193] Tt: толщина (мм) образца для испытаний по истечении времени t
[0194] До: толщина (мм) испытательного образца перед началом испытания
Ширина набухания (%)=[(WIt−WIo)/WIo×100
[0195] WIt: ширина (мм) образца для испытаний по истечении времени t
[0196] WIo: ширина (мм) испытательного образца до начала испытания
[0197] Тест 2
[0198] Ламинированные пиломатериалы из шпона, приготовленные в Примере 8 и Сравнительном примере 6, погружали в воду при комнатной температуре на 30 минут, вынимали и оставляли при комнатной температуре на 8 часов в таких условиях, чтобы вода не могла испаряться изнутри испытуемого образца. Далее их погружали в воду комнатной температуры на 30 минут, вынимали и оставляли стоять при комнатной температуре на 16 часов. Во время процесса через соответствующие интервалы времени измеряли вес, толщину и ширину образцов для испытаний, исходя из которых рассчитывали процент водопоглощения и набухание по толщине и ширине, получая результаты, показанные на фиг. 6–8. Расчетные уравнения, используемые при расчетах, такие же, как описано в тесте 1.
[0199] Используемый образец для испытаний представлял собой пятислойную фанеру из сосны лучистой толщиной 12 мм (конструкция шпона: 1.8+3,3+1,8+3,3+1,8 мм), шириной 50 мм и длиной 50 мм. Образец для испытаний был предварительно высушен обдувом горячим воздухом при 120°С в течение 2 часов. Массу испытуемого образца измеряли сразу после предварительной сушки, то есть массу до начала испытания. В этот момент на все поверхности испытуемого образца наносили водный раствор, содержащий 2% репеллента 1, с массой покрытия 200 г/м2. Испытываемый образец выдерживали в течение 10 дней, погружали в воду комнатной температуры на 32 часа.В ходе процесса через соответствующие интервалы времени измеряли массу испытуемого образца, исходя из которого рассчитывали процент водопоглощения в соответствии с приведенным ниже уравнением. Результаты показаны на фиг. 9.
Водопоглощение(%)=[(Wt-Wo)/Wo×100
[0200] Вес: вес (г) испытуемого образца после истечения времени t
[0201] Wo: вес (г) испытательного образца перед началом испытания
Сравнительный пример 7[0202] Та же фанера, что и в примере 9, была погружена в воду при комнатной температуре на 32 часа.Во время процесса через подходящие интервалы времени измеряли массу испытуемого образца, исходя из которого рассчитывали процент водопоглощения в соответствии с тем же уравнением, которое использовалось в примере 9. Результаты также показаны на фиг. 9.
Пример 10 [0203] Водный раствор с заданной концентрацией репеллента 1 распыляли к древесным волокнам, полученным с помощью дефибриллятора высокого давления непрерывной варки, в таких количествах, чтобы обеспечить 0. 2 г, 0,5 г или 1 г Репеллента 1 на 100 г массы древесно-сухого волокна с последующей сушкой. После этого была сформирована древесноволокнистая плита средней плотности путем термокомпрессионного формования древесных волокон в обычных условиях с использованием универсального клея. После старения древесноволокнистой плиты определяли удельную внутреннюю прочность сцепления, удельную прочность на изгиб, удельный модуль Юнга при изгибе, набухание по толщине за счет водопоглощения рассчитывали в соответствии с методом испытания древесноволокнистой плиты JIS A5905 и набухание по толщине с помощью испытания в горячей воде (погружение в горячая вода 70°С.за 2 часа). Результаты представлены в таблице 10. Отмечено, что удельная прочность внутреннего сцепления, удельная прочность на изгиб и удельный модуль Юнга при изгибе представляют собой прочность внутреннего сцепления, прочность на изгиб и модуль Юнга при изгибе, деленные на удельный вес испытуемого образца. , соответственно.
[0204] Древесноволокнистую плиту получали, используя те же древесные волокна, что и в примере 10, и добавляя заданное количество обычно используемого акрилового воска вместо вышеупомянутого реагента. После этого значения производительности были рассчитаны теми же методами, что и в примере 10. Результаты также показаны в таблице 10.
[0205] Репеллент 1 смешивали с клеем таким образом, чтобы 10 г, 15 г или 20 г Репеллента 1 приходилось на 100 г высушенного в печи веса древесных волокон, полученных с помощью дефибриллятора высокого давления непрерывной варки с последующей сушкой. После этого формовали древесноволокнистую плиту средней плотности путем термокомпрессионного формования древесных волокон в обычных условиях.После старения древесноволокнистой плиты удельную внутреннюю прочность сцепления, удельную прочность на изгиб, удельный модуль Юнга при изгибе, набухание по толщине за счет водопоглощения рассчитывали в соответствии с методом испытания древесноволокнистой плиты JIS A5905 и набухание по толщине с помощью испытания в горячей воде (погружение в горячей воды при 70°С в течение 2 часов). Результаты представлены в таблице 11. Отмечено, что удельная прочность внутреннего сцепления, удельная прочность на изгиб и удельный модуль Юнга при изгибе представляют собой прочность внутренней связи, прочность на изгиб и модуль Юнга при изгибе, деленные на удельный вес испытуемого образца. , соответственно.
[0206] Древесноволокнистую плиту получали, используя те же древесные волокна, что и в примере 11, и добавляя заданное количество обычно используемого акрилового воска вместо вышеупомянутого реагента. После этого значения производительности были рассчитаны теми же методами, что и в примере 11. Результаты также показаны в таблице 11.
[0207] Из этих результатов видно, что по сравнению с древесноволокнистыми плитами из сравнительных примеров 8 и 9, древесноволокнистые плиты из примеров 10 и 11, подпадающие под объем изобретения, имеют улучшенные показатели удельной прочности внутреннего соединения, удельной прочности на изгиб и удельной внутренней прочности. модуль Юнга связи при изгибе, несмотря на примерно равные значения водостойкости (размерной стабильности).12 ТАБЛИЦА 10 Количество реагента Толщина добавляемого Толщина набухания на 100 г Удельная Удельная Удельная набухаемость после внутренней сушки в печи Удельная Модуль Юнга горячей деревянной связки Модуль изгиба в воде Прочность водных волокон Прочность на изгиб испытание на абсорбцию (г) (Н/мм2) (Н/мм2 ) (103 Н/мм2) (%) (%) Пример 10 0,2 1,36 82 7,3 6,1 28,9 0,5 1,20 76 6,9 5,8 27,5 1,0 1,06 70 6,2 5,1 27,3 Сравнительный воск 0,66 60 5,9 5,0 27,1 Пример 8 9000
[0208] 13 ТАБЛИЦА 11 Количество реагента Толщина добавленная толщина Толщина набухания на 100 г Удельная Удельная Удельная набухаемость после внутренней сушки в печи Удельная Модуль Юнга горячей деревянной связки Модуль изгиба в воде Прочность водных волокон Прочность на изгиб испытание на абсорбцию (г) (Н/мм2) (Н/мм2 ) (103 Н/мм2) (%) (%) Пример 11 10 1. 26 80 7,4 6,4 30,3 15 1,14 74 7,2 5,9 28,6 20 0,98 70 6,6 5,1 27,4 Парафин для сравнения 0,71 62 6,1 4,9 26,2 Пример 9
[0209] Водный гидрофобизатор согласно изобретению обладает улучшенной растворимостью в воде и стабильностью при хранении, и его можно использовать в качестве гидрофобизатора для нейтральных субстратов просто после разбавления водой. Нейтральные подложки, на которые нанесен или пропитан репеллент, обладают удовлетворительными водоотталкивающими свойствами и стабильностью размеров.
[0210] С использованием водоотталкивающего средства, упомянутого выше, способ получения модифицированной фанеры или модифицированного клееного бруса из шпона в соответствии с изобретением может сделать фанеру или клееный брус из шпона стойкими к термитам, гниению, плесени, водостойким, влагостойким и стабильным по размеру. в соответствии с желаемыми характеристиками на конкретном участке обслуживания, без ущерба для пористости, малого удельного веса и простоты обработки (обрабатываемость, удержание гвоздя, адгезия, окрашиваемость и т. д.).) присущие деревянным панелям.
[0211] Кроме того, способ изготовления древесноволокнистых плит в соответствии с изобретением предусматривает управление процессом на заводе-изготовителе, что позволяет эффективно выполнять операцию пропитки, предотвращая при этом увеличение производственных затрат.
[0212] Кроме того, изобретение позволяет производить в массовом масштабе модифицированную фанеру и пиломатериалы из клееного шпона, которые можно использовать в качестве элементов строительных конструкций, отвечающих требованиям Закона о новых строительных стандартах Японии, или в качестве элементов внутренней и внешней отделки зданий, и при утилизации они оказывают меньшую нагрузку на окружающую среду.
[0213] Кроме того, изобретение предлагает способ изготовления древесноволокнистой плиты, в котором древесноволокнистая плита с улучшенными прочностными характеристиками при сохранении водонепроницаемости может быть изготовлена с высокой производительностью и низкой стоимостью.
Ламинированная фанера
Ламинированная фанераФанеру ламинированную также называют опалубочной фанерой, опалубочной фанерой, опалубкой.
Фанера ламинированная – это специальная фанера, покрытая с двух сторон износостойкой и водоотталкивающей пленкой.Пленка представляет собой пропитанную клеем бумагу, которая отличается от меламиновой бумаги, ПВХ, МДО ( фанера МДО ) и HDO (фанера HDO). Функция пленки заключается в защите внутренней древесины от влаги, воды, непогоды и продлении срока службы фанеры. Фанера ламинированная может использоваться в суровых и наружных условиях: фанера опалубочная , опалубочная фанера, опалубка для бетона, половая доска, автостроение.
Спецификация ламинированной фанеры (1).Цвет пленки: коричневый, черный или другие Наиболее распространенной пленкой является коричневая пленка или черная пленка. В Китае коричневая ламинированная фанера обычно имеет лучшее качество, чем черная ламинированная фанера. Однако это не всегда так. Некоторая фанера с черным ламинированным покрытием имеет такое же высокое качество, как фанера с коричневым ламинированным покрытием. Когда вы делаете запрос, опытный продавец будет знать, какое реальное качество вам нужно.
В Китае существует 2 классификации пленки: местная пленка и импортная пленка.Под местным фильмом подразумеваются фильмы, сделанные китайскими компаниями. Импортная пленка означает пленку, произведенную иностранными компаниями, такими как Dynea. Пленка Dynea — лучший бренд пленки в Китае. Поэтому, если вам нужна лучшая пленка для вашей фанеры, мы будем использовать пленку Dynea.
(3). Сердцевина: тополь, твердая древесина, эвкалипт, береза 70% ламинированной фанеры, которую мы продаем, составляет ламинированная фанера из тополя , которая отличается высоким качеством и конкурентоспособной ценой. Если вам нужна ламинированная фанера из лиственных пород, мы используем шпон из лиственных пород или эвкалипта.Если вам нужна ламинированная фанера для строительства мостов или высотных зданий, вы можете выбрать ламинированную фанеру из твердой древесины , как следует из ее названия, она очень твердая. Мы также поставляем березовую ламинированную фанеру , которая также является твердой и прочной.
Мы используем эти 3 вида клея. Что касается знаний о клее, вы можете обратиться к следующим статьям:
Что такое клей MR — который обычно используется для фанеры / ламинированной фанеры / столярных плит
Что такое клей WBP — который обычно используется для фанеры WBP / ламинированной фанеры
Мы производим размеры в соответствии с требованиями клиентов. Самый широкий размер может быть 2000 мм, максимальная длина 6000 мм.
Мы поставляем очень тонкую ламинированную фанеру толщиной 4 мм и самую толстую фанеру толщиной до 50 мм. Это наше преимущество.
(6).Упаковка: Стандартная упаковка.Наша упаковка является стандартной морской упаковкой.
Применение ламинированной фанеры (1) Строительная промышленность: опалубочная фанера с пленочным покрытием, бетонная опалубка, опалубочная бетонная опалубка, опалубочная фанера Фанера ламинированная в основном используется в строительстве. Поэтому фанеру с пленочным покрытием также называют опалубочной фанерой, бетонной опалубкой, опалубочной бетонной опалубкой. Из-за этого конечного использования клиенты обычно хотят фанеру с пленочным покрытием WBP, которая больше подходит для использования в качестве опалубки для крупных проектов. Тем не менее, некоторым клиентам требуется ламинированная фанера MR, которая используется в качестве опалубки для обычных проектов.
В зависимости от типа лицевой/обратной стороны фанеру с пленочным покрытием можно разделить на гладкую фанеру с пленочным покрытием и фанеру с противоскользящим покрытием. Фанера, облицованная противоскользящей пленкой, обычно используется в качестве напольного покрытия для транспортных средств, грузовиков и платформ.
(3) Ламинированная фанера также может быть использована для полок и мебели.По сравнению с фанерой, облицованной деревянным шпоном, фанера с пленочным покрытием более долговечна и имеет более износостойкую поверхность. Так что его можно использовать для изготовления прочной мебели и полок.
ПОКРЫТИЯ ДЛЯ ДЕРЕВА НА ВОДНОЙ ОСНОВЕ ПОЛНОЕ РУКОВОДСТВО
Характеристики покрытий на водной основе
Покрытия на водной основе Hydroplus предназначены для уменьшения поглощения влаги и солнечного излучения. Таким образом, они гарантируют преимущества с точки зрения устойчивости к внешним воздействиям и сокращения выбросов растворителей.
Прозрачные и пигментированные тиксотропные верхние покрытия Hydroplus обладают хорошей эластичностью, отсутствием явлений слипания , хорошей вертикальной стойкостью, отличным растяжением и хорошей стойкостью к осаждению олова.
Долговечность всегда была первым критерием при оценке деревянных покрытий для наружных работ .
Благодаря продуктам на водной основе Hydroplus долговечность деревянных окон с покрытием стала значительным шагом вперед.Продолжительность снаружи выше.
В отличие от покрытий на основе растворителей, покрытия для дерева на водной основе сохраняют высокую степень эластичности с течением времени, что позволяет пленке краски повторять движения древесины, не повреждаясь. Многие верхние покрытия Hydroplus являются тиксотропными . Эта функция позволяет наносить продукт большой толщины, сохраняя превосходный уровень релаксации и прозрачности.
Чтобы гарантировать хорошую устойчивость к внешним воздействиям, прозрачные продукты серии Hydroplus были разработаны с оптимальной дозой поглотителей УФ-излучения , которые предотвращают прямое попадание УФ-излучения на древесину и уменьшают потерю цвета древесины. древесина , таким образом избегая деградации.
Лакированные покрытия содержат очень непрозрачных пигмента, устойчивых к солнечному свету . HYDRO GOLD представляет новейшую линейку покрытий для наружных работ: международный патент и гарантия долговечности до 18 лет.
Покрытия Hydroplus, выбранные для СИСТЕМЫ ANTI-AGE, разработаны для обеспечения максимальной защиты дерева и лакокрасочного покрытия: эти акриловые покрытия гарантируют 10-летнюю долговечность наружным дверям и окнам, покрытым выбранными для этой цели системами покрытий Hydroplus. .
В покрытии мебели и ее компонентов эстетический результат имеет основополагающее значение. Покрытие древесины продуктами на водной основе Hydroplus позволяет получить отделку, которая благодаря своему внешнему виду и мягкости неотличима от тех, которые получаются продуктами на основе растворителей.
На самом деле они гарантируют уровень механической и химической стойкости , сравнимый с уровнем полиуретановых покрытий .
«Использование покрытия на водной основе означает выбор типа продукта, который является более экологичным и снижает выброс вредных веществ» За последние несколько лет возросла забота об окружающей среде, забота о здоровье операторов и конечных потребителей . Мебель с экологически совместимой отделкой пользуется все большим спросом и, следовательно, с минимально возможным выделением растворителей, как во время нанесения покрытия, так и во время фазы медленной окончательной сушки.
Маляры должны использовать продукты, содержащие минимум вредных веществ, чтобы гарантировать бережное отношение к окружающей среде .
Преимущества использования покрытий на водной основе
Однокомпонентные продукты на водной основе, особенно покрытия для дерева для внутренних работ , не имеют жизнеспособности проблем, таких как традиционные полиуретановые продукты на основе растворителей.
Они просты и практичны, потому что они готовы к использованию, а продукт можно восстановить и использовать повторно, при условии, что он будет повторно помещен в исходную банку и тщательно закрыт. Следует избегать длительного контакта с воздухом.
Когда невозможно отказаться от максимальных характеристик, обеспечиваемых добавлением изоцианового катализатора (кухни, мебель для баров и дискотек, столешницы и т. д.), можно использовать отвердители Ah2545 или Ah2550.
Эти продукты химически реагируют подобно обычным изоцианатным смолам второго компонента полиуретанов. Однако, благодаря своему особому составу, они стабилизируются и, следовательно, смешиваются с продуктом на водной основе s, гарантируя жизнеспособность до 4 часов, после чего материал становится непригодным к использованию.
Экономические преимущества:
- Уменьшение избыточного распыления до 25%.
- Восстановление избыточного распыления в автоматических системах.
- Неограниченная жизнеспособность однокомпонентных продуктов.
Экологические преимущества:
- Снижение выбросов на 95 % по сравнению с синтетическими продуктами, поэтому низкое воздействие на окружающую среду
- Улучшение рабочей среды.
Преимущества производительности:
- Отличная химическая стойкость.
- Акриловые системы с пониженным пожелтением.
- Короткое время высыхания
- Увеличенный срок службы на открытом воздухе
- Фиксация блеска
- Нежелтеющая пленка
- Без образования «корки»
- Эластичность пленки
- Высокая тиксотропность отделки
Практические преимущества:
- Готов к использованию.
- Использование воды для мытья оборудования.
- Простота использования.
- Нет проблем воспламеняемости и самовозгорания, а значит и хранения.
Покрытия для дерева на водной основе, способы нанесения и наиболее распространенные основы
Покрытия на водной основе обычно наносят распылением, валиком или кистью. Продукты Hydroplus можно наносить с помощью обычных систем распыления (баночный, безвоздушный, аэромикс, электростатический), если конструкционные материалы оборудования подходят для контакта с водой.
Доступные в различных составах и степенях блеска , покрытия на водной основе в основном используются для отделки дерева, стекла и железа , но они также дают отличные результаты на пластике, ПВХ и т. д.
Покрытия для древесины на водной основе производства Sayerlack
Прозрачная фунгицидная морилка для наружных работ – Hydroplus AM0570/00
Идеально подходит для обработки древесины, размещаемой снаружи, а соответствует европейской директиве BPR (ЕС) 528/2012 и используется для получения исключительной защиты от гниения, окрашивания древесины и деревоядных насекомых. Продукт готов к использованию и может наноситься ручным распылением, погружением, обливом . Легкое проникновение в древесину гарантирует сцепление между последовательными слоями.
Можно покрывать всеми морилками для наружных работ, грунтовками и верхними покрытиями на водной основе для наружных работ серий Hydroplus и Hydro Gold.
Антигельминтная морилка для наружных работ – XE0197 Hydroplus
Медико-хирургическое наблюдение . Рег. № 19153 Минздрава – антигельминтная морилка для наружных работ для обработки пиломатериалов, балок и арматуры. Он оснащен активными ингредиентами, предназначенными для проникновения в древесину и осуществления профилактического и лечебного действия против нападения насекомых.
При профилактической обработке арматуры, балконов, ограждений, которые должны длительное время выдерживать очень влажную среду, ХЕ0197/00 можно наносить в вакууме, погружением или кистью. Для высыхания их придется ждать от 3 до 7 дней в зависимости от случая, после чего вам нужно будет нанести пропитку и, возможно, также кроющую отделку .
Прозрачная морилка для наружных работ – AM0631/XX Hydroplus
Прозрачная морилка для наружных работ доступна в широкой цветовой гамме, подходит для покрытия беседок, заборов, деревянных домов, балконов и обшивки шпунтованной доской.
Наносится импрегнатором, а также губкой и кистью; Возможность чистить щеткой в открытом режиме позволяет легко возобновить работу даже после перерыва. Специальные акриловые смолы делают пропитку древесины чрезвычайно эффективной, придавая ей приятный внешний вид и подчеркивая текстуру.
AM0631/XX соответствует требованиям стандарта EN 71-3 – часть 3 по миграции тяжелых металлов.
Белая морилка для наружных работ – AML3390/13 Hydroplus
Белая морилка для наружных работ, наносимая с помощью автоматических пропиточных машин, высокий сухой остаток которых позволяет получить продукт с высокой укрывистостью и отличным наполнением.
Благодаря отличной точке белого AML3390/13 придает изделию хорошую стойкость и отличный эстетический результат . Идеально подходит для покрытия ферм и досок из мягкой древесины, продукт готов к использованию и может быть нанесен в один или несколько слоев для получения различной степени покрытия в зависимости от желаемой степени белизны.
Покрытие для наружных работ – AZL3497/00 Hydroplus
Верхнее покрытие для наружных работ, предназначенное для погружения в воду деревянных изделий, выставленных на улицу.Продукт позволяет легко, быстро и экономично покрывать сложные и многочисленные изделия, такие как балконные рейки.
Покрытие для наружных работ – AZ2330/86 Hydroplus
Финишное покрытие для наружных работ, наносимое кистью и распылением на окна, балконы, доски, фермы, коттеджи, заборы и т. д.
Благодаря своей эластичности и долговечности AZ2330/86 идеально подходит для наружной защиты древесины . Верхний слой содержит , в дополнение к поглотителям УФ-излучения и поглотителям радикалов, а также консерванты пленки против грибков синевы и гниения.
Супергидрофобное прозрачное верхнее покрытие на водной основе – H₂NO,
Финишное покрытие предназначено для наружных работ – беседок, настенных покрытий, уличной мебели, заборов – а также защищает древесину, сохраняя ее естественный внешний вид. AZV2317/00 Hydroplus проникает глубоко, проникая в древесные волокна и образуя гидрофобный слой, отталкивающий воду . Отделка сохраняет древесину паропроницаемой и позволяет ей обменивать содержащуюся в ней влагу. Этот механизм повышает его долговечность с течением времени и снижает вероятность атаки микроорганизмов.
AZV2317/00 подходит для вертикальных или слегка наклонных опор, чтобы облегчить поток воды. Наносится на любой пропиточный состав серии Hydroplus методом погружения, кистью, пропиточным аппаратом, валиком и безвоздушным краскопультом низкого давления.
Масло на водной основе для наружных работ – AOV3793/00
Масло на водной основе для наружных работ, характеризующееся отличной устойчивостью к внешним воздействиям, сохраняет естественную красоту дерева, легко наносится.
Идеально подходит для покрытия уличной деревянной мебели, , такой как скамейки, столы, стулья и беседки.Обеспечивает защиту от УФ-лучей, сохраняя естественный вид продукта.
Может наноситься кистью, распылителем или тряпкой в 2 или 3 слоя, в зависимости от типа обрабатываемой эссенции и желаемого эффекта. Также возможно выполнить техническое обслуживание продукта, просто повторно нанеся продукт (максимум 1-2 слоя).
Этот продукт имеет высокое содержание сырья природного происхождения (около 25%), что делает его экологически чистым.
Прозрачный верхний слой для наружных работ – AZ8130/00 Hydroplus
Однокомпонентный прозрачный продукт, обладающий исключительной долговечностью снаружи.Его следует использовать в сочетании с прозрачной базой Hydroplus и промежуточной базой, в зависимости от основы или поверхности.
AZ8130/00 – идеальное решение для защиты опоры от любых атмосферных воздействий и сохранения ее красоты.
Его сильными сторонами являются прозрачность, устойчивость к ультрафиолетовым лучам и воде, а также немедленная устойчивость к проникновению воды.
Двухкомпонентный самогерметик — AF0618/00 Hydroplus
Двухкомпонентный грунт с высокими химико-физическими характеристиками, инновационное решение необходимости усиления и сохранения характеристик натуральности, яркости и уникальности древесины.
Исключительная стойкость к полировке и царапинам, устойчивость к пятнам, моющим средствам и пожелтению под действием света позволяют использовать его во всех интерьерах.
Изоляция дубильных пород древесины превосходна настолько, что не требует обработки необработанной основы специальным изолятором. Отличные результаты могут быть получены на предварительно композитных деталях, которые исключают изменение цвета благодаря хорошей светозащите, даже на термообработанных продуктах, все чаще представленных на рынке, с использованием специального отвердителя.
Один раствор для каждого отвердителя: Ah2564/00 для светлой древесины и готовых материалов, Ah2550/00 для оживления натуральной древесины, Ah2503/00 для темных опор, чтобы улучшить прозрачность.
Сертифицированные результаты : продукт, нанесенный в два слоя на бук, протестирован в лабораториях сертификационного института CATAS, проходит испытания устойчивости поверхностей к холодным жидкостям EN 12720: 2013, достигая класса B согласно CEN/TS 16209.
Верхнее покрытие на водной основе 0 глянец под натуральное дерево – Hydroplus AT0601/00
Мягкая на ощупь финишная краска на водной основе подходит для лакировки деревянных предметов интерьера , с хорошей химической стойкостью, отличной прозрачностью и устойчивостью к письму.
Продукт характеризуется естественным эффектом и рекомендуется, если вы хотите, чтобы внешний вид дерева оставался неизменным на ощупь и на вид.
AT0601/00 можно использовать в виде однокомпонентного покрытия без отвердителя или в качестве базового покрытия непосредственно на древесине.
Самогерметизирующийся -AFL7931/00 Hydroplus
Отделка с очень низкой укрывистостью, однокомпонентная, с восковым эффектом, особенно подходящая во всех случаях, когда требуется получить натуральный эффект покрытия без покрытия.
Благодаря особому составу AFL7931/00 придает древесине приятную мягкость и ощущение на ощупь , не предполагающее наличия обработки.
Прозрачный самогерметик — Hydroplus AFL3675/00
AFL3675/00 представляет собой прозрачную грунтовку на водной основе с глянцем 35, которая также доступна в версиях с глянцем 15, 20 и 60.
Этот продукт готов к использованию, обладает хорошей тиксотропностью и хорошей прозрачностью. Он также характеризуется хорошим выравниванием и выделением пор, высокой мягкостью и прозрачностью, а также высокой тиксотропностью.
Эти свойства делают его универсальным решением. Также можно получить хороший эффект открытых пор на таких эссенциях, как дуб или ясень, нанеся 2 слоя по 100-120 г/м² каждый.
Масло на водной основе с восковым эффектом – AOV2343/00
Масло с восковым эффектом и длительным сроком годности, идеально подходит для внутренней отделки мебели.
Может наноситься распылителем, тряпкой или кистью. AOV2343/00 можно катализировать при 5%-ном содержимом с Ah2564/00, чтобы улучшить его адгезию и химическую стойкость, поддерживая высокую жизнеспособность.
Рекомендуется добавлять отвердитель для покрытия деревянных полов или обновлять уже обработанные поверхности для достижения более высоких характеристик.
AOV2343/00 можно окрашивать красителями и/или пигментами серий AC2110/XX, AC0600/XX, AC1810/XX, XA2006/XX и XA4034/XX.
Фанера WBP ⋆ 🌲 ThePlywood.com
Водостойкая фанера
Когда кто-то ищет фанеру с максимальной стойкостью к атмосферным воздействиям , важно обратить внимание на WBP . Эта аббревиатура означает «Защита от кипячения воды» или «Защита от непогоды и кипячения». стандарт, используемый для определения водостойкости фанерного изделия.На самом деле, это больше рейтинг клея , используемого при производстве фанеры, чем самой древесины.
Обратите внимание, что WBP не является отдельным типом фанеры от других; скорее, это рейтинг, который будет иметь некоторая фанера, если производитель решит протестировать ее, чтобы определить, соответствует ли она требованиям. Чаще всего это делается с фанерой морского класса, но это также может быть сделано с другими типами фанеры, которые предназначены для использования во влажной или влажной среде, например, с фенольной фанерой.
ФанераWBP не является водонепроницаемой фанерой. Изготавливается из того же шпона, что и другие виды фанеры. Этот рейтинг не означает, что он обработан давлением или пропитан смолой, как строительные пиломатериалы и фанера, которые должны быть действительно атмосферостойкими и водонепроницаемыми, хотя это может быть так. Все рейтинги относятся к клейкой смоле, которая используется для скрепления слоев шпона при производстве фанеры.
Фанера WBP не является такой же, как фанера морского класса, хотя фанера морского класса также может иметь рейтинг MBP. Что делает морскую фанеру уникальной, так это то, что она на 100% не содержит пустот, без сучков и трещин. Фанера WBP может все еще содержать их, хотя фанера морского класса WBP не будет.
Многие говорят, что рейтинга WBP больше не существует. Тем не менее, вы все еще можете найти фанеру с таким рейтингом. Те, кто говорит, что это устарело, указывают на европейский стандарт EN314, класс 3. Это относится к фанере, которая пригодна для наружного использования или аналогичной влажной/влажной/влажной среде.Обратите внимание, что европейский стандарт предусматривает те же требования к испытаниям, что и для фанеры WBP, поэтому единственная разница заключается в том, какой стандарт применяется; фанера и клей одинаковые.
Тестирование WBP
Испытание WBP состоит из погружения образца фанеры в кипящую воду и оставления его там на продолжительное время. Если фанера не расслаивается от нагретой воды, то она считается WBP.
В этом испытании обоснование использования кипящей воды, а не воды комнатной температуры или холодной воды, заключается в том, что многие клеи размягчаются при нагревании. При использовании горячей воды тестируемые клеи подвергаются как растворяющему действию самой воды, так и смягчающему потенциалу тепла. Кроме того, движущиеся пузырьки воздуха при кипячении взбалтывают фанеру, повышая вероятность ее расслоения. Отслоение всегда более вероятно, когда клей подвергается напряжению движения из-за постоянной нагрузки на клеевой шов, чем это происходит при простое.
Использование кипящей воды также обеспечивает согласованность при тестировании, поскольку вода кипит при 100°C или 212°F на уровне моря.Нет другой такой постоянной температуры, кроме замерзания; но ледяная вода не сильно повлияет на клейкость канифолей, используемых при производстве фанеры.
Никогда не считайте фанеру WDP, если она не имеет такой маркировки. Хотя фанера может пройти тест WDP, это не так. Специфические характеристики фанеры WDP не повторяются в других типах фанеры, даже в фанере для наружных работ, которая химически обработана, чтобы выдерживать суровые условия воздействия погоды.
Клей WBP
Не существует клея, который считается клеем WBF. Скорее, WBP — это свойство, определяемое тестированием . Ряд различных типов клея может быть WBF. Однако разные типы клеев обеспечивают разный уровень защиты от воды. Поэтому рейтинг WBP — это только минимум. Часто конкретная фанера имеет дополнительную оценку того, как долго она может выдерживать испытание WBP.
Наиболее распространенными клеями WBP, используемыми в фанере, являются меламиновый и фенольный .Обычная меламиновая фанера выдерживает испытание WBP от 4 до 8 часов без расслоения. Существует также лучший сорт меламиновой фанеры WBP, которая выдерживает испытание более 10 часов, в некоторых случаях до 20 часов. Тем не менее, фенольная фанера WBP превосходит меламин , выдерживая испытания WBP от 24 до 72 часов.
Использование правильных клеев — это не единственное, что определяет WBP определенного типа фанеры, имеет значение и то, как наносится клей. Даже самые лучшие клеи при плохом нанесении не обеспечат надежного соединения.Точно так же качество подложки будет иметь значение, как и в случае многих клеев, которые часто прочнее, чем материалы, которые они склеивают.
Обратите внимание: : Когда мы говорим о фенольном клее WBP, это не то же самое, что фенольная фанера. Стандартная фенольная фанера не является WBP , так как фенольная смола наносится только на лицевые ламинаты. Для внутреннего ламинирования используется другой клей, не являющийся WBP. Тем не менее, фенольная фанера WBP будет использовать фенол в качестве клея на всех слоях ламинирования, в дополнение к тому, что лицевые слои пропитаны им, что делает его очень водостойким.
Рынок Великобритании
Рейтинг WBP возник в Великобритании как часть стандарта Британского института стандартов 1203:1963, который озаглавлен «Спецификация клеев на основе синтетических смол (фенольных и аминопластовых) для фанеры». В нем указаны четыре общеизвестных сорта клея, используемые для склеивания слоев фанеры, в зависимости от их долговечности. WBP является самым высоким из этих слоев.
- WBP
8 WBP — Доставка погоды и варка
- BR — вачь устойчивый к
- MR — устойчивый к влажности
- INT — интерьер
Вы можете найти любую из этих отметок на фанерных продуктах, которые вы покупаете на местная лесопилка или домостроительный центр.
Хотя чаще используется в Англии , вы можете найти фанеру WBP в Соединенных Штатах. Вот почему цены обычно выражаются в британских фунтах стерлингов (£). Поскольку WPB — это рейтинг водостойкости, этот термин может применяться к ряду различных типов фанерных изделий. Таким образом, фанера для наружных работ может быть или не быть «устойчивой к кипячению в воде», в зависимости от производственного процесса.
Применение
Разница между фанерой WBP и фанерой для наружных работ заключается в том, что рейтинг WBP относится к клейкой смоле, используемой для соединения слоев шпона фанеры вместе. С другой стороны, «внешний» рейтинг фанеры относится к химической обработке деревянного шпона, а не смолы. Одно не подразумевает другое; вам нужно будет искать оба рейтинга, если они вам нужны. Наружная фанера WBP, очевидно, будет противостоять погодным условиям лучше, чем фанера для наружных работ или фанера с рейтингом WBP.
WBP может использоваться в качестве фанеры для наружных работ в строительстве. Есть те, кто говорит, что фанера WBP — единственная фанера, которую следует использовать для внешней обшивки из-за ее устойчивости к атмосферным воздействиям.Это может быть указано в случаях, когда внешняя обшивка или черновой пол будут подвергаться воздействию элементов в течение большего времени, чем обычно. По сравнению с обычной фанерой для наружных работ WBP может выдерживать воздействие погодных условий значительно дольше. Его указание в этих случаях поможет гарантировать, что обшивка или черновой пол не будут повреждены элементами во время строительства.
Фанеру WBP обычно используют для чернового пола, особенно в местах, где пол может подвергаться разливам и другой влаге.Несмотря на то, что сам пол в кухнях и ванных комнатах обычно является водонепроницаемым, наличие влагостойкого основания является дополнительным преимуществом на случай повреждения пола.
Однако чаще используется вместо морской фанеры, особенно для внутренних работ. Разница между WBP и стандартной морской фанерой заключается в том, что морская фанера гарантированно на 100% свободна от пустот, без каких-либо сучков и трещин, в то время как другая фанера WBP может не иметь таких дефектов.
Имейте в виду, что фанера с рейтингом WBP не является фанерой морского класса, и не следует ожидать, что она будет обладать такими же преимуществами. Это особенно актуально для реальных морских применений, где вода может просачиваться и накапливаться в пустотах, содержащихся в сердцевине облицовки продукта. Хотя фанера WBP в некоторых отношениях может быть лучше морской фанеры, она не может просто заменить морскую фанеру во всех областях применения.
Вывеска, особый вид фанеры, часто оценивается как WBP, потому что для вывесок требуется древесный продукт с высокой устойчивостью к атмосферным воздействиям, который не будет подвергаться воздействию погодных условий.Ряд типов внутренней фанеры также имеют рейтинг WBP, например, многие типы корпусной фанеры, даже если они не используются в приложениях, где они подвергаются воздействию погодных условий.
Классификация фанеры из твердой древесины корпусного класса как фанеры WDP больше связана с демонстрацией качества производственного процесса, а не с ожиданием того, что готовые шкафы будут подвергаться воздействию воды. Тем не менее, изготовление шкафов из фанеры класса WDP может оказаться полезным, если у вас есть протечки воды и затопление на кухне или в ванной.В то время как другие изделия из фанеры могут расслоиться, они выдержат воздействие воды.
Конечно, рейтинг WDB клея, используемого при изготовлении фанеры, не защищает шпон фанеры от гниения, если он подвергается постоянной влажности или затоплению. Для этого потребуется фанера, которая была обработана, чтобы фанера не могла впитывать воду.
Работа с фанерой WDP
Фанера WDP поддается резке, шлифовке, фрезерованию или соединению ничем не отличается от любой другой фанеры.В большинстве случаев канифоли, используемые для изготовления фанеры WDP, такие же, как те, которые используются при производстве фанеры, не имеющей рейтинга WDP. Единственная реальная разница может заключаться в том, что производитель не удосужился протестировать фанеру.
Имейте в виду, что любая канифоль, используемая при производстве фанеры, при соединении с древесным волокном образует абразивную смесь, которая затупляет пильные полотна. Важно периодически менять пильные полотна, чтобы это притупление не приводило к появлению большего количества сколов в древесине.
Современные твердосплавные пильные полотна выдерживают абразивное воздействие фанеры намного лучше, чем полотна из быстрорежущей стали. Это позволяет дольше использовать лезвия перед повторной заточкой. Это также делает повторную заточку более выгодным финансовым решением, поскольку разница в стоимости между повторной заточкой пильного диска и покупкой нового диска с твердосплавным наконечником больше, чем разница между заточкой и заменой диска из быстрорежущей стали.
Рейтинг WDP на фанере не влияет на использование клея для соединения фанерных листов или деталей.Это также не влияет на использование каких-либо конкретных креплений. Однако, если существует достаточно опасений по поводу влажности, чтобы указать фанеру WDP, было бы целесообразно использовать какой-либо крепеж с покрытием для защиты от ржавчины. Многие типы крепежных изделий теперь предлагаются в версии с покрытием, например, различные типы шурупов для гипсокартона, которые стали стандартными универсальными крепежными элементами для деревообработки и строительства.
Метрическая толщина
Фанера WBP часто продается с метрической толщиной, а не с долями дюйма.Он доступен как в толщине 18 мм, так и в 19 мм, при этом 18 мм немного толще 5/8 дюйма и используется вместо него, а 19 мм чуть толще 3/4 дюйма и используется вместо него.
Также можно найти фанеру WDP толщиной 6 мм, которая представляет собой пятислойную плиту толщиной примерно 1/4 дюйма. Используется в качестве подложки для выравнивания существующего основания. Будучи более водостойким, он идеально подходит для влажных помещений или помещений с высокой влажностью. Одной из таких ситуаций будет укладка керамической плитки.Вода в мастике, используемой для крепления плитки и затирки, может неблагоприятно воздействовать на некоторые виды фанеры, ослабляя пол. При использовании фанеры WDP вместо внутреннего сорта нет риска расслоения фанеры.
Можно ли влагостойкую древесностружечную плиту
Можно ли использовать водостойкий ДСПЧто можно использовать для герметизации ДСП?
Использование грунтовки на основе растворителя, вероятно, является лучшим средством для герметизации ДСП, если вы хотите сделать его водонепроницаемым.Убедитесь, что вы опорожняете его, прежде чем наполнять, иначе у вас будут проблемы! Можно ли в этом смысле сделать ДСП водонепроницаемой?
Ничто не сравнится с водостойким ДСП.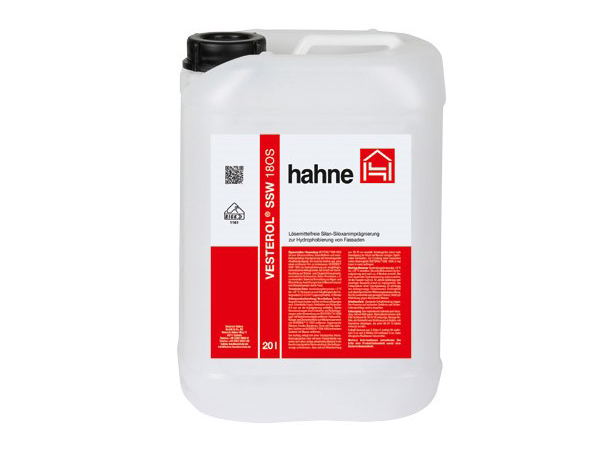
Итак, вопрос в том, можете ли вы запечатать МДФ, чтобы сделать его водонепроницаемым?
Аналогично водостойкому МДФ. Вы также можете сделать МДФ водонепроницаемым, добавив качественный влагостойкий герметик, лак или лак, чтобы помочь вашему проекту противостоять влаге и влаге.Не используйте полиуретан на водной основе, так как он плохо прилипает к поверхности МДФ.Во-вторых, как делаются кромки МДФ?
Герметизация наиболее впитывающих кромок МДФ. Края панелей МДФ впитывают много краски. Опечатайте их, особенно если на них есть проверенные детали. Вы можете использовать герметик для акриловой краски или герметик для гипса, а также клей или грунтовку на масляной основе, которые предотвратят вздутие краев.Чем заклеить края фанеры?
Закройте края фанеры полиуретановой краской для наружных работ.Нанесите краску на фанеру маленькой кистью.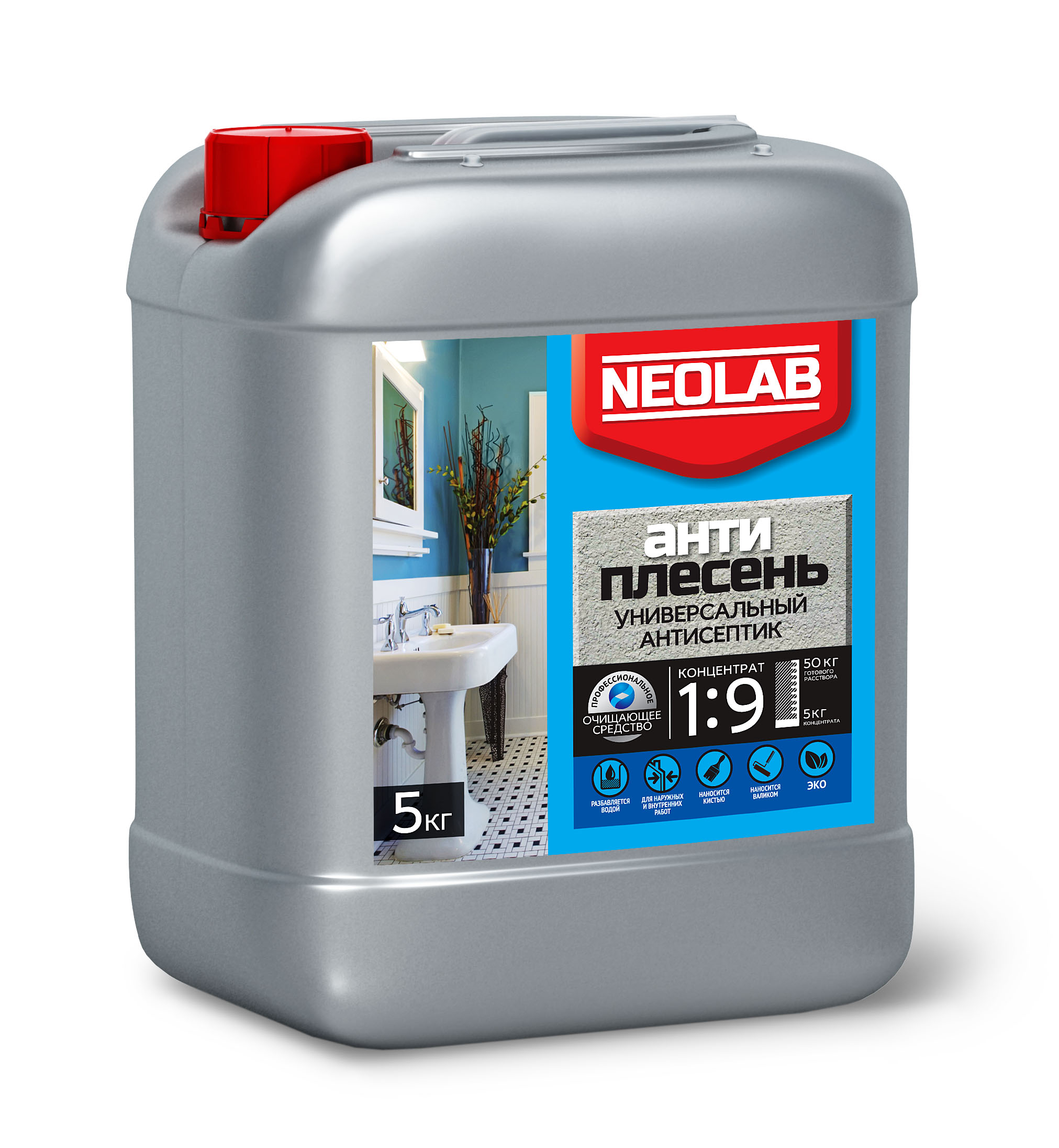
Можно ли шлифовать МДФ?
МДФ и вода не смешиваются. Прежде чем использовать грунтовку, рассмотрите возможность шлифовки МДФ наждачной бумагой средней зернистости (около 120 зерен должно подойти). Удостоверьтесь, что вы сосредоточились в первую очередь на шлифовании краев МДФ, так как шероховатые края не впитывают краску.Можно ли использовать шеллак на МДФ? МДФ
поглощает большую часть того, что попадает в первую очередь, поэтому шеллак относительно дешев, а быстросохнущий — хороший выбор.Конечно, вы можете просто начать с поли, но это займет больше времени и может занять много времени, чтобы полностью зажить.ДСП такая же прочная, как фанера?
В то время как фанера, как правило, прочнее, поверхность ДСП обычно более гладкая. Это связано с тем, что крестообразная поверхность, придающая фанере прочность, также препятствует равномерному распределению поверхностных материалов, таких как декоративный ламинат.
Как отверждается древесно-стружечная плита?
Ремонт полки из ДСПЧто тверже ДСП или МДФ?
Можно ли облицовывать влагостойкой ДСП?
Кроме того, это всего лишь влагонепроницаемый контейнер, он не является водонепроницаемым и при намокании набухает.Нанесение клея на цементной/водной основе также может стать проблемой, как и ваша плитка, когда все высохнет.Можно ли пропитывать фанеру?
Фанера представляет собой ламинированный материал со слабой водостойкостью. При использовании на открытом воздухе во всех отношениях пропитка продлит срок ее эксплуатации. Поскольку фанера изготавливается путем склеивания слоев древесины и отделки шпоном, слои подвержены повреждению водой.Какой толщины пол из ДСП? Полы из ДСП
доступны толщиной 18 мм и 22 мм, а размеры шпунтовых досок 2400 x 600 мм (примерно 8 x 2 фута).В панелях используется ДСП высокой плотности, и они подходят для жилых и коммерческих полов.Можно ли покрасить ДСП?
Для покраски ДСП вам понадобится газетная бумага или большая тряпка, наждачная бумага среднего размера, большая сухая тряпка, грунтовка, акриловая краска, прозрачный лак, трехваликовая краска, резиновые перчатки.
Как герметизируется прессованная древесина?
Как отключить плату OSB? №
Окуните кончик щетки в герметик и начните сглаживать поверхность и торцы плит OSB.Убедитесь, что вы повторяете этот процесс с каждой стороны, а не только там, где были сделаны надрезы. Покройте части, лежащие на брезенте, и дайте пропитке высохнуть в течение 12-14 часов.Как обновить ДСП?
Как шлифовать и полировать шпон из ДСПМожно ли шлифовать ДСП?
Убедитесь, что ДСП выметена и чистая, затем покройте пол смесью воды и ПВА 20/80%, при необходимости нанесите 2 слоя поддерживающего слоя и затем отполируйте. Перед использованием ПВС убедитесь, что отверстия и прокладки заполнены.Как сделать крышку на ДСП?
ДСП Твердый переплет Часть 1 YouTubeМожно ли красить ДСП?
Как выглядит ДСП?
Можно ли влагостойкую ДСПВодоотталкивающие средства для дерева и древесных материалов
Состав специальный водоотталкивающий «Неогард-дерево40»
Общеизвестно, что древесина имеет достаточно низкую устойчивость к воздействию воды и влаги, что приводит к набуханию, короблению и растрескиванию после высыхания. Еще более критическим может быть воздействие воды на фанеру, ДСП и подобные материалы – даже после одного смачивания эти материалы могут деформироваться, отслаиваться и терять свои товарные свойства.
Кроме того, влажная древесина является хорошей средой для развития плесени, грибков и водорослей, которые сначала образуют на поверхности изделия отвратительные белые, черные или зеленые пятна, а затем достаточно быстро разрушают его. Обычно древесину защищают от воздействия воды путем пропитки олифой или покрытия лаками или красками, эти способы обработки лишают древесину главного преимущества – способности «дышать».Альтернативным способом является обработка древесины водоотталкивающими средствами. Эти композиции уменьшают смачиваемость древесины водой, не снижая ее воздухо- и влагообменной способности.
Капли воды на поверхности фанеры, обработанной гидрофобизатором Неогард-дерево40.
Образец ДСП после пребывания под слоем воды в течение суток. Правая половина образца была предварительно обработана гидрофобизатором «Неогард-дерево40».
В 2007 году НПФ «НЕО+» разработан и начал производить специальный водоотталкивающий состав «Неогард-дерево40».Его эффективность, основанная на специальном выборе комбинации растворитель – активное вещество (полиорганосилоксан) – катализатор, описывается следующими данными. При кратковременном (2 – 4 часа) воздействии воды водопоглощение древесины лиственных пород снижается в 4 – 6 раз, древесины хвойных пород – в 2 – 4 раза, фанеры – в 3 – 5 раз, древесно-стружечных плит – в 15 раз. – 25 раз.
Гидрофобизаторы «Неогард-дерево40» — комплексные композиции, предназначенные для поверхностно-объемной защиты от проникновения воды и влаги в изделия из дерева и древесно-стружечных материалов (фанера, ДСП и др.).Водоотталкивающие вещества могут использоваться для бумаги, картона и других материалов на основе целлюлозы. Полиорганосилоксаны являются активной основой композиций.
Гидрофобизаторы проникают в поверхность материала и удерживаются на ней за счет химического связывания с целлюлозным волокном с одновременной полимеризацией. В результате таких реакций образуются безвредные для человека и животных покрытия, устойчивые к воздействию окружающей среды. Кроме того, это покрытие препятствует развитию плесени, грибков и микроорганизмов на поверхности изделия.
Поскольку гидроизоляционное действие композиций «Неогард-дерево40» достигается на молекулярном уровне, внешний вид, структура и механические свойства древесного материала не изменяются.
На рис. приведен пример зависимости водопоглощения от времени выдержки под слоем воды для древесностружечных плит (1 – необработанный образец, 2 – обработанный образец «Неогард-дерево40»).
Вода – Репелленты Средства «Неогард-дерево40»: технические характеристики
1) Маловязкая прозрачная бесцветная жидкость с запахом спирта.
2) Глубина проникновения в изделие несколько миллиметров (в зависимости от влажности древесины).
3) Расход: 100 – 150 г/м 2 .
4) Температура замерзания композиций ниже минус 75°С.
5) Плотность: 0,870 – 0910 г/м 2 , при 20°C.
Упаковка
Гидрофобизатор «Неогард-дерево40» поставляется комплектами по 10 литров (две емкости по 5 литров). Меньшие тома упакованы под наименованием «Неогард для дерева»