Литье пластмасс в силикон — доступное мелкосерийное производство в домашних условиях
Многие из тех, кто печатает на 3D-принтере сталкиваются или с необходимостью получить партию моделей в короткие сроки, или скопировать удачно получившуюся деталь, или получить изделия с прочностными характеристиками, превосходящими таковые у пластиков для домашней 3d-печати.3D-принтер далеко не всегда способен выполнить такие задачи, но отлично подойдет для создания единственного образца, или мастер-модели. А дальше на помощь нам приходят материалы производства компании Smooth-On, наверное, самого популярного производителя материалов холодного отверждения.
В этом обзоре мы сравним самые основные и популярные силиконы, полиуретаны и добавки к ним, кратко посмотрим на основные способы создания форм и изделий, подумаем, где это может найти применение и, наконец, создадим свою силиконовую форму и модель.
Перед написанием этого поста мы прошли трехдневный тренинг у официального дилера Smooth-On в России, чтобы разобраться во всех тонкостях литья в силикон.
Обзор процесса
Процесс создания изделий методом литья практически всегда одинаков: создаем модель, с её помощью создаем силиконовую форму, заливаем в нее материал, получаем изделие. Но в зависимости от модели, необходимых свойств, количества отливок, каждый этап может кардинально меняться. Существует несколько способов как создания формы, так и готового изделия.
Пару слов о подготовке моделей, напечатанных на 3D-принтере. Компания Smooth-On обратила своё внимание на эту технологию и выпустила специальный лак под названием XTC-3D. Он прекрасно сглаживает характерные для напечатанных моделей огрехи, видимые слои, которые обязательно перейдут на силиконовую форму, и придает поверхности гладкость и глянцевый вид.
Методы создания форм
• Сплошная заливка
Самый простой способ: модель помещается в опалубку (специальную герметичную емкость из обычного оргстекла, пластика или другого материала), фиксируется в ней и заливается силиконом. Хорошо подходит для простых двухмерных моделей, рельефов, сувенирной и брендинговой продукции.
• Разрезная форма
Аналогичен предыдущему, только модель размещается с учетом того, что форма будет разрезаться полностью или частично для облегчения съема. Модель может быть подвешена с помощью проволоки или размещена на тонкой опоре. Способ предназначен для более сложной геометрии, технических изделий, сложных фигур.
• Двухсоставная форма
Это один из самых сложных способов. Заключается в помещении модели на глиняную или пластилиновую основу, которая делит силиконовую форму пополам.
На основе размещаются специальные замки, которые будут обеспечивать точное совмещение двух форм и отсутствие смещений. Вокруг основы собирается опалубка, герметизируется горячим клеем или пластилином, и в неё заливается первая половина формы. Затем, после отверждения силикона, форма переворачивается, глина или пластилин счищаются, силикон покрывается разделительным составом, и заливается вторая половина формы.
• Метод «в намазку»
Этим методом создаются так называемые «чулочные» формы, когда силикон точно повторяет форму объекта и имеет толщину от 3 мм до нескольких сантиметров. Для создания формы «в намазку» необходим достаточно вязкий силикон, который бы не стекал с модели.
Можно использовать как специально предназначенные для этого силиконы, называемые тиксотропными, так и обычные, но модифицированные с помощью загустителей.
Силикон наносится кисточкой или шпателем в несколько слоёв, в которых чередуется вязкость и скорость отвердевания, чтобы форма была максимально детализированной и прочной. После того, как все слои готовы, с помощью специального состава создается жесткая внешняя оболочка, которая будет держать форму.
Методы заливки пластиков
Самый простой метод заключается в обычной заливке пластика в форму, он подходит для домашнего использования и позволяет достичь приемлемого качества. Но, по необходимости, для более качественного результата возможно использование установок высокого давления, что позволит практически полностью убрать пузырьки воздуха.
Для этого форма вместе с залитым пластиком помещается в камеру, в которой создается повышенное до 4 атмосфер давление. Форма должна оставаться в камере все время отвердевания полиуретана. При таком давлении пузыри уменьшаются до почти невидимых глазу размеров, что значительно повышает качество изделия.
Еще один метод, так называемая заливка «в обкатку», используется для создания полых изделий. В форму заливается небольшое количество пластика, около 10% от общего объема, отверстие для заливки закрывается, и начинается вращение формы по всех плоскостях, вручную или на специальной ротационной машине. При этом пластик отвердевает на стенках формы, создавая полую модель, что позволяет существенно снизить вес изделия и экономить материал.
Обзор силиконов
• Серия Mold Star 15, 16, 30
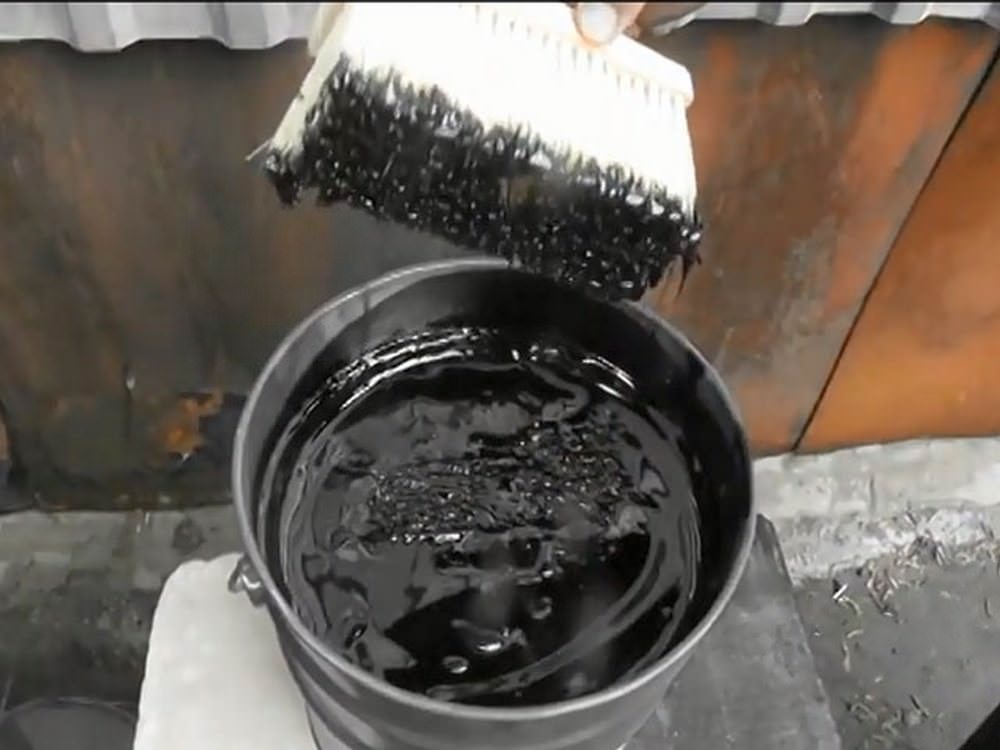
Самые базовые и основные силиконы, способные решать большинство задач. Цифра в названии отражает твердость по шкале Шор А. Обладает низкой вязкостью, что позволяет в большинстве случаев работать без оборудования для дегазации. Материал двухкомпонентный, части смешиваются в удобном соотношении 1:1 по объему. В основном предназначены для создания форм методом сплошной заливки.
• Серия Rebound 25, 40
Серия силиконов для создания форм методом «в намазку», который состоит в том, чтобы наносить силикон кистью или шпателем на поверхность модели. Обладает высокой вязкостью, возможностью модификации свойств с помощью загустителей и ускорителей для создания качественной многослойной формы. Двухкомпонентный, смешивается в соотношении 1:1 по объему.
• Серия Equinox 35, 38, 40
Силиконовые пасты с временем жизни 1, 4 и 30 минут. Предназначены для ручного смешивания, по консистенции напоминают густое тесто.
• Серия SortaClear 18, 37, 40
Серия полупрозрачных силиконов. Такая особенность, как оптическая прозрачность, используется для создания сложных разрезных форм — изделие прекрасно просматривается, что позволяет сделать точный разрез. Как и серия Equinox, является безопасным при контакте с пищевыми продуктами.
Также к силиконам существует большое количество добавок, обладающих самыми разными эффектами. Accel-T и Plat-Cat являются ускорителями отверждения, Slo-jo — увеличивает время жизни силикона, Thi-Vex увеличивает вязкость силикона и позволяет намазывать его кистью или шпателем на модель, Silc-Pig — это концентрированные пигменты для окрашивания.
Обзор полиуретанов
• Серия Smooth-Cast
Самая основная и популярная серия полиуретанов для создания конечных изделий. Линейка включает в себя более 10 наименований различных пластиков с самыми разными свойствами, позволяющими подобрать материал именно для Вашего проекта. Например, Smooth-Cast 300 обладает коротким временем жизни в 3 минуты и временем отверждения в 10 минут, что позволяет быстро воспроизводить большие партии деталей. Smooth-Cast 305 аналогичен предыдущему, но «живет» уже 7 минут, что позволяет провести дегазацию смешанных компонентов и получить еще более качественное изделие. ONYX обладает глубоким черным цветом, которого не достичь с помощью красителей, 65D ROTO предназначен для создания полых моделей с помощью метода «в обкатку», 325 незаменим для точного воспроизведения цвета, 385 отверждается практически без усадки и максимально точно копирует изделие.
• Серия TASK
Серия полиуретанов специального назначения. Разработана для промышленного применения и обладает специфическими свойствами для конкретных задач.
Для Вашего удобства мы сформировали специальные фильтры по сферам применения:
• Пищевые:
Smooth-Sil 940, серия Sorta Clear, серия Equinox, TASK 11.
• Архитектурные, заливка бетона и других абразивных материалов:
Серия VytaFlex, серия Brush-On, серия Ez-Spray, серия PMC.
• Медицинские: симуляция тканей и органов
Серия Dragon Skin, добавки Slacker, Ecoflex 0030, Ecoflex Gel, Body Double.
• Прототипирование:
Практически любые полиуретаны и силиконы, в зависимости от задач и требований. Серии Mold Max, Mold Star, Smooth-Cast, TASK.
• Спецэффекты и грим:
Skin Tite, Body Double, Dragon Skin, Alja-Safe, Ecoflex, Soma Foama, Rubber Glass, Encapso K.
Обзор процесса
Мы будем использовать только те материалы и оборудование, которые можно применить в домашних условиях. Мы попробуем создать самую сложную в изготовлении двухсоставную форму.
Нам понадобятся:
• Платиновый силикон Mold Star 30
• Заливочный полиуретан Smooth-Cast 300
• Лак для 3D-моделей XTC-3D
• Упаковка виниловых перчаток
• Несколько одноразовых пластиковых стаканчиков
• Емкости для смешивания
• Термоклеевой пистолет
• Материал для опалубки (пластиковые панели)
• Скульптурная глина
• Несколько малярных кистей
В роли мастер-модели выступит модель довольно популярного среди печатников тестового болта. Мы распечатали его черным PLA пластиком на Picaso 3D Designer с толщиной слоя 100 микрон. Сделали мы это специально для того, чтобы продемонстрировать эффект XTC 3D, поскольку далеко не каждый 3D принтер может печатать с качеством 50 микрон.
Далее — обработка, чтобы отлитая модель не переняла слоистость напечатанного объекта. Обрабатываем болт лаком XTC-3D (подробнее об этом процесс можно прочитать тут), а затем шкурим, чтобы получить гладкую матовую поверхность.
Теперь модель готова к заливке силиконом. Помещаем её на глиняную основу, с помощью которой мы создадим силиконовую форму из двух частей.
Модель должна быть погружена в глину ровно наполовину, так что начинаем процесс выравнивания глины. Края должны быть максимально ровными и полностью прилегать к модели, от этого зависит качество разделения силиконовых половинок. Убираем лишнюю глину и заключаем модель в пластиковую опалубку.
Все стыки пластика обрабатываем термоклеевым пистолетом и закрываем опалубку, окончательно обрабатываем глиняную основу, делаем в ней выемки для замков.
Все готово к заливке силикона. Поскольку двухкомпонентные силиконы и полиуретаны склонны к разделению на фракции, перед каждым использованием их необходимо тщательно перемешивать в емкости.
После перемешивания отмеряем равное количество двух компонентов по объему и приступаем к смешиванию.
Для данной марки силикона дегазация в вакуумной камере необязательна, что очень удобно: исключены появления пузырьков, которые могут испортить нашу форму. Медленно заливаем силикон в опалубку, в самую нижнюю её точку.
И оставляем застывать. Время застывания для этой марки силикона составляет 6 часов. По истечении этого времени освобождаем модель от опалубки.
Затем убираем глину, тщательно очищаем модель от её остатков, смазываем силикон разделительным составом. В случае его отсутствия, можно использовать и обычный вазелин, но качество будет немного хуже.
И дальше полностью повторяем процесс, заливая вторую половину силиконовой формы.
Спустя еще 6 часов силиконовая форма готова. С помощью лезвия аккуратно разъединяем половинки, вынимаем деталь и оцениваем, что у нас получилось.
Хорошо видны замки, закладывавшиеся в глиняной основе, хорошая детализация, несмотря на то, что разделительная линия проходила по довольно сложным местам, вроде вдавленных букв.
На самом деле, для данной модели это не самый оптимальный способ создания формы. Но нам было интересно протестировать именно этот метод, несмотря на сложности.
Итак, все готово к заливке полиуретана. Соединяем две половинки формы, используя элементы опалубки для жесткости, скрепляем с помощью резинок, скотча или другим способом, и приступаем к подготовке полиуретана.
Хорошо перемешиваем оба компонента, встряхивая их в течение 5-10 минут. После этого даем немного отстояться, чтобы вышли образовавшиеся пузыри. Все остальное точно так же, как и с силиконом: отмеряем равное количество по объему и смешиваем их. А дальше действовать нужно быстро: время жизни этого полиуретана составляет всего 3 минуты, а время начинает идти сразу, как вы смешали два компонента вместе. Так что мешаем быстро, но аккуратно, чтобы не создавать лишних пузырьков, и сразу заливаем в форму.
Примерно через 3 минуты, в зависимости от объема материала, произойдет быстрое схватывание пластика, а через 10 минут деталь готова к извлечению.
Модель готова. Переданы абсолютно все детали оригинала.
Заключение
Хочется отметить, что поистине огромные возможности использование материалов Smooth-On открывает в совокупности с 3D-печатью.
Теперь Вы можете получать изделия из огромного количества материалов с самыми различными свойствами, а не ограничиваться лишь классическими PLA и ABS. К тому же, доступным станет мелкосерийное производство: распечатав всего один экземпляр и должным образом его обработав, Вы сможете в довольно короткие сроки создать необходимое Вам количество копий в домашних условиях. Для достижения приемлемого результата вовсе не обязательно использование дорогостоящего оборудования.
В случае если Вам необходимы услуги мелкосерийного производства Top 3D Shop к вашим услугам.
Как сделать сырую резину в домашних условиях — MOREREMONTA
Если вам нужно сделать надежную, долговечную и прочную защиту от влаги, воспользуйтесь преимуществами жидкой резины. А для этого не помешает знать, как расплавить резину до жидкого состояния. Ведь именно в таком виде она наносится на нужную поверхность, полностью покрывая ее и заполняя собой все впадины и трещины. Она хорошо сцепляется с любым покрытием, а после затвердевания превращается в твердый и прочный защитный слой. Жидкую резину можно применять во многих сферах, начиная от строительства для изоляции зданий от контакта с водой, до ремонта автомобилей и колес велосипедов.
Как расплавить резину до жидкого состояния
Сам процесс достаточно прост, из дополнительных материалов понадобится только растворитель, например, бензин. Залейте им резину и подождите, пока она набухнет. Затем добавьте еще бензина, чтобы получить нужную консистенцию. Чтобы ускорить растворение, можете подогреть раствор на водяной бане. Но учтите, что делать это можно только на улице или в хорошо проветриваемом помещении. В результате химической реакции выделяется очень неприятный и опасный для здоровья запах.
Следует понимать, что расплавить удастся не любую, а только сырую резину. Полученный раствор будет напоминать клей. А вот старые покрышки для этого не подойдут, поскольку они сделаны из сшитой серой резины. Такой материал в углеводородных растворителях не растворяется.
Если вам не удалось достать сырую резину, можно воспользоваться и подошвами из старых ботинок. Единственное требование – они должны быть изготовлены из тероэластопласта (сополимер бутадиена и стирол) без вулканизации.
Жидкая резина своими руками
Сделать жидкую резиновую массу можно и в домашних условиях и это более доступный способ, чем искать сырую резину. Вам понадобится купить всего лишь 1 пачку буры и 2 бутылочки клея ПВА. Само приготовление заключается в следующем:
- Смешайте буру с 0,5 ст. воды, чтобы жидкость стала прозрачной.
- Добавьте клей и снова хорошо перемешайте.
При необходимости можете окрасить резину в нужный цвет. Для этого предварительно добавьте в клей краситель и только после этого смешивайте с разведенной бурой.
Домашнюю жидкую резину можете использовать сразу или же поставить в холодильник. Там она сможет некоторое время храниться в жидком виде, не застывая.
Как сделать пористую резину – видео
11 апреля 2018
Резина бывает летняя, зимняя, иногда даже жидкая. Последнюю используют в строительстве для герметизации или для защиты поверхностей от влаги
Последняя стоит недешево, да и покупать целую упаковку нет смысла, если тебе нужно лишь несколько граммов.
Зачем покупать жидкую резину, если ее можно изготовить и собственноручно. Как? Знает ведущий шоу “Оттак мастак“ на телеканале НЛО TV Сержио Куницын.
Для этого понадобится:
- 1 упаковка буры
- 2 бутылки клея ПВА
- полстакана воды
- краситель (по желанию)
- две емкости
- палочка для размешивания.
Смешиваем в одной посудине воду с бурой. Размешиваем, пока жидкость не станет прозрачной. В другом сосуде смешиваем клей с красителем и добавляем туда жидкость. Тщательно перемешиваем. После того как жидкость застынет, ее можно наносить на поверхность.
Такая резина прилипает (пристает) к любой поверхности даже при повышенной влажности. Она способна проникнуть во все поры, щели, трещины, заполнить их и герметизировать.
Видеоинструкция (производство жидкой резины своими руками) здесь. А еще больше лайфхаков — по будням в 06:30 на телеканале НЛО TV.
Еще один способ овладеть искусством производства жидкой резины в домашних условиях + умением покрыть этой резиной поверхность — смотри в следующем ролике:
Силиконом называется кремнийорганический материал, довольно мягкий и пластичный, поэтому его применяют для изготовления разного вида форм для статуэток и фигур, и не только. Его подобие можно изготовить и в домашних условиях.
Но прежде чем перечислить способы его изготовления, давайте разберемся, где применяется этот материал.
Где применяют силикон
Этот материал используется практически во всех сферах человеческой жизни — в строительстве, быту, медицине и на производстве. Популярность силикон заслужил благодаря своим уникальным и ценным качествам, которые отсутствуют у аналогов этого вещества.
Силикон способен уменьшать, наращивать процесс адгезии, а также придавать целевому предмету свойства гидрофобности. Этот универсальный материал способен сохранять свои базовые параметры при экстремально высоких, низких температурах и в условиях повышенной влажности. Помимо этого, силиконы обладают диэлектрическими характеристиками, биоинертностью, высокой степенью эластичности, долговечны и экологичны.
В промышленных масштабах силиконовые жидкости и эмульсии на их основе, используют в качестве антиадгезионных смазок для огромных тяжелых пресс-форм, изготовления гидрофобизирующих жидкостей, пластичных смазок, специальных масел, амортизационных, охлаждающих веществ, теплоносителей, герметиков и диэлектрических составов. Особенно популярными являются пеногасители, произведенные на основе силиконовых смесей.
Из этого материала производят силиконалкиды, силиконполиэфиры для различных покрытий, которые должны характеризоваться особой стойкостью и устойчивостью. Отсюда следует, что разного вида прокладки, втулки, кольца, манжеты, заглушки и другие детали можно использовать при температурах от минус 60о С и до плюс 200о С.
Еще одним свойством силикона является устойчивость к таким веществам, как озон, радиация, морская вода, ультрафиолетовое излучение, кипяток, спирт, кислотные растворы, щелочи, минеральные масла, различные топлива и электроразряды.
Как сделать силикон в домашних условиях
Первый способ
Для приготовления силиконового каучука (полидиэтилсилоксана) понадобятся жидкое стекло и этиловый спирт. Берется пластиковая емкость, в которую наливаются компоненты в равных пропорциях и аккуратно перемешиваются любым инструментом. Когда смесь загустеет, нужно доводить до состояния пластилина разминая руками.
Далее, из силиконовой массы можно лепить необходимые формы, которые оставить затвердевать на некоторое время, пока изделие не станет твердым.
Второй способ
- 150 г уайт-спирита;
- 1 капля акриловой краски;
- 3 капли жидкого глицерина;
- 30 г силиконового герметика.
Для изготовления силикона нужно погрузите герметик в емкость, добавить туда краску, глицерин и уайт-спирит. Раствор нужно перемешивать до получения однородной массы. С этим раствором можно работать не более пяти часов, так как после этого времени он затвердевает.
Третий способ
Нужно взять равное количество силиконового герметика и картофельного крахмала. Перемешивать массу около 10 минут, пока силикон не начнет легко отставать от рук, тогда можно приступать к изготовлению необходимой формы.
Четвертый способ
Берется желатин и глицерин в равных пропорциях, тщательно перемешиваются. Затем раствор нужно греть на водяной бане примерно 10 минут, постоянно перемешивая. Важно не допустить закипания желатина, иначе может появиться резкий неприятный запах.
Пятый способ
Он используется для изготовления силикона для форм своими руками. Для этого нужно взять форму немного большего размера, чем копируемый объект. На дно формы наливается немного силикона и оставляется до застывания — это основание предмета.
Толщина основания должна быть один сантиметр и более, чтобы «домашняя резина» надежно обертывала предмет со всех сторон. Если форма выйдет тонкой, тогда быстро порвется при извлечении прототипа или совсем не будет держаться.
Затем прототип окунается в емкость с желатином для избавления от воздушных пузырей, а затем быстро переносится на дно формы, чтобы приклеился. Затем форму нужно полностью заполнить силиконом. Хорошо подойдет самодельная смола из четвертого способа, которая твердеет очень быстро. Сразу после остывания форму необходимо разобрать, сделать надрез и аккуратно извлечь прототип.
На последнем этапе, потребуется замешать и залить в форму эпоксидную смолу. Застывший отливок извлечь будет сложно, поэтому нужно будет полностью разорвать силикон.
Избавляемся от силикона на одежде
Силиконовые герметики широко применяются в ремонте и строительстве. Но небрежное обращение с этой субстанцией может привести к образованию стойких пятен на ткани, и для избавления от них придется использовать специальные очистители или подручные средства.
- Кислотно-силиконовый герметик обладает характерным запахом уксуса, при этом его удаление производится при помощи 70% раствора уксусной кислоты. Удаляя пятно от такого силикона, нужно принять меры предосторожности: надеть очки, крепкие резиновые перчатки и респиратор, так как уксусная кислота отрицательно влияет на глаза, кожу руки и дыхательные пути. Для очищения пятна нужно его обильно, оставить на 30 минут и удалить силикон ветошью.
- Силиконовый нейтральный герметик на основе спирта легко удаляется при помощи спиртосодержащих жидкостей. Можно взять медицинский, технический, денатурированный спирт или водку и нанести на загрязненное место, а затем удалить пятно щеткой.
- Оксимный, аминнный или амидный силиконовый герметик удаляется с помощью уайт-спирита, бензина, ацетона или растворителя. Жидкость наносится на губку, затем на пятно и оставляется на 30 минут до растворения силикона. При необходимости обработку можно повторить. Затем постирать ткань обычным способом со стиральным порошком.
Также существуют специальные составы для очищения поверхности тканей от силикона. Идеально подойдет смывка под торговым названием «Пента-840» или ANTISIL. Необходимо, перед применением любого средства внимательно ознакомьтесь с прилагаемой инструкцией.
Помимо этого, силиконовое пятно можно очистить механическим способом при помощи пластикового скребка. Для этого ткань натягивается на ровную поверхность и пятно аккуратно соскабливается. Остатки можно удалить одним из перечисленных выше способов.
Важно! Работать с силиконовыми герметиками нужно только в хлопчатобумажной плотной одежде, так как удалить его остатки с деликатных вещей без помощи специалистов химчистки не получится!
Удаляем силикон с рабочих поверхностей
Силикон является средством, помогающим склеивать поверхности и герметизировать швы. Это вещество препятствует проникновению воздуха и влаги. Герметики с антибактериальным составом применяются для работы в ванных комнатах, для автомобилей, в строительстве, любителями аквариумов и т. д. Герметик не так легко удалить с поверхности, но возможно.
Герметик производится на основе растворителей, которые придают этому составу резкий запах. Помимо запаха, растворители придают силикону эластичность и помогают более крепкому сцеплению поверхностей.
Поэтому для удаления силикона часто используют химические вещества, которые продаются в магазинах.
Но и при помощи народных методов можно удалить силикон с любой поверхности, для чего используют уайт-спирит, тряпки, лезвия и моющие средства.
Для удаления силикона с рабочей поверхности нужно сначала смочить его уайт-спиритом при помощи тряпки. Примерно через 60 секунд силикон приобретет желеобразную консистенцию и легко поддастся очистке лезвием. Затем это место нужно промыть моющим средством и насухо вытереть ветошью.
Еще силикон можно удалить механическим способом, при помощи ножа и пемзы. Но этот вариант подходит для поверхностей, которые не подвержены царапинам и сколам.
Видео
Из этого видео вы узнаете, как можно самостоятельно сделать силикон.
переработка шин в домашних условиях с помощью дробилки, самостоятельная сборка измельчителя для резины и покрышек
Каждый год тысячи покрышек пропадают на свалках и полигонах, несмотря на то, что для предприимчивого человека они являются бесплатным ресурсом, из которого можно производить резиновую крошку.
Если она понадобилась лишь единожды, можно купить ее в нужном количестве у производителей.
Но где взять резиновую крошку, если она нужна на постоянной основе и в больших количествах?
Стоит задуматься о приобретении собственного оборудования для переработки шин.
Однако полноценная установка не всем по карману, и не для всех окажется рентабельным такое вложение. Выход — создать оборудование своими руками, и с его помощью производить резиновую крошку из покрышек в домашних условиях.
Переработка небольшого количества резины в домашних условиях
Если сырья нужно совсем мало, можно обойтись вовсе без оборудования.
Для этого потребуются потребуются только ножницы и резак.
С покрышки вначале убирают металлический корд, затем разделяют на ленты и измельчают их на более мелкие фракции до необходимого размера.
На этом процесс считается законченным.
Материал для оформления дорожек, клумб или отдельной детской площадки готов к использованию.
Но чтобы получить больший объем сырья или иметь доход от переработки шин в домашних условиях, нужно соответствующее оборудование.
Сооружение дробилки для переработки шин
Применяются три основных способа производства крошки:
- Дробление шин после их охлаждения жидким азотом до –190 градусов.
- Получение крошки на промышленном оборудовании полного цикла с удалением корда и последующим измельчением резины.
- Переработка с использованием универсальных дробилок, которую можно осуществлять в домашних условиях самому.
Первые два способа требуют больших инвестиций. Третий вариант доступен каждому, кто имеет возможность и желание изготовить дробилку дома.
Необходимые агрегаты можно изготовить самостоятельно в мастерской или на производственном участке – там, где есть металлорежущие станки (токарные, фрезерные) и сварочный аппарат для изготовления комплектующих деталей.
Если нельзя самостоятельно выполнить механическую обработку заготовок и придется заказывать их по своим чертежам, все равно стоимость станков по переработке шин будет в несколько раз дешевле, чем аналогичных покупных агрегатов.
Основным комплектующим устройством на линии по переделке покрышек является шредер (измельчитель для резины). Рассмотрим более подробно и назначение узлов данного станка.
Устройство агрегата
Станок состоит из следующих основных узлов:
- электродвигатель 5 кВт – 2 шт;
- корпус с дисковыми валами;
- решетка;
- редуктор червячный – 2 шт;
- каркас шредера;
- загрузочный бункер;
- направляющий лоток;
- шкаф управления.
Детали установки монтируются на мощной раме, сваренной из швеллеров.
Коробка с режущими дисками
Главным узлом дробилки для резины является корпус с фрезерными валками.
При этом режущие ножи выполнены из высокопрочной стали и термически обработаны, что ощутимо снижает их износ. Они практически не требуют заточки во время эксплуатации.
Расчет отверстий коробки, валов и режущих элементов должен быть точный, поэтому его нужно производить специалисту в этой области (конструктору).
Решетка для калибровки крошки
Для того чтобы получить калиброванную фракцию шинного сырья, шредеры снабжаются специальной решеткой, которая устанавливается под валками.
Редуктор червячный
Вращение валов с дисковыми фрезами осуществляется обособленно, непосредственно от червячных редукторов, соединенных с электродвигателями через муфты.
Передаточное отношение выбирается от 25 до 35 таким образом, чтобы резание было без заедания и с достаточной скоростью.
Рама агрегата
Каркас сварен из профильных элементов, обеспечивает надежность и устойчивость агрегата во время работы, а также погрузочно-разгрузочных действий.
Загрузочный бункер
Установка для переработки шин оборудуется бункером загрузки покрышек и лотком при выемке готовой резиновой крошки.
Благодаря своей конструкции бункер исключает образование заторов из сырья и гарантирует направленное движение массы к вращающимся валкам.
Приспособление для разрезания покрышки
Установка для разрезания шины и удаления корда состоит из несущей рамы и стойки.
На каркасе находится зажимной механизм шины, вращающийся вместе с покрышкой во время резания. Обороты двигателя уменьшены за счет разного диаметра шкивов. На стойке расположен встроенный клиновидный резак, который настраивается на определенный размер за счет перемещения пиноли.
Как измельчить покрышки?
Технологичная цепочка представляет собой несколько подготовительных этапов, прежде чем получится продукция необходимой фракции.
Эта процедура включает:
- Осмотр и удаление посторонних предметов из полости покрышки.
- Вырезка корда.
- Нарезка шины на ленты размером 50-80 мм.
- Измельчение сырья посредством шредера.
- Сепарирование и отделение металлических от текстильных частей.
- Калибрование крошки на фракции с помощью вибрационного сита.
Производительность оборудования
Работа этих двух основных агрегатов при переработке покрышек делается в полуавтоматическом режиме.
Для нормальной работы этой линии необходимо помещение около 150-200 кв. метров. Это вызвано тем, что нужно место для расположения не только оборудования, но и для складирования изношенных покрышек, готовой шинной продукции и металлических отходов.
Выпуск резиновой крошки на данном оборудовании за час составит примерно 200-800 кг и до 100 кг металлического лома, для обслуживания станков понадобится 2-3 работника без квалификации.
Кроме покрышек, на этом оборудовании можно перерабатывать другую резину (транспортерную ленту, камеры, противогазы). На выходе получается крошка с размерами от 0,7 до 4 мм, при этом она составляет 65-85% от всей массы сырья.
Куда применить полученное сырье?
Резиновую крошку можно:
Цена крошки будет зависеть главным образом от качества сырья, и уже во вторую очередь — от фракции.
Наиболее популярной является крошка, фракция которой составляет 2-4 мм.
Она отлично подходит для создания:
Популярность такой крошки вызвана тем, что на склеивание данных гранул идет минимальное количество клея. А полиуретановое связующее вещество иногда дороже крошки в 5-8 раз.
Видео по теме
В данном видео вы можете увидеть, как измельчить резину и сделать крошку в домашних условиях.
Заключение
Создание дробилки для шин своими руками — хорошая идея для тех, кто хочет сделать резиновую крошку своими руками, но не готов тратить десятки тысяч долларов на оборудование.
Создать измельчитель можно при наличии столярной мастерской, а также определенных навыков и материалов, либо воспользоваться услугами людей, которые на этом специализируются.
Полученную в домашних условиях крошку можно использовать для своих нужд или реализовывать предприятиям и населению.
Вконтакте
Одноклассники
Мой мир
Как сделать самодельную автошину — (старые методы) » Полезные самоделки
Автомобильные и мотоциклетные изготавливают с наличием так называемого «каркаса», силовой части, воспринимающей толчки и удары, которые испытывает при движении колесо. Даже на ровной дороге количество таких толчков весьма велико. Если изготовить шину из одной только резиновой массы (а модельные шины именно так и изготовляются), она очень быстро потеряет форму и разрушится, не выдержав прилагаемых к ней нагрузок, Чтобы этого не случилось, в конструкцию шины вводится каркас.
Он состоит из большого количества прочных нитей, которые расположены по всему ее периметру и образуют как бы сетку, которая способна выдерживать высокое давление заключенного в шине воздуха и большое количество толчков и ударов, воспринимаемых шиной извне. А для того, чтобы шина надежно держалась на ободе колеса, в ее борта заформовываются кольца из гибкой стальной проволоки.
Детали каркаса шины соединяются между собой резиновой массой, имеющей достаточную прочность и эластичность. А внешняя часть шины защищается слоем протектора — из резины более жесткой. Толщина и рисунок протектора зависят от назначения шины. Например, для езды по бездорожью применяется более высокий и крупный рисунок протектора (так называемые «грунтозацепы»).
А для асфальта изготовляются шины с более мелким рисунком. Поперечный разрез шины показан на рис. 1. и рис. 2
Рис.1. Поперечный разрез самодельной шины.
На микромотоциклах шины работают в исключительно тяжелых условиях. К примеру, если нормальное мотоциклетное колесо при прохождении десяти метров дороги должно повернуться вокруг своей оси восемь раз, то колесо микромотороллера совершает в три или четыре раза больше оборотов, поскольку диаметр его меньше.
Так, при скорости 70 км/час колесо микромотоцикла диаметром 320 мм должно делать 1200 об/мин. При таких больших оборотах частота деформаций шины и нагрев очень велики. Перегрев шины приводит к ее быстрому разрушению. В самых неблагоприятных условиях находится шина заднего колеса.
У микромотоциклов примерно г/з веса приходятся на заднее колесо, которое к тому же охлаждается хуже, чем переднее. Вследствие небольших размеров микромотоциклов и микромотороллеров расстояния между горячим двигателем и колесами очень невелики. От этого шины могут быстро перегреваться.
Поэтому самой трудной проблемой при проектировании шин для микро мототранспорта является увеличение их теплоотдачи. Стенки шины, имеющие большую теплоемкость, не позволяют рассеивать в окружающее пространство необходимое количество тепла.
Уменьшать толщину покрышки можно только в определенных допустимых пределах, поскольку нагрузка на нее очень велика. Учитывая все это, при конструировании микрошин мы руководствуемся следующими соображениями: каркас покрышки изготовляется из двух слоев высокопрочного капронового корда, больше других материалов отвечающего условиям работы в шине, поскольку он обладает малым весом и высоким сопротивлением многократным изгибам. Мы изготовили несколько покрышек из вискозного и хлопчатобумажного корда, каркасы которых ввиду малой прочности пришлось делать 4-х слойными. эти покрышки быстро выходили из строя из-за перегрева.
При накачивании шины воздухом в нитях слоев корда действуют большие растягивающие усилия. Величина этих усилий зависит не только от давления воздуха, но и от количества слоев корда, и от геометрического профиля шины, ее размеров, нагрузки и ширины обода. Каждый профиль шины рассчитан на определенную ширину обода. Применение ободьев от детских роллеров (самокатов) не обеспечивает необходимых условий для нормальной работы шин, даже при скорости движения 40 км/час и нагрузке порядка 50 кг. Для обеспечения необходимых условий работы ободья должны быть значительно шире (не менее 35-З8 мм между буртиками). В этом случае можно изготовить покрышки, рассчитанные на нагрузку 60-80 кг и скорость порядка 60-70 км/час.
Геометрический профиль спроектированной нами шины приведен на рис. 2 в натуральную величину, а конструкция покрышки изображена на рис. 3.
Рис.3. Конструкция авто шины.
Технология изготовление шин (мини завод по производству шин
При работе покрышки важно, чтобы нити корда были хорошо изолированы,, друг от друга резиной и не перетира лись. Для этого между слоями корда (хотя он уже обрезинен) прокладывается тонкий слой резины (0,5 мм), так называемый «сквидж». Для этой цели можно использовать сырую резину, применяемую для ремонта автомобильных камер в автохозяйствах. Наличие слоя эластичной резины между слоями корда и такой же резины поверх всего каркаса не только предотвращает перетирание нитей корда, но сообщает каркасу эластичность и увеличивает прочность связи между слоями каркаса и следующим слоем, называемым брекером.
Брекер — это дополнительный слой эластичной резины толщиной 2- 2,5 мм, служащий для повышения прочности связи каркаса покрышки с протектором. Он предохраняет каркас от возможных пробоев и повреждений. При резких торможении и ускорении получается внутренний сдвиг между малоэластичным, но износостойким слоем протекторной резины и каркасом. Задача брекерного слоя — погасить энергию этого сдвига, не дать шине расслоиться. Резина брекера должна быть эластичной, теплостойкой и прочной на разрыв.
При сборке шины брекерная лента делается шире протекторной на 5-6 мм. Для нее наиболее подходящей является готовая сырая резина на основе изопренового или натурального каучука. Но поскольку такую резину не всегда возможно достать, нами с успехом применяется следующий способ: берем обычную сырую резину, предназначенную для ремонта камер (толщина примерно 0,8-1 мм) и кусок натурального каучука для изготовления резинового клея. Из него остро отточенным ножом вырезаются пластинки толщиной 1-1,5 мм. Затем, тщательно промазав клеем для горячей вулканизации заготовленную полоску из сырой резины и нарезанные пластинки каучука и дав клею подсохнуть 5-6 мин., наклеиваем пластинки на полоску сплошным слоем, без щелей и наползания друг на друга.
Полученная двухслойная лента приклеивается к каркасу стороной из каучуковых пластинок, а затем на нее наклеивается протекторный слой. Протектор изготовляется из высокопрочной, износостойкой резины. Он располагается только на беговой дорожке покрышки. Его толщина зависит от величины самой шины. Для наших шин, имеющих диаметр 320 мм, толщина протектора должна быть в пределах 4-6 мм. Качество протектора определяет долговечность шины, поэтому требования к резине, из которой он изготовляется, несколько иные, чем к резине брекерного слоя. Наилучшей оказывается резина, предназначенная для ремонта протекторов покрышек автомобилей.
Для большего удобства сборки шины двухслойную ленту брекерного слоя и ленту протекторного слоя можно склеить между собой, а затем уже приклеить полученную трехслойную ленту к каркасу покрышки. Ширина протекторной ленты для наших покрышек равна 50-55 мм.
Рисунок протектора может быть различным, в зависимости от назначения шины и условий эксплуатации.
Показанный на рис. 4 рисунок протектора является универсальным. Шины с таким протектором одинаково хорошо работают на дорогах с самыми различными покрытиями.
Рис.4. Универсальный рисунок протектора шины.
Изготовление матрицы для получения такого рисунка протектора не представляет трудностей и может быть выполнено даже в домашних условиях.
Для этого берется полоса мягкого алюминия толщиной 4-6 мм (толщина материала определяет желаемую глубину рисунка) и в ней согласно рис. 5 высверливаются отверстия. Затем полоса разрезается ножовкой вдоль по осевой линии на две равные части. В каждой части выпиливаются фасонные пазы, острым ножом снимаются фаски и заусенцы, напильником выравниваются все неровности, а концы, оставшиеся после выпиливания шипов, стачиваются под углом 45°.
Рис.5. изготовления матрицы для рисунка протектора.
После окончательной зачистки шкуркой части матрицы приклепываются заклепками из мягкой алюминиевой проволоки к половинкам пресс формы с ее внутренней стороны. Такая конструкция пресс формы позволяет избежать сложных фрезерных работ. Сама пресс форма изготовляется путем отливки в землю, из алюминия или другого легкого сплава (нами были использованы для этого старые поршни от автомобильных двигателей, собранные на свалке).
Оснастка для отливки (форма и ящик) показаны на рис. 6. Расплав алюминия можно вести прямо в форме, нагревая его пламенем газовой горелки или, как обычно, в муфельной печи. Мы, например, выполнили отливку на месте ремонта металлической ограды парка, где велись газосварочные работы.
Рис.6. Оснастка для отливки шин.
Отливки надо вынимать из формы, не разрушая ее, и только после полного их остывания. Ускорять остывание, смачивая отливку водой, нельзя.
Подготовка матрицы заканчивается сверлением отверстий под болты, стягивающие ее во время варки покрышки.
Отлитые заготовки для пресс-формы обрабатываются на токарном станке в соответствии с рисунком. Особое внимание должно быть уделено подгонке половинок формы и дисков друг к другу, а также тщательной наклепке решетки протектора (рис. 2).
Сборка покрышки
В качестве оправки для сборки мы используем негодную («лысую», но не деформированную) покрышку от детского самоката. Сначала на наждаке, а потом — шкуркой разной зернистости с нее удаляются остатки протектора, чтобы поверхность стала совершенно гладкой.
Заправив внутрь обработанной таким путем покрышки камеру и слегка подкачав ее воздухом, сшиваем внутренние края покрышки прочными нитками, тщательно прихватывая при этом и бортовые кольца. Расстояние между бортами должно быть одинаковым по всей окружности (рис. 9).
Порядок сборки покрышки на оправке
1) Приготовление кусков обрезиненной кордовой ткани.
Их длина должна быть такой, чтобы после оборачивания вокруг оправки под углом 52° на загиб вокруг бортового, (проволочного) кольца оставалось 20-25 мм.
2) Накачивание воздухом оправки.
3) Укладка первого слоя корда.
При этом необходимо слегка растягивать середину заготовок, увеличивая тем самым расстояние между нитями с таким расчетом, чтобы они были одинаковыми по всему периметру колеса. Нити корда должны ложиться ровно, в один слой, и не наползать друг на друга даже в месте расположения бортового кольца (там, где густота нитей максимальна). Для облегчения укладки не рекомендуется делать слишком широких заготовок корда, удобнее всего ширина 40-50 мм.
4) Укладка бортовых колец из стальной проволоки диаметром 0,25-0,3 мм — очень ответственная операция.
Как показала практика, быстрый выход из строя покрышек от детских самокатов объясняется именно плохим качеством бортовых колец — они расходятся, так как концы их ничем не скреплены, посадочный диаметр покрышки изменяется, и это приводит к саморазбортовыванию колеса. Для изготовления кольца в качестве оправки мы используем сам обод колеса.
Для этого необходимо сначала вырезать полоску из 3-мм резины (например, из старой автомобильной камеры) шириной 10-12 мм и из нее склеить кольцо диаметром несколько меньше посадочного места обода. Это кольцо натягивается на обод, затем из сырой резины толщиной 0,5 мм вырезается ленточка шириной 10 мм и из нее делается один виток вокруг надетого на обод кольца. Наматывая после этого проволоку (8- 10 витков) непосредственно на сырую резину, большой натяг делать не следует, так как можно прорезать тонкой проволокой резину насквозь. Скрепив концы готового кольца скруткой, обильно смажем его клеем, дадим подсохнуть и завернем, не снимая с обода, в ленточку из сырой резины, на которую оно наматывалось. Готовое кольцо снимается с обода вместе с резиновым кольцом, которое можно использовать многократно.
Промазывание клеем и обрезинивание проволочного кольца необходимо для того, чтобы проволока не отслаивалась от борта покрышки при ее дальнейшей обработке.
Для каждой покрышки надо изготовить два кольца. Они тщательно промазываются клеем и укладываются на свои места после укладки первого слоя корда.
5) Оклейка сырой резиной толщиной 0,5-0,7 мм поверхности первого слоя корда.
Приклеенная резина не должна наползать на бортовые кольца. Но не должно оставаться больших промежутков между ними; обклеивать удобнее, предварительно нарезав, сырую резину в виде ленты, немного более широкой, чем расстояние между бортовыми кольцами, а затем — после приклейки — удалить ее излишки при помощи кривых маникюрных ножниц.
6) Заворачивание концов корда вокруг бортовых колец с приклейкой их к слою сырой резины (сквиджу).
Приклеенные концы не должны наползать друг на друга и быть длиннее 15-20 мм. Если они получились длиннее, их необходимо обрезать.
7) Укладка второго слоя корда. Она производится так же, как и первого, с той лишь разницей, что угол наклона нитей корда должен быть противоположен углу наклона первого слоя. Концы нитей корда второго слоя заворачиваются вокруг бортовых колец не наружу, как первого, а внутрь покрышки. Эту операцию удобнее сделать, когда готовая покрышка будет снята с оправки.
8) Приклеивание ленты брекерного слоя.
Лента должна закрывать беговую дорожку и несколько заходить на борта (примерно на 2-3 мм на каждую сторону).
9) Оклеивание бортов сырой резиной.
Применима сырая резина для ремонта камер толщиной 0,5-0,7 мм. Сначала ее нарезают в виде ленты, которая должна наклеиваться плотно к борту покрышки встык с краем уже наклеенной брекерной ленты. При этом надо тщательно приглаживать ленту к борту покрышки, чтобы не образовывались воздушные пузыри. Излишки бортовой ленты обрезаются кривыми ножницами по внутреннему (посадочному) диаметру покрышки.
10) Приклеивание слоя протекторной резины толщиной 4-5 мм.
Протекторная лента не должна заходить на борта покрышки и обязательно плотно прилегать к наклеенной ленте брекерного слоя.
11) Удаление оправки из покрышки.
Для этого из нее выпускают воздух, вынимают из покрышки, после чего второй слой корда заворачивается и приклеивается к внутренней поверхности покрышки с перехлестом порядка 15-20 мм. На этом сборка покрышки заканчивается. Желательно еще обклеить посадочные места собранной покрышки «чефером», то есть слоем обрезиненной ткани полотняного переплетения. Это укрепляет борта, что особенно важно, если покрышка будет эксплуатироваться на колесе, имеющем обод с мелким ручьем. Но если у обода глубокий ручей, как, например, у микромотоцикла «Агидель», — оклейке чефером не обязательна. Лента из чефера наклеивается на посадочные места так, чтобы по наружной стороне покрышки ширина ее равнялась 30-35 мм, а 20-25 мм было завернуто внутрь.
Рис. 7. Пресс-форма для отливки шин.
Рис. 8. Пресс-форма с решеткой протектора.
Рис. 9. Порядок сборки покрышки.
1 — участок с уложенным первым слоем, 2 — сшитые края понрышни1 3 вентиль, 4 — прослойка из сырой резины (толщина = 0,5 мм), 5 — второй слой корда, 6 — бортовое кольцо, 7 — завернутые наружу концы корда, 8 — вворачиваемые внутрь края корда.
Собранную описанным способом покрышку необходимо вулканизировать, чтобы придать ей износоустойчивость и прочность. Ведь сырая резина, из которой мы собирали покрышку, потому и называется сырой, что она не обладает достаточной стойкостью против различных механических и химических воздействий. Но после непродолжительного нагревания до определенной температуры сырая резина необратимо меняет свои физико-химические свойства — она становится практически нерастворимой, твердой, упругой, способной выдерживать большие ударные и растягивающие нагрузки и хорошо сопротивляться истиранию. Этот процесс называется вулканизацией.
Вулканизация в настоящее время широко применяется не только в промышленности, но и для бытовых нужд, например, при ремонте резиновой обуви и других предметов обихода. Портативные вулканизаторы, работающие от аккумулятора или снабженные бензиновой горелкой, позволяют ремонтировать автомобильные камеры в пути.
Клей для горячей вулканизации
Такой клей не всегда удается достать, но его можно изготовить и в домашних условиях. Для этого натуральный каучук растворяют в чистом бензине (авиационном, или так называемом «калоша») и на один литр клея добавляют 50 г порошкообразной серы. Если такой серы в готовом виде нет, следует размельчить кусковую серу и просеять ее через металлическое сито с ячейками 0,2X0,2 мм. Перед нанесением клея на поверхность вулканизированной резины она должна быть подготовлена: тщательно зачищена на наждачном круге или вручную — крупнозернистой шкуркой. Касаться пальцами зачищенных поверхностей нельзя. Сырую резину зачищать не нужно. Если ее поверхность окажется загрязненной, достаточно протереть тряпочкой, смоченной в бензине.
Нанеся клей на обе склеиваемые поверхности, их подсушивают на воздухе и плотно прижимают друг к другу, следя За тем, чтобы между ними не оставалось воздушных пузырьков. При склейке колец, варочных или ходовых камер концы ленты надо не только зачистить, но и свести на конус, чтобы толщина склейки не была толще самой ленты. Если клей долго стоял без употребления, его необходимо тщательно размешать, доставая до дна Посуды, в которой он хранился, так как сера со временем осаждается на дно.
В. Петровский, г. Уфа
Переплавка пластиковых бутылок в домашних условиях — как расплавить пластмассу и зачем
В этом руководстве я расскажу вам, как плавить пластмассу в домашних условиях. Переплавка пластиковых бутылок из полиэтилена высокой плотности (HDPE) и изготовление из них блоков, которые можно использовать разными способами.
Каждый день мы используем и выбрасываем много пластиковых бутылок… Давайте изменим это!
Дэйв Хаккенс удивительный парень, который сделал много видео об утилизации пластика. Он показывает, как собирать, расплавлять и обрабатывать пластиковые предметы, чтобы создавать новые вещи. Однако, если вы хотите просто попробовать переработать несколько бутылок, следуйте этому краткому руководству.
Шаг 1: Материалы и инструменты
МАТЕРИАЛЫ:
- Бутылки из полиэтилена высокой плотности (HDPE)
- Деревянные дощечки (для изготовления формы)
ИНСТРУМЕНТЫ:
- зажимы
- бумага для выпечки
- перчатки с термозащитой
- ножницы/нож
Шаг 2: Форма
Нет необходимости делать очень сложную форму для плавки пластика.
Поскольку мы собираемся расплавить пластик и получить обычный блок, нам нужна простая коробка. Чем точнее и аккуратнее будет собрана коробка, тем точнее и аккуратнее будет блок.
Как вы можете видеть из приведенных выше рисунков, я использовал деревянные доски, которые лежали в моей мастерской, так же я накрыл каждую внутреннюю поверхность коробки бумагой для выпечки. Это будет важно позднее, когда будем извлекать блок из формы. Древесина — пористый материал, а расплавленный пластик — очень липкий, так что не стоит им соприкасаться.
Шаг 3: Как разрезать бутылки
Прежде всего, HDPE, что это такое? Как можно отличить его от всех других видов пластика?
HDPE — полиэтилен высокой плотности. Это довольно распространенный материал, используемый специально для производства пластиковых бутылок и коррозионностойких трубопроводов.
Как вы можете видеть на рисунке №1, его легко отличить от другого типа пластика благодаря цифре «2» в качестве идентификационного кода смолы.
После удаления этикеток и мытья бутылок нам нужно разрезать их на мелкие кусочки. Чем меньше, тем лучше, так как потребуется меньше времени для плавления. Используйте нож или крепкие ножницы.
Обычно я начинаю с ножа, отрезаю горлышко (фото № 2), которое является более жесткой частью, затем отрезаю основание и, наконец, ручку.
После этого вы можете использовать ножницы, чтобы сделать из больших кусков более мелкие (фото № 4).
Шаг 4: Плавление
Каждый тип пластика имеет разную температуру плавления.
Дэйв Хаккенс отлично изучил каждый тип, чтобы индивидуализировать правильную точку плавления (здесь вы можете увидеть его работу).
Я узнал, что в моей печи HDPE обычно плавится при температуре около 180°C.
В то время пока нагревается духовка, положите кусок бумаги для выпечки на противень и расположите на ней кусочки пластика. Наконец поместите противень в духовку и проверяйте его каждые 10 минут.
Шаг 5: Эффект мрамора
Первый раскрас, который я покажу вам, мой любимый: эффект мрамора.
Через 10/15 минут, если вы видите, что пластик выглядит липким, вы можете вытащить его из духовки. Оденьте жаростойкие перчатки и скрутите пластик (фото № 2/3).
Действуйте быстро (пластик остывает), но имейте ввиду, что он очень горячий и липкий.
Как только у вас получится что-то вроде того, что вы можете увидеть на фото №4, вы можете положить обратно в духовку.
ПРЕДУПРЕЖДЕНИЕ: Используйте перчатки! Если пластик попал на вашу кожу, немедленно промойте пораженное место холодной водой, чтобы уменьшить боль.
Шаг 6: Закрепляем форму
Через 10 минут извлеките пластик из духовки и положите его в форму. Зажмите его так сильно, как можете, и каждые 5 минут, затягивайте зажимы сильнее. HDPE сжимается, когда он остывает, поэтому, чтобы получить плоский блок, вы должны часто затягивать зажимы.
Шаг 7: Мраморный блок
Это результат после 2 часов охлаждения.
Как видно из фото, благодаря технике крутильно-вращательного движения, которую мы использовали, получился прекрасный эффект мрамора. Мне очень нравится этот метод, потому что вы можете видеть все используемые цвета.
Шаг 8: Эффект «Камуфляжа»
Вот еще один раскрас. Я называю его эффектом камуфляжа.
Это проще и безопаснее, чем эффект мрамора, потому что нет нужды касаться пластика руками. Как и в Шаге 5, после 10/15 минут, если вы видите, что пластик выглядит липким, вы можете извлечь его из духовки.
На этот раз мы будем использовать технику складывания. Очень аккуратно (и всегда используйте перчатки), поднимите бумагу для выпечки с одной стороны и сложите пластик на себя (фото № 2).
Повторите тоже самое с другой стороны и положите обратно в духовку.
Шаг 9: Закрепляем форму
После 10 минут плавления выньте пластик из духовки, сложите в последний раз, сделав что-то вроде яичного рулета (фото № 1) и поместите его в форму.
Как и на шаге 6, зажмите его так сильно, как можете, и возвращайтесь каждые 5 минут, чтобы затянуть зажимы. Затем оставьте его остывать на пару часов.
Шаг 10: Камуфляжный блок
Вот результат. Выглядит действительно как камуфляж.
Шаг 11: Что можно сделать из блоков?
Эти блоки невероятно прочные, простые и тяжелые. Вы можете использовать их по-разному.
На фотографии № 3 вы можете увидеть, кастет, спиннер, несколько брелков и юлу. На сайте preciousplastic вы можете найти другие способы применения HDPE, такие как, например, плитка — фото № 1.
Шаг 12: Самодельная юла
Вот пример того, что вы можете сделать с помощью единственной бутылки из-под моющего средства.
Прежде всего, я удалил этикетку, и я очень хорошо промыл бутылку, избавляясь от всех мыльных остатков. Затем я расплавил пластик в тонкий блок (по методу, показанному на предыдущих этапах), и я сплющил его до толщины 5 мм (фото № 2).
Я нарисовал юлу, состоящую из 3-х частей и приклеил шаблон к блоку. Затем, разрезал все фигуры по линиям с помощью лобзика и отшлифовал вручную все края.
Спустя 2 часа, после того как я сделал блок из бутылки, и двадцати минут работы над блоком, у меня получилась эта классная юла.
Надеюсь, вам понравилось, и вы попытаетесь переработать несколько пластиковых бутылок, сделав из них что-нибудь интересное.
Спасибо, что прочитали мое руководство!
Как сделать резиновую крошку своими руками: измельчитель и переработка шин
С ростом количества автомобильного транспорта в результате увеличения объема отходов остро встал вопрос экологической ситуации. Ежегодно тысячи покрышек вывозятся на свалки и полигоны, где они становятся источником негативного воздействия на окружающую среду.
Автомобильные шины относятся к 4 классу опасных отходов из-за выделяемых в процессе разложения канцерогенных и токсичных веществ, которые разрушают биосферную оболочку. В последние годы, ужесточились требования утилизации отходов в крупных городах, регулярно проверяется соблюдение техники переработки резиновых изделий.
Правила пожарной безопасности запрещают складировать шины из-за возможности их самовозгорания. Деятельный человек, владеющий базовыми знаниями физики и столярными навыками может превратить переработку резиновых отходов в основной источник дохода. Резиновая крошка, получаемая в процессе утилизации, выступает вторичным сырьем в изготовлении товаров.
Из чего изготавливается резиновая крошка в домашних условиях
Резиновая крошка производится из пришедших в негодность автомобильных шин, они лучше поддаются механическому воздействию и извлечению металлической проволоки (корда). Переработка отработанных покрышек позволяет получить крошку требуемого диаметра при минимальных потерях сырьевого материала. Вырезанные из шин объемные фигуры используют в качестве украшения во дворах жилищных массивов или садовых участков. Нередко можно встретить клумбы, невысокие заборы, ограждения детских площадок, выполненных из шин.
Резиновой крошкой крупных размеров выкладывают дорожки частных домов и дачных участков, придавая им эстетически красивый вид. Резиновыми покрытиями, обладающими гидроизоляционными и шумопоглощающими свойствами, оборудуются игровые зоны и спортивные площадки.
Переработка небольшого количества резины в домашних условиях
Получение небольшого объема резиновой крошки в личных целях не требует большого количества сырьевого материала и специального оборудования. Воспользоваться можно подручными средствами, такими как ножницы, гильотинный резак или топор. Для разрезания старых шин также подойдет хорошо заточенный нож.
Этапы переработки шин в крошку в домашних условиях:
- удаление корда
- резка отработанных шин на ленты
- измельчение полученного сырьевого материала
Для работы с большими объемами резиновых отходов в коммерческих и личных целях необходимы финансовые вложения, покупка оборудования и наличие помещения для переработки сырьевого материала. Стоимость предлагаемых производителями агрегатов зависит от их мощности и комплектации. Отечественные и импортные производители предоставляют линии переработки резиновых отходов полного цикла. Владея базовыми знаниями по физике можно изготовить оборудование для переработки шин в крошку своими руками, отвечающее личным потребностям.
Способы изготовления крошки из шин
Способы получения резиновой крошки:
- Охлаждение сырья жидким азотом до хрупкого состояния и последующее измельчение. Такой вид переработки требует наличия специальных морозильных камер, охлаждение сырьевого материала производится до температуры -70 — -90 градусов и невозможно в домашних условиях.
- Измельчение резиновых изделий на специализированных линиях полного цикла переработки. Этот способ применяется на промышленном производстве, где выработка резиновой крошки производится в большом объеме и требует крупных финансовых вложений.
- Переработка резины в домашних условиях на самодельных агрегатах (дробилках). Располагая фрезерным и сварочным оборудованием можно изготовить измельчитель своими руками. При отсутствии такой возможности, детали можно заказать в мастерской по личным схемам. Себестоимость дробилки, изготовленной самостоятельно, значительно дешевле готового оборудования.
При регулярной переработке резиновых отходов требуется хорошо проветриваемое и просторное помещение, для установки оборудования и хранения большого количества резиновых отходов. Плюсом станет расположение помещения в промышленной зоне.
Устройство агрегата
Конструкция измельчителя представляет собой ножевой механизм (шредер), который позволяет перерабатывать шины, камеры и другие элементы из резины. Материал при таком способе измельчения сохраняет свою молекулярную формулу и не теряет свойства эластичности. Производительность оборудования полностью зависит от показателя его мощности.
Основные узлы агрегата по переработке резины:
- Электрический двигатель — обеспечивает скорость переработки резиновых отходов, рекомендованная мощность двигателя 4-5 кВт.
- Коробка с режущими дисками — измельчает сырьевой материал до требуемого размера.
- Решетка для калибровки крошки — регулирует диаметр получаемой резиновой крошки.
- Червячный редуктор — исключает заедание и замятие материала.
- Рама агрегата — обеспечивает устойчивое положение станка.
- Загрузочный бункер
- Направляющий лоток
Весь механизм станка помещается в корпус, поверх которого устанавливается загрузочный бункер. Перед погрузкой материала обязательно удаляются посторонние металлические предметы (шипы, гвозди и тд). Шины разрезаются на ленты сокращая время переработки.
Коробка с режущими дисками
Основная часть агрегата – это шредерная установка. Коробка содержит термически обработанные стальные фрезеровочные диски высокой прочности. Они достаточно износостойкие и не требуют частой замены при эксплуатации станка. Изготовление конструкции требует точного расчета отверстий и режущих дисков, поэтому работу стоит доверить конструктору.
Решетка для калибровки крошки
Под коробкой с фрезерными валами устанавливается калибрующая решетка, позволяющая регулировать диаметр резиновой крошки, получаемой при измельчении шин в шредере.
Редуктор червячный
Механический редуктор преобразует угловую скорость используя червячную передачу и позволяет перерабатывать резиновый материал различной эластичности без наматывания и зависания. Механическая передача вращательного движения устанавливается в диапазоне от 25 до 35 единиц, обеспечивая высокую производительность агрегата.
Рама агрегата
Безопасную работу гарантирует каркас станка, изготавливаемый из профильных материалов. Он обеспечивает устойчивое положение агрегата в период измельчения и погрузки сырьевого материала.
Загрузочный бункер
Станок оснащен бункером для загрузки шинного сырья, который для удобства располагается на верхней части корпуса и направляющим лотком. Они обеспечивают равномерное поступление сырьевого материала в шредер (измельчитель) препятствуя образованию заторов в процессе работы.
Приспособление для разрезания покрышки
Для разрезания шин и удаления металлического корда используется конструкция из стойки и несущей рамы. В корпусе расположена система зажима шины, которая во время резки вращается совместно с шиной. Стойка конструкции оснащена клиновидным ножом, настраиваемым на конкретный размер покрышки. Данная технология монтажа конструкции экономит время на подготовку расходного материала к дальнейшему измельчению в шредере.
Измельчение покрышек
Технологический процесс измельчения предполагает следующий порядок действий:
- Сортировка шинного сырья и удаление постороннего металла (гвоздей, шипов и тд)
- Удаление металлического корда
- Резка покрышек на ленты
- Измельчение сырьевого материала в шредере
- Калибровка полученной крошки
Вторичное использование
Резиновая крошка широко применяется в разных сферах производства, реализуется населению или используется в личных целях. Избыток пришедших в негодность автомобильных покрышек и резиновых изделий обеспечивает постоянное наличие расходного материала.
Стоимость резиновой крошки зависит от диаметра и качества гранул. Большим спросом пользуется порошкообразная крошка и гранулы диаметром 2-4 мм. Популярность данного размера обусловлена более низкими затратами на производство товаров и меньший расход клеевого вещества, цена которого превышает стоимость вторичного сырья в несколько раз.
Резиновая крошка используется для изготовления следующих изделий:
- Рулонные покрытия
- Резиновая обувь
- Тротуарная плитка
- Топливо
- Утеплители и уплотнители из резины
- Объемные фигуры, вырезанные из бывших в употреблении шин
- Дорожки для частных домов, садовых и дачных участков
- Гидроизоляционные и шумопоглощающие покрытия для детских и спортивных площадок
- Резиновые технические изделия
- Асфальтовые смеси
- Бесшовные резиновые покрытия
В настоящее время сфера утилизации считается перспективной для открытия собственного бизнеса из-за низкой конкуренции и растущего спроса на услуги по переработке отходов. Даже при небольшом объеме выполняемой работы, финансовые вложения, потраченные на оборудование, окупают себя в короткий срок. Переработка шин в дробилке признана самым экологически безопасным способом утилизации, позволяющим получать прибыль при небольших финансовых вложениях.
Точка плавления силиконового каучука
22 сентября 2015 г.
Это вопрос, который компании Silicone Engineering часто задают инженеры и дизайнеры, которые ищут точную температурную точку, при которой силиконовая резина начнет разлагаться при применении.
В большинстве случаев наши специалисты не могут дать однозначного ответа, не обсуждая условия окружающей среды, в которой будет находиться силикон, и температуры, которым будет подвергаться материал.
Силиконовый каучук, в отличие от большинства других каучуков, может выдерживать экстремальные температуры от 200 ° C до -60 ° C без деформации. Однако один аспект определяет, какие фактические температуры силикон действительно может выдерживать, и это ВРЕМЯ — Продолжительность времени, в течение которого силикон подвергается экстремальным температурам, определяет его срок службы и рабочие характеристики в применении, и это очень важный фактор при выборе резиновых материалов для приложений. .
Конечно, компания Silicone Engineering может говорить только о наших сортах силикона, но давайте приведем пример; Если силиконовая прокладка , изготовленная из нашего высокотемпературного сорта kSil ™ THT, подвергается воздействию температур до 300 ° C в течение непостоянных периодов, мы можем с уверенностью сказать, что наш силикон прошел испытания на выдерживание такой степени нагрева в течение коротких периодических периодов и будет поддерживать свои физические свойства.Однако, если инженер сообщил нам, что прокладка будет применяться в среде, где эта температура была постоянной 300 ° C, мы бы посоветовали, что силикон, скорее всего, разложится в течение более короткого срока службы, поэтому могут потребоваться другие варианты материалов. считается.
Тот же сценарий применим к нашим маркам силикона общего назначения. Материал был протестирован на способность выдерживать постоянную температуру 230 ° C, что в большинстве случаев подходит для многих высокотемпературных применений.Однако мы также знаем, что этот сорт будет хорошо работать при более высоких температурах 250 ° C в течение снова прерывистых периодов , поэтому вопрос о «времени воздействия» этих температур необходимо оценить, прежде чем мы сможем посоветовать подходящий сорт силикона. использовать при высоких температурах.
Следовательно, при понимании силикона или любого другого эластомера, используемого в условиях высоких / низких температур, период воздействия, который резина будет испытывать при определенной температуре, является решающим фактором при попытке ответить на вопрос «Какие температуры может выдерживать силиконовая резина».
Что мы действительно знаем, так это то, что для любых приложений, подвергающихся постоянному воздействию температур выше 150 ° C, скорее всего, потребуется силиконовая резина, чтобы обеспечить эффективную работу и более длительный срок службы. Именно здесь компания Silicone Engineering может предоставить силиконовые решения для многих секторов промышленности и приложений.
Насколько сильно нагревается силикон, прежде чем он расплавится?
Первое, что вы заметите, это то, что силикон плавится не только от температуры!
Например, при нагревании до 150 ° C вы увидите очень мало изменений в силиконе, даже если выдерживать при этой температуре в течение очень долгого времени. При 200 ° C силикон со временем станет тверже и менее эластичным, и если бы силикон нагреть до температуры выше 300 ° C, вы бы быстро заметили, что из-за таких экстремальных температур материал становится тверже и менее эластичным, но он не плавится.
Доступны специальные марки для дальнейшего повышения уже естественно высокой термостойкости силиконов, например, наш силикон марки THT, который можно периодически использовать при температурах до 300 ° C. Температура самовоспламенения силиконов составляет примерно 450 ° C, эксплуатация при такой высокой температуре не рекомендуется.
Если у вас есть еще один вопрос, который вы хотели бы задать одному из наших экспертов по силиконе, почему бы не перейти на страницу Задать вопрос экспертам , чтобы задать вопрос.
Найти продукты по отраслямЧто заставляет лед таять быстрее?
Что заставляет лед таять быстрее? Давайте рассмотрим простой эксперимент по плавлению льда, который понравится детям разного возраста.Дошкольное обучение, наука в детском саду и наука для младших классов могут использовать эксперименты со льдом как часть увлекательной учебной программы для детей. Мы любим простые научные эксперименты для детей!
ЧТО ДЕЛАЕТ ЛЬДА БЫСТРЕЕ? И ДРУГИЕ ЭКСПЕРИМЕНТЫ ПЛАВЛЕНИЯ ЛЬДА
ПРИМЕРЫ ФИЗИЧЕСКИХ ИЗМЕНЕНИЙ
Приготовьтесь добавить этот простой ледяной эксперимент в свои планы уроков по естествознанию в этом сезоне. Если вы хотите выяснить, почему лед тает быстрее всего, давайте углубимся! Лед — отличный способ исследовать физические изменения, в частности, состояния вещества и переход от жидкого к твердому.
ВАМ ТАКЖЕ МОГУТ ПОНРАВИТЬСЯ: Научные эксперименты с водой
Наши научные занятия и эксперименты предназначены для вас, родителей или учителей! Легко настроить, быстро выполнить, большинство действий займет всего 15–30 минут и доставляет массу удовольствия! Кроме того, наши списки расходных материалов обычно содержат только бесплатные или дешевые материалы, которые вы можете получить из дома!
Ниже вы исследуете:
- Сравнение твердых тел: что заставляет лед таять быстрее?
- Почему соль тает лед?
- Сохраняйте прохладу: можно ли предотвратить таяние льда?
- Ледяная гонка: Как быстро вы сможете растопить кучу кубиков льда?
Обязательно ознакомьтесь со списком рекомендованных книг в конце этой страницы!
ВСЕ ДЕТИ МОГУТ БЫТЬ УЧЕНЫМ!
Итак, что же такое ученый и как вы можете побудить своих детей стать хорошими учеными без особых усилий, модного оборудования или слишком сложных занятий, которые создают путаницу, а не любопытство.
Ученый — это человек, который стремится получить знания о мире природы. Угадай, что? Дети делают это естественно, потому что они все еще учатся и исследуют окружающий мир. Все эти исследования вызывают много вопросов!
Хороший ученый задает вопросы, исследуя мир природы, и мы можем еще больше поощрять это с помощью этих супер простых научных экспериментов. Знания приобретаются через все эти вопросы, исследования и открытия! Давайте поможем им с увлекательными научными занятиями, которые по-настоящему зажгут их внутреннего ученого.
Ознакомьтесь с нашим научным методом для детей . Мы также будем обновлять эту информацию с учетом новых передовых научных практик, которые будут применяться вместе с NGSS.
ЭКСПЕРИМЕНТЫ ПЛАВЛЕНИЯ ЛЬДА
Давайте приступим к изучению льда. Идите на кухню, откройте морозильник и будьте готовы экспериментировать с этими различными проектами льда.
ПРОБЛЕМА №1: ЧТО ДЕЛАЕТ ЛЕД РАСПЛАВЛЯЕТСЯ БЫСТРЕЕ?
В этом эксперименте вы исследуете, что заставляет лед таять быстрее, добавляя к нему несколько различных твердых частиц.
ВАМ НУЖНО:
- Кубики льда
- Форма, банки или контейнеры для маффинов
- Различные твердые тела. Вы можете начать с соли и сахара, но также можете добавить различные виды соли, пищевой соды, песка или грязи и т. Д.
- Секундомер или часы для определения времени эксперимента
НАСТРОЙКА ПЛАВНОГО ЛЬДА:
1: Добавьте 4-5 кубиков льда в 6 чашек для кексов. Убедитесь, что в каждом из них одинаковое количество льда.
2: Добавьте по 3 столовые ложки каждого твердого вещества в отдельный контейнер со льдом.
- Добавьте 3 столовые ложки пищевой соды в чашку №1.
- Добавьте 3 столовые ложки соли в чашку №2.
- Добавьте 3 столовые ложки песка в чашку №3.
Чашка №4, чашка №5 и чашка №6 являются вашими элементами управления, и ко льду ничего не добавляется.
3: Установите таймер, чтобы проверять кубики льда каждые 10 минут в течение 1/2 часа и записывать результаты. Тогда делайте выводы.
Что заставило лед таять быстрее всего?
РАСШИРЕНИЕ: Используйте таймер и запишите, сколько времени потребовалось каждому материалу, чтобы растопить лед.Запишите результаты. Попробуйте добавить твердые тела по своему выбору и запишите эти данные. Теперь превратите данные в график!
ПОЧЕМУ СОЛЬ РАСПЛАВАЕТ ЛЕД?
Неудивительно, что соль оказалась самой быстрой. На втором месте пищевая сода, так как это разновидность соли, которая снижает температуру замерзания воды. Однако это порошок. Песок особо не делал! Так почему же соль тает лед?
Соль снижает температуру замерзания или плавления воды. Соль взаимодействует с кристаллами льда и, смешиваясь с жидкой водой на тающем льду, ускоряет процесс таяния.
ICE STEM ЗАДАЧА № 2: КАК БЫСТРО МОЖНО РАСПЛАВИТЬ ЛЕД?
В этом эксперименте вы узнаете, как быстро можно растопить гору кубиков льда! При какой температуре тает лед? Читайте дальше, чтобы узнать больше!
Задача состоит в том, чтобы увидеть, как быстро вы сможете растопить кубики льда. Это можно делать индивидуально или в небольших группах. Если вы все же решите использовать формат малых групп, обязательно дайте детям несколько минут, чтобы вместе обсудить идеи.
ТАКЖЕ ПРОВЕРИТЬ: Хеллоуинский эксперимент с таянием льда
ВАМ ПОТРЕБУЕТСЯ:
- Кубики льда
- Плиты
- Бумажные полотенца
ПРЕДЛАГАЕМЫЕ ПРЕДМЕТЫ:
- Соль
- Ткань
- Бумага
- Малые пластиковые контейнеры для пищевых продуктов
ЭКСПЕРИМЕНТАЛЬНАЯ УСТАНОВКА:
ШАГ 1: Дайте каждому ребенку или группе детей материалы, включая бумажные полотенца и определенное количество кубиков льда на тарелке.
ШАГ 2: Предложите детям использовать материалы, чтобы попытаться быстро растопить лед!
ШАГ 3: Когда гонка закончится (установите конкретное время, которое подходит вам), попросите группы поделиться этапами своего процесса плавления. Обсудите, что сработало и почему? Также обсудите, что бы вы сделали иначе в следующий раз!
РАСШИРЕНИЕ: Используйте таймер и запишите, сколько времени понадобилось каждому ребенку или группе детей, чтобы растопить лед. Запишите результаты.Попробуйте еще два раза и запишите эти данные. Теперь превратите данные в график!
ПРИ КАКОЙ ТЕМПЕРАТУРЕ ЛЕД плавится?
При какой температуре тает лед? Вода не только замерзает при 0 градусах Цельсия или 32 градусах по Фаренгейту, но и тает при той же температуре! Вот почему мы называем эту температуру точкой ЗАМЕРЗАНИЯ и ТЛАПЕНИЯ воды!
При этой температуре происходит замерзание, поскольку тепло отводится от воды с образованием кристаллов льда. Чтобы растопить лед, нужно использовать тепловую энергию.Тепловая энергия сначала идет на разрушение льда, прежде чем он поднимет температуру воды.
Лед при температуре замерзания воды на самом деле содержит меньше энергии или тепла, чем вода той же температуры!
ЧТО ПЛАВИТ ЛЬД БЫСТРЕЕ?
Есть много способов растопить лед. Самый простой способ — просто дать льду таять при комнатной температуре. Тепловая энергия в более теплой комнате разрушает структуру льда и превращает его в воду. Мы постоянно видим это с кубиками льда в наших стаканах для напитков или если случайно оставляем один на прилавке.
Чтобы ускорить процесс таяния, вы можете держать кубик льда в руке (бррр, холодно), так как ваше тело обычно теплее, чем в комнате. Чтобы он растаял еще быстрее, попробуйте как можно быстрее потереть руки, прежде чем держать кубик льда. Когда вы быстро потираете руки вместе, вы создаете трение, которое добавляет тепла за счет повышения температуры!
Еще один способ получить больше тепла и более высокую температуру — это потереть кубик льда о кусок ткани.
Как насчет того, чтобы положить кубик льда на темный кусок ткани или бумаги и поместить его на солнечный свет? Темные цвета лучше сохраняют тепло от солнечного света, чем светлые, поэтому вам может быть жарче в темной футболке в разгар жаркого летнего дня!
Наконец, мы знаем, что еще один способ быстро растопить лед — это соль, которую мы обнаружили в первом эксперименте выше!
Щелкните ниже, чтобы получить быстрые и простые таблицы научных методов.
ПРОБЛЕМА №3: Как предотвратить таяние льда?
В этом третьем эксперименте вы исследуете, как предотвратить таяние льда. Вместо того чтобы смотреть, как тает припай, давайте попробуем охладить его!
ВАМ ТАКЖЕ МОЖЕТ ПОНРАВИТЬСЯ: Blubber Experiment
Задача состоит в том, чтобы увидеть, как медленно вы можете предотвратить таяние льда, уменьшив количество тепла или энергии, окружающей лед. Это также можно делать индивидуально или в небольших группах.Помните: если вы все же решите использовать формат малых групп, убедитесь, что у детей есть время, чтобы вместе обсудить идеи.
ВАМ НУЖНО:
- Кубики льда
- Маленькие сумки на молнии
- Маленькие пластиковые контейнеры (как можно ближе к одному размеру, чтобы они были однородными)
ПРЕДЛАГАЕМЫЕ ПРЕДМЕТЫ:
Есть довольно много предметов, которые потенциально могут быть использованы в этом ледяном STEM испытании! Обратите внимание на мусорный ящик, ящик для мусора, гараж и многое другое.Здесь также пригодится наш инженерный комплект для долларового магазина. Вы можете использовать имеющиеся у вас предметы для недорогого STEM-задания.
- Алюминиевая фольга
- Арахис фасовочный
- Войлок
- Ткань
- Крафт пена
- Ватные шарики
- Помпоны
- Куски пенопласта
- Солома или сено
- Салфетки или бумажные полотенца
- Оберточная бумага или папиросная бумага
- Пузырьковая пленка
- Газета
- Пряжа
- Вощеная бумага
- Пластиковая пленка
- Воздушные шары
- Лента
- Резинки
ЭКСПЕРИМЕНТАЛЬНАЯ УСТАНОВКА:
ШАГ 1: Мозговой штурм.Какие самые лучшие материалы предотвращают таяние льда?
ШАГ 2: Решите, какие материалы или комбинацию материалов вы хотите использовать, чтобы кубики льда не таяли, изолируя их! Создайте один или несколько изолированных контейнеров, чтобы проверить свои идеи. Вы можете выбрать определенное количество времени для этой части проекта или разделить задачу STEM на несколько дней.
ШАГ 3: Когда все изотермические контейнеры готовы, поместите кубик льда в небольшой пластиковый пакет с застежкой-молнией, а затем поместите его в изотермический контейнер.Обязательно закрывайте крышки!
СОВЕТ: В качестве элемента управления вы можете поместить сумку с застежкой-молнией и кубиком льда в аналогичную емкость без теплоизоляции. Этот контрольный контейнер предназначен для сравнения. Создавая элемент управления, вы позволяете определить, влияют ли выбранные вами материалы (переменные) на результат!
ШАГ 4: Поместите все контейнеры в сухое прохладное место вдали от источников тепла или прямых солнечных лучей. Никакой дополнительной энергии здесь не требуется!
ШАГ 5: Проверяйте контейнеры каждые 10 минут.Обратите внимание на любые различия. Записывайте свои наблюдения, пока весь лед полностью не растает. Убедитесь, что вы не трогаете лед и не вынимаете лед из контейнера во время наблюдений.
Подумайте, какие материалы работают лучше всего и почему. Как вы можете улучшить свои результаты?
РАСШИРЕНИЕ: Выберите одну вещь, которую нужно изменить (переменную), например, меньший или больший контейнер или больший или меньший кубик льда.
РАЗГОВОР ОБ ЭТОМ: Отличной темой для обсуждения было бы обсуждение того, где изоляция используется в наших домах или в машинах, таких как автомобили?
БЫСТРАЯ НАУКА
Всем известно, что когда вы достаете лед из морозильника, он со временем тает.Однако большинство из нас не задумывается, почему это происходит. Воздух вокруг кубиков льда обычно теплее, чем лед, и из-за этого лед (твердый) превращается в воду (жидкость). Состояния материи тоже!
Итак, если вы не хотите, чтобы лед таял, вам нужно удерживать теплый воздух (тепловую энергию) подальше от льда с помощью изоляционного материала. Некоторые отличные изоляторы только для намека — войлок, газеты и шерсть. Изоляция предотвращает передачу тепла льду, поэтому кристаллы льда дольше остаются ледяными и холодными.
Изоляциятакже используется для сохранения тепла в наших домах зимой в холодных частях света, не допуская холода! Кроме того, изоляция может удерживать тепло в доме даже в жаркий день! Изоляция может оставаться комфортной как при понижении, так и при повышении температуры!
РЕКОМЕНДУЕМЫЕ КНИГИ ДЛЯ ICE STEM
Посмотрите эти забавные книги, чтобы продолжить свои эксперименты по таянию льда. Это партнерские ссылки Amazon для вашего удобства, и мы получаем часть всех продаж, если вы совершаете покупки по этим ссылкам.
ВЕСЕЛЫЕ СПОСОБЫ УЗНАТЬ, ЧТО ДЕЛАЕТ ЛЕД РАСПЛАВЛЯТЬСЯ БЫСТРЕЕ!
Откройте для себя другие увлекательные и простые занятия в области науки и STEM прямо здесь. Щелкните ссылку или изображение ниже.
Ищете удобные для печати задания и недорогие решения проблем?
Мы вам поможем…
Нажмите ниже, чтобы получить быстрые и легкие задания по STEM.
Как растопить шоколад в пароварке, микроволновой печи, духовке или га
Задача
Если вы запекаете, скорее всего, вы встретили рецепт с использованием растопленного шоколада, и, скорее всего, ваш рецепт содержал хоть какие-то инструкции.Шеф-кондитеры и профессионалы в области выпечки, в том числе четверо, с которыми мы говорили, обычно имеют предпочтительный метод плавления, и, хотя они не всегда соглашаются, существует несколько неоспоримых правил.
Шоколад требует тонкой руки — думайте о нем как о грудинке в мире десертов и выбирайте низкий и медленный подход. Никогда не растапливайте шоколад прямо на горячей сковороде; это опалит. Чистые и сухие инструменты необходимы, так как даже небольшое количество воды может испортить ваш красивый шоколад.
Отдельные шоколадные диски — это здорово, но избегайте чипсов, которые разработаны так, чтобы сохранять свою форму и не будут такими жидкими при плавлении.Нарежьте плитку шоколада на мелкие однородные кусочки, чтобы он таял быстро и равномерно, и отлично подойдет к молоку и белому шоколаду, которые плавить сложнее.
Техника: пароварка
Использование пароварки — традиционный метод плавления, хотя на самом деле у немногих людей есть настоящая пароварка. Большинство домашних поваров и профессионалов импровизируют, ставя жаропрочную миску на кастрюлю, наполовину наполненную водой. «Несмотря на распространенное предупреждение о том, что миска никогда не должна касаться воды, на самом деле все в порядке», — говорит Алиса Медрич, автор многочисленных книг о шоколаде, а также недавно опубликованной книги Flavor Flours .Ей нравится создавать «открытую» водяную баню, в которой миска с шоколадом стоит на большой сковороде с едва кипящей водой, чтобы вы могли следить за происходящим и не перегревать шоколад.
Ник Мальджери, основатель программ выпечки в Институте кулинарного образования Нью-Йорка, придерживается пароварки, но выключает пламя перед тем, как поставить сверху чашу с шоколадом. В любом случае, помешивание является ключевым моментом. Это не должно быть постоянным, говорит Лиза Вега, исполнительный шеф-кондитер Dandelion Chocolate в Сан-Франциско, но держитесь поблизости и перемешивайте резиновым шпателем каждые несколько минут.
СВЯЗАННЫЕ 11 Choc Recipes »
Техника: микроволновая печь
Если кипячение воды и импровизированные пароварки звучат суетливо, не отчаивайтесь. Каждый эксперт, с которым мы говорили, полностью согласен с использованием микроволновой печи. Это быстрее и менее грязно, и может быть лучшим вариантом, если вам нужно быстро растопить небольшое количество шоколада.
Средняя или половинная мощность может быть идеальной для некоторых микроволновых печей; разморозка может быть лучше для других. Мальжери даже добился успеха, используя полную мощность.Уловка, по его словам, состоит в том, чтобы использовать 30-секундные интервалы и перемешивать после каждого всплеска тепла. Медрич отмечает, что шоколад часто более растоплен, чем кажется, поэтому всегда помешивайте, прежде чем наносить ядерный заряд. Микроволны могут быть синонимом скорости, но вам все равно нужно работать медленно.
Еще два варианта
Если у вас нет микроволновой печи, есть еще две возможности. Минди Сигал, кондитер и владелец ресторана Hot Chocolate в Чикаго и автор готовящегося к выпуску Cookie Love , рекомендует ставить миску с шоколадом на духовку с температурой 350 °.Это займет больше времени, но тепло духовки медленно и равномерно растопит шоколад — это метод, который она использует на своей профессиональной кухне.
Более быстрый подход — это метод фена Medrich, который работает только с меньшими объемами, но прост и просто забавен. Начните с большого расстояния, направьте сушилку прямо в миску с шоколадом и постепенно приближайтесь к нему по мере его таяния. Одно предупреждение Медрича: если вы не будете осторожны, из миски могут вылететь более мелкие кусочки. И уж точно не хотим терять шоколад.
Как удалить расплавленный пластик из духовки
Английская компания по обслуживанию недвижимости- Посетитеantasticservices.com Категории
Меню
- Товары для дома
Категории
- Посмотреть все Товары для дома
- Электрические наконечники
- Охрана и безопасность
- Отделка
- Сантехника
- Garden Advice
Категории
- Посмотреть все Садовые советы
- Уход за газоном
- Правила сада
- Ландшафтный дизайн
- Заводы в Великобритании
- Руководства по очистке
Категории
- Посмотреть все руководства по очистке
- Чистка ковров
- Очистка духовки
- Мойка окон
- Разборка
- Советы по перемещению и упаковке
Категории
- Посмотреть все советы по перемещению и упаковке
- Переезд за границу
- Переезд офиса
- Советы по упаковке
- Советы по хранению
- Проблемы с вредителями
Категории
- Просмотреть все проблемы с вредителями
- Насекомые
- Заражение грызунами
- Истории компании
Категории
- Посмотреть все истории компании
- В центре внимания
- Партнеры
- Жизнь в изоляции
- Товары для дома
- Поиск Общие селекторы
Только точные совпадения
Только точное совпадение
Искать в заголовке
Искать в названии
Искать в содержании
Искать в содержании
Искать в отрывке
Искать в сообщениях
Искать в сообщениях
Искать на страницах
Искать на страницах
Скрытый
Фильтр по категориямВсе о лужайке
Все о лужайке
Советы по чистке ковров
Советы по чистке ковров
Как часто вы должны делать это ради выгоды?
Преимущества микронидлинга в домашних условиях
Введение игл в кожу — это похоже на то, с чем должен обращаться только профессионал, поэтому, когда дело доходит до микронидлинга (то есть небольших колотых ран на коже), зачем выбирать домашнюю версию? Что ж, обошлось.
Можно с уверенностью предположить, что каждый сеанс будет стоить от 200 до 700 долларов — цена, недоступная для многих людей, особенно когда вам нужно дополнительное лечение.
Ролики онлайн, однако, доступны в среднем по 20 долларов.
«Домашние процедуры редко бывают достаточно глубокими, чтобы дать впечатляющие результаты [для более пораженной кожи], но могут улучшить отшелушивание и впитывание продукта», — говорит Динн Мраз Робинсон, доктор медицины, FAAD, доцент клинической дерматологии в Йельской больнице Нью-Хейвен и соавторы. создатель Pure BioDerm.«Пациенты, которые регулярно проводят домашнее лечение в течение четырех-шести месяцев, определенно могут увидеть улучшения».
Что касается процедуры микронидлинга в офисе, потенциальные преимущества включают:
- уменьшение шрамов от угревой сыпи и обесцвечивание
- уменьшение морщин и растяжек
- омоложение кожи для текстуры и цвета лица
- улучшение впитывания продукта
- увеличение количества кожи толщина
Вот что вам нужно знать о микронидлинге в домашних условиях, от выбора ролика до предотвращения инфекций.
Исследования показали, что некоторые люди могут добиться значительного улучшения состояния кожи после двух-трех сеансов с иглами длиной 1,5 миллиметра (мм), но обычно это делается в офисных условиях. Вам нужно будет начать с малого, обычно менее 0,15 мм.
Несколько брендов для домашнего использования, которые стоит попробовать:
Выбор дома по сравнению с профессионалом
Более крупная игла не означает более быстрых результатов. Терпение — это достоинство, когда дело доходит до микронидлинга, и если контроль вызывает беспокойство, вы можете вместо этого обратиться к профессионалу.
Если лечение в офисе соответствует вашему бюджету, хорошая новость заключается в том, что результаты могут быть быстрее, процесс станет более безопасным, и вы сможете добиться лучших результатов, поскольку они, вероятно, будут использовать более длинные и более острые иглы медицинского класса.
«Серия очень агрессивных процедур может дать результаты, аналогичные световым или даже более глубоким процедурам лазерной шлифовки. Результаты обычно видны после одного-четырех процедур », — говорит Кэтлин Уэлш, доктор медицины, дерматолог из Сан-Франциско и основательница косметической дерматологии Bay Area.
Она также предупреждает, что тем, кто попытается сделать валик дермы дома, придется дольше ждать.
«Крошечные травмы, которые вызывают тонкие иглы, — это сигнал нашей коже для выработки нового коллагена», — утверждает Робинсон. «Синтез нового коллагена может занять от трех до шести месяцев».
Поскольку здесь используются иглы, безопасность будет вашей проблемой номер один при выполнении микроигл в домашних условиях.
«Если пациент хочет лечиться дома, он должен тщательно очистить кожу перед этим и продезинфицировать свои инструменты для микронидлинга, чтобы снизить риск заражения», — говорит Уэлш.«Они также должны быть осторожны, чтобы не надавить на игольное устройство слишком сильно, так как это может привести к образованию рубцов. Сообщалось также об аллергических реакциях на продукты, применяемые после инъекции, при лечении в офисе и в домашних условиях ».
Домашний набор для микронидлинга
Вот ваш пятиступенчатый метод:
1. Дезинфицируйте дерматический валик
Всегда начинайте с дезинфекции дерматологического валика, давая ему пропитаться 70-процентным изопропиловым спиртом примерно на 5-10 минут, прежде чем ты начинаешь.
2. Вымойте лицо
Очистите кожу мягким очищающим средством со сбалансированным pH, а затем снова очистите ее. Вам также следует аккуратно протереть лицо этим 70-процентным изопропиловым спиртом, прежде чем начинать кататься.
Если вы чувствительны к боли, подумайте о применении обезболивающего крема после умывания. Вам определенно понадобится , если вы перешли на более длинные иглы.
При необходимости нанесите любой обезболивающий крем.«Это может быть немного неудобно из-за глубины и калибра используемых игл», — говорит Робинсон, отмечая, что она предлагает своим пациентам вдыхать закись азота по мере необходимости, когда она выполняет процедуру в офисе.«Я использую обезболивающий крем местного действия за 30 минут до процедуры. После процедуры у вас будет точечное кровотечение ».
3. Начните катиться
Перед тем, как начать, мысленно разделите свое лицо на четыре части, полностью избегая области вокруг глаз:
- верхний левый
- верхний правый
- нижний левый
- нижний правый
Осторожно и твердо перекатывайтесь по одной области в одном направлении (вертикально или горизонтально) два-три раза и обязательно поднимайте ролик перед каждым рулоном.
Допустим, вы начинаете вертикально: после того, как вы пройдете один участок таким образом 2–3 раза, слегка переместите ролик и повторяйте, пока вы не покроете весь участок в одном направлении. Затем вернитесь и повторите весь процесс в этом разделе, но на этот раз прокручивайте горизонтально, используя узор перекрестной штриховки.
Для визуальных инструкций посмотрите видео ниже:
4. Ополосните лицо
Промойте лицо чистой водой только после того, как закончите кататься, и промокните его насухо чистой подушечкой.
5. Продезинфицируйте дерма-валик
Сначала промойте дерма-валик с мылом для посудомоечной машины. Затем снова погрузите его в 70-процентный изопропиловый спирт на 10 минут и положите обратно в коробку.
Не ждите слишком долго, чтобы заменить дерма-валик — вам следует отказаться от текущего валика и заменить его новым после 10-15 использований, поэтому вам может понадобиться новый валик каждый месяц, если вы катаетесь несколько дней в неделю.
Одно из самых больших преимуществ микронидлинга — это его способность помогать таким продуктам, как сыворотки и увлажняющие кремы, проникать глубже и становиться более эффективными.
«[Прокалывание улучшает проникновение сыворотки] в более глубокие слои», — говорит Уэлш. Проницаемость кожи — это хорошо, если вы вводите полезные для кожи ингредиенты, но это также означает, что вы должны быть особенно осторожны с продуктами, которые вы используете.
«Использование дома должно быть разумным», — говорит Робинсон. «Одна из самых больших проблем с микронидлингом — это отсутствие актуальных или химических веществ, которые не должны проникать сквозь эпидермис глубже в нашу кожу».
Вот ингредиенты, которые нужно искать в ваших сыворотках:
- Витамин С. Чрезвычайно важно найти высококачественную сыворотку для осветления и стимулирования выработки коллагена. «Имеются сообщения о случаях гранулем (твердых узелков) у людей, применяющих местные средства, такие как витамин С, которые содержат ингредиенты в составе, которые вызывают реакцию на инородное тело в коже», — говорит Робинсон. «Кроме того, стерильность игл имеет первостепенное значение для предотвращения инфекции».
- Гиалуроновая кислота. Гиалуроновая кислота притягивает и удерживает влагу, поэтому нанесение ее после микронидлинга поможет сделать кожу гладкой и увлажненной.
- Пептиды . Пептиды меди представляют собой естественные комплексы в коже, которые при местном применении, как было обнаружено, увеличивают выработку коллагена.
- Факторы роста . Факторы роста — это белки, которые способствуют производству здоровых клеток и тканей. Они связываются с клетками кожи и сигнализируют о необходимости восстановления и омоложения кожи. При микронидлинге они действуют рука об руку с утолщением кожи.
Частота процедур будет зависеть от длины игл дерма-валика и чувствительности вашей кожи.Если ваши иглы короче, вы можете перекатывать их через день, а если иглы намного длиннее, вам может потребоваться интервал между процедурами каждые три-четыре недели.
Если вы действительно хотите улучшить свои результаты, вы можете рассмотреть возможность добавления дополнительных процедур по уходу за кожей между сеансами микронидлинга.
Согласно Dermascope, профессиональному журналу по уходу за кожей, микронидлинг и химический пилинг дают лучшие результаты в качестве дополнительных методов лечения при применении с интервалом от 4 до 6 недель.
Если ваша кожа переносит это, другие процедуры, такие как гуаша и акупунктура лица, могут ускорить ваши результаты, если их перемежать с микронидлингом.
Помните, что если вы выполняете микронидлинг дома, вы будете прокалывать кожу, поэтому маловероятно, что процедура будет полностью приятной.
«Уровень боли зависит от агрессивности лечения», — говорит Уэлш. «Кровотечение всегда возникает и выявляется при более легком лечении и более сильное при более глубоком.Кожа открытая, поэтому мы рекомендуем использовать только специальные мягкие, не раздражающие продукты в течение первых 24 часов после процедуры ».
«Безопасность прежде всего!» — говорит Робинсон. «Не применяйте местные средства [например, кислоты или агрессивные активные вещества], которые не должны сочетаться с микронидлингом. Кроме того, не забывайте чистить иглы после каждого использования. Каждый раз, когда вы прокалываете кожу, вы рискуете вызвать инфекцию ».
Хотя эксперты согласны с тем, что микронидлинг может быть полезен для людей, которые хотят повысить уровень коллагена и лечить такие проблемы, как тонкие линии и шрамы от прыщей, не все являются кандидатом.
«Пациенты с розацеа обычно не переносят микронидлинг», — говорит Уэлш. «Хотя некоторые пациенты с активными угрями могут получить пользу, мы предпочитаем не лечить пациентов с активными угрями из-за возможности обострения. Пациентам с очень тонкой кожей и чувствительной кожей следует избегать использования микроигл ».
Микроиглы в домашних условиях, вероятно, не то, что одобрило бы большинство экспертов по коже, но если вы собираетесь включить этот шаг по уходу за кожей в свой распорядок дня, действуйте осторожно и проведите исследование.
«Эффективность лечения зависит от глубины, достигаемой набором игл [длины набора игл на устройстве]», — говорит Уэлш.
Помните не только о безопасности, но и о том, что эти процедуры требуют повторения. Исследования показали долгосрочные преимущества всего от трех процедур, но, опять же, индивидуальный успех будет зависеть от множества факторов и большого терпения.
«Домашние устройства не способны производить столько же изменений, как офисные медицинские устройства», — говорит Робинсон. «Помните, что изменение требует времени, и наилучшие результаты видны после серии процедур».
Мишель Константиновски — журналист из Сан-Франциско, специалист по маркетингу, писатель-призрак, выпускница Высшей школы журналистики Калифорнийского университета в Беркли.Она много писала о здоровье, образе тела, развлечениях, образе жизни, дизайне и технологиях для таких торговых точек, как Cosmopolitan, Marie Claire, Harper’s Bazaar, Teen Vogue, O: The Oprah Magazine и других.
Simple English Wikipedia, бесплатная энциклопедия
Резина — это материал, который может растягиваться и сжиматься. Это полимер. Его можно производить из природных источников (например, натуральный каучук) или синтезировать в промышленных масштабах. Многие вещи сделаны из резины, например перчатки, шины, заглушки и маски.Некоторые вещи можно сделать только из резины.
Иногда это слово означает только натуральный каучук (латекс ). Натуральный каучук производится из белого сока некоторых деревьев, таких как Hevea brasiliensis (Euphorbiaceae). Другие эластомеры, называемые синтетическими каучуками, производятся химическими процессами.
Hevea brasiliensis — это дерево, из которого производится большая часть каучука. Другие растения, которые имеют особый сок (называемый латексом): инжир ( Ficus elastica ), Castilla (панамское каучуковое дерево), молочай, салат, одуванчик обыкновенный, Taraxacum kok-saghyz (русский одуванчик), Scorzonera tau-saghyz , и Гуаюле.
В 1800-х годах большая часть сока для производства каучука поступала из Южной Америки. В 1876 году Генри Викхем получил семена каучуковых деревьев в Бразилии, отвез их в сады Кью, Англия, и отправил на Цейлон (Шри-Ланка), Индонезию, Сингапур и Британскую Малайю. Позже Малайя (ныне Малайзия) производила больше всего резины. Люди пытались выращивать каучук в Индии в 1873 году в Ботаническом саду Калькутты. Первые фермы Hevea в Индии были построены в Таттекаду в Керале в 1902 году. Свободное государство Конго в Африке также выращивало много деревьев для производства каучука в начале 20 века, и большинство людей, которые работали на этих фермах, были вынуждены труд, работа.Либерия и Нигерия также начали выращивать деревья для производства каучука.
Шарль Мари де ла Кондамин представил образцы каучука Королевской академии наук Франции в 1736 году. [1] В 1751 году Франсуа Френо прочитал в Академии документ (в конечном итоге опубликованный в 1755 году), в котором описаны многие свойства каучука. . Это было названо первой научной работой по каучуку. [1]
В 1770 году британский химик Джозеф Пристли заметил, что каучук очень хорош для удаления следов карандаша с бумаги.
Натуральный каучук плавится при нагревании и замерзает на морозе. В 1844 году Чарльз Гудиер нашел способ улучшить натуральный каучук с помощью химического процесса, известного как вулканизация, который сделал его полезным во многих других продуктах, включая, спустя десятилетия, шины.
В 20 веке начали использоваться синтетические (искусственные) каучуки, такие как неопрен. Они широко использовались, когда Вторая мировая война прекратила поставки натурального каучука.