Использование смолы КФЖ в мебельном производстве — kleyOk
Облицовка заготовок является очень важной частью процесса изготовления мебели из ДСП, МДФ, ДВП, ОSB плит. Материалом для облицовки может быть шпон из натуральных или искусственных материалов, а также самые разнообразные виды плёнок или другой подходящий материал, выполненный в виде листов, например, акриловые.
Для прочного и качественного соединения необходимо подготовить поверхность, на ней не должно быть пыли, смолы дерева. Во многом, на качество соединения влияет наличие выпуклостей, вмятин или сколов. Если есть какой-либо недостаток из перечисленных, его необходимо устранить, обезжирив поверхность и при необходимости зашпаклевать. После полного застывания обработать шлифовальной машинкой.
В качестве клеящего вещества очень часто применяется карбамидоформальдегидной смола. Такие смолы получают в процессе поликонденсации формальдегида с карбамидом. В результате получается водная суспензия. Вязкость и прозрачность, отличаются в зависимости от назначения смолы.
- простота в применении;
- высокий уровень адгезии со многими материалами;
- небольшое содержание вредных веществ;
- более низкая стоимость по сравнению с другими видами клея
К недостаткам можно отнести немного более низкий уровень водо- и теплостойкости. Применение кфж клея очень распространено как при ручной, так и при механической облицовке. При ручном облицовывании можно применять и холодный и горячий способ. Во втором случае клей и поверхность нагревается до температуры +80°С, далее наносится на плиту склеивается и выдерживается 15-20 минут под давлением до 3-х часов. Нагретую смесь необходимо применить в течение 20-25 минут. Если использовать технологию прессования с охлаждением, то на поверхности можно получить глянец с эффектом тиснения.
Нанесение клея
В первую очередь необходимо помнить, что работать с клеем необходимо используя средства защиты и в хорошо проветриваемом помещении. Температура воздуха не должна быть менее +18°С, а влажность необходимо поддерживать в районе 65%. От способа приготовления клея будет зависеть его температура застывания и может составлять +20-25°С и +110-130°С. Если клей кфж готовится для горячего прессования, тогда необходимо в раствор добавить хлорид аммония. Обычно это 50% от общей массы, а в случае холодного 10%. Клей необходимо тщательно перемешивать в течение 20 минут. Оборудование, перед работой, необходимо проверить и настроить так, чтобы распределяющие валики равномерно наносили клей.
Устранение дефектов
Если все же, по каким-то причинам, возникли дефекты, например, клей по консистенции получился более жидким чем необходимо, то он будет попадать на саму облицовочную поверхность и в этом случае его необходимо счищать с помощью цикли. Если в каком-то месте скопилось много клея, то возможно появление пузырей. В таком случае этот участок необходимо немного разрезать и удалить лишний клей, а далее произвести притирку.
Если вас заинтересовала данная информация, то клей кфж купить можно у нас по выгодным ценам. За более детальной информацией обратитесь к менеджерам компании по телефону или электронной почте.
Как снизить токсичность карбамидоформальдегидных смол
Карбамидоформальдегидная смола используется в качестве клея для ДСП, в производстве непосредственно самих древесно-стружечных плит, фанеры и мебели. По сравнению с другими клеящими составами, она обладает хорошей клейкостью и способностью к быстрому отверждению.
Необходимость купить смолу КФМТ-15 оптом (или другую разновидность) возникает у многих предприятий, а вследствие широкой сферы применения неизменно встает вопрос, насколько вещество безопасно для жизни и здоровья людей. Действительно, у данного типа смол есть такой недостаток, как токсичность, которая обусловлена содержанием в составе свободного формальдегида.
Над решением этой проблемы ученые трудятся уже не одно десятилетие, в результате чего появился ряд вариантов, цель которых – чтобы карбамидоформальдегидная смола стала менее токсичной:
- применение модифицированных лигносульфанатов в составе карбамидоформальдегидного связующего, за счет чего не только происходит значительное снижение формальдегида, но и повышаются качественные характеристики смолы;
- обработка древесных частиц перед сушкой акцепторами;
- осуществление синтеза карбамидоформальдегидной смолы с заданными свойствами, что является, к тому же, более экономичным и технологичным способом производства древесных плит.
За счет того, что сырье для производства карбамидоформальдегидной смолы относительно недорогое, ее выпуск весьма перспективен, и вещество находит все более широкое применение в строительстве и производстве. Этому способствуют и ее важные технические характеристики: способность быстро затвердевать при комнатной температуре и при нагревании, практически полное отсутствие запаха и возможность окрашивания в любой цвет.
Токсичность – серьезный недостаток большинства синтетических смол, но без этих составов практически невозможно обойтись в современном производстве. Именно поэтому снижение токсичности имеет весьма важное значение.
Клей
Изобретение относится к изготовлению клея, предназначенного для клееных древесных материалов в производстве нетоксичной водостойкой фанеры, влагостойких древесно-стружечных плит и других клееных древесных материалов. Клей включает клеевую композицию, содержащую карбамидомеламиноформальдегидную смолу, аэросил, пшеничную муку и хлористый аммоний. В качестве карбамидомеламиноформальдегидной смолы клей содержит карбамидомеламиноформальдегидную смолу, модифицированную полиацетальгликолем и фурфуриловым спиртом, в соотношении карбамид: полиацетальгликоль: фурфуриловый спирт 1:0,1-0,5:0,1-0,5.
Изобретение относится к изготовлению клеевых составов, предназначенных для клееных древесных материалов, и может быть использовано в производстве нетоксичной водостойкой фанеры, влагостойких древесно-стружечных плит и других клееных древесных материалов.
Известна клеевая композиция, включающая карбамидомеламиноформальдегидную смолу и хлористый аммоний (Романов Н.М., Иванов Б.К. Карбамидоформальдегидный концентрат и смолы на его основе. М.: «Ключ», 2008, — 148 с).
Известен также клей, включающий клеевую композицию, содержащую карбамидомеламиноформальдегидную смолу (ЦНИИФ) СКМФ, пшеничную муку и активный наполнитель, в качестве которого он содержит аэросил (Кондратьев В. П. Справочник фанерщика. Глава IV. Клеевые материалы. Санкт-Петербург, Издательство Политехнического университета. 2010, с.217-218 — прототип).
Недостатками известных клеев является высокая токсичность клеевых композиций и изготовленных с их применением фанеры и плитных материалов, низкая прочность клеевого соединения, высокое водопоглощение и водоразбухание.
Техническая задача изобретения состоит в повышении качества клея за счет снижения токсичности клеевой композиции, фанеры и древесных плитных материалов на ее основе, повышения прочности клеевого соединения, а также снижения показателей водопоглощения и водоразбухания.
Поставленная задача достигается тем, что клей для производства клееных древесных материалов, включающий клеевую композицию, содержащую карбамидомеламиноформальдегидную смолу (ЦНИИФ) СКМФ, аэросил, пшеничную муку и хлористый аммоний, содержит карбамидомеламиноформальдегидную смолу (ЦНИИФ) СКМФ, модифицированную полиацетальгликолем и фурфуриловым спиртом с соотношением карбамид:полиацетальгликоль:фурфуриловый спирт (1:0,1-0,5:0,1-0,5) при следующем соотношении компонентов, мас.
Карбамидомеламиноформальдегидная | |
смола (ЦНИИФ) СКМФ, модифицированная | |
полиацетальгликолем и фурфуриловым | |
спиртом с соотношением | |
карбамид, полиацетальгликоль и | |
фурфуриловый спирт 1:0,1-0,5:0,1-0,5 | 100 |
Аэросил | 6-10 |
Пшеничная мука | 1-6 |
Аммоний хлористый | 1-2 |
Изобретение имеет следующие отличия от прототипа:
— клей содержит карбамидомеламиноформальдегидную смолу (ЦНИИФ) СКМФ, модифицированную полиацетальгликолем и фурфуриловым спиртом с соотношением карбамид:полиацетальгликоль:фурфуриловый спирт (1:0,1-0,5:0,1-0,5) при следующем соотношении компонентов, мас.ч.:
Карбамидомеламиноформальдегидная | |
смола (ЦНИИФ) СКМФ, модифицированная | |
полиацетальгликолем и фурфуриловым | |
спиртом с соотношением | |
карбамид, полиацетальгликоль и | |
фурфуриловый спирт 1:0,1-0,5:0,1-0,5 | 100 |
Аэросил | 6-10 |
Пшеничная мука | 1-6 |
Аммоний хлористый | 1-2 |
Это позволяет повысить качество клея за счет снижения токсичности клеевой композиции, фанеры и древесных плитных материалов на ее основе, повышения прочности клеевого соединения, а также снижения показателей водопоглощения и водоразбухания.
В просмотренном нами патентно-информационном фонде не обнаружено аналогичных технических решений, а также технических решений, содержащих указанные признаки.
Изобретение применимо и будет использоваться в отрасли в 2011-2012 гг.
Для изготовления клея использовали следующие ингридиенты:
— Карбамидомеламиноформальдегидная смола (ЦНИИФ) СКМФ — ТУ 2221-001-74767616-2009.
— Полиацетальгликоль ГОСТ 10437-80.
— Спирт фурфуриловый ГОСТ 28960-91 Технические условия.
— Карбамид ГОСТ 2081-92 Технические условия.
— Пшеничная мука ГОСТ Р 52189-2003 Технические условия.
— Аэросил ГОСТ 14922-77 Технические условия.
— Аммоний хлористый ГОСТ 2210-73 Технические условия.
Карбамидомеламиноформальдегидная смола (ЦНИИФ) СКМФ — ТУ 2221-001-74767616-2009, разработанная ЦНИИФ в 2009 г. успешно внедрена на ОАО «Мостовдрев», при этом на основе ее имеются следующие нормативно-технические документы:
— Технологическая инструкция ТИ1 — 2009 по производству карбамидомеламиноформальдегидной смолы марки (ЦНИИФ) СКМФ.
— Технологическая инструкция ТИ2-2009 по производству фанеры повышенной водостойкости на основе карбамидомеламиноформальдегидной смолы (ЦНИИФ) СКМФ.
— Технические условия ТУ 5512-001-74667616-2009. Фанера облицованная.
Производство смолы карбамидомеламиноформальдегидной (ЦНИИФ) СКМФ освоено в промышленных условиях ОАО «Мостовдрев», получают ее путем конденсации карбамида с формальдегидом и меламином периодическим способом в реакторе объемом 5 м3.
Используемую в заявленном клее карбамидомеламиноформальдегидную смолу получали модифицированием карбамидомеламиноформальдегидной смолы (ЦНИИФ) СКФМ полиацетальгликолем и фурфуриловым спиртом с соотношением карбамид:полиацетальгликоль:фурфуриловый спирт (1:0,1-0,5:0,1-0,5).
На производство карбамидомеламиноформальдегидной смолы (ЦНИИФ) СКМФ, модифицированной полиацетальгликолем и фурфуриловым спиртом, разработана следующая нормативно-техническая документация:
— Производство модифицированной карбамидомеламиноформальдегидной смолы марки (ЦНИИФ) СКМФ. ТИ1-2010.
— ТУ 2221-001-74767616-2010. Смола модифицированная карбамидомеламиноформальдегидная (ЦНИИФ) СКМФ.
Клей изготавливали следующим образом.
ПРИМЕР.
Карбамидомеламиноформальдегидную смолу (ЦНИИФ) СКМФ (изготовленую на ОАО «Мстовдрев»), соответствующую ТУ 2221-001-74767616-2009, модифицировали полиацетальгликолем и фурфуриловым спиртом с соотношением карбамид: полиацетальгликоль:фурфуриловый спирт (1:0,1-0,5:0,1-0,5), при этом получали модифицированную карбамидомеламиноформальдегидную смолу марки (ЦНИИФ) СКМФ в соответствии с ТУ 2221-001-7476616-2010.
Приготовление клея проводили в смесителе объемом 150 л, оборудованном лопастной мешалкой с числом оборотов 100 об/мин. Время перемешивания клея перед нанесением на шпон составило 10-15 мин.
Склеивание фанеры проводили из березового шпона толщиной 1,5 мм; влажностью 6±2%.
В таблице 1 представлен состав клеевой композиции клея (по примерам).
В таблице 2 представлены основные физико-механические показатели модифицированной карбамидомеламиноформальдегидной смолы (по примерам).
В таблице 3 представлены основные физико-механические показатели клеевой композиции с модифицированной карбамидомеламиноформальдегидной смолой.
В таблице 4 представлены физико-механические и экологические показатели фанеры, полученной с применением заявленного клея.
В таблице 5 представлены физико-механические показатели древесно-стружечных плит полученных с применением заявленного клея.
Таблица 1 | ||||||||
Состав клевой композиции | ||||||||
Компоненты композиции | Содержание компонентов в примерах, мас.ч | |||||||
1 | 2 | 3 | 4 | 5 | 6 | 7 | Прототип | |
Карбамидомеламиноформальдегидная смола СКМФ | — | — | — | — | — | — | — | 100,0 |
Карбамидомеламиноформальдегидная смола СКМФ, модифицированная полиацетальгликолем и фурфуриловым спиртом в соотношении по карбамиду: | — | |||||||
1:0,08:0,08 | 100 | |||||||
1:0,1:0,1 | 100 | |||||||
1:0,2:0,2 | 100 | |||||||
1:0,3:0,3 | 100 | |||||||
1:0,4:0,4 | 100 | |||||||
1:0,5:0,5 | 100 | |||||||
1:0,55:0,55 | 100 | |||||||
Аэросил | 5,5 | 6 | 7 | 8 | 9 | 10 | 10,5 | 10 |
Пшеничная мука | 0,8 | 1 | 2 | 3,5 | 5 | 6 | 7 | 2 |
Аммоний хлористый | 0,8 | 1 | 1,3 | 1,5 | 1,8 | 2 | 2,1 | 1 |
Таблица 2 | ||||||||
Основные физико-механические показатели модифицированной карбамидомеламиноформальдегидной смолы.![]() | ||||||||
Наименование показателей | Величина показателей | |||||||
ПРИМЕРЫ | Прототип | |||||||
1 | 2 | 3 | 4 | 5 | 6 | 7 | ||
Внешний вид, цвет | соотв. | соотв. | соотв. | соотв. | соотв. | соотв. | соотв. | От белого до св. желтого |
Массовая доля сухого остатка, % | 66,1 | 68.5 | 67,8 | 68,1 | 66,9 | 67,5 | 67,0 | 66-70 |
Массовая доля свободного формальдегида, % | 0,28 | 0,13 | 0,12 | 0,15 | 0,13 | 0,14 | 0,35 | 0,3 |
Условная вязкость по ВЗ-246 | 117 | 80 | 85 | 75 | 90 | 72 | 125 | 40-200 |
Водородный показатель, pH | 9,4 | 9,1 | 9,3 | 9,2 | 9,5 | 9,3 | 9,6 | 9,0-9,5 |
Время желатинизации с 1 мас.![]() | 127 | 82 | 81 | 83 | 81 | 84 | 135 | 80-120 |
Пред. смешиваемость смолы с водой | 1,0:1,0 | 1,0:1,0 | 1,0:1,0 | 1,0:1,0 | 1,0:1,0 | 1,0:1,0 | 1,0:1.0 | 1,0:1,0-1,0:2,0 |
Предел прочности при скалывании по клеевому слою фанеры после кипячения образцов в воде в течение 1 ч, МПа не менее | 1,42 | 1,82 | 2,01 | 1,97 | 2,03 | 1,89 | 1,43 | 1,5 |
Таблица 3 | ||||||||
Основные физико-механические показатели клеевой композиции с модифицированной карбамидомеламиноформальдегидной смолой. | ||||||||
Наименование показателей | Величина показателей | |||||||
ПРИМЕРЫ | Прототип | |||||||
1 | 2 | 3 | 4 | 5 | 6 | 7 | ||
Вязкость по ВЗ-4 после выдержки через 16 ч, с | 161 | 141 | 144 | 136 | 150 | 131 | 170 | 180-200 |
Концентрация (сухой остаток), % | 66,9 | 68,8 | 68,3 | 69,0 | 68,8 | 68.![]() | 68,8 | 66-70 |
Содержание свободного формальдегида: | ||||||||
после выдержки в течение 8 ч, % | 0,19 | 0,10 | 0,11 | 0,12 | 0,10 | 0,10 | 0,26 | 0,3 |
после выдержки в течение 12 ч, % | 0,15 | 0,09 | 0,08 | 0,07 | 0,08 | 0,07 | 0,15 | 0,2 |
Продолжительность отверждения клея, с | 123 | 79 | 78 | 81 | 78 | 79 | 129 | 80-120 |
Предел прочности при скалывании по клеевому слою фанеры после кипячения образцов в воде в течение 1,0 ч, мПа | 1,45 | 1,97 | 1,98 | 2,04 | 2,01 | 2,07 | 1,41 | 1,5 |
Таблица 4 | ||||
Физико-механические и экологические показатели фанеры с применением заявленного клея | ||||
Толщина фанеры, мм | Предел прочности при скалывании по клеевому слою фанеры, МПа, после кипячения в воде в течении | Содержание формальдегида мг/100 г сух.![]() | Выделение формальдегида, мг/м3 (метод газового анализа) | |
1 ч | 6 ч | |||
Береза, 9 мм | 2,30 | 1,68 | 2,0 | 0,38 |
Береза, 12 мм | 2,40 | 1,60 | 2,5 | 0,25 |
Береза, 18 мм | 2,20 | 1,50 | 3,0 | 0,51 |
Таблица 5 | |||
Физико-механические показатели древесно-стружечных плит с применением заявленного клея. | |||
Наименование показателя | Номинальная толщина плиты, мм | ||
6-13 | 13-20 | 20-25 | |
Предел прочности при изгибе, МПа, EN-310 | 18 | 16 | 14 |
Модуль упругости при изгибе, МПа | 2550 | 2400 | 2150 |
Прочность на отрыв поперек пласти, МПа | 0,45 | 0,45 | 0,40 |
Разбухание по толщине за 24 часа, %, EN-317 | 11 | 10 | 10 |
Прочность поперек пласти после циклических испытаний, МПа | 0,25 | 0,22 | 0,20 |
Разбухание по толщине после циклических испытаний, % | 11 | 11 | 10 |
Прочность поперек пласти после кипячения, МПа | 0,15 | 0,14 | 0,12 |
Таким образом, изобретение позволяет повысить качество клея за счет снижения токсичности клеевой композиции, фанеры и древесных плитных материалов на ее основе, повышения прочности клеевого соединения, снижения показателей водопоглощения и водоразбухания, а также снижения времени отверждения клея, что обеспечит повышение производительности прессового оборудования.
Клей для производства клееных древесных материалов, включающий клеевую композицию, содержащую карбамидомеламиноформальдегидную смолу, аэросил, пшеничную муку и хлористый аммоний, отличающийся тем, что он содержит в качестве карбамидомеламиноформальдегидной смолы карбамидомеламиноформальдегидную смолу СКМФ, модифицированную полиацетальгликолем и фурфуриловым спиртом, с соотношением карбамид:полиацетальгликоль:фурфуриловый спирт 1:0,1-0,5:0,1-0,5 при следующем соотношении компонентов, мас.ч.:
Карбамидомеламиноформальдегидная | |
Смола СКМФ, модифицированная | |
полиацетальгликолем | |
и фурфуриловым спиртом | |
с соотношением карбамид, полиацетальгликоль | |
и фурфуриловый спирт 1:0,1-0,5:0,1-0,5 | 100 |
Аэросил | 6-10 |
Пшеничная мука | 1-6 |
Аммоний хлористый | 1-2 |
Код 3909100000 — ТН ВЭД ТС
РАЗДЕЛ VII. Пластмассы и изделия из них; каучук, резина и изделия из них
I. ПЕРВИЧНЫЕ ФОРМЫ
Мы готовы оформить для Вас все эти документы
Документ | Примечание |
---|---|
Сертификат (декларация) соответствия Техническим регламентам Таможенного Союза (ТР ТС) | Решение Коллегии Евразийской экономической комиссии от 13.06.2012 N 79 (ред. от 25.06.2013) «Об утверждении Перечня продукции с указанием кодов ТН ВЭД ТС, в отношении которой подача таможенной декларации должна сопровождаться представлением таможенному органу одного из документов о соответствии, подтверждающих соблюдение требований технического регламента Таможенного Союза «О безопасности средств индивидуальной защиты» (ТР ТС 019/2011)» |
Приведенный список документов основан на коде товара по ТН ВЭД и является ориентировочным. Необходимость получения документов зависит от характеристик конкретного товара.
Свяжитесь с нами для получения более точной информации

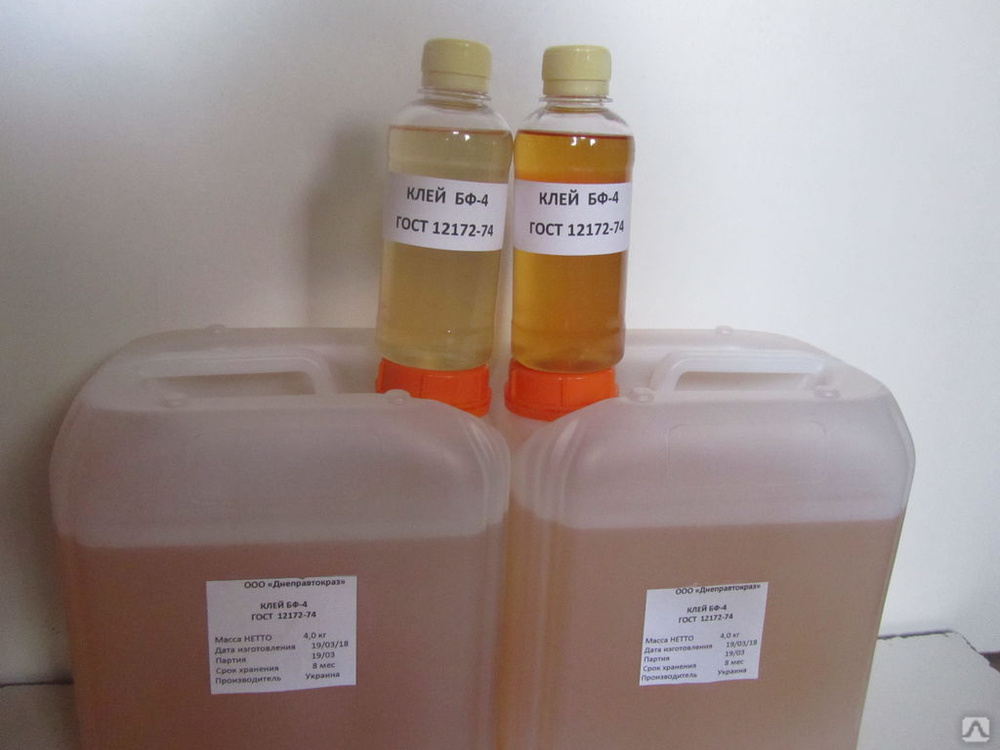
Производители Карбамидоформальдегидных смол из России
Продукция крупнейших заводов по изготовлению Карбамидоформальдегидных смол: сравнение цены, предпочтительных стран экспорта.
- где производят Карбамидоформальдегидные смолы
- ⚓ Доставка в порт (CIF/FOB)
- Карбамидоформальдегидные смолы цена 15.08.2021
- 🇬🇧 Supplier’s Urea-formaldehyde resins Russia
Страны куда осуществлялись поставки из России 2018, 2019, 2020, 2021
- 🇺🇦 УКРАИНА (57)
- 🇱🇻 ЛАТВИЯ (35)
- 🇰🇿 КАЗАХСТАН (18)
- 🇱🇹 ЛИТВА (5)
- 🇺🇿 УЗБЕКИСТАН (4)
- 🇰🇬 КИРГИЗИЯ (3)
- 🇪🇪 ЭСТОНИЯ (3)
- 🇮🇳 ИНДИЯ (2)
- 🇬🇪 ГРУЗИЯ (2)
- 🇹🇯 ТАДЖИКИСТАН (2)
- 🇦🇿 АЗЕРБАЙДЖАН (1)
- 🇩🇪 ГЕРМАНИЯ (1)
- 🇪🇸 ИСПАНИЯ (1)
- 🇳🇴 НОРВЕГИЯ (1)
- 🇮🇹 ИТАЛИЯ (1)
Выбрать Карбамидоформальдегидные смолы: узнать наличие, цены и купить онлайн
Крупнейшие экспортеры из России, Казахстана, Узбекистана, Белоруссии, официальные контакты компаний. Через наш сайт, вы можете отправить запрос сразу всем представителям, если вы хотите купить
Карбамидоформальдегидные смолы.
🔥 Внимание: на сайте находятся все крупнейшие российские производители Карбамидоформальдегидных смол, в основном производства находятся в России. Из-за низкой себестоимости, цены ниже, чем на мировом рынке
Поставки Карбамидоформальдегидных смол оптом напрямую от завода изготовителя (Россия)
Крупнейшие заводы по производству Карбамидоформальдегидных смол
Заводы по изготовлению или производству Карбамидоформальдегидных смол находятся в центральной части России. Мы подготовили для вас список заводов из России, чтобы работать напрямую и легко можно было купить Карбамидоформальдегидные смолы оптом
Смолы карбамидные и тиокарбамидные
Изготовитель растворы красок и лаков
Поставщики плиты
Крупнейшие производители Прочая мебель для сидения с деревянным каркасом
Экспортеры Феноло-альдегидные смолы
Компании производители бумага и картон с покрытием
Производство Вещества связующие готовые
Изготовитель растворы красок и лаков
Поставщики растворы красок и лаков
Крупнейшие производители Мочевина
О хвойной фанере — Чемпион — строительные и отделочные материалы в Красноярске
Свойства хвойной фанеры, применение, достоинства и многое другое
Хвойная фанера — отличный строительный и отделочный материал. Выпускается в листах различного формата и толщины. Каждый лист хвойной фанеры состоит из множества слоёв лущеного шпона, количество которых в листе колеблется в пределах от 3 до 17. Толщина листа при этом составляет от 6,5 до 30,0 мм, соответственно. Соседние слои обычно имеют перпендикулярное направление волокон, однако встречаются варианты склейки под углом 300, 400, 600 и 700.
Все слои шпона склеены между собой с помощью фенолформальдегидного либо (реже) — карбамидоформальдегидного клея. В первом случае хвойную фанеру относят к марке ФСФ, во втором — к марке ФК. Сферы применения хвойной фанеры ФК традиционно ограничиваются внутренними отделочными работами и производством мебели, т.к. карбамидоформальдегидный клей является менее токсичным — содержание свободного формальдегида в нём не превышает 0,9%, однако такая фанера не столь влагостойка, как ФСФ. Хвойная фанера ФСФ, в свою очередь, несколько более токсична из-за содержания свободного формальдегида в фенолформальдегидном клее (10 мг на 100 г сухого фанерного листа), но этот же клей придаёт ей повышенную влагостойкость и прочность, что позволяет широко использовать такую фанеру во внешней отделке и возведении каркасных конструкций.
Благодаря такому оптимальному сочетанию лёгкости и прочности хвойная фанера приобрела популярность в малоэтажном домостроении в качестве материала под так называемую «мягкую» кровлю, например, под гибкую черепицу. Лёгкость хвойной фанеры позволяет снизить нагрузку на стропильную систему при кровельных работах, а её прочность значительно увеличивает срок эксплуатации кровли.
Повышенная влагостойкость наряду с относительно невысокой стоимостью сделали данный вид фанеры незаменимым материалом при изготовлении многоразовой опалубки для заливки фундаментов. С этой целью, как правило, используют хвойную фанеру марки ФСФ толщиной 19-21 мм. и ее же в ламинированном виде. Кроме того, хвойная фанера нашла применение в автомобиле-, вагоно- и судостроении. Из неё изготавливают боковые стенки автомобильных кузовов и прицепов, обшивку трейлеров, черновые полы вагонов, обшивку и сидения для паромов, катеров и теплоходов.
Следует отметить, что хвойная фанера известна не только своими хорошими утилитарными качествами. Красота и расцветки древесины делают её широко востребованной в производстве мебели, оформлении интерьеров квартир и офисов (декоративная отделка стен, сооружение раздвижных и стационарных перегородок). При этом естественная привлекательность внешнего вида хвойной фанеры может быть дополнена различными декоративными покрытиями, например, ламинатом (специальной бумагосмоляной плёнкой).
Применение
Хвойные водостойкие сорта могут быть использованы в качестве подложки при укладке деревянного паркета ( использование березы в данном случае нецелесообразно) и ламинированного покрытия. Некоторые породы применяют при создании настила под кровлю: в таких условиях относительно низкая прочность хвойных видов не играет существенной роли Кроме того, сосновые и особенно еловые (ГОСТом предусмотрено использование ели, сосны, лиственницы пихты и кедра) нередко используют для возведения временных построек изготовления дешевой и довольно прочной упаковки и т.п. В целом хвойные сорта несколько дешевле березы, посему используется преимущественно в строительстве.
В общем и целом хвойная фанера несколько лучше лиственной, поскольку шпон, изготовленный их древесины хвойных пород, как правило, имеет меньше дефектов; кроме того, благодаря наличию природных смол древесина хвойных пород обладает большей водостойкостью.
Применяется:
- в строительстве;
- в мебельной промышленности;
- в автомобиле и вагоностроении;
- при производстве упаковки.
Чем хороша хвойная фанера?
Хвойная фанера представляет собой замечательный строительный и отделочный материал, характеризующийся:
- устойчивостью к воздействию: влаги, резких перепадов температуры, агрессивных сред, плесневых и трутовых грибков
- лёгкостью и одновременной прочностью
- удобством монтажа и обработки
- красивой текстурой древесины
Хвойную фанеру производят из древесины хвойных пород, в основном, сосны и ели. Отдельный лист хвойной фанеры состоит из нескольких слоёв шпона (тонких срезок древесины с чурака — соснового или елового полена, тщательно очищенного от коры и подвергшегося интенсивной термообработке). При этом хвойной также считается фанера, у которой из хвойной древесины состоят лишь внешние слои шпона, а внутренние могут быть изготовлены из древесины лиственных пород.
Слои шпона в листах склеены между собой синтетическим клеем. В зависимости от состава клея, хвойная фанера выпускается 2-х марок: ФСФ (с применением фенолформальдегидного клея) и ФК (с применением карбамидоформальдегидного клея). Фанера хвойная марки ФК распространена значительно уже, чем фанера хвойная марки ФСФ, что связано с ограниченностью области её применения, поскольку такая фанера менее водостойка. Как правило, хвойная фанера ФК задействована в производстве корпусной мебели и во внутренних отделочных работах. При этом её несомненным преимуществом является малотоксичность карбамидоформальдегидного клея.
Но и хвойная фанера ФСФ не столь токсична, как принято считать: она полностью соответствует экологическому стандарту Е1, предусматривающему содержание свободного формальдегида в пределах 10 мг на 100 г сухой фанеры. Эта марка традиционно применяется в каркасном строительстве, изготовлении опалубки, автомобиле- и судостроении (производство обшивки и сидений). Повышенная водостойкость и сопротивляемость гниению хвойной фанеры ФСФ делают её незаменимым материалом при проведении внешних отделочных работ. Для продления сроков эксплуатации и придания специфических декоративных свойств данную фанеру подвергают ламинированию или окраске.
По материалам fanera-bazar.ru
Фанера ФК и ФСФ — в чем разница?
Фанера ФК и ФСФ — два варианта одного из самых простых, доступных и прочных материалов, который находит широчайшее применение. Они одинаково хорошо востребованы в строительных работах, промышленности, упаковочной отрасли, машино- и вагоностроении. Из-за высокого удобства их практически не с чем сравнить, поскольку подходят для пола, стен, потолков, перегородок. Неплохи и в качестве основы под любые конструкторские задумки.
Что такое фанера ФК и ФСФ?
В первую очередь, стоит разобраться в аббревиатурах:
- ФК — древесно-слоистая плита, склеенная при помощи карбамидоформальдегидного состава, откуда и пошло данное сокращение «фанера + карбамидоформальдегидный клей»;
- ФСФ — материал, изготовленный методом соединения шпона фенолформальдегидными веществами, что и дает сочетание «фанера + смоляной фенолформальдегидный клей».
В чем принципиальное отличие?
Первая совершенно не устойчива к влажной среде, но достаточно прочна и универсальна. Рассчитана только на сухие условия. Намного дешевле второго варианта, поэтому широко применяется для производства мебели, облицовки стен, изготовления упаковочной тары, в качестве подложки под ламинат, паркет и другие покрытия.
Производится из лущенной древесины березы, ольхи и некоторых других лиственных пород (также возможна их комбинация). После проникновения влаги обычно расслаивается и скручивается, в чем серьезное отличие фанеры ФК от ФСФ. По уровню толщины подобные листы могут достигать 40 мм. Делятся по сортам, исходя из наличия сучков.
Пачка листов фанеры ФКВторая отличается повышенной устойчивостью к влаге, которой противостоит очень успешно. Благодаря этому свойству находит спрос в кровельных процессах, может применяться не только внутри, но и снаружи зданий. Обладает хорошей сопротивляемостью износу и прочностью к механическим воздействиям.
Изготавливается преимущественно из березового и хвойного шпона. Может пропитываться составами не только против влаги, но и от огня (ФСФ ТВ), отчего имеет расширенный спектр применения: строительство, промышленность, машино- и авиастроение.
Как отличить фанеру ФК от ФСФ внешне?
Без опыта в данном вопросе можно запутаться, поскольку по внешним признакам они мало чем отличимы, что и вызывает иногда недоразумение. Единственным фактором, который отчетливо показывает разницу между ними — оттенки прослоек.
ФК более светлая, так как соединена клеем без наличия фенола, отчего на срезе листы максимально приближены к натуральному цвету шпона. Тогда как ФСФ с повышенной пропиткой от влаги обладает более темным колером с присутствием красноватого подтона.
Сравнение данных | ФК | ФСФ |
Тип шпона | Лиственные породы (береза, ольха, осина) | Лиственно-хвойные породы (береза, сосна, лиственница) |
Склеивание | Карбамидоформальдегидный состав | Фенолформальдегидный состав |
Сопротивление влаге | Среднее (для нежилых и жилых помещений) | Максимальное (для интерьерных и внешних работ) |
Присутствие фенола | Нет | Есть |
Обработка | Ламинирование, шлифование | Ламинирование, шлифование |
Различия по физико-механическим показателям
Какая фанера менее вредная — ФК или ФСФ?
Для изготовления древесно-слоистых плит типа ФК применяется силикатное клеящее вещество, которое нетоксично для человека и животных. Это приравнивает фанеру к безопасным стройматериалам, пригодным для внутренних отделок и монтажа перегородок в условиях сухости.
ФСФ более устойчива к влаге, поскольку имеет особую пропитку на базе потенциально небезвредных смол. Клей также содержит 8 мг/100 г фенола, который негативно сказывается на здоровье окружающих.
Основные отличия
Чтобы четче разграничить для себя эти два вида фанеры, предлагаем их краткое сравнение.
Итак, ФК абсолютно безопасна для здоровья, неустойчива к влаге, подходит для внутренних работ и производства мебели, непрочна и плохо выдерживает механическое воздействие, легко ломается и расслаивается.
В то время как у ФСФ низкая экологичность, отчего она может вредить человеку и животным, обладает отличным сопротивлением влаге, применима для интерьерных, фасадных, а также любых других внешних работ, имеет увеличенную прочность на излом и давление.
Клеи на основе карбамида и формальдегида, также известные как клей на основе пластиковой смолы.

Мочевинно-формальдегидные клеи — это самый важный тип клея, который используется при производстве фанеры и деревянных панелей.
Что такое карбамидоформальдегидный клей, также известный как клей для пластмассовых смол
Смола карбамидоформальдегидная — это линейка синтетических смол, полученных путем химической комбинации формальдегида (газа, полученного из метана) и мочевины (твердого кристалла, полученного из аммиака).Смолы карбамидоформальдегидные используются в основном для склеивания фанеры, ДСП и других изделий из дерева. Смолы UF полимеризуются в постоянно связанные сети, которые влияют на прочность отвержденного клея. После схватывания и отверждения карбамидоформальдегидные смолы образуют нерастворимую трехмерную сетку, которую нельзя расплавить или подвергнуть термоформованию.
Мочевина формальдегидная изоляция (UFFI) получила плохую репутацию, когда было обнаружено, что она выделяет формальдегид. Эта проблема больше не является серьезной проблемой, потому что практика добавления дополнительного формальдегида для обеспечения полной реакции больше не применяется в современных рецептурах. Выделение газа не является серьезной проблемой в судостроении.
Вот статья, в которой рассказывается о дегазация газообразного формальдегида в изделиях из древесины. pdf файл.
Любой любитель химии может прочитать эту статью из Международного журнала адгезии и адгезивов на карбамидоформальдегидных (УФ) клеящих смолах для древесины.
Для чего используется формальдегид мочевины?
Формальдегид мочевины — широко используемый клей для фанеры, ДСП, деревянных панелей и гнутых ламинатов.
Институт деревообработки включил мочевину Formaldehide в список 6 лучших клеев.
Если склеенный продукт имеет маркировку «мебельный», он, вероятно, содержит формальдегид мочевины и является водостойким. Если указано строительное качество, клей, скорее всего, представляет собой фенолформальдегид и полностью водонепроницаем. Вот ссылка на мою страницу о фенолформальдегидном клее.
Какие преимущества у карбамидоформальдегидного клея?
- Наборы жесткие и жесткие.
Это преимущество для гнутых пластин, так как снижает упругость.
- Он используется в течение длительного времени и со временем доказал свою надежность. Он прост в использовании и не так требователен к качеству швов, как резорцин или полиуретан.
- Хотя его необходимо закрепить, он в некоторой степени заполняет зазоры и выдерживает нагрузку (прочный) и после затвердевания можно шлифовать.
- Cured Strength UF превосходит древесину, поэтому прочность не является проблемой.
- В зависимости от состава он имеет хорошее открытое время 20-30 минут и не схватывается, как некоторые другие клеи для дерева.Время зажима обычно составляет около 6 часов, в зависимости от температуры и марки.
- Формальдегид мочевины можно смыть водой, пока он не затвердел.
- Влагостойкость II типа. Это означает, что клей устойчив к многократному замачиванию и высыханию. В этом тесте он не кипятится, как клей для морской фанеры. Некоторые бренды, такие как Circa 1850 и Dural, заявляют, что их клей на основе пластмассовой смолы имеет статус водостойкости, но почти все бренды водостойкие.
- Поскольку это преимущественно бежевый цвет (цвет варьируется в зависимости от марки, от светло-коричневого до бежевого), он хорошо сочетается с деревом без выраженных клеевых линий.
- Не деформируется и не ползет при высоких температурах.
- Не дорогой клей.
- Прост в использовании, обычно приобретается в виде порошка, смешиваемого с водой. Для схватывания предпочитает более высокие температуры. Большинство брендов указывают 70 градусов F.
Каковы недостатки мочевиноформальдегидного (пластикового) клея
- При добавлении воды при высокой температуре отвержденный формальдегид мочевины может гидролизоваться и высвобождать формальдегид, что ослабляет клеевое соединение.По этой причине она считается водостойкой, а не водонепроницаемой и не используется для изготовления морской фанеры.
- Формальдегид мочевины необходимо использовать в хорошо вентилируемом помещении, поскольку неотвержденная смола вызывает раздражение и может быть токсичной.
Это не уникально, так как большинство неотвержденных современных клеев содержат серьезные предупреждения.
Клей мочевиноформальдегидный - имеет ограниченный срок хранения — один год. Его нужно хранить в сухом месте, поэтому его обычно продают в герметичных пластиковых контейнерах.
Можно ли использовать мочевину формальдегид в судостроении?
Водостойкость Формальдегид мочевины имеет несколько применений.Порча клея происходит во влажных и горячих условиях.
Его, безусловно, можно использовать в защищенном сухом месте, которое нельзя погружать в воду, но которое может иногда намокать. Он должен получить такую отделку, как краска или лак.
Самодельные самолеты эксплуатируются с удовольствием уже много лет.
На нем построено много лодок. Вот ссылка на Всемирные форумы по яхтингу и лодочному спорту по клеям. Cascamite, Aerolite, Balcotan и т. Д. Неоднократно упоминались как успешные клеи для лодок.
Это не единственный клей, используемый при постройке лодки, но его можно использовать вместе с эпоксидным или другим водонепроницаемым клеем.
С другой стороны, если вы облицовываете, лучшего клея не найти.
Для улучшения водостойкости иногда добавляют меламин. Обычно это тот случай, когда производитель заявляет об улучшенной водонепроницаемости.
AkzoNobel производит клей на основе карбамида и формальдегида, а также другие клеи.Мелкий шрифт
Я не претендую на звание эксперта.Я не инженер и не химик. Я делаю ошибки. Эта страница не является рекомендацией продуктов, она предназначена для информации и развлечения. ЕСЛИ вы хотите построить лодку с использованием клея на основе карбамида и формальдегида, убедитесь, что вы используете материал в соответствии с инструкциями производителя. Неотвержденная смола опасна для здоровья, поэтому наденьте перчатки и работайте в хорошо вентилируемом помещении или наденьте паровую маску. Делай домашнее задание и будь в безопасности.
Напишите мне, если обнаружите ошибки, я исправлю их, и мы все выиграем: Кристина
Мочевинно-формальдегидный клей — обзор
Общие принципы производства и применения
В промышленном производстве карбамидоформальдегидных (УФ) смол очень важно иметь возможность контролировать размер молекул с помощью реакции конденсации, поскольку их свойства непрерывно изменяются по мере роста. Наиболее заметное изменение — увеличение вязкости. Сначала образуются сиропы с низкой вязкостью. Они превращаются в сиропы с высокой вязкостью, от прозрачных до мутных. Молекулярная масса может варьироваться от нескольких сотен до нескольких тысяч с широким диапазоном молекулярных размеров. Эти молекулы образуются за счет случайного отщепления воды между реактивными группами соседних молекул, что увеличивает их размер. После определения их растворимости, вязкости, pH, концентрации и т. Д. Они составляют смолы, доступные на рынке.Наиболее важными факторами, влияющими на конечные свойства аминопластических смол при промышленном производстве, являются чистота реагентов, молярные пропорции используемых материалов, используемый процесс приготовления, а также изменение и контроль pH.
Наиболее распространенным методом приготовления коммерческих клеев на основе УФ-смол является добавление второго количества мочевины во время реакции приготовления. Он состоит из реакции мочевины и формальдегида в более чем эквивалентных пропорциях. Обычно начальное молярное соотношение мочевина / формальдегид составляет 1: 2.Используется от 0 до 2,2. В этом случае метилолирование может быть проведено за гораздо более короткое время при использовании температур до 90–95 ° C. Затем смесь кипятят с обратным холодильником. Когда экзотермический эффект утихает (обычно через 10–30 мин), образуются соединения метилола, и реакция завершается при кипячении с обратным холодильником путем добавления следовых количеств кислоты для снижения pH до стадии образования УФ-полимера (pH от 5,0 до 5,3). Как только достигается нужная вязкость, pH увеличивается, чтобы остановить образование полимера, и раствор смолы охлаждают примерно до 25-30 ° C.Добавляется больше мочевины (называемой второй мочевиной), чтобы израсходовать избыток формальдегида, пока молярное отношение мочевины к формальдегиду не будет в диапазоне от 1: 1,1 до 1: 1,7. После добавления мочевины смолу оставляют реагировать при температуре от 25 до 30 ° C в течение 24 часов. Избыток воды удаляют перегонкой в вакууме до тех пор, пока концентрация твердых веществ смолы не достигнет 64-65%, а pH регулируется для достижения подходящего срока годности или срока хранения.
Окончательное добавление мочевины может быть выполнено за одну операцию, или мочевина может быть добавлена с подходящими интервалами меньшими партиями.Вторая или дополнительные мочевины могут быть добавлены при температуре, немного превышающей температуру окружающей среды, или могут быть добавлены при более высоких температурах от 60 до 90 ° C в зависимости от типа желаемой конечной смолы [29–32]. Увеличение количества добавок второй или дополнительной мочевины имеет тенденцию улучшать качество связи, особенно при низких молярных соотношениях формальдегид / мочевина [29–32]. Смолы с более высоким молярным соотношением обычно демонстрируют в целом лучшее начальное качество связки [14], но представляют собой экспоненциально увеличивающуюся проблему эмиссии формальдегида [16], что чаще всего лишает их пригодности для многих или большинства современных применений.Некоторые УФ-смолы, используемые для столярных изделий, также производятся без окончательной или второй добавки мочевины. Значение pH, используемое во время реакции конденсации (не при метилолировании), обычно находится в диапазоне от 4,8 до 5,3.
Контроль среднего молекулярного размера готовой смолы важен для правильной текучести фанеры и ДСП при горячем прессе перед отверждением. Слишком низкий уровень конденсации (например, низкомолекулярные смолы) может привести к слишком большой текучести; смола «убегает» от древесины или быстро погружается в нее под давлением, оставляя «истощенные» клеевые полосы.Это можно исправить, снизив pH путем добавления кислоты или вещества, продуцирующего кислоту, обычно отвердителя, катализатора отвердения или просто отвердителя. Если имеется смола со слишком высокой степенью конденсации (т.е. смолы с высокой молекулярной массой), ее поток при нормальном давлении и температуре может быть слишком низким для получения хороших результатов. Обычно это можно исправить, добавив к нему вещества, повышающие текучесть, при условии, что в смоле остается хотя бы некоторая текучесть. Как правило, производство смол с высокой текучестью на заводе является преимуществом.Их срок хранения более длительный, а окончательную отделку можно произвести в любое время и в короткие сроки в соответствии со спецификациями, в частности, путем регулирования потока и скорости отверждения.
Смолы, потерявшие часть текучести во время производства или хранения, должны быть исправлены добавлением агента текучести. Самым простым средством часто является добавление воды, распыленной на состав и хорошо перемешанной. Если смола все еще способна течь, эта процедура дает смолу с приемлемыми свойствами. В случаях, когда контроль содержания влаги имеет решающее значение, может потребоваться немного больше времени для «нагревания», чтобы позволить дополнительной влаге уйти.Однако, если поток очень низкий и необходимо использовать большое количество воды, чтобы вернуть поток в норму, этот метод не рекомендуется. Большое количество воды потребует более длительного времени «дыхания» из-за чрезмерного количества летучих компонентов; может произойти чрезмерная усадка, что приведет к чрезмерной нагрузке на клеевые швы. Следует иметь в виду, что чрезмерное добавление воды вызывает осаждение УФ-смолы. Наилучший способ скорректировать поток в этих случаях — это смешать смолу с большим количеством смолы того же качества, которая имеет более высокую текучесть.Можно использовать любую пропорцию, чтобы вернуть поток в норму. Если желательна повышенная текучесть, можно также добавить от 0,5 до 2,0% высушенной распылением смолы UF или MF для работы в качестве агента текучести. Соединения метилола, такие как диметилолмочевина, также увеличивают текучесть, но они увеличивают воду, выделяемую во время реакции, больше, чем смолы, высушенные распылением. Смазывающие агенты, такие как стеарат кальция, также способны значительно увеличить текучесть.
Многие вещества были предложены в качестве отвердителей. К ним относятся следующие кислотные продукты: (1) борная кислота, (2) фосфорная кислота, (3) кислые сульфаты, (4) гидрохлориды, (5) аммониевые соли фосфорной или полифосфорной кислоты, (6) этилсульфат натрия или бария, (7) кислотные соли гексаметилентетрамина, (8) фталевый ангидрид, (9) фталевая кислота, (10) кислотные смолы, такие как поли (основная кислота) –поли (водный спирт), (11) щавелевая кислота или ее соли аммония и многие другие. Однако наиболее широко используемыми отвердителями в деревообрабатывающей промышленности по-прежнему являются хлорид аммония или сульфат аммония. Их действие можно изменить, замедляя реакцию смолы. Это достигается одновременным добавлением небольших количеств раствора аммиака (который удаляется при горячем отверждении) для увеличения срока годности клеевой смеси. Также можно использовать скрытые катализаторы, которые производят кислоту только при нагревании, такие как диметилоксалат и другие легко гидролизуемые сложные эфиры, или галогенированные вещества, такие как 0.От 1 до 0,2% бромгидрокоричной кислоты и др.
Движущей силой использования этих солей в качестве отвердителей является их способность выделять кислоту, которая снижает pH смолы и тем самым ускоряет отверждение. Скорость реакции между солью аммония и формальдегидом (или аммиаком и формальдегидом, если он присутствует) также определяет, вместе с количеством подводимого тепла, скорость выделения кислоты и, следовательно, скорость отверждения (Схема 4. 6).
Схема 4.6.
Хлорид аммония является лучшим отвердителем, чем соляная кислота, поскольку последняя дает более слабые соединения.
Часто, особенно в UF-смолах холодного отверждения для столярных изделий, отвердители, состоящие из смесей соли, такой как хлорид аммония или сульфат аммония, с кислотой, такой как фосфорная кислота, лимонная кислота или другие, используются для регулирования жизнеспособности и скорости жизнеспособности. лечение. Жизнеспособность и скорость отверждения смолы затем можно регулировать путем (1) изменения концентрации отвердителя в смоле, (2) изменения относительных пропорций кислоты и соли и (3) изменения типа кислота и / или соль, составляющие отвердитель.Следуя этим трем принципам, можно легко получить время настройки от нескольких минут до нескольких часов.
Адгезивные и связывающие смолы
Мочевинно-формальдегидные и меламино-формальдегидные смолы, обычно в жидкой или высушенной распылением форме, используются в качестве клея (см. Рисунки 4.1 и 4.2). Хотя меламино-формальдегидные смолы более водо- и термостойкие и дают более прочные клеи и связующие смолы, чем карбамидо-формальдегидные смолы, их более высокая стоимость ограничивает их использование.
Рисунок 4.1. Светлые подставки на основе аминосмол по сравнению с темными подставками на основе фенольных смол.
Рисунок 4.2. Изготовлены изделия из ДСП. ДСП обладает превосходной структурной прочностью и дешевле, чем ДВП средней плотности.
(Любезно предоставлено Weyerhaeuser.) Их долговечность и водостойкость способствуют использованию меламино-формальдегидных смол в наружных и морских применениях. Светлоокрашенные аминосмолы привлекательны для декоративных фанерных покрытий, не сталкиваясь с проблемой обесцвечивания, вызванной просачиванием смолы.Обычно адгезивные и связующие смолы имеют соотношение мочевина: формальдегид от 1: 1,5 до 2,0 и соотношение меламин: формальдегид 1: 3,0. Реакции проводят при pH от 7,5 до 8,0 и при кипячении с обратным холодильником в течение до 8 часов до достижения 50-60% твердого состава. PH снижается с увеличением вязкости; затем реакцию останавливают и смолу стабилизируют с помощью каустической соды путем повышения pH до 8,0. Типичный состав адгезивных смол составляет около 15% смолы; Обычными наполнителями являются древесная мука, орех пекан и скорлупа грецких орехов.Кислотные катализаторы предпочтительны в адгезионных и связывающих аминосмолах.
Условия обработки или прессования аминосмол обычно составляют 70 ° C и давление 200 фунтов на квадратный дюйм (холодное прессование) в течение до 24 часов. Меламиноформальдегидные смолы можно отверждать или прессовать без катализатора, но только при более высокой температуре обработки (горячее прессование).
Клеи на основе аминосмол обычно используются при склеивании древесины. Прочность соединения аминокислот наиболее эффективна при нагревании и давлении для древесных частиц размером от 40 до 80 меш.Горячее прессование заставляет аминосмолы просачиваться через поры древесной сердцевины и полимеризоваться (сшиваться) внутри древесины. Это сшивание связывает древесину вместе, в результате чего получается более прочная и влагостойкая структура, чем исходная древесина. Некоторые клеи на основе аминосмол состоят из смесей мочевины и меламина. Смола McClure от American Cyanamid Company представляет собой высушенный совместно распылением меламин-мочевинно-формальдегидный клей в сыпучей порошкообразной форме, предназначенный для наружной гидроизоляции.
Смолы для покрытий
Аминосмолы служат в качестве сшивающих агентов для полимеров с гидроксильными, карбоксильными и амидными функциональными группами, таких как акрилы, полиэфиры, эпоксиды и алкиды. Смолы для жидких амино-покрытий получают путем взаимодействия исходных метилолированных частиц, диметилолмочевины и гексаметилолмеламина, либо с n, -бутанолом, либо с метанолом. Эта стадия приводит к получению аминосмолы, которая более растворима в смолах для покрытия и совместима с ними. Повышенная совместимость усиливает реакцию обмена эфира между аминосмолами и реакционными центрами полимеров покрытия для получения пленок покрытия с очень высокой степенью сшивки.
Смолы для покрытия карбамидоформальдегидом отверждаются быстрее, но имеют более низкую влагостойкость, чем смолы для покрытия меламиноформальдегидные. В целом смолы для покрытий на основе меламина обладают лучшими общими характеристиками, но, опять же, их более высокая стоимость ограничивает их использование. Обычно используется комбинация смол на основе мочевины / меламина для достижения правильного баланса свойств, стоимости и производительности.
Beetle, Cymel и Melmac являются торговыми наименованиями жидких смол для покрытия American Cyanamid Company [33].
Марки Beetle представляют собой бутилированные и изобутилированные карбамидоформальдегидные смолы с низкотемпературными характеристиками отверждения, очень хорошей адгезией между субстратом и межслойным слоем и низкой стоимостью. Эти карбамидоформальдегидные смолы для покрытий совместимы с гидроксилсодержащими полимерами, такими как эпоксидные смолы, катализируемые амином, масляно-алкидные смолы, эпоксидно-сложноэфирные смолы, целлюлозы и конверсионные лаки.
Марки Cymel представляют собой метилированные или бутилированные меламиноформальдегидные смолы, обладающие стойкостью к ультрафиолетовому излучению, химической стойкостью, внешней износостойкостью, быстротвердеющими характеристиками и очень хорошей адгезией.Эти меламиноформно-альдегидные смолы для покрытия демонстрируют совместимость с широким диапазоном типов смол с тио-, гидроксильными, карбоксильными и амидными функциональными группами, такими как алкидные и полиэфирные смолы, эпоксидные смолы, акрилы, виниловые полимеры и целлюлозы. Совместимые целлюлозы включают этилцеллюлозу, гидроксиэтилцеллюлозу, нитроцеллюлозу и производные карбоксилированной целлюлозы. Они также являются хорошими смачивающими и диспергирующими агентами для технического углерода и органических пигментов. Некоторые смолы Cymel требуют наличия сильных кислотных катализаторов для эффективности и высокой степени сшивки. p -Толуолсульфоновая кислота — самый популярный катализатор, используемый со смолами Cymel. Другими катализаторами являются додецилбензолсульфоновая кислота, щавелевая кислота, малеиновая кислота, гексамовая кислота и соли металлов. Соли металлов, такие как бромид магния (MgBr 2 ), нитрат алюминия (A1 (NO 3 ) 3 ) и нитрат цинка (Zn (NO 3 ) 2 ), используются для достижения жесткости и устойчивости к растворителям. , но они вызывают обесцвечивание и низкий блеск.
Смолы для ламинирования
Смолы для ламинирования содержат преимущественно меламиноформальдегидные смолы.Обычно 1 моль меламина реагирует с 2 молями формальдегида при pH от 8 до 10 с получением смолы от 50 до 65% твердого вещества. Катализаторы и пластификаторы обычно добавляют для улучшения отверждения и гибкости. Меламиноформальдегидные смолы для ламинирования обладают характерной твердостью, прозрачностью, устойчивостью к пятнам и УФ-излучению. Иногда для достижения длительного срока хранения используется сушка распылением.
Метилолированные меламиноформальдегидные смолы образуют стабильные катионные коллоиды в присутствии таких кислот, как карбоновые кислоты. Коллоидные меламиновые смолы пропитывают и образуют прочные ионные связи с целлюлозными волокнами (бумагой) в водных дисперсиях [5] с последующим увеличением прочности на разрыв во влажном состоянии. Степень пропитки повышается за счет использования водных дисперсий, содержащих от 0,5 до 1,0 процента спирта в качестве поверхностно-активного вещества. Спиртовое поверхностно-активное вещество снижает поверхностное натяжение раствора смолы и увеличивает смачиваемость волокна. Типичный коллоидный состав имеет отношение меламиновой смолы к кислоте и воде 1: 1: 6,5 по массе.
Насыщение волокнистого материала смолой обычно связано со свободным вращением-вытягиванием волокнистого материала через ванну с раствором смолы.Затем пропитанное смолой полотно направляют в сушилку. Концентрация смолы, скорость вытягивания и время пребывания волокна в ванне влияют на скорость пропитки. Сушка и процесс сушки являются неотъемлемой частью процесса ламинирования. Процесс сушки помогает испарить растворитель смолы и повысить степень полимеризации смолы.
Аминоформовые смолы
Гранулы и порошки карбамидоформальдегидных и меламиноформальдегидных смол используются при формовании смол (Таблица 4.1). Их характерная прозрачность способствует их использованию в различных цветных продуктах. Аминоформующие соединения обычно включают наполнители для обеспечения прочности и стабильности размеров. Химически очищенные волокна альфа-целлюлозы являются наиболее популярными наполнителями для амино-формовочных смол. Другие наполнители — тальк, слюда, стекловолокно, измельченный хлопковый флок и древесная мука.
Таблица 4.1. Свойства амино (мочевина, меламин) формовочных смесей
Материалы | Свойства * | Метод испытаний ASTM | Мочевина | Меламин формальдегид | |||||||||
---|---|---|---|---|---|---|---|---|---|---|---|---|---|
Наполненное альфа-целлюлозой | Стекло с целлюлозным наполнителем | Армированный||||||||||||
Обработка | 1.![]() | Температура плавления, ° С. | Thermoset | Thermoset | Thermoset | ||||||||
T m (кристаллический) | |||||||||||||
Диапазон температур обработки, ° F. (C = сжатие; T = перенос. I — впрыск; E = экструзия) | C: 275–350 | C: 280–370 | C: 280–350 | ||||||||||
I: 290–320 | I: 200–340 | ||||||||||||
T: 270–300 | T: 300 | ||||||||||||
3. | Диапазон давления формования, 10 3 p.s.i. | 2–20 | 8–20 | 2–8 | |||||||||
4. | Степень сжатия | 2 2–3,0 | 2,1–3,1 | 5–10 | |||||||||
Усадка пресс-формы (линейная), дюйм / дюйм | D955 | 0,006–0,014 | 0,005–0,015 | 0,001–0,006 | |||||||||
Механический | 6.![]() | Предел прочности при разрыве, p.s.i. | D638 | 5500–13.000 | 5000–13.000 | 5000–10 500 | |||||||
7. | Удлинение при разрыве,% | D638 | & lt; 1 | 0,6191 | 8. | Предел текучести при растяжении, пс i. | D638 | ||||||
9. | Прочность на сжатие (разрыв или текучесть), фунтов на квадратный дюйм | D695 | 25,000–45,000 | 33,000–45,000 | 20,000–35,000 | ||||||||
10. | Прочность на изгиб (разрыв или текучесть), p.s i | D790 | 10,000–18,000 | 9000–16,000 | 14,000–23,000 | ||||||||
11. | Модуль упругости при растяжении, 10 s. 3 9025. 3 | 0638 | 1000–1500 | 1100–1400 | 1600–2400 | ||||||||
12. | Модуль упругости при сжатии, 10 3 p.![]() | D695 | |||||||||||
13. | Модуль упругости при изгибе, 10 3 p.s.i. | 73 ° F. | D790 | 1300–1600 | 1100 | ||||||||
200 ° F | D790 | ||||||||||||
250 ° F | F | D790 | |||||||||||
14. | Удар по Изоду, фут-фунт / дюйм (выемка *** в толстом образце) | D256A | 0 25–0,40 | 0 2–0,4 | 0 6–18 | ||||||||
15. | Твердость | по Роквеллу | 0785 | Μ110–120 | M115–125 | M115 | |||||||
Shore / Barcol | 02240 / D2583 | 02240 / D2583 | линейное тепловое расширение. 10 −6 дюйм / дюйм / ° C. | 0696 | 22–36 | 40–45 | 15–28 | ||||||
17.![]() | Температура прогиба при изгибной нагрузке.° F. | 264 p s i | D648 | 260–290 | 350–390 | 375–400 | |||||||
66 p s i | D648 | C 177 | 7–10 | 6,5–10 | 10–11,5 | ||||||||
Физический | 19. | Удельный вес | D792 | 1,47–1.52 | 1,47–1,52 | 1 5,20 | |||||||
20. | Водопоглощение (образец толщиной *** дюймов). % | 24 ч. | D570 | 0,4 0,8 | 0 1–08 | 009,1 *** | |||||||
Насыщенность | D570 | ||||||||||||
21 | образец Толщина диэлектрика *** время. объем / мл *** | D149 | 300–400 | 270–400 | 130–370 | ||||||||
175–215 *** 100 ° C |
Материалы | Свойства * | Метод испытаний ASTM | Меламин Фенольный | |||||
---|---|---|---|---|---|---|---|---|
Древесная мука и целлюлоза с наполнителем | ||||||||
Переработка | 1.![]() | Температура плавления. ° C | Термостат | |||||
T м (кристаллический) | ||||||||
Tg (аморфный) | ||||||||
2. | Диапазон температур обработки, ° F. (C = сжатие; T = перенос; I = впрыск; E = экструзия) | C: 300–350 | ||||||
1: 350–400 | ||||||||
3. | Диапазон давления формования, 10 3 фунтов на квадратный дюйм | 5–20 | ||||||
4. | Степень сжатия | 2,1–4,4 | ||||||
5. | Усадка пресс-формы (линейная), дюйм / дюйм. | D955 | 0,009–0,010 | |||||
Механический | 6. | Предел прочности при разрыве, p.s.i. | D638 | 6000–8000 | ||||
7. | Удлинение при разрыве,% | D638 | 0,4–0,8 | |||||
8.![]() | Предел текучести при растяжении, пс i. | 0638 | ||||||
9. | Прочность на сжатие (разрыв или текучесть), фунтов на квадратный дюйм | D695 | 26,000–30,000 | |||||
10. | Прочность на изгиб (разрыв или текучесть), psi | D790 | ||||||
11. | Модуль упругости. 10 3 шт. / Кв. Дюйм | D638 | 800–1700 | |||||
12. | Модуль упругости при сжатии.10 3 шт. / Кв. Дюйм | D695 | ||||||
13. | Модуль упругости при изгибе. 10 3 шт. / Кв. Дюйм | 73 ° F. | ||||||
200 ° F. | D790 | 1000–1200 | ||||||
250 ° F | D790 | |||||||
300 ° F. | ||||||||
14. | Удар по Изоду, фут. — внутр. / Дюйм.![]() | D256A | 0.2–0,4 | |||||
15. | Твердость | по Роквеллу | ||||||
Шор / Баркол | D785 | E95–100 | ||||||
16. | Коэффициент линейного теплового расширения, 10 5 дюйм / дюйм / ° C. | D696 | 10–40 | |||||
17. | Температура прогиба при (физической нагрузке, ° F. | 264 p.s.i. | D648 | 285–310 | ||||
66 p s i. | 0648 | |||||||
18. | Теплопроводность, 10 -4 * кал.-см / с-см. 2 — ° С. | C177 | 4–7 | |||||
Физический | 19. | Удельный вес | D792 | 1,5–1,7 | ||||
20. | Водопоглощение (%), толщина образца | % 24 ч.![]() | D570 | 0.3–0,65 | ||||
Насыщение | D570 | |||||||
21. | Электрическая прочность (образец толщиной *** — дюймов), кратковременная. v./mil*** | D149 | 220–325 |
Перепечатано с разрешения Modern Plastics Encyclopedia, McGraw-Hill, Inc.
Обычные мольные отношения мочевины или меламина к формальдегиду в аминосмолах равны 2 : 3 и 3: 4. Процесс осмоления осуществляется за пределами водорастворимости, а затем смесь смолы и наполнителя нагревается в условиях контролируемой влажности.Соотношение смолы и наполнителя, тип наполнителя, тип катализатора и степень полимеризации меняются для достижения различных свойств формования.
Методы компрессионного переноса для обработки и литья под давлением (винтовой и холодный коллектор) являются основными смолами для формования аминов. Температура формования составляет 260–340 ° F для карбамидоформальдегидных смол и 260–360 ° F для меламиноформальдегидных смол. Для аминосмол характерно давление формования прессованием от 2000 до 8000 фунтов на квадратный дюйм. Обработка усиливается за счет присутствия кислотного катализатора, такого как фталевый ангидрид, и ингибитора, такого как гексаметилентетрамин («HEXA»).Небольшие количества ингибитора помогают стабилизировать формовочную смолу во время хранения и перед формованием, а также контролировать скорость отверждения во время формования.
Как использовать клеи на основе порошкообразной мочевины — CP Adhesives, Inc.
(Версия в формате .pdf по использованию клея на основе карбамида.)
Введение:
Смолы на основе карбамида — это действительно универсальный клей, который подходит для большинства монтажных склеек, торцевого и краевого склеивания, ламинирования и облицовки. Клеи на основе мочевины доступны либо в виде жидких смол с порошковыми катализаторами, либо в виде предварительно приготовленных предварительно катализированных порошков.Оба материала будут давать одинаковые характеристики клеевого шва: прочный, жесткий, термореактивный, водостойкость типа II и отличная термостойкость.
Порошковые мочевины предпочтительны там, где производственные циклы нечасты, при высокой температуре окружающей среды и где требуется более длительный срок хранения. Срок годности порошкообразных мочевины составляет один год. Они имеют предварительно составленные рецептуры и содержат необходимые наполнители, добавки и катализатор, чтобы удовлетворить широкий спектр технологических требований. Продукт CPi из порошковой пластмассы (PPR) может подвергаться горячему прессованию, холодному прессованию или отверждению с помощью радиочастоты (RF).
Микс:
Вода — это все, что необходимо для восстановления порошковой смолы. Количество используемой воды должно составлять 50-65% от веса смешиваемого сухого порошка.
- 65% — идеальный уровень воды.
- Определив необходимое количество воды, сначала добавьте 2/3 этого количества воды в емкость для смешивания.
- Медленно добавьте порошок, перемешивая смесь на медленных оборотах (<2000) с помощью механической мешалки.
- Продолжайте перемешивание в течение 3-5 минут, используя лопатку соскребать порошок с боков обратно в жидкость.На этом этапе смесь должна быть кремообразной и практически без комков.
- Добавьте оставшуюся 1/3 воды и перемешивайте еще минуту. Смесь должна быть гладкой, кремообразной и без комков.
- ** Примечание: если порошок плохо растворяется в воде или если смесь выглядит песчаной и / или зернистой, продукт не следует использовать. Эти рабочие характеристики обеспечивают встроенную проверку безопасности, сигнализирующую о том, что срок годности порошка истек.
- ** Примечание: имейте в виду, что номинальный срок годности относится к неоткрытой таре, хранящейся в прохладном (60–70 ° F) и сухом месте.Более высокие температуры сильно сократят срок хранения (всего 6 месяцев при 90 ° F), а воздействие высокой влажности может вызвать сильное комкование или фактическую катализацию порошковой смолы.
Распространение:
Укрывистость во многом зависит от характера выполняемой работы и применяемого метода отверждения. Ставки обычно определяются в фунтах. клея на 1 000 кв. м склеиваемой поверхности плиты (MSGL). Во многих случаях может быть более практичным отбросить по одному нулю с каждой стороны уравнения и говорить в терминах фунтов.за 100 кв. Например, вы облицовываете площадь поверхности 4 x 6 и ищете спред 30 # / 1000 MSGL, затем цифру 3 # / 100 кв. требуется 0,5 # клея.
- Укрывистость будет варьироваться от 25 # до 50 # / MSGL, в зависимости от характера работы, временных ограничений на нанесение клея и метода отверждения.
- Обычно для склеивания массивных пиломатериалов используются более высокие ширины (40-50 #), чем для облицовки шпоном.
- RF отверждение, скорость распространения ниже (32-36 #), чем обычно, для предотвращения помех работе оборудования.Эта скорость распространения должна быть достаточной, чтобы показать небольшую каплю выдавливания при приложении давления. Более легкий намаз тяжелой смеси обычно предпочтительнее более плотного намазывания тонкой смеси.
- Намазать одну поверхность — это все, что требуется, однако, выход за пределы номинального времени сборки может потребовать покрытия обеих поверхностей. Аналогичным образом, работа с твердыми или влажными породами древесины (например, твердым кленом, ясенем, гикорием) также может потребовать двустороннего покрытия.
- Тонкие спреды имеют решающее значение при работе с необработанным шпоном, чтобы уменьшить эффект просачивания.Просачивание — это появление клея, просачивающегося через поры древесины, чтобы проявиться на лицевой стороне панели. Помните о толщине вашего шпона и относительной пористости материала, с которым вы работаете, и соответствующим образом отрегулируйте разброс. Во многих случаях потребуется тонкий слой вместе с обязательным временем открытой сборки (возможно, до 10 минут), чтобы предотвратить чрезмерное просачивание. Следите за тем, чтобы клей не высох, если оставьте время открытой сборки. Он должен быть достаточно влажным, чтобы перейти на сопрягаемую поверхность.
- Более низкая укрывистость также является нормой для прессования ламината высокого давления (HPL) в картон, отчасти благодаря хорошей консистенции склеиваемых поверхностей.
- Давление пресса также оказывает большое влияние на норму внесения. При более низком давлении должно быть меньше клея на линии клея, поскольку толстые линии клея требуют больше времени для отверждения и будут слабым местом на линии клея.
- Все это, конечно же, связано с возможностью измерения и контроля разброса. Нанесение может быть выполнено очень грубо с помощью кистей или малярных валиков, или может быть выполнено сложным способом с помощью автоматизированного оборудования для склеивания.Чем точнее можно будет контролировать разброс, тем лучше будет ваш успех. Хотя клей в некоторой степени щадящий, уменьшение переменных дает лучшие результаты. Если выполняется большое количество склеивания, рекомендуется установить более качественное разбрасывающее оборудование. С более грубым оборудованием обычно невозможно различить нормы внесения.
- Измерение нормы внесения обычно производится по весу или измерению пленки. При измерении толщины влажной пленки датчик влажной пленки используется для получения показаний в милах, и хотя это измерение не такое точное, как # / MSGL, его можно преобразовать для получения точных показаний.Формулы и инструкции также доступны для взвешенного измерения, хотя это более сложный процесс. Работа с нанесением клея с течением времени обычно дает хорошее представление о том, какой уровень нанесения необходим, без использования измерений. Однако, если вы новичок в склеивании или не проверяли себя какое-то время, возможно, стоит внимательнее присмотреться к измерению разброса.
- Количество выдавленного клея под давлением по-прежнему является хорошим показателем того, какова ваша степень разбрасывания. Помните, что важно не только количество клея, но и то, насколько равномерно он был нанесен, и выдавливание может дать вам представление о каждом из них.
Жизнеспособность:
После смешивания с водой смола продвигается на стадии отверждения до тех пор, пока не станет непригодной для использования. Время между первым перемешиванием и достижением точки непригодности для использования называется жизнеспособностью. Как и большинство указаний по приклеиванию, это динамическое значение. Он изменится, прежде всего, из-за температуры. Более высокие температуры сокращают жизнеспособность, и наоборот, при более низких температурах. Нет проблем с помещением смешанной смолы в холодильник, чтобы продлить ее жизнеспособность; однако температура не должна быть ниже 55 ° F, так как она загустеет до такой степени, что не сможет хорошо растекаться.Не допускайте замерзания клея!
- При температуре 70 ° F жизнеспособность составляет 5-1 / 2 часа, а при 90 ° F — 3 часа.
- Клей будет продолжать отверждаться до тех пор, пока он не станет твердым, как правило, в течение 24 часов.
- Только опыт и внимательный взгляд подскажут вам, в какой момент смесь непригодна для использования, так что ошибайтесь в сторону производительности, а не отдачи. Когда он загустеет до такой степени, что не будет хорошо растекаться, считайте смесь непригодной для использования.
- Прежде чем клей станет слишком тяжелым, можно добавить небольшое количество воды (до 3%), чтобы клей оставался достаточно жидким для использования.Кроме того, новую клеевую смесь можно добавить к небольшому количеству более густого продукта, и после перемешивания она даст новую полную жизнеспособность.
Время сборки:
Время, которое у вас есть после нанесения клея, до приложения полного давления пресса, называется временем сборки. Смолы мочевины обеспечивают очень длительное время сборки, что делает их идеальными для сложных работ, требующих более длительного времени укладки.
- Открытая сборка — это после нанесения клея на заготовку, но до того, как она будет соединена с сопрягаемой поверхностью.
- Закрытая сборка — это после того, как поверхности были соединены вместе, но до приложения полного давления пресса / зажима.
- Время открытой и закрытой сборки взаимосвязано: макс. Время закрытой сборки достигается только тогда, когда практически не задано открытое время, и сокращается примерно на 2 минуты на каждую минуту открытого времени сборки.
- Опять же, они являются динамическими, зависящими от нормы внесения, пористости основания, содержания влаги и температуры — как окружающей среды, так и температуры запаса.
- Максимальный размах необходим для получения максимального времени сборки.
- При повышении температуры допустимое время сборки сокращается. Максимум. время сборки при температуре 70 ° F составляет 40 минут, а при температуре 90 ° F — 20 минут.
- Более важным, чем просто измерение времени, является уверенность в том, что нанесенный клей достаточно влажный, чтобы перейти на сопрягаемую поверхность, и, опять же, на это указывает небольшая полоска выдавливания.
Подготовка запаса:
Наилучшие результаты достигаются при наилучшей подготовке массы.Чем точнее соблюдаются эти условия, тем лучше результаты.
- Равновесная влажность (EMC) должна составлять 8-10%, максимум 12% для холодного прессования и 6-8%, максимум 10% для горячего прессования. Очень важно знать назначение наконечника, чтобы изменение содержания влаги не было значительным.
- Древесина должна быть свежеобработанной — в идеале в течение 12 часов.
- На поверхностях не должно быть пыли, грязи, жира или других загрязнений.
Прессование / отверждение:
- Как и в случае жизнеспособности, давление прессования и время отверждения являются динамическими и зависят от конкретных условий.
- Давление, необходимое для развития достаточной прочности сцепления, зависит от конструкции и используемой породы древесины, с основным правилом, согласно которому поверхности должны находиться в тесном контакте друг с другом в течение достаточно длительного времени отверждения, чтобы развить достаточную прочность для снятия с пресса / зажимов.
- Для склеивания массивной древесины потребуется от 150 фунтов на квадратный дюйм для пород с низкой плотностью до 250 фунтов на квадратный дюйм для пород с высокой плотностью.
- Для панелей холодного прессования при 70 ° F потребуется от 4 часов времени прессования для материалов с низкой плотностью до 6 часов для материалов с высокой плотностью.При 90 ° F этот диапазон будет от 2 часов до 4 часов.
- Холодное прессование HPL на картон может выполняться под давлением 40-70 фунтов на квадратный дюйм при указанном выше времени прессования.
- Для панелей горячего прессования потребуется от 100 до 200 фунтов на квадратный дюйм и, в зависимости от глубины до самой глубокой линии клея, потребуется от 1 до 3,5 минут при 250 ° F.
- После холодного прессования панели следует уложить в стопку с утяжелением по верхнему краю в течение 24-48 часов перед обработкой или шлифованием.
- После горячего прессования панели перед обработкой или шлифовкой следует уложить в стопку с верхним грузом в течение 18-24 часов.
- Мочевина отверждается химическим действием, при котором необходимо присутствие воды. Если вода покидает клейкий слой до завершения химической реакции, полученная связь будет слабой.
- Как видно выше, скорость отверждения зависит от температуры, при этом более высокие температуры приводят к более быстрому отверждению.
Очистка:
- Мочевина — это продукты на водной основе, поэтому их можно смывать водой. Предпочтительна теплая вода, так как холодная или горячая вода затруднит очистку.
- Перед добавлением воды удалите как можно больше клея с очищаемых поверхностей. Прямой клей следует собрать в ведро и дать ему отстояться, пока он полностью не затвердеет, после чего останется плотная пробка из мочевины. Его можно выбросить как твердые отходы в мусорный контейнер.
- Отвердевший клей с деталей можно удалить шлифованием или механической обработкой. Считается, что мочевину легче шлифовать, чем большинство клеев, поскольку она не нагружает шлифовальные ленты и не размягчается от тепла.На обработанных поверхностях они считаются более твердыми.
Безопасность:
Как и при использовании любых промышленных химикатов, следует соблюдать осторожность при обращении с адгезивами на основе мочевины. Они специально указаны в паспорте безопасности материалов, который доступен для этого и любого продукта, который вы покупаете и используете.
Устранение неисправностей:
Пожалуйста, проконсультируйтесь с CP Industries для получения полного списка устранения неполадок, если возникнут проблемы с качеством смеси или связки.
Таблица смешивания:
Свойства и применение карбамидоформальдегидной смолы
Мочевина-формальдегид, более известный как мочевина-метаналь, назван в честь его структуры и общего пути синтеза.Изготовленный из мочевины и формальдегида, он создает непрозрачную термореактивную смолу или полимер, который стал обычным компонентом различных продуктов. Но давайте углубимся в детали и обсудим свойства и применение карбамидоформальдегидной смолы, чтобы вы могли решить, подходит ли этот полимер для вас.
Свойства карбамида и формальдегида
Во-первых, давайте определим свойства карбамидоформальдегидной смолы, которые делают ее такой полезной и податливой для самых разных целей.
- Высокая прочность на разрыв — максимальное напряжение, которое может выдержать материал при растяжении или растяжении перед разрушением.
- Высокий модуль упругости при изгибе — отношение напряжения к деформации, которое материал может выдержать при изгибе, прежде чем он поддается.
- Высокие температуры тепловой деформации — при какой температуре материал начнет «размягчаться» при воздействии фиксированной нагрузки при повышенных температурах.
- Низкое водопоглощение
- Усадка формы — когда объем расплавленного пластика, заполненного внутри полости формы, сжимается в процессе охлаждения и затвердевания.
- Высокая твердость поверхности
- Относительное удлинение при разрыве — Отношение измененной длины к начальной длине после разрушения материала.
- Объемное сопротивление — электрическое сопротивление тела току, проходящему через его тело.
- Содержит показатель преломления 1,55
Общее применение
Учитывая, насколько широко распространена карбамидоформальдегидная смола, во многих отраслях промышленности используются производители карбамидоформальдегидной смолы. Некоторые из более общих применений включают ламинат, текстиль, бумагу, устойчивые к складкам ткани, хлопчатобумажные смеси и вспененный искусственный снег. Его также можно найти в качестве покрытия для электрических приборов, таких как настольные лампы.
Использование в сельском хозяйстве
Свойства и применение карбамидоформальдегидной смолы распространяются на сельское хозяйство в качестве медленно высвобождающегося источника азота, который полезен для питания сельскохозяйственных культур. Высвобождение этого азота зависит от микробной активности в почве, и скорость высвобождения может быть изменена в зависимости от температуры, при этом оптимальная температура составляет от 70 до 90 градусов по Фаренгейту.
Пеноизоляция
Другим основным применением карбамидоформальдегидной смолы является ее преобразование в изоляционную пену.По консистенции он похож на крем для бритья и идеально подходит для инъекций в стены и помещения необычной или сложной формы. Пена затвердеет в течение нескольких минут и застынет в течение нескольких недель.
Характеристики карбамидоформальдегидного клея с окисленным крахмалом кассавы :: BioResources
Ван, Х., Лян, Дж., Чжан, Дж., Чжоу, X., и Ду, Г. (2017). «Характеристики карбамидоформальдегидного клея с окисленным крахмалом кассавы», BioRes. 12 (4), 7590-7600.Abstract
Мочевинно-формальдегидные (UF) смолы на основе различных мольных соотношений формальдегид / мочевина (F / U) были синтезированы с добавлением окисленного крахмала маниоки на заключительной стадии процесса синтеза смолы. Были изучены основные характеристики смол, включая содержание твердых веществ, вязкость и время отверждения, а прочность сцепления в сухом и влажном состоянии была оценена путем производства трехслойной фанеры. Кроме того, характеристики отверждения различных смол исследовали с помощью дифференциальной сканирующей калориметрии (ДСК).Структурное распределение между UF и окисленным крахмалом кассавы исследовали с помощью FT-IR и 13C ЯМР-анализа. Результаты показали, что добавление окисленного крахмала не только улучшило прочность связи смолы, но также заметно снизило температуру начала отверждения модифицированных смол. Кроме того, была выявлена отрицательная взаимосвязь между мольным отношением F / U и степенью восстановления. Структурное распределение UF-смол резко изменилось из-за окислительного добавления крахмала маниоки, но изменения варьировались из-за различных мольных соотношений F / U.
Скачать PDF
Полная статья
Характеристики карбамидоформальдегидного клея с Окисленным крахмалом маниока
Хуэй Ван, * Цзянькунь Лян, Цзюнь Чжан, Сяоцзянь Чжоу и Гуаньбэнь Ду
Мочевина-формальдегидные (UF) смолы на основе различных мольных соотношений формальдегид / мочевина (F / U) были синтезированы с добавлением окисленного крахмала маниоки на заключительной стадии процесса синтеза смолы. Были изучены основные характеристики смол, включая содержание твердых веществ, вязкость и время отверждения, а прочность сцепления в сухом и влажном состоянии была оценена путем производства трехслойной фанеры.Кроме того, характеристики отверждения различных смол были исследованы с помощью дифференциальной сканирующей калориметрии (DSC) . Структурные распределения между UF и окисленным крахмалом кассавы исследовали посредством анализа FT-IR и анализа ЯМР 13 C. Результаты показали, что добавление окисленного крахмала не только улучшило прочность связи смолы, но также заметно снизило температуру начала отверждения модифицированных смол. Кроме того, была выявлена отрицательная взаимосвязь между мольным отношением F / U и степенью восстановления.Структурное распределение UF-смол резко изменилось из-за окислительного добавления крахмала маниоки, но изменения варьировались из-за различных мольных соотношений F / U.
Ключевые слова: окислительный крахмал маниоки; Смола карбамидоформальдегидная; Прочность сцепления; Характеристики отверждения
Контактная информация: Юго-Западный университет лесного хозяйства, Юньнань ключевая лаборатория клеев для древесины и клееных изделий, Куньмин, Юньнань, П. Р. Китай; * Автор для переписки: [email protected]
ВВЕДЕНИЕ
Смола карбамидоформальдегидная (UF) — важная синтетическая смола, используемая в производстве древесных композитов, благодаря ее относительно низкой стоимости и превосходным свойствам.В настоящее время около 90% УФ-смолы используется для изготовления изделий из дерева. Однако некоторые недостатки, особенно выбросы формальдегида, создают серьезный барьер для более широкого использования UF-смолы.
Многие методы были эффективно использованы для уменьшения выбросов формальдегида, включая снижение моля формальдегида / мочевины (F / U), использование поглотителя формальдегида, оптимизация формулы смолы, и т. Д. . (Dunky 1998; Nuryawan et al. 2014). В настоящее время мольное отношение F / U может быть уменьшено до низкого значения, равного примерно 1.0. Дальнейшее уменьшение мольного отношения F / U снижает прочность сцепления и водостойкость фанеры из-за ограничения сшивки. Хотя оптимизация формулы смолы может снизить выбросы формальдегида, степень сокращения ограничена. Поэтому для уравновешивания мольного соотношения и характеристик смол используются некоторые виды добавок, включая меламин (Tohmura et al. 2001; Young No and Kim 2007; Zhang et al. 2013), фенол (Sinha and Khali 2015) , танин (Vazquez et al. 2004; Zanetti et al. 2014), крахмал (Zhu et al. 2013), гиперразветвленные полимеры (Zhou et al. 2013) и фторированный полиэфир (Mansouri et al. 2010) широко используются в рецептурах смол.
По сравнению с материалами, полученными из нефти, материалы биомассы, используемые в качестве добавок к УФ-смолам, имеют больше преимуществ, таких как обилие, возобновляемость и нетоксичность (Kaewtatip and Tanrattanakul 2008). В этой работе крахмал маниоки использовался в качестве добавки, поскольку он не имеет цвета, запаха и безвреден для окружающей среды.Кроме того, добавление крахмала кассавы также может снизить стоимость смол UF. Крахмал кассавы, как регенерирующий ресурс, широко используется во многих отраслях промышленности. Отношение амилопектина к амилозе составляет примерно 80:20 (Wang et al. 2013), что придает модифицированной смоле более высокую степень разветвления. Однако применение крахмала маниоки в клеях для древесины все еще ограничено. Следовательно, необходимо дальнейшее изучение его влияния на характеристики ультрафильтрации.
Крахмал кассавы имеет сложную молекулярную структуру, но гидроксильные группы крахмала легко подвергаются различным типам реакций после окисления.В этой работе окисленный крахмал маниоки применяли для модификации УФ-смолы, и характеристики УФ-смолы с различными мольными отношениями F / U оценивали путем добавления окисленного крахмала маниоки на заключительной стадии процесса синтеза смолы. Были исследованы характеристики фанеры, включая прочность сцепления и водонепроницаемость. Кроме того, характеристики отверждения исследовали с помощью дифференциальной сканирующей калориметрии (ДСК). Структуры смол были охарактеризованы с помощью инфракрасной спектроскопии с преобразованием Фурье (FTIR) и спектроскопии ядерного магнитного резонанса на углероде 13 ( 13 C-ЯМР).
ЭКСПЕРИМЕНТАЛЬНАЯ ИНФОРМАЦИЯ
Материалы
Окисленный крахмал маниоки (90%) был приобретен у Xuan Kang Starch Co., Ltd. (Гуанси, Китай). Шпон тополя влажностью от 8% до 10% и толщиной 1,5 мм был закуплен на фабрике шпона Zhi Wei (Хэбэй, Китай) для изготовления фанеры. Все остальные химические вещества, использованные в этой работе, были реактивными и поставлялись отделом обработки химических реагентов Danchi Trading Co., Ltd. (Куньмин, Китай).
Подготовка смолы
Смолы, использованные в этой работе, были синтезированы в лаборатории с помощью следующего процесса. Сначала в реактор добавляли 37% формальдегида с помощью термометра, конденсатора и механической мешалки. PH доводили до 8,0-8,5 с помощью 40% гидроксида натрия и добавляли первую порцию мочевины. Когда температура достигала 90 ° C, добавляли вторую порцию мочевины. Через 30 минут pH доводили до 5,0-5.5 с 30% муравьиной кислотой и выдерживали в течение 2 ч при 90 ° C. После доведения pH до 7,5-8,0 добавляли последнюю мочевину. Спустя почти 30 мин реакционную смесь охлаждали до комнатной температуры. Регулируя добавление последней мочевины, получали смолы с различными мольными отношениями F / U (1,0, 1,3). Смолы были названы UF1.0 и UF1.3. На последней стадии добавляли 3% окисленного крахмала маниоки, исходя из количества мочевины в реакции, а также получали различные модифицированные УФ-смолы.Эти смолы были определены как UF1.0-3 и UF1.3-3. В предыдущих экспериментах (одна статья была принята китайским журналом, но не опубликована) было обнаружено, что использование 3% окисленного крахмала маниоки дает оптимальные результаты.
Характеристика смол
Содержание твердого вещества в смолах определяли путем измерения веса смол до и после сушки в термостатической печи при 120 ± 1 ° C в течение 2 часов. Было взято среднее из трех повторов. Вязкость смолы измеряли с помощью чашки Tu-4 при 25 ° C.Время отверждения оценивали в кипяченой воде с NH 4 Cl в качестве отвердителя, а время от жидкого клея до высоковязкого клея регистрировали в соответствии с китайским национальным стандартом GB / T 14074 (2006).
Подготовка трехслойной фанеры и свойства
Прочность сцепления и водонепроницаемость смол были проверены путем подготовки трехслойной фанеры и оценки ее прочности на сдвиг в сухом и влажном состоянии. Фанера была изготовлена из трех слоев шпона тополя размером 200 мм × 200 мм × 2 мм, и содержание влаги в шпоне составляло от 8% до 12%.К смеси смол добавляли всего 1% твердого хлорида аммония (NH 4 Cl) в расчете на общую массу смолы. Дозировка используемого клея составляла 200 г / м 2 (односторонняя). Фанеру подвергали горячему прессованию при 140 ° C и давлении 1 МПа в течение 3 мин. После горячего прессования фанеру хранили в окружающей среде (около 20 ° C и относительная влажность 12%) в течение 3 дней. Прочность сцепления в сухом и влажном состоянии была испытана в соответствии с процедурой, описанной в Китайском национальном стандарте GB / T 17657 (2013).В этом тесте были протестированы по 6 образцов каждого вида, и в качестве окончательного результата использовалось среднее значение.
Дифференциальная сканирующая калориметрия (ДСК)
Дифференциальная сканирующая калориметрия использовалась для определения характеристик отверждения смол с различным содержанием окисленного крахмала маниоки. Каждый образец тестировали на анализаторе NETZSCH DSC 204 (Selb, Германия). Примерно 5 мг образца жидкой смолы с 1% отвердителя взвешивали на алюминиевом поддоне и закрывали другой алюминиевой крышкой.В качестве эталона использовалась алюминиевая сковорода. Подготовленный образец нагревали от 25 ° C до 200 ° C со скоростью нагрева 10 ° C / мин в токе азота. Были измерены начальная температура, пиковая температура и конечная температура.
Анализ FT-IR и 13C-ЯМР
Инфракрасные спектры с преобразованием Фурье смол измеряли в форме таблеток KBr на приборе Perkin Elmer model Spectrum V10 (Waltham, MA, USA). Каждый образец был приготовлен из 100 мг KBr и 1 мг жидкой смолы.После испарения воды при 25 ° C (комнатная температура) диски с образцами сканировали с диапазоном волновых чисел от 500 см -1 до 4000 см -1 . Было собрано 32 скана с разрешением 4 см -1 .
Спектры C-ЯМР 13 были измерены на приборе Bruker Avance 600 МГц (Карлсруэ, Германия). В качестве растворителя использовали ДМСО. Образец был приготовлен путем смешивания жидкой смолы с растворителем в объемном соотношении 1: 3. Спектры регистрировались на частоте 125.75 Гц и задержка релаксации 10 с. Химические сдвиги измеряли относительно ТМС в качестве внутреннего стандарта.
Пики FT-IR и 13 C-ЯМР были назначены, как описано ранее (Park et al. , и др. 2008; Kim 2010; Roumeli et al. 2012; Zhang 2013; Li et al. ). 2016).
РЕЗУЛЬТАТЫ И ОБСУЖДЕНИЕ
Свойства чистых и модифицированных карбамидоформальдегидных смол
Основные характеристики и прочность сцепления смол UF с различными молярными отношениями показаны в таблице 1.Окисленный крахмал маниоки с содержанием 3% явно увеличивал вязкость смол и сокращал время их отверждения, но твердые содержания смол были неразличимы с учетом ошибки эксперимента. Этот результат свидетельствует об отсутствии прямой зависимости между содержанием твердого вещества и вязкостью. Более вероятно, что окисленный крахмал кассавы изменил молекулярную структуру смолы, что увеличило вязкость модифицированных смол. Модифицированные смолы имели более короткое время отверждения при том же содержании отвердителя (NH 4 Cl).
Таблица 1 также показывает, что прочность сцепления смолы значительно улучшилась после добавления окисленного крахмала кассавы. В частности, сопротивление сдвигу во влажном состоянии (F / U = 1,0) увеличилось на 56% с 0,32 МПа до 0,50 МПа. Эти результаты также показывают, что окисленный крахмал кассавы не является наполнителем, но, вероятно, играет роль молекулярного сшивающего агента.
Таблица 1. Свойства чистых и модифицированных карбамидоформальдегидных смол
FT-IR анализ смол
Спектры FT-IR различных UF-смол показаны на рис.1. Новые и модифицированные УФ-смолы имели довольно схожие структуры, что указывает на отсутствие свободного окисленного крахмала маниоки (Sheng et al. 2011). Сильное поглощение полосы модифицированной смолы между 3000 см -1 до 3500 см -1 было приписано водородным связям N-H и O-H или воде. Когда мольное отношение F / U составляло 1,0, этот пик становился слабее. В диапазоне от 1500 см -1 до 1700 см -1 пики поглощения полосы изгибных колебаний N-H функциональной группы амида II также уменьшались.
Рис. 1 (а). ИК-Фурье спектры чистой и модифицированной УФ смолы с окисленным крахмалом кассавы. а) смола UF1.0; б) Смола UF1.3
Рис. 1 (б). ИК-Фурье спектры чистой и модифицированной УФ смолы с окисленным крахмалом кассавы. а) смола UF1.0; б) Смола UF1.3
В полосе, расположенной на 1658 см -1 , растяжения не наблюдалось, что означает, что могла иметь место реакция между -COOH и N-H или -NH 2 .Аналогичные изменения произошли в полосе, расположенной на 1264 см -1 , относящейся к колебаниям растяжения COC эфирной связи, и на 1030 см -1 , отражая режим растяжения и колебаний связей CO и OH в -CH . 2 ОН группа. Однако полоса, расположенная на 1141 см -1 , относящаяся к растяжению C-N, и полоса, расположенная на 616 см -1 , были подобны до и после добавления окисленного крахмала кассавы. Когда мольное отношение F / U было равно 1.3, изменения в спектрах были аналогичны таковым для смолы UF 1.0 , но содержание функциональных групп было другим.
Анализ смол ЯМР
13 C-ЯМР-анализ использовали для дальнейшего изучения структурных изменений чистых и модифицированных смол, как показано на фиг. 2 и 3 соответственно. Распределение сдвигов для различных групп приведено в таблице 2. Распределение сигналов в этих спектрах показывает, что окисленный крахмал кассавы был интегрирован в систему смолы UF.Также наблюдались различные эффекты на структурное распределение смол из-за различных молярных соотношений F / U. Кроме того, добавление окисленного крахмала кассавы эффективно снижает содержание различных типов эфиров как в смолах с низкими мольными отношениями F / U, так и в смолах с высокими мольными отношениями F / U. Это одна из причин, по которой окисленный крахмал кассавы используется для снижения содержания свободного формальдегида в смолах. Этот феномен также соответствовал ранее опубликованным результатам (Li 2001; Zhu 2013).
При более низких мольных соотношениях F / U снижение содержания эфира (-CH 2 -O-CH 2 -) было несколько более значительным, чем при более высоких мольных соотношениях F / U.Это было связано с перестройкой некоторых нестабильных структур УФ-смолы и относительно высоким содержанием конечной мочевины и окисленного крахмала, которые могли соединяться с большим количеством формальдегида. Следовательно, легко получить метилолмочевину с небольшой молекулярной массой, которая обеспечивает высокое содержание связей с метилольными связями (-CH 2 OH). Однако содержание связи метиленовой (-CH 2 -) связи уменьшается, особенно амидного типа I, что приводит к снижению общего содержания метилена. Эти изменения указывают на то, что окисленный крахмал может препятствовать реакции между свободной мочевиной и формальдегидом, уменьшая количество метиленовых мостиковых связей.Следовательно, в Таблице 2 заметно увеличение содержания гидроксиметила с 22,2% до 28,3%, но содержание метилена уменьшилось с 61,6% до 58,9%. Кроме того, для щелочных условий можно комбинировать солевое соединение между оставшимся окислительным крахмалом и мочевиной.
Рис. 2. 13 C-ЯМР спектр УФ смол (F: U = 1,0)
Рис. 3. 13 C-ЯМР спектр УФ смол (F: U = 1,3)
По мере того, как мольное отношение F / U продолжало увеличиваться, изменения содержания связей метилена (-CH 2 -) и метилола (-CH 2 OH) также можно увидеть в таблице 2, которые отличаются от таковых для более низкого F / U мольные отношения.Это можно объяснить относительно высоким содержанием формальдегида в смоле из-за меньшего количества добавленной конечной мочевины. Конечный мочевина может сначала прореагировать с формальдегидом с образованием метилолмочевины после добавления мочевины из-за нестабильности эфирной связи и оставшегося содержания формальдегида в смоле. Конечная мочевина прореагировала с альдегидными (-CHO) группами окислительного крахмала, образуя полимеры на основе крахмала. В UF 1 было более высокое содержание метиленовой (-CH 2 -) связи и более низкое содержание метилольной связи (-CH 2 OH).3-3 , что указывает на то, что метиленовые (-CH 2 -) мостиковые связи в значительной степени становятся основным типом комбинации между окислительным крахмалом и мочевиной.
Таблица 2. 13 Определение C-ЯМР и содержание чистых и модифицированных УФ-смол с различным молярным соотношением
Дифференциальная сканирующая калориметрия
Кривые отверждения различных УФ-смол, показанные на рис. 4, имеют несколько общих черт. Модифицированные смолы имели более низкие температуры начала и пиковые температуры, что означает, что окисленный крахмал маниоки с содержанием 3% заметно ускорял отверждение УФ-смолы.Однако разные мольные отношения F / U показали разные тенденции изменений. Начальная температура снижалась на 20 ° C, когда мольное отношение F / U составляло 1,0, но степень изменения температуры начала отверждения была намного меньше, когда мольное отношение F / U составляло 1,3. Эти результаты согласуются с изменением времени отверждения, приведенным в Таблице 1.
По мере уменьшения мольного отношения F / U скорость отверждения UF-смолы может снижаться из-за уменьшения плотности сшивки. В этом исследовании окисленный крахмал кассавы играет роль сшитого агента в процессе отверждения УФ-смолы.Таким образом, более низкое мольное отношение F / U привело к более быстрому отверждению УФ-смолы.
Из-за различий в распределении функциональных групп в чистых и модифицированных смолах, смолы показали разные характеристики отверждения, а полученные модифицированные смолы имеют гораздо более высокую прочность сцепления и водостойкость. Результаты отверждения и анализа 13 C-ЯМР смол подтвердили, что механизм окисления, посредством которого крахмал кассавы модифицирует карбамидоформальдегидную смолу, различен для различных мольных соотношений F / U, хотя они имеют идентичные пропорции добавления окисленного крахмала.
Рис.4. Кривые ДСК смол UF1.0 (а) и UF1.3 (б)
ВЫВОДЫ
- Окисленный крахмал маниоки был использован для модификации смол UF. Окисленный крахмал маниоки добавляли в систему УФ-смолы на заключительной стадии процесса смолы. Это увеличило вязкость смолы и прочность связки, а также уменьшило время отверждения и температуру начала отверждения. Для смол с более низкими мольными отношениями F / U результаты анализа DSC показали, что эффекты были особенно заметными. Анализ
- FT-IR и 13 C-NMR показал, что окисленный крахмал кассавы оказывает видимое влияние на содержание функциональных групп в смолах. Это уменьшило содержание эфира как для низких, так и для высоких мольных соотношений F / U. Однако, когда мольное соотношение F / U было ниже, добавление окисленного крахмала маниоки препятствовало реакции между мочевиной и формальдегидом, что приводило к относительно более низкому содержанию метилена. Из-за высокого конечного использования мочевины смола UF 1.0-3 имела больше гидроксиметильных групп.Более высокое мольное отношение F / U показало другие изменения, поскольку в смоле присутствовало достаточное количество формальдегида. Окисленный крахмал играет ключевую роль в снижении содержания формальдегида.
- Приведенные выше результаты продемонстрировали, что окисленный крахмал маниоки модифицирует УФ-смолу. В сложных системах окисленный крахмал не действует как наполнитель, а скорее химически реагирует с УФ-полимерами. Однако механизм реакции остается неясным.
ПОДТВЕРЖДЕНИЕ
Эта работа была поддержана ключевыми проектами Национальной программы развития науки и технологий в течение 12-го пятилетнего периода (2015BAD14B03) и Фондом научных исследований Юго-Западного университета лесного хозяйства.Кроме того, авторы благодарят Пу Лонга за помощь в исследовании.
ССЫЛКИ
Данки, М. (1998). «Мочевинно-формальдегидные (УФ) адгезивные смолы для дерева», International J. Adhesion Adhesives 18 (2), 95-107. DOI: 10.1016 / S0143-7496 (97) 00054-7
ГБ / Т 14074 (2006 г.). «Методы тестирования клея и смолы для древесины», Управление по стандартизации Китая, Пекин, Китай.
ГБ / т 17657 (2013 г.). «Методы испытаний для оценки свойств древесных панелей и древесных панелей с декорированной поверхностью», Управление по стандартизации Китая, Пекин, Китай.
Kaewtatip, K., and Tanrattanakul, V. (2008). «Получение крахмала маниоки, привитого полистиролом, путем суспензионной полимеризации», Углеводные полимеры, 73 (4), 647-655. DOI: 10.1016 / j.carbpol.2008.01.006
Ким, М. Г. (2010). «Исследование выбранных параметров синтеза карбамидоформальдегидных смол клеевого типа для древесины с помощью спектроскопии C-ЯМР 13 III», Journal of Applied Polymer Science 80 (14), 2800-2814. DOI: 10.1002 / app.1397
Ли, Т.Х., Лян, Дж. Х., Цао, М., Го, Х. С., Се, Х. Г., и Ду, Г. Б. (2016). «Повторное выяснение кислотно-катализируемых реакций мочевины и формальдегида: теоретическое исследование и исследование 13 C-ЯМР», J. Appl. Polym. Sci. 133 (48), 44339-44356. DOI: 10.1002 / APP.44339
Мансури, Х. Р., Томас, Р., Гарнье, С., и Пицци, А. (2010). «Фторированные полиэфирные добавки для улучшения характеристик карбамидоформальдегидных клеев для деревянных панелей», Journal of Applied Polymer Science 106 (3), 1683-1688.DOI: 10.1002 / app.26749
Нуряван А., Парк Б.-Д., Адья П. и Сингх А. П. (2014). «Проникновение карбамидоформальдегидных смол с различным мольным соотношением формальдегид / мочевина в ткани мягкой древесины», Wood Science and Technology 48 (50), 889-902. DOI: 10.1007 / s00226-014-0649-9
Парк, Б. Д., Санг, М. Л., и Парк, Дж. Ю. (2008). « 13 C-ЯМР-спектроскопия адгезивов на основе карбамидоформальдегидной смолы с различным соотношением формальдегид / уреамол», журнал Корейского института пожарных наук и инженерии, 36 (2), 63-72.DOI: 10.5658 / WOOD.2008.36.2.063
Румели Э., Пападопулу Э., Павлиду Э., Бикиарис Д., Параскевопулос К. М. и Криссафис К. (2012). «Синтез, характеристика и термический анализ карбамидоформальдегидных / наноразмерных смол 2 », Thermochimica Acta 527, 33-39. DOI: 10.1016 / j.tca.2011.10.007
Синха, С. К., Хали, Д. П. (2015). «Синтез и сравнение термореактивной смолы фенол-мочевино-формальдегид (ППУ) с коммерческими синтетическими смолами», Asian Journal of Research in Chemistry 8 (7), 449-452.DOI: 10.5958 / 0974-4150.2015.00072.3
Шэн Ю., Ван, К., Сюй, X. С., Цзян, В., Ган, С. К., и Цзоу, Х. Ф. (2011). «Окисление кукурузного крахмала с использованием кислорода в качестве окислителя без катализатора», LWT — Food Science and Technology 44 (1), 139-144. DOI: 10.1016 / j.lwt.2010.05.004
Тохмура С. И., Иноуэ А. и Сахари С. Х. (2001). «Влияние содержания меламина в меламино-мочевиноформальдегидных смолах на выделение формальдегида и структуру отвержденной смолы», Journal of Wood Science 47 (6), 451-457.DOI: 10.1007 / BF00767897
Васкес, Г., Лопес-Суэвос, Ф., Вильяр-Гареа, А., Гонсалес-Альварес, Дж., И Анторрена, Г. (2004). « 13 C-ЯМР анализ фенол-мочевино-формальдегидных форполимеров и фенол-мочевино-формальдегид-таниновых клеев», Journal of Adhesion Science and Technology 18 (13), 1529-1543. DOI: 10.1163 / 1568561042411231
Ван С., Чжан Ф., Чен Ф. и Панг З. (2013). «Приготовление сшивающего адгезива из крахмала маниоки и его применение в мелованной бумаге», BioResources 8 (3), 3574-3589.DOI: 10.15376 / biores.8.3.3574-3589
Янг Но Б. и Ким М. Г. (2007). «Оценка мочевиноформальдегидных смол, модифицированных меламином, в качестве связующих для древесностружечных плит», Journal of Applied Polymer Science 106 (6), 4148-4156. DOI: 10.1002 / app.26770
Занетти М., Каузин В., Сайни Р., Кардин А. и Кавалли Р. (2014). «Влияние танина на повышение адгезионных свойств УФ при высокой температуре исследовано с помощью анализа ТМА и ТГА», European Journal of and Wood and Wood Products 72 (3), 385-392.DOI: 10.1007 / s00107-014-0795-7
Чжан, Дж., Ван, X., Чжан, С., Гао, К., и Ли, Дж. (2013). «Влияние стадии добавления меламина на характеристики и характеристики отверждения меламино-мочевиноформальдегидной смолы» BioResources 8 (4), 5500-5514. DOI: 10.15376 / biores.8.4.5500-5514
Чжоу, X., Эссави, Х.А., Пицци, А., Ли, X., Паш, Х., и Преториус, Н. (2013). «Дендримеры поли (амидоаминов) различных поколений в качестве компонентов меламино-мочевиноформальдегидных клеев (MUF), используемых для производства древесностружечных плит: каковы положительные последствия?» Journal of Polymer Research 20 (10), 1-14.DOI: 10.1080 / 01694243.2012.727166
Чжу, X., Сюй, Э., Линь, Р., Ван, X., и Гао, З. (2013). «Снижение выделения формальдегида в карбамидоформальдегиде с использованием модифицированного крахмала с помощью сильнокислотного процесса», Journal of Applied Polymer Science 131 (9), 40202. DOI: 10.1002 / app.40202
Статья подана: 13 июня 2017 г .; Рецензирование завершено: 19 августа 2017 г .; Доработанная версия получена и принята: 22 августа 2017 г .; Опубликовано: 30 августа 2017 г.
DOI: 10.15376 / biores.12.4.7590-7600
Микросферы карбамидоформальдегида как потенциальная добавка к клею для древесины | Journal of Wood Science
Синтез УФ-микросфер в соответствии со ссылкой [21] был несложным и привел к порошку УФ, как показано на рис. 1. Как и ожидалось, частицы имели красивую сферическую форму и располагались в ламинарной субструктуре, обеспечивающей высокую удельную поверхность. площадь. Диаметр сфер обычно составлял от 5 до 20 мкм.
Рис. 1Сканирующая электронная микроскопия УФ-микросфер при разном увеличении; a × 500, b × 1.2 × 10 4
Различные молекулярные массы гидроксиэтилцеллюлозы приводили к различным формам и поверхностям микросфер, как показано на рис. 2. При более низкой молекулярной массе все сферы имели структурированные поверхности и были сферическими, за исключением небольшого количества с искаженной геометрией. С увеличением молекулярной массы эта пропорция увеличивалась, и особенно глобулярные микросферы имели плоские неструктурированные поверхности. Сухой порошок, как показано на фиг. 1 и 2, приготовленные из низкомолекулярной гидроксиэтилцеллюлозы, использовали для всех последующих экспериментов без какой-либо дополнительной обработки.
Рис. 2Изображение УФ-микросфер, полученных с помощью сканирующей электронной микроскопии, при различных молекулярных массах гидроксиэтилцеллюлозы; a 9 × 10 4 г / моль, b 1,3 × 10 6 г / моль
Составы UF-микросфер с промышленным клеем, приготовленные в различных соотношениях, показали разную вязкость, как показано в таблице 1. Вязкость эталона составляла около 300 мПа · с и снижалась с добавлением микросфер до 200 мПа · с (-33%).Однако вязкость состава, содержащего 1 часть микросфер и 1 часть смолы, была выше и сравнима с вязкостью сравнения, измеренной сразу после добавления отвердителя. Замечательна была высокая вязкость эталона через 1 и 2 часа после добавления отвердителя. Также были измерены высокие вязкости состава 0,1: 1 (микросферы: УФ). Через 1 час вязкости эталона и состава 0,1: 1 составили 1 × 10 3 и 650 мПа · с, поэтому все еще подходят для обычных промышленных систем нанесения клея.Но через 2 часа вязкости увеличились почти до 7 × 10 4 и 3 × 10 4 мПа · с, поэтому они больше не применимы. Однако для составов 0,5: 1 и 1: 1 были измерены вязкости ниже 1 × 10 3 мПа · с. Это наблюдение можно объяснить более низким содержанием отвердителя при добавлении микросфер, поскольку содержание отвердителя было установлено постоянным на уровне содержания твердой УФ-смолы (3%). При добавлении микросфер содержание реактивного UF последовательно заменяется микросферами, одновременно снижая содержание отвердителя.Через 3 часа все клеевые составы стали твердыми.
Таблица 1 Вязкость различных композиций смола-микросфера, измеренная с помощью реометра конус / пластина при постоянной скорости сдвига 10 с -1 , при 20 и 40 ° C, сразу после добавления отвердителя, а также через 1 и 2 часа после этого , для определения жизнеспособностиДля оценки прочности склеивания на образцы древесины были нанесены различные клеевые составы. В отличие от ссылки, составы, содержащие микросферы, оказались слишком сухими и очень быстро затвердевали после нанесения, хотя жизнеспособность увеличивалась.Это могло быть признаком того, что жидкая часть состава очень быстро впитывалась древесной массой, и на поверхности шпона были видны только твердые микросферы. Однако общая обработка и характеристики отверждения не изменились и были сопоставимы с немодифицированным клеем.
Прочность адгезионного соединения образцов облицовки, склеенных немодифицированным и модифицированным микросферами UF, показала некоторые эффекты добавления микросфер, которые, однако, не были значимыми в статистическом смысле из-за высокой вариабельности внутри групп (рис.3). В целом, прочность связи образцов, отвержденных при более высокой температуре, была выше, как и ожидалось от кинетики УФ отверждения [2]. Самые низкие средние значения прочности связи наблюдались для двух вариантов, склеенных немодифицированным клеем, с 3,1 МПа при 90 ° C и 3,5 МПа при 120 ° C. Соответственно, для обеих температур наблюдалось небольшое, но последовательное увеличение прочности связи с увеличением содержания микросфер (рис. 3). Фактически, самые высокие значения адгезионной прочности были измерены с использованием клеевого состава, содержащего 1 часть смолы (в пересчете на сухую массу) и 1 часть микросфер, отвержденных при 120 ° C.При среднем значении 4,2 МПа было достигнуто увеличение на 20%. Хотя эти результаты не демонстрируют существенного улучшения прочности связи, они представляют собой четкое доказательство того, что высокая фракция порошка UF микросфер, отвержденного в сухом состоянии, может быть добавлена к UF адгезиву без ухудшения характеристик сцепления.
Рис.3Прочность адгезионной связи образцов древесины, скрепленных УФ-смолой, модифицированной разным количеством УФ-микросфер, отвержденных при двух разных температурах (t-образные полосы: 1.5 × высота поля или, если значение в этом диапазоне отсутствует, минимальное или максимальное значения)
Сравнение кинетики отверждения двух наиболее крайних используемых вариантов адгезива, т.е. немодифицированного УФ-адгезива и адгезива, содержащих равные количества смолы и твердых УФ-микросфер, показано на рис. 4. При более низких температурах сигнал дифференциальной сканирующей калориметрии (ДСК) происходило в первую очередь из-за испаряющейся влажности, экзотермическое отверждение немодифицированного клея началось при температуре около 70 ° C и достигло максимума при 90 ° C, что хорошо согласуется с литературными данными [26,27,28,29].
Рис. 4Дифференциальная сканирующая калориметрия ( a ) и термогравиметрический анализ ( b ) немодифицированного УФ и адгезива, содержащих равные количества смолы и твердых микросфер УФ
По сравнению с немодифицированным клеем состав, содержащий микросферы, показал аналогичное поведение при отверждении с заметной разницей в менее интенсивном максимуме при 90 ° C. Это различие можно объяснить тем, что количество реактивного материала в модифицированном адгезиве уменьшилось на 50%.При 130 ° C оба состава показали острый и интенсивный эндотермический пик, связанный с эндотермическим отщеплением формальдегида [26], создавая этиленовые связи из эфирных связей с высвобождением формальдегида. Эндотермическое разложение смолы начиналось при 215 ° C для немодифицированного клея и при 220 ° C для модифицированного. В хорошем согласии с литературными данными [28] сильный эндотермический пик соответствует отчетливому падению массы сигнала термогравиметрического анализа.
Таким образом, добавление УФ-микросфер к УФ-смоле не повлияло на ее свойства отверждения.Различия в интенсивности пиков можно объяснить кинетикой реакции, известной из литературы. Открытие того, что адгезионная прочность осталась неизменной или даже немного улучшилась, когда 50% реакционноспособной УФ-смолы было заменено в основном инертными УФ-микросферами (соотношение 1: 1), оставалось объяснить. Для этого были исследованы линии склеивания и, в частности, проникновение клея. Превосходный контраст между клеем и массивной древесиной был получен с применением метода двойного окрашивания, показанного на рис.5. Уже при оптическом осмотре были отчетливо видны четкие различия между образцами, склеенными немодифицированным клеем, и составами, модифицированными УФ-микросферами. Немодифицированный УФ проникал в древесину глубже (рис. 5а, б), чем модифицированный УФ, который концентрировался близко к поверхности образца (рис. 5в, г). В количественном отношении средняя глубина проникновения составляла около 0,15 мм для немодифицированного UF и 0,08 мм для модифицированного UF (рис. 6).
Рис. 5Поперечные срезы образцов древесины после испытания прочности адгезионного соединения, окрашенных Brilliant Sulphaflavin и Gentian Violet.Контрольный образец (0,0: 1) в псевдоцвете ( a ) и в виде двоичного изображения ( b ), где клей и нижняя линия шпона черные. Такое же соотношение микросфер и УФ-смолы (1,0: 1) в псевдоцвете ( c ) и в виде двоичного изображения ( d )
Рис. 6Изменчивость проникновения клея в древесную массу для двух клеевых составов (t-образные стержни: 1,5 × высота коробки или, если нет значения в этом диапазоне, минимальное или максимальное значения)
Вязкость является определяющим фактором проницаемости жидкостей.Реологическое поведение изменилось с добавлением микросфер. Наблюдаемое начальное снижение вязкости с последующим увеличением вязкости (таблица 1) могло быть связано с морфологией микросфер. Шарики позволяют легко прокручивать матрицу ультрафильтрации, но на определенных уровнях загрузка слишком высока, что останавливает поток ультрафильтрации и микросфер. Это предположение хорошо сравнивается с исследованием, предлагающим объяснение сопоставимого реологического поведения в дисперсиях наносфер кремния и пластинок монтмориллонита и их взаимодействия [30].
Пенетрация измерялась для немодифицированных адгезивов и при максимальном добавлении микросфер, тогда как оба состава демонстрировали сопоставимые вязкости. Таким образом, вязкость может быть исключена для объяснения уменьшения проникновения, а добавление микросфер привело к уменьшению глубины проникновения смолы до половинного значения, измеренного для немодифицированного адгезива.
Помимо глубины проникновения, изменчивость глубины проникновения была значительно уменьшена в модифицированном варианте, что указывает на отчетливую концентрацию клея вблизи поверхности образца.Одно из объяснений может заключаться в том, что микросферы остаются на поверхности образца, будучи твердыми телами, неспособными проникнуть в структуру твердой древесины из-за размера выше микрона. Предполагается, что из-за большой удельной поверхности значительные количества жидкого клея адсорбируются на поверхности микросфер и, следовательно, остаются иммобилизованными на поверхности древесины, уменьшая общее проникновение. В хорошем согласии с недавним исследованием УФ-адгезива, модифицированного микрофибриллированной целлюлозой [18], предполагается, что концентрация адгезива на поверхности образца, обеспечиваемая добавлением УФ-микросфер, позволяет формировать связи с прочностью, аналогичной немодифицированному адгезиву.Только небольшая часть клея способствует образованию склеивания, в то время как значительное количество смолы проникает глубоко в массу и не способствует склеиванию.
Хотя в настоящем исследовании были обнаружены интересные и неожиданные эффекты, его практическое значение остается неясным. Интересно, что в адгезив можно добавлять значительные количества инертной добавки, не ухудшая его прочности сцепления. Это открытие может послужить основой для дальнейших исследований, в которых микросферы UF снабжены дополнительными функциями, такими как, например,например, свободные метилольные группы, иммобилизирующие ферменты [31], или микрокапсулированные ароматизаторы, компенсирующие нежелательные терпеновые запахи древесины [32], включены в линию связи. Кроме того, аминопласты являются основным полимером, используемым в микрокапсулировании [33, 34]. Микрокапсулирование широко обсуждается с точки зрения обеспечения дополнительных функций покрытиям [35] или полимерам в целом [36]. Поскольку настоящее исследование показало, что добавление микросфер UF возможно без ухудшения прочности связи, также должно быть осуществимо включение микрокапсул из аминопласта с, например,g., функция самовосстановления в клеевых линиях для дерева. Самовосстановление особенно интересно для производителей ДСП, использующих УФ в качестве клея из-за его высокой хрупкости, например, для увеличения срока службы мебели. В некоторых исследованиях уже сообщается о микрокапсулировании полимеризуемых жидкостей в качестве заживляющих агентов, таких как дициклопентадиен, стирол или эпоксидная смола [37,38,39].
(PDF) Клеи карбамидоформальдегидные
Крупное мировое производство древесноволокнистых плит средней плотности (МДФ) за несколько десятилетий может генерировать аналогичное количество отходов МДФ (wMDF) после срока службы более двадцати годы.Образование wMDF вызовет экологические проблемы при захоронении или захоронении мусора. сжигание, которое требует переработки wMDF в переработанный MDF (rMDF). Тем не менее переработка wMDF — непростая задача, потому что они содержат карбамидоформальдегид (UF) смолы в качестве клея для склеивания волокон. Поэтому данная диссертация посвящена развитию клеевые технологии для переработки wMDF в панели rMDF. Эта диссертация состоит из девяти глав, в которых обсуждаются клеевые технологии для переработка wMDF.Вкратце, первая глава представляет собой общее введение в это исследование. включая предысторию, цели и организацию диссертации. Вторая глава изучил доступную литературу, касающуюся МДФ, УФ-смол, окисленного крахмала (ОС) и переработка wMDF. Третья глава посвящена механизмам гидролиза отвержденных смол UF. Необработанный и отвержденные УФ-смолы, полученные с двумя различными мольными отношениями формальдегида к мочевине (F / U) и с разными уровнями отвердителя подвергались гидролизу за разное время.Их гидролизаты были проанализированы с помощью гель-проникающей хроматографии (ГПХ), инфракрасного излучения с преобразованием Фурье. (FTIR) и жидкостная 13-углеродная спектроскопия ядерного магнитного резонанса (13C-ЯМР). В гидролизаты имели молярную массу в диапазоне 580-706 г / моль, которые состоят из метиленовые связи, гидроксиметильные группы, моно- и три-гидроксиметилмочевины. Эти считалось, что химические соединения вносят основной вклад в гидролиз затвердевшего UF смолы. В четвертой главе для гидролиза МДФ использовались две кислоты, две щелочи и вода. для удаления отвержденных смол УФ из вМДФ.Для гидролиза МДФ использовали различные условия гидролиза, такие как температура, время и химический состав. Более высокая температура и кислая среда извлекают почти 75% отвержденных смол, тогда как вода и щелочи удаляют менее 55% отвержденных смол. Кислый раствор гидролизует более отвержденные УФ смолы в МДФ. Таким образом, гидролиз с использованием раствора щавелевой кислоты при 80 ° C в течение 2 часов оказался оптимальным условием для удаления затвердевших УФ-смол из МДФ. Влияние содержания переработанных волокон (RF) на свойства переработанных панелей из МДФ (rMDF). были оценены в пятой главе.Различное содержание RF, такое как 0, 5, 10, 20, 30, 50 и 100% были использованы для приготовления rMDF. Характеристики RF и первичного волокна (VF), такие как также оценивались физические, химические и морфологические особенности. Более высокое содержание RF дало большую щелочную буферную способность и более высокий pH. В результате самый высокий прочность внутреннего скрепления (IB) была получена при 10% RF, и прочность IB снизилась. потом. Аналогичная тенденция к прочности IB наблюдалась для модуля разрыва (MOR). и модуль упругости (MOE) rMDF при увеличении содержания RF.Однако набухание по толщине (TS), водопоглощение (WA) и выделение формальдегида (FE) rMDF обычно уменьшаются по мере увеличения содержания RF. Свойства rMDF были приемлемы для комбинации 10% RF и 90% VF. Улучшение свойств rMDF рассматривалось за счет армирования RF-содержащих отвержденных UF-смол. В шестой главе исследована модификация УФ смол различными окисленными уровни крахмала (OS). Клеи УФ – ОС были приготовлены путем смешивания 5, 10 и 15% ОС. на основе твердого содержания смол УФ.1% блокированного полимерного 4,4-дифенилметана диизоцианат (B-pMDI) в расчете на сухую массу ОС был добавлен в качестве сшивающего агента. В реакция между -COOH-группами OS с -NCO-группами B-pMDI привела к образованию амидных связей при 1586 и 1348 см-1, что подтверждено FTIR. При добавлении ОС изменено реакционная способность УФ смол. Независимо от мольного отношения F / U, статистический анализ показал, что добавление 10% OS в УФ смолы обеспечивает наилучшие характеристики фанеры. В седьмой главе описывается приготовление клеев ОС в сочетании с B-pMDI как сшивающий агент и PVA как усилитель адгезии для вторичной переработки МДФ.Группы -COOH OS реагировали с группами -NCO B-pMDI с образованием амида связей, и группы -CHO реагировали с группами -OH ПВС через водород склеивание. При использовании в качестве клея -COOH OS образует сложноэфирные связи с -OH из Волокна МДФ. МДФ, склеенный клеем 1% B-pMDI / 15% PVA / OS, имел прочность по IB 0,13 МПа и 0,01 мг / л (почти ноль) FE. Это демонстрирует, что B-pMDI / PVA / OS клей является возможной альтернативой существующим УФ смолам для подготовки МДФ. панели с нулевым выбросом.В восьмой главе рассказывается о клеях OS, обеспечивающих баланс их адгезии и дезинтеграция МДФ за счет контроля степени окисления, а также типов и уровней сшивающий агент для замены УФ-смол для легкой переработки МДФ.