Сверление алюминия и отверстий в алюминии на заказ
Сверление – это эффективный и простой метод получения отверстий в сплошном материале. Он выполняется при помощи сверла, которое совершает по отношению к своей оси вращательное и поступательной движение.
Основные инструменты для сверления алюминия
Сверление применяется для получения отверстий под:
- резьбу;
- заклепки;
- крепежные болты;
- шпильки и т.д.
Нужные инструменты — электродрель и сверла. Электродрель устанавливается в сверлильную стойку. В основном для сверления металлов используются малые и средние обороты от 500 до 1000 оборотов в минуту. Применение высоких оборотов приводит к разогреву сверла, может произойти его отжиг либо разупрочнение. При работе не надо применять сильное давление. Подача должна быть медленной и плавной.
Спиральные сверла для дрели изготавливаются:
- из инструментальной стали;
- с напылением из твердого сплава;
- цельные твердосплавные;
- со вставкой из твердого сплава.
Их применяют для всех работ по всяким материалам.
Сверление алюминия как металла
Алюминий относится к металлу:
- очень вязкому;
- мягкому;
- легкоплавкому.
Он имеет температуру плавления 660 градусов. Это сказывается на его сверлении, при выполнении такой работы может произойти:
- расплывание отверстия;
- расплавление алюминия на режущей кромке;
- набухание краев;
- закусывание сверла.
В работе алюминий обволакивает сверло, что способствует затруднению его проникновения вглубь металла. Получаемое отверстие значительно расширяется. Поэтому сверление алюминия необходимо проводить при оборотах в 1,5 раза меньше, чем для других металлов. Также сверло можно охлаждать:
- эмульсией;
- жидким машинным маслом;
- или водой.
Инструмент нужно подавать без налегания, понемногу. Сверло, предназначенное для сверления алюминия, должно быть с фабричной заточкой, острое или заостренное на специальном станке. Для алюминия не пригодны сверла, которые наточены вручную. В процессе сверления оно тупится. Это зависит от:
- оборотов;
- силы подачи;
- охлаждения и т.д.
Перед тем, как начать работу, нужно при помощи керна разместить само отверстие. Для этого его отверстие устанавливают в нужный центр отверстия, потом производят по нему удар молотком.
Если необходимо в алюминии сделать точное отверстие, допустим для изготовления резьбы, то нужно:
- применять охлаждающую жидкость. Использование смазочно-охлаждающей жидкости является обязательным, иначе сверло может сломаться;
- чаще вытаскивать его из отверстия;
- очищать.
При сверлении алюминия наилучшим считается угол приблизительно от 130 до 140 градусов.
Советы по проведению сверления
При необходимости получения в металле множества отверстий, есть вероятность перегрева и затупления сверла из любого металла. Чтобы этого избежать периодически в процессе сверления необходимо сверло опускать в емкость, где налито машинное масло, можно и отработанное.
Используя этот простой прием, удается просверлить много отверстий всего одним сверлом, которое на протяжении всей работы и после не имеет признаков износа. Недостатком такого метода является разбрызгивание смазывающего масла. Однако решить проблему можно сверлением через бумагу либо полиэтиленовый пакет.
Наша компания на заказ готова выполнить работу по сверлению алюминия.
Как добиться точной сверловки алюминия в домашних условиях?
avex29.06.2019
1326
Вопросы и ответы Без решения проблемы не могу начать строить 3d принтер системы ультимейкер. (Все необходимое, кроме корпуса, кареток и основания стола уже куплено и ждет монтажа).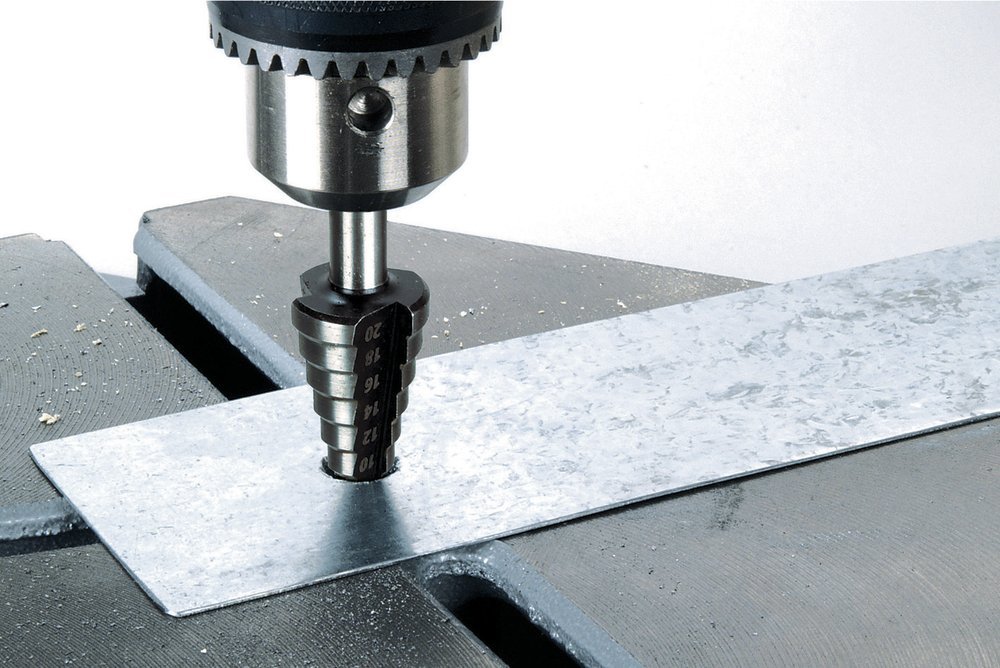
Подскажите, пожалуйста, пути решения этой задачи.
Если дома нельзя, к кому обращаться? К фрезеровщику с ЧПУ? У него может быть та же точность, что и у лазерщиков.
Ответы на вопросыПопулярные вопросы
Mr_Pon4ik15. 07.2021
828
Если вкратце, то происходит засор сопла(пластиком) на одинаковой высоте(на мой взгляд). Собрал принтер для печати мелких деталек соплом 0.2мм. Однако…
Читать дальше Xray600623.07.2021
275
Тема то обречена, но не попытки исправить печать))Собрал себе принтер ZAV mini с платой Lerdge, прошивка новая, Драйверы 2208, на эк.
Загрузка
22.02.2018
17722
Понимаю, что тема 100500 раз обсуждалась, но не удалось нигде найти обобщающей информации, в основном все в одной куче советуется.Пр…
Сверление алюминиевых сплавов — Энциклопедия по машиностроению XXL
Для сверления алюминиевых сплавов необходимо применять сверла с большими углами ф и со, чем для сверления черных металлов угол ф должен быть равен 66—70°, а угол наклона винтовых канавок равен 35— 45°, задний угол а = 8 10°.
Сверление алюминиевых сплавов спиральными сверлами из стали Р9 и Р18
Сверление алюминиевых сплавов [c.269]
В уз.че крепления стальной подшипниковой втулки в корпусе из алюминиевого сплава способ крепления винтом, завинчиваемым с торца во втулку и корпус (рис. 160, а), практически неосуществим при сверлении по стыку втулки и корпуса сверло уходит в сторону более мягкого металла. В этом случае необходимо применять крепление с разновременным сверлением корпуса и втулки (виды б, в). [c.143]
Ra = 20 мкм. При сверлении отверстий диаметром до 10 мм в деталях из чугуна и алюминиевых сплавов при подаче по III группе может быть достигнута шероховатость поверхности Ra = 10 мкм.
Алюминиевые сплавы Сверление Растачивание, фрезерование Сливная Дробленая 0,1—0,2 0,7 — 0,75
[c. 154]
Для сверления отверстий в алюминиевых сплавах, кроме Д16, глубиной до id [c.337]
Для сверления отверстий в алюминиевых сплавах типа Д16, глубиной более d [c.337]
Подачи при сверлении зенкеровании и развертывании сквозных отверстий в алюминиевых сплавах инструментами из быстрорежущей стали Р18 [c.376]
Поправочные коэффициенты на скорость резания при сверлении и зенковании отверстий в алюминиевых сплавах
Сверление отверстий глубиной до 4d в алюминиевых сплавах, кроме сплава марки Д16 [c.202]
Сверление отверстий глубиной более 4d в алюминиевых сплавах типа Д16 [c.202]
Сверление ё -6… 30 мм глубиной до 4 в деталях из алюминиевых сплавов (кроме Д16) [c.167]
Сверление ё=Ъ… 30 мм глубиной АО А ё в деталях из алюминиевых сплавов типа Д16 [c.167]
Скорость резания v при сверлении и зенкеровании деталей из алюминиевых сплавов
[c. 411]
Смазочно-охлаждающие жидкости. Применение при сверлении соответствующих смазочно-охлаждающих жидкостей вызывает по сравнению с обработкой всухую уменьшение осевой силы (силы подачи) и момента от сил сопротивления резанию на 10—30% при обработке сталей, на 10—18% при обработке чугунов и на 30—40% при обработке алюминиевых сплавов. [c.199]
Наконец, к самым последним решениям может быть отнесена конструкция показанная на фиг. 74, д, где, кроме жидкостного уплотнения, предусмотрено питание правой полости цилиндра не через каналы в крышке и стенках цилиндра, а через центральную трубку 1, полость а и радиальные отверстия б штока 2. Последнее позволяет делать стенки цилиндра значительно тоньше и тем самым уменьшить его вес и, кроме того, избавляет от трудоемкой операции по сверлению каналов в самом цилиндре. Уменьшение веса достигается также изготовлением цилиндра и его крышки из алюминиевого сплава. Для повышения тяговой силы пневмоприводов
[c. 141]
Подачи, мм/об, при сверлении стали, чугуна, медных и алюминиевых сплавов сверлами из быстрорежущей стали [c.381]
Сверло (сверление и рассверливание) Серый и ковкий чугун, медные и алюминиевые сплавы Быстрорежущая сталь 20 35 60 75 105 140 170 [c.384]
В исследованиях установлено, что чем больше силовые нагрузки, тем больше погрешности обработки. При сверлении отверстий диаметром 25 мм погрешность расположения их осей почти в 2 раза больше, чем при сверлении аналогично расположенных отверстий диаметром 16 мм. При обработке деталей из алюминиевого сплава точность для одинаковых условий в 1,5-2 раза выше, чем для чугунных деталей. [c.740]
На Волжском автомобильном заводе и ряде машиностроительных предприятий наиболее широко были испытаны СОЖ Укринол-1, МР-1 и ОСМ-3. Данные испытаний свидетельствуют в целом о высокой технологической эффективности эмульсий, приготовленных из Укринола-1, как при обработке конструкционных сталей, алюминиевых сплавов на различных операциях лезвийной и абразивной обработки, так и при обработке труднообрабатываемых материалов нержавеющих сталей — на операциях точения, сверления, фрезерования титановых сплавов — на операция точения, фрезерования и на операции точения тугоплавких металлов и сплавов.

Резка с середины листа, в свою очередь, может производиться, начиная с кромки предварительно просверленного отверстия, диаметр которого не должен быть менее 6 мм, или после пробивки металла непосредственно плазменной дугой. Предварительное сверление отверстий применяется лишь при резке металла большой толщины, когда невозможно пробить металл плазменной дугой, так как сверление отверстий связано с потерями времени и с неудобством выполнения работы, особенно при резке на стационарных машинах. При ручной резке стали, меди и сплавов на медной основе сверление отверстий обычно применяют при толщине более 40 мм, а при резке алюминиевых сплавов — более 50 мм. При резке переносными машинами и на стационарных машинах предварительное сверление отверстий производится при толщине разрезаемого металла более 28 мм для всех металлов.
[c.132]
Насадка СМ-01 представляет собой сменную головку, которая устанавливается на пневматическую сверлильную машину Д2М и позволяет производить сверление отверстий диаметром до 8 мм в алюминиевых сплавах. [c.358]
Подачи при сверлении, зенкеровании, развертывании деталей из алюминиевых сплавов [c.253]
На рис. 74 представлена конструкция поршня из алюминиевого сплава, являвшаяся ранее типичной для двигателей грузовых автомобилей. Поршень имеет четыре канавки для поршневых колец — две для компрессионных и две для маслосъемных (маслосбрасывающих) колец. Последние канавки имеют сверления, предназначенные для пропуска масла внутрь поршня. Поршневой палец рассматриваемого поршня плавающего типа. В связи с этим в бобышках поршня имеются проточки для стопорных колец, удерживающих поршневой палец от осевых перемещений. Юбка поршня имеет цилиндрическую форму с поперечным и продольным разрезами. Разрезы обеспечивают минималь-
[c.144]
Точение, сверление, зенкерование, развертывание, резьбонарезание, фрезерование углеродистых и легированных сталей, серых чугунов и алюминиевых сплавов Точение высокопрочных и жаропрочных сталей [c.100]
Влияние охлаждающе-смазываюш,ей жидкости. Исследованиями установлено положительное влияние жидкости на величину силы подачи и момента. Применение при сверлении жидкостей, и особенно поверхностно-активных, способствует уменьшению силы подачи и момента на 10—35% при обработке пластичных металлов (сталей) на 10—18% при обработке чугуна на 30—40% при сверлении алюминиевых сплавов по сравнению с обработкой всухую. [c.166]
После реконструкции, проведенной с целью устранения недостатков, выявившихся при эксплуатации, завод-автомат выполняет автоматически в определенной последовательности следующие стадии производственного процесса на позициях / — загрузка чушек алюминиевого сплава 2—плавление, рафинирование и очистка сплава от шлака 3 — кокильная отливка 4 — отрезка литников и возврат их в плавильную печь для переплавки 5 — загрузка контейнеров поршнями 6—термическая обработка 7 — автоматический бункер 8 — возврат контейнеров 9 — обработка базовых поверхностей (одновременно у двух деталей) 10 — черновое растачивание и зацентровка (одновременно четырех деталей) 11 — черновое обтачивание (одновременно четырех деталей) 12 — фрезерование горизонтальной прорези (одновременно у четырех деталей) 13 — сверление десяти смазочных отверстий в каждой детали (одновременно у четырех деталей) 14 — чистовое обтачивание (одновременно четырех деталей 15 — разрезание юбки и срезание центровой бобышки (одновременно у четырех деталей) 16 — подгонка веса поршней (одновременно у двух деталей) путем удаления лишнего мет 1лла на внутренней стороне юбки 17 — окончательное шлифование на автоматическом бесцентрово-шлифовальном станке (одновременно четырех деталей) 18 — мойка 19 — автоматический бункер 20 — обработка отверстий под поршневой палец (тонкое растачивание отверстий растачивание канавок под стопорные кольца развертывание отверстий) 21 —мойка 22 — контроль диаметров и конусности юбки и сортировка на размерные группы 23 — контроль формы и размеров отверстий под палец и сортировка на размерные группы 24 — покрытие поршней антикоррозийной смазкой (консервация) 25 — завертывание в водонепроницаемую бумагу (пергамент) 26 — набор комплекта поршней, формирование картонной коробки, заклейка ее и выдача.
[c.467]
Для ориентировочного определения минимального диаметра отверстий можно пользоваться формулой d = d( + ОД /, где I — длина отверстия, мм (рис. 105). Для алюминиевых сплавов и бронз i/q = 5 для чугуноа il = 7 для сталей i/q = 10 мм. Отверстия меньшего диаметра следует сверлить. Длинные отверстия (типа масляных каналов) лучше выполнять сверлением, заливкой трубок или заменять их трубчатыми съемными магистралями. [c.86]
На рис 1 показана схема прибора для ДТА. В центральной части находятся ячейки с двенадцатью образцами, размещенными вокруг эталона. Простые и дифференциальные термопары подводятся через сверления малого диаметра в стенках ячейки. Хороший тепловой контакт между образцами и стенками ячеек обеспечивается заполнением промежутка одной или двумя каплями жидкости с высокой теплопроводностью (октадекана и днэтилфталата). Ячейки с образцами, находятся на плите-осповании, к которой болтами из высокопрочного алюминиевого сплава через вакуумные уплотнения из индиевой проволоки крепится крышка. Камера с образцами крепится на небольшом холодильнике Джоуля — Томпсона (мощностью до 4 Вт при 23 К), в котором имеется подающая трубка из нержавеющей стали, контактирующая с плитой-основанием. С помощью медной струны эта трубка соединена с экраном — так осуществляется контакт этих деталей одной с другой и с резервуаром для жидкого азота.
[c.390]
Скорости резания при сверлении и эенкеровании отверстий в алюминиевых сплавах инструментом из быстрорежущей стали с применением охлаждения [c.380]
В-31 (ТУ 38-10189—70) — масло, содержащее серу, хлор и фосфор и органические соединения, применяемое при точеппи, сверлении и фрезеровании алюминиевых сплавов. [c.476]
У драйеров, изготовленных из алюминиевого сплава, в местах сверления отверстий под направляющие штыри рекомендуется укреплять стальные пластины. Все вертикальные или слабо наклонные плоскости драйера, [c.44]
Режимы резания при сверлении дуралюмина, = 40 -н 50 кГ1мм , силумина и литейных алюминиевых сплавов,
[c. 532]
Подача при сверлении, яенкеровании и развертывании стали, чугуна, медных и алюминиевых сплавов инструментами [c.433]
Смазывающе-охлаждающие жидкости. В гл. IV было рассмотрено влияние смазывающе-охлаждающих жидкостей на силу резания при токарной обработке. Положительное действие жидкости проявляется и при сверлении, так как процесс резания при сверлении сопровождается теми же явлениями, что и при точении. Поэтому применение соответствующих смазывающе-охлаждающих жидкостей и особенно поверхностно активных эмульсий приводит, по сравнению с обработкой всухую, к уменьшению осевой силы (силы подачи) и момента от сил сопротивления резанию на 10—30% при обработке сталей, на 10—1Ь% при обработке чугу-нов и на 30—40% при рбработке алюминиевых Сплавов. [c.239]
Средняя интенсивность износа отверстий кондукторных втулок при сверлении отверстий диаметром 10— 20 мм на длине 10 м составляет 1—2 мкм при обработке деталей из алюминиевых сплавов 3—5 мкм при обработке деталей из серого чугуна 4—6 мкм при обработке деталей из стали 40. Ориентировочно срок службы кондукторной втулки принимают равным 10 —l.SxlO сверлений, а при обработке грубых отверстий — 1,5X10 -f-4X 10 твердого сплава на порядок выше. Для уменьшения износа и увода инструмента зазор между поверхностью заготовки и нижним торцом втулки принимают равным (0,3—0,5)d при сверлении по чугуну, бронзе и другим хрупким материалам (0,5—l)i при сверлении по стали и другим вязким материалам 0,3d при зенкеровании d — диаметр направляющего отверстия кондукторной втулки) d[c.277]
Точность диаметральных размеров отверстий при окончательной обработке на АС соответствует 6. .. 8 квалитетам. При этом, в сравнимых условиях, точность обра тки деталей из алюминиевых сплавов на один квалитет выше, а из стали — на один квалитет ниже, чем при обработке чугунных деталей. Обработку отверстий выполняют по нескольким вариантам (табл. 2) При применении ружейных и эжекторных сверл (глубокое сверление) для отверстий диаметром 12. .. 30 мм обеспечивается точность 7. .. 9 квалитетов и необходимость в многопереходной обработке отпадает. В связи с незначительным уводом оси отверстия (5. .. 10 мкм на 100 мм длины) применять метод глубокого сверления наиболее целесообразно для обработки глубоких отверстий (/ > 5d).
[c.700]
Сверлильная машина П1019 предназначена для сверления отверстий диаметром до 9 мм в сталях средней твердости и алюминиевых сплавах. [c.144]
Сверлильная машина П7006 представляет собой силовую 1 оловку, предназначенную для сверления отверстий диаметром до 9 мм в сталях средней твердости и алюминиевых сплавах. Головки встраиваются в многошпиндельные [c.146]
В ремонте широко применяются сварные соединения. Хорошо поддаются сварке нержавеющие и конструкционные стали Х18Н9Т, ЗОХГСА и другие, алюминиевые сплавы АМгб и другие, магниевые сплавы МА2, МА8 и другие для титановых сплавов, которые плохо поддаются механической обработке (в частности, сверлению), сварка является одним из основных видов соединений.
[c.170]
Как сверлить мягкий металл в домашних условиях
Сверление металлов- действие, к которому домашний мастер вынужден прибегать весьма часто: сверление отверстий необходимо при изготовлении деталей к ударно-спусковому механизму, револьверных барабанов и так далее. Два необходимых инструмента для этого – электрическая и простая механическая дрели. Для дрели в свою очередь необходим целый арсенал сверл: от самых маленьких до крупных диаметром от 15 миллиметров.
При сверлении отверстий главную роль играет не мощность самой дрели, а острота сверла, поэтому не нужно сбрасывать со счетов механические дрели, которые мало уступают электрическим. Хорошо заточенное сверло гарантирует хорошую работу как ручной дрели, так и электродрелей от 400 Вт до 15кВт. Кроме того, механическая дрель идеальна для сверления отверстий небольшого и среднего диаметра до 10 мм, которые требуют точности и ответственности. Электрическая дрель используется при сверлении отверстий диаметром более 10 миллиметров.
Однако если в куске металла нужно просверлить, например, несколько сквозных отверстий, расположенных через определённые промежутки (как в револьверном барабане), необходим сверлильный станок, так как подобные работы должны выполняться с высочайшей точностью. Если вы не располагаете таким станком, можете обратиться в слесарный цех завода. При этом заготовка должна быть предварительно размечена. Это обойдётся вам в 3-5$ и примерно полчаса ожидания. При более сложной задаче, когда необходимо сверление сквозных отверстий в длинном (от 10 см) и толстом пруте или куске болта для получения «трубки» с определённым диаметром, обращаться нужно уже в токарный цех, так как такая работа предназначена для электрического токарного станка. Сверление отверстий такого рода тоже не очень дорогое – 2-3$.
В домашних условиях возможно сверление отверстий в мягких металлах, таких как алюминий и алюминиевые сплавы, медь, бронза, латунь, свинец, олово, цинк и мягкая сталь, в обиходе именуемая железом. Обычные свёрла годятся для немного подкалённой стали и некоторых сортов нержавейки. Для сверления отверстий в твёрдой калёной и высокоуглеродистой стали требуются спецсвёрла, изготовленные из особых сверхтвёрдых сплавов. Таки свёрла весьма дороги и малодоступны, кроме того, легко ломаются, поэтому при работе с ними нужно использовать малые обороты, избегать сильных нажимов, а рабочая поверхность должна быть смазана машинным маслом.
Услуги сверления алюминиевого профиля и нарезания резьбы в Алувин
Температура плавления алюминия составляет 660°С, что сказывается на его сверлении. К основным характеристикам этого материала, препятствующим сверлению, также относятся:
- высокая вязкость;
- пластичность;
- высокая теплопроводность.
Сверление алюминия требует профессиональной подготовки и современного оборудования. Неправильная техника работы может привести к набуханию краев детали или закусыванию сверла. Следует учитывать, что частота оборотов сверла должна быть в полтора раза меньше чем для остальных металлов.
Процесс обработки алюминиевых сплавов требует соблюдения определенных условий. Достичь оптимальных углов резки можно только за счет использования режущих инструментов с особой геометрией.
Оборудование для сверления
Сверлильные операции происходят на станке Jet GHD-50PF. Высокоточное сверление достигается путем надежного фиксирования головы. Частота оборотов головки сверла у конструкции достигает 3150 оборотов в минуту. Для обработки различных металлов имеется 8 скоростей.
Станок KST-340 Maschtec
Оборудование предназначено для выполнения сверлильных и резьбонарезных работ. Позволяет сверлить отверстия диаметром от 0,3 до 1,6 см. Девятискоростная ременная система передач позволяет выбрать одиночный цикл или режим повторяющейся операции. Можно регулировать глубину подачи, что исключает вероятность ошибок. Вращение шпинделя автоматизировано. Предусмотрен счетчик циклов для контроля операций. Система подачи охлаждающей жидкости защищает металл от перегрева и деформаций.
Стоимость сверления алюминиевого профиля
Цена заказа зависит от объемов и сроков поставки. Оставить заявку можно, заполнив форму на сайте или позвонив по номеру телефона: 8 (800) 500-49-71
Как правильно сверлить металл: свёрла и приспособления
Просверлить отверстие в металле — что может быть проще? Однако, ProfiDom.com.ua считает, что в этой слесарной операции довольно много тонкостей, касающихся правильного выбора инструмента, заточки и режимов резания.
В данном материале журналисты ProfiDom.com.ua рассказывают обо всех нюансах сверления металла.
Для проделывания отверстий в металле используют свёрла — механические стержни из сплава, который твёрже, чем обрабатываемая деталь. Свёрла по металлу изготавливают из быстрорежущей стали марок Р6М5, Р9, Р18 под общим обозначением HSS, либо из твёрдых сплавов: ВК, Т5К10, предназначенных для обработки закалённых и твёрдосплавных заготовок.
Сверло состоит из трёх элементов:
- Кромки врезаются в дно отверстия и снимают с него тонкую стружку.
- Спиральная нарезка выталкивает стружку из отверстия.
- Хвостовик предназначен для крепления сверла в патроне инструмента.
Конструкция спирального сверла по металлу
О режущих кромках стоит рассказать более подробно. Это два скоса на остром конце сверла, которые сходятся в вершине — самой выступающей точке передней части, образуя перемычку. Угол, под которым сходятся кромки, называют главным углом при вершине, его величина стандартизирована для различных материалов и режимов обработки:
- Твёрдая сталь и нержавейка: 135–140°
- Конструкционная сталь: 135°
- Алюминий, бронза, латунь: 115–120°
- Медь: 100°
- Чугун: 120° задний угол и 90° угол заточки кромки
Рекомендуемые углы заточки сверла по металлу
Каждая кромка, также, имеет собственный угол заточки порядка 20–35°, определяющий её остроту. Этот угол, называемый задним, обеспечивает касание сверла к металлу только по линии кромок, при этом за ними остаётся свободное пространство. Такая форма необходима для более лёгкого снятия и выброса стружки. У некоторых свёрл кромка заточена под более тупым углом, вплоть до прямого. Такие режущие кромки хорошо справляются с обработкой хрупких металлов, например, чугуна, латуни и бронзы.
Шаблон для проверки угла заточки свёрл
Спиральная часть включает несколько канавок для отвода стружки, на вершине которых расположены дополнительные кромки, плоскость которых параллельна оси сверла. Это так называемая ленточка, которая при погружении сверла подчищает стенки отверстия и способствует более качественной центровке.
Виды свёрл по металлу и техника их заточки
Выше, ProfiDOm.com.ua рассмотрел базовую разновидность свёрл. Чтобы понять, как формируются углы при заточке, нужно лишь немного знаний и практики. Точить свёрла лучше всего на шлифовальном станке с подручником, в худшем случае можно воспользоваться универсальной заточной машинкой. На УШМ («болгарке») свёрла точить нельзя: во-первых, это противоречит технике безопасности при работе с этим электроинструментом, а во-вторых, из-за большой скорости вращения металл сильно перегревается и отпускается, становясь мягким.
Подручник на наждаке для заточки свёрл
При заточке, сверло устанавливается на подручник так, чтобы его режущая часть была немного приподнята. Проворачивая сверло и сдвигая хвостовик влево, нужно добиться, чтобы режущая кромка расположилась строго горизонтально и параллельно торцу круга. Затачивать левую и правую кромку нужно поочерёдно, снимая тонкий слой металла и периодически охлаждая сверло в воде.
Заточка сверла на наждаке
Если просто зафиксировать сверло в требуемом положении и подвести его к наждаку, правильно обточить заднюю поверхность не удастся. Из-за того, что точильный камень круглый, затылочная часть кромки получается вогнутой. Это приводит к быстрому затуплению кромки и проблемам с отводом стружки. Чтобы избежать такого явления, переднюю часть сверла после касания о камень нужно немного приподымать, подавая вперёд и не снимая нажима. Так, формируется выпуклая задняя поверхность, которая намного лучше воспринимает нагрузку при резании.
Правильное движение при заточке сверла
Обточка кромок должна выполняться до выведения острых граней без сколов и заусенцев. При этом съём с обеих сторон должен быть равномерным, о чём можно судить по форме и положению остающейся перемычки, а также по длине самих кромок. Если перемычка будет смещена, сверло будет вращаться эксцентрично, что приведёт к увеличению диаметра отверстия. Этот эффект можно использовать, если в наличии нет сверла нужного диаметра.
Правильная и неправильная заточка сверла по металлу
Когда основные кромки выведены, выполняется стачивание перемычки. Для этого, сверло нужно поставить на подручник, под углом около 45° и прижать задней частью к ребру круга, не задевая режущую кромку. На перемычке образуются две небольшие насечки длиной до 1/10 диаметра сверла, которые выполняют роль заходных и центрирующих кромок.
Стачивание перемычки сверла
Более специфическая разновидность свёрл используется для сверления тонколистового металла. При изготовлении глубокого отверстия сверло сначала центрируется вершиной, а на выходе удерживается ленточками спиральной части. Однако в тонком металле вершина проходит насквозь до того, как ленточки упираются в края, из-за чего отверстие получается рваным, смещённым или овальным.
Заточка сверла для тонкого листового металла
В таких ситуациях, лучше использовать сверло перьевого типа, имеющее центрирующий носик. Изготовить такое можно из обычного сверла по металлу, переточив его определённым образом. Всё делается так же и с теми же углами, но при этом кромки не развёрнуты от вершины к краям, а сведены навстречу друг другу. Перьевое сверло нужно затачивать о край камня, оставляя перемычку нетронутой. Стачивание кромок выполняется до тех пор, пока перемычка не образует носик, выступающий над вершинами режущей части на 1–2 мм.
Ступенчатое сверло по металлу
Третий вид свёрл по металлу — конусные ступенчатые. У них есть несколько режущих кромок различного диаметра, что позволяет проделывать разные по размеру отверстия всего одним инструментом. Однако, несмотря на кажущуюся универсальность, найти действительно хорошее ступенчатое сверло довольно сложно, а его стоимость составит не менее $25. Другой минус — заточку таких свёрл можно выполнить только на специализированном станке.
Для сверления твёрдых сплавов и закалённой стали лучше использовать победитовые свёрла по бетону. Их заточка изначально рассчитана на дробящее действие, однако если вывести кромки под углом при вершине около 135° и заточить их под углом 20°, даже в очень твёрдой детали можно без усилий проделать аккуратное отверстие.
Как правильно сверлить металл
Вне зависимости от того, выполняется сверление дрелью или на станке, главное — правильно выбрать скорость вращения. В большинстве случаев оптимальная скорость находится в диапазоне 1800–2500 об/мин, однако на практике могут выбираться совершенно разные значения в зависимости от точности заточки и свойств материала.
Для эффективного и быстрого сверления не обойтись без умения правильно соотносить скорость вращения и усилие подачи. Легко почувствовать, как сверло врезается в металл, непрерывно выделяя стружку, и само начинает заглубляться в дно отверстия без существенного усилия. Обороты при этом, как правило, довольно низкие — порядка 300–500 об/мин.
Лучший показатель, что процесс сверления проходит технологически верно, а сверло заточено правильно — равномерный выход стружки с обеих спиральных канавок. Качество стружки — тоже значимый показатель:
- при сверлении стали выделяется цельная стружка в виде длинных спиралей;
- чугун, закалённая сталь и прочие хрупкие материалы образуют россыпь иголок;
- алюминий сверлится с образованием коротких завитков;
- при сверлении нержавейки могут получаться пыль и мелкие хлопья.
Правильная стружка при сверлении металла
Если сверло не врезается в металл, а трёт по нему с характерным писком, либо на выходе образуется нетипичный вид стружки, лучше остановиться и поправить заточку, иначе есть риск отпуска металла от перегрева или слома рабочей части.
Обязательно соблюдение техники безопасности! Сверлить следует без перчаток, защитив глаза слесарными очками.
Перед началом сверления, необходимо разметить все отверстия, которые нужно проделать в детали. Центр каждого отверстия следует наметить кернером. Сначала, сверлится небольшая лунка глубиной 2–3 мм, в неё вносится несколько капель машинного масла. Нужно научиться позволять сверлу самому выполнять свою работу: сначала сильно прижать инструмент, а когда произойдёт врезание кромок в металл — ослабить нажим и просто слегка придавливать, удерживая равномерную скорость вращения.
Вместо масла, могут использоваться и другие охлаждающие жидкости. Так, при сверлении нержавейки сверло нужно смачивать олеиновой кислотой. Её испарения вредны, поэтому работать необходимо в респираторе. Для охлаждения также хорошо подходит керосин и мыльная вода — брусок хозяйственного на литр.
Особое внимание требуется в момент выхода сверла при сверлении сквозных отверстий. Достаточно часто в таких случаях тонкое дно прорывается с образованием крупных заусенцев, которые попадают в спиральные канавки и затягивают сверло вперёд. На выходе из детали требуется ослабить нажим и немного увеличить обороты.
Сверлить отверстия большого диаметра лучше в несколько этапов, постепенно увеличивая диаметр сверла. Это не только снизит нагрузку на инструмент, но также продлит срок жизни заточки и обеспечит чистоту обработки. Отверстия диаметром свыше 13 мм лучше сверлить с помощью коронок.
Вместо масла рекомендуется использовать консистентную смазку, так будет меньше брызг. Коронке нужно периодически давать время остыть, а во время работы тщательно следить за тем, чтобы зубья погружались равномерно, иными словами — держать шпиндель строго перпендикулярно поверхности детали.
Завершающий этап сверления — снятие фасок с обеих сторон отверстия. Для этого можно использовать зенковку, а при её отсутствии — сверло вдвое большего диаметра, которое подаётся с минимальным усилием на больших оборотах. Для снятия заусенцев с больших отверстий разумно воспользоваться круглым напильником и наждачной бумагой.
Число оборотов при сверлении различных видов металла
Рекомендации по числу оборотов при сверлении различных видов металла в зависимости от диаметра сверла:
Вид металла | Ø 2 мм | Ø 5 мм | Ø 10 мм | Ø 15 мм | Ø 20 мм |
Скорость резания, м/мин. |
---|---|---|---|---|---|---|
Нелегированная сталь | 4780 | 1910 | 960 | 640 | 480 | 26-30 |
Листовая сталь | 4480 | 1780 | 890 | 590 | 440 | 26-28 |
Нелегированния инструментальная сталь | 4460 | 1780 | 890 | 590 | 440 | 26-28 |
Легированная инструментальная сталь | 3980 | 1600 | 800 | 530 | 400 | 12-14 |
Нержавеющая сталь | 2390 | 960 | 480 | 320 | 240 | 14-16 |
Пружинная сталь | 1450 | 570 | 290 | 190 | 140 | 8-10 |
Серый чугун | 4460 | 1780 | 890 | 590 | 450 | 25-30 |
Ковкий чугун | 4460 | 1780 | 890 | 590 | 450 | 25-30 |
Стальное литье | 3500 | 1400 | 700 | 460 | 350 | 20-24 |
Легированный алюминий | 7950 | 3180 | 590 | 1060 | 790 | 50-60 |
Легированная медь | 4780 | 1910 | 960 | 640 | 480 | 28-30 |
Бронза | 7960 | 3180 | 1500 | 1060 | 790 | 40-60 |
Латунь | 7960 | 3180 | 1500 | 1080 | 790 | 40-60 |
Рекомендуемое охлаждение при сверлении любого из материалов — сверлильная эмульсия, либо охлаждающее масло, кроме сверления чугуна и бронзы — где сверление необходимо производить всухую.

Сверла с покрытием TIN — для повышенных нагрузок на промышленном производстве и в мастерской. Титан-нитридное покрытие снижает трение при сверлении и тем самым повышает производительность.
Сверла кобальтовые HSS Co (Р6М5К5) — эксперт по высокоточной стали. Легирование кобальтом обеспечивает жаростойкость и в месте с тем высокую износостойкость. Идеальное решение для высокоточного сверления в корозионно — и жаростойких сталях с пределом прочности при растяжении до 1000 Н/мм2.
При сверлении по металлу в любом случае рекомендуется применять охлаждение. Но поскольку выполнение данной рекомендации не всегда представляется возможным, спиральные сверла сконструированы таким образом, что бы оптимальный результат достигался за счет быстрого отвода стружки.
Алюминий трудно сверлить, несмотря на то, что его легко повторить.
При сверлении, возможно, нет такой важной переменной, как материал заготовки. Он определяет геометрию сверла и основу, покрытие инструмента, нанесение СОЖ, а также скорость и подачу.
Хотя он известен своей относительной мягкостью и пластичностью, среди тех, кто регулярно сверлит алюминий, существует множество заблуждений.
«Многие считают алюминий одним из самых простых в обработке материалов, но он действительно представляет свои уникальные проблемы» — особенно при сверлении, — пояснил Эллиот Фрейзер, менеджер по продукции в Tungaloy America Inc., Арлингтон-Хайтс, Иллинойс. «Алюминий — это обычно мягкий, цветной, пластичный материал с низкой плотностью и, естественно, высокой устойчивостью к коррозии. Алюминий трудно сверлить, потому что его пластичность и мягкость заставляют материал постоянно и в течение длительного времени контактировать с передней поверхностью или режущими кромками сверла ».
Несмотря на то, что существует множество различных алюминиевых сплавов с уникальными характеристиками обрабатываемости, Фрейзер сказал, что наиболее широко просверливаемые алюминиевые сплавы — это 6061 и 7075, добавив, что в аэрокосмической и медицинской промышленности используются исключительно специальные сплавы.
Кромки, канавки и покрытия
Две основные проблемы при сверлении алюминия, объяснил Чад Линч, инженер по продажам Allied Machine & Engineering Corp. (AMEC), Довер, Огайо, — это стружкообразование и удаление стружки. «Если вы подойдете к нему без правильной геометрии инструмента, без надлежащего покрытия, без надлежащей охлаждающей жидкости, это может очень быстро превратиться в ситуацию, когда длинные волокнистые стружки наматываются вокруг инструмента».
Frazier дополнил список основных проблем при сверлении алюминиевых сплавов.Алюминий будет накапливаться и прилипать к режущей кромке, препятствуя образованию новой стружки из основного материала, что может привести к склеиванию стружки из-за засорения канавок. Это приводит к налипанию алюминия на сверло, что способствует еще большему прилипанию и уплотнению стружки.
Давление в направляющем канале gundrill может повлиять на качество поверхности, в зависимости от смазывающей способности охлаждающей жидкости, из-за присущей алюминию пластичности. Изображение предоставлено Sandvik Coromant.
«Чипы имеют тенденцию« растягиваться »из-за мягкости материала», — пояснил Линч. «Основной способ обойти это с помощью геометрии». По его словам, AMEC предлагает специальную алюминиевую геометрию для своей линейки продуктов TA, которая имеет высокий передний угол, который эффективно формирует стружку в более вязких материалах типа 6061. Более высокий передний угол создает больший сдвиг в резе и заставляет материал попадать в место удара на инструменте.
Основное различие между сверлением алюминия и более твердых материалов, — отметил Джейсон Хаут, глобальный специалист по продукции DHM (обработка глубоких отверстий) и специалист по применению Sandvik Coromant Co., Fair Lawn, штат Нью-Джерси, заключается в том, что точка сдвига алюминия достаточно низкая, чтобы его можно было разрезать режущей кромкой инструмента, а не выталкивать на
при обработке более твердых материалов. Это означает, что вертикальный большой угол сдвига с минимальным заострением кромки идеально подходит для сверления алюминия.
«Как правило, сверла с большим углом наклона спирали, полированными канавками и углом при вершине от 130 ° до 140 ° обеспечивают наилучший отвод стружки и режущие характеристики», — сказал Фрейзер. «Однако, поскольку алюминий очень мягкий, операции сверления с использованием вышеупомянутой геометрии, как правило, вызывают трудности с поддержанием надлежащего диаметра отверстия и чистоты поверхности боковой стенки.Если целью является поддержание размера отверстия, чистоты обработки и округлости отверстия, использование сверла с прямой канавкой и сквозной подачей СОЖ является преимуществом ».
Однако острая кромка — это слабая кромка, и многие марки алюминия содержат большое количество кремнезема — твердых стекловидных частиц в матрице алюминия, которые могут быстро сломать кромку инструмента. «С износом [из-за кремнезема] иногда можно бороться с помощью покрытий или путем перехода с карбида на суперабразивный инструментальный материал, такой как PCD», — сказал Хаут.
При применении твердосплавного инструмента важно, чтобы на нем не было покрытия на основе алюминия, потому что алюминий будет иметь тенденцию прилипать к поверхности заготовки, добавил он.Обычные покрытия, такие как Al2O3 или AlTiN, при контакте с алюминием под действием тепла и давления не только вступают в реакцию с деталью, но и обладают абразивными свойствами, которые могут способствовать BUE. Вместо этого Хаут рекомендует либо диборид титана, либо аморфную алмазную пленку.
Если они недоступны, твердый сплав без покрытия с полированной поверхностью обеспечивает более чем адекватные характеристики в большинстве случаев, — отметил Хаут. «Вам нужно отполировать флейты, чтобы материал мог выскользнуть, и если внутри флейты есть радиус, вам не нужны квадратные края или прямая стена, если только это не неизбежно [например, при ручном сверлении].”
Фрейзер рекомендует микрозернистый карбид с твердостью от 92 до 93 HRA для сплавов с низким содержанием кремния, но сказал, что некоторые алюминиевые сплавы, используемые для поковок или отливок, содержат более 11 процентов кремния и лучше всего подходят для сверл с наконечником из поликристаллического алмаза или алмазоподобного углерода. .
«Обычно покрытия не наносят на сверла в алюминиевых приложениях, так как большинство покрытий содержат алюминий», — сказал он. Поскольку большинство покрытий содержат алюминий в качестве одного из основных составляющих элементов, Фрейзер сказал, что некоторые производители начали использовать титан. -цирконий-нитридное покрытие для алюминия.«Но общепринятое мнение в этой области — использовать острое, отполированное и твердосплавное сверло без покрытия».
Использование сверла с прямой канавкой и сквозной подачей СОЖ является преимуществом, если целью является сохранение размера отверстия, чистоты обработки и круглости отверстия. Изображение предоставлено Тунгалой.
Одним из таких производителей является R.I. Carbide, шлифовальный и механический цех в Смитфилде, штат Род-Айленд, который предлагает покрытие ZETA ZrN в качестве альтернативы TiN, когда требуется дополнительная смазывающая способность.
«У нас был заказчик, которому нужно было просверлить 3 000 отверстий в алюминиевой пластине, и если они сломали сверло, обрабатывающее одно отверстие, вся деталь оказалась ломом», — сказал Джон Ломбарди, президент компании. «Они обратились к нам с проблемой, и мы сделали для этой работы сверло диаметром 0,156 дюйма с основанием ½ дюйма длиной около 3 дюймов». R.I. Carbide применил покрытие ZETA на сверле, и, запустив это сверло с высокой смазывающей способностью и пропускной способностью охлаждающей жидкости на высоких скоростях, заказчик смог успешно выполнить деталь за первый проход.
Охлаждение
Правильный отвод стружки требует правильного нанесения СОЖ, и сверление алюминия не является исключением. Клевание — это всегда вариант, но многие производители деталей стараются не извлекать сверло, когда это возможно, что означает, что полированные канавки и сверла со сквозной подачей охлаждающей жидкости — в порядке вещей.
«Особенно когда вы работаете на больших глубинах, проблема всегда заключается в потоке охлаждающей жидкости для удаления стружки, и это не является чем-то уникальным для алюминия», — отметил Линч из AMEC.«Мы предпочитаем не клевать, и я считаю, что если людям приходится клевать, то это, вероятно, потому, что они не формируют хорошую фишку. Фактически мы обнаружили, что тип смазочно-охлаждающей жидкости менее важен, чем концентрация — чем выше концентрация, тем лучше ваши результаты, вообще говоря ».
Tungaloy’s Frazier всегда рекомендует сквозную подачу СОЖ. «Более высокая скорость съема металла требует [подачи] большого количества охлаждающей жидкости, очень быстро, чтобы удалить стружку из зоны резания, а mrr обычно очень высока в алюминии.«Для подачи СОЖ потребуются циклы клевания, а минимальное количество смазки просто не имеет значения смещения при сверлении отверстий, особенно при сверлении глубоких отверстий», — сказал он. «Чем выше расход и выше давление, тем лучше».
Компания Hout от Sandvik Coromant обнаружила по крайней мере одну уникальную характеристику алюминия при глубоком сверлении. «При использовании самонаводящихся сверл, таких как gundrills, из-за пластичности алюминия давление в направляющем тракте может повлиять на отделку отверстия положительно или отрицательно, в зависимости от смазывающей способности охлаждающей жидкости», — сказал он. Чистая смазочно-охлаждающая жидкость обычно приводит к гладкой поверхности, в то время как синтетическая жидкость на водной основе может позволить некоторому количеству алюминия прилипать к направляющей, создавая грубую, «размазанную» поверхность.
Работа на высоких скоростях резания при одновременном сопротивлении искушению перекачать и нанесение охлаждающей жидкости с высокой смазывающей способностью и средней или низкой вязкостью — лучший способ обеспечить чистоту поверхности, сказал Хаут. «Вы хотите, чтобы масло двигалось быстро».
Быстрое время
Насколько высоки могут быть эти скорости резания? По словам Хаута, современное машинное оборудование еще не достигло точки, при которой может быть достигнут потолок наземной скорости для алюминия.
«Порог для алюминия составляет около 60 000 футов в минуту, что очень быстро», — сказал он. «Я видел, как алюминий работал со скоростью 24 000 футов в минуту с твердосплавной пластиной без покрытия, и это не повредило алюминий или пластину. Я говорю нашим клиентам, что в безопасной рабочей среде не бойтесь запускать его, потому что я видел, что более высокие скорости вращения алюминия увеличивают стойкость инструмента и улучшают качество обработки поверхности ».
Поскольку многие считают, что алюминий дешев и с ним легко работать, легко попасть в ловушку, полагая, что любая установка для обработки будет работать.Однако, по словам Фрейзера из Тунгалоя, некоторые из «самых простых» материалов в конечном итоге приносят самую низкую рентабельность в конце работы.
«Если больше магазинов смогут работать с« легкими »материалами, будет больше конкуренции за те же самые работы, что неизбежно приведет к снижению цен на резку алюминия», — сказал он. «В этом смысле важно максимально увеличить скорость и эффективность при работе с этими материалами, используя обновленные инструменты и передовые концепции, чтобы оставаться конкурентоспособными.”
Американский / английский
Хотя жители Северной Америки знают его как «алюминий», в большинстве англоязычных стран используется суффикс «-ium». В канадском Оксфордском словаре написано слово «алюминий», а в австралийском словаре Macquarie — «алюминий». Причина?
«В 1926 году Американское химическое общество официально решило использовать алюминий в своих публикациях; Американские словари обычно обозначают правописание «алюминий» как «главным образом британское», — поясняет Tungaloy America Inc.Эллиот Фрейзер. «Самая ранняя ссылка, приведенная в Оксфордском словаре английского языка для любого слова, использованного в качестве названия для этого элемента, — это алюминий, который британский химик и изобретатель Хамфри Дэви использовал в 1808 году для металла, который он пытался изолировать электролитически от минерального оксида алюминия.
«По сути, британская мысль« алюминий »казалась более классической и научной, поэтому они добавили дополнительную букву».
—E. Джонс Торн
Flowdrill, Baby, Flowdrill
Сверление включает образование стружки.Это просто данность — в конце концов, удаленный материал должен куда-то отправляться, верно? Но в то время как процесс, при котором не образуется стружка, может показаться некоторым не похожим на сверление, компания Flowdrill Inc. , специализирующаяся на термофрикционном сверлении, из Сент-Луиса предлагает альтернативу традиционному сверлению.
«Бурение с термическим трением — это процесс, который включает в себя выделение тепла за счет трения и давления», — сказал Митч Рэй, президент Flowdrill. «Мы создаем то, что мы называем втулкой, из тонкостенного материала, толщина стенок которого примерно в три-четыре раза превышает исходную.”
Эта втулка добавляет больше резьбы к отверстию и дает заказчику альтернативу существующим методам крепления, таким как приварные гайки или резьбовые вставки. После создания втулки метчик для форм может создавать резьбу или вставлять самонарезающий винт для завершения работы. В любом случае фишек не создается.
Геометрия Aludrill Flowdrill специально разработана для обработки алюминия. Изображение предоставлено Flowdrill.
Каждый диаметр долота инструмента имеет определенный набор параметров, объяснил Рэй. Например, размер резьбы-20 потребует, чтобы инструмент работал со скоростью 2400 об / мин из алюминия или мягкой стали, потребовал 1,5 л.с. и время цикла около 3 секунд на отверстие. Бита контактирует с материалом, и трение этого контакта нагревает материал, в то время как давление за битой проталкивает материал и образует втулку. Нет внешнего источника тепла, и сверла Flowdrill можно использовать на любом стандартном станке с ЧПУ без каких-либо специальных адаптеров.
Новейшая геометрия компании называется Aludrill, она разработана специально для алюминия.
Сверление с термическим трением создает отверстие и втулку — но без сколов — за счет тепла и давления. Изображение предоставлено Flowdrill.
«В отличие от других наших долот, оно не требует специальной смазки; он может работать со стандартной охлаждающей жидкостью для машин », — сказал Рэй. «Он также зенковывает фаску в материале, что делает его единственным из наших битов, который создает чип».
На стандартном сверле Flowdrill отшлифован многоугольник, состоящий из четырех вершин и четырех впадин, каждая из которых называется «выступами», которые создают трение и нагревают.Aludrill избегает этой геометрии в пользу большего контакта с металлом, что создает достаточное трение в более мягком алюминии для выработки достаточного количества тепла.
«У нас есть несколько крупных приложений для Aludrill, — сказал Рэй. — В прошлом году он использовался на новом пикапе Ford F150, проделав отверстия в передних фартуках этих грузовиков. Они используют саморез, чтобы прикрепить различные провода к передней части грузовиков ».
—E. Джонс Торн
Авторы
Allied Machine & Engineering Corp.
(330) 343-4283
www.alliedmachine.com
Flowdrill Inc.
(314) 968-1134
www.flowdrill.com
R.I. Carbide
(401) 231-1020
www.ricarbide.com
Sandvik Coromant Co.
(800) SANDVIK
www. sandvik.coromant.com/us
Tungaloy America Inc.
(888) 554-8394
www.tungaloyamerica.com
Исследования сверления подготовленного алюминиево-металлического матричного композита из частиц каменной пыли мокрого шлифовального станка
Спрос на высокоэффективные и экономичные композитные материалы привлекает внимание в современном конкурентном мире.В этой работе была сделана попытка получить недорогой армированный композит с металлической алюминиевой матрицей путем усиления 10% и 20% весовых фракций частиц каменной пыли (WSD), являющихся промышленными отходами, образующимися во время операции обработки камня в мокром измельчителе. промышленность. Поскольку сверление является одной из основных операций механической обработки, выполняемой в промышленности, подготовленные композитные материалы подвергаются исследованиям сверления с использованием твердосплавных сверл, карбида с покрытием TiN и сверл из быстрорежущей стали диаметром 5 мм в сухих условиях.Основная проблема при обработке композитов — это чрезмерный износ инструмента. Износ инструмента — очень важная и сложная задача для инженеров-технологов, поскольку он отрицательно сказывается на качестве продукции и увеличивает стоимость производства. Следовательно, необходимо определить факторы, которые имеют наиболее значительное влияние на износ инструмента. В этой работе план экспериментов на основе Тагучи и дисперсионный анализ использовались для определения оптимальных параметров резания и анализа их влияния на силу тяги, крутящий момент и износ инструмента.Анализ многовариантной линейной регрессии также использовался для определения корреляций между факторами и откликом, а именно осевым усилием, крутящим моментом и износом инструмента. Наконец, был проведен подтверждающий тест для проверки метода оптимизации Тагучи. По результатам экспериментов скорость подачи была определена как доминирующий фактор, влияющий на силу тяги, а скорость шпинделя была определена как значительный фактор, влияющий на крутящий момент. Было обнаружено, что сила тяги, крутящий момент и износ инструмента увеличиваются с увеличением содержания арматуры независимо от сверла, использованного для исследования.
1 Введение
Композиты с алюминиевой металлической матрицей (AMMC) широко используются во многих промышленных приложениях, таких как оборона, аэрокосмическая промышленность, автомобилестроение и спорт, благодаря множеству замечательных свойств, таких как высокая прочность, высокая жесткость, высокая теплопроводность, очень хорошая износостойкость и коррозионная стойкость. Основной проблемой при обработке AMMC является экстремальный износ инструмента, вызванный абразивным действием армированных частиц, что приводит к высокой стоимости обработки [1], [2], [3].Обычно процесс сверления выполняется на последнем этапе перед сборкой. Сообщается, что почти треть процесса удаления металла, выполняемого в промышленности, — это операции бурения [4], [5], [6], [7], [8].
Износ инструмента — очень важная и сложная задача для инженеров-технологов, поскольку износ сверла влияет на качество отверстия, увеличивает шероховатость поверхности и стоимость производства, а также снижает стойкость инструмента [9], [10], [11]. Износ инструмента зависит от типа материала инструмента, скорости резания, скорости подачи, выбранной смазки и рабочего материала [11], [12].Таким образом, чтобы повысить производительность и снизить стоимость обработки, необходимо понять причину снижения стойкости инструмента [13]. Износ инструмента можно измерить двумя методами: прямым и косвенным [14], [15]. Косвенный метод оценивает износ инструмента путем измерения сигналов силы резания, акустической эмиссии, вибрации и тока [12], [14], тогда как прямой метод использует оптические методы для оценки износа инструмента [14], [16]. Между этими двумя методами исследователи предпочитают использовать косвенный метод для измерения износа инструмента, потому что косвенный метод позволяет непрерывно контролировать состояние инструмента для оценки износа инструмента; это невозможно с прямым методом, потому что поверхность износа не видна во время операции резания [16], [17].
В этой работе AMMC был получен путем усиления 10% и 20% весовых фракций частиц мокрой измельчительной каменной пыли (WSD), побочного продукта промышленных отходов, образующихся во время обработки карьерного камня. Самым важным сырьем, используемым для производства мокрого шлифовального станка, является необработанный камень. Частицы пыли, образующиеся в процессе обработки карьерного камня, сохраняют химический состав и характеристики породы. Как правило, эти частицы каменной пыли используются либо в качестве грунтовки, либо при производстве различных строительных добавок и штукатурок.
В данной работе сплав Al6063 выбран в качестве основного матричного сплава для получения AMMC, поскольку он широко используется в промышленности из-за его желаемых свойств, таких как коррозионная стойкость, хорошая экструдируемость, свариваемость и высококачественная обработка поверхности. Сплав Al6063 используется в различных приложениях, таких как секции теплоотвода, гибкие сборочные системы, элементы специального оборудования, перила, полы для грузовиков и трейлеров, радиаторы и другие теплообменники.
План экспериментов и дисперсионный анализ Тагучи (ANOVA) были применены для анализа эффективности параметров, направленных на минимизацию осевой силы, крутящего момента и износа инструмента.Анализ многовариантной линейной регрессии также использовался для определения корреляции между факторами и откликом (сила тяги, крутящий момент и износ по задней поверхности инструмента).
2 Материалы и методы
СплавAl6063, который используется в качестве основного матричного материала при изготовлении композита, имеет следующий химический состав (%): Si 0,303, Fe 0,071, Cu 0,0050, Mn 0,0759, Mg 0,529, Cr 0,0037, Ni 0,014, Zn 0,025, Ti 0,0151, Ca 0,0146 и Al 98,94. Композит был приготовлен путем усиления 10% и 20% частиц WSD с размером зерна менее 45 мкм, как показано на Рисунке 1.Отчет об испытаниях частиц WSD EDAX, показанный на рисунке 2A, показывает присутствие Si, Ca, Fe, Al, Mg и Na в качестве основных элементов. В таблице 1 показаны физические свойства частиц WSD. Плотность частиц WSD оказалась равной 2,2 г / см 3 . На Рисунке 2B кристаллическая форма WSD оказалась сферической и неправильной по форме. Частицы WSD имеют серый цвет, а их удельный вес составляет 2,4 г / см 3 .
Рисунок 1:
частиц WSD указано стрелками.
Рисунок 2:
(A) Отчет об испытаниях EDAX частиц WSD, (B) SEM частицы WSD и (C) удельная поверхность частицы WSD.
Таблица 1:Физические свойства частиц WSD.
Цвет | серый |
Плотность | 2,2 г / см 3 |
Площадь | 0.30–0,60 м 3 / г |
Удельный вес | 2,4 г / см 3 |
Форма кристалла | Сферический / неправильный |
Композиты с 10% и 20% массовыми долями частиц WSD были приготовлены с помощью двухэтапного процесса литья с перемешиванием. Первоначально частицы WSD были предварительно нагреты до 250 ° C, чтобы удалить влагу и улучшить их смачиваемость основным матричным сплавом.Сплав Al6063 загружали в тигель и нагревали до температуры 750 ° C для расплавления сплава. Затем жидкому сплаву давали остыть до полутвердого состояния при температуре около 600 ° C. Предварительно нагретые частицы WSD вместе с 0,1 мас.% Магния добавляли в расплав и перемешивали со скоростью 400 об / мин в течение 15 мин. Температуру повышали до 850 ° C и проводили второе перемешивание в течение 15 минут. В завершение приготовленные образцы композита заливали в подготовленные песчаные формы.
2.1 Микроструктура и механические свойства
На рис. 2B и C показано изображение, полученное с помощью сканирующей электронной микроскопии (SEM), и удельная поверхность частиц WSD. Микроструктура приготовленных композитов показана на рис. 3A и B при увеличении в 100 раз. Результат SEM показывает, что распределение армированных частиц достаточно равномерное. CaCO 3 , присутствующий в частицах WSD, реагирует с расплавом алюминия с образованием различных твердых фаз, таких как CaO, Al 2 O 3 и Al 4 C 3 .
Рисунок 3:
(A) SEM образца 1 порошка AL6063 / 10% WSD и (B) SEM образца 2 порошка AL6063 / 20% WSD.
На рис. 4A и B показан протокол испытаний EDAX подготовленных образцов. Спектр как 10%, так и 20% частиц WSD показывает присутствие элементов Al, O и C, что указывает на присутствие частиц Al 2 O 3 и Al 4 C 3 частиц в алюминии. матрица.Из рисунков 3A и B видно, что частицы Al 2 O 3 показаны в виде небольших сферических белых точек, а частицы Al 4 C 3 показаны в виде темно-коричневых кристаллов, достаточно однородных, распределенных в основной матрице. .
Рисунок 4:
(A) протокол испытаний EDAX образца 1 и (B) протокол испытаний EDAX образца 2.
Подготовленные образцы были подвергнуты испытаниям на твердость и растяжение для изучения их механических свойств.Согласно результатам испытаний на твердость, средняя твердость образцов, полученных путем армирования 10% и 20% WSD, составила 62 и 74 BHN соответственно. Было установлено, что твердость полученных композитов выше, чем твердость основной матрицы — сплава Al6063. Увеличение твердости полученного композита можно объяснить присутствием твердых армирующих элементов, таких как частицы Al 2 O 3 в частицах WSD. Таблица 2 показывает результаты механических свойств, таких как предел текучести, предел прочности и относительное удлинение (%) подготовленных образцов.Из таблицы 2 видно, что предел текучести и предел прочности полученных композитов выше, чем у базовой матрицы. Предел текучести и предел прочности увеличиваются с увеличением содержания арматуры. Наибольшее значение прочности на разрыв было получено для композита, полученного путем армирования 20% частиц WSD.
Таблица 2:Механические свойства полученных композитов и сплава Al6063 (состояние отпуска Т1).
SI № | Материал | Значение твердости (BHN) | Предел текучести (МПа) | Предел прочности при растяжении (МПа) | Относительное удлинение (%) |
---|---|---|---|---|---|
1 | Сплав Al6063 | 43 | 67 | 131 | 13,5 |
2 | Al6063 + 10% Prm | 62 | 114 | 153 | 7.83 |
3 | Al6063 + 20% Prm | 74 | 132 | 166 | 5,80 |
Увеличение содержания арматуры с 10% до 20% увеличивает твердость и предел прочности композитов, но снижает их пластичность, что совпадает с предыдущими выводами [18], [19]. Это может быть связано с плохим сцеплением и агломерацией армированных частиц в алюминиевой матрице.Напротив, уменьшение содержания армирования <10% приводит к плохому равномерному распределению армирующих частиц. Таким образом, в данной работе для приготовления композита использовалось 10% и 20% арматуры.
2.2 Экспериментальная процедура и оптимизация с использованием техники Тагучи
В данной работе испытание на сверление проводилось в условиях сухого резания на обычном вертикальном сверлильном станке. Образцы для механической обработки были изготовлены в виде прямоугольных пластин размером 100 × 55 × 15 мм.Затем прямоугольную пластину прочно закрепили на приспособлении, прикрепленном к динамометру, который был установлен на столе. На рис. 5А показана экспериментальная установка, используемая для преобразования усилия сверления, приложенного к обрабатываемой детали, в сигналы силы тяги и крутящего момента. Этот метод является косвенным методом измерения сигналов силы тяги и крутящего момента. Испытание на бурение проводилось в соответствии с планом экспериментов, и такие параметры, как сила тяги и крутящий момент, измерялись с использованием многокомпонентного динамометра Kistler типа 9257B.
Рисунок 5:
(A) Экспериментальная установка для измерения силы тяги и крутящего момента, (B) SEM изношенного твердосплавного сверла при скорости шпинделя = 1260 об / мин и подаче = 0,03 мм / об, (C) поперечный разрез просверленного отверстия образца 2, и (D) SEM-изображение просверленного отверстия с использованием твердосплавного сверла при скорости шпинделя = 1260 об / мин и подаче = 0,03 мм / об.
В данной работе износ инструмента измерялся с помощью инструментального микроскопа в лабораторных условиях.В предварительном испытании мы наблюдали увеличение сил резания, когда износ по задней поверхности достиг 0,3 мм для всех сверл; следовательно, новый инструмент был заменен, когда износ по задней поверхности достиг 0,3 мм. СЭМ-изображение изношенного твердосплавного сверла, используемого для процесса сверления, вид в разрезе просверленного отверстия образца 2 и СЭМ-изображение просверленного отверстия показаны на рис. 5B – D, соответственно.
В промышленности выбор оптимальных параметров резания на основе справочной информации может снизить производительность и увеличить стоимость производства из-за неоптимального использования возможностей обработки.Наилучшее использование потенциала процесса сверления требует сочетания правильного набора параметров обработки [20]. Следовательно, существует потребность в методике оптимизации для решения проблемы неправильного выбора параметров процесса.
Поскольку традиционный метод экспериментального проектирования сложен и требует много времени, в этой работе экспериментальный план, основанный на Тагучи, был применен для определения оптимальных параметров резания для минимальной силы тяги, крутящего момента и износа инструмента.Экспериментальный план с методом Тагучи использует специальную конструкцию ортогональной решетки, которая очень проста и эффективна по сравнению с традиционным методом экспериментального дизайна. Метод Тагучи — полезный инструмент для изучения всех параметров процесса для определения экспериментального плана с небольшим количеством экспериментов [3], [20], [21], [22], [23]. Главный недостаток метода Тагучи заключается в том, что он не может судить и определять влияние отдельного параметра на весь процесс.Полученные результаты не могут указывать на уровень влияния или наибольшее влияние того или иного параметра на значение характеристики производительности.
Однако процентный вклад отдельных параметров в отклик, который необходимо изучить, можно определить с помощью дисперсионного анализа [11], [24]. На основе конструкции смешанного уровня ортогонального массива L18 (2 1 × 3 3 ) Тагучи, были выбраны управляющие факторы, такие как процентное содержание армирующих материалов (Prm), тип сверла, скорость шпинделя и скорость подачи, и показаны их уровни. в таблице 3.Используемые уровни и пределы были определены из предварительных экспериментов [25]. Отклики, которые необходимо изучить, — это сила тяги, крутящий момент и износ по задней поверхности инструмента.
Таблица 3:Факторы контроля и их уровни.
Символ | Факторы контроля | Уровень 1 | Уровень 2 | Уровень 3 |
---|---|---|---|---|
A | Prm | 10% | 20% | Нет |
B | Тип сверла | HSS | Карбид | Твердый сплав с покрытием TiN |
С | Скорость шпинделя (об / мин) | 850 | 1260 | 1860 |
D | Подача (мм / об) | 0.03 | 0,05 | 0,07 |
Ортогональный массив был выбран с учетом следующих условий: количество степеней свободы для ортогонального массива должно быть больше или равно количеству степеней свободы, необходимых для изучения основных эффектов и эффектов взаимодействия [26]. В этой работе необходимо изучить один фактор на двух уровнях и три фактора на трех уровнях, а также взаимодействие между типом сверла Prm *, скоростью шпинделя Prm * и скоростью подачи Prm *.Требуемая степень свободы — 11. Поскольку степени свободы для ортогонального массива больше, чем количество степеней свободы, необходимое для изучения основных эффектов и эффектов взаимодействия, был выбран ортогональный массив L18. В Таблице 4 показаны экспериментальные результаты измеренных значений осевой силы, крутящего момента и износа инструмента.
Таблица 4:Экспериментальные результаты с использованием ортогональной матрицы L18 (2 1 × 3 3 ) вместе с отношением сигнал / шум.
№ след. | Факторы контроля | Ответ | ||||||||
---|---|---|---|---|---|---|---|---|---|---|
Prm | Тип сверла | Скорость шпинделя (об / мин) | Подача (мм / об) | Усилие тяги (Н) | Отношение сигнал / шум (дБ) | Крутящий момент (Нм) | Отношение сигнал / шум (дБ) | Износ инструмента (мм) | Отношение сигнал / шум (дБ) | |
(А) | (В) | (К) | (Г) | |||||||
1 | 1 | 1 | 1 | 1 | 156.6 | −43,8958 | 33,97 | −30,6219 | 0,121 | 18.3443 |
2 | 1 | 1 | 2 | 2 | 201,32 | −46,0777 | 45,12 | −33,0874 | 0,195 | 14,1993 |
3 | 1 | 1 | 3 | 3 | 293.50 | −49,3522 | 66,28 | −36,4276 | 0,310 | 10,1728 |
4 | 1 | 2 | 1 | 1 | 145,20 | −43,2393 | 38,57 | −31,7250 | 0,112 | 19.0156 |
5 | 1 | 2 | 2 | 2 | 162.12 | −44,1967 | 49,95 | −33,9707 | 0,151 | 16.4205 |
6 | 1 | 2 | 3 | 3 | 233,70 | −47,3732 | 79,86 | −38,0466 | 0,287 | 10,8424 |
7 | 1 | 3 | 1 | 2 | 207.90 | −46,3571 | 26,58 | −28,4911 | 0,148 | 16,5948 |
8 | 1 | 3 | 2 | 3 | 265,48 | −48,4806 | 38,65 | −31,7430 | 0,208 | 13,6387 |
9 | 1 | 3 | 3 | 1 | 178.95 | -45,0546 | 62,56 | −35,9259 | 0,328 | 9,6825 |
10 | 2 | 1 | 1 | 3 | 348,15 | −50,8353 | 64,51 | −36,1925 | 0,133 | 17,5230 |
11 | 2 | 1 | 2 | 1 | 218.40 | −46,7851 | 78,95 | −37,9470 | 0,231 | 12,7278 |
12 | 2 | 1 | 3 | 2 | 245,00 | −47,7833 | 89,95 | −39.0800 | 0,322 | 9,8429 |
13 | 2 | 2 | 1 | 2 | 225.65 | −47,0687 | 39,87 | −32,0129 | 0,120 | 18,4164 |
14 | 2 | 2 | 2 | 3 | 340,30 | −50,6372 | 52,19 | −34,3517 | 0,196 | 14,1549 |
15 | 2 | 2 | 3 | 1 | 179.00 | -45,0571 | 85,95 | −38,6849 | 0,302 | 10,3999 |
16 | 2 | 3 | 1 | 3 | 385,20 | −51,7137 | 29,82 | −29,4902 | 0,165 | 15,6503 |
17 | 2 | 3 | 2 | 1 | 235.00 | −47,4214 | 54,65 | −34,7518 | 0,228 | 12,8413 |
18 | 2 | 3 | 3 | 2 | 297,20 | −49,4610 | 68,95 | −36,7707 | 0,362 | 8,8258 |
2.3 Анализ отношения сигнал / шум (S / N)
Результаты экспериментов были проанализированы с помощью коммерческого программного обеспечения MINITAB 16. Влияние факторов контроля на реакцию было проанализировано, и ранг задействованных факторов, которые поддерживают соотношение сигнал / шум, приведен в таблицах 5–7.
Таблица 5:Таблица отклика для серийного номера на силу тяги.
Уровень | Prm | Тип сверла | Скорость шпинделя | Подача |
---|---|---|---|---|
1 | −46.00 | −47,45 | −47,19 a | −45,24 a |
2 | −48,53 | −46,26 a | −47,27 | −46,82 |
3 | Нет | −48,08 | −47,35 | −49,73 |
Дельта | 2.53 | 1,82 | 0,16 | 4,49 |
Рейтинг | 2 | 3 | 4 | 1 |
Таблица отклика для серийного номера на крутящий момент.
Уровень | Prm | Тип сверла | Скорость шпинделя | Подача |
---|---|---|---|---|
1 | −33.34 a | −35,56 | −31,42 а | −34,94 |
2 | −35,48 | −34,80 | −34,31 | −33,90 a |
3 | Нет | −32,86 а | −37,49 | −34,38 |
Дельта | 2.14 | 2,70 | 6,07 | 1,04 |
Рейтинг | 3 | 2 | 1 | 4 |
Таблица реакции для серийного номера на износ инструмента.
Уровень | Prm | Тип сверла | Скорость шпинделя | Подача |
---|---|---|---|---|
1 | 14.323 a | 13,802 | 17,591 a | 13,835 |
2 | 13,376 | 14,875 a | 13,997 | 14.050 a |
3 | Нет | 12,872 | 9,961 | 13,664 |
Дельта | 0.948 | 2,003 | 7,630 | 0,386 |
Рейтинг | 3 | 2 | 1 | 4 |
Тагучи предлагает соотношение сигнал / шум для измерения качественных характеристик [27]. Тагучи предложил три категории рабочих характеристик при анализе отношения сигнал / шум: чем меньше, тем лучше, номинальное — лучше, и чем больше, тем лучше [7, 28].Поскольку самые низкие значения осевого усилия, крутящего момента и износа инструмента считаются оптимальными для высокого качества продукции, для расчета отношения сигнал / шум была выбрана категория «чем меньше, тем лучше».
Оптимальные параметры обработки для откликов, а именно силы тяги, крутящего момента при сверлении и износа инструмента, были найдены на уровне, где каждый фактор имеет самое высокое отношение сигнал / шум [20], [24], [25], [26] ], [27], [28], [29]. Из Таблицы 5 видно, что сила тяги самая низкая на первом уровне Prm (A1), втором уровне типа сверла (B2), первом уровне скорости шпинделя (C1) и первом уровне скорости подачи (D1).График основных эффектов отношения сигнал / шум для осевой силы, показанный на рисунке 6A, также является самым высоким на этих уровнях параметров, что приводит к наименьшей осевой силе. Следовательно, комбинация A1B2C1D1 (A1 = 10% Prm, B2 = твердосплавное сверло, C1 = 850 об / мин, D1 = 0,03 мм / об) считается оптимальной для минимальной осевой силы в исследуемом диапазоне параметров, а также имеет самое высокое отношение сигнал / шум. Из порядка расположения в таблице 5 ясно, что наибольшее влияние на силу тяги оказывает скорость подачи, за которой следуют Prm, скорость шпинделя и тип сверла.
Рисунок 6:
(A) График основных эффектов для отношения сигнал / шум для осевой силы, (B) график основных эффектов для отношения сигнал / шум для крутящего момента и (C) график основных эффектов для отношения сигнал / шум для износа инструмента.
Поскольку для крутящего момента была выбрана меньшая, тем лучше категория, из таблицы 6 был найден оптимальный уровень для минимального крутящего момента, когда каждый фактор имеет наивысшее отношение сигнал / шум как A1B3C1D2 (A1 = 10% от Prm, B3 = сверло из быстрорежущей стали, C1 = 850 об / мин, D2 = 0.05 мм / об). Основные эффекты отношения сигнал / шум для крутящего момента, показанного на рисунке 6B, также являются самыми высокими на этих уровнях параметров, что приводит к самому низкому крутящему моменту. Порядок ранжирования крутящего момента показывает, что скорость шпинделя имеет наибольшее влияние на крутящий момент, за которым следуют тип сверла, Prm и скорость подачи. Точно так же из таблицы 7 и рисунка 6C оптимальные уровни износа инструмента могут быть определены как A1B2C1D2 (A1 = 10% Prm, B2 = твердосплавное сверло с покрытием TiN, C1 = 850 об / мин, D2 = 0,05 мм / об).
2.4 Метод ANOVA
В этой работе ANOVA использовался для определения оптимальной комбинации параметров процесса путем исследования относительной значимости факторов с точки зрения их процентного вклада в ответ [7], [11].Помимо значимости контрольных факторов, также была изучена значимость взаимодействия между контрольными факторами на ответ. Взаимодействие между управляющими факторами было между типом сверла и Prm (B × A), скоростью шпинделя и Prm (C × A), а также скоростью подачи и Prm (D × A).
Выполненный план эксперимента оценен с доверительной вероятностью 95%. В таблице 8 представлены результаты ANOVA для силы тяги. Значение R 2 , полученное для осевой силы, составляет 99,2%, что является желательным [30].Из Таблицы 8 видно, что значение p для Prm, типа сверла и скорости подачи составляет <0,05, что указывает на то, что факторы являются статистически значимыми и имеют значительное влияние на реакцию (силу осевого усилия) [30], [31 ], тогда как значение p> 0,05 для скорости шпинделя и для взаимодействия между факторами, что указывает на то, что скорость шпинделя и взаимодействие между факторами не имеют какого-либо значительного влияния на силу тяги. Помимо p-значения, F-тест Фишера также может использоваться для определения того, какие параметры обработки имеют существенное влияние на отклик.Согласно F-критерию Фишера, если рассчитанное значение F-отношения больше табличного F-значения, то эффект считается значительным [2], [32]. В этой работе табличное значение F для параметров бурения составляет (F0,05, 1, 4 = 7,708) и (F0,05, 2, 4 = 6,944) для взаимодействия факторов. Из таблицы дисперсионного анализа 8 для осевой силы ясно, что значения F-теста для скорости подачи, типа сверла и Prm больше, чем значение F-таблицы, что указывает на то, что они статистически значимы и имеют значительное влияние на осевое усилие. силы, тогда как значения F-теста для скорости шпинделя и взаимодействия факторов меньше, чем значения F-таблицы, что указывает на их статистическую незначимость.Поскольку статистическая значимость скорости шпинделя и взаимодействия факторов минимальна, они имеют незначительное влияние на силу тяги и им можно пренебречь [33]. Из экспериментальных результатов ясно, что скорость подачи имеет большее влияние на силу тяги, что совпадает с результатами предыдущих исследований, касающихся бурения ГМК [5], [6], [23], [32], [34] ]. Порядок процентного вклада (%) из таблицы 8 дисперсионного анализа отражает относительную важность каждого фактора в управлении откликом, а именно, силы тяги.Среди четырех выбранных параметров бурения скорость подачи имеет наибольший вклад в силу осевого усилия (59,77%), за ней следуют Prm (27,58%) и тип сверла (9,84%). Взаимодействие между скоростью шпинделя Prm * составляет 1,08%, тип сверла Prm * — 0,58%, подача Prm * — 0,23%, и, наконец, скорость шпинделя оказывает влияние на силу тяги 0,075%.
Таблица 8:ANOVA для отношения сигнал / шум для силы тяги.
Источник | DF | Seq SS | Adj SS | Adjj MS | F | п. | Процентный взнос |
---|---|---|---|---|---|---|---|
Prm | 1 | 28.717 | 28,7167 | 28,7167 | 136,75 | 0,000 | 27,58 |
Тип сверла | 2 | 10,251 | 10,2510 | 5,1255 | 24,41 | 0,006 | 9,84 |
Скорость шпинделя | 2 | 0,079 | 0.2514 | 0,1257 | 0,60 | 0,592 | 0,075 |
Скорость подачи | 2 | 62,234 | 42,5209 | 21.2605 | 101,24 | 0,000 | 59,77 |
Prm * тип сверла | 2 | 0,610 | 0.6097 | 0.3049 | 1,45 | 0,336 | 0,58 |
Prm * скорость шпинделя | 2 | 1,132 | 1,1324 | 0,5662 | 2,70 | 0,181 | 1,08 |
Prm * подача | 2 | 0,244 | 0,2439 | 0,1220 | 0.58 | 0.601 | 0,23 |
Остаточная ошибка | 4 | 0,840 | 0,8400 | 0,2100 | 0,81 | ||
Итого | 17 | 104.107 | 100 |
В таблице 9 представлены результаты ANOVA для крутящего момента.Значение R 2 , равное 96,9%, было получено из таблицы ANOVA, что является желательным [35]. Из Таблицы 9 видно, что Prm, тип сверла и скорость шпинделя имеют p-значения <0,05, что указывает на то, что они оказывают значительное влияние на отклик (крутящий момент) [30], [31], тогда как p-значение равно > 0,05 для скорости подачи и взаимодействия между факторами, которые указывают на то, что скорость подачи и взаимодействие между факторами не имеют какого-либо значительного влияния на крутящий момент. Из таблицы 9 ANOVA ясно, что рассчитанное значение F-отношения для скорости подачи и взаимодействий факторов меньше, чем значения в F-таблице, которые показывают, что скорость подачи и взаимодействия факторов незначительны и не имеют какого-либо значительного влияния. по крутящему моменту.Из таблицы 9 видно, что скорость шпинделя является доминирующим параметром для крутящего момента и дает 62,55% влияния, за которым следуют тип сверла (13,13%), Prm (11,64%) и скорость подачи (1,84%). Взаимодействие между сверлом типа Prm * составляет 6,88%, скорость шпинделя Prm * составляет 0,63%, а скорость подачи Prm * влияет на крутящий момент 0,18%.
Таблица 9:ANOVA для отношений сигнал / шум для крутящего момента.
Источник | DF | Seq SS | Adj SS | Adjj MS | F | п. | Процентный взнос |
---|---|---|---|---|---|---|---|
Prm | 1 | 20.571 | 20,5709 | 20,5709 | 14,85 | 0,018 | 11,64 |
Тип сверла | 2 | 23.209 | 23.2089 | 11.6045 | 8,38 | 0,037 | 13,13 |
Скорость шпинделя | 2 | 110,513 | 71.1095 | 35,5548 | 25,67 | 0,005 | 62,55 |
Скорость подачи | 2 | 3,258 | 2,8798 | 1.4399 | 1,04 | 0,433 | 1,84 |
Prm * тип сверла | 2 | 12,165 | 12,1646 | 6.0823 | 4,39 | 0,098 | 6,88 |
Prm * скорость шпинделя | 2 | 1,082 | 1.0818 | 0,5409 | 0,39 | 0,700 | 0,63 |
Prm * подача | 2 | 0,320 | 0,3202 | 0,1601 | 0.12 | 0,894 | 0,18 |
Остаточная ошибка | 4 | 5,540 | 5,5399 | 1,3850 | 3,13 | ||
Итого | 17 | 176.657 | 100 |
В таблице 10 представлены результаты ANOVA для износа инструмента.Как правило, износ инструмента взаимосвязан со многими факторами, помимо параметров, взятых для этого исследования. Некоторые параметры, такие как время контакта между природой инструмента и заготовкой и абразивное воздействие армированных частиц, также могут способствовать износу инструмента [11]. Из ANOVA для износа инструмента было получено значение R 2 , равное 99,1%, что является желательным [30]. Скорость подачи и взаимодействие между параметрами имеют p-значения> 0,05, что указывает на то, что скорость подачи и взаимодействие между параметрами не имеют существенного влияния на износ инструмента.В дополнение к p-значению, значения F-теста для скорости подачи и взаимодействия факторов меньше, чем значение F-таблицы, что указывает на то, что они статистически незначимы и имеют незначительное влияние на износ инструмента. Согласно таблице 10 дисперсионного анализа, очевидно, что скорость шпинделя имеет большее влияние на износ инструмента (89,98%), за которым следуют тип сверла (6,20%), Prm (2,08%) и скорость подачи (0,23%). Взаимодействие между скоростью шпинделя Prm * составляет 0,32%, скорость подачи Prm * — 0,23%, а тип сверла Prm * — 0.03% влияние на износ инструмента.
Таблица 10:ANOVA для отношения сигнал / шум для износа инструмента.
Источник | DF | Seq SS | Adj SS | Adjj MS | F | п. | Процентный взнос |
---|---|---|---|---|---|---|---|
Prm | 1 | 4,041 | 4,041 | 4.0410 | 9,01 | 0,040 | 2,08 |
Тип сверла | 2 | 12,053 | 12,053 | 6,0265 | 13,44 | 0,017 | 6,20 |
Скорость шпинделя | 2 | 174,832 | 115.005 | 57.5025 | 128.21 | 0,000 | 89,98 |
Скорость подачи | 2 | 0,449 | 0,304 | 0,1522 | 0,34 | 0,731 | 0,23 |
Prm * тип сверла | 2 | 0,054 | 0,054 | 0,0270 | 0,06 | 0.942 | 0,03 |
Prm * скорость шпинделя | 2 | 0,616 | 0,616 | 0,3078 | 0,69 | 0,554 | 0,32 |
Prm * подача | 2 | 0,443 | 0,443 | 0,2215 | 0,49 | 0,643 | 0.23 |
Остаточная ошибка | 4 | 1,794 | 1,794 | 0,4485 | 0,92 | ||
Итого | 17 | 194.282 | 100 |
2.5 Анализ многомерной линейной регрессии
Регрессионный анализ — это статистический инструмент, используемый для нахождения взаимосвязи между переменными, выбранными для исследования [36].В этой работе многомерный линейный регрессионный анализ использовался для определения корреляций между факторами управления (Prm, тип сверла, скорость подачи и скорость шпинделя), силой тяги, крутящим моментом и износом инструмента. Стандартный коммерческий статистический пакет программного обеспечения MINITAB 16 был использован для вывода уравнения регрессии вида:
(1) Т час р ты s т ж о р c е знак равно — 1.4 + 69,9 А + 8,90 B — 3,45 C + 6 2 . 8 D р 2 знак равно 0.854.
(2) Т о р q ты е знак равно 18,8 + 13,7 А — 8,13 B + 18,4 C — 1 9 .5 D р 2 знак равно 0,867.
(3) Т о о л ш е а р знак равно — 0.0181 + 0,0221 А + 0,0106 B + 0,0927 C — 0 . 0 0 1 9 2 D
В анализе множественной линейной регрессии R 2 — это значение коэффициента корреляции, которое должно быть между 0.8 и 1 [5], [37]. В этой работе статистические результаты R 2 показывают, что модель соответствует требованиям, и объясняют 85,4%, 86,7% и 92,75% изменчивости силы тяги, крутящего момента и износа инструмента, соответственно. На рис. 7A – B показан график нормальной вероятности невязок для осевой силы, крутящего момента и износа инструмента во время регрессионного анализа. В этой работе невязки обычно лежат на прямой линии, подразумевая, что ошибки нормально распределены [2], [38], [39].
Рисунок 7:
(A) График нормальной вероятности для осевой силы, (B) график нормальной вероятности для крутящего момента и (C) график нормальной вероятности для износа инструмента.
2.6 Подтверждающий эксперимент
Подтверждающий эксперимент настоятельно рекомендуется Тагучи, и это важный шаг для проверки экспериментальных результатов [7], [20]. В этой работе подтверждающий эксперимент был проведен после определения оптимального сочетания факторов, влияющих на силу резания и износ инструмента.
Эксперимент повторяли три раза, чтобы получить среднее значение, и результаты сравнивали с предсказанными значениями.Результаты подтверждающего испытания представлены в Таблице 11. Расчетная сила тяги оказалась равной 145,65 Н, а экспериментальное значение — 145,20 Н. Видно хорошее соответствие между расчетными и экспериментальными значениями, а ошибка была в пределах 0,31%. Расчетный крутящий момент оказался равным 24,56 Нм, а экспериментальное значение крутящего момента — 25,35 Нм. Было обнаружено удовлетворительное совпадение между прогнозируемыми и измеренными значениями крутящего момента, и ошибка была в пределах 3,11%. Прогнозируемый износ по задней поверхности инструмента оказался равным 0.114 мм, а экспериментальное значение — 0,115 мм. Видно хорошее соответствие между предсказанными и экспериментальными значениями, а ошибка была в пределах 0,86%.
Таблица 11:Результаты подтверждающего эксперимента.
Тест | Оптимальные уровни | Экспериментальное значение | Среднее экспериментальное значение | Прогнозируемое значение из уравнения регрессии | % Ошибка | ||
---|---|---|---|---|---|---|---|
След 1 | След 2 | Trail 3 | |||||
Усилие тяги (Н) | A (1), B (2), C (1), D (1) | 145.15 | 144,85 | 145,69 | 145,20 | 145,65 | 0,31 |
Крутящий момент (Нм) | A (1), B (3), C (1), D (1) | 25,10 | 24,32 | 26,64 | 25,35 | 24,56 | 3,11 |
Износ инструмента (мм) | A (1), B (2), C (1), D (2) | 0.110 | 0,116 | 0,120 | 0,115 | 0,114 | 0,86 |
3 Результаты и обсуждение
3.1 Анализ сигналов силы резания
На рисунках 8A – F и 9A – F показаны измеренные значения типичной осевой силы и крутящего момента образцов 1 и 2 с использованием сверла из быстрорежущей стали, карбида и сверла из карбида TiN, соответственно. Процесс бурения состоит из трех этапов, которые обозначены как I, II и III на рис. 8A – F и 9A – F.Во время этапа I процесса сверления лезвие долота и режущая кромка сверла выполняют операцию сверления и полностью входят в рабочую деталь. Также на этапе I сила тяги и крутящий момент резко возрастают. На этапе II канавки сверла также начинают резать, и кончик сверла достигает нижней части заготовки. На этапе II сила тяги и крутящий момент достигают максимального значения. Наконец, на этапе III процесс сверления завершается, и сила тяги и крутящий момент постепенно уменьшаются, поскольку долото и режущие кромки постепенно отделяются от обрабатываемой детали.
Рисунок 8:
Типичные значения силы тяги, измеренные во время предварительного испытания: (A) типичная сила тяги, измеренная при скорости вращения шпинделя = 850 об / мин, подаче = 0,03 мм / оборот, заготовка (усиление 10%), с использованием сверла из быстрорежущей стали; (B) типичная сила тяги, измеренная при скорости вращения шпинделя = 850 об / мин, подаче = 0,07 мм / об, обрабатываемая деталь (усиление 20%), с использованием сверла из быстрорежущей стали; (C) типичная сила тяги, измеренная при скорости вращения шпинделя = 850 об / мин, подаче = 0,03 мм / об, обрабатываемая деталь (усиление 10%), с использованием твердосплавного сверла; (D) типичная сила тяги, измеренная при частоте вращения шпинделя = 1260 об / мин, подаче = 0.03 мм / об, деталь (армирование 20%), используя твердосплавное сверло; (E) типичное осевое усилие, измеренное при скорости вращения шпинделя = 850 об / мин, подаче = 0,03 мм / об, обрабатываемая деталь (10% -ное усиление) с использованием твердосплавного сверла с покрытием TiN; и (F) типичное осевое усилие, измеренное при скорости вращения шпинделя = 1260 об / мин, подаче = 0,07 мм / об, обрабатываемая деталь (усиление 20%) с использованием твердосплавного сверла с покрытием TiN.
Рисунок 9:
Типичные значения крутящего момента, измеренные во время предварительного испытания: (A) типичный крутящий момент, измеренный при частоте вращения шпинделя = 850 об / мин, подаче = 0.05 мм / об, заготовка (10% армирования) сверлом из быстрорежущей стали; (B) типичный крутящий момент, измеренный при скорости вращения шпинделя = 1860 об / мин, подаче = 0,05 мм / оборот, заготовка (усиление 20%) с использованием сверла из быстрорежущей стали; (C) типичный крутящий момент, измеренный при частоте вращения шпинделя = 850 об / мин, подаче = 0,03 мм / об, обрабатываемая деталь (усиление 10%), с использованием твердосплавного сверла; (D) типичный крутящий момент, измеренный при частоте вращения шпинделя = 850 об / мин, подаче = 0,07 мм / об, обрабатываемая деталь (усиление 20%) с использованием твердосплавного сверла; (E) типичный крутящий момент, измеренный при частоте вращения шпинделя = 850 об / мин, подаче = 0.03 мм / об, заготовка (усиление 10%) с использованием твердосплавного сверла с покрытием TiN; и (F) типичный крутящий момент, измеренный при частоте вращения шпинделя = 1260 об / мин, подаче = 0,07 мм / об, обрабатываемой детали (усиление 20%) с использованием твердосплавного сверла с покрытием TiN.
3.2 Анализ сигналов силы тяги
При анализе сигналов силы тяги сверла из быстрорежущей стали становится ясно, что на этапе I процесса бурения сила тяги достигает 175 Н для образца 1, как показано на рисунке 8A, тогда как для образца 2 сила тяги резко увеличивается до 320 N, как показано на рисунке 8B.На этапе II сила тяги постепенно увеличивается и достигает максимального значения 207,9 Н для образца 1 и 385,2 Н для образца 2. Процесс сверления завершается на этапе III, и сверло полностью отсоединяется от обрабатываемой детали.
В случае твердосплавного сверла на этапе I сила тяги составляла около 125 Н для образца 1, как показано на Рисунке 8C, и 170 Н для образца 2, как показано на Рисунке 8D. На этапе II было обнаружено, что сила тяги постепенно увеличивается и достигает 156,6 Н для образцов 1 и 218.4 Н для образца 2. По мере завершения процесса бурения на этапе III в течение этого периода сила тяги постепенно уменьшается и падает до нуля.
В случае твердосплавного сверла с покрытием TiN на этапе I сила тяги составляла около 123 Н для образца 1, как показано на рисунке 8E, и 220 Н для образца 2, как показано на рисунке 8F. На этапе II сила тяги постепенно увеличивается и достигает 145,2 Н для образца 1, а сила тяги резко увеличивается и достигает 340,30 Н для образца 2.Сила тяги для образца 2 резко возрастает из-за увеличения износа инструмента, вызванного выкрашиванием режущей кромки при более высоких оборотах шпинделя и скорости подачи. По результатам экспериментов было отмечено, что твердосплавное сверло с покрытием из TiN дает минимальную осевую силу по сравнению с другими сверлами, взятыми для исследования.
Из экспериментальных результатов видно, что сила тяги резко возрастает с увеличением скорости подачи. Это может быть связано с тем, что более высокая скорость подачи создает большую стружку, а инструмент передает большее усилие резания [40].Из таблицы 8 дисперсионного анализа ясно, что скорость подачи является наиболее значительным фактором, влияющим на силу тяги. Кроме того, для сверл из быстрорежущей стали создавалась более высокая осевая сила, чем для сверл из карбида и карбида с покрытием, особенно с более высокой фракцией частиц. Это может быть связано с низкой твердостью и механизмом износа сверла из быстрорежущей стали [33].
Также можно увидеть, что сила тяги имеет тенденцию резко увеличиваться с увеличением содержания арматуры, особенно для образца 2, независимо от используемых сверл, что совпадает с выводами [6].Увеличение силы тяги, особенно для образца 2, может быть связано с увеличением твердости композита, увеличением трения между заготовкой и инструментом и усилением износа инструмента [33].
Кроме того, из таблицы 8 дисперсионного анализа также ясно, что скорость шпинделя не оказывает какого-либо значительного влияния на силу тяги. Увеличение частоты вращения шпинделя с 850 до 1260 об / мин не оказывает существенного влияния на снижение силы тяги, что совпадает с выводами [6].Хотя ранее проводились противоречивые исследования [32], в которых утверждается, что сила тяги уменьшается с увеличением скорости шпинделя, этот эффект незначителен, потому что, помимо скорости шпинделя, время контакта между инструментом и заготовкой, температура и абразивный износ Эффекты армированных частиц играют жизненно важную роль в износе инструмента. Комбинация более низкой скорости подачи и более низкой скорости шпинделя увеличивает время контакта между инструментом и заготовкой, что, в свою очередь, увеличивает износ инструмента.Дальнейшее сверление изношенным инструментом резко увеличивает силу тяги [11].
Таким образом, из экспериментальных результатов ясно, что более высокая скорость подачи и комбинированный эффект более низкой скорости подачи с более низкой скоростью шпинделя имеют большое влияние на резкое увеличение осевой силы.
3.3 Анализ сигналов крутящего момента
При анализе сигналов крутящего момента сверла из быстрорежущей стали можно увидеть, что на этапе I процесса сверления крутящий момент достигает 20 Н для образца 1, как показано на рисунке 9A, и 37 Н для образца 2, как показано на рисунке 9B.На этапе II процесса сверления крутящий момент резко увеличивается и достигает максимального значения 26,58 Н для образца 1 и 61,32 Н для образца 2. На этапе III процесс сверления завершается, и сверло отсоединяется от обрабатываемой детали.
В случае твердосплавного сверла на этапе I значение крутящего момента достигает 29 Н для образца 1, как показано на Рисунке 9C, и 58 Н для образца 2, как показано на Рисунке 9D. На II этапе процесса сверления крутящий момент резко увеличивается и достигает максимального значения 33.97 Н для образца 1 и 64,51 Н для образца 2, тогда как для твердосплавного сверла с покрытием TiN на этапе I значение крутящего момента резко увеличивается и достигает 39 Н для образца 1, как показано на рисунке 9E, и 37 Н для образца 2, как показано на Рисунок 9F. На этапе II процесса сверления крутящий момент постепенно увеличивается и достигает максимального значения 38,57 Н для образца 1 и 52,19 Н для образца 2.
Сила крутящего момента, создаваемая твердосплавным сверлом с покрытием TiN, меньше, чем у твердосплавного сверла. Это может быть связано с наличием защитного покрытия, которое действует как смазка и снижает трение и температуру в зоне резания [4].
Из таблицы 9 дисперсионного анализа ясно, что скорость шпинделя является наиболее значимым фактором, влияющим на крутящий момент. Сверление на более низкой скорости шпинделя предпочтительнее более высокой скорости вращения шпинделя. Однако существует противоречивое исследование [35], противоречащее нашей работе, утверждающей, что при более низкой скорости шпинделя существует относительно больший крутящий момент, чем при более высокой скорости шпинделя. Однако сверление с низкой скоростью шпинделя не рекомендуется для всех типов материалов. Скорость шпинделя должна варьироваться в зависимости от рабочего материала, типа усиления, типа материала инструмента и матрицы.
Есть еще одна работа [8], в которой утверждается, что износ инструмента значительно меньше при более низкой скорости резания. Согласно их работе, развитие нестабильной нароста кромки (BUE), вызванное длительным временем контакта между заготовкой и инструментом, защищает режущую кромку от дальнейшего износа. Дальнейшее сверление изношенным инструментом резко увеличит силы резания.
Из экспериментальных результатов также видно, что значение крутящего момента значительно увеличивается с увеличением скорости подачи.Сила крутящего момента, создаваемая сверлом из быстрорежущей стали, сравнительно меньше, чем у сверла из карбида или карбида TiN с покрытием. Это может быть связано с тем, что сверло с меньшим углом при вершине оказывает на обрабатываемую деталь очень меньшую крутящую силу. Угол при вершине сверла из быстрорежущей стали, используемого в этой работе, составляет 118 ° и 130 ° как для твердосплавного сверла, так и для твердосплавного сверла с покрытием. Согласно предыдущим исследованиям [7], [41], режущий момент увеличивается с увеличением угла при вершине, что коррелирует с нашими выводами.
4 Выводы
В данной работе было проведено испытание сверления с использованием сверл из быстрорежущей стали, карбида и карбида TiN с покрытием в сухих условиях на подготовленном AMMC.AMMC был приготовлен путем усиления сплава Al6063 10% и 20% массой частиц WSD, промышленных отходов, образующихся во время операции по обогащению горного камня.
Сила резания и износ инструмента регистрировались при различных режимах резания для различных комбинаций параметров сверления.
Из исследования можно сделать следующие выводы:
Увеличение содержания арматуры с 10% до 20% увеличивает твердость и предел прочности композитов, но снижает их пластичность.
Скорость подачи была определена как наиболее значимый фактор, влияющий на силу тяги, за которой следовали Prm, тип сверла и скорость шпинделя.
На крутящий момент и износ инструмента сильно влияла скорость шпинделя, за которой следуют тип сверла, Prm и скорость подачи соответственно.
Судя по результатам экспериментов, композит с более высоким содержанием армирования имеет более высокую осевую силу, крутящий момент и износ инструмента независимо от сверл, использованных для исследования.
При сверлении сверлом из быстрорежущей стали зафиксировано максимальное значение осевой силы по сравнению со сверлами из карбида и карбида TiN, особенно при сверлении композитов с более высокой фракцией частиц.
Сверление с очень низкой скоростью шпинделя и скоростью подачи резко увеличивает силу тяги и крутящий момент.
Сверло с меньшим углом при вершине предпочтительнее, чем сверло с большим углом, потому что сверло из быстрорежущей стали с углом при вершине 118 ° дает меньший крутящий момент по сравнению со сверлами из карбида и карбида с покрытием 130 °.
Подтверждающие тесты показали хорошее приближение при сравнении предсказанных и экспериментальных результатов. Таким образом, план экспериментов Тагучи и дисперсионный анализ можно эффективно использовать для определения оптимального уровня управляющих факторов для минимизации осевой силы, крутящего момента и износа инструмента.
Ссылки
[1] Даш К., Сукумаран С., Рэй BC. Sci. Англ. Compos. Матер. 2016, 3, 1–20.Искать в Google Scholar
[2] Palanikumar K, Muniaraj A. Measurement 2014, 53, 240–250.10.1016 / j.measurement.2014.03.027 Искать в Google Scholar
[3] Basavarajappa S, Chandramohan G, Davim JP. J. Mater. Процесс. Technol. 2008, 196, 332–338.10.1016 / j.jmatprotec.2007.05.043 Поиск в Google Scholar
[4] Davim JP. J. Mater. Процесс. Technol. 2003, 132, 250–254.10.1016 / S0924-0136 (02) 00935-4 Поиск в Google Scholar
[5] Davim JP, Baptista AM. Proc. Inst. Мех. Англ. Pt. E J. Process. Мех. Англ. 2001, 215, 177–183.10.1243 / 0954408011530334 Искать в Google Scholar
[6] Рамулу М., Рао П.Н., Као Х. J. Mater. Процесс. Technol. 2002, 124, 244–254.10.1016 / S0924-0136 (02) 00176-0 Искать в Google Scholar
[7] Taskesen A, Kütükde K. Mater. Technol. 2013, 47, 169–176. Искать в Google Scholar
[8] Francis Xavier L, Suresh P, Balaragavendheran R, Yeshwanth Kumar P, Deepak S. ARPN J. Eng. Прил. Sci. 2016, 11, 1277–1280. Искать в Google Scholar
[9] Chang SSF, Bone GM. Внутр. J. Mach. Инструменты Manuf. 2009, 49, 1070–1076.10.1016 / j.ijmachtools.2009.07.011 Поиск в Google Scholar
[10] Rajmohan T., Palanikumar K, Davim JP. J. Mater. Sci. Technol. 2012, 28, 761–768.10.1016 / S1005-0302 (12) 60127-3 Искать в Google Scholar
[11] Таскесен А., Кутукде К. Пер. Цветные металлы. Soc. Китай 2013, 23, 2524–2536.10.1016 / S1003-6326 (13) 62764-8 Поиск в Google Scholar
[12] Davim JP, Baptista AM. J. Mater. Процесс. Technol. 2000, 103, 417–423.10.1016 / S0924-0136 (00) 00495-7 Поиск в Google Scholar
[13] Парк К.Х., Бил А., Ким Д., Квон П., Лантрип Дж. Wear 2011, 271 , 2826–2835.10.1016 / j.wear.2011.05.038 Искать в Google Scholar
[14] Jantunen E. Int. J. Mach. Инструменты. Manuf. 2002, 42, 997–1010.10.1016 / S0890-6955 (02) 00040-8 Поиск в Google Scholar
[15] Ghani JA, Rizal M, Nuawi MZ, Ghazali, Haron CHC. Wear 2011, 271, 2619–2624.10.1016 / j.wear.2011.01.038 Поиск в Google Scholar
[16] Dimla Sr DE, Lister PM. Внутр. J. Mach. Инструменты. Manuf. 2000, 40, 739–768.10.1016 / S0890-6955 (99) 00084-X Искать в Google Scholar
[17] Таскесен А., Кутукде К. Пер. Цветные металлы. Soc. Китай 2015, 25, 271–283.10.1016 / S1003-6326 (15) 63602-0 Поиск в Google Scholar
[18] Нагарал М., Ауради В., Равишанкар М.К. Внутр. J. Res. Англ. Technol. 2013, 1, 193–198.Искать в Google Scholar
[19] Anilkumar HC, Hebbar HS, Ravishankar KS. Внутр. J. Mech. Матер. Англ. 2011, 6, 41–45. Искать в Google Scholar
[20] Tosun G. Int. J. Adv. Manuf. Technol. 2011, 55, 477–485.10.1007 / s00170-010-3103-7 Поиск в Google Scholar
[21] Haq AN, Marimuthu P, Jeyapaul R. Int. J. Adv. Manuf. Technol. 2008, 37, 250–255.10.1007 / s00170-007-0981-4 Искать в Google Scholar
[22] Ай М., Алтунпак Ю. J. Eng. Fundam. 2015, 2, 42–50.10.17530 / jef.15.17.2.2 Поиск в Google Scholar
[23] Раджмохан Т., Паланикумар К., Катирвел М. Пер. Цветные металлы. Soc. Китай 2012, 22, 1286–1297.10.1016 / S1003-6326 (11) 61317-4 Поиск в Google Scholar
[24] Удая Пракаш Дж., Мурти ТВ. Внутр. J. Appl. Англ. Res. 2015, 10, 526–529. Искать в Google Scholar
[25] Deng CS, Chin JH. Внутр. J. Adv. Manuf. Technol. 2005, 25, 420–426.10.1007 / s00170-003-1825-5 Поиск в Google Scholar
[26] Энтони Дж., Прис Д. Понимание, управление и реализация качества. Фреймворки и кейсы . Рутледж, Лондон, 2002. Поиск в Google Scholar
[27] Гайтонде В.Н., Карник С.Р., Давим Дж.П. J. Mater. Процесс. Technol. 2008, 196, 73–78.10.1016 / j.jmatprotec.2007.05.003 Поиск в Google Scholar
[28] Navanth A, Karthikeya Sharma T. Int. J. Eng. Sci. Emerg. Technol. 2013, 6, 65–75.Искать в Google Scholar
[29] Palanikumar K. Measurement 2011, 44, 2138–2148.10.1016 / j.measurement.2011.07.023 Искать в Google Scholar
[30] Vinayagamoorthy R, Rajeswari N, Karuppiah B. Jourdan J. Mech. Ind. Eng. 2014, 8, 385–392. Искать в Google Scholar
[31] Campos Rubio JC, Silva LJD, Leite WDO, Panzera TH, Davim JP. Composites: Part B 2013, 55, 338–344.10.1016 / j.compositesb.2013.06.042 Искать в Google Scholar
[32] Munia Raj A. Внутр. J. Eng. Technol. 2014, 6, 2426–2434. Искать в Google Scholar
[33] Taskesen A, Kutukde K. Measurement 2013, 42, 321–330. Искать в Google Scholar
[34] Алтунпак Ю., Ай М., Аслан С., Межд. J. Adv. Manuf. Technol. 2012, 60, 513–517.10.1007 / s00170-011-3644-4 Поиск в Google Scholar
[35] Munia Raj A, Manoharan N. Indian J. Sci. Technol. 2014, 7, 87–94. Искать в Google Scholar
[36] Mayyas A, Qasaimeh A, Alzoubi K, Lu S, Hayajneh MT, Hassan AM. Дж. Майнер. Матер. Charact. Англ. 2012, 11, 1039–1049. Искать в Google Scholar
[37] Ficici F, Koksal MS, Karacadag C. Int. J. Sci. Adv. Technol. 2012, 23, 114–121. Искать в Google Scholar
[38] Vankanti VK, Ganta V. J. Mater. Res. Technol. 2014, 3, 35–41.10.1016 / j.jmrt.2013.10.007 Поиск в Google Scholar
[39] Киратсис П., Билалис Н., Антониадис А. Comput.-Aided Des. 2011, 43, 1879–1890.10.1016 / j.cad.2011.06.002 Искать в Google Scholar
[40] Чандрашекхар С., Осман М.М., Санкар Т.С. Внутр. J. Prod. Res. 1984, 22, 697–721.10.1080 / 00207548408942489 Искать в Google Scholar
[41] Jayabal S, Natarajan U. Indian J. Eng. Матер. Sci. 2010, 17, 463–470. Искать в Google Scholar
Поступила: 2016-2-9
Принято: 2016-9-27
Опубликовано в сети: 17.11.2016
Напечатано в печати: 2018-4-25
© 2018 Walter de Gruyter GmbH, Берлин / Бостон
Эта статья распространяется в соответствии с условиями некоммерческой лицензии Creative Commons Attribution, которая разрешает неограниченное некоммерческое использование, распространение и воспроизведение на любом носителе при условии правильного цитирования оригинальной работы.
Обзор: производительность сверления и качество отверстий в алюминиевых сплавах для аэрокосмической промышленности
Мухаммад Аамир получил степень магистра в области машиностроения с отличием в Университете информационных технологий и новых наук CECOS, Пешавар, Пакистан, в 2016 году. получение степени доктора философии в Школе инженерии Университета Эдит Коуэн, Австралия. В настоящее время его научные интересы включают в себя обработку аэрокосмических материалов, разработку электронных материалов и методы оптимизации.Г-н Аамир получил Золотую медаль в области машиностроения в 2016 году, премию Fazaia за выдающиеся достижения в программе социального обеспечения в области образования, Пакистан в 2017 году, и стипендию на высшую степень в области исследований Университета Эдит Коуэн, Австралия в 2018 году. Гиасин получил степень доктора философии в Университете Шеффилда, Великобритания, в 2017 году. Он является преподавателем инженерного дизайна в Школе машиностроения и проектирования в Портсмутском университете. Он присоединился к школе в 2019 году с преподавательскими и исследовательскими обязанностями.Его основная исследовательская база связана с обработкой аэрокосмических материалов с использованием экспериментальных и численных методов.
Д-р Маджид Толуэи-Рад является профессиональным инженером-технологом в Школе инженерии Университета Эдит Коуэн. Он работал инженером в промышленности, прежде чем продолжить учебу в аспирантуре и сделать академическую карьеру. После получения докторской степени в 1997 году он постоянно участвовал в обучении в высших учебных заведениях и руководил исследованиями в уважаемых университетах Ближнего Востока, Северной Америки и Австралазии.Его исследовательские интересы включают материалы и производство, автоматизацию и робототехнику.
Доктор Ана получила докторскую степень в Университете Эдит Коуэн (ECU), Австралия в 2017 году. Ее докторская диссертация была посвящена реконфигурируемым производственным системам. В январе 2019 года она начала работать преподавателем и научным сотрудником в области венчурного капитала в инженерной школе ECU, и ее исследования сосредоточены на разработке высокоэффективных теплообменников. В настоящее время она руководит тремя студентами высших учебных заведений (HDR), и ее исследовательские интересы включают передовые и аддитивные производственные системы, моделирование принятия решений, оптимизацию топологии и процессы оптимизации.
© 2020 Издано Elsevier BV
Лучшие сверла по металлу (Руководство покупателя)
Фото: depositphotos.com
Центры домашнего благоустройства часто выделяют целый проход для сверл, которые бывают самых разных типов и размеров для сверления отверстий в различных материалах. Многие сверла могут пробивать материал более чем одного типа, но не все сверла могут просверливать металл, не нагреваясь и не ломаясь пополам. Этикетки на сверлах указывают тип материала, для которого они подходят, поэтому достаточно легко найти сверла, предназначенные для сверления металла.В зависимости от типа металла, который вы сверляете, одни сверла подходят для этой задачи лучше, чем другие.
Если вы работаете над проектом, в котором требуется просверлить металл, прочтите, чтобы узнать о факторах, которые следует учитывать, прежде чем отправиться в магазин за лучшими сверлами по металлу. Следующие наборы сверл превосходят конкурентов и помогут вам проделать отверстия во множестве металлов.
- ЛУЧШИЙ В ЦЕЛОМ: Hymnorq Набор сверл 13PC от 1/16 дюйма до 1/4 дюйма
- НАИЛУЧШИЙ УДАР ДЛЯ БАКА: Титановые сверла amoolo 1/8 ″ (10 шт.) БИТЫ: TACKLIFE, 5 шт., Набор титановых ступенчатых сверл
- НАИЛУЧШЕЕ ДЛЯ ЗАКАЛЕННОЙ СТАЛИ: Drill Hulk 1/16-дюймовые спиральные сверла из кобальтовой стали
- НАИЛУЧШИЕ ДЛЯ ЛЕГОМЕРНОЙ СТАЛИ: Bosch 21-сегментное сверло по металлу с черной оксидом Набор бит
Фото: Amazon.com
Большинство сверл подходят как для стандартных сетевых, так и для аккумуляторных дрелей. Хотя все эти маленькие кусочки металла выглядят очень похоже, каждый тип сверла специализируется на проделывании отверстий в определенных материалах, включая дерево, пластик и металл, но не будет работать с другими материалами. Биты, которые просверливают металл, также классифицируются по типам металла, который они прокалывают. Например, некоторые долота могут просверливать черные металлы, такие как чугун, а другие — цветные металлы, такие как медь и олово.
Материал сверлаБольшинство сверл изготавливается из быстрорежущей стали, кобальта или карбида. Как вы увидите ниже, материал долота может влиять на его эффективность при сверлении различных металлов.
- Быстрорежущая сталь (HHS): Это универсальное сверло, которое можно использовать для сверления как черных и цветных металлов, так и углеродистой стали.
- Карбид: Сверла по металлу из твердого сплава подходят для сверления цветных металлов, но не черных металлов.
- Кобальт: Этот тип сверла по металлу хорошо подходит для сверления черных металлов, но не так хорош для сверления цветных металлов.
Сверла по металлу обычно покрыты титаном или оксидом черного. Это покрытие снижает трение, что предохраняет сверло от нагрева и, в конечном итоге, поломки. Поскольку покрытие снижает трение, оно также увеличивает скорость сверления.
Конструкция хвостовикаХвостовик — это конец сверла без сверления, который входит в оправку сверла или «патрон».Это конец того, что вы «подключаете» к сверлу. Размер хвостовика сверла, который вы выбираете (обычно ¼ дюйма, ⅜ дюйма или ½ дюйма), должен соответствовать размеру патрона сверла.
Хвостовики одних конструкций лучше подходят для сверления металла, чем другие. Большинство хвостовиков для этого типа сверл не вращаются или имеют шестигранник.
- Хвостовик без прокрутки: Этот тип сверла имеет рифленый хвостовик, который предотвращает проскальзывание сверла при сверлении.
- Шестигранный хвостовик: Подобно форме некоторых бит для отверток, шестигранник имеет шесть сторон, которые помогают сверлу оставаться устойчивым при сверлении твердых металлов.
Изучение конструкции хвостовика, материала долота и покрытия долота может сбивать с толку, но, к счастью, производители сверл делают покупки относительно легкими для покупателя. Сверла маркируются не только размером отверстия, которое они будут просверливать, но и по типу материала, который они будут просверливать. Найдите на упаковке слова «сверло по металлу», за которыми следует список металлов, для прокалывания которых оно предназначено. Вот несколько дополнительных советов, которые помогут вам сверлить более гладкие отверстия и поддерживать сверла в отличной форме.
- Используйте кернер для создания углубления в металле перед сверлением. Это снизит вероятность соскальзывания сверла с бурового материала.
- Используйте смазку при сверлении. Капля масла «три в одном» или смазочно-охлаждающей жидкости смазывает буровое долото, облегчая бурение и уменьшая износ долота.
- Трение, создаваемое сверлом при просверливании металла, может вызвать его нагрев и поломку. Это особенно верно для битов большего размера.Если сверлить медленнее и делать перерывы каждые несколько минут, чтобы долото остыло, ваша коронка прослужит дольше.
Лучшие сверла по металлу должны изготавливаться из стали, предназначенной для того металла, который вы хотите сверлить. Биты также должны быть прочными и выдерживать трение и нагревание при сверлении металла. Следующие ниже рекомендации являются лучшими в своем классе для сверления металла, и одна (или несколько) может оказаться полезным для вашей коллекции инструментов.
Фото: amazon.com
Конические носики и скрученные боковые канавки сверл в этом наборе Hymnorq быстро проникают во многие твердые металлы, включая железо, для сверления устойчивого самоцентрирующегося отверстия. Сверла также подходят для сверления более мягких металлов, таких как алюминий и медь. Обратной стороной является то, что они не подходят для сверления самых твердых металлов, включая титан и высокоуглеродистую сталь. Изготовленные из кобальтовой стали в сочетании с молибденом для дополнительной прочности, биты Hymnorq обладают устойчивостью к трению и высокой температуре.Этот набор включает 13 бит размером от 1/16 дюйма до 1/4 дюйма, чтобы удовлетворить ваши потребности в сверлении металла.
Фото: amazon.com
Хороший набор сверл по металлу не обязательно должен быть дорогим. Набор сверл для титана по металлу amoolo включает 10 сверл из быстрорежущей стали с титановым покрытием, которые просверливают ⅛-дюймовые отверстия в более мягких металлах, включая алюминий, медь и сплавы. Эти сверла не подходят для обработки железа, нержавеющей стали и других закаленных металлов. Нам нравится, как закрученные боковые канавки долот помогают стабилизировать долота во время бурения; Эти канавки также направляют металлическую стружку вверх и наружу для более чистого и гладкого отверстия.amoolo также производит 10-битные наборы других размеров, включая ¼ дюйма, ⅜ дюйма и 3/16 дюйма. Биты поставляются в пластиковом футляре для удобного хранения.
Фото: amazon.com
Для сверления отверстий нескольких размеров в листовом металле сложно превзойти набор титановых ступенчатых сверл TACKLIFE из пяти частей, который поставляется с четырьмя ступенчатыми сверлами, которые могут просверливать отверстия 50 размеров. В этот комплект также входит кернер для создания направляющей ямки в металле перед началом сверления. Каждый бит в коллекции имеет легко читаемые, нанесенные лазером измерения, которые не стираются.
Изготовленные из быстрорежущей стали с покрытием из титана для уменьшения трения, эти сверла достаточно долговечны для сверления отверстий в мягких листовых металлах, таких как алюминий, сплав, олово и медь. Ступенчатые насадки также имеют форму отверстия X-типа, которая помогает удалять металлическую стружку из отверстия во время сверления. Набор поставляется в защитном алюминиевом футляре для хранения.
Фото: amazon.com
Если вам нужно просверлить закаленные металлы, такие как кованое железо или нержавеющая сталь, обратите внимание на набор сверл Drill Hulk по металлу по кобальту.В набор входит дюжина ⅛-дюймовых спиральных сверл из быстрорежущей стали и кобальта, обеспечивающих долговечность и термостойкость. Конические точки разъема битов могут быстро и чисто проникать в металл, а их рифленые боковые канавки удаляют металлическую стружку во время сверления. Эти биты не поставляются в футляре для хранения.
Фото: amazon.com
Для простого сверления тонкой стали, такой как алюминий, медь или сплав, воспользуйтесь набором сверл по металлу Bosch. Изготовленные из быстрорежущей стали и покрытые черной оксидной пленкой, сверла Bosch выдерживают трение и нагрев, поэтому вы можете сверлить непрерывно, не нагревая сверла.Канавки по бокам скрученных хвостовиков долот будут выводить металлическую стружку вверх и из отверстия во время сверления. Их конические наконечники могут быстро проникать в металл, уравновешивать сверло и производить чистое ровное отверстие. В набор входит 21 бит размером от 1/16 дюйма до ½ дюйма, упакованный в пластиковый футляр для хранения.
Если вы только начинаете заниматься слесарными работами или хотите расширить свой набор сверл, добавление сверл по металлу в свой арсенал инструментов — хорошее вложение. Если сверление металла — новое занятие для вас, у вас, вероятно, возникнут вопросы.
Что лучше — кобальтовое или титановое сверло?Это зависит от того, какой металл вы просверливаете. Титановые сверла подходят для сверления мягких металлов, таких как алюминий, в то время как кобальтовые сверла лучше подходят для сверления твердых металлов, таких как чугун.
Как просверлить толстый металл?Лучший способ просверлить толстые металлы — использовать сверлильный станок, а не ручное сверло. Пресс даст вам чистое и гладкое отверстие.Обязательно сверлите медленно и используйте смазочно-охлаждающую жидкость для смазки сверла. Дайте сверлу остыть каждые несколько минут, чтобы оно не перегрелось и не сломалось.
Как заточить сверла по металлу?Многие домашние мастера не утруждают себя заточкой своих коронок, когда режущие кромки затупляются и возникают проблемы при сверлении отверстия, но это обслуживание инструмента стоит того. Вы увеличите срок службы сверл, если заточите их режущие кромки настольным шлифовальным станком.
Нужно ли чистить сверла после каждого использования?Неплохая идея. После сверления сотрите все остатки на сверле мягкой тканью, а затем нанесите на него немного смазочно-охлаждающей жидкости перед хранением.
Как удалить сломанное сверло из металла?Добавьте одну-две капли смазочного масла в сверло, а затем возьмитесь за сломанный конец его хвостовика плоскогубцами. Поверните против часовой стрелки, чтобы удалить бит.
Сверление стопок из титана / углепластика / алюминия | Научный.Нетто
[1] Х. Чжан, В. Чен, Д. Чен и Л. Чжан: Key Eng. Матер. Vol. 196 (2001), стр.43.
[2] Дж.П. Давим и П. Рейс: Compos. Struct. Vol. 59 (4) (2003), с. 481.
[3] C.C. Цао и Х. Хоченг: Междунар. J. Mach. Инструменты Manuf.Vol. 44 (10) (2004), стр.1085.
[4] К. Мерфи, Дж. Бирн и М.Д. Гилкрист: Proc. Inst. Мех. Англ. Часть B J. Eng. Manuf. Vol.216 (2) (2002), стр.143.
[5] W. Konig, Ch. Wulf, P. Graβ и H. Willerscheid: Ann. CIRP Vol. 34/2 (1985), стр. 537.
[6] Л.Б. Чжан, Л.Дж. Ван и X.Y. Лю: Proc. Inst. Мех. Англ. Часть B J. Eng. Manuf. Vol. 215 (2) (2001), с.135.
[7] К.Ю. Парк, Дж.Х. Чой и Д.Г. Ли: Дж. Компос. Матер. Vol. 29 (15) (1995), стр. (1988).
[8] Э. Бринксмайер и Р. Янссен: CIRP Ann., Manuf.Technol. Vol. 51/1 (2002), стр.87.
[9] C.C. Цао и Х. Хоченг: Междунар. J. Mach. Инструменты Manuf. Vol. 45 (11) (2005), стр. 1261.
[10] Я.У. Парк, Д.А. Дорнфельд: J. Eng. Матер. Technol. Vol. 122 (2) (2000), стр.229.
[11] S.C. Lin и C.J. Ting: Wear Vol. 180 (1-2) (1995), стр.53.
[12] ЯВЛЯЕТСЯ. Шиха Д. Аспинуолл, С. Су и С. Брэдли: Int. J. Mach. Инструменты Manuf. Vol. 49 (1213) (2009), стр.1008.
Влияние параметров резания, ориентации волокон и распыления тумана
Abstract
Повышение температуры резания в процессе обработки может повлиять на окончательное качество обработанной детали.Влияние температур резания более критично при механической обработке пакетов композит-металл и слоистых материалов из волокнистого металла из-за характера штабелирования этих гибридов, в результате чего композит подвергается нагреву от прямого контакта с металлической частью пакета и удаленной горячей стружкой. В этой статье исследуется температура поверхности заготовки двух марок волокнистых металлических ламинатов, известных как GLARE. Экспериментальное исследование было проведено с использованием термопар и инфракрасной термографии для определения излучательной способности верхней, нижней и боковых поверхностей ламината GLARE.Кроме того, инфракрасная термография использовалась для определения максимальной температуры нижней поверхности обработанных отверстий во время сверления GLARE в условиях охлаждения с сухим и минимальным количеством смазки (MQL) при различных параметрах резания. Результаты показали, что в процессе обработки температура поверхности заготовки увеличивалась с увеличением скорости подачи, а ориентация волокон влияла на развиваемую температуру в ламинате.
Ключевые слова: сверление, ОСВЕЩЕНИЕ, минимальное количество смазки, инфракрасное излучение, температура, волокнистые металлические ламинаты, СОЖ, обработка
1.Введение
Волоконно-металлические ламинаты (FML) — это гибридные материалы, состоящие из чередующихся слоев металлов и композитов, соединенных вместе с помощью адгезивной эпоксидной смолы. Некоторые из наиболее широко известных волоконно-металлических ламинатов включают армированный арамидом алюминиевый ламинат (ARALL) и эпоксидную смолу, армированную стекловолокном и алюминием (GLARE). Последний в настоящее время используется в частях конструкции фюзеляжа коммерческого Airbus A380 [1]. Изготовление и установка этих конструктивных деталей аэрокосмической отрасли обычно требует операций механической обработки, таких как фрезерование и сверление [1,2].Сообщалось об ограниченном количестве исследований обрабатываемости FML [3,4,5,6,7,8,9]. резюмирует некоторые из наиболее проделанных работ по сверлению тех FML, из которых в нескольких исследованиях изучалось влияние типа, размера и покрытия инструмента на качество отверстия [9,10]. В то время как другие исследования изучали влияние охлаждающей жидкости, толщины заготовки и ориентации волокон на качество отверстий [6,7,8,11]. В других исследованиях сообщалось, что толщина ламината может влиять на тепловыделение и состояние кромки фрезерования с точки зрения повышенного расслоения, деформации и адгезии стружки к режущему инструменту [1], в то время как полусухое фрезерование улучшает качество кромки, когда фрезерование тонких ламинатов GLARE [1].
Таблица 1
Резюме опубликованных исследований по механической обработке волоконных металлических ламинатов [11].
Процесс обработки | Используемые режущие инструменты | Описание заготовки | Цели | Ref |
---|---|---|---|---|
AWJM | Отверстие: Сапфировое, диаметр сопла 0,38116 мм, диаметр сопла 1,0 мм, диаметр сопла 1,0 мм, диаметр сопла Гранат, сетка 80 Угол удара 90 ° | Титан / графит (Ti / Gr) | Mrr K | [5] |
Алмазное отверстие диаметром 0.3 мм Пластина диаметром 1,1 мм, длиной 51 мм и углом удара 90 °, Гранат: оливиновый абразив, сетка 60 | БЛИК 2–3 / 2–0,2 БЛИК 2–3 / 2–0,3 БЛИК 4–5 / 4–0,3 | BD Ke | [4] | |
Фрезерование | Не указано | GLARE | DFM | [3] |
Сверло% | 5 мм HSS с покрытием TiN Совместное сверло, твердосплавное сверло из быстрорежущей стали 5 и твердосплавное сверло 5,5 мм 4.Сверло из быстрорежущей стали с алмазным напором 8 мм | GLARE 3–3 / 2–0,3 GLARE 3–2 / 1–0,3 GLARE3–4 / 3–0,3 | BCZ | [9] |
Твердосплавное сверло 6 мм без покрытия | БЛЕСК из листов Al2024 и стекловолокна типа R | CZ | [8] | |
6,35 твердосплавные сверла | БЛИК 5 3 / 2–0,3 БЛИК 6 3 / 2–0,3 | CZ | [10] | |
Твердосплавное сверло с покрытием TiAlN 6 мм | GLARE 2B 11 / 10–0.4 GLARE 2B 8 / 7–0,4 GLARE 3 8 / 7–0,4 | CRQBZYO | [6,7,11,12] |
В процессе обработки происходит тепловыделение из-за постоянного трения между заготовкой и режущим инструментом. Приблизительно 98% энергии при механической обработке преобразуется в тепло [13]. Повышение температуры может отрицательно повлиять на свойства материалов заготовки и режущего инструмента, вызвать термическое повреждение заготовки, вызывая изменение размеров, и ускорить износ инструмента или привести к химическим изменениям в материалах заготовки и инструмента, снижая качество обрабатываемых деталей. [14].Более того, повышение температуры резания в композитах может привести к выгоранию матрицы, ускорению вытягивания волокна и может вызвать снижение прочности ламината на сдвиг [15]. Использование охлаждающей жидкости в процессе обработки оказалось мощным методом снижения температуры резания. Тем не менее, влияние температур обработки остается серьезной проблемой, особенно в условиях сухой и высокоскоростной обработки. Одним из наиболее важных факторов, определяющих повышение температуры в процессе обработки, является теплопроводность материала заготовки [16].Материалы с низкой теплопроводностью подвержены более высокому повышению температуры во время обработки из-за их неспособности быстро рассеивать тепло. Кроме того, содержание сплава в материале также может влиять на температуру обработки, Ozek et al. [17] ранее сообщали, что при сверлении различных алюминиевых сплавов (A5083, A6061, A7075-T651, A1050) температура заготовки может достигать 242 ° C в A5083 и 164 ° C в A1050 при одинаковых условиях резания из-за к различию в их легирующем содержании.Тепло, выделяемое при обработке композитов, распределяется иначе, чем при обработке металлов [18]. В металлах примерно 75% тепла генерируется в зоне сдвига, 20% — при скольжении стружки по торцу инструмента и около 5% возникает из-за пластической деформации металлической заготовки [16] и составляет 80–85%. генерируемой тепловой энергии уносится откачиваемыми чипами [19]. Действительно, относительно более высокая пластичность большинства металлов по сравнению с композитами означает, что во время резки происходит обширная пластическая деформация стружки, что увеличивает тепловыделение и температуру [20].Просверливание композитов ограничено температурой размягчения матричной системы, несмотря на то, что волокна имеют высокие температуры плавления. Тем не менее, температуры, возникающие в процессе обработки, не должны превышать температуру размягчения матрицы [21]. Кроме того, недостаточная пластичность, необходимая для пластической деформации, приводит к образованию очень мелких фрагментов стружки в сочетании с низкой теплопроводностью композитов, что означает, что большое количество тепла рассеивается заготовкой и режущим инструментом.
Температура резания при сверлении сильно зависит от скорости резания и подачи [18]. Fliescher et al. [22] ранее сообщали, что заготовка принимает на себя большую долю распределения тепла во время процесса сверления, которая может составлять от 10% до 35% по сравнению с токарными и фрезерными операциями, в которых заготовка занимает от 1,1% до 20% и 1,3%. –25% тепла соответственно. Повышение температуры заготовки во время процесса обработки становится критическим при обработке композитных металлических стопок и волоконных металлических ламинатов (FML), поскольку это может отрицательно повлиять на целостность композитной детали в стопке из-за плохой теплопроводности по сравнению с металлической частью. что делает его более восприимчивым к термическим повреждениям.Wang et al. [23] сообщили, что потеря тепла из композитного металлического пакета происходит быстрее, когда металлическая заготовка помещается сверху композитной заготовки из-за лучшего отвода стружки и того факта, что развитые температуры сверления в композитном материале выше, чем в алюминиевом. из-за плохой теплопроводности. Размещение металлической заготовки под композитом приведет к тому, что удаленная металлическая стружка будет контактировать с композитной поверхностью, таким образом, увеличивая вероятность забивания стружки и повреждения поверхности в композитной части [23].
Измерение температуры во время процесса обработки было основной целью многих исследований фрезерных и токарных операций и, в меньшей степени, операций сверления, особенно в пакетах композитных металлов и FML. Некоторые из наиболее распространенных методов измерения температуры в процессе бурения были обобщены Taskesen et al. [24] с использованием либо контактных методов путем встраивания термопар в заготовку или режущий инструмент, либо бесконтактных методов, таких как инфракрасные пирометры и инфракрасные камеры.В предыдущих исследованиях обработки алюминиевых сплавов сообщалось, что температура заготовки может достигать 271 ° C при сухом сверлении и до 440 ° C при сухом точении [25]. В то время как для композитов температура заготовки может составлять от 128 ° C до 580 ° C при сверлении штабелей композитных металлов [23,26]. Использование охлаждающих жидкостей может значительно снизить температуру обработки. Предыдущие исследования показали, что токарная обработка стали Inconel 718 с использованием криогенного метода и метода охлаждения MQL привела к резкому снижению температуры заготовки по сравнению со сверлением при комнатной температуре, причем криогенное охлаждение было более эффективным, чем MQL [27].Аналогичные результаты по снижению температуры были зарегистрированы при шлифовании нержавеющей стали 318 с использованием мокрого и криогенного охлаждения [28]. Dhar et al. [29] показали, что использование MQL при токарной обработке стали AISI 1040 привело к снижению температуры на 125 ° C по сравнению со сверлением при комнатной температуре. Shetty et al. [25] сообщили, что использование водомасляной эмульсии, сжатого воздуха и пара снижает температуру заготовки сплава AA6061-15 об.% SiC на 40, 120 и 280 ° C соответственно.
Было проведено значительное количество исследований, посвященных влиянию параметров резания и охлаждающей жидкости на максимальную температуру в процессе обработки различных металлов, включая сталь [27,28,29,30,31,32,33,34,35 , 36,37,38,39], алюминиевые сплавы [17,25,34,40,41,42,43,44], титан в основном сплав Ti6Al64 [43,45,46] и, в меньшей степени, другие материалы , например, магниевый сплав [47].В то время как исследования по измерению температуры композитных [15,23,48,49,50,51,52,53,54,55,56,57,58,59] и композитных металлических штабелей [23,50,60] резко возросли. За последние несколько лет не было сообщений об исследованиях по измерению температуры при механической обработке FML. Ранее сообщалось, что появление зон термического влияния в режущем инструменте и краях ламината влияет на качество обработанных FML [1], и, следовательно, это считается особой областью интереса, которая требует дальнейшего изучения.В этом исследовании сравнивались температуры сверления нижней поверхности обработанных отверстий в двух сортах металлических ламинатов с волокном GLARE, чтобы определить влияние ориентации волокна. В исследовании также рассматривается влияние использования минимального количества смазки на развиваемую температуру по сравнению с сухим сверлением при комнатной температуре на температуру выходной поверхности ламината. Кроме того, в исследовании сообщается о значениях излучательной способности поверхностей GLARE, которые могут быть использованы в других исследованиях, которые могут потребовать температурного анализа с использованием инфракрасных методов.
2. Материалы и методы
2.1. Заготовка и режущий инструмент
Материалом заготовки, использовавшимся в этом исследовании, были металлические ламинаты с однонаправленным волокном GLARE. Это исследование рассматривало две категории панелей GLARE: GLARE 2B и GLARE 3. иллюстрирует конфигурацию ламинатов GLARE 2B и GLARE 3. Образцы были предоставлены Центром ламината металлического волокна (FMLC) в Делфте, Нидерланды. Каждый образец GLARE состоял из слоев Al2024-T3, имеющих номинальную толщину 0 мкм.4064 мм и препреги из стекловолокна S2, залитых в клей FM94, имеющий приблизительную толщину 0,133 мм [1], как показано на рис.
Схематические изображения ламинатов GLARE: ( a ) GLARE 2B с однонаправленным волокном, совпадающим с направлением прокатки; и ( b ) GLARE 3 с поперечно сложенными волокнистыми слоями ( c ) Вид спереди на образцы GLARE 2B 11 / 10-0.4 и GLARE 3 8 / 7-0.4, использованные при пробных сверлениях [6].
Таблица 2
Марки GLARE, использованные в экспериментах по бурению, и их свойства [6,7,11].
Материал | Блики 3 8 / 7-0,4 | Блики 2B 8 / 7-0,4 | Блики 2B 11 / 10-0,4 |
---|---|---|---|
Толщина алюминиевого слоя (мм) | 0,4064 | 0,4064 | 0,4064 |
Толщина слоя стекловолокна S2 (мм) | 0,266 | 0,266 | 0,266 |
Общая толщина (мм) | 5,113 | 5,113 | 7,110 |
63,58% | 63,58% | 62,69% | |
Размеры заготовки (мм) | 200 × 150 | 200 × 150 | 200 × 150 |
Каждый слой волокна состоял из двух однонаправленных препреги ориентированы под [90 ° / 90 °] в GLARE 2B и [0/90 °] в GLARE 3 [6,7,11], где направление прокатки алюминиевых листов определяется как (0 °) (см.). изображает некоторые из механических свойств препрега из стекловолокна S2 и Al2024-T3, рассмотренных в экспериментальной работе.Образцы выдерживали в автоклаве около 300 мин при повышенных температурах 120 ° C и давлении 6 бар [6,7,11,61]. Поверхность алюминиевых листов предварительно обрабатывается и обезжиривается с последующим анодированием хромовой или фосфорной кислотой и последующим грунтованием антикоррозийной грунтовкой BR-127 [1]. Волокна поставляются в виде препрега, включая адгезивную систему FM94 от Cytec в Великобритании [1]. В качестве режущего инструмента в данной работе использовались твердосплавные спиральные сверла OSG HYP-HP-3D ϕ6 мм с покрытием TiAlN с углом при вершине 140 ° и углом спирали 30 ° [6,7,11].
Таблица 3
Механические свойства препрега из стекловолокна S2 и Al2024-T3 [11,62,63,64,65].
Механические свойства | UD S2 Стекло / FM 94 Эпоксидный препрег V F = 60 % | Al2024-T3 | Ед. –55 | 72,2 | ГПа | |||
---|---|---|---|---|---|---|---|---|
T | 9.4–9,5 | — | ||||||
Предел прочности при растяжении (σ) | L | 2640 | 455 | МПа | ||||
T | 57 | 448 | ||||||
Предельная деформация | L | 3,5–4,7 | 19 | — | ||||
T | 0,6 | — | ||||||
Модуль сдвига (G) | L | 5,55 | 27,6 | 923 9011 ГПа3 | — | |||
Коэффициент Пуассона (ν) | L | 0.33 | 0,33 | — | ||||
T | 0,0575 | — | ||||||
Плотность (ρ) | — | 1980 | 2770 | кг / м 3 | Коэффициент теплового расширения 3 9020 (α)L | 3,9–6,1 | 23,4 | (1 / ° C) 10 −6 |
T | 26,2–55,2 | 23,4 | ||||||
Теплопроводность (K) 907 (K) 90 | L | 1.1–1,4 | 121 | Вт / м-К | ||||
T | 0,43–0,53 | — |
2.2. Определение коэффициента излучения поверхностей GLARE Fiber Metal Laminate
Коэффициент излучения можно описать как количество тепловой энергии, которую материал излучает в форме инфракрасной энергии, значение коэффициента излучения для материалов находится в диапазоне от 0 (материал, который не излучает инфракрасная энергия) до 1 (черное тело), которое полностью излучает тепловую энергию.У разных материалов разные коэффициенты излучения, на коэффициент излучения объекта могут влиять несколько факторов, например, его температура и температура окружающей среды, размер и форма материала. Поскольку ранее сообщалось, что зона термического влияния на краях обработанных ламинатов представляет собой явление, которое заслуживает рассмотрения во время операций механической обработки, предпринята попытка оценить развивающуюся температуру вокруг краев отверстий на выходной стороне ламината, когда режущий инструмент выходит из заготовки.В текущем исследовании метод нагрева материала использовался для определения коэффициента излучения верхней и нижней поверхностей GLARE и его краев. Наружные алюминиевые листы GLARE обычно покрываются тонким плакированным слоем для повышения устойчивости поверхности к коррозии; Кроме того, все алюминиевые листы также иногда анодируются и покрываются антикоррозийной грунтовкой [1]. Химическая обработка алюминиевого листа придает поверхности различный уровень интенсивности цвета, что приводит к диапазону коэффициента излучения, а не к постоянному значению.Коэффициент излучения GLARE был определен путем проведения трех тестов на коэффициент излучения, как показано на рис. Каждое испытание проводилось с использованием различных инфракрасных (ИК) камер и различных типов покрытий / лент с известными значениями коэффициента излучения.
Таблица 4
Коэффициент излучения металлических ламинатов с волокном GLARE с использованием трех ИК-камер и методов термопары.
Описание | Тест 1 | Тест 2 | Тест 3 | |||
---|---|---|---|---|---|---|
Тип камеры | Электрофизическая PV320 Линза 20 ° | AGEMA 550 20 ° FL | Линза 0.4 м, объектив 24 ° ||||
Количество используемых камер | 1 | 2 | 2 | |||
Тип покрытия / ленты | Черный спрей краска | Краска для особо высоких температур и 3M Виниловый скотч Super 88 | Виниловый скотч 3M Super 88 | |||
Коэффициент излучения используемого покрытия | 0,94 | 0,94 и 0,95 | 0,95 | 923Конфорка | Конфорка | Духовка |
Используемый уровень температуры | 60–70 ° C | 60–90 ° C | 90 ° C | |||
T окружающей среды | 24 ° C 9020 C | 24 ° C | ||||
T отражают | — | 21 ° C | 21 ° C | |||
Используемые термопары | Да | Да | Нет | 9230 84 E1 (верх и низ)0.8 | 0,82 | 0,832–0,843 |
E2 (слои S2-FM94) | 0,6 | 0,6 | 0,594–0,683 | |||
E3 (листы Al2024) | 0,4 0,395 | |||||
Расстояние между камерой и целевой поверхностью | 0,5 м | 0,45 м | 0,4 м и 0,1 м |
Существует несколько методов определения излучательной способности объекта, обработки поверхности и нагрева материала: Некоторые из наиболее распространенных и простых методов, последний из которых использовался для определения коэффициента излучения GLARE-поверхности в этом исследовании.Метод нагрева материала осуществлялся путем покрытия поверхности материала спреем для покрытия или липкой лентой с известным коэффициентом излучения, который находится в диапазоне от 0,9 до 1. Образцы GLARE затем были равномерно нагреты до известного и устойчивого уровня температуры выше температуры окружающей среды. , это можно сделать с помощью нагревательной плиты, тепловизора и термопар для измерения температуры поверхности. Покрытие распылением или лента наносится на часть поверхности материала, а оставшуюся часть выдерживают в тех же условиях.Затем образцы были равномерно нагреты до известной температуры, термопары были прикреплены к поверхности, и температура также контролировалась, чтобы соответствовать используемой температуре горячей пластины. Различные тепловизионные камеры использовались для определения коэффициента излучения путем измерения температуры поверхности с покрытием или лентой с известным коэффициентом излучения и прилегающей поверхности GLARE по отдельности. Была измерена температура поверхности покрытой или заклеенной лентой поверхности, а затем камера была перемещена в область поверхности без покрытия или ленты, и излучательная способность была снижена до тех пор, пока температура ЯРКОСТИ поверхности не сравнялась с температурой покрытой или заклеенной лентой области, зарегистрированный коэффициент излучения — это коэффициент излучения GLARE поверхности.Первый тест проводился с использованием ИК-камеры Electrophysic PV320 с объективом 20 °, камера способна обеспечивать разрешение по излучательной способности с шагом 0,1, а данные обрабатывались с использованием программного обеспечения скоростной тепловизионной съемки.
В первом и втором тестах также использовались высокочувствительные термопары K-типа, которые были размещены в разных местах на верхней поверхности ламината, чтобы подтвердить, что его температура соответствует температуре поверхности горячей пластины, контактирующей с ламинатом GLARE. Второй и третий тесты проводились отдельно с использованием четырех откалиброванных ИК-камер, способных определять значения коэффициента излучения в диапазоне от 0.01 шаг. Второй тест был проведен в AMRC-Sheffield, как показано на, с использованием двух калиброванных AGEMA 550 с линзой 20 °.
Определение излучательной способности ЯРКОСТИ во втором тесте.
Третий тест был проведен ired.co.uk, британской компанией, специализирующейся на предоставлении услуг тепловидения в Великобритании, как показано на a, b.
( a ) Измерение излучательной способности верхней и нижней поверхностей ламината GLARE в третьем испытании. ( b ) Измерение излучательной способности стороны ламината GLARE в третьем испытании.
2.3. Измерение температуры на выходной стороне просверленных отверстий
Целью данной части исследования является измерение зоны термического влияния нижней поверхности ламината путем определения максимальной температуры во время процесса сверления. Поскольку результаты по излучательной способности верхней и нижней поверхностей GLARE показали, что они даже не близки к идеальным черным телам. Кроме того, обработка поверхности верхнего и нижнего алюминиевых листов в GLARE обеспечивает высокую светоотражающую способность, а поскольку тепловизионные камеры фиксируют интенсивность излучения в инфракрасной части, которая состоит из комбинации испускаемого, проходящего и отраженного света.Измеренная температура будет результатом комбинации испускаемого, прошедшего и отраженного излучения, что окажется неточным. Поэтому, чтобы исключить отражательную способность поверхностей, на нижнюю поверхность образцов наносят черное напыляемое покрытие с известной излучательной способностью, которое ранее использовалось для определения излучательной способности GLARE, как показано на рис. Распыление черной краски на заднюю часть пластины обеспечивает высокий коэффициент излучения, который ближе к определению черного тела. Это означает, что поверхность будет поглощать большую часть тепла и света и минимально отражаться от своей поверхности.Коммерческое название краски — черная чрезвычайно высокотемпературная краска E-TECH, разработанная для поверхностей, подвергающихся экстремально высоким температурам, которая обеспечивает высококачественную отделку. Краска легко наносится, имеет быстрое время отверждения и прочную адгезию, а ее максимальная рабочая температура составляет 650 ° C.
GLARE образец покрыт черной аэрозольной краской.
Испытания по измерению температуры проводились на фрезерном станке MORI SEIKI SV 500 с максимальной скоростью шпинделя 10 000 об / мин, который ранее использовался в наших предыдущих работах по обработке GLARE [6,7,11,66].показывает, как деталь и камера устанавливаются внутри станка с ЧПУ. Инфракрасная камера, использованная в этом исследовании, представляла собой откалиброванную тепловизионную камеру FLIR AGEMA 550 со встроенным объективом 20 ° и оптическим разрешением 320 × 240 пикселей. Камера имеет рабочий диапазон измерения от −20 ° C до 250 ° C и до 1500 ° C со стандартным фильтром. Камера имеет спектральный диапазон от 3,6 до 5 мкм и скорость 50 кадров в секунду (fps). Камера управляется с помощью программного обеспечения FLIR tools, которое также использовалось для обработки записанных данных с ИК-камеры.Камера была размещена вертикально, линзы были обращены к задней поверхности образца GLARE. Затем прибор закрывали толстой непрозрачной крышкой, чтобы свести к минимуму количество света, попадающего в камеру.
Подробная информация о настройке измерения температуры с помощью ИК-камеры.
Параметры сверления (скорость шпинделя и скорость подачи), используемые в GLARE 2B и GLARE 3 в сухих условиях и условиях MQL, показаны на. Для каждого режима резания на заготовке просверливали ряд из 10 отверстий, и температуру непрерывно измеряли на выходе, и за максимальную температуру принимали самую высокую температуру, зафиксированную в последних семи отверстиях.
Таблица 5
Параметры резания, использованные при измерениях температуры бурения в сухих испытаниях и испытаниях MQL.
Скорость шпинделя (об / мин) | |||
---|---|---|---|
Скорость подачи (мм / мин) | 3000 | 6000 | 9000 |
300 | A, B | C, D | C, D |
600 | A, B | C, D | C, D |
900 | A, B | C, D | C, D |
3.Результаты и обсуждение
3.1. Влияние ориентации волокна на температуру сверлильной детали
показывает максимальные показания температуры двух отверстий, просверленных в GLARE 2B 11/10. а показывает температурные профили для последнего алюминиевого листа непосредственно перед его отделением от заготовки. b показывает профили максимальной температуры отделения заусенца от заготовки. Профиль температурного контура отверстия на каждом рисунке показывает, что различные области температуры формируются равномерно по периферии отверстия во время процесса сверления.Было обнаружено, что температура снижается при удалении от центра отверстия (см. А) центр отверстия и до его краев показал самые высокие показания температуры с максимальной зарегистрированной температурой около 192,3 ° C в этом случае, и со средним показателем 176,1 ° C вплоть до отверстия. b показывает алюминиевый колпачок заусенца перед отделением от нижней поверхности отверстия, который дает оценку температуры удаленной стружки во время процесса сверления, указывая на то, что она также может достигать высокотемпературных уровней, подобных тем, которые наблюдаются на обработанной поверхности отверстия. .
Максимальные показания температуры при сверлении GLARE 2B 11/10 при ( a ) 6000 об / мин и 300 мм / мин с использованием MQL; ( b ) 9000 об / мин и 900 мм / мин, показывающие отделение крышки заусенца в сухих условиях.
Было замечено, что показание максимальной температуры быстро спадает, что может быть связано с высокой теплопроводностью алюминиевых листов, приводящей к быстрому рассеиванию тепла, прежде чем остается достаточно времени для накопления тепла в заготовке. Коэффициент теплопроводности клеевой эпоксидной системы S2 / FM94 равен 1.1–1,4 Вт / м.К (1,45 Вт / м.К для стекловолокна S2), в то время как сплав Al2024-T3 составляет 121 Вт / м.К [67,68]. Твердосплавные сверла имеют мощность около 110 Вт / м · К, что означает, что слои стекловолокна в GLARE плохо проводят тепло. В процессе сверления тепло накапливается в слоях стекловолокна и затем передается на соседние алюминиевые листы и режущий инструмент. Повышение температуры в слоях стекловолокна может повлиять на физические свойства эпоксидной системы, так что повышение температуры резки может размягчить эпоксидную матрицу и вызвать большую нестабильность волокон из-за микроизгиба [21].Это также указывает на то, что температуры сверления могут превышать температуру размягчения эпоксидной смолы, используемой в GLARE, которая имеет рабочую температуру (температура стеклования T g ) 103 ° C в сухих условиях [1]. Повышение температуры резания ослабляет эпоксидную смолу и влияет на границу раздела между стекловолоконной матрицей, которая играет значительную роль в передаче напряжений в слоях стекловолокна во время процесса сверления. Тепло, выделяемое в процессе сверления, также способствует быстрому ухудшению прочности волокон на сжатие.Поверхности отверстий подвергаются размягчению материала матрицы, что приводит к размыванию границ отверстий из-за тепла, выделяемого в процессе обработки.
Результаты показали, что температура сверления увеличивалась с увеличением скорости подачи. Например, при увеличении скорости подачи с 300 мм / мин до 600 мм / мин при постоянной скорости шпинделя n = 3000 об / мин в GLARE 2B 8/7 температура сверления увеличилась с 163,2 ° C до 185,6 ° C. Увеличение скорости подачи до f = 900 мм / мин немного увеличило температуру сверления, достигнув 188.1 ° C, что может быть связано с увеличением толщины стружки и трения с увеличением скорости подачи. По мере увеличения подачи стружка становится толще, и за один оборот отрезается большая площадь поверхности стружки, что означает меньшую возможность рассеивания тепла и, следовательно, повышение температуры. Этот результат не согласуется с предыдущими исследованиями сверления монолитного алюминиевого сплава, пакетов CFRP / Al7075-T651 и CFRP / Al6061-T6 [23,34,41,69], которые показали, что температура режущего инструмента снижалась с увеличением скорости подачи для того же Значения скорости шпинделя и глубины сверления из-за увеличения скорости съема материала и, следовательно, большего количества тепла уносится стружкой, что приводит к меньшему количеству тепла, передаваемому в заготовку [69].Однако в другом исследовании сверления титановых сплавов увеличение скорости подачи увеличивало температуру сверления при той же скорости шпинделя и глубине сверления [43]. Это также может быть связано с различными параметрами резки и инструментами, используемыми для каждого исследования, что может отрицательно повлиять на процесс измерения температуры и результаты.
показывает максимальные показания температуры отверстий, просверленных в GLARE 2B и GLARE 3 при одинаковых параметрах резания. Результаты показали, что максимальные температуры сверления в GLARE 3 8/7 были ниже, чем в GLARE 2B 8/7, что указывает на то, что ориентация волокна может влиять на температуру заготовки во время процесса обработки.Zitoune et al. [55] ранее сообщали, что температура резки зависит от ориентации волокон, поэтому при сверлении с ориентацией волокон 90 ° она выше, чем при 0 °, из-за более высоких разрушающих напряжений. При 90 ° волокна изгибаются, а затем разрезаются на части, а при 0 ° стружка образуется после разрушения при сжатии. Напряжения разрушения в изгибаемых волокнах выше, чем при сжатии, и поэтому требуются большие энергии (силы резания), которые увеличивают трение, когда наконечник инструмента проходит через волокна, что увеличивает нагрев.Например, при сверлении при скорости подачи f = 900 мм / мин и n = скорости шпинделя 3000 об / мин максимальная зарегистрированная температура сверления составила 188,1 ° C в GLARE 2B 8/7 и 179,9 ° C в GLARE 3. Волокна ориентированные в разных направлениях, имеют разные значения теплопроводности матрицы и волокна, которые влияют на повышение температуры в процессе сверления. Повышение температуры с увеличением скорости подачи также может быть учтено при образовании заусенцев, так как по мере увеличения температуры и осевой силы нижний алюминиевый лист испытывает повышенную пластичность, что увеличивает размер образовавшихся заусенцев.Результаты согласуются с выводами Ghafarizadeh et al. [51], который ранее сообщил, что ориентация волокна оказывает значительное влияние на силы резания и температуру резания при фрезеровании однонаправленных углепластиков, так что максимальные и минимальные значения получаются при ориентации волокон 90 ° и 0 ° соответственно. Разница температур сверления не превышала 10 ° C в испытанных параметрах резания, что могло быть связано с малой толщиной слоев стекловолокна в GLARE. Как сообщалось в одном из наших предыдущих исследований, результаты силы резания показали незначительную разницу в силе осевого напора между GLARE 2B и GLARE 3, возникающую из-за разницы в ориентации волокон при одинаковой толщине [7].Однако было замечено, что крутящий момент в GLARE 2B был выше, чем в GLARE 3 при тех же испытанных параметрах резания, что могло привести к более высокому трению между режущим инструментом и заготовкой, вызывая большее повышение температуры в GLARE 2B. Кроме того, относительно небольшая толщина волоконных слоев может оказаться недостаточной для обеспечения значительного повышения температуры из-за разницы в ориентации волокон. Зарегистрированные температуры находятся в диапазоне, полученном в предыдущих исследованиях сверления алюминиевых сплавов, таких как Al2024-T3, Al6061-T6 и Al7075-T6, которые показали, что максимальные температуры находятся в диапазоне от 131 ° C до 360 ° C при сверлении монолитного алюминия, и до 199 ° C в композитных металлических пакетах [23,34,40,41,43,50].
Максимальная температура сверления и влияние ориентации волокон в GLARE.
3.2. Влияние охлаждающей жидкости MQL на температуру детали
показывает сравнение температуры отверстия на выходе между сухим тестом и тестом MQL. Испытания MQL проводились с использованием охлаждающей жидкости с расходом 20 мл / ч и давлением воздуха 3 бара, поскольку в одном из наших предыдущих исследований они показали лучшие результаты среди всех других протестированных значений расхода и давления воздуха. Результаты показали, что применение СОЖ MQL может снизить температуру обработки при сверлении с высокими скоростями подачи f = 900 мм / мин.Это может быть связано с эффектом смазки, который снижает трение вокруг стенок отверстия во время контакта сверла с заготовкой. Сверление при скорости подачи f = 300 мм / мин и скорости шпинделя n = 6000 об / мин дало результаты, аналогичные результатам, полученным при сухом резании, что могло быть связано с быстрым испарением смазки до того, как было достаточно времени для смазки резания. инструмент и заготовка. При той же скорости подачи, но при более высоких скоростях шпинделя n = 9000 об / мин, применение MQL снизило температуру примерно на 22 ° C и увеличило примерно на 10 ° C при сверлении со скоростью подачи f = 600 мм. / мин, что указывает на то, что сочетание скорости шпинделя и скорости подачи играет важную роль в разработке температуры в GLARE.При сверлении GLARE с использованием скоростей шпинделя n = 6000 и 9000 об / мин увеличение скорости подачи приводит к снижению температуры резания, что указывает на то, что MQL становится более эффективным, когда время сверления сокращается (то есть, когда скорость подачи увеличивается). Это может быть связано с небольшим количеством смазки, используемой в MQL, которая имеет тенденцию быстро испаряться, что ограничивает ее способность должным образом смазывать обрабатываемую деталь режущего инструмента.
Сравнение выходной температуры сверления отверстий в условиях MQL и в сухих условиях.
Было обнаружено, что использование охлаждения MQL снижает количество отходов, образующихся на обработанных поверхностях ламината, особенно при сверлении с высокими скоростями шпинделя и низкой скоростью подачи, как показано на. Смазка MQL снижает трение между заготовкой и режущим инструментом, а давление воздуха помогает транспортировать стружку и отходы из зоны резания. Увеличение скорости вращения шпинделя привело к увеличению температуры заготовки из-за увеличения трения между режущим инструментом и поверхностью скважины в единицу времени, что вызывает более высокое трение, тем самым повышая температуру обработки.Увеличение скорости подачи дало несколько разные результаты в зависимости от используемой скорости шпинделя. Снижение температуры резания с увеличением скорости подачи связано с уменьшением времени контакта инструмента с деталью. Хотя не проводилось сравнения для определения влияния толщины ламината на развиваемую температуру, предполагается, что большая толщина ламината дает большую площадь контакта, которая производит больше тепла, в то время как отвод стружки в более тонких ламинатах легче, и, следовательно, выделяемое тепло уменьшается. ниже из-за меньшей площади контакта, что также уменьшило прилипание стружки к режущему инструменту [1].При более высоких скоростях шпинделя создается более высокая температура, которая увеличивает склонность стружки и волокон прилипать к режущему инструменту, а затем выталкивается в кромки ламината и обработанные поверхности, и это известно как отходы, вызывающие расслоение и деформации [1] .
СЭМ-изображения состояния верхней поверхности ствола скважин при ( a ) MQL и ( b ) в сухом состоянии.
Было обнаружено, что использование охлаждения MQL снижает количество отходов, образующихся на обработанных поверхностях ламината, особенно при сверлении с высокими скоростями шпинделя и низкой скоростью подачи, как показано на.Смазка MQL снижает трение между заготовкой и режущим инструментом, а давление воздуха помогает транспортировать стружку и отходы из зоны резания. Увеличение скорости вращения шпинделя привело к увеличению температуры заготовки из-за увеличения трения между режущим инструментом и поверхностью скважины в единицу времени, что вызывает более высокое трение, тем самым повышая температуру обработки. Увеличение скорости подачи дало несколько разные результаты в зависимости от используемой скорости шпинделя.Снижение температуры резания с увеличением скорости подачи связано с уменьшением времени контакта инструмента с деталью. Хотя не проводилось сравнения для определения влияния толщины ламината на развиваемую температуру, предполагается, что большая толщина ламината дает большую площадь контакта, которая производит больше тепла, в то время как отвод стружки в более тонких ламинатах легче, и, следовательно, выделяемое тепло уменьшается. ниже из-за меньшей площади контакта, что также уменьшило прилипание стружки к режущему инструменту [1].При более высоких скоростях шпинделя создается более высокая температура, которая увеличивает склонность стружки и волокон прилипать к режущему инструменту, а затем выталкивается в кромки ламината и обработанные поверхности, и это известно как отходы, вызывающие расслоение и деформации [1] .
Сравнение материалов и типов сверл— Какой материал для сверл лучше всего
1. Сверло из углеродистой стали
— Низкоуглеродистая сталь: это самый дешевый вариант изготовления сверл, из-за их плохого состояния сверла из низкоуглеродистой стали обычно используются для сверления мягкой древесины и некоторых пластмасс и требуют частой заточки для продления срока службы.
— Высокоуглеродистая сталь: лучший материал, чем низкоуглеродистая сталь, сверло из высокоуглеродистой стали может дольше сохранять свою форму и эффективность, поэтому его можно использовать для резки более прочных материалов, таких как лиственная древесина и мягкие металлы.
2. Сверло из быстрорежущей стали
По сравнению с долотами из углеродистой стали, сейчас на рынке более популярны сверла из быстрорежущей стали. HSS — это особый тип углеродистой стали, сохранение структурной целостности при высоких температурах является отличительным преимуществом сверла HSS, более того, сверло из быстрорежущей стали имеет более высокую износостойкость и твердость, а также может хорошо работать при нормальной температуре.Сверла из быстрорежущей стали подходят для большинства процессов сверления дерева и металла, включая сверление с ЧПУ . На инструмент из быстрорежущей стали можно наносить нитрид титана и другие виды покрытий, чтобы повысить смазывающую способность и уменьшить трение.
3. Сверло с титановым покрытием
Титан — это не только популярный материал в аэрокосмической и медицинской промышленности, но и универсальный материал для покрытия сверл, который может продлить срок их службы. Благодаря высокой коррозионной стойкости, хорошему пределу выносливости, пределу нагрева, относительно небольшому весу и более длительному сроку службы сверло с титановым покрытием идеально подходит для серийного массового сверления стали, железа, дерева, пластика и различных поверхностей, оно позволяет более высокая частота вращения и более короткое время цикла.Наиболее распространенными типами титановых покрытий являются нитрид титана (TiN), нитрид титана-алюминия (TiAN) и нитрид титана-углерода (TiCN). Считается, что TiAN и TiCN превосходят TiN, поскольку они могут в значительной степени увеличить срок службы. Недостатком покрытия сверла является то, что, как только инструмент затупится, его нельзя будет заточить, чтобы избежать износа материала покрытия.
4. Кобальтовое сверло
Кобальт — это еще один тип покрытия для сверла, сверло из кобальта используется для резки материалов, которые не могут быть обработаны сверлом из быстрорежущей стали, таких как нержавеющая сталь и другие трудные материалы, оно может сохранять твердость при гораздо более высоких температурах, чем быстрорежущая сталь, и не подвержено сильным воздействиям. сильная жара.Но кобальт — слишком хрупкое покрытие.
5. Сверло с твердосплавными напайками
Сверлос твердосплавным наконечником очень твердое, легко отводит тепло и может удерживать лезвие дольше, чем сверла другого типа. Подобно кобальтовому сверлу, оно также очень хрупкое и может разрушиться при неправильном использовании.