Абразивная способность — Энциклопедия по машиностроению XXL
Действительно, при испытании на изнашивание по незакрепленному абразиву помимо образца изнашивается наковальня, на которой расположен слой абразива. Исследования показали, что наковальня всегда изнашивается меньше, чем образец. Это можно объяснить главным образом различным воздействием слоя незакрепленного абразива на образец и наковальню, краевым эффектом и шаржированием абразивными частицами поверхности наковальни. Расположенный на плоской наковальне абразив имеет всегда большую абразивную способность по отношению к поверхности образца, чем по отношению к наковальне. Это связано с тем, что при свободном размещении на плоскости, незакрепленные абразивные частицы сложной формы и различных раз- [c.87]Получение покрытий методом погружения. Для получения режущего инструмента, обладающего высокой абразивной способностью и одновременно достаточной эластичностью, на заготовки из твердых сплавов наносят многослойные покрытия различных веществ [60].
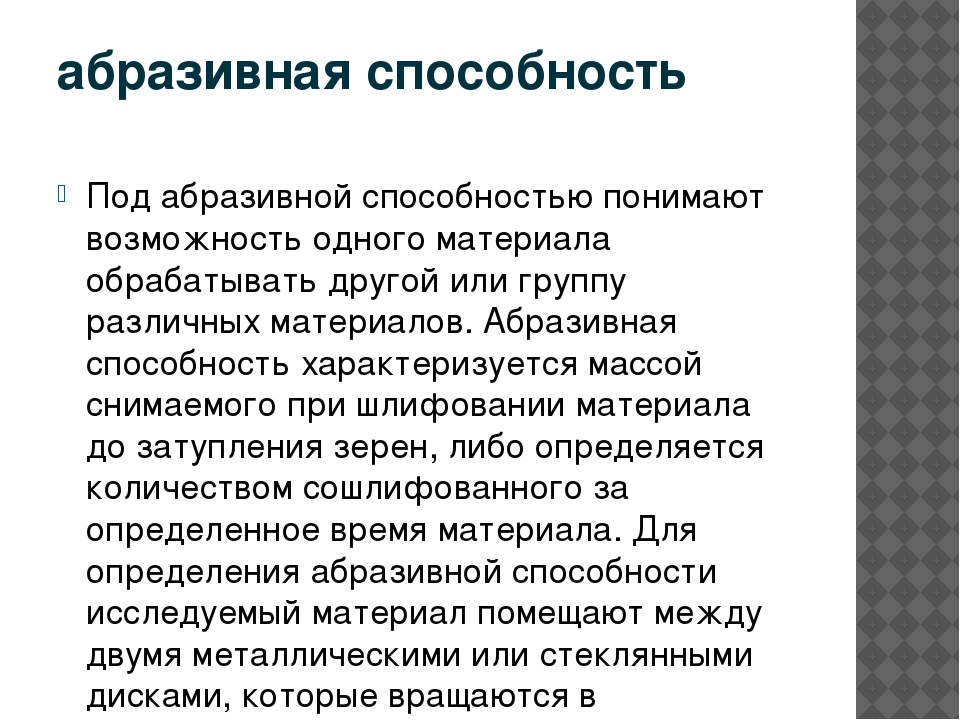
Микропорошки марки A M обладают нормальной, а марки АСН— повышенной абразивной способностью. Первые применяют для изготовления инструментов, паст и суспензий, используемых при обработке деталей из закаленных сталей и твердых сплавов, а вторые — для обработки природных и синтетических алмазов, специальной керамики и других труднообрабатываемых материалов. Самая крупная зернистость микропорошков 60/40, самая мелкая 1/0, что соответствует размеру основной фракции 60—40 мкм и менее 1 мкм.
Микропорошки марок АН и АСН обладают повышенной абразивной способностью по сравнению с порошками марок AM и A M.
[c. 625]
Карбид кремния (карборунд) i — соединение кремния с углеродом. Плотность 3,12—3,2 г/сж микротвердость 2900— 3500 кГ мм абразивная способность (по алмазу) 0,25—0,45. Подразделяют на зеленый КЗ с повышенной абразивной способностью и черный КЧ, применяемый для шлифования чугуна, алюминия, латуни и других вязких сплавов.
Абразивная способность (А. с.) является безразмерной величиной (коэффициент А. с.) и определяется отношением [c.378]
Абразивная способность по прибору [c.154]
Для устранения влияния фактора неоднородности абразивных свойств шлифовальной шкурки на результаты опыта, на каждом листе, натянутом на диск, испытывается не только изучаемый образец, но и один и тот же эталонный образец. Это позволяет приводить результаты опыта к одной и той же абразивной способности шкурки, принятой за норму, или выражать износ испытуемого материала как отношение его износа к износу эталона.
Важно отметить, что при повторном использовании одной и той же навески зерна большое число раз его абразивная способность (т. е. износ образца за опыт) практически не меняется. [c.27]
Согласно исследованиям [12], износостойкость при использовании этого метода изменяется с изменением концентрации сплава не так, как при воздействии закрепленным зерном. В ряде случаев метод оказывается весьма чувствительным. Например, упрочнение при старении дюраля он обнаруживает, что не выявляется изнашиванием о жестко закрепленное зерно [13]. Основным фактором, определяющим мгновенную абразивную способность высокотвердого зерна [14], является острота режущих выступов зерна, характеризуемая величиной среднего радиуса закругления этих выступов [15]. Показано, что разрушительное действие зерна велико лишь в том случае, когда его твердость выше твердости разрушающего металла, причем дальнейшее повышение твердости зерна не эффективно.
27]
Недостатки абразивного круга как истирающей поверхности состоят в том, что в результате трения испытуемого образца о круг меняется его абразивная способность в одних случаях происходит засорение пор круга продуктами изнашивания, что ведет к снижению абразивной способности в других случаях -под воздействием образца происходит разрушение поверхности круга, ведущее к повышению его абразивной спо- , собности.
При стирании металлов (при трении по одной и той же поверхности ш.курки) износ, после его снижения, часто стабилизируется на некоторый период, а затем снижается вследствие засорения шкурки продуктами износа. Засорение хотя и происходит с самого начала истирания, но вследствие небольшой величины отделившихся частиц и малого их количества (металлы изнашиваются слабо) не сказывается заметно на процессе изнашивания. Лишь значительное засорение абразивной поверхности продуктами изнашивания приводит к потере абразивной способности шкурки, что характеризуется на кривой 6 для алюминия хвостом .
Шлифование эльборовыми кругами. Новый синтетический сверхтвердый материал — эльбор — открывает широкие перспективы в области шлифования твердых сталей и сплавов. Эльбор, обладая твердостью и абразивной способностью, близкой к алмазу, значительно превосходит последний по термообработке. Инструменты из эльбора вырабатываются на органических и керамических связках, причем инструменты, изготовленные на керамических связках, по конструкции близки к абразивным. Помимо зернистости, концентрации и вида связки, они, как и обычный абразивный инструмент, характеризуются регулируемыми твердостью и структурой. Инструмент из эльбора обладает следующим преимуществом повышенной режущей способностью и ее постоянством в процессе длительной эксплуатации низким удельным расходом (почти в 30 раз ниже абразивного) отсутствием засаливания, исключающего необходимость правки кругов высокой стойкостью рабочего профиля.
Притирочные порошки режущего действия применяют следующие (по нисходящей абразивной способности)
40]
Микропорошки марок АН и АСН обладают повышенной абразивной способностью [c.333]
Карбид бора — соединение бора с углеродом, отличается высокими твердостью и хрупкостью, применяется в виде порошков и паст для шлифования и доводки изделий из твердых материалов. Абразивные материалы характеризуются зернистостью, формой абразивных зерен, твердостью, механической прочностью, абразивной способностью. [c.229]
Наименование Микротвердость, кГ/мм Абразивная способность. е Плотность, е/см[c.235]
Абразивные материалы (228). Условное обозначение абразивных материалов (229). Широко применяемые номера зернистости абразивных материалов (230). Химический состав электрокорунда (232). Химический состав карбида кремния (233). Химический состав и абразивная способность карбида бора (234). Физико-механические свойства абразивных материалов (235).
Абразивные материалы характеризуются зернистостью, формой абразивных зерен, твердостью, механической прочностью, абразивной способностью.
[c.258]
Особенностью этого метода является испытание материалов на изнашивание путем последовательных многократных ударов по монолиту абразива [10]. Удар образца в течение одного цикла испытаний происходит все время по одному месту абразива, поскольку в результате разрушения породы ее абразивная способность самообновляется. Для применения этого метода создана установка У-1-АМ (рис. 16). Основание установки /, представляющее собой стол с размещенным на нем узлом крепления блока горной породы, жестко соединен с колонной. Привод, состоящий из двигателя 2, редуктора 5 со сменными шестернями и шкивами 3, 6 п шпиндель 13 укреплены на массивной траверсе 4, которая может подниматься и опускаться по колонне с помощью гайки 7.
Качество микропорошков оценивается зернистостью, абразивной способностью и шероховатостью обработанной ими поверхности. Абразивная способность выражается отношением веса сошлифован-ного корунда к весу израсходованного микропорошка.
Инструменты из алмазных порошков и микропорошков изготовляют на органических, металлических, керамических и металлогальванических связках. Шлйфпврошки АСО, имеющие повышенную хрупкость и наибольшую абразивную способность, рекомендуются для изготовления инструментов в основном на органических связках шлифпорошки АСР — для изготовления инструмента на керамических и металлических связках, а шлифпорошки АСВ — только на металлических связках. Наиболее прочные алмазы АСК и АСС для шлифования, заточки и доводки режущего инструмента не применяют, инструмент на их основе изготовляют только на металлической связке и в машиностроении используется для правки шлифовальных кругов.
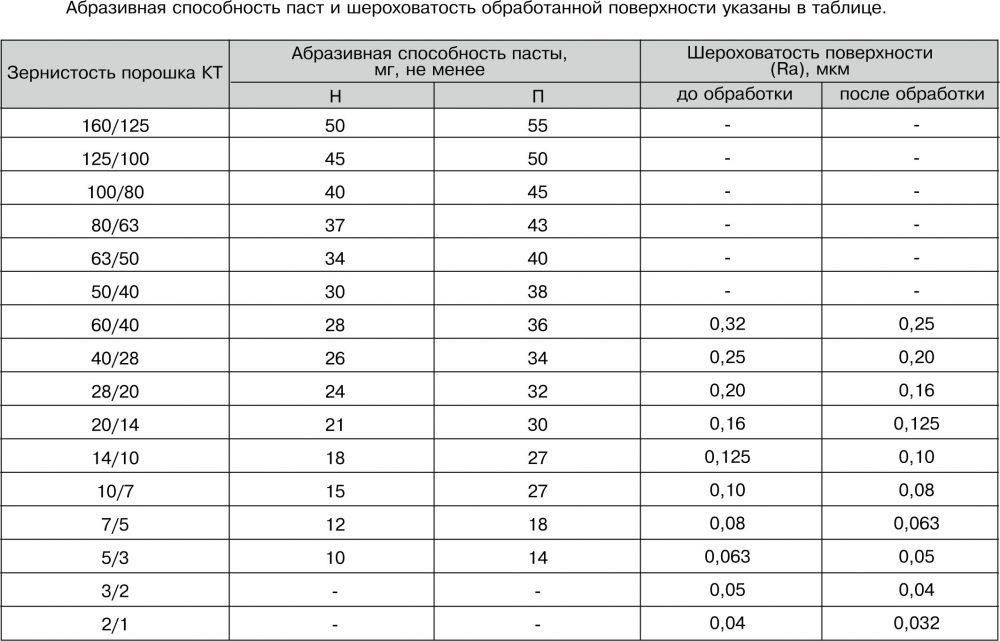
Из кубонита выпускают шлифопорошки двух марок КО зернистостью от 160/125 до 50/40 и КР с размером зерен от 250/200 до 50/40. Кроме того, выпускают микропорошки КМ с размером зерен от 60/40 до 1/0. Изготовляют также кубонит марки КН, отличающийся повышенной абразивной способностью и состоящий в основном из монокристаллов. Эльбор выпускают в виде порошков марок ЛО и ЛП и микропорошка ЛМ. [c.90]
Корунд — природный безводный глинозем AljOg — минерал, уступаюш,ий по твердости только алмазу, с плотностью от 3,82 до 4,28 и температурой плавления 1750— 2050° С в зависимости от примесей. Наиболее чистые прозрачные корунды являются драгоценными камнями — красный рубин и синий сапфир. Технические корунды используют в оптических генераторах, в качестве абразивов в производстве оптики и частично при тонкой доводке точных стальных деталей. Абразивная способность по алмазу 0,14—0,15. [c.266]
Осповным показателем качества абразивов является их абразивная способность, определяющая производительность процесса абразивной обработки при заданных параметрах шероховатости обработанио поверхности.
[c.378]
AM и AGM обладают нормальной абразивной способностью и рекомендуются для обработки твердых сплавов, закаленных сталей, стекла и другпх твердых материалов АН и АСН обладают повышенной абразивной способностью и рекомендуются для обработки природных и синтетических алмазов, корундов, керамики н других сверхтвердых хрупких и труднообрабатываемых материалов. [c.381]
Качество мпкропорошков определяется абразивной способностью при шли-фювании корунда и параметрами шероховатости обработанной ими поверхпо-сти. Их зерновой состав приведен в табл. 6. [c.381]
Карбид бора В4С — химическое соединенпе бора с углеродом — плотная сплавленная масса с раковистым изломом серовато-черного цвета. При дроблении образуются зерна с острыми кромками, поставляемые по ГОСТ 5744—74. По твердости и абразивной способности карбид бора превосходит все абразивные материалы, за цсключенпелМ алмаза и КНБ. [c.383]
Электрокоруид — продукт алектроперешлава глинозема. Абразивная способность (по алмазу) 0,14—0,15. Подразделяют па нормальный, белый, монокорунд п легированный.
[c.384]
Карбид кремния Si (ОСТ 2-114—71)—соединение кремния с углеродом. Подразделяют на зеленый с повышенной абразивной способностью и черный, нрпмеияемып для шлифования чугуна, латуни, алюминия, пластмасс. [c.384]
Нами предложен простой способ сравнительного исследования абразивной износостойкости в потоке движущихся частиц, а также абразивной способности самих частиц, позволяющий вести исследования при повышенных темцературах на достаточно высоких скоростях. Абразивное зерно в определенном количестве из воронки 1 (рис. 1) через приспособление 2 (основанное на принципе разрушения абразивного свода в коническом отве1рстии вибрирующей иглой) попадает в вертикальную трубку 3, где под действием собственного веса набирает скорость и затем ударяется о поверхность вращающегося Т-образного диска 4 из исследуемого металла, заключенного в коробку 5 из нержавеющей стали, обогреваемую электрической печкой 6. При одновременном исследовании нескольких металлов на пе риферии диска 4 в пазах клиновидной
[c.25]
В машинах такого типа абразивные частицы трутся между собой и о другие поверхности, что приводит к изменению их изнашивающей способности. Исследование изменения изнашивающей способности сухого кварцевого 1песка, состоящего из частиц диаметром 0,25—0,50 мм, показало, что 1при прохождении образцом шути в 200 км их механический состав и форма изменились незначительно, а абразивная способность снизилась приблизительно на 7%. [c.37]
Алмаз является самым твердым в природе веществом его твердость в 4—5 раз превышает твердость корунда и твердых сплавов и в 2 раза — карбида бора. Кроме того, он обладает высокими прочностью и износостойкостью, абразивной способностью, хорошей теплопроводностью, самым высоким модулем упругости и низким коэффициентом трения. Недостатком алмазов является их повышенная хруйкость. По твердости и прочности алмазы анизотропны.
[c.220]
Группа зернистости по ГОСТ 3647-59 Номер зернистости Содержание, % В С 1 Вобщ Абразивная способность, % , не менее [c.235]
Карбид кремния — химическое соедииенпе кремния с углеродом, по твердости превосходит корунд, обладает высокими механической прочностью, тепло- и электропроводностью, температурой плавления н стойкостью при резких изменениях температуры, стойкостью против кислот и окисляющего действия воздуха при высоких температурах применяется для изготовления абразивных инструментов, в огнеупорной, химической и электротехнической промышленности. Выпускается карбид кремния двух сортов черный и зеленый. Зеленый карбпд кремния отличается от черного меньшим количеством примесей, большей абразивной способностью и повышенной хрупкостью. [c.258]
G Химический состак и абразивная способность карбида бора [c.268]
Абразивная способность материало — Справочник химика 21
Абразивная способность порошков оценивается по потере веса дисков до полного истирания порошка.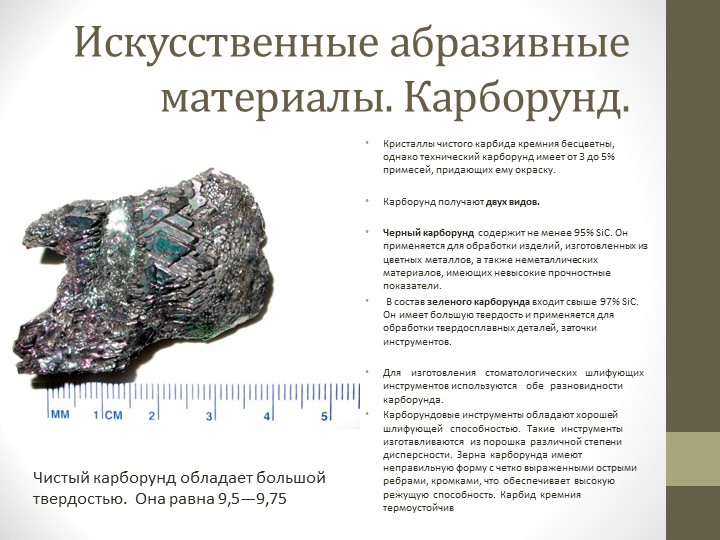
Твердость абразивного материала определяют царапанием образца исследуемого материала эталоном того или иного материала, указанного в шкале твердости (см. стр. 45). Чем тверже материал, тем выше его абразивная способность. [c.335]
Важнейшей характеристикой абразивного материала является его абразивная способность, характеризуемая величиной износа одного из двух медных дисков, между которыми свободно насыпается навеска абразивного материала в течение определенного времени вращения диска. [c.336]
Очень высокая абразивная способность алмаза, с помощью которого можно обрабатывать металлические изделия любой известной нам твердости, не может быть практически широко использована, так как алмаз дефицитен и очень дорог. Поэтому задача получения достаточно дешевого материала с высоким абразивным эффектом уже давно привлекала к себе научную мысль. Продолжительные поиски привели к получению ряда абразивов, более или менее отвечающих новым требованиям современной техники. [c.207]
Обработка карбида бора. Наплавленный любым способом карбид бора подвергается дроблению, а затем сортировке по внешним признакам цвету, характеру кристаллизации и чистоте. В дальнейшем куски карбида бора дробят на вальцах (среднее дробление) и затем в шаровых мельницах (тонкое дробление). После контрольного грохочения материал идет на обогащение, которое позволяет повысить абразивную способность зерновых продуктов карбида бора. После промывки зерно и порошки карбида бора поступают на классификацию (табл. 3). [c.212]
Для характеристики производственной ценности абразивного материала он рекомендует пользоваться величиной не суммарной (или удельной суммарной) абразивной способностью, а технически используемой (полезной) абразивной способностью, которую он принимает равной суммарной (или удельной суммарной), умноженной на некоторый коэффициент, меньший единицы. [c.225]
Абразивный материал Суммарная абразивная способность Уд. суммарная абразивная способность [c.226]
Среди тугоплавких соединений карбид бора занимает особое положение благодаря высокой твердости, уступающей лишь твердости алмаза. Высокая твердость карбида бора в сочетании с абразивной способностью, износостойкостью, жаростойкостью и химической инертностью делают его перспективным для использования в качестве материала правящего инструмента взамен алмаза [c.165]
Абразивность — способность перерабатываемого материала изнашивать рабочие органы машины. [c.9]
Эти свойства заключаются в способности смазочных материалов снижать процесс изнашивания трущихся деталей за счет образования на них граничного слоя, препятствующего непосредственному контакту трущихся поверхностей. Изнашивание деталей происходит в результате механического, абразивного, гидроабразивного, коррозионно-механического и окислительного воздействия на трущиеся поверхности и отделения материала с поверхности твердого тела при трении с постепенным изменением размеров и форм тела. [c.52]
Износостойкость характеризует способность резин сопротивляться потере материала в результате разрушения поверхности под действием фрикционных сил. Различают следующие виды износа резин [6, 12] абразивный, усталостный, скатыванием, макроскопический, пиролитический. [c.76]
НИН металла служат минералы природного и искусственного происхождения, обладающие определенной твердостью, режущей способностью, внутренней вязкостью, формой зерен и другими свойствами (табл. 7.1). Широко применяют наждак, карборунд, корунд, кварц, пемзу, трепел, известь, окись хрома и др. Выбор абразивного материала и степени его зернистости определяется природой обрабатываемого металла, состоянием его поверхности и требуемой чистотой отделки. При выборе величины зерна абразива следует учитывать форму обрабатываемых изделий. Чем выше степень отделки, тем меньше должно быть зерно. [c.123]
Противоизносные свойства масел позволяют судить о их способности предотвращать любой вид удаления материала с контактирующих поверхностей (умеренный износ, задир, выкрашивание, коррозионно-механический, абразивный и др. ). При работе узлов и механизмов в условиях гидродинамического режима трения требования по противоизносным свойствам обеспечиваются минеральными маслами соответствующей вязкости без присадок. При работе узлов и механизмов в условиях полужидкостного и граничного режима трения противоизносные свойства масел не обеспечиваются естественным составом минеральных масел для улучшения этих свойств в масло нужно ввести соответствующие присадки. [c.177]
Подобно шестеренчатым насосам винтовые насосы обш,его назначения не приспособлены для перекачивания жидкостей, лишенных смазывающей способности, содержащих абразивные взвеси и вызывающих коррозию материала деталей. Это очень ограничивает сферу их применения в химической промышленности. Однако имеется несколько насосов, специально сконструированных для перекачивания химически активных сред. [c.87]
Для осуществления шлифующего и полирующего действия необходимо, чтобы зерна абразивного материала обладали определенной твердостью и прочностью, способностью сохранять свою форму и не разрушаться до тех пор, пока кромки зерен достаточно остры. Однако постепенно кромки затупляются. [c.335]
Основные компоненты, входящие в состав шлифовального круга, — это абразивные зерна, которые являются истирающим или режущим компонентом, и связующий материал, удерживающий абразивные зерна на подложке. Очень важно знать соотношение между абразивными зернами и связующим, расстояние между зернами, а также способность связующего материала удерживать абразивные зерна на подложке. [c.406]
Лабораторные и полевые опыты 1958 г. показали, что бентонитовая глина, обычно применяемая при бурении нефтяных скважин, является лучшим средством тушения пожара, чем борат. Ее главное достоинство состоит в способности суспензии стойко удерживаться в воде в течение 2—3 час. прй летних сухих условиях. Она сравнительно дешева, в применяемых дозировках дешевле бората в Калифорнии в 10 раз, а в Висконсине, учитывая затраты на доставку, в 12 раз. Сообщение о применении бентонита вскоре будет опубликовано Калифорнийской опытной станцией, лесной и пастбищной станциями. Но необходимо найти еще лучшее. средство для тушения и подавления огня. Особенно нужен материал, который дешев, легкодоступен, положителен по своим огнегасительным свойствам, нетоксичен для растений и животных, удобен в обращении, не вызывает серьезного абразивного износа насосного оборудования. Необходимо также изучить возможность применения пенообразующих веществ для повышения эффективности огнегасительных средств. [c.368]
Для быстрых лабораторных испытаний применяют специальные истирающие материалы — шлифовальные шкурки, корундовые круги и барабаны, абразивные порошки, металлические сетки. В СССР [130, 131) и странах СЭВ [150] стандартным истирающим материалом служат шлифовальные шкурки на бумажной основе, которые могут быть легко заменены при потере истирающей способности это значительно труднее осуществить в случае абразивных кругов [148] и особенно барабанов [151]. Для того чтобы не слишком ужесточать условия истирания по сравнению с эксплуатационными, используется сравнительно небольшой размер зерна (№8) [152]. В соответствии с рекомендациями ИСО [153] используется шлифовальная шкурка из карбида кремния (№ 6 по ГОСТ 3647—71). Относительная износостойкость резин зависит от типа абразивного материала (например, отношение интенсивностей истирания двух резин на шкурках различных типов [154] изменяется от 0,36 до 1,25). [c.50]
Зернистость абразивного материала на рабочей поверхности шлифовального камня может меняться в процессе механической обработки. У карборундовых камней КЗ с повышенной хрупкостью в результате притупления граней, а в связи с этим и повыщения удельного давления и температуры происходит раскалывание зерен и обновление режущих граней. Режущая способность камня при этом повышается. [c.152]
Выбор оптимального антифрикционного материала зависит от условий его эксплуатации, в частности работы трения, приходящейся на единицу площади трущихся поверхностей, и количества смазки, используемой для снижения коэффициента и работы трения. Основными требованиями к антифрикционным материалам являются способность нести нагрузку, без проявления текучести или ползучести при температурах, развиваемых при работе подшипников, стойкость к средам, в которых эксплуатируются подшипники, и стойкость к абразивному износу. Особенно важным требованием является способность обеспечивать нормальные режимы работы при неравномерной подаче смазки. Три основные фактора обусловливают широкое применение полимеров и полимерных композиционных материалов в качестве антифрикционных материалов для подшипников. [c.215]
По твердости и абразивной способности карбид бора уступает только алмазу поэтому его широко применяют для обработки твердых сплавов. В промышленности карбид бора используют также для создания борированного слоя на сталях, противостоящего износу деталей, изготовленных из этих сталей, и широко применяют в автоматике и ядерной энергетике (для изготовления термопар с высоким значением ЭДС, бораля — материала, защищающего от нейтронного излучения, и др. ). В металлургии карбид бора применяют как раскислитель. [c.33]
Дезинтеграторы (рис. 2,м) служат преим. для сухого помола хрупких, мягких материалов с малой абразивной способностью (напр., каолин, мел, литопои). Исходный материал через загрузочную воронку поступает в центр, часть одного из роторов, вращающихся в противоположных направлениях, и попадает между их пальцами. Под действием центробежных сил куски (зерна) материала продвигаются от центра к периферии роторов, многократно ускоряются, ударяясь о пальцы и сталкиваясь. Измельченный продукт отбрасывается из роторов в кожух и ссьшается через спец. патрубок. Осн. достоинства простота устройства, высокий смешивающий эффект недостатки интенсивный износ пальцев, большое пылеобразование, значит, расход энергии степень измельчения 5-10. [c.182]
АБРАЗИВНОСТЬ (от лат. аЬга 1о — соскабливание), абразивная способность — свойство твердых частиц (абразивных зорен) разрушать поверхность материала при механической обработке (шлифовании, хонинговании, суперфинишировании, доводке) или трении. А. зерен (бд), к-рая характеризуется интенсивностью (массой за единицу времени) разрушения поверхности, может быть количественно оценена [c.12]
Применяют в качестве абразивного материала. В зависимости от гранулометрического состава дробленый карбид бора выпускают в виде шлифпорошков разных номеров зернистости и микропорошка зернистостью М28. По химическому составу и абразивной способности карбид бора должен удовлетворять следующим требованиям [c.154]
Карбид бора — искусственный абразивный материал, полученный из борной кислоты и нефтяного кокса в электрической печи и состоящий из кристаллического карбида бора и небольшо го количества примесей (бора, графита и др.). Карбид бора отдельных номеров зернистости должен соответствовать по зерновому составу — требованиям ГОСТ 3647-47 по химическо-му составу и абразивной способности—нормам, приведенным в табл. 3-2. [c.245]
Для этих процессов по нашим разработкам успешно используются аппараты КС с инертной насадкой из термостойкого и достаточно твердого материала с высокой абразивной способностью, обеспечивающей сомоочищение поверхности частиц. Весь материал, загружаемый в аппарат, выносится из КС с газами очистку газов проводят в две ступени в циклонах с последующей санитарной обработкой (рис. IV. 17). Производительность аппаратов КС с инертной насадкой по испаренной влаге при проведении процесса с высокой начальной температурой газов соответствует максимально достигнутым показателям при обычной сушке с выгрузкой из слоя, что более, чем на порядок выше производительности распылительных сушилок. [c.106]
Твердость является весьма важным свойством, поскольку ояа связана с прочностью материала, а главным образом потому, что определяет способность матер -.ала сопрот Ивляться износу при трении, в том числе к абразивному изиосу. [c.98]
Смазывающие свойства характеризуют способность масел улучщать работоспособность поверхностей трения путем максимального уменьшения износа и трения. Они оцениваются показателем износа, антифрикционными и противозадирными свойствами. Смазывающие свойства масел позволяют судить об их способности предотвращать любой вид удаления материала с контактирующих поверхностей (умеренный износ, задир, выкращивание, коррозионно-механический, абразивный и др. ). При работе узлов и механизмов в условиях гидродинамического режима трения требования по смазьшающим свойствам обеспечиваются нефтяными маслами соответствующей вязкости без присадок. При работе узлов и механизмов в условиях граничной смазки смазывающие свойства масел не обеспечиваются естественным составом нефтяных масел. Учитывая, что при работе мащин и механизмов имеет место как граничная (при пуске, остановке), так и гидродинамическая (в рабочих условиях, например, гидравлической системы) смазка, к большинству индустриальных масел предъявляют более жесткие требования по показателю износа, чем к маслам без присадок. Для предотвращения износа и заедания в масло вводят соответствующие присадки, которые на поверхности трения при определенных температурах создают защитные пленки. [c.267]
Защитными свойствами обладают оксидные пленки со структурой а-корунда, так как они утрачивают способность гидратироваться. А12О3 — а-корунд используется как абразивный материал ввиду высокой твердости кристаллов. Из специально приготовленного корунда делают пластинки для резцов, обрабатывающих металл. Чистый А12О3 используется для изготовления керамических материалов. [c.409]
Водоэмульсионные ПИНС широко используют для дополнительной защиты неповрежденных и поврежденных битумных мастик, изоляционных продуктов, грунтовок, лаков и красок (табл. 34, 35). Эмульсолы (НГЛ-205), неингибированные восковые составы на водной основе (ЗВВД), моюще-консервационные жидкости (Олинол) не эффективны при дополнительной защите ими битумной мастики (БМП-1) или лакокрасочного материала (НЦ-125). Более того, в динамических условиях при испытаниях по метору ТОНЭР (мойка машин, гидроабразивный и абразивный износы) продукты такого типа способны разрушать защитные изоляционные материалы (см. табл. 35). [c.218]
Основной областью применения полиэфирных смол является производство лаков и эмалей. Лишь в небольшом количестве они используются для производства пластмасс, в особенности электроизоляционного материала — миканита, являющегося слоистым пластиком на основе слюды и полиэфирной смолы. Эти смолы находят применение также в производстве граммофонных пластинок, линолеума, клеенки, а также цемента для цоколей электроламп. Высокая клеящая способность полиэфирных смол обусловливает их применение в качестве клеящих материалов, в частности в производстве абразивных инструментов. При взаимодействии терефталевой кислоты [c.144]
Способность к самозатачиванию является необходимым свойством абразивного материала, которое может проявляться только в том случае, если материал наряду с твердостью и определенной прочностью обладает хрупкостью, т. е. способностью разрушаться без пластических деформаций. Сочетанием таких свойств обладают только минералы, что и обусловливает их применение в качестве абразивных материалов. Необходимость самозатачивания абразивного инструмента обусловливает также определенный комплекс свойств связки, применяемой для скрепления зерен между собой. Связующее вещество должно обладать как определенной собственной прочностью (когезией) и клеящей способностью (адгезией),- так и х,рупкостью, чтобы обеспечить выкрашивание затупившихся зерен из абразивного инструмента. [c.335]
Сыпучие материалы характеризуются объемным (или насыпным) весом, т. е. весом единицы объема, который различен для свободно насыпанного и уплотненного материала плотностью углом естественного откоса, образующимся при свободном ссыпании материала коэффициентом трения покоя и при движении по дереву, стали, бетону, обрезиненной ленте и т. п. влажностью, гигроскопичностью, абразивностью, липкостью, способностью к возбуждению зарядов статического тричества и образованию искры и пр. [c.341]
Основным условием правильной работы абразивного инструмента является его способность самозатачиваться, т. е. способность затупившихся зерен выкрашиваться в процессе резания из связующей массы, в результате чего в работу вступают новые зерна. Если притупившиеся зерна не выкрашиваются из связки, то процесс резания постепенно прекращается, поры шлифовального круга забиваются мелкой стружкой, благодаря чему его поверхность засаливается , а обрабатываемое излелие быстро нагревается и на нем появляются прижоги. Совершенно очевидно, что чем тверже обрабатываемый материал, тем быстрее затупляются зерна и тем скорее они должны выкрашиваться из связки. Поэтому при обработке мягких металлов (например, конструкционных сталей) выбирают более твердые шлифовальные круги, так как их зерна будут затупляться сравнительно медленно, а при обработке твердых металлов (например, закаленной стали) выбирают более мягкие шлифовальные круги. [c.53]
За рубежом также широко применяют шлюзовые затворы. Так, западногерманская фирма Мёллер Moller) выпускает затворы различных размеров с производительностью до 500 м /ч, и в зависимости от свойств транспортируемого материала различных исполнений. Обычное исполнение рассчитано на рабочие температуры до +200 °С, а для регулировки в процессе эксплуатации пропускной способности затвор оснащают регулируемым приводом. Для транспортирования абразивных сыпучих материалов делают затвор с барабаном, оборудованным регулируемыми износостойкими уплотнительными элементами и со сменой износостойкой гильзой корпуса, подвергнутой твердому никелированию. Для транспортирования гранулированного материала затвор производят с регулирующим устройством, которое подает материал [c.252]
Для отощения коксовых шихт можно применять также коксовую мелочь, которая обладает чрезвычайно большой отоша-ющей способностью. Использование коксовой мелочи (как и антрацита) весьма заманчиво, так как можно использовать готовый малоценный материал. Однако применение коксовой мелочи встречает большие трудности, поскольку она весьма трудно поддается тонкому дроблению, благодаря ее высокой абразивности дробилки быстро изнашиваются, ее необходимо предварительно сушить, она обладает высоким содержанием золы. Поэтому коксовая мелочь в производстве не может полностью вытеснить полукокс как отощающий компонент в коксовых шихтах. [c.466]
Выбор абразива для абразивоструйной обработки
Выбирая абразивный материал для пескоструйного аппарата, нужно знать, что от его выбора будет зависеть качество, скорость и цена за выполненную работу. Выбор современных материалов довольно большой, однако для каждой задачи следует подбирать определенный абразив и составляющие пескоструйной смеси, что обеспечит максимальную скорость, качество и экономичность очистки. Кроме этого, расход абразива для очистки зависит от компрессора, пескоструйного оборудования, опыта мастера и от условий работы.
Существует очень много видов абразива, поэтому следует остановиться на тех, которые используются в нашей стране. Мы привели в таблице конкретные цифры, однако они являются не самыми точными, так как главные характеристики абразива зависят от его производства, места добычи и от других показателей. Данная таблица поможет сравнить материалы по главным параметрам и сделать правильный выбор, учитывая поставленные задачи.
Таблица сравнения абразивов для пескоструйной очистки
Кварцевый песок |
Купершлак, никельшлак |
Пластиковые абразивы |
Стеклянная дробь |
Гарнет (гранатовый песок) |
Корунд (оксид алюминия) |
Чугунная колотая дробь |
Стальная колотая дробь |
|
Твердость |
5 — 7 Moohs |
6 — 7 Moohs |
4 Moohs |
6 Moohs |
8 Moohs |
8 — 9 Moohs |
50-62 HRC |
40-65 HRC |
Абразивная способность |
Низкая |
Средняя |
Низкая |
Средняя |
Высокая |
Высокая |
Высокая |
Высокая |
Хрупкость |
Высокая |
Высокая |
Низкая |
Средняя |
Средняя |
Средняя |
Низкая |
Низкая |
Пылеобразование |
Очень высокое |
Высокое |
Минимальное |
Среднее |
Среднее |
Среднее |
Среднее |
Низкое |
Кварц в свободной форме |
Более 1% |
Менее 1% |
Отсутствует |
Более 1% |
Менее 1% |
Отсутствует |
Отсутствует |
Отсутствует |
Возможность повторного использования (рекуперации), циклов |
— |
1 — 2 |
8 — 12 |
5 — 35 |
5 — 7 |
5 — 7 |
8 — 10 |
50 — 100 |
Средний расход на очистку 1м2 до степени Sa 2 ½ |
60 — 110 кг |
30 — 75 кг |
—* |
—* |
3 — 7 кг |
3 — 10 кг |
5 — 10 кг |
0,2 — 0,6 кг |
Скорость очистки |
Низкая |
Средняя |
Средняя |
Средняя |
Высокая |
Очень высокая |
Высокая |
Высокая |
Стоимость |
Низкая |
Средняя |
Высокая |
Высокая |
Высокая |
|||
Себестоимость очистки |
Высокая |
Средняя |
Высокая |
Низкая |
Низкая |
Низкая |
Низкая |
Минимальная |
Условия применение |
Очистка в закрытых камерах или с системами подавления пыли |
Открытая очистка |
Очистка с использованием оборудования с замкнутым циклом: камеры, кабины, беспылевые пескоструйные аппараты |
* Обработка данными абразивами не регламентируется стандартом ISO 8501.
Кварцевый песок
Данный строительный материал остается самым распространенным и востребованным абразивом, так как отличается невысокой стоимостью и доступностью. Технология работы и оборудование получило название пескоструйный аппарат и пескоструйная очистка. Для пескоструйных работ содержание кварца довольно ограничено, так как после разрушения его частиц образуется мелкокристаллическая пыль, которая очень вредная для здоровья человека. И если работник долго работает с данным материалом, то у него может развиться такое серьезное заболевание, как силикоз. Во многих странах мира использование кварца в свободной форме с содержанием более 1% строго запрещено законом.
Кварцевый песок
Разрешается использовать кварцевый песок для выполнения пескоструйной очистки поверхностей только при таком оборудовании, где предусмотрена система пылеподавления. Поэтому, если необходимо работать с песком, то нужно следить за тем, чтобы в рабочей зоне не находилось посторонних людей. Довольно часто кварцевый песок используют для очистки каменных или бетонных поверхностей, где предусмотрена система пылеподавления. При пескоструйной очистке идет самый большой расход кварцевого песка, что связано с его минералогическими характеристиками. Подсчет необходимого количества песка для работы пескоструйки довольно затруднительный без его предварительной подготовки, куда входит: промывка, сушка и фракционирование.
Купершлак и никельшлак
Если сравнить купершлак и никельшлак, то оба они являются абразивными порошками, которые получают путем переработки шлаков при никелеплавильном и медеплавильном производстве. Если сравнивать песок и данные материалы, то они содержат меньше 1% кварца, поэтому их используют для выполнения открытой пескоструйной очистки. Они имеют высокую абразивную способность, динамическую прочность частиц и твердость, поэтому отличаются низким пылеобразованием и подходят для повторного использования, что отсутствует у песка.
|
|
||
Купершлак (купрошлак) |
Никельшлак |
Отличия никельшлака и купершлака
Благодаря высокой твердости и динамической прочности частиц никельшлак можно использовать до 3 раз, несмотря на это уровень его запыленности ниже, чем имеет купершлак. Однако его удельная плотность частиц меньше, поэтому энергия действия на поверхность ниже, чем дает купершлак. В среднем расход абразивного порошка на 1 м2 потребует около 30-75 кг м2, но если подобрать правильное оборудование, объем сжатого воздуха и давление, то расход сокращается до 15-20 кг м2. Приобрести купершлак и никельшлак в России легко, так как в стране работает несколько крупных предприятий по их производству, которые поставляют материал практически в каждый регион страны.
Пластиковые абразивы (пластиковая дробь)
Этот материал выпускают в виде пластиковой дроби, которая относится к группе мягких абразивов и используется для деликатной обработки изделий, получившей название – мягкий бластинг. Довольно часто данный материал используется для обработки пластмассы, сплавов, стекла, дерева, композиционных материалов, керамики. Абразив из пластика – это идеальный вариант для реставрации и очистки спортивных лодок, автомобилей, яхт или катеров. Его часто используют для удаления старого порошкового покрытия, так как он не способен повредить подложку.
|
|
||
Пластиковый абразив (меламиновая смола) |
Пластиковый абразив (амино-альдегидная смола) |
На производстве пластиковые абразивы для максимальной эффективности работы используются с дробеметным и дробеструйным оборудованием, которые выполняют финишную обработку алюминиевых деталей, удаляя все дефекты литья и заусенцы. Самая первая отрасль, которая по достоинству оценила абразивы этого вида, была авиационная промышленность. Сегодня пластиковые абразивы охотно применяют в сервисных и клининговых компаниях, которые работают с антикварными изделиями, памятниками архитектуры или дорогими раритетными автомобилями.
Так как абразив состоит из мягкого пластика, то отличается минимальной агрессивностью. В нашей стране он не используется так широко, как за границей. Препятствием в этом служит его высокая цена и небольшое количество заказов, которые требуют мягкой, деликатной очистки. Помимо этого, не каждая компания имеет специальное оборудование для работы с мягким бластингом.
Стеклянная дробь (стеклянные шарики)
Круглые, стеклянные шарики – это качественный промышленный абразив, который зачастую используют для финишной обработки изделий, например, для сатинирования, матирования, термической и финишной обработки. Очистка поверхности при помощи стеклянных шариков относится к наиболее щадящим способам обработки, так как здесь исключается чрезмерное удаление обрабатываемого материала, а также любые нежелательные изменения цвета.
Стеклянная дробь (стеклянные шарики) |
Обработка поверхности стеклянной дробью позволяет получить наклеп, снять напряжение и подготовить поверхность к дальнейшей полировке, если требуется нанести на нее гальваническое покрытие.
Благодаря своим уникальным свойствам стеклянная дробь часто используется для обработки сложных высокоточных деталей в приборостроении, машиностроении, часовой промышленности и в оптике. Данный абразивный материал – это идеальный вариант для обработки нержавеющей стали. Довольно часто к абразиву предъявляют высокие требования по намагничиванию и металлизации, стеклянная дробь отвечает данным параметрам.
А еще этот материал отличается высокой экологичностью, поэтому его очень часто используют в пищевой и фармацевтической промышленности, а также при изготовлении медицинских инструментов и посуды. Хорошая стеклянная дробь отличается высоким ресурсом работы, поэтому ее можно использовать до 35 раз. Этот материал разрешается использовать в замкнутой системе очистки, например, в кабинах и дробеструйных камерах.
Гарнет (гранатовый песок)
Гарнет или же гранатовый песок относится к группе абразивных порошков минерального происхождения, который производят в Индии, Австралии, ЮАР, Чехии.
|
|
||
Гарнет (гранатовый абразивный песок) |
Благодаря работе дистрибьюторов его можно купить и в нашей стране. По своим техническим характеристикам гарнетпревосходит кварцевый песок, никельшлак и купершлак. Он отличается высокой прочностью частиц и твердостью, поэтому может многократно использоваться для пескоструйной очистки. Этот материал в пескоструйке очень часто применяется для аппарата беспылевой очистки, в системе или камере рекуперации абразива.
Электрокорунд (корунд, оксид алюминия)
Оксид алюминия, корунд или же электрокорунд – это супертвердый материал, обладающий высокой абразивной способностью. Он состоит из оксида алюминия и небольшого количества примесей. Его твердость немного ниже, чем у алмаза, а зерна отличаются наличием острых режущих кромок, которые в процессе работы самозатачиваются. Благодаря его высокой прочности корунд можно многократно использовать в качестве абразива, а его высокая абразивная способность увеличивает скорость очистки. Именно поэтому данный материал является наиболее эффективным для проведения пескоструйной обработки различных поверхностей.
Электрокорунд белый 25А |
Электрокорунд изготавливается двумя способами: регенерацией или бывает первично произведенным, в первом случае его получают путем восстановления боя абразивных кругов. Безусловно, свойства первичного электрокорунда выше, чем у восстановленного, поэтому в его составе могут присутствовать загрязняющие примеси в небольшом количестве. Регенерированный корунд имеет прекрасные эксплуатационные характеристики и эффективно применяется для выполнения целого перечня работ. Например, для пескоструйной обработки стеклянных, металлических, каменных или керамических поверхностей. А еще он считается самым востребованным материалом для обработки нержавеющей стали, алюминия, сплавов и цветных металлов.
Однако для обработки нержавеющей стали желательно не брать регенерированный электрокорунд, ведь его загрязняющие частицы приводят к коррозии обрабатываемой поверхности. Для нержавеющей стали правильно использовать специальный электрокорунд белый 25А. Для работы с камнем, стеклом, керамикой или черным металлом чаще выбирают электрокорунд 14А или восстановленный 14А и 25А.
Так как данный абразивный материал имеет возможность повторного использования, а также не высокую стоимость, то его применении является экономически оправданным и эффективным, если используется оборудовании с замкнутым циклом вращения абразива. Например, сюда входят обитаемые камеры, пескоструйные кабины или беспылевые пескоструйные аппараты.
Техническая дробь (чугунная и стальная дробь)
К технической дроби относятся: стальная и чугунная дробь, по форме они бывают рубленными, колотыми или литыми, изготавливают этот материал из сталей или чугуна с разными свойствами. Литая дробь имеет сферическую форму, а колотая – остроугольную.
Стальная и чугунная дробь используется для работы дробеметной и дробеструйной машины при обработке различных поверхностей, которые требуют профилирования. Мелкие частицы колотой дроби имеют неправильную многогранную форму и высокую твердость, что увеличивает их абразивную способность. Металлическая поверхность, обработанная чугунной или стальной дробью, получает высокие адгезионные свойства и отличное сцепление с защитным покрытием, которое в дальнейшем будет наноситься.
|
|
||
Дробь стальная колотая (ДСК) |
Дробь чугунная колотая (ДЧК) |
Если сравнить чугунную стальную и колотую дробь, то первая имеет высокую твердость, однако достаточно хрупкая, поэтому повторно может использовать меньше раз, нежели стальная колотая дробь. Качество технической дроби регулируется по ГОСТУ 11964-81. По документу, колотые дроби делятся на три категории: стальная колотая улучшенная, стальная и чугунная. Если используется улучшенная колотая дробь, то она отличается максимальными показателями по прочности, что было обеспечено, благодаря дополнительной термической обработке, которую выполняют на производстве. Кроме этого, она получила увеличенный ресурс эксплуатации.
|
|
||
Дробь стальная литая (ДСЛ) |
Дробь чугунная литая (ДЧЛ) |
Главная область применения колотой технической дроби – это очистка тяжелого, среднего и мелкого литья, а также очистка проката любых марок стали, включая высокопрочные виды. Помимо этого, она незаменима для подготовки металлической поверхности под покраску, нанесения гальванического покрытия.
Стальные и чугунные литые дроби широко используются, если необходимо выполнить дробеметное и дробеструйное упрочнение поверхностей, очистку проката от низкоуглеродистых и углеродистых или легированных сталей от окалины, деталей машиностроения, подготовки поверхностей до нанесения гальванического покрытия. Профиль поверхности после тщательной обработки литой дробью приобретает форму правильных полусферических впадин.
На сегодня известно несколько видов технической литой дроби: первая – это обычная чугунная литая дробь, которая маркируется буквами – ДЧЛ. Второй тип – это стальная литая дробь, ее название – ДСЛ, а к третьему относят улучшенную стальную дробь, которую ставят буквами – ДСЛУ. Последняя марка отличается от других высокими эксплуатационными свойствами и большим ресурсом работы.
Нержавеющая дробь
Она используется для дробеметной и дробеструйной обработки поверхности из нержавеющей стали, титана, алюминия, бронзы, латуни, меди и других цветных металлов или сплавов, а также для качественной очистки изделий из гранита, бетона, мрамора. Металлические поверхности, которые были обработаны нержавеющей дробью, приобретают дополнительную защиту от процессов коррозии. Если сравнивать другие материалы, то нержавеющая дробь остается самым дорогим и высококачественным абразивом, который отличается максимальным ресурсом службы.
Так как технические дроби получили высокие эксплуатационные характеристики, то они являются самым экономичным и эффективным абразивом, выполняющим большой перечень работ. Они имеют возможность для повторного использования, что насчитается до нескольких сотен раз. При дробеструйной обработке расход данного материала меньше, нежели при использовании других типов абразивов. Кроме этого, качество обработанной поверхности тоже выше. Расход дроби зависит от типа и марки применяемого материала, а также от состояния обрабатываемой поверхности изделия. Ко всему прочему расход нержавеющей дроби на один квадратный метр минимальный.
Техническая нержавеющая дробь используется в условиях, когда удается собрать отработанный абразив, очистить его и повторно вернуть для работы. Так как дробь можно многократно использовать, то расходы на обработку поверхностей существенно сокращаются. Что касается покупки кабины и строительства дробеструйной камеры, то все это быстро компенсируется, благодаря минимальной себестоимости выполненных работ и увеличению ресурса оборудования.
Абразивные материалы
Абразивные материалы
Абразивные материалы — это преимущественно материалы высокой твердости, природные и искусственные, применяемые для обработки менее твердых материалов. Используются в виде зерна или порошков в свободном виде или в виде изготовленных из них инструментов.
Искусственные абразивные материалы отличаются большей стабильностью физико-механических свойств по сравнению с природными. В настоящее время искусственные абразивные материалы практически полностью вытеснили в промышленности природные. К искусственным абразивным материалам относятся алмаз синтетический, карбид бора, карбид кремния, техническое стекло, эльбор (борозон), электрокорунд и др.
Алмаз синтетический (Маркировка — АСВ, АСР) — абразивный материал, получаемый синтезом из графита при высоких давлениях и температуре. Свойства и применение аналогично природному. При изготовлении инструмента основной характеристикой является содержание алмаза в алмазоносном слое или концентрация алмаза. 100% концентрации соответствует его содержание в количестве 4,39 карата в 1 см.куб. алмазоносного слоя. Выпускают инструмент с концентрацией 50, 75, 100%, по заказу — 25, 125 и 150 %.
Карбид бора (Маркировка — карбид бора) — абразивный материал, получаемый в электрических печах из борной кислоты (В2O3) и нефтяного кокса. Твердость по МООСу — 9,32; микротвердость — 4000-4500 кгс/мм.кв.; плотность 2,48-2,52 кгс/см.кв.. Применяется в виде порошков и паст для доводки режущего инструмента из карбидовольфрамовых и карбидотитановых сплавов, а также, в атомной промышленности.
Карбид кремния (Маркировка 64С — 62С и 55С — 52С) — абразивный материал, представляющий собой химическое соединение кремния с углеродом (SiC), твердость по МООСу — 9,1; микротвердость 3300-3600 кгс/мм. кв., получаемых в электрических печах из кварца и нефтяного кокса при температуре 1500-2300 С°. Различают зеленый и черный карбид кремния. Зеленый карбид кремния содержит меньше примесей, более хрупок, более высокая абразивная способность. Широко используется для всех видов шлифовального инструмента.
Техническое стекло (Маркировка — 71 F) — бой листового и бутылочного стекла, после дробления и рассева получают шлифзерно и шлифпорошки, применяемые для изготовления шлифовальной шкурки для обработки дерева.
Эльбор (борозон) — кубический нитрид бора. Получают из гексагонального нитрида бора при высоких давлениях и температуре. Плотность 3,45-3,54 г/см.куб., микротвердость 8000-10000 кгс/мм.кв.. Разновидность кубического нитрида бора, разработанная за рубежом, имеет торговую марку — борозон. Используется в промышленности достаточно широко, в основном как аналог алмазного инструмента, также на режущие пластинки для резцов, буров, сверл.
Электрокорунд — абразивный материал, состоящий из корунда (Аl2O3) и небольшого количества примесей. Промышленность производит несколько разновидностей электрокорунда, в том числе нормальный, белый, хромистый, титанистый, циркониевый, моно- и сферокорунд.
Наиболее широко используются нормальный электрокорунд (Маркировка — 16А — 12А), получаемый в электрических печах из бокситов, (микротвердость 1900-2000 кгс/мм2, плотность 3,85-3,95 г/см.куб..
Белый электрокорунд (Маркировка — 25А — 22А) — получаемый в электрических печах расплавлением глинозёма (микротвердость 2000-2100, плотность 3,9-4,00 г/см.куб.).
Корунд циркониевый (Маркировка — 38А) — разновидность электрокорунда с примесью окиси циркония (от 10 до 45%) для тяжелых обдирочных операций (микротвердость 2300-2400 кгс/мм.кв., плотность 4,05-4,15 г/см.куб.).
Из этих видов электрокорундов производится до 80-90% абразивного инструмента самого разного назначения. В специальных инструментах используется электрокорунд хромистый и титанистый (Маркировка — 34А — 32А и 37А) имеющие отличные от белого электрокорунда свойства благодаря соответствующим примесям.
Монокорунд (Маркировка 45А — 43А) — шлифзерно представлено монокристаллами в отличие от нормального электрокорунда, имеющего поликристаллическую структуру, что обеспечивает высокую режущую способность, но и высокую стоимость этого материала.
Сферокунд (Маркировка — ЭС) — абразивный материал в виде полых корундовых сфер, используется для обработки мягких и вязких материалов: кожи, резины, пластмассы, цветных металлов и т.д.
К природным (естественным) абразивным материалам, имеющим промышленное значение, относятся алмаз, гранат, корунд, кремень и др.
Алмаз (Маркировка — А) — минерал, состоящий из кристаллического углерода с кубической структурой решетки. Обладает наибольшей твердостью из всех известных абразивных материалов (твердость по МООСу 10,0; микротвердость 8600-10000 кгс/мм. кв.). До 80% добываемых алмазов используется на технические цели (20% идут на изготовление ювелирных изделий). Масса алмаза определяется в каратах. Один карат равен 0,205 гр. Из технических алмазов изготавливаются инструменты для шлифования, доводки и резки различных материалов, для бурения горных пород, обработки камня, сверления стекла и т.д.
Гранат (Маркировка — 92 Е) — минерал, представляющий собой соединение алюминия, железа, хрома, кальция, магния и марганца с кремнекислотой. В зависимости от примесей гранат бывает темно-красного (пироп), красного (альмандин), оранжево-желтого (спессартин), буро-красного, черного (андрадит) или изумрудно-зеленого (уваровит) цветов. Микротвердость 1300-1650 г/см.куб., твердость по МООСу 6,5 -7,5;плотность 3,5 -4,2 кгс/см.кв.. Получают шлифзерно и микро порошки. Первое используют для изготовления шлифовальной шкурки, применяемой при обработке дерева, пластмасс, кожи. Вторые — в свободном виде при обработке стекла.
Корунд — черная порода, состоящая в основном из кристаллической окиси алюминия (Аl2O3) с небольшой примесью кварца и других минералов. Цвет зависит от примесей: красный, бурый, желтый, синий, серый или белый. Плотность 3,9-4,1 г/см.куб., микротвердость 1900-220 кгс/мм.кв; твердость по МООСу — 9,0. Изготавливают шлифпорошки для производства абразивного инструмента и микропорошки для полировки стекла и металла.
Кремень (Маркировка — 81 Кр) — плотная горная порода, состоящая из кремнезёма и микроскопических зерен кварца и примесей. Цвет от светло-серого до черного. Микротвердость 1000-1100 кгс/мм.кв.; плотность 2,5-2,6 г/см.куб.. Применяется для изготовления шлифовальной шкурки, идущей для обработки кожи, эбонита, дерева.
Наждак — тонкозернистая горная порода, состоящая из корунда (до 30%) магнетита с примесью гематита и кварца. Используется для шлифования свободным зерном. Можно отнести к древнейшим абразивным материалам, используемых человеком, в частности, для мельничных жерновов.
Виды абразивного материала | Центр Пескоструйной Обработки в Волжском
Купершлак и никельшлак
Купершлак и никельшлак — абразивные порошки, получаемые в результате переработки шлаков медеплавильного и никелеплавильного производств. В отличии от песка содержат менее 1% кварца в свободном виде и могут применяться для открытой пескоструйной очистки. Обладают более высокой абразивной способностью, твердостью и динамической прочностью частиц, в следствии этого — более низким пылеобразованием и возможностью повторного использования. Удельная плотность частиц купершлака и никельшлака выше, чем у песка, соответственно выше и масса частиц, что еще в большей степени увеличивает эффективность этих абразивов.
Купершлак (купрошлак) | Никельшлак |
Электрокорунд (корунд, диоксид алюминия)
Электрокорунд — это сверхтвердый материал с высокой абразивной способностью, состоящий из оксида алюминия Al2O3 (до 99%) с незначительным содержанием примесей. Твердость электрокорунда уступает алмазу всего на 1 единицу по шкале Мооса, а зерна имеют острые режущие кромки и способны самозатачиваться. Высокие прочностные характеристики допускают многократное повторное использование абразива, а высокая абразивная способность существенно повышает скорость очистки. Все эти свойства делают электрокорунд одним из наиболее эффективных абразивных материалов для пескоструйной обработки.
Электрокорунд нормальный 14А | Электрокорунд белый 25А | Электрокорунд хромотитанистый 93А |
Электрокорунд может быть как первично произведенным (выплавленым), так и регенерированным: восстановленным из боя абразивных кругов. По своим свойствам восстановленный электрокорунд уступает первичному и может содержать незначительное количество загрязняющих примесей, но при этом регенерированный электрокорунд сохраняет достаточно высокие эксплуатационные характеристки и может эффективно применяться для широкого круга задач, а его стоимость существенно ниже.
Электрокорунд широко применяется для пескоструйной обработки металлических, стеклянных, керамических и каменных поверхностей. А также является одним из наиболее предпочтительных абразивов для обработки алюминия, нержавеющей стали, цветных металлов и ряда сплавов.
Для обработки нержавеющей стали не рекомендуется использовать регенерированный электрокорунд, так как загрязняющие его частицы могут привести в последствии к корродированию обрабатываемой поверхности. В этом случае наиболее целесообразно будет использовать электрокорунд белый 25А.
Для обработки стекла, камня, черного металла и керамики наиболее предпочтителен электрокорунд нормальный 14А, а также востановленный электрокорунд 25А.
Возможность повторного использования (рекуперации) электрокорунда и высокая стоимость этого абразива делают его применение наиболее эффективным и экономически оправданным при использовании оборудования замкнутого цикла обращения абразива, такого как пескоструйные кабины, обитаемые камеры, беспылевые пескоструйные аппараты.
Техническая дробь (чугунная и стальная дробь)
Технические дроби бывают колотые, рубленные и литые и изготавливаются из чугунов или сталей с различными свойствами. Колотые дроби имеют остроугольную форму частиц, литые — сферическую.
Чугунные и стальные колотые дроби используются для дробеструйной и дробеметной обработки поверхностей, требующих профилирования (нанесения насечки) GRIT. Частицы колотой дроби обладают высокой твердостью и имеют форму неправильного многогранника с остроугольными краями, что обеспечивает им высокую абразивную способность. Обработанная стальной или чугунной колотой дробью металлическая поверхность обладает высокими адгезионными свойствами и обеспечивает хорошее сцепление с наносимыми защитными покрытиями.
Чугунная колотая дробь отличается от стальной более высокой твердостью, но при этом она более хрупкая, поэтому ее ресурс повторного применения зачастую в несколько раз уступает высококачественной стальной колотой дроби.
Дробь стальная колотая (ДСК) | Дробь чугунная колотая (ДЧК) |
Качество технической дроби и рекомендации по применению регулирует ГОСТ 11964-81. Согласно ему колотые дроби подразделяются на дробь чугунную колотую (ДЧК), дробь стальную колотую (ДСК) и дробь стальную колотую улучшенную (ДСКУ). Улучшенная колотая дробь отличается более высокими прочностными характеристиками, приобретаемыми за счет дополнительной термической обработке на производстве, и имеет повышенный ресурс эксплуатации.
Основными сферами применения технической колотой дроби являются очистка мелкого, среднего и тяжелого литья, очистка проката из всех марок стали, в том числе и высокопрочных, подготовка металлических изделий под окаску и нанесение гальванических покрытий, а дробь ДСКУ используется также для упрочнения торсионных валов, рессорных листов и витых пружин.
Чугунные и стальные литые дроби используются для дробеструйного и дробеметного упрочнения поверхностей (наклепа), очистки проката из углеродистых, низкоуглеродистых и легированных сталей от окалины, литья от формовочных смесей, деталей машиностроения после термической обработки и подготовки поверхностей перед окраской и нанесением гальванических покрытий. Профиль поверхности после обработки литой дробью имеет форму полусферических впадин.
Дробь стальная литая (ДСЛ) | Дробь чугунная литая (ДЧЛ) |
Существуют следующие типы технической литой дроби: ДЧЛ (дробь чугунная литая) и ДСЛ (дробь стальная литая), ДЧЛУ (дробь чугунная литая улучшенная) и ДСЛУ (дробь стальная литая улучшенная). Улучшенные марки литой дроби отличаются более высокими эксплуатационными характеристками и ресурсом. Качество литой дроби и рекомендации по областям ее применения регламентируются ГОСТом 11964-81.
Нержавеющая дробь используется для дробеструйной и дробеметной обработки нержавеющей стали, алюминия, цинка, титана, меди, латуни, бронзы и других цветных металлов и специальных сплавов, а также для очистки изделий из бетона, гранита, мрамора. Обработанные нержавеющей дробью металлические поверхности получают дополнительную защиту от коррозии. Нержавеющая дробь — высококачественный и дорогой абразив, имеющий высокий ресурс службы.
Высокие эксплуатационные характеристки делают технические дроби одним из наиболее эффективных и экономичных абразивов в широком спектре задач. Высококачественные дроби имеют ресурс повторного использования до нескольких сотен циклов. Расход дроби при дробеструйной обработке существенно ниже других абразивов, а качество обработанной поверхности в большинстве случаев лучше. Нормы расхода дроби зависят от марки и типа используемого материала и характера обрабатываемой поверхности. Но можно с уверенностью сказать, что расход дроби на 1м2 при дробеструйной очистке в подавляющем большинстве случаев будет минимальным.
Техническую дробь рекомендуется использовать в условиях, позволяющих сбор отработанного абразива, его очистку и возврата для повторного применения. Возможность многократного использования дроби позволяет существенно сократить расходы на обработку поверхностей, а расходы на строительство дробеструйной камеры или покупку кабины быстро компенсируются минимальной себестоимостью производимых работ и увеличенным ресурсом оборудования.
Пожалуйста, расскажите о нас:
Шлифовальное зерно: виды, свойства и применение.
Шлифовальное зерно: виды, свойства и применение.
Что такое абразивные материалы
Абразивные материалы — это мелкозернистые или порошковые химические соединения элементов. Также будет верным название “шлифовальное зерно” или “шлифовальный материал”. Абразивы характеризуются твердостью и имеют режущие грани. Входят в состав жесткого и гибкого шлифовального инструмента, полировальных паст.
Виды абразивных материалов
Абразивные материалы разделяют на природные и искусственные.
Среди природных шлифматериалов выделяют:
- Алмаз — минерал, состоящий из чистого углерода. Встречается в виде кристаллов различной формы;
- Корунд — горная порода, до 95 % состоит из кристаллической окиси алюминия.
Зерна его очень тверды и имеют острые грани;
- Наждак — мелкозернистый корунд-порошок из смеси зерен корунда с другими минералами — магнитным железняком, гематитом, полевым шпатом;
- Кварц — минерал, состоящий из кристаллического кремнезема. Разновидностью является кварцевый песок;
- Гранат — соединение алюминия, железа, хрома, кальция, магния, марганца с кремнекислотой;
- Пемза — излившаяся вулканическая порода из кремнезема и глинозема.
Наиболее распространенные искусственные (синтетические) абразивные материалы это:
- Электрокорунд нормальный (марки 12А, 13А, 14А 15А и 16А) — сплав оксида алюминия AL2O3, содержит до 95 % окиси алюминия.
- Электрокорунд белый (марки 22А, 23А, 24А и 25А) получается при плавке технического глинозема, содержит до 99 % корунда.
Относительно электрокорунда нормального обладает повышенной твердостью и более острыми кромками зерна.
- Электрокорунд керамический получают путем спекания порошка Al2O3 с водой и различными вспомогательными веществами.
- Электрокорунд циркониевый (38А) состоит из диоксида циркония и оксида алюминия, имеет мелкую кристаллическую структуру, отличается высокой прочностью. Стойкость абразивного инструмента из электрокорунда циркониевого в 10 — 40 раз выше, чем аналогичного инструмента из электрокорунда нормального.
- Монокорунд (марки 43А, 44А и 45А) — это сплав боксита с сернистым железом, кристаллической окиси алюминия в нем не менее 96%.
- Электрокорунд титанистый (марка 37А) представитель легированных электрокорундов, где корунд выплавляется с добавлением окиси титана. В его составе от 91% до 98% AL2O3 (чаще – не менее 97%) и 2% оксида титана.
- Электрокорунд хромистый (технический рубин, электрорубин) (марки 32А, 33А, 34А) — сплав глинозема и оксида хрома. Электрорубин содержится от 91% до 98% AL2O3.
- Карбид кремния (марок К38 и К39, К47 и К48) получают в результате взаимодействия кремнезема и углерода.
- Карбид бора — сплав борной кислоты с нефтяным или пековым коксом, сажей и др.
- Борсиликокарбид — соединение бора, кремния и углерода.
- Синтетический алмаз — сверхтвердый материал, полученный методом каталитического синтеза графита при высоких температурах.
Абразивные материалы подразделяют на группы:
- шлифзерно с зернистостью 200, 160, 125, 100, 80, 63, 50, 40, 32, 25, 20, 16 в сотых долях миллиметра;
- шлифпорошки с зернистостью 12, 30, 8, 6, 5, 4, 3 в сотых долях миллиметра;
- микропорошки М63, М50, М40, М20, M14, зернистость указывается в микрометрах;
- тонкие микропорошки М10, М7, М5, зернистость указывается в микрометрах.
Свойства абразивных материалов
Основные свойства абразивов — это твердость, прочность и способность к самозатачиванию или наличие острых краев. А главный показатель качества абразива — это его режущая способность. Она определяется массой снимаемого при шлифовании материала до затупления зерен.
По режущей способности абразивные материалы можно расположить в следующем порядке: алмаз, карбид бора, карбид кремния, электрокорунд, наждак.
В Таблице 1 мы представили сравнительную характеристику свойств и структуры популярных искусственных абразивных материалов.
Таблица 1. Свойства искусственных абразивных материалов
Тип абразивного материала | Твердость/Прочность | Структура | Свойства/ Изнашивание |
Карбид кремния | очень твердый/ менее прочный | кристаллический | |
Электрокорунд нормальный | твердый/ прочный | кристаллический/ неровный | |
Электрокорунд циркониевый | твердый/ очень прочный | кристаллический/ ровный | |
Электрокорунд керамический | твердый/ очень прочный | микрокристаллический |
Назначение абразивных зерен
В производстве гибкого шлифовального инструмента Белгородский абразивный завод используются только зерна из синтетических абразивных материалов:
- электрокорунд нормальный;
- электрокорунд белый;
- электрокорунд циркониевый;
- электрокорунд керамический;
- карбид кремния черный;
- электрокорунд компакт и карбид кремния компакт – представляют собой соединение зерен электрокорунда или карбида кремния, скрепленных между собой связующим.
Набор свойств определяет оптимальный выбор шлифзерна для обработки той или иной поверхности. В Таблице 2 приведены сферы применения абразивных материалов.
Таблица 2. Сферы применения абразивных материалов
Абразивные материал | Применение |
Электрокорунд нормальный | материалы с высоким пределом прочности на разрыв, таких как углеродистая сталь, сплавы, твердые породы древесины, лак. |
Электрокорунд белый | легированная и жаропрочная сталь, шпаклеванные и оштукатуренные поверхности |
Электрокорунд циркониевый | легированные и углеродистые стали, цветные металлы |
Электрокорунд керамический | легированные и углеродистые стали, цветные металлы |
Карбид кремния черный | алюминий, стекло, камень, керамика, титан и его сплавы, резина, полиуретаны, пластмассы, ДСП и МДФ плиты |
Электрокорунд компакт | нержавеющие, жаропрочные и конструкционные стали, безосколочное стекло, титановые сплавы |
Карбид кремния компакт | нержавеющие, жаропрочные и конструкционные стали, безосколочное стекло, титановые сплавы |
Шлифовальные материалы в сериях, выпускаемых ОАО «БАЗ»
Электрокорунд нормальный используется в качестве шлифовального материала при изготовлении шлифовальной шкурки следующих серий: 14А, КК, КР, КТ, KD, KX, KF, KM.
Электрокорунд белый в качестве абразива встречается в шлифовальных инструментах серии LP. Прозрачность зерна позволяет окрашивать его в яркие цвета.
Карбид кремния используется при изготовлении шлифшкурки и изделий из нее серий СК, СТ, СР, CX.
Электрокорунд циркониевый применяется в производстве шлифовального инструмента серий ZK, ZX, ZD.
Электрокорунд керамический используется при изготовлении гибкого шлифовального инструмента в сериях SX и SF.
Электрокорунд компакт в качестве шлифматериала применяется в серии RX, а карбид кремния компакт в серии MX.
В нашем каталоге Вы можете более детально познакомиться с гибким шлифовальным инструментом и, в зависимости от своих целей подобрать изделие, шлифматериал, зернистость.
За подробной консультацией обратитесь к менеджеру отдела продаж ОАО «БАЗ».
Рекомендованные статьи:
Состав и особенности применения наждачной бумаги
Зернистость шлифовальной шкурки
АБРАЗИВНЫЕ МАТЕРИАЛЫ — это 📕 что такое АБРАЗИВНЫЕ МАТЕРИАЛЫ
вещества высокой твёрдости для механической обработки металлов, керамических материалов, горных пород, минералов, стекла, дерева, кожи, резины и др. С конца 19 в. применяются искусственные А. м. (электрокорунд, карбид кремния, карбид бора, монокорунд, синтетический алмаз и др.), ранее использовались только естественные А. м. (кремень, наждак, гранат, пемза, корунд, алмаз).
Основные характеристики А. м.: твёрдость, прочность и вязкость; форма абразивного зерна; абразивная способность; зернистость.
Твёрдость А. м. определяется (Мн/м2) методом вдавливания алмазной пирамиды в поверхность испытуемого материала, (например, для кварца 11 000—11 300, электрокорунда 18 000—24 000, алмаза 84 250—100 000). Распространено определение твёрдости в кгс/мм2(1 кгс/мм2≈ 10 Мн/м2). С увеличением прочности А. м. улучшается сопротивляемость усилиям резания. Сопротивление А. м. сжатию в несколько раз больше, чем сопротивление растяжению и изгибу. Прочность А. м. на растяжение и сжатие снижается с повышением температуры шлифования.
Абразивное зерно — кристаллический осколок (кристаллит), реже монокристалл или агрегат, состоящий из множества мелких кристаллов (поликристалл). Режущая кромка зерна — ребро, образованное любой парой пересекающихся кристаллографических плоскостей. Зерно может иметь приблизительно равные размеры по высоте, ширине и толщине (изометрическая форма) или обладать мечевидной и пластинчатой формой, что определяется родом А. м. и степенью измельчения исходного зерна. Рациональна изометрическая или близкая к ней форма зерна, т. к. каждое зерно является резцом. Наименее выгодная форма — игольчатая. Зерно имеет несколько граней, образующих вершины с углами от 30 до 130° и с радиусами округлений у зёрен от 200 до 4 мкм. У зёрен синтетических алмазов углы и радиусы округлений меньше, чем у природных, поэтому возможно снимать тонкую стружку.
Абразивная способность характеризуется массой снимаемого при шлифовании материала до затупления зёрен. По абразивной способности А. м. располагаются в следующем порядке: алмаз, кубический нитрид бора, карбид кремния, монокорунд, электрокорунд, наждак, кремень. Абразивная способность зависит от вида шлифуемых материалов, режима работы, вязкости и прочности зёрен. Чем меньше в А. м. примесей, тем выше абразивная способность.
Зернистость характеризует размер и однородность зёрен А. м.; определяется она классификацией зёрен по линейным размерам методом ситового анализа, осаждением в жидкости или др. Номер зернистости устанавливается в соответствии с линейными размерами зерна основной фракции. Чем однороднее по форме и размеру зёрен А. м., тем выше его эксплуатационные качества. Зернистость А. м. регламентируется стандартом. Обработка с помощью А. м. характеризуется участием в резании одновременно большого числа случайно расположенных режущих граней зёрен. Твёрдость абразивного инструмента (См. Абразивный инструмент) позволяет применять высокие скорости резания, что в соединении с большим числом одновременно работающих лезвий обеспечивает достаточный объём снимаемого материала. С другой стороны, при помощи А. м. достигается наиболее тонкая обработка, например Доводка.
А. м. используются в виде зёрен, скрепленных связкой в различные по форме и назначению абразивные инструменты, или нанесёнными на гибкую основу (ткань, бумагу и др.) в виде шлифовальной шкурки, а также в несвязанном состоянии в виде порошков, паст и суспензий.
Лит.: Каменцев М.В., Искусственные абразивные материалы, М., 1950; Филоненко Н.Е., Лавров И.В., Абразивные инструменты и их эксплуатация, М., 1959.
Г. М. Ипполитов
Знай свои абразивы и сокращай сроки изготовления
Каждый абразивный продукт обладает уникальными качествами, которые делают его подходящим или неподходящим для определенных областей применения. Определение того, какие комбинации абразивного зерна и связки лучше всего подходят для ваших потребностей в чистовой обработке металла, является ключом к оптимизации рабочего процесса. Неправильный выбор расходных материалов может привести к тому, что производственный цех будет работать дольше, чтобы производить детали среднего качества.
Выберите лучшее зерно для своей работы
С введением десятков новых наполнителей и запатентованных связующих веществ руководители цехов, которым поручено выбирать абразивные круги, могут быть перегружены вариантами и выбирать то, с чем они знакомы.Знание качеств состава колеса может помочь в принятии этих решений. Начните со следующими характеристиками:
- Зерновая сыпучесть
- Твердость зерна
- Тип связки
Возможности абразива зависят от комбинации всех трех факторов, применяемых к конкретному материалу. Проведите повторную оценку абразивного кабинета в магазине, посмотрев непосредственно на зерна и связки, используемые в абразивном круге, чтобы определить, что лучше всего подходит для работы .
Разрушение и хрупкость
Каждое абразивное зерно обладает способностью самозатачиваться по мере разрушения.Такая скорость распада называется рыхлостью. Гранат является примером зерна с очень низкой рыхлостью. Его естественное разложение приводит к образованию большого количества пыли, что делает его правильным выбором для абразивоструйной очистки или гидроабразивной резки.
Более рыхлые зерна, такие как черный и зеленый карбид кремния, лучше подходят для шлифования и финишной обработки очень твердых материалов. Например, при удалении заусенцев с титановых деталей подойдет черный карбид кремния. Во время работы круга зерно ломается и обнажает новые острые кромки, что позволяет непрерывно резать и избегать ожогов поверхности.
Сочетание хрупкости с твердостью зерна
Совместное рассмотрение характеристик зерна даст вам лучшее представление об их возможностях. Зерна с высокой твердостью и резким естественным изломом создадут более агрессивное зерно. Если зерно недостаточно твердое для конкретной работы, вы можете слишком быстро проходить шлифовальные круги. Или наоборот, если зерно слишком агрессивное, вы можете снять больше металла, чем планировали, выбрасывая дорогие детали.
Твердость абразивных зерен оценивается по шкале твердости Мооса.Оценка 9 и выше считается очень твердой, большинство абразивных зерен соответствуют этому показателю. Тем не менее, разная степень рассыпчатости делает каждое зерно индивидуально подходящим для разных задач. Оксид алюминия, оксид циркония и керамический оксид алюминия имеют оценку 9, но:
- Оксид алюминия представляет собой прочное зерно с низкой хрупкостью. Но когда он разбивается, он обнажает острые края, что делает его рабочей лошадкой для работы с различными металлами.
- Циркониевый оксид алюминия имеет микроструктуру, которая позволяет этому зерну разламываться на более мелкие и острые края, чем у оксида алюминия, что делает его превосходным для тяжелого шлифования.
- Керамический оксид алюминия представляет собой микрокристаллическое зерно, что означает, что он состоит из миллионов более мелких кристаллов. Зерно ломается снова и снова в процессе измельчения, что делает его очень агрессивным зерном.
Каждое зерно и абразивный круг имеют уникальную твердость. Если вы сомневаетесь, обратитесь к документации производителя , чтобы узнать, используете ли вы лучшее зерно для работы.
Облигации для повышения производительности
Связка, используемая при производстве абразивного круга, оказывает заметное влияние на характеристики абразивного круга.Одно и то же абразивное зерно может действовать по-разному в зависимости от того, какую связку использовал производитель.
- Полимерные круги прочны и используются для грубого шлифования. Абразивное зерно смешивается с фенольной смолой для создания изделий из резиноида.
- Керамические круги прочные и жесткие, изготовлены из тонкоизмельченной глины и флюсов с добавлением абразивного зерна.
Стеклокерамические круги также могут иметь плохую ударопрочность.
- Абразивные круги из хлопкового волокна содержат абразивные зерна в нетканом хлопчатобумажном материале.По мере того, как хлопок изнашивается, круг постоянно показывает больше абразивных зерен, что обеспечивает равномерную отделку. Хлопковое волокно лучше всего известно благодаря контролируемому удалению металла.
- Унифицированные круги представляют собой рулонный материал, пропитанный абразивным зерном, объединенный в пластину из смолы. Они часто используются для удаления очень легкого металла.
Следующим шагом после рассмотрения каждого зерна и доступных вариантов связки является выбор наиболее подходящих вариантов и начало испытаний.Если вы потратите время на подбор правильного абразива для конкретных задач, это может значительно повысить производительность
Многоцелевые абразивные круги
Слишком быстрая или слишком частая замена инструмента может быть пустой тратой времени и энергии для операторов.
Металлисты, от трубомонтажников до машинистов аэрокосмической отрасли, следуют тренду и обращаются к абразивным кругам из хлопкового волокна для снятия фаски, удаления заусенцев и чистовой обработки за один шаг. Меньшее количество остановок для замены абразивных кругов экономит драгоценное время и значительно снижает количество ошибок.
Эффективность шлифовки и чистовой обработки металла зависит от сцепления материала абразивного круга и эффективности используемого режущего зерна. Узнайте больше об абразивных зернах, чтобы найти то, что идеально подходит для вашей мастерской.
Узнайте больше об абразивных зернах. Получите копию нашей таблицы зерна.
Выберите лучший абразивный материал на связке
Эта статья служит в качестве учебника
по основам
выбора лучшего обычного шлифовального круга
.
Абразивы и зерна
Шлифовальные круги и другие абразивы на связке состоят только из двух основных компонентов. Абразив с зернами , которые непосредственно режут, и связка , которая удерживает зерна вместе и поддерживает их во время резки. Процент зерна и связки, а также расстояние между ними в круге определяют структуру круга.
Конкретный абразив, используемый в круге, выбирается в зависимости от того, как он будет взаимодействовать с обрабатываемым материалом.Каждый тип абразива уникален, с различными свойствами твердости, прочности, вязкости разрушения и ударопрочности.
Оксид алюминия является наиболее распространенным абразивом, используемым в клеевых изделиях. Обычно это абразив, выбираемый для шлифования углеродистой стали, легированной стали, быстрорежущей стали, отожженного ковкого железа, кованого железа, бронзы и подобных металлов.
Циркониевый оксид алюминия — это еще одно семейство абразивов, каждый из которых состоит из различного процентного содержания оксида алюминия и оксида циркония.
Карбид кремния — абразив, используемый для шлифования серого чугуна, закаленного железа, латуни, мягкой бронзы и алюминия, а также камня, резины и других цветных металлов.
Керамический оксид алюминия — новейшая разработка в области абразивов. Это зерно высокой чистоты, полученное в процессе агломерации геля. В результате получается абразив, способный разрушаться с контролируемой скоростью на субмикронном уровне, постоянно создавая тысячи новых точек резания.Этот абразив исключительно твердый и прочный. Он в основном используется для прецизионного шлифования в сложных условиях обработки сталей и сплавов, которые трудно шлифовать.
Каждый шлифовальный круг имеет номер, обозначающий размер зерна. Крупное зерно используется для быстрого съема материала, когда чистота не важна. Мелкозернистые круги подходят для придания тонкой отделки, для небольших площадей контакта и для использования с твердыми, хрупкими материалами.
Типы связки
В обычных шлифовальных кругах используются три основных типа связки.Каждый тип способен придавать различные характеристики шлифовальному действию круга. Выбранный тип связки зависит от таких факторов, как рабочая скорость круга, тип шлифовальной операции, требуемая точность и шлифуемый материал.
Большинство шлифовальных кругов изготавливаются с керамической связкой . Шлифовальные круги на керамической связке очень жесткие, прочные и пористые. Они удаляют материал с высокой скоростью и измельчают в соответствии с точными требованиями. На них не влияет вода, кислота, масла или колебания температуры.
Некоторые соединения сделаны из органических веществ. Эти связи размягчаются под действием тепла шлифования. Наиболее распространенным типом органической связки является резиноидная связка , изготовленная из синтетической смолы. Круги с резиноидной связкой — хороший выбор для операций, требующих быстрого удаления материала, а также для тех случаев, когда требуется более качественная отделка.
Другим типом органической связки является каучук . Колеса с резиновой связкой обеспечивают плавное шлифование.Резиновые связки часто используются в колесах, где требуется высокое качество отделки, например, в шариковых и роликовых подшипниках. Твердость или прочность связки обозначают как класс шлифовального круга. Связка считается твердой, если скрепляющие штифты или промежутки между каждым абразивным зерном очень прочны и могут удерживать зерна от шлифовальных усилий, стремящихся их вырвать. Говорят, что колесо имеет мягкий сорт, если для высвобождения зерен требуется лишь небольшое усилие.Следовательно, именно относительное количество связки в круге определяет его класс или твердость.
Круги из твердого сплава используются для увеличения срока службы круга, для работ на машинах высокой мощности, а также для работ с небольшими или узкими контактными площадками. Круги с мягким профилем используются для быстрого съема материала, для работ с большой площадью контакта и для твердых материалов, таких как инструментальные стали и карбиды.
Выбор обычных абразивных материалов на связке
Существует ряд факторов, которые необходимо учитывать при выборе лучшего шлифовального круга.Во-первых, это материал, который нужно измельчить. Это определяет тип абразива, который вам понадобится в круге. Например, оксид алюминия или оксид циркония следует использовать для шлифования сталей и стальных сплавов. Выбор между этими двумя будет зависеть от типа выполняемого измельчения. Для шлифования чугуна, цветных металлов и неметаллических материалов выберите абразив из карбида кремния.
Для твердых, хрупких материалов обычно требуется круг с мелкой зернистостью и более мягкой маркой.Твердые материалы препятствуют проникновению абразивных зерен и вызывают их быстрое затупление. Таким образом, сочетание более мелкого зерна и более мягкого сорта позволяет абразивным зернам отрываться по мере того, как они становятся тупыми, обнажая свежие острые режущие кромки. Для мягких, пластичных и легко проникающих материалов следует выбирать круги с крупнозернистым и твердым зерном.
Еще одним соображением является количество удаляемого материала. Более крупные зерна обеспечивают быстрое удаление материала, поскольку они способны к большему проникновению и более тяжелым резам. Однако, если в рабочий материал трудно проникнуть, круг с более мелкой зернистостью будет резать быстрее, поскольку для выполнения работы имеется больше точек резания.
Круги на керамической связке обеспечивают быструю резку. Связки на основе смолы, каучука или шеллака следует выбирать, если необходимо удалить меньшее количество материала или если требования к отделке выше.
Другим фактором является рабочая скорость колеса. Если специально не предназначено для высокоскоростного шлифования, керамические круги используются при скоростях менее 6500 футов поверхности в минуту; при более высоких скоростях застеклованная связка может разрушиться.Колеса с органической связкой обычно выбирают между 6500 и 9500 футов поверхности в минуту.
Для работы на более высоких скоростях обычно требуются специально разработанные круги для высокоскоростного шлифования. В любом случае не превышайте безопасную рабочую скорость, указанную на колесе или его промокательной бумаге.
Следующим фактором, который следует учитывать, является площадь шлифовального контакта между кругом и заготовкой. Для большей площади контакта используйте круг с более грубым зерном и более мягкой фракцией. Это обеспечивает свободное, холодное резание при более высокой нагрузке, связанной с размером обрабатываемой поверхности.Меньшие площади шлифовального контакта требуют кругов с более мелкой зернистостью и более твердых сортов, чтобы выдерживать большее единичное давление.
Далее, рассмотрите жесткость шлифовального действия. Это определяется как давление, под которым шлифовальный круг и заготовка сводятся и удерживаются вместе. Некоторые абразивы были разработаны, чтобы выдерживать тяжелые условия шлифования при шлифовании стали и стальных сплавов.
Также необходимо учитывать мощность шлифовального станка. Если мощность меньше диаметра колеса, следует использовать более мягкое колесо.Если мощность больше диаметра колеса, выберите колесо более твердого сорта. В общем, тверже
Заключение
Сегодняшние процессы шлифования действительно можно рассматривать как инженерные системы, состоящие из четырех ключевых компонентов: станок, абразивный продукт, рабочий материал и эксплуатационные факторы. Производители, которые хотят оптимизировать производительность своих шлифовальных систем, рассматривают все эти переменные и оценивают, как изменения в одной из них влияют на другие, при принятии решения о том, какой шлифовальный круг лучше всего подходит для их применения. TMD
Боб Смит,
Директор по разработке приложений
SaintGobain Abrasives
nortonabrasives.com
Ⅲ. Что такое абразивное зерно (абразивы)?
Основные характеристики абразивов
Твердость (твердость абразивных материалов) | ・Тверже, чем заготовка. ・Излом (абразивное разрушение и образование новой режущей кромки) под действием внешней силы во время шлифования. |
---|---|
Прочность, ударопрочность. | ・Устойчив к деформации и разрушению под действием внешней силы во время эксплуатации. ・Микротрещины |
Огнестойкость | ・Абразивные материалы обладают умеренной огнестойкостью, что предотвращает затупление кромки из-за тепла при шлифовке.![]() |
Инертность | ・Химическая инертность (отсутствие реакции с заготовкой). |
Твердость и ударная вязкость являются противоречивыми свойствами.Когда твердость высокая и самозатачивание выполняется хорошо, в то время как зерна с низкой ударной вязкостью увеличивают расточительный расход и влияют на чистовую обработку.
* Абразивы отваливаются, когда они изнашиваются и теряют остроту, тогда они постоянно обнажают новые режущие кромки.
Тип абразивных материалов
Существует множество видов абразивных материалов.
Основные виды зерна и его применение следующие.
Имя | Код | Цветовой тон | Приложения |
---|---|---|---|
Коричневый глинозем | А | Коричневый | Безручное шлифование углеродистой стали, Прецизионное шлифование углеродистой стали |
Монокристаллический плавленый оксид алюминия | ГА | Пепельно-серый | Прецизионное шлифование легированных, инструментальных и закаленных сталей |
Розовый глинозем | ПА | Розовый | Прецизионное шлифование легированной, инструментальной и закаленной стали |
Белый глинозем | WA | Белый | Прецизионное шлифование легированных, инструментальных и закаленных сталей |
Оксид циркония | АЗ | Серый | Удаление кромок, заусенцев и резка сталей |
Черный карбид кремния | С | Черный | Шлифование, прецизионное шлифование цветных металлов и неметаллических материалов |
Зеленый карбид кремния | ГК | Зеленый | Шлифовка суперсплава |
О зернистости
Размер абразивных частиц, называемый «зернистостью», выбирается в зависимости от точности обработки шлифовальной поверхности.
Зернистость указана в JIS R6001, она обозначается «F + число».
(Пример: если размер зерна равен 36, он будет обозначаться как «F36»)
Меньшие числа означают большое расстояние между абразивами.
Абразивы играют наиболее важную роль в сырье, как описано выше.
Дополнительная информация – История абразивных материалов –
С незапамятных времен люди полировали и шлифовали дерево, камень и камень из различных материалов.
Полировка и шлифовка нам хорошо знакомы.
Различные абразивы из песчаника (кремнезема), наждака и граната, глинозема вошли в употребление в каменном веке, медном веке и железном веке соответственно, но все абразивы являются природными камнями.
В 1881 году американский химик Эдвард Гудрич Атчесон работал над разработкой методов получения искусственного алмаза. Он нагрел смесь глины и кокса в дуговой печи и обнаружил твердые крупные кристаллы. Он предположил, что это соединение углерода и корунда и назвал его «карборундом», результат химического анализа показал, что это карбид кремния (SiC).
Это был первый синтетический абразив. Технология была реализована компанией Carborundum и позже распространилась по всему миру.
В 1897 году С. Б. Джейкобс разработал метод производства искусственного корунда путем нагревания смеси боксита (алюминия) и кокса в дуговой печи. Это вещество было названо «алунд» и было коммерциализировано компанией Norton. Позже алунд стал производиться по всему миру.
В Японии карбид кремния и искусственный корунд были впервые произведены соответственно в 1917 и 1918 годах компанией Kagoshima Tramway Co., Ltd. Хотя производство было временно приостановлено, многие компании возобновили производство после 1930 года.
С тех пор, как были созданы зерна карбида кремния и зерна оксида алюминия, с развитием промышленности многие страны улучшили и произвели различные искусственные абразивы.
Существует много видов абразивов на основе оксида алюминия (WA, MA, PW и т. д.). AZ представляет собой абразив с кристаллической структурой, который производится сплавлением оксида алюминия и диоксида циркония. Это новаторский абразив, обладающий высокой ударной вязкостью в сочетании с желательным свойством микроразрушения.
Искусственные абразивы достигли большого прогресса благодаря практическому применению кубического нитрида бора (CBN) и искусственного алмаза, началу ночной эксплуатации в точной механической обработке.
В настоящее время несколько компаний разработали новый абразивный материал, называемый керамическим абразивом, который имеет микрокристаллическую структуру. Он производится химическим синтезом, а не методом плавления, и уже нашел практическое применение в некоторых отраслях промышленности.
Техническая информация — Основы абразивных материалов на связке
Техническая информация включает в себя:
- Как прочитать облигационные абразивные спецификации
- облигационные абразивы терминология ключевой
- скорости колеса конверсионные таблицы
- абразивные зерна, сорт, структура колеса и облигации
- правильное хранение связанных абразивов
полный доступ ко всем этим ресурсам, смотрите подробности в нашем каталоге.
Абразивные зерна
Абразивные зерна (керамический корунд, циркониевый корунд, оксид алюминия и карбид кремния) выполняют режущее действие. Идеальный шлифовальный абразив обладает способностью разрушаться до того, как произойдет серьезное затупление, и обеспечивает максимальную устойчивость к точечному износу. Каждый абразив имеет особую кристаллическую структуру и характеристики излома, что делает его пригодным для шлифования определенных материалов.
Medalist – Ceramic Alumina
Зерно с превосходными характеристиками для жаропрочных сплавов, таких как Inconel, Waspalloy и Haspalloy, закаленных инструментальных сталей, напыляемого металла или стеллита и других закаленных сталей.
Циркониевый глинозем
Жесткий, острый абразив, предназначенный для оптимальной работы в отрезных кругах, отрезных кругах и кругах с вогнутым центром для шлифовки или резки литой стали, легированной стали, а также ковкого и ковкого чугуна.
Оксид алюминия
Прочное острое зерно, полученное в контролируемых условиях и специально предназначенное для шлифования или резки материалов с высокой прочностью на растяжение, таких как легированная сталь, быстрорежущая сталь, отожженное, ковкое железо и прочная бронза.
Карбид кремния
Это очень твердое острое абразивное зерно, используемое для шлифования карбида вольфрама и материалов с низкой прочностью на растяжение, таких как чугун, бронза, алюминий, медь, и неметаллических материалов, таких как пластик, стекло, мрамор, гранит и камень.
Сорт
Сорт представляет собой прочность сцепления шлифовального круга и часто упоминается как его твердость. Чем выше буквенное обозначение, тем прочнее связь.
Структуры кругов
Структуры кругов (расстояние между частицами зерна) варьируются от открытых до плотных и варьируются в зависимости от различных операций шлифования, в зависимости от площади контакта и типа измельчаемого материала, скорости съема материала и требуемой отделки. Карборунд предлагает круги со стандартной структурой, которые хорошо работают с широким спектром материалов.
Связки
Связка предназначена для удержания частиц абразивного зерна вместе.
Витрифицированные связки
Витрифицированные круги имеют состав на основе стеклянной связки. Керамические круги очень хорошо сохраняют форму и обеспечивают высокое отношение съема материала к использованию круга. Керамические круги обычно используются для прецизионного шлифования на рынке инструментов и штампов.
Пористость
Керамические круги могут быть изготовлены с искусственной пористостью. Все застеклованные связки, оканчивающиеся на P (VLP, V40P, VPP), указывают на индуцированную пористость. Эта пористость обеспечивает превосходный поток охлаждающей жидкости и удаление стружки.Для материалов, которые нагружаются, или для контакта с большой площадью поверхности это обеспечивает более холодное режущее действие, меньшую нагрузку и меньшую вероятность ожога заготовки.
Резиноидные связки
Резиноидные или органические связки более устойчивы к ударам, чем стекловидные связки, и обычно работают при более высоких окружных скоростях. Большинство кругов на полимерной связке используются для быстрого съема материала в металлообработке и литейном производстве.
Три столпа эффективности керамического абразивного зерна
Абразивная обработка уходит своими корнями в глубь тысячелетий, когда речь идет о производстве муки из различных пищевых зерен, а также о заточке металлических инструментов и холодного оружия.Хотя шлифовальные круги из натурального камня существовали тысячелетиями, изобретение искусственных шлифовальных кругов, какими мы их знаем сегодня, произошло в конце 1800-х годов. Круги на основе каучука и глины существовали недолго, но самый большой технологический прорыв в ту эпоху произошел, когда Свен Пулсон изобрел шлифовальный круг на керамической связке в 1873 году. Г-н Пулсон был сотрудником Фрэнка Нортона, который запатентовал этот продукт, который затем стала основой для того, что впоследствии стало известно как Norton Abrasives Company.
Несмотря на скачок в технологии связки шлифовальных кругов, активный компонент кругов оставался в сфере природных абразивов, таких как наждак. Только после изобретения карбида кремния (1891 г.) и коричневого плавленого оксида алюминия (1905 г.) шлифовальные круги, а также наждачная бумага (шлифовальные абразивы) не имели специально разработанных зерен для повышения производительности. Самые ранние абразивные зерна и их последующие поколения продуктов использовали процесс электроплавления, работающий при температурах до ~ 2000 ° C.Преимущество искусственного зерна сочетает в себе твердость, ударную вязкость и гораздо большую способность к самозатачиванию до того, как зерно будет полностью израсходовано. В течение десятилетий процесс электроплавки использовался для удовлетворения мировых потребностей в абразивном зерне.
Новейшие и наиболее эффективные традиционные абразивные зерна в настоящее время производятся путем спекания керамики на основе оксида алюминия. Это более поздняя разработка, когда Norton SG был выпущен на рынок в 1984 году после его изобретения Ральфом Бауэром. Из керамики в сыром состоянии, которую легко раздавить пальцами, можно спекать чрезвычайно прочный и долговечный продукт до состояния, более твердого и жесткого, чем расплавленные зерна. Кроме того, технология керамического зерна приводит к получению зерен с тонкой микроструктурой, которая создает тысячи участков излома по сравнению с несколькими плоскостями излома для каждого сплавленного зерна. Способность керамических зерен к самозатачиванию во много раз выше, чем у сплавленных зерен, и повышает производительность обычных абразивных материалов на связке и с покрытием до самого высокого уровня.
В последние годы многие покупатели специальных зерен и порошков Saint-Gobain связывались с нами, чтобы заказать зерна особой формы или, по крайней мере, чтобы лучше понять, как зерна особой формы могут влиять на характеристики керамического зерна. Действительно, манипулирование Saint-Gobain формой зерна является ключевым рычагом для изменения характеристик зерна, но это только один из факторов. Благодаря обширным исследованиям и опыту мы разработали три различных фактора или «столпа», которые могут по отдельности или в сочетании обеспечивать производительность зерна, которая лучше всего подходит для определенного диапазона применений.
SEEDED GEL — CERPASS XTL
Чистота >99,6% Al2O3
Плотность – 3,9 г/см3
Пористость <1,5%
Твердость – 21,6 гПа
α-Al2O3 xtal – <0,2 мкм
ЗОЛ-ГЕЛЬ, ДОПИРОВАННЫЙ С ОКСИДОМ РЕДКОЗЕМЕЛЬНЫХ МЕХАНИЗМОВ
Чистота ~ 94-96% Al2O3
Плотность – 3,9 г/см3
Пористость ~ 5%
Твердость – 19 гПа
α-Al2O3 xtal – 4-10 мкм
Оригинальный затравочный гель Norton SG, выпущенный на рынок в 1984 году, отличался очень тонкой микроструктурой, высокой чистотой и высокой прочностью.Размер кристаллов составляет приблизительно 0,20 мкм по сравнению с типичными зернами голубого типа при размере кристаллов приблизительно 4-10 мкм. Крупные кристаллы зерен голубого типа пересекаются пластинками, образованными из оксидов редкоземельных элементов, обычно из комбинации оксида лантана и оксида иттрия. Этот оригинальный засеянный гель, также известный как Cerpass XTL, благодаря своей более высокой прочности и ударной вязкости подходит для другого диапазона применений, чем конкурентное зерно с более высокой ломкостью. Производительность Cerpass XTL лучше подходила для шлифования твердых материалов с большой подачей, в то время как более рыхлый конкурентный продукт, по-видимому, был разработан, чтобы лучше подходить для абразивных работ с покрытием.
Способность манипулировать зернами в очень тонкую и прочную микроструктуру является основным принципом работы керамического зерна Saint-Gobain. Более поздние поколения зерна могут иметь различную микроструктуру и размеры кристаллов, в зависимости от необходимости.
Макроструктура
Первые зерна Saint-Gobain с тонкой и прочной микроструктурой были выпущены на рынок в двух формах, подвергнутых механической дробленой обработке: блочной и острой. После достижения больших успехов в приложениях, связанных с более высокими усилиями (повышенная мощность, подача и перемещение) на более твердых материалах, остались некоторые приложения и материалы, требующие зерна, которые могли бы работать при более низких усилиях.Благодаря внутренним исследованиям, а также полевым испытаниям было разработано зерно сверхострой формы, которое не только превзошло характеристики зерен затравочного геля стандартной формы, но и часто превзошло характеристики конкурирующих зерен, отличающихся более высокой ломкостью благодаря химическим присадкам.
ЗАСЕЯННЫЙ ГЕЛЬ – ‘DELTA’ CERPASS DGE
Чистота >99,6% Al2O3
Плотность – 3,9 г/см3
Пористость <1,5%
Твердость – 21,6 гПа
Соотношение α-Al2O3 xtal – <0,2 мкм LPD 9004спект 2.5:1
Дельта-зерно (DGE) было создано из того же чистого оксида алюминия по химическому составу и микроструктуре, что и исходные зерна, но имеет чрезвычайно острую форму. Зерна были сформированы с помощью термического формования или процесса «взрыва». В результате этого процесса были получены зерна с более высоким соотношением сторон, острыми точками и острыми краями. Успешное применение этого зерна связано с применением меньших усилий и/или более мягких материалов. Использование этого зерна значительно улучшило такие области применения, как абразивы с покрытием для нержавеющей стали, а также шлифование внутреннего диаметра.
SEEDED GEL – ‘TARGA’ CERPASS TGE
Чистота >99,6% Al2O3
Плотность – 3,9 г/куб.см
Пористость <1,5%
Твердость – 21 гПа
α-Al2O3 xtal – <0,2 мкм
*TG2 Соотношение сторон — ~8:1 Зерно
Targa (TGE) также было создано из исходного чистого химического состава и микроструктуры исходных зерен, но было специально сформировано с чрезвычайно высоким соотношением сторон ~ 4: 1. Форма зерна Targa обеспечивает агрессивное резание с малым усилием, а также способствует очень открытой структуре при использовании для склеивания. В приложениях с большой глубиной резания (DOC), таких как глубинная подача и зубошлифование, это зерно демонстрирует превосходные характеристики по сравнению с зернами стандартной формы и во многих случаях по сравнению с другими специальными формами, такими как треугольники. Последнее поколение, TG2, предлагает еще более высокое соотношение сторон ~8:1 для высочайшего уровня производительности при глубинном шлифовании и зубошлифовании.
Химия
Последним компонентом характеристик керамического зерна Saint-Gobain является изменение химического состава зерна для улучшения определенных характеристик, таких как устойчивость к высокотемпературным процессам стеклования или специально разработанная хрупкость для оптимизации характеристик в ряде применений.С помощью запатентованных процессов можно изменить химический состав зерен, чтобы модифицировать границы кристаллов внутри зерен или продвигать различные кристаллические фазы.
SEEDED GEL – CERPASS HTB
Чистота >95% Al2O3
Плотность – 3,9 г/см3
Пористость <1,5%
Твердость – <20 гПа
α-Al2O3 xtal – <0,22 мкм
LPD — 9000
Одним из очень успешных примеров является зерно Cerpass HTB. Это конкретное зерно обеспечивает повышенную производительность в широком спектре абразивных материалов на связке, а также обладает предполагаемым преимуществом в виде стойкости к повреждениям в высокотемпературных системах с керамической связкой.Основным элементом, определяющим эти характеристики, была модификация химического состава, чтобы противостоять повреждению кристаллической структуры при использовании стеклянных связок, а также обеспечивать оптимальную хрупкость, независимо от того, является ли система связки стекловидной или органической.
Типы зерна в приложении
Независимо от того, тестируете ли вы недавно разработанное зерно или сравниваете его с существующим или конкурирующим зерном, необходимо провести испытания на измельчение в контролируемой среде. Компания Saint-Gobain разработала метод испытаний на шлифование, который контролирует как можно больше переменных, но при этом позволяет осуществлять фактическое шлифование различных материалов при различных рабочих параметрах. Размер, количество и расстояние между зернами нормализуются для достижения более значительных результатов. Параметры могут быть скорректированы для имитации различных полевых условий, таких как нанесение абразива с покрытием с низким усилием или нанесение на связке грубого шлифования с высоким усилием.
После того, как в ходе этих испытаний зерно окажется перспективным кандидатом, проводятся полевые испытания для определения производительности в приложениях. В следующей информации приведены примеры того, как «три столпа» Seeded Gel могут повлиять на производительность, с результатами внутреннего сравнительного анализа, а также с некоторыми связанными историями.
Высокая производительность благодаря сверхострой форме и микроструктуре
В этом случае производительность по сравнению с зернами синего типа была достигнута за счет сверхострой формы зерен Delta (DGE), работающих при малом усилии на нержавеющей стали серии 304. Параметры испытаний были установлены для аппроксимации сил, возникающих при нанесении абразивных материалов с покрытием или при шлифовании внутренних отверстий абразивными материалами на связке.
Достигнутый результат был получен путем тестирования дельта-зерен (DGE) по сравнению с обычным золь-гелем синего типа при параметрах станка для средней глубины резания на нержавеющей стали 304.В таблице мощности указана мощность шпинделя станка.
DGE по сравнению с Blue Sol Gel на нержавеющей стали 304, резка с малым усилием
• DGE → удельная энергия (Дж/мм3) ниже на 28 %
• DGE → на 20 % больше срок службы до отказа (с)
• Значительно ниже нормальное усилие (J) генерируется с помощью DGE
*** Обратите внимание, что каждый временной шаг на диаграммах указывает на одинаковую подачу для сравниваемых зерен. Например, при 400 секундах в пределах диаграммы нормального усилия для DGE требуется примерно половина усилия золь-гелевой керамики при идентичной общей подаче.***
Во время шлифования энергия, измеряемая мощностью шлифования, расходуется на преодоление трения и удаление материала. Параметр удельной энергии измельчения указывает на эффективность процесса измельчения путем нормализации потребления энергии с количеством удаленного материала. Более острые зерна инициируют резку при меньшей силе трения и, следовательно, производят меньшую энергию измельчения и более высокую эффективность измельчения. Такой эффект обеспечивает сверхострая форма зерен ДГЭ. Кроме того, зерна продолжают резать более эффективно, особенно на мягких, но трудных материалах, таких как нержавеющая сталь серии 300.Помимо меньшей мощности шпинделя станка, DGE режет с гораздо меньшим нормальным усилием, что потребовало бы меньших усилий со стороны оператора и/или меньшей нагрузки на станок. Тонкая микроструктура и прочная связь между кристаллами позволяют свести к минимуму износ зерен, поскольку они избавляются от притупленных краев.
Производительность благодаря агрессивной форме
В этом случае характеристики зерна TGE (Targa) измеряются по сравнению с белым плавленым оксидом алюминия (WFA). WFA обычно считается наиболее рыхлым из типов плавленого оксида алюминия, хорошо работающим в приложениях, требующих возможности удаления металла без металлургического пригорания детали. WFA несколько ограничен в возможности увеличения производительности съема, при этом избыточное дробление зерна происходит при выходе за его пределы. Другие, более прочные сплавленные зерна, могут подвергаться более высокой скорости съема, хотя повышенные усилия могут создавать избыточное тепло и быть несовместимыми с чувствительными к горению деталями и/или сплавами.
Приведенные ниже диаграммы мощности и нормальной силы показывают характеристики зерна TGE по сравнению с WFA на углеродистой стали. Параметры испытаний были установлены таким образом, чтобы имитировать очень высокие подачи, которые могут иметь место при глубинной подаче или зубошлифовании.
Достигнутые результаты для TGE по сравнению с WFA за счет большой глубины резания и агрессивных параметров подачи следующие:
TGE по сравнению с WA: большая глубина резания углеродистой стали 45 Rc
• TGE → удельная энергия (Дж/мм3) в 9,5 раз ниже.
• TGE → MRR выше примерно в 4 раза.
Впечатляющие результаты TGE с точки зрения эффективности и производительности привели к значительному успеху в таких сложных областях, как глубинное шлифование и зубошлифование. Шлифовальные круги, сформированные из зерен TGE, во многих случаях превосходили круги, состоящие из золь-гелевых зерен голубого типа треугольной формы.Возможна чрезвычайно высокая скорость съема материала с минимальной тенденцией к металлургическому прижогу детали.
Дополнительным преимуществом зерна TGE является способность образовывать очень открытые структуры внутри шлифовальных кругов на керамической связке. Такая открытая конструкция позволяет подавать большие объемы охлаждающей жидкости в зону измельчения. Кроме того, эта очень открытая структура обеспечивает пространство для отвода большего количества стружки от зоны шлифования, что повышает устойчивость шлифовального круга к нагрузкам.Последняя версия зерна Targa, TG2, благодаря примерному соотношению сторон 8:1 поддерживает наиболее открытую структуру, возможную для этого типа зерна.
Приведенные ниже диаграммы мощности и нормальной силы показывают характеристики зерна HTB по сравнению с BFA и DGE на подшипниковой стали. Параметры испытаний были установлены для имитации умеренно высоких подач, которые могут возникнуть при шлифовании по внешнему диаметру или при шлифовании валков горячего проката.
Результаты лабораторных испытаний на шлифование HTB показали значительно улучшенные результаты шлифования закаленной подшипниковой стали.Сравнение с DGE показало, что искусственно созданная хрупкость становится более важной, чем очень острая форма:
HTB по сравнению с DGE и BFA на подшипниковой стали 52100 (100Cr6) после закалки
• HTB → Удельная энергия (Дж/мм3) ниже на 17% по сравнению с DGE, более чем в 8 раз ниже, чем для BFA
• HTB → G-коэффициент 1,8X по сравнению с DGE, более чем в 5 раз по сравнению с BFA
• HTB → MRR выше примерно в 4 раза.
Это зерно оказалось очень успешным не только для подшипников, но и для множества других применений, таких как валковое шлифование, плоское шлифование, переносные шлифовальные круги и пружинное шлифование. Новая доступность в размерах P открывает возможность применения этого зерна в изделиях с покрытием, таких как лепестковые диски и фибровые диски. Универсальность этого зерна можно рассмотреть в двух приведенных ниже примерах.
Успешные примеры клиентов — зерно HTB
Валковая шлифовка (по сравнению с кругами с синим Sol Gel)
• +100 % G-коэффициента
• +100 % скорости съема металла
• ИЛИ → некоторая комбинация этих двух параметров в зависимости от регулировки подачи, скорости перемещения и колеса скорость.
• Выдающиеся характеристики на новейших сплавах для вальцов (CPC и т. д.) → G-Ratios 2X конкурентоспособный золь-гель, даже с содержанием керамического зерна на 33% меньше, чем у конкурирующего круга.
Шлифовка автомобильных подшипников по внешнему диаметру: HTB по сравнению с обычной плавленой смесью
• 100 % увеличение количества деталей на заправку
• 50 % снижение компенсации зачистки на каждую заправку
• Высочайшее качество и постоянство (6-сигма и т. д.) за счет меньшего вариация от детали к детали и меньшее количество циклов правки.
Заключение
Хотя абразивные зерна должны работать совместно с другими компонентами, из которых создается готовый абразивный продукт, такой как шлифовальный круг или отделочная лента, именно зерна обеспечивают ключевые рабочие характеристики, превосходящие возможности обычных плавленых зерен.Традиционно достижение одного параметра производительности требует некоторой жертвы другими. Например, операция, требующая самых высоких скоростей съема, может дать результаты с некоторыми уступками в отношении чистоты поверхности и/или отсутствия прижога детали. Некоторого снижения пригара можно добиться, но обычно за счет использования очень хрупких зерен, что сокращает срок службы продукта. Аналогичным образом, для достижения жестких допусков по размерам и чистовой обработки часто приходится жертвовать производительностью.
Как показано в приведенных выше результатах и примерах, инженерный подход с использованием факторов микроструктуры, формы и химического состава керамического зерна может обеспечить желаемые результаты по наиболее важным критериям эффективности при сохранении или даже улучшении результатов по другим критериям. Во многих, если не в большинстве случаев, включение керамического зерна имеет низкий риск проблем, связанных с зерном, при замене им обычного плавленого зерна.
Хотя существуют некоторые требования к станкам, чтобы они могли использовать преимущества такой производительности, требования, как правило, намного меньше, чем для преобразования в суперабразивные продукты. Кроме того, стоимость включения керамических зерен значительно ниже, чем для суперабразивов. Будущее керамического зерна будет заключаться в повышении производительности за пределы существующих уровней и несколько ближе к производительности суперабразивов, но с более традиционными продуктами и оборудованием.
(PDF) Влияние микроструктуры стеклокристаллической связки на режущую способность шлифовальных кругов с абразивным зерном Al2O3
Герман Д., Надольный К., Соча Е. | Журнал машиностроения и энергетики, Vol. 3(43), № 3, 2019, стр. XXX-XXX 7
В то же время за счет микрокристаллической
структуры связки, ее микроизноса, в значительной степени
совместимого с механизмом изнашивания абразива
зерна, возможно. Это влияет на повышение стойкости
шлифовального круга, особенно
шлифовального круга с открытой конструкцией (объем пористого
Vp = 42% и небольшая доля связки Vb = 12%), который
при в то же время гарантирует высокие (требуемые) показатели производительности.
4. ВЫВОДЫ
Разработанная стеклокристаллическая связка
позволяет изготавливать инструмент из микрокристаллического оксида алюминия
и монокорунда
с открытой структурой и высокой самозатачивающейся способностью.Инструменты можно обжигать при относительно
низких температурах (940°C). Благодаря микро-
кристаллической структуре стеклокристаллической связки процесс микрорезки
включает систематическое (постепенное)
микродробление зерна и связки, что увеличивает
стойкость инструмента шлифовального круга. Такой процесс
определяется как самозатачивание, и его наличие в процессе шлифования
имеет решающее значение для получения
воспроизводимых результатов обработки. В случае разработанных
шлифовальных кругов самозатачивание инициируется более
и происходит в гораздо более широком диапазоне рабочих
параметров.
Благодарности
Работа выполнена при поддержке Министерства
Науки и высшего образования Польши в рамках гранта №
RPWP.01.02.00-30-0132/16 под названием: Круги шлифовальные для высокопроизводительного
шлифования с использованием стеклокерамические связки нового поколения
.Авторы выражают благодарность г-ну
Станиславу Бокею и г-ну Петру Яскольскому из лаборатории машиностроения
за помощь во время экспериментальных
исследований процесса измельчения, г-ну Кшиштофу
Мачеевскому из лаборатории метрологии И
Измерительные системы для измерений щупом, а также
Г-н Рышард Грицман из Центральной лаборатории
Института технологии и образования для получения микрофотографий
СЭМ.
Nomunclature
Nomronys
CBN — кубический нитрид бора
DTA — дифференциальный термический анализ3
DTA — дифференциальный термический анализ3
GF — шлифовальная жидкость
SEM — сканирующая электронная микроскопия
символы
AD — пособие, мм
AE. – общее рабочее усилие (припуск),
мм
bw – диаметр заготовки, мм
ds – наружный диаметр шлифовального круга, мм
dw – диаметр заготовки, мм
G – коэффициент шлифования, мм3/мм3
id – количество проходов правки
K1c – трещиностойкость, МПа·м½
nsd – частота вращения шлифовального круга при правке
, 1/мин
vfa – скорость осевой подачи стола при шлифовании, мм/с
vfd – осевая скорость подачи стола при правке, мм/с
vs – окружная скорость шлифовального круга, м/с
Vs – объемный износ шлифовального круга, мм3
vw – окружная скорость заготовки, м/с
Vb – объем связки в шлифовальном круге, %
Vp – объем пор в шлифовальном круге, %
Vw – съем материала, мм3
P – мощность шлифования, Вт
q – передаточное число
Ra – среднее арифметическое отклонение
профиль, мкм
Raav – среднее арифметическое отклонение профиля
шероховатость, мкм
ts – время шлифования, с /мин
Qw – скорость съема материала, мм3/с
– коэффициенты термического расширения, К-1
ΔP – прирост мощности шлифования, Вт
ΔPav – средний прирост мощности шлифования, Вт
σ – стандартное отклонение
Ссылки
1. Zi-cheng Li, Zhi-hong Li, Ai-ju Zhang, Yu-mei Zhu,
Влияние условий термообработки на двухмерный рост кристаллов нанокристаллического корунда
абразивы, Materials Research Bulletin 44 (2009)
762-767.
2. Wen Feng Ding & Jiu Hua Xu & Zhen Zhen Chen &
Hong Hua Su & Yu Can Fu, Износ зерна паяных
поликристаллических абразивных инструментов CBN при постоянном усилии
шлифование сплава Ti–6Al–4V, Int J Adv Manuf Technol
(2011) 52:969–976.
3. Франтишек Холесовски, Михал Храла, Целостность грунта
цилиндрическая поверхность, Журнал обработки материалов
Технология 153–154 (2004) 714–721.
4. Qing Miao, Wenfeng Ding, Yulong Gu, Jiuhua Xu,
Сравнительное исследование характеристик износа абразивных кругов из коричневого
и микрокристаллического оксида алюминия
при глубинном шлифовании различных жаропрочных сплавов на основе никеля
, Wear 426 –427 (2019) 1624–1634.
5. Jiang Shia, Feng He, Junlin Xie, Xiaoqing Liu, Hu Yang,
Влияние отношения Na2O/BaO на структуру и физические свойства низкотемпературных стеклокерамических
, Ceramics International 44 (2018)
10871–10877.
6. Xuezhi Wang, Zhelun Ma, Xue Sun, Tianbiao Yu,
Wanshan Wang, Влияние ZrO2 и Y2O3 на физические
и механические свойства керамической связки и керамики
CBN композиты, International Journal of Refractory
Metals и твердые материалы 75 (2018) 18–24.
7. Dongdong Shan, Zhihong Li, Yumei Zhu, Hang Ye, Kai
Gao, Yanyan Yu, Влияние TiO2 на физические свойства
низкотемпературной керамической стекловидной связки и
механические свойства CBN композитов, Керамика
International 38 (2012) 4573–4578.
8. Baohui Zhao, Zhihong Li, Yumei Zhu, Влияние частиц муллита
на механическую прочность и химическую
долговечность застеклованных композитов CBN, Composites:
Part B 54 (2013) 265–268.
9. Baohui Zhao, ZhihongLi, YumeiZhu, Влияние поликристаллических муллитовых волокон
на свойства
Керамические и циркониевые абразивы: какой вариант лучше?
Когда вы работаете над проектом, вы хотите убедиться, что он завершен в меру ваших возможностей и выглядит так же. Одним из важных факторов для этого является выбор лучших инструментов для вашей заготовки. В Empire Abrasives часто задают вопрос: «В чем разница между диоксидом циркония и керамикой?» Понимание этого позволит вам принимать наиболее обоснованные решения относительно ваших покупок, инструментов и материалов, которые вы используете.Вы можете найти различные шлифовальные ленты, диски и многое другое как из циркония, так и из керамики. Хотя оба отлично подходят для агрессивной работы и превосходны при зернистости 24-120, их различия становятся более очевидными в их долговечности, структуре и возможностях.
Как упоминалось ранее, способность абразивного материала становится более очевидной при использовании. Почти все знакомы с оксидом алюминия как с абразивом, и он является отличной отправной точкой для понимания других абразивных материалов. Оксид алюминия был разработан для замены граната и других хрупких зерен, и он прекрасно справляется как с мягкой, так и с твердой древесиной.Он также хорош для некоторых марок стали и цветных металлов. Однако в конечном итоге вы столкнетесь с проектом или исходным материалом, для которого требуется более агрессивный абразив, который служит дольше и лучше подходит для шлифовки металла, и именно тогда вам понадобится керамика или диоксид циркония. И керамика, и диоксид циркония представляют собой высокоэффективные абразивные зерна, которые служат намного дольше, чем вышеупомянутый оксид алюминия, благодаря их способности затачиваться при каждом использовании, в отличие от оксида алюминия. Это позволяет диоксиду циркония и керамике постоянно обновляться для достижения максимальной режущей способности до полного износа зерна.
Циркониевые абразивы
Цирконий изготавливается литьем под давлением и, как правило, доступен с более крупным зерном до 120. Это крупное зерно, которое обладает высокой термостойкостью и значительно прочнее, чем оксид алюминия. Вы обычно найдете абразивы из диоксида циркония в различных цветах от светло-голубого до ярко-зеленого. Цирконий — отличный выбор для шлифовки и механической обработки под высоким давлением. Для шлифования требуется большее давление. Ленты и шлифовальные диски лучше подходят для работы на твердых поверхностях и не подходят для полировки.Цирконий чаще всего используется в цехах по производству стали. Но вы также обнаружите, что цирконий является предпочтительным выбором для резки, шлифования и других абразивных работ из нержавеющей стали. Он отлично подходит для удаления заусенцев с очень твердых металлов, таких как углеродистая сталь, сплав стали, железа и никеля, нержавеющая сталь, вольфрам, карбид вольфрама и титан, и это лишь некоторые из них. Цирконий, как правило, доступен на толстой тканевой основе. Наши ленты из циркония с закрытым покрытием предлагают более абразивный материал, поскольку он полностью покрыт, и если у вас много грубой шлифовки для ржавчины или других металлических работ, цирконий будет лучшим вариантом.
Цирконий будет иметь гораздо более длительный срок службы, чем оксид алюминия, будет более пластичным и обеспечит более прохладное шлифование / шлифование. Шлифовальные диски из диоксида циркония и шлифовальные ленты из диоксида циркония являются наиболее популярными типами абразивов на рынке.
Несмотря на то, что он прочнее оксида алюминия, у диоксида циркония могут возникать трудности с измельчением прокатной окалины.
Используйте цирконий на:
- Нержавеющая сталь
- Инструментальная сталь
- Никелевый сплав
- Алюминий
- Титан
- Чугун
- Углеродистая сталь
- Лезвия
- Роторы
- Сварные швы
Керамические абразивы
Керамические абразивы более уникальны своей микрозернистой структурой, поскольку они имеют микрокристаллическую структуру и доступны с более крупными зернами до 120.Это означает, что керамика способна разрушаться гораздо более контролируемым образом, что расширяет как область применения, так и ее способность работать с более твердыми металлами. Именно эта способность делает керамику предпочтительным выбором для аэрокосмических приложений и металлов, таких как титановый сплав. Он также хорошо работает с алюминиевым литьем, отделкой из нержавеющей стали и прокатной окалиной из мягкой стали. По мере того, как керамика все больше адаптируется в промышленности, керамические ленты, в частности, оказали сильное влияние как на эффективность, так и на качество шлифования и шлифования металлов.Керамические ленты становятся все более популярными в ножевой промышленности для отделки высокоуглеродистой стали. Он быстро становится фаворитом из-за того, что керамика ломается и самозатачивается при меньших усилиях, что обеспечивает самый быстрый диапазон резки и самый долгий срок службы из всех абразивных зерен на сегодняшний день. Микрозернистая структура керамики приводит к тому, что более мелкие фрагменты откалываются в процессе шлифования или шлифования. Этот процесс разрушения оставляет больше абразивных частиц, с которыми можно продолжать работать, и, таким образом, увеличивается срок службы продукта.
Керамика работает холоднее, но чувствительна как к теплу, так и к давлению, что делает ее идеальной для шлифования при низком давлении, но ее использование должно быть тщательно продумано, чтобы керамика обеспечивала наилучшие характеристики и максимально использовала абразив с самым долгим сроком службы.
Используйте керамику на:
- Алюминиевые отливки
- Углеродистая сталь
- Черные металлы
- Инконель
- Весы из мягкой стали
- Цветной металл
- Отделка из нержавеющей стали
- Титановый сплав (и другие аэрокосмические металлы)
- Инструментальная сталь
Цирконий или керамика лучше?
И диоксид циркония, и керамика прослужат дольше и удалят металл быстрее, чем оксид алюминия.Однако, когда вы решаете, что использовать, важно учитывать тепло проекта и давление, необходимое для проекта. Керамика более чувствительна к ним и лучше всего подходит для проектов с более низким давлением. А если вам нужно более высокое давление, цирконий — лучший выбор для этих целей.
Хотя керамика служит дольше, чем диоксид циркония, они оба являются отличным выбором. Оба абразивных зерна самозатачиваются по мере износа, и оба в основном используются для обработки металлов.В конце важно вернуться к тому, является ли это высоким или низким давлением, как отличное начало вашего процесса принятия решений.
Ссылка на краткий обзор:
Цирконий:
- Самозатачивающийся при использовании
- Служит дольше, чем оксид алюминия
- Лучше всего работает при высоком давлении
- Высокая термостойкость
- Не действует на окалину
- Не подходит для полировки
- Лучше всего работает на твердых поверхностях
Керамика:
- Самозатачивающаяся при использовании
- Служит дольше, чем диоксид циркония.
- Лучше всего работает при низком и среднем давлении
- Отлично подходит для отделки ножей
- Отлично подходит для титана и других аэрокосмических металлов
- Лучше всего работает при низкой и средней температуре
- Работа с мягкой окалиной
Цирконий и керамика — отличный выбор. Цирконий в целом является более универсальным абразивом для новичков и опытных пользователей. Он экономичен по цене, долговечен и хорош для металлов и дерева.Керамика имеет свое место в промышленности, но лучше подходит для тех, кто может обеспечить применение при низком давлении, или для тех, кто работает с более экзотическими металлами.
Чат с нашей командой экспертов
Мы предлагаем широкий ассортимент шлифовальных лент и дисков из диоксида циркония и керамики. Если вы все еще не уверены или не определились, позвоните нам по телефону 1-800-816-3824 или откройте чат в правом нижнем углу экрана. Мы всегда рады помочь.
.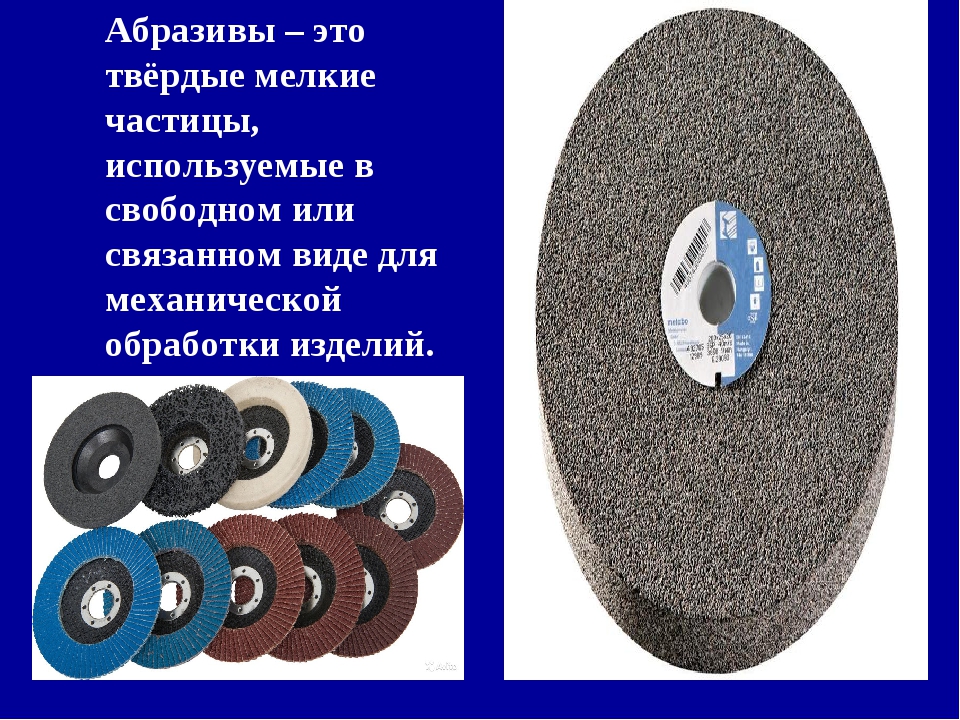